Menghemat Waktu dan Uang dengan Pemantauan Kondisi
Sebuah studi emisi akustik (AE) baru-baru ini mengidentifikasi potensi kegagalan bantalan kritis yang menjadi tindakan pencegahan yang direncanakan untuk produsen makanan terkemuka. Ini juga menghindari biaya yang cukup besar dan waktu henti yang tidak direncanakan.
Peralatan emisi akustik dan alat utama yang digunakan selama rute inspeksi yang direncanakan dibuat oleh Holroyd Instruments. Contoh ini akan menunjukkan nilai peralatan jenis ini dalam menghindari peristiwa besar yang tidak direncanakan yang dapat menimbulkan konsekuensi biaya besar bagi bisnis. Kerusakan tambahan pada peralatan terkait akan terbukti sangat mahal, dan waktu tunggu untuk membangun kembali dapat menyebabkan downtime yang ekstensif yang berarti pelanggan yang tidak puas tidak dapat mengandalkan ketersediaan stok.
Cerita dimulai pada April 2010 ketika beberapa pembacaan awal yang meningkat dicatat pada dua titik simpul pada gearbox transfer step-down besar yang diambil sampelnya pada rutinitas tujuh hari. Pembacaan marabahaya ditinggikan dan memicu tingkat alarm. Mereka menjadi perhatian dan terbukti pada inspeksi berikutnya. Pembacaan tinggi ketiga yang merupakan bagian dari tren naik memicu perintah kerja yang direncanakan dalam sistem manajemen pemeliharaan terkomputerisasi (CMMS) untuk menyelidiki dan mengambil tindakan lebih lanjut. Peralatan ini tidak dapat diabaikan begitu saja, karena pada saat itu terkendala oleh tuntutan produksi yang tinggi. Pengalaman dengan perubahan bantalan yang direncanakan sebelumnya juga memainkan peran penting dalam eskalasi risiko.
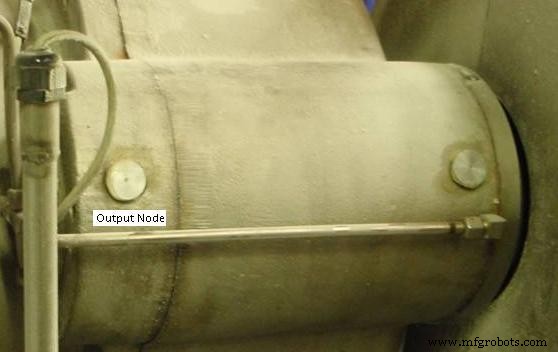
Sisi masukan dari transfer gearbox ditunjukkan dengan titik simpul bantalan keluaran di sisi kiri.
Pada pemeriksaan yang lebih rinci, ditentukan bahwa bantalan dengan tekanan tertinggi memang merupakan bantalan keluaran yang dicurigai. Suara klik terdengar keras dan jelas pada bantalan ujung keluaran. Dua bantalan di lokasi simpul berada di jalur penggerak motor di ujung input dan output gearbox transfer. Bantalan yang berdekatan pada gigi step-down heliks yang besar masih terbaca rendah dan tidak memiliki bunyi klik yang terdengar. Manajer teknik diberitahu bahwa ada anomali pada salah satu bantalan input, bahwa yang lain dalam kondisi baik dan produksi dapat dilanjutkan dengan pemantauan kondisi yang ditargetkan. Pengambilan sampel oli rutin ditingkatkan dari bulanan menjadi setiap dua minggu. Inspeksi AE ditingkatkan, dengan pembacaan spektrum sekarang dalam siklus empat hari. Ini akan memberikan beberapa bukti komparatif ketika bantalan baru akhirnya dipasang.
Perubahan yang direncanakan dari set bantalan diatur dengan perencana produksi, manajer pemeliharaan dan spesialis produk. Menjadi jelas bahwa peralatan tersebut harus beroperasi setidaknya selama enam bulan lagi sampai tersedia. Rencana kontinjensi dirumuskan untuk perubahan darurat jika salah satu pembacaan AE atau sampel oli menunjukkan kemajuan menuju kegagalan. Peringatan dikeluarkan bahwa ini bisa terjadi dengan cepat jika bantalan gagal. Satu set bantalan baru dibeli, dan pertemuan dijadwalkan dengan produsen bantalan untuk memeriksa bantalan bekas saat akhirnya diganti pada awal 2011.
Pembacaan AE tetap pada level yang tinggi selama fase menunggu yang lama ini, dan hasil sampel oli menunjukkan tidak ada pembacaan yang meningkat pada elemen kunci yang terkait dengan kegagalan bantalan rol. Selama minggu-minggu sebelum pembaruan, banyak spektrum diambil dari semua titik gearbox untuk evaluasi di masa mendatang. Ini akan mengesampingkan frekuensi dari pompa oli dan komponen lain di sekitar rakitan. Grafik spektrum amplop AE sebelum perubahan bantalan ditunjukkan di bawah ini.
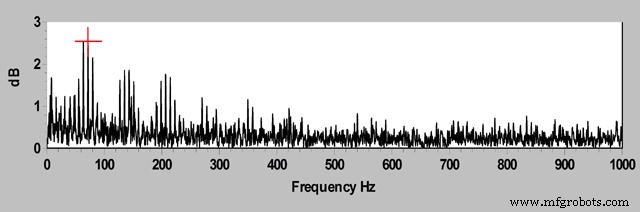
Seperti yang bisa dilihat, ada sesuatu yang menciptakan lonjakan pada 73Hz, yang kebetulan cocok dengan frekuensi balapan bantalan. Ini memberikan petunjuk bahwa ada semacam cacat permukaan balapan dan bukan elemen yang rusak atau kandang yang hancur.
Penggantian bantalan akhirnya terjadi, dan pabrik produksi dihidupkan dalam waktu 12 jam sehingga peralatan tidak mengalami downtime yang tidak direncanakan. Set bantalan bekas dikembalikan dengan gearbox transfer, dan dua unit diturunkan. Pada pemeriksaan pertama, mereka berdua tampak mirip dan dalam keadaan baik. Elemen dan sangkar kemudian dibongkar dari bagian luar dan dalam, dengan hati-hati agar tetap rapi dan dalam aspek yang benar untuk dipasang kembali nanti.
Menjadi jelas bahwa pada bantalan keluaran yang dicurigai, kebocoran besar pada balapan bagian dalam telah berkembang, dan setiap elemen diadu dengan puing-puing yang telah dipancarkan. Pada titik ini, perwakilan dari produsen bantalan diundang untuk mengunjungi dan memeriksa bantalan. Dia setuju bahwa bantalan telah bertahan dengan sangat baik mengingat atmosfer dan panas di mana mereka telah beroperasi selama hampir 10 tahun. Ini akan dianggap sebagai mode kegagalan akhir masa pakai. Ini mungkin telah berlangsung berbulan-bulan lagi atau bisa dipercepat hingga gagal dalam beberapa hari atau minggu. Foto di bawah ini adalah spall yang berukuran panjang sekitar 10 mm dan lebar 2,5 mm.
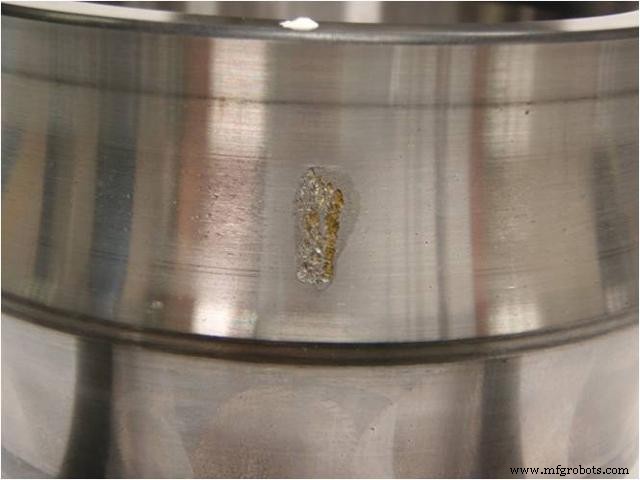
Kerusakan spall pada balapan ditunjukkan di atas dengan tepi berbulu dan lubang permukaan di area yang terisi spalling. Perhatikan lapisan bahan berikutnya di sisi kanan yang akan memberi jalan.
Ketika pekerjaan perbaikan telah selesai, sampel spektrum tambahan dicatat dan dipantau untuk mempelajari lebih lanjut. Tingkat kebisingan karpet lebih rendah, dan skala desibel adalah sepertiga dari contoh grafik sebelumnya. Puncak maksimum sekarang kurang dari 0,4 desibel, sedangkan tingkat karpet kurang dari 0,2 desibel.
Kesimpulannya, sistem dan alat yang diandalkan setiap hari terbukti efektif dalam menangkap anomali ini sebelum berubah menjadi peristiwa besar. Kuncinya adalah keterlibatan penuh bagian teknik dengan operasi untuk merencanakan pekerjaan perbaikan dengan gangguan sesedikit mungkin.
Di antara pelajaran yang didapat adalah bahwa frekuensi inspeksi pada interval tujuh hari sudah benar untuk pabrik kritis ini, tindakan pencegahan dimulai pada kesempatan paling awal, peralatan memungkinkan penentuan kesalahan bantalan, fasilitas audio memungkinkan referensi kedua yang menghubungkan rpm dengan klik yang terdengar dan bahwa ini semua memberikan bukti yang cukup untuk pekerjaan yang direncanakan untuk dimulai pada kesempatan paling awal.
Analisis akar penyebab dilakukan langsung setelah penggantian bantalan selesai untuk menyelidiki rekomendasi di masa mendatang untuk menyervis peralatan ini. Diputuskan bahwa karena bantalan telah mencapai siklus akhir masa pakainya, tidak perlu mengubah pemeliharaan terencana di masa mendatang. Pemantauan kondisi dengan AE telah memberikan kepercayaan diri untuk mendeteksi anomali apa pun pada tahap yang sangat awal dalam kurva.
Untuk informasi lebih lanjut tentang sistem pemantauan kondisi, kunjungi Kittiwake Holroyd di www.kittiwakeholroyd.com.