Piston Plant Mengambil Pendekatan Proaktif untuk Keandalan dan OEE
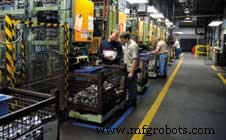
Dick Cole, wakil presiden operasi untuk Karl Schmidt Unisia, menyebut pabrik perusahaan di Marinette, Wis., "fasilitas piston paling beragam di dunia."
Dia menawarkan berbagai alasan untuk itu.
Produk dan pelanggan yang beragam: Fasilitas Karl Schmidt Unisia seluas 510.000 kaki persegi, terletak beberapa mil dari Upper Peninsula Michigan, menghasilkan beragam piston (hampir semua ukuran, dan kapasitas harian mendekati 75.000) untuk pelanggan mesin bensin dan diesel - OEM dan perusahaan aftermarket di sektor otomotif, pertanian, industri, rekreasi dan kelautan. General Motors, Nissan, DaimlerChrysler, Ford, Cummins, John Deere, International, Harley-Davidson, dan Mercury Marine adalah di antara nama-nama besar.
Kemampuan manufaktur yang beragam: Operasi pengecorannya yang mencakup semua termasuk tungku peleburan induksi, sel pengecoran otomatis dan sel pengecoran cetakan manual, ditambah perlakuan panas dan solusi anil in-house, pengeringan chip, pengerasan las dan pembuatan prototipe. Operasi pemesinan dan penyelesaian lengkapnya mencakup jalur pemesinan transfer otomatis dan sel pemesinan/penyelesaian lengkap, ditambah pelapisan timah internal, anodizing, pelapisan sablon, perakitan modul, dan pembuatan prototipe.
Warisan yang beragam: Karl Schmidt Unisia adalah perusahaan patungan yang berkantor pusat di Amerika dari Kolbenschmidt Pierburg AG Jerman dan Hitachi Automotive Systems Ltd. Jepang. "Kualitas Jepang, presisi Jerman, dan kecerdasan Amerika - kami memiliki yang terbaik dari semua dunia," kata Cole.
Tetapi sama pentingnya, fasilitas ini adalah model keragaman dalam pendekatan pemeliharaan dan keandalan. Operator dan teknisi, karyawan per jam dan gaji, veteran dan karyawan baru - yang terbaik dari semua dunia - bekerja sama sebagai tim untuk mendorong produktivitas, daya saing biaya, dan layanan pelanggan. Hal ini dibuktikan melalui:
-
1) komposisi program Total Productive Maintenance pabrik;
-
2) penempatan program Continuous Improvement di bawah arahan departemen layanan teknis (alias pemeliharaan);
-
3) fokus dan keberhasilan Sistem Manajemen Peralatan Dini; dan,
-
4) penggunaan metrik "efektivitas peralatan secara keseluruhan", atau OEE.
"Itu adalah orang-orangnya. Ini adalah pola pikirnya. Ini adalah budayanya," kata Cole. "Kami melihat pemeliharaan bukan sebagai 'kejahatan yang diperlukan', tetapi sebagai penambah kapasitas dan sebagai misi penting untuk kesuksesan kami."
Sejak tahun 2002, hampir 25 persen peningkatan OEE, 41 persen pengurangan biaya pemeliharaan dan 3 persen lebih pengurangan pekerjaan pemeliharaan reaktif bertepatan dengan lebih dari 15 persen peningkatan dolar penjualan. Dengan mempertimbangkan tahun 2001, dolar penjualan naik hampir 50 persen.
"Keandalan tidak pernah lebih penting bagi kami dan pelanggan kami," kata Scott Haulotte, manajer layanan teknis dan Peningkatan Berkelanjutan di pabrik Marinette. "Ini diterjemahkan menjadi pengulangan, kemampuan, berjalan ramping. Itu berarti kepercayaan dan pengiriman ke pelanggan."
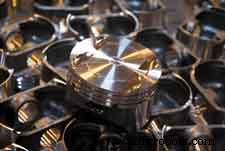
Pabrik Karl Schmidt Unisia di Marinette, Wis., memproduksi piston dalam berbagai ukuran untuk pelanggan mesin bensin dan diesel.
Bagian pengecoran pabrik melelehkan hingga tujuh jenis paduan aluminium yang berbeda. Setiap produk piston perusahaan membutuhkan paduan tertentu. Suhu aluminium bervariasi menurut produk, tetapi berada dalam kisaran 700 hingga 800 derajat Celcius.
Hanya Fakta
Perusahaan:Karl Schmidt Unisia adalah perusahaan patungan Kolbenschmidt Pierburg AG Jerman dan Hitachi Automotive Systems Ltd Jepang. Pabrik AS berlokasi di Marinette, Wis., dan Fort Wayne, Ind. Pabrik tambahan berlokasi di Jerman (dua), Jepang, Meksiko , Brasil, Prancis, Cina, India, dan Republik Ceko. Penjualan pada tahun 2005 adalah $204 juta.
Situs fokus:Karl Schmidt Unisia di Marinette. Pabrik ini terletak 50 mil timur laut Green Bay, Wis., dan dua mil barat daya Menominee, Michigan.
Ukuran situs:Kompleks manufaktur dan perkantoran meliputi 510.000 kaki persegi. Lantai pabrik dibagi antara area pengecoran dan permesinan/penyelesaian.
Pekerjaan di pabrik:1.105 karyawan, termasuk 91 di layanan teknis.
Produk:Pabrik membuat piston untuk mesin mobil penumpang; mesin truk ringan; mesin truk tugas sedang; dan aplikasi kelautan, industri, dan rekreasi.
FYI:Pabrik ini awalnya dibangun pada tahun 1944 untuk Badger Piston Co. Eric Barggren, cucu dari pendiri Badger Ed Barggren, saat ini adalah seorang insinyur di pengecoran pabrik.
TOTALLY TPM
Di sebagian besar pabrik A.S., Total Productive Maintenance dipotong dan dikeringkan. Operator menyeka mesin mereka dan memastikannya memiliki cukup oli. Di pabrik Marinette milik Karl Schmidt Unisia, prosesnya lebih terlibat dan - begitulah lagi - beragam.
Di sini, TPM dimulai dengan kegiatan CIL (Clean, Inspect and Lubricate) standar harian yang dijabarkan pada plakat laminasi. Setiap mesin memiliki daftar instruksi khusus sendiri. Setiap item baris pada daftar periksa terikat dengan nomor item (yaitu 2), jenis item (pelumasan), kriteria peralatan (Waylube oiler), tugas/kondisi yang diinginkan (isi dengan Waylube 68 hingga level yang diperlukan) dan level frekuensi (setiap shift) . Bagian atas lembaran menampilkan gambar berwarna dari bagian depan, belakang dan samping mesin. Komponen kunci yang berhubungan dengan item pada lembar CIL dicatat dengan angka dan panah. Jadi, No. 2 pada plakat ini menunjukkan bahwa kapal tangki Waylube ditemukan di sisi belakang mesin, di paling kiri, tepat di bawah pengukur tekanan Waylube.
Catatan lain tentang CIL:
-
Pembersihan adalah elemen dari proses 5-S pabrik yang ketat dan diaudit. Ini dimaksudkan tidak hanya untuk estetika, tetapi untuk membantu mesin bekerja dengan kemampuan maksimalnya. Ini juga bertujuan untuk mengungkap potensi atau masalah yang muncul (kebocoran oli, keausan sabuk, panas berlebih) sebelum menyebabkan waktu henti atau bahaya keselamatan.
-
Operator menangani semua fungsi manajemen pelumasan dan cairan (oli, gemuk, pendingin) untuk mesin atau mesin mereka, kecuali dilarang oleh peraturan keselamatan khusus (pelepasan pelindung khusus) atau aturan perawatan (perlu perkakas khusus). "Dulu kami telah menunjuk orang-orang pemeliharaan yang berjalan di sekitar mesin pelumasan," kata Haulotte. "Hari ini, kami tidak memilikinya."
-
Operator didorong untuk menggunakan pengetahuan, pengalaman, dan indra mereka (penglihatan, penciuman, suara, dan rasa) selama inspeksi untuk mengidentifikasi potensi atau masalah yang muncul. Mereka menandai komponen yang dimaksud dan menulis perintah kerja yang terperinci. "Tidak ada manajer bisnis yang duduk di belakang mejanya atau petugas pemeliharaan yang sedang memperbaiki mesin yang mengetahui masalahnya lebih baik daripada orang yang mengerjakan mesin tertentu," kata Haulotte, yang sebelum memimpin layanan teknis adalah pemimpin tim manufaktur. di fasilitas.
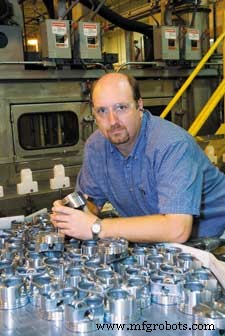
Scott Haulotte, Perbaikan Berkelanjutan dan manajer layanan teknis pabrik, mengatakan "keandalan tidak pernah lebih penting bagi kami dan pelanggan kami."
Apa yang terjadi selanjutnya juga membedakan pabrik Karl Schmidt Unisia ini dari pabrik lain di dalam atau di luar sektor otomotif.
Di sebagian besar pabrik, teknisi pemeliharaan mengambil kendali setelah identifikasi masalah, dan keterlibatan operator dalam pemeliharaan dan keandalan alat berat berakhir. Itu tidak terjadi di sini.
Di pabrik piston non-serikat 24/7 ini, peran dan tanggung jawab karyawan tidak kaku. Fluiditas itu memungkinkan operator yang termotivasi untuk terlibat secara mendalam dengan aktivitas pemeliharaan. Sebagai hasil dari minat dan kemampuan yang kuat, mereka mengangkat tangan dan mampu membuat dampak yang luar biasa.
"Jika seorang operator atau orang semi-terampil mengatakan mereka dapat menanganinya, beri mereka kesempatan," kata Mark Greenlund, pemimpin tim bisnis untuk lini produk tugas menengah. "Beberapa tahun yang lalu, kami mengambil jalur pengecoran. Salah satu mesin pengecoran memiliki silinder hidrolik yang buruk. Segera, petugas pemeliharaan kami berjalan dan berkata, 'Kami akan mengurusnya,' dan operator berkata, 'Aku bisa melakukan ini.' Kami bertanya, 'Anda tahu cara merawat silinder hidrolik ini?' Operator itu berkata, 'Anda tidak akan percaya apa yang saya lakukan di luar pekerjaan. Saya bisa menangani ini. Ini sangat mudah.' Kami membiarkan dia melakukannya. Petugas pemeliharaan berada sejauh 15 kaki jika ada masalah. Tapi itulah bakat yang dimiliki beberapa orang."
Haulotte mencatat bahwa sebelum kegiatan pemeliharaan yang dipimpin operator tersebut, anggota layanan teknis akan melakukan pemeriksaan penuh dan pemeriksaan keamanan (lockout/tagout). Orang tersebut juga dapat melakukan pemeriksaan pasca-aktivitas dan menghapus perangkat lockout/tagout.
Operator juga dapat terlibat selama penghentian untuk pekerjaan pemeliharaan preventif bulanan dan tahunan.
"Ketika kami menjadwalkan kegiatan PM tahunan - kami mencoba mengunjungi semuanya setidaknya setahun sekali - kami mengadakan pertemuan perencanaan dengan grup produksi," kata supervisor pemeliharaan pengecoran Jeff Welty. "Di sisi pemeliharaan, kami mendapatkan komitmen dari operator untuk membantu melakukan pekerjaan PM. Kami memberi mereka tugas penting yang mampu mereka lakukan. Ini adalah pelatihan berkelanjutan untuk mereka, dan ini sangat membantu kami."
Sebagai hasil dari pengalihan tugas pemeliharaan, Haulotte mengatakan operator sekarang melakukan 30 persen dari semua tugas PM. Dia mengatakan tujuannya adalah untuk mendapatkan angka itu menjadi 70 persen.
Layanan teknis membalas budi dengan membuat hidup lebih mudah bagi operator. Mereka memeriksa area produksi dan, berdasarkan umpan balik operator, pengukur gerak, kancing, pedal, fitting Zerk, dll., agar lebih mudah diakses, terlihat, dan ergonomis. Mereka menambahkan panel inspeksi, pemutus, dan pencahayaan yang memungkinkan operator melakukan pemeriksaan komponen/proses dengan lebih cepat dan mudah.
"Saya pikir kita mendapatkan informasi yang lebih baik dari lantai," kata Welty. "Itu memungkinkan kami untuk merencanakan dengan lebih baik, mendapatkan suku cadang lebih awal, mengetahui apa yang kami hadapi. Ada lebih sedikit kejutan karena operator memiliki pengetahuan yang lebih tentang peralatan. Anda dapat mengajukan pertanyaan spesifik tentang cara kerja peralatan. Anda dapat melakukan pekerjaan detektif Anda dan mendapatkan perasaan yang benar-benar baik. Mereka telah mengembangkan lebih banyak jargon teknis. Mereka tahu apa komponennya, apa fungsinya, dan mengapa itu penting."
Welty yakin keterlibatan aktif operator telah memicu efek domino.
"Ini telah memberi kami kesempatan untuk melakukan perbaikan yang tidak akan kami punya waktu untuk sebaliknya," katanya. "Ini memberi kami kesempatan untuk melakukan lebih banyak aktivitas analisis akar masalah. Ini memungkinkan kami untuk membuat solusi dan perbaikan yang mencakup baterai penuh mesin. Anda mengambil apa yang dipelajari di satu dan membawanya ke yang lain. Saya pikir hal terbesar adalah bahwa hal itu memberikan lebih banyak waktu bagi kami untuk benar-benar meningkatkan berbagai hal daripada hanya memadamkan api sepanjang waktu. Kecuali jika Anda dapat meluangkan waktu itu di suatu tempat dalam prosesnya, Anda tidak akan pernah bisa mengatasi masalah dan mencegah masalah."
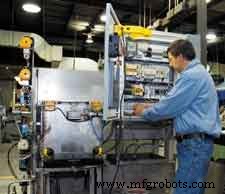
Sebuah aspek dari Sistem Manajemen Peralatan Awal Karl Schmidt Unisia berfokus pada mengambil mesin pabrik yang ada dan membangunnya kembali "lebih baik dari sebelumnya".
MEMIMPIN LEAN
Dengan operator yang melakukan lebih banyak tugas pemeliharaan rutin dan terukur, departemen layanan teknis memang telah mengalihkan fokusnya ke upaya yang lebih proaktif, strategis, dan beragam. Yang terpenting dalam mode pemecahan masalah/pencegahan baru ini adalah arah program Perbaikan Berkelanjutan pabrik. CI adalah metodologi yang identik dengan kaizen dan lean manufacturing yang diciptakan oleh Toyota.
Berapa banyak pemimpin pemeliharaan yang benar-benar dapat mengatakan bahwa mereka tidak hanya memiliki visi untuk masa depan pabrik, tetapi juga memiliki kemampuan untuk mengarahkannya menuju keadaan ideal itu? Haulotte bisa.
Cole membuat keputusan untuk menempatkan Perbaikan Berkelanjutan dalam keranjang layanan teknis berdasarkan pengalaman masa lalunya.
"Pengaturan itu efektif di fasilitas tempat saya bekerja sebelumnya," kata Cole, mantan karyawan General Motors dan Cummins. "Anda mendapatkan sinergi yang hebat dengan menggabungkan tanggung jawab tersebut."
Haulotte tidak perlu meluncurkan CI. Akarnya di pabrik kembali ke awal 1990-an, ketika diperkenalkan sebagai kaizen oleh wakil presiden perusahaan Masaaki Watarai. Haulotte dipercaya untuk mempertahankannya, mengencangkannya, dan membuatnya sesuai dengan lingkungan pabrik yang berubah dan mengandalkan keandalan saat ini.
"Kami mengubah beberapa hal, mendefinisikan beberapa hal lainnya, tetapi ini adalah struktur yang kami gunakan untuk berperang," katanya.
Konsep yang menonjol dari rencana lean berbasis layanan teknis adalah:
Alat visual: Lembar CIL berisi foto, yang dijelaskan sebelumnya, adalah salah satu contoh keyakinan kuat Haulotte pada visual. Lainnya adalah kode warna dari semua wadah pelumasan untuk menghindari kesalahan aplikasi dan kontaminasi silang; lampu andon dan alarm untuk memberikan peringatan kepada operator dan teknisi saat mesin produksi mulai menunjukkan karakteristik yang tidak diinginkan; peningkatan jumlah pengukur untuk memberikan gambaran kesehatan aset kepada operator; dan pusat komunikasi yang menampilkan kinerja pabrik melalui berbagai metrik utama dan membandingkan angka tersebut dengan tingkat yang direncanakan KSU, berbasis industri, atau yang dibutuhkan pelanggan.
Alat gesit/seluler: Ini menyerang beberapa "pemborosan mematikan" yang diidentifikasi dalam Sistem Produksi Toyota. Contoh yang telah menghemat waktu, gerak, dan uang layanan teknis adalah gerobak PM dan truk bah.
Gerobak yang dirancang khusus - pada dasarnya meja kerja layanan lengkap di atas roda - digunakan oleh teknisi untuk aktivitas PM tingkat lanjut. Mereka menampung semua alat dan perlengkapan yang diperlukan untuk pekerjaan itu, dan dapat dilengkapi untuk menahan tangga, wakil, mesin bor, atau barang lainnya.
Sebuah truk bah digunakan dalam hubungannya dengan pekerjaan PM besar. Beberapa jam sebelum PM, teknisi menggunakan perangkat vakum yang disebut pengisap bah untuk mengeluarkan semua cairan pendingin dari mesin. Pendingin disimpan ke dalam tangki besar yang dipasang di bagian belakang kendaraan bergerak bertenaga. Cairan tersebut kemudian didorong ke area lain di pabrik untuk menjalani proses daur ulang.
"Ini menghilangkan mengambil beberapa perjalanan dengan tangki yang lebih kecil, dan menghilangkan harus memindahkan tangki berat dengan tangan," kata Haulotte.
Efisiensi melalui data: Haulotte mengatakan departemen telah melakukan upaya bersama untuk meningkatkan informasi yang disimpan dalam sistem perangkat lunak manajemen pemeliharaan terkomputerisasi (CMMS), dan memanfaatkan persentase yang lebih besar dari fungsinya. Hal ini menyebabkan kegiatan rasionalisasi PM. "Dalam banyak kasus, kami belajar bahwa kami tidak perlu mengganti oli terlalu sering," kata Welty.
Peningkatan penggunaan data juga menyebabkan proyek rasionalisasi dan standardisasi di gudang terpusat, yang mengurangi inventaris dan pengeluaran untuk bahan pemeliharaan, perbaikan, dan operasi (MRO).
Berbagi informasi praktik terbaik secara formal juga telah menyebabkan penurunan substansial dalam masalah kontaminasi (kotoran, serpihan, dll.).
Kegiatan identifikasi limbah: Analisis Chokotei hanyalah salah satu alatnya. Aktivitas ini merupakan pendekatan berteknologi rendah untuk melacak penghentian mesin dalam jumlah besar dalam waktu singkat dan mengidentifikasi kerugian produksi berikutnya. Satu analisis baru-baru ini mengidentifikasi kondisi miss-loading yang sangat tinggi untuk piston pada tiga mesin. Dengan kondisi dan akar penyebab yang teridentifikasi, langkah-langkah diambil untuk memperbaikinya.
MENYUSUN BEBERAPA PERBAIKAN TERUS MENERUS:Ramping DAN SENI MEMBUAT KOPI
Pemimpin tim bisnis Unisia Karl Schmidt Mark Greenlund mengatakan mentalitas Perbaikan Berkelanjutan pabrik Marinette menular. Kopi, siapa saja?
"Saya menantang diri saya dan orang-orang saya untuk bekerja lebih cerdas, bukan lebih keras. Saya juga menerapkan pemikiran itu pada apa yang saya lakukan, baik di tempat kerja maupun di rumah," katanya. "Misalnya, saya bangun pagi. Saya bangun jam 4.30 pagi. Saya membuat kopi setiap pagi untuk saya dan istri saya. Memikirkan semua gerakan kecil yang saya lakukan untuk membuat kopi, saya menantang diri saya untuk perbaiki prosesnya.
"Tepat di sebelah teko kopi adalah microwave dengan timer di atasnya. Suatu pagi, saya menghitung berapa lama waktu yang dibutuhkan untuk membuat kopi. Butuh sedikit lebih dari 2 menit. Setiap pagi, saya memikirkan cara baru untuk meningkatkan kualitas kopi. Saya mengirim e-mail (layanan teknis dan direktur CI) Scott (Haulotte) beberapa hari yang lalu dan berkata, 'Saya harap Anda tidak berpikir saya sakit, tapi saya hanya punya waktu kurang dari 40 detik.'
“Mentalitas peningkatan itu tertanam dalam diri saya. Ke mana pun Anda melihat, ada pemborosan. Misalnya, ada satu sendok di dalam wadah kopi. Dibutuhkan dua sendok untuk teko kopi. Keluarkan sendok kecil dan masukkan ke dalam satu sendok yang dua kali lipat. besar.
"Di tempat kerja dan di rumah, semuanya memiliki peluang dan tantangan. Sesederhana membuat kopi."
UNIQUELY PROACTIVE
Pola pikir proaktif, strategis, ramping berlanjut dengan Sistem Manajemen Peralatan Awal, atau EEMS. Ini adalah salah satu cara paling ampuh yang digunakan Karl Schmidt Unisia untuk mencapai keandalan melalui keragaman.
EEMS memiliki dua elemen, masing-masing didukung oleh tim lintas fungsi.
Salah satu elemennya adalah spesifikasi untuk desain peralatan baru. Saat mesin baru dibutuhkan, tim perwakilan pembelian, teknik, kualitas, dan layanan teknis bekerja sama untuk mengidentifikasi semua fungsi, komponen, program, dan opsi yang diperlukan. Kebutuhan dibangun ke dalam kriteria penerimaan mesin.
"Kami menginginkan komponen tertentu pada mesin itu, karena sejumlah alasan. Misalnya, kami menginginkan kontrol Allen-Bradley dan katup Vickers," kata Haulotte. "Spesifikasi kami didasarkan pada pengalaman, layanan dan dukungan, akses ke suku cadang, dan/atau standarisasi suku cadang yang sudah kami miliki di rak gudang."
Persyaratan untuk vendor juga mencakup tiga salinan manual mesin dan daftar suku cadang yang disarankan. Sub-tim teknisi pabrik, layanan teknis, dan personel toko MRO meninjau daftar suku cadang. Berdasarkan riwayat, tingkat kegagalan, dll., grup dapat melakukan modifikasi.
"Ada daftar periksa ekstensif hal-hal yang kami lalui untuk memastikan bahwa ketika mesin itu masuk, itu akan:1) mencapai tingkat kualitas yang kami butuhkan untuk program; 2) mencapai kapasitas dengan menjadi andal; 3) memiliki komponen yang kami dapat dengan mudah mengakses atau mengganti dengan stok yang ada; dan 4) berasal dari perusahaan yang dapat diakses dengan respons dan catatan layanan yang baik," kata Haulotte.
Elemen lain dari EEMS berfokus pada mengambil mesin pabrik yang ada dan membangunnya kembali "lebih baik dari sebelumnya." Cacat desain asli yang terkait dengan perawatan, pengoperasian, dan keamanan dihilangkan dan diganti dengan teknologi dan solusi baru. Proyek pembangunan kembali memperhitungkan masukan dari operator, insinyur, pembeli, dan teknisi. Namun, seorang teknisi tunggal bertindak sebagai pemimpin proyek.
"Kami tidak selalu bisa membeli peralatan baru," kata Haulotte. "Jika tidak ada kemajuan teknologi yang bisa kita peroleh dari membeli yang baru, kita harus melihat perbaikan sendiri."
Ukuran dan cakupan proyek ini bervariasi.
"Beberapa alat berat sangat besar, hampir tidak bisa masuk melalui pintu area pembangunan kembali," kata teknisi Jerry Dean, seorang veteran 30 tahun yang telah menjabat sebagai pemimpin untuk beberapa proyek. “Kami mengganti semua yang perlu diganti dengan komponen yang mutakhir. Secara mekanis, kami memeriksa dan menyempurnakannya. Kami menambahkan pelindung dan membuatnya lebih aman. Kami memotong bahan kami sendiri. Kami mengebor lubang kami sendiri. Kami melakukan apa saja diperlukan untuk menghadirkan produk baru yang ramah perawatan dan pengoperasian."
Lebih dari 25 proyek pembangunan kembali diselesaikan pada tahun tertentu. Ini telah menghemat banyak uang bagi perusahaan vs. membeli yang baru dan mengungkap kapasitas tersembunyi.
"Semakin Anda membawa teknologi Anda sendiri ke dalam organisasi, semakin Anda membangun kembali peralatan Anda sendiri, semakin Anda meningkatkan peralatan Anda sendiri, semakin baik Anda nantinya," kata Cole.
BAHASA OEE
Pada hari tertentu, pabrik Marinette dapat menerima pengunjung dari kantor perusahaan di Jerman dan Jepang; dari pabrik saudara KSU di Meksiko, Brasil, Prancis, Cina, India, dan Republik Ceko; dan dari situs pelanggan di AS dan di seluruh dunia.
Dalam diskusi dengan para tamu ini, atau dalam pembicaraan antara berbagai organisasi fungsional pabrik, pemahaman tentang kesehatan dan kemampuan fasilitas ini sangat jelas. Semua orang berbicara dalam bahasa yang sama - bahasa OEE.
"Semua orang memahami metrik OEE dengan sangat baik di sini," kata Greenlund. "Ini menggerakkan pabrik kami."
Haulotte menambahkan, "Setiap manajer produksi, setiap supervisor, setiap insinyur melihat nomor itu karena itu memberi tahu kita di mana kita berada."
OEE adalah metrik matematis yang melacak sumber kerugian operasi. Ini dihasilkan dengan mengalikan ketersediaan peralatan (dinyatakan sebagai persentase dari kemampuan optimal dunia nyata peralatan) dengan kinerja [alias hasil] (persentase optimal) dengan kualitas (persentase optimal). Angka OEE dihitung untuk mesin individu, sel kerja, proses terkait, unit bisnis dan sebagai komposit pabrik, dan dapat dianalisis pada tingkat makro atau mikro.
"Setelah dipecah dan dapat melihat ketiga parameter yang masuk ke dalamnya, Anda dapat benar-benar fokus pada apa yang mendorong beberapa masalah dan di mana Anda mungkin memiliki beberapa peluang," kata Greenlund. "Kalau kinerja bulan ini mati, kenapa begitu? Kalau kinerjanya bagus tapi mesinnya tidak ada, kenapa tidak tersedia?"
Haulotte berkata, "Anda mulai mencari sumber kerugian atau pemborosan. Saya dapat mengatasi semuanya sekarang sebelum ada waktu henti."
Dia menambahkan bahwa di situs ini, produksi memiliki metrik OEE. "Produksi mengumpulkan dan memasukkan data OEE," katanya. "Kami digunakan sebagai sumber daya."
Ketika pabrik pertama kali mulai melacak metrik pada tahun 2002, OEE keseluruhannya adalah 51,4 persen. Angka tersebut meningkat menjadi 55 persen pada tahun 2003, 68 persen pada tahun 2004 dan 72,2 persen pada tahun 2005. Angka akhir tahun 2006 diproyeksikan menjadi 75 persen. Target untuk tahun 2007 adalah antara 77 dan 78 persen.
"Setiap persen peningkatan OEE bernilai satu setengah minggu tambahan kapasitas bagi kami," kata Haulotte. "Itulah dampaknya dan itulah yang membuat kami terus kehilangan setiap poin persentase."
Namun, setiap tahun, semakin sulit untuk mendapatkan keuntungan itu. Sebagian besar buah yang menggantung rendah telah hilang, dan Haulotte mencatat bahwa pakar industri menyematkan 85 persen OEE sebagai tolok ukur kinerja pabrik "kelas dunia".
"Sepertinya 10 persen seharusnya relatif mudah didapat, tapi sangat sulit," katanya. "Mengetahui seberapa keras kami telah bekerja dan bahwa kami masih 10 persen dari kelas dunia adalah tantangan besar. Jadi, kami akan mendorong pada tahun 2007. Kami memiliki pengukuran OEE untuk setiap baris, sel, mesin. Kami akan menargetkan area teratas kami. Kami akan menggabungkannya dengan persyaratan bisnis. Program piston apa yang akan berkembang? Mana yang akan dihapus secara bertahap? Kami akan menyerang dua atau tiga aset teratas tersebut untuk menghasilkan peningkatan."
HASIL YANG BAGUS, TAPI. . .
Peningkatan kapasitas, ketersediaan, kinerja dan kualitas penting untuk masa kini dan masa depan pabrik Karl Schmidt Unisia ini. Selama setahun terakhir, penjualan melonjak, terutama untuk produk dieselnya. Pelanggan menarik berat, membuat rantai pasokan rendah lemak bahkan lebih kencang. Pelanggan yang membayar - dan menuntut - ini memiliki kebutuhan yang peka terhadap waktu, dan tidak dapat dibebani dengan "kejutan" keandalan dari pemasok Tingkat 1.
"Dengan sistem pengiriman dari tangan ke mulut seperti itu, Anda sebaiknya memiliki saluran yang dapat diandalkan," kata Greenlund. "Peningkatan keandalan berarti peningkatan ketenangan pikiran bagi pelanggan. Ini berarti lebih sedikit telepon dari saya yang memberi tahu mereka bahwa pasokan piston akan menipis."
Pemimpin pabrik seperti Haulotte sangat senang dengan kemajuan yang telah dicapai.
"Kami, saya yakin, adalah kisah sukses," kata Haulotte. "Kami menunjukkan bahwa Anda dapat berhasil, bahkan di negara dengan biaya tenaga kerja tinggi, jika Anda bekerja keras, berpikir cerdas, dan bersatu."
Namun, pabrik dan perusahaan tidak mau dibuai dengan kepuasan.
"Bilahnya memang lebih tinggi," kata Cole. "Ada ekspektasi yang tinggi dan tekanan yang tak henti-hentinya. Ekspektasi hari ini seputar biaya sangat besar. Untuk kutipan, industri kami dibulatkan dalam sen. Industri lain, seperti kedirgantaraan dan perawatan kesehatan, dibulatkan dalam dolar. Ini ketat."
Jadi, mereka melanjutkan dengan memanfaatkan akar bisnis yang beragam.
"Filosofi Jepang memang salah satu perbaikan terus-menerus, selalu melihat ke depan," kata Haulotte. “Ketika saya menjadi supervisor garis depan di area Nissan, kami memiliki tingkat memo 0,05 persen, yang terbaik di perusahaan. Kami memiliki 26 lembar memo sepanjang tahun. Saya pikir itu mendekati kesempurnaan Anda akan mendapatkan. Ketika tiba saatnya untuk merencanakan tahun depan, Pak Watarai memberi saya tujuan memo baru:.03. Sejujurnya, saya terkejut, tetapi mentalitasnya adalah untuk selalu meningkat.
"Bagian lain datang dari pemilik Jerman kami. Pepatah mereka adalah, 'Anda melakukan pekerjaan dengan baik, tapi ...'. Penghargaan diberikan, namun 'tetapi' adalah cara untuk mengungkapkan bahwa 'kita selalu bisa melakukan yang lebih baik; don 'jangan puas dengan posisi Anda sekarang; mari kita lakukan apa yang kita lakukan hari ini dan dorong ke tingkat berikutnya.'"
Dengan operator dan teknisi, karyawan per jam dan gaji, veteran dan karyawan baru - yang terbaik dari semua dunia - memberikan dorongan itu, Karl Schmidt Unisia dapat mengatakan, dengan tingkat keandalan tertentu, bahwa kemajuan sudah dekat.