Worthington Industries:Pengejaran dan kekuatan nol
Jody Willeman mulai merasakan tekanan yang luar biasa pada kaki kirinya. Kemudian terdengar suara tulang kakinya patah, satu per satu.
"Kaki itu terpeleset dan retak setidaknya lima kali," katanya. "Saya tahu sesuatu yang buruk terjadi."
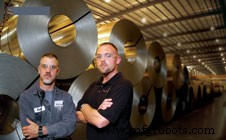
Koordinator keselamatan Ryan Lamb (kanan) dan pekerja lini Jason Willeman. Jason adalah saudara kembar Jody Willeman, yang terluka dalam kecelakaan pabrik pada tahun 2004.
Pada hari musim gugur tahun 2004 ini, Willeman, operator saluran galvanis di pabrik pengolahan baja Worthington Industries di Delta, Ohio, berusaha melakukan perawatan cepat pada saluran udara bertekanan tinggi dan menghindari penghentian saluran yang mahal. Dia telah melakukan tugas ganti-dan-perbaiki "lima sampai 10 kali sebelumnya" sendiri. Namun pada kesempatan ini, kesalahan prosedur yang dikombinasikan dengan pelebaran nosel memaksa kakinya di antara sepotong tabung baja persegi dan kerangka mesin. Kaki sedang dikompresi dalam wakil darurat ini.
"Saya bisa dengan mudah kehilangan kaki saya jika teknisi pemeliharaan terdekat tidak membuang sakelar dan melepaskan peralatan itu dari kaki saya," katanya. "Kalau tidak, tidak ada yang bisa menghentikannya."
Willeman menghabiskan dua bulan berikutnya untuk menstabilkan tulang metatarsalnya yang patah.
"Saya membayar harganya," katanya. "Saya tidak akan pernah melupakan betapa tidak berdayanya saya."
Pabrik Worthington di Delta adalah salah satu yang paling aman di sektor logam Amerika Serikat, dan di industri Amerika secara keseluruhan. Ini menyelesaikan tahun fiskal perusahaan baru-baru ini pada tanggal 31 Mei 2007 dengan nol cedera atau penyakit yang dapat dicatat oleh OSHA dan nol kasus DART (cedera atau penyakit yang memerlukan beberapa hari lagi, pembatasan dan/atau pemindahan) - rentang 306.559,25 jam kerja. Pabrik ini telah mempertahankan catatan keamanan yang bersih sejak 7 Mei 2006. Sebagai perbandingan, data terbaru dari Departemen Tenaga Kerja AS menunjukkan pesaing pabrik dalam manufaktur bentuk baja canai (mereka yang memiliki kode Sistem Klasifikasi Industri Amerika Utara 331221) memiliki tingkat cedera/sakit OSHA yang tercatat sebesar 10,2 kasus untuk setiap 100 karyawan penuh waktu yang setara dan tingkat kehilangan waktu kerja sebesar 4,5 kasus per 100.
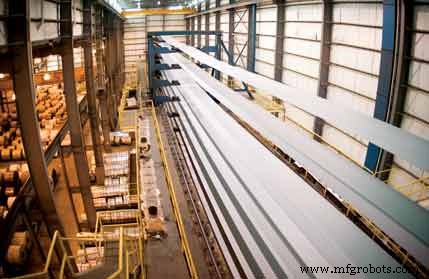
Situs Delta memproses lebih dari 1,55 juta ton baja per tahun.
Foto oleh Kim Koluch/Considering Lilies Photography
Tetapi para pemimpin pabrik ingin agar 185 orang tenaga kerja tidak pernah melupakan insiden masa lalu - cedera kaki pada Willeman, dan cedera tangan beberapa tahun yang lalu oleh teknisi pemeliharaan Terry Hardin dan operator Hugo Barajas. Ketiganya termasuk di antara para pekerja yang secara sukarela ditampilkan dalam rekaman video testimoni yang diputar secara rutin di pertemuan pabrik.
"Jika Anda pernah mengambil hari libur atau satu menit dari memikirkan praktik yang aman, saat itulah cedera berikutnya akan terjadi," kata pengawas Cleve Deskins. "Kamu tidak bisa istirahat. Tidak di sini."
Bahaya selalu ada di pabrik bervolume tinggi dan bergerak cepat ini. Gulungan gulungan baja dan gulungan pita penahan logam yang tak berujung bisa sangat tajam. Gunting dan pisau putar yang menggorok dan mengiris bahan menimbulkan risiko laserasi dan tebasan yang sama atau lebih besar. Mesin besar dan kompleks - dengan roda gigi dan konveyor berputar - mendorong, menarik, dan menyeret baja melalui berbagai tahap pemrosesan. Panci dan lubang sedalam 10 kaki menampung seng cair yang melebihi 870 derajat Fahrenheit. Bahan kimia, gas dan asam sangat penting untuk resep produksi. Derek overhead terus mengangkut muatan multi-ton. Dan, motor forklift dengan beban penuh di gang naik dan turun.
"Kami tidak bekerja di pabrik donat," kata manajer operasi Jeff Leeper. "Ini adalah industri berat."
Semua ini membuat catatan keselamatan Worthington begitu luar biasa, dan keengganan untuk lengah sangat diperlukan.
Masa lalu membentuk masa kini.
"Bertahun-tahun yang lalu, proses berpikir dulu adalah ketika Anda mengerjakan sebuah peralatan, terutama slitter, Anda akan dipotong. Itu adalah bagian dari pekerjaan," kata Deskins. "Kami tidak berpikir seperti itu lagi."
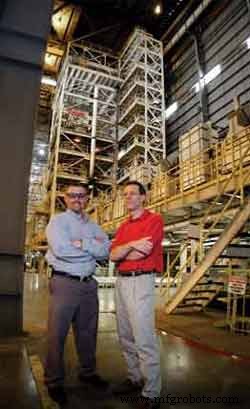
David Leff (kiri) adalah manajer korporat kesehatan dan keselamatan lingkungan di Worthington. Jeff Leeper adalah manajer operasi situs Delta.
Leeper mengenang perayaan pabrik, lengkap dengan steak panggang, ketika departemen slitter membuat rekor produksi di akhir 1990-an.
"Empat orang dipotong di sana selama sebulan dan kami membalik steak," katanya. "Melihat ke belakang, itu tidak masuk akal. Ini seperti, untuk apa kita merayakannya?"
Namun, seperti video cedera, peristiwa semacam itu merupakan bagian penting dari sejarah 10 tahun situs dan menjadi pendorong pekerjaan dan alat yang telah mengubah Delta menjadi model untuk keselamatan pabrik di Worthington Industries.
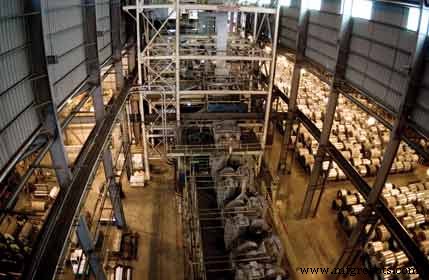
Matt Frey memeriksa lubang seng cair 870 derajat.
Hanya Fakta
Tanaman: Pabrik pengolahan baja Worthington Industries di Delta, Ohio. Delta terletak 25 mil barat daya Toledo.
Ukuran tanaman: 426.000 kaki persegi.
Pekerjaan pabrik: 185 karyawan non-serikat, termasuk 14 pekerja pemeliharaan dan satu manajer pemeliharaan.
Produk: Pabrik ini berfungsi sebagai jembatan antara kemampuan produsen baja utama dan kebutuhan khusus pengguna akhir. Prosesnya meliputi pengawetan, galvanisasi panas, pemotongan, dan pemerataan tegangan.
Produksi: Situs ini memproses lebih dari 1,55 juta ton baja per tahun. Produksi di jalur galvanizing dan pickling berjalan 24 jam per hari, tujuh hari per minggu. Produksi di jalur slitting berjalan 24 jam per hari, lima hingga enam hari per minggu.
Untuk diketahui: Pabrik tersebut dibangun di atas lahan bekas ladang jagung. Dibuka pada tahun 1997 dengan 20 karyawan. ... Situs ini terletak di seberang jalan dari pemasok terbesarnya, North Star BlueScope, sebuah pabrik mini yang memproduksi baja. ... Pabrik menyerahkan seluruh persediaan bajanya dalam tiga minggu.
ATURAN EMAS DAN SELANJUTNYA
Keamanan pabrik di Worthington berasal dari Aturan Emas perusahaan, sebuah filosofi yang dibuat oleh pendiri perusahaan John H. McConnell pada tahun 1956. Ini menyatakan bahwa "kami memperlakukan pelanggan, karyawan, investor, dan pemasok kami seperti yang kami inginkan untuk dirawat." Terkait dengan itu adalah keyakinan bahwa "manusia adalah aset terpenting kita".
Dorongan untuk mencapai kesempurnaan keselamatan (nol cedera akibat kerja, penyakit, dan nyaris celaka) setiap hari muncul 45 tahun kemudian, pada tahun 2001.
"Kami menyadari bahwa selain ingin menjadi warga korporat yang baik, kami harus memastikan bahwa kami memiliki lingkungan kerja yang baik dan aman," kata George P. Stoe, wakil presiden eksekutif dan chief operating officer perusahaan.
Produksi dan keuntungan sangat penting, tetapi mereka tidak datang sebelum keselamatan.
"Kami meminta orang-orang untuk memastikan bahwa mereka tidak mengambil jalan pintas, mencoba melakukan hal-hal yang menurut mereka akan membantu perusahaan tetapi dengan cara yang tidak aman," kata Stoe. "Kami menemukan bahwa ketika ada insiden, sering kali mereka terkait langsung dengan seseorang yang mencoba melakukan pekerjaan 'lebih baik dan lebih efisien'."
Ini bisnis yang berisiko.
"Kami memiliki karyawan yang bersedia menerima risiko jika itu berarti menyelesaikan pekerjaan lebih cepat," kata Deskins.
"Ada kecenderungan bagi karyawan untuk melakukan 'tindakan heroik' untuk mencegah penutupan," kata Leeper.
"Ada kecenderungan untuk melewatkan bagian penilaian risiko dan hanya menyelesaikannya," tambah koordinator keselamatan Ryan Lamb.
Pada tahun 2000, Stoe mengatakan bahwa perusahaan memiliki 1.000 klaim kompensasi pekerja yang menelan biaya hampir $6 juta.
David Leff, manajer korporat kesehatan dan keselamatan lingkungan Worthington, menyatakan bahwa pada tahun 2001, sebelum "revitalisasi" program keselamatan, biaya perusahaan pekerja rata-rata hampir $900 per karyawan.
Sesuatu harus dilakukan.
"Kita bisa aman hanya dengan tinggal di rumah dan tidak pernah datang bekerja," kata Leeper. "Tetapi kami di sini sebagai bisnis manufaktur yang berfungsi untuk menghasilkan uang bagi pemegang saham kami. Kami harus menghasilkan produk sehingga kami dapat dibayar untuk itu dan menghasilkan uang. Tetapi, kami ingin melakukannya dengan cara yang aman; kami tidak' tidak ingin ada yang terluka dalam prosesnya. Entah bagaimana, kita harus mencapai kedua hal itu. Keduanya sangat saling terkait. Keselamatan, produksi, kualitas, dan biaya, semuanya mendorong bisnis kita."
Hubungan simbiosis antara keselamatan dan produksi diformalkan dengan penciptaan pada tahun 2001 dari inisiatif yang dikelola secara terpusat dan dikelola secara lokal yang sekarang dikenal di Safe Works.
"Proyek produksi, proyek keselamatan - semuanya terikat bersama," kata pengawas pemrosesan Zac Guisinger.
Komponen terpusat memungkinkan standarisasi dan mengejar praktik terbaik di seluruh perusahaan. Komponen yang dilokalkan memungkinkan pabrik kebebasan untuk mengatasi masalah dan kebutuhan mereka yang paling mendesak.
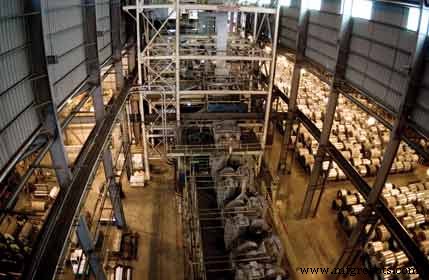
Fasilitas yang dibuka pada tahun 1997 ini memiliki luas 426.000 kaki persegi.
Inisiatif ini telah berkembang dan berkembang sejak awal, menghasilkan peningkatan besar di Delta dan situs Worthington lainnya.
-
Di seluruh perusahaan, ini termasuk:
-
pengurangan 55 persen dalam rekaman OSHA sejak 2002;
-
pengurangan 73 persen dalam biaya kompensasi pekerja per kasus sejak 2001 (dari $900 per karyawan ke angka saat ini $330 per karyawan; itu penghematan besar jika Anda mempertimbangkan Worthington mempekerjakan 8.000 orang);
-
21 persen dari 63 lokasi manufaktur Worthington mencatat nol kasus yang dapat direkam OSHA dan nol kasus waktu kerja yang hilang pada tahun fiskal 2007, dan 16 persen lainnya mencatat tanpa rekaman tetapi memiliki nol kasus DART.
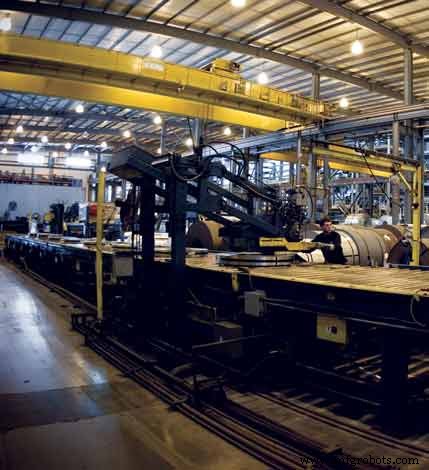
Pabrik Worthington di Delta, Ohio, memiliki 185 karyawan.
Delta telah turun dari tingkat rekor OSHA sebesar 4,99 per 100 karyawan penuh waktu pada tahun 2001 menjadi 3,35 pada tahun 2004 menjadi 0,00 pada tahun fiskal 2007. Tingkat kasus DART-nya meningkat dari 2,24 pada tahun 2004 menjadi 0,00 pada tahun fiskal 2007.
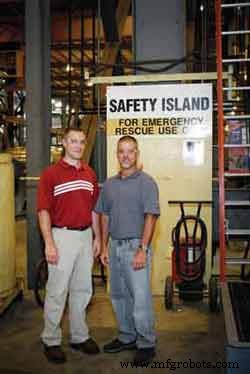
Ketua tim lini galvanis Jody Willeman (kanan), berpose dengan pengawas pemrosesan Zac Guisinger, mengatakan bahwa situs tersebut bertujuan untuk belajar dari setiap situasi keselamatan.
INISIATIF SEMUA ORANG
Sukses datang dari Safe Works yang serba bisa. Meskipun program ini bersifat sukarela, setiap karyawan bertanggung jawab dan diminta untuk terlibat.
Bagi para pemimpin pabrik dan departemen, itu berarti "menjalankan pembicaraan" - memainkan peran aktif, menunjukkan dukungan yang terlihat, menyediakan komunikasi harian dan menantang orang untuk melakukan yang terbaik. Untuk pekerja per jam, itu berarti meningkatkan, berpartisipasi, dan menggunakan alat dan proses yang membuat perubahan positif terjadi di lantai pabrik.
"Kebanyakan orang percaya bahwa keselamatan adalah inisiatif dari atas ke bawah, tetapi kami tidak merasa seperti itu," kata Stoe. "Semua orang mendapat manfaat dari proses peningkatan keselamatan dan semua orang harus memiliki suara tentang cara kerjanya."
Saat Anda melibatkan teknisi pemeliharaan, operator, dan pihak lain dan dalam peran kepemimpinan tersebut, Deskins mengatakan, hasilnya adalah tipe pekerja yang berbeda.
"Orang-orang kami tidak hanya meninju, meninju, dan pulang," katanya. "Kami memiliki orang-orang yang bersemangat, termotivasi, dan merasa tertantang. Mereka tahu bahwa mereka memiliki peluang untuk melakukan hal yang berbeda."
Itu mungkin menjelaskan mengapa pabrik memiliki 1 persen ketidakhadiran dan 2 persen pergantian.
"Orang-orang kami ingin terlibat," kata Deskins. "Mereka ingin menjadi bagian darinya."
Safe Works adalah tentang menjaga keselamatan Anda, dan keselamatan orang-orang di sekitar Anda. "Kamu adalah penjaga saudaramu," kata Lamb.
"Jika menyangkut keselamatan vs. mendapatkan kembali peralatan, tidak ada keseimbangan," kata teknisi pemeliharaan Tim Bandy. "Jika Anda tidak dapat melakukannya dengan aman, Anda tidak melakukannya. Sesederhana itu."
Dan, itu didasarkan pada pesan positif dan penguatan positif.
"Tidak apa-apa untuk membuat kesalahan," kata Willeman, yang hari ini adalah pemimpin tim di garis menggembleng. "Kamu membuat kesalahan. Kami harus menjadi lebih baik. Apa yang bisa kami pelajari darinya? Kami tidak keluar untuk menghukum. Kami ingin terus meningkatkan dan menghilangkan peluang kesalahan yang berulang."
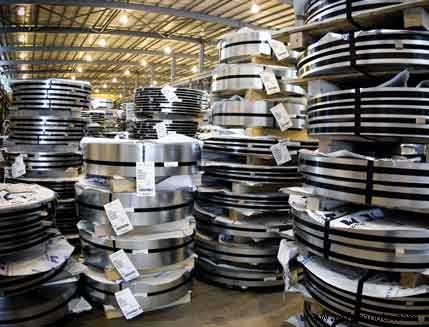
Gulungan baja dan pita penahan logam bisa setajam silet.
ALAT YANG DAPAT ANDA GUNAKAN
Safe Works mencakup berbagai komponen, alat, dan proyek. Berikut ini adalah penjelasan dari beberapa elemen terpenting di pabrik Delta, dan untuk Worthington secara keseluruhan.
BRITE: Singkatan dari Business and Risk Improvement Techniques for Everyone, ini adalah program penguatan berbasis perilaku perusahaan. Ini menggunakan kekuatan penguatan positif untuk memodifikasi tindakan pekerja yang ada sehingga karyawan membuat keputusan yang aman saat melakukan aktivitas yang berhubungan dengan pekerjaan.
Karyawan secara sukarela mengamati rekan kerja mereka untuk perilaku aman yang dipilih oleh tim kerja (dikenal sebagai Pinpoints) dan secara anonim menyerahkan kartu kepada manajer yang menandai tindakan yang benar dan salah. Data dipetakan pada papan metrik di area kerja. Ketika pekerja tim dengan benar mengikuti prosedur untuk Pinpoint yang diberikan selama 30 hari berturut-turut, diasumsikan bahwa perilaku tersebut sudah mendarah daging dan telah menjadi kebiasaan kerja yang aman. Pinpoint kemudian dipensiunkan dan anggota tim mendapatkan hadiah ucapan selamat (kartu hadiah pompa bensin, sertifikat hadiah makanan cepat saji, dll.).
Pekerja yang ditempatkan di ruang kontrol jalur galvanis baru-baru ini membahas tiga Poin Penting berikut:
-
Selalu kenakan alat pelindung diri yang tepat pada dudukan pelapis.
-
Selalu gunakan pegangan tangan saat menaiki atau menuruni tangga.
-
Buang semua bahaya terpeleset.
"Mereka memilih Pinpoints mereka sendiri," kata Lamb. "Mereka melihat area mereka dan memutuskan apa yang penting untuk dikerjakan."
Dewan keamanan: Manajer dan perwakilan dari setiap departemen pabrik secara sukarela melayani selama dua tahun di dewan keselamatan, yang juga dikenal sebagai Tim Produksi Aman. Anggota bertindak sebagai duta keamanan untuk rekan-rekan mereka. Grup merumuskan dan menyebarluaskan kebijakan, prosedur dan praktik yang mempromosikan lingkungan kerja yang aman. Ini juga merupakan sarana untuk komunikasi dua arah dan memungkinkan karyawan untuk terlibat dalam proses tersebut.
"Ketika kami mengemukakan proyek selama pertemuan, itu tetap ada dalam daftar sampai proyek selesai," kata Willeman. "Tidak hanya muncul di satu pertemuan lalu dilupakan. Ada pertanggungjawabannya. Jika ditetapkan sebagai proyek, apa yang harus kita lakukan untuk menyelesaikannya?"
Identifikasi masalah dan akar penyebab pemecahan masalah: Tim dikumpulkan secara teratur untuk secara formal memeriksa setiap operasi dan proses. Masalah atau potensi masalah yang terkait dengan keselamatan, ergonomi dan efisiensi dicatat. Anggota tim menggunakan analisis akar penyebab, mode kegagalan dan analisis efek, diagram tulang ikan, analisis lima alasan, diagram Pareto, dll., untuk sampai ke inti masalah.
"Untuk masalah keamanan atau ergonomis, kami mencoba menghilangkan bahaya dengan merekayasanya," kata Rick Mitchell, manajer keselamatan di Worthington's Steel Group. "Kami turun ke akar penyebab yang menyebabkan potensi cedera atau situasi. Kami tidak bisa dan tidak akan masalah Band-Aid."
Di salah satu area produksi di pabrik Delta, sebuah proses meminta operator untuk menempatkan selip kayu di atas meja putar. Sebanyak 150 sarad harus ditempatkan dalam satu shift. Masalahnya adalah lebarnya mencapai 54 inci dan berat masing-masing seberat 90 pon.
"Kami memiliki seorang pria di sini yang beratnya 120 pon yang melemparnya," kata Lamb. "Pekerjaan itu baik-baik saja ketika Anda berusia 20 tahun, tetapi beban itu bertambah seiring waktu."
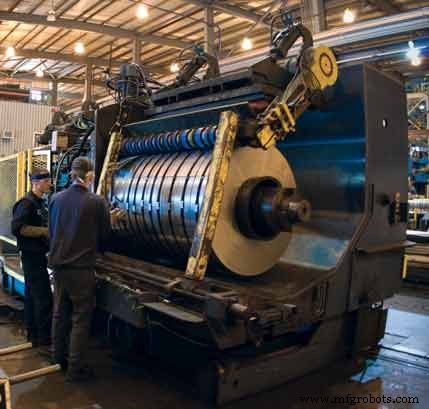
Anggota tim secara teratur memeriksa setiap operasi dan proses untuk masalah keselamatan.
Masalah terkait adalah bahwa proses ini tidak dapat memenuhi permintaan proses hulu dan hilir.
Untuk mengatasi masalah tersebut, teknisi membeli robot bekas pakai dari perusahaan sejenis. Pekerja pemeliharaan melakukan semua pemrograman otomatisasi, pemasangan dan penjagaan. Dengan biaya kurang dari $10.000, operasi dibuat lebih aman, lebih cepat, dan lebih efisien.
"Kami mengevaluasi apa yang dapat kami lakukan untuk membantu di area produksi tertentu," kata manajer pemeliharaan Bob Hardin. "Operasi memberikan masukan mereka dan kami mengembangkan solusi bersama. Perencana pemeliharaan juga terlibat. Rencana permainan dibuat. Perintah kerja kemudian dikeluarkan untuk memperbaikinya."
Sementara tim adalah metode yang paling terlihat, individu juga telah mengangkat tangan mereka untuk menyelesaikan masalah. Misalnya, pekerja garis galvanis Jason Willeman (saudara kembar Jody) memperhatikan bahwa prosedur ruang terbatas di area tersebut tidak sesuai dengan bagaimana pekerjaan itu benar-benar dilakukan. Dia melakukan percobaan tiruan dan melanjutkan untuk menulis ulang prosedur. Setelah karyanya menjalani tinjauan dan persetujuan penuh, ia ditawari tugas untuk menulis ulang prosedur ruang terbatas untuk semua lokasi pabrik yang memerlukan klasifikasi ulang. Dia menerima tantangannya.
"Saya tahu tidak mudah baginya untuk menyatukan semua itu. Ada banyak, banyak revisi," kata Leeper. "Dia melakukannya lebih baik daripada yang bisa kita lakukan karena dia sangat terlibat dalam prosesnya."
Hari ini, Jason Willeman juga memberikan pelatihan kepada pekerja tentang prosedur dan keselamatan ruang terbatas.
"Ketika saya bekerja di lantai pabrik, saya tidak pernah harus memasuki ruang terbatas," kata Lamb. "Jadi ketika saya melakukan pelatihan di ruang terbatas, pada dasarnya itu memberi tahu mereka sesuatu yang seseorang katakan kepada saya. Jason benar-benar melakukan ini. Kami menyuruhnya berlatih. Kami mendorong orang-orang di lantai untuk melatih orang-orang di lantai."
Penilaian APD: Pemeriksaan dan penilaian dilakukan secara teratur untuk mengukur kinerja dan kelayakan alat pelindung diri.
Dalam satu contoh, pemimpin produksi dan keselamatan memperhatikan bahwa pekerja yang mengenakan pelindung lengan gaya tertentu mengalami cedera (terutama luka dan goresan) di sekitar area ibu jari pemakainya. Pabrik mengirim 30 pekerja ke pameran dagang Ohio Safety Congress, di mana, di antara produk lainnya, mereka mengidentifikasi gaya pelindung lengan anti-potong yang memberikan perlindungan jempol yang lebih besar.
"Produknya bagus, tapi bisa lebih baik lagi," kata Leeper. "Jadi, berdasarkan masukan kami, pemasok mengubah desain dan fungsi pelindung. Mereka merekayasa ulang dan mengubah produk untuk memenuhi keinginan dan kebutuhan kami."
Pemasok juga datang membantu pabrik dengan memberikan sampel sarung tangan, kacamata pengaman, dan bahan habis pakai lainnya untuk diuji dan dibandingkan.
"Para pekerja memiliki suara tentang APD apa yang mereka sukai," kata Mitchell. "Dalam hal kenyamanan dan daya tahan, tidak ada yang tahu lebih baik daripada mereka."
Proyek tim: Tim lintas fungsi yang terdiri dari tujuh individu disatukan untuk mewujudkan perubahan.
"Awalnya, kelompok orang ini tidak begitu mengenal satu sama lain," kata Willeman. "Tujuannya adalah untuk membangun hubungan, tetapi apa yang kami lihat adalah jumlah pekerjaan yang berarti dan luar biasa yang harus diselesaikan."
Tim bertemu di ruang kelas selama dua hari dan mengidentifikasi proyek pabrik untuk dikerjakan. Proyek dapat berhubungan dengan apa saja. Tim memilih target dan rencana. Banyak proyek berakhir dengan keselamatan. Basis tiang dicat baru-baru ini agar lebih terlihat oleh pengemudi forklift. Signage didirikan untuk memperingatkan bahaya keamanan di satu area. Stasiun pencuci mata di sepanjang jalur pengawetan dicat oranye agar lebih terlihat oleh calon pengguna. Stasiun simulasi dibuat untuk mengajari karyawan baru cara mengikat gulungan baja dengan aman.
"Kami melibatkan seorang manajer dengan proyek karena alasan anggaran," kata Deskins. "Tim mencoba menemukan nilai untuk uangnya. Kami menginginkan sesuatu yang akan terlihat bagus dan bertahan lama dengan harga yang bagus. Kami memiliki beberapa orang terampil di sekitar sini yang melakukan pekerjaan beton, pekerjaan kayu, melukis. Keterampilan mereka terbukti sangat berharga."
Tim Respon Pertama: Ke-28 anggota Tim Tanggap Pertama pabrik bertemu sebulan sekali untuk menerima pelatihan dan meninjau prosedur tentang topik-topik seperti pertolongan pertama, resusitasi kardiopulmoner, dan defibrilator eksternal otomatis (AED). Mereka siap siaga jika terjadi keadaan darurat. Pemimpin tim adalah Dean Witt, seorang operator di jalur galvanizing.
"Dean menjalankan pertunjukan," kata Lamb. "Dia mengambil dua bulan pelatihan di waktu senggangnya untuk mendapatkan sertifikasi Palang Merah Amerika sebagai instruktur. Itu mengambil inisiatif di pihaknya. Dia melakukan semua pelatihan untuk kita sekarang."
Witt juga membentuk tim untuk meninjau dan mengubah kantong trauma pabrik. Masing-masing tas besar ini, ditempatkan secara strategis di sekitar pabrik, dulunya berisi 75 pon persediaan dan peralatan.
"Jika saya berlari dengan salah satu tas itu, saya merasa seseorang harus menggunakan AED pada saya," kata Witt. "Tas itu awalnya dibuat oleh paramedis. Mengingat paramedis dapat berada di pabrik kami dalam waktu lima menit, isinya melampaui lingkup misi dan fokus tim. Kami memeriksa dan memutuskan apa yang perlu dan apa yang tidak. "
Yang dihilangkan adalah tangki oksigen, berbagai macam masker oksigen, dan banyak bidai. Membuat potongan adalah barang-barang seperti perban, kain kasa, masker resusitasi dan salep untuk luka bakar. Saat ini, kebutuhan tersebut disimpan dalam tas tali bahu yang beratnya delapan pon.
Pelatihan keselamatan: Pabrik Delta biasa melakukan semua pelatihan keselamatan tahunannya dalam satu sesi massal. "Menempatkan orang di sebuah ruangan dan berbicara dengan mereka sepanjang hari, itu berlebihan," kata Lamb. "Sulit untuk memperhatikan kalau selama itu."
Saat ini, pelatihan secara teratur ditawarkan dalam sesi 15 hingga 30 menit. Pekerja menyimpan kartu punch di dompet atau meja mereka yang memberi tahu mereka kelas apa yang perlu diambil. Sesi meliputi:tingkat listrik I, lockout/tagout, rencana tindakan darurat, kesadaran stormwater (pembuangan bahan kimia dan peraturan lingkungan), komunikasi bahaya, limbah berbahaya RCRA, insiden dan nyaris celaka, izin kerja panas, sistem manajemen dan ruang terbatas. Kartu itu dilubangi ketika orang tersebut mengambil kelas. Ketika pekerja mendapatkan semua 10 pukulan yang diperlukan, dia diikutsertakan dalam undian untuk kartu hadiah $50.
Lembar visual: Kartu punch adalah salah satu contoh penggunaan alat visual untuk meningkatkan kinerja keselamatan. Visual lain yang digunakan pabrik Delta adalah:lembar berisi foto yang menunjukkan kepada pekerja APD apa yang harus dipakai (dan tidak boleh dipakai) untuk area produksi tertentu; papan video di ruang makan siang yang menyediakan pesan keselamatan dan slide pelatihan; dan lampu lalu lintas yang memperingatkan pekerja ketika laporan keselamatan baru diposting di metrik dan papan informasi. Papan tersebut juga menyertakan gambar anggota Tim Produksi Aman dan Tim Tanggap Pertama.
Video: Jika sebuah gambar bernilai 1.000 kata, kesaksian keamanan yang direkam dalam video jauh lebih berharga. Seperti yang direferensikan di awal cerita, pabrik menawarkan pekerja kesempatan untuk menceritakan kisah langsung mereka tentang cedera di tempat kerja dan nyaris celaka dalam video Momen Keselamatan. Beberapa dari klip tiga sampai lima menit menggambarkan peristiwa yang terjadi di lokasi. Namun mengingat kelangkaan insiden dalam beberapa tahun terakhir, studi kasus sering menceritakan cedera atau peristiwa yang terjadi di majikan sebelumnya.
Mendidik orang luar: Pekerja Worthington berfokus pada keselamatan, tetapi bagaimana dengan pengunjung, distributor, kontraktor, dan pengemudi truk yang tiba di pabrik setiap hari? Satu-satunya cedera yang diderita di Delta selama setahun terakhir-plus terjadi pada orang luar yang menghindari praktik kerja yang aman.
"Semua orang di sini ditugaskan untuk mengawasi mereka," kata Ray Marteney, seorang pemimpin tim di jalur galvanisasi. "Sering kali, kami mendapatkan orang-orang yang berkata, 'Kami tahu apa yang kami lakukan.' Mereka bergegas dan melakukan pekerjaan mereka dan Anda dapat melihat bahaya yang mereka hadapi sendiri."
Meskipun sulit untuk melacak pengemudi truk yang mengunjungi pabrik untuk waktu yang singkat, pengunjung yang sering atau lama harus mengikuti kursus pelatihan singkat sebelum mereka diizinkan masuk ke pabrik.
Penghargaan: Perusahaan dan pabrik menawarkan banyak penghargaan untuk kinerja keselamatan. Penghargaan Ketua Worthington diberikan setiap tahun kepada pabrik yang menyelesaikan tahun fiskal dengan nol recordables dan nol kasus DART. Delta adalah salah satu dari 13 pemenang tahun ini (lihat sidebar di Halaman 16). Penghargaan Presiden diberikan kepada pabrik yang menyelesaikan tahun fiskal dengan nol kasus DART atau mereka yang mencapai peningkatan keselamatan yang signifikan. Penghargaan Tim Pekerjaan Aman diberikan setiap tiga bulan kepada departemen di setiap pabrik yang bebas kecelakaan dan mencapai kriteria tambahan yang ditetapkan oleh dewan keselamatan pabrik. Penghargaan Pekerja Aman diberikan setiap tiga bulan kepada individu di setiap pabrik yang bebas dari kecelakaan, memiliki catatan keselamatan dan kehadiran yang luar biasa, berpartisipasi dalam BRITE, dan mencapai kriteria yang ditetapkan oleh dewan keselamatan setempat.
MENINGKATKAN BAR
185 karyawan pabrik Worthington di Delta, Ohio, telah bersatu untuk meningkatkan keselamatan dan membuat sedikit sejarah.
Stoe menyebut pabrik itu "berlian" bagi perusahaan.
Tanaman saudara Delta sangat menghargainya. "Saya telah bekerja di beberapa pabrik di Worthington, dan Anda selalu dibandingkan dengan Delta," kata Guisinger.
Semua ini berarti dua hal:
1) Bilah telah dinaikkan.
"Kami ingin mengambil ini dari sangat baik menjadi sempurna," kata Leff. "Kami telah mengubah budaya. Kami mulai bergerak menuju metrik terkemuka seperti nyaris celaka. Kami melihat potensi insiden. BRITE juga lebih merupakan metrik terkemuka. Kami berfokus pada mengubah perilaku orang. Kami berfokus pada bagian pencegahan, bukan murni pada apa yang terjadi."
Nol bisa menjadi angka yang menakutkan.
"Ketika kami pertama kali mulai berbicara tentang nol cedera dan nol kecelakaan, bagi saya, itu adalah pekerjaan besar," kata Guisinger. “Saya lebih suka keluar dan membangun pabrik karena Anda dapat membangunnya dan menghubungkan titik-titik dan Anda memiliki sesuatu ketika itu selesai. Ketika kita berbicara tentang tanpa cedera, saya pikir itu akan menjadi sangat sulit karena mencakup setiap aspek your business. The expectations must be communicated. To achieve a complete zero (no recordables, lost-worktime cases, near misses) for a plant of our size, with all of the equipment and operations we have here, that would be an incredible thing . I think with the programs in place, and the people making the right decisions and choices, there's no limit to what we can do."
2) There is no rest on the quest to work safely.
"Continuous improvement in safety never ends," Mitchell says. "There isn't a finish line. Even with this facility having this great accomplishment of zero injuries in one year, there are still things we need to work on and improve upon. Just walking around the plant today, I saw five or six things that I will talk to Ryan Lamb about. These are little things, but there is always room for improvement."
Leeper is just as cautionary.
"Reaching that one-year goal scared the heck out of us," he says. "The fear was that we would have this big sigh of relief. 'We made it.' Yeah, we got that, but don't stop doing what you're doing. It's not all over. Keep your head in the game."
The pressure to achieve zero is always there. However, it certainly is better than the pressure of a mechanical vice on an operator's foot.
TAKE FIVE AND SLAM:A FEW SIMPLE STEPS CAN IMPROVE PLANT SAFETY
The Worthington plant in Delta, Ohio, utilizes a neat program called Take Five and SLAM (Stop, Look, Assess and Manage), which was developed by former DuPont engineer and plant manager Will Kraft. The concept seeks to have plant-floor personnel take five minutes before starting an assignment to:
STOP: Begin the plan with risk assessment. Ask yourself five important questions:
How can I be injured?
How can others be injured?
How can equipment be damaged?
What is the safest, most productive, highest-quality way to accomplish the task?
What information do I need?
Consider the following:surroundings/ environment, equipment/tools/parts, skills required, assistance needed, changes from previous experience, and procedures/job safety analyses (JSAs)/regulations.
LOOK: Look for hazards created through interaction of human, machine and the environment. These can include:energies in the workplace, ergonomics, health, etc.
ASSESS: Assess the risk by understanding the results of hazardous interactions. Consider the likelihood of risks (rare, possible or certain) and the consequences (insignificant, moderate or catastrophic).
MANAGE: Reduce the consequence through:
Reducing energy - electrical; mechanical (motion, spring, etc.); chemical; thermal; gravity; noise; dll.
Isolation and guarding - mechanical, PPE.
Reduce the likelihood through knowledge and skills, job planning with risk assessment, procedures with JSAs, and effective tools and processes.
Controls include the elimination of the hazard; substitution or redesign; training, planning and management; and guarding or PPE.
Work the plan by noting safety, cost, quality, productivity and the environment.
PLANT RECIPIENTS OF THIS YEAR'S CHAIRMAN'S AWARD
The 13 plant winners of Worthington Industries' Chairman's Award for fiscal year 2007:
Steel-processing facilities
Delta, Ohio
Decatur, Ala.
Dietrich metal framing facilities
Baytown, Texas
Denver, Colo.
Kapolei, Hawaii
Hutchins, Texas
Lenexa, Kan.
McDonough, Ga.
Phoenix, Ariz.
Stockton, Calif.
Wildwood, Fla.
Pressure cylinders facilities
Westerville, Ohio
Mid-rise construction products facilities
Cleveland, Ohio