Kasus bisnis untuk biaya siklus hidup
Banyak profesional industri telah mempertimbangkan untuk menerapkan prinsip biaya siklus hidup sebagai sarana untuk menurunkan biaya dan meningkatkan kinerja selama masa pakai peralatan. Hanya sedikit yang benar-benar menerapkan proses yang komprehensif dan berkelanjutan untuk mencapainya.
Sebagian besar setuju bahwa menerapkan prinsip biaya siklus hidup akan meningkatkan kinerja jangka panjang dari aset yang sedang dikembangkan. Namun, insinyur proyek biasanya diukur pada anggaran dan jadwal proyek, bukan pada kinerja biaya siklus hidup, sehingga memberikan insentif yang kuat untuk fokus pada biaya terpasang terendah dan mengabaikan prinsip-prinsip siklus hidup, terutama ketika menggunakan prinsip-prinsip tersebut menghasilkan anggaran yang berlebihan. atau penundaan jadwal. Makalah ini memberikan beberapa pemikiran tentang pembenaran penggunaan prinsip biaya siklus hidup dan, lebih khusus lagi, untuk membantu Anda mengembangkan model untuk menentukan "periode pengembalian" untuk menerapkan prinsip-prinsip ini.
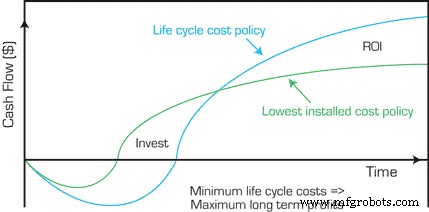
Gambar 1. Biaya siklus hidup dan arus kas.
Konsep dasar dalam menerapkan prinsip life cycle cost diwujudkan dalam Gambar 1.
Dalam model ini, prinsip yang diterapkan adalah bahwa jika kita menghabiskan sedikit lebih banyak uang dan waktu di bagian depan proyek, pengembaliannya akan tertunda tetapi sepadan, karena hal itu berlaku selama umur peralatan. Biaya siklus hidup minimum memberikan keuntungan jangka panjang maksimum! Tapi, bagaimana kita tahu apa pengembaliannya. Apa imbalannya? Sulit untuk dikatakan, sehingga membuatnya kurang menarik bagi insinyur proyek untuk menerima dan menerapkan penggunaan prinsip biaya siklus hidup. Namun, mari kita perhatikan data berikut dari produsen bahan kimia besar:
Data menunjukkan, dan banyak dari Anda mungkin pernah mengalami, bahwa dalam dua tahun pertama setelah startup, biaya perawatan lebih tinggi, terutama karena kebutuhan untuk memperbaiki dan mengganti komponen tertentu yang:A) tidak memenuhi persyaratan fungsional operasi , atau B) mengalami kegagalan masa pakai awal karena pemasangan yang buruk dan masalah startup.
Akibatnya, tambahan 3 persen dari nilai penggantian aset, atau dalam hal ini nilai modalnya, dihabiskan dalam dua tahun pertama untuk memperbaiki masalah yang seharusnya ditangani selama upaya desain dan pemasangan/pemulaan. Perhatikan bahwa ini tidak termasuk efek dari kerugian produksi, yang kemungkinan memiliki nilai yang jauh lebih tinggi (misalnya, lima kali biaya pemeliharaan), tergantung pada margin laba kotor untuk produk yang dibuat.
Bagaimanapun, upaya desain dan pemasangan yang lebih baik harus meminimalkan risiko yang terkait dengan masalah ini (misalnya, biaya pemeliharaan, kerugian produksi, dan risiko cedera; lebih banyak kegagalan peralatan menghasilkan risiko cedera yang lebih tinggi).
Selanjutnya, pertimbangkan data yang ditunjukkan pada Gambar 3 dari pabrikan Fortune 500 lainnya. Data ini menggambarkan kerugian produksi yang sering dialami selama satu hingga dua tahun pertama pendirian pabrik baru. Seperti yang ditunjukkan dalam Skenario No. 1, pabrik mencapai 70 persen dari kemampuan produksi desainnya selama enam bulan pertama setelah upaya permulaan awal, tetapi kemudian membutuhkan waktu satu tahun lagi sebelum mencapai kemampuan produksi penuh.
Mari kita asumsikan bahwa kita dapat, melalui desain dan pemasangan/penyalaan yang lebih baik, menangkap sebagian besar kerugian ini dan membuat pabrik berproduksi penuh dalam enam bulan pertama setelah upaya pengaktifan awal, seperti yang ditunjukkan pada Skenario No. 2.
Nilai produksi yang hilang diperkirakan sebagai selisih antara luasan di bawah dua plot untuk dua periode waktu di setiap skenario (nol sampai enam bulan dan enam sampai 18 bulan). Dengan kata lain, (A3 + A4) - (A1 + A2) =22,5 persen dari kapasitas produksi satu tahun, seperti yang ditunjukkan di bawah ini:
Skenario No. 2:
A3 + A4 =([6/12] x 100% x [1/2]) + (1 x 100) =25% + 100% =125%.
Skenario No. 1:
A1 + A2 =([6/12] x 70% x [1/2]) + [(1 x 70) + ([100-70] x )] =17,5% + 85% =102,5%
Dengan kata lain, dalam Skenario No. 1, selama 18 bulan pertama produksi awal, kami mencapai 102,5 persen dari produksi setara satu tahun. Apalagi, jika kita bisa meminimalkan masalah ini, kita akan mencapai 125 persen dari produksi setara satu tahun. Apa ini layak? Jelas, itu akan bervariasi dari bisnis ke bisnis, dan Anda harus mengembangkan data Anda sendiri untuk memperkirakan ini.
Namun, untuk mengilustrasikan nilai potensial, mari kita lakukan sebuah contoh. Mari kita asumsikan bahwa Anda dapat menangkap semua nilai produksi dalam Skenario No. 2, dan dapat mengurangi biaya perawatan awal Anda sehingga tambahan 3 persen dari biaya perawatan sebagai persentase dari nilai penggantian tidak dikeluarkan dalam dua tahun pertama setelah startup. Mari kita misalkan lebih lanjut berikut ini:
Biaya modal awal =$100 juta
Nilai produksi yang direncanakan =$100 juta per tahun
Kontribusi laba kotor =$30 juta per tahun
Biaya pemeliharaan =$6 juta di Tahun 1, $5 juta di Tahun 2 dan $4 juta di Tahun 3 (Gambar 2).
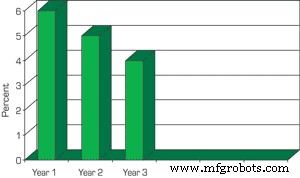
Gambar 2. Biaya pemeliharaan sebagai persentase dari nilai penggantian aset, setelah dimulai.
Jadi, berapa nilai relatif dari kedua skenario tersebut. Dalam Skenario No. 1, kami menghabiskan tambahan $3 juta untuk pemeliharaan, dan kehilangan sekitar 22,5 persen dari produksi setara satu tahun, dan laba kotor terkait, atau 0,225 x $30 juta, atau $6,75 juta. Total kerugiannya adalah $9,75 juta. Jadi, argumennya adalah jika kami menghabiskan $ 10 juta di muka untuk mengatasi masalah yang kami miliki di Skenario No. 1, dan kami yakin kami benar-benar dapat mencapainya, kami akan memulihkan investasi ekstra itu dalam 18 bulan pertama produksi. Dan yang lebih penting, kita harus memiliki lebih sedikit masalah dan kemampuan produksi yang lebih tinggi selama masa pakai peralatan. Apa itu layak? Anda menjadi hakim.
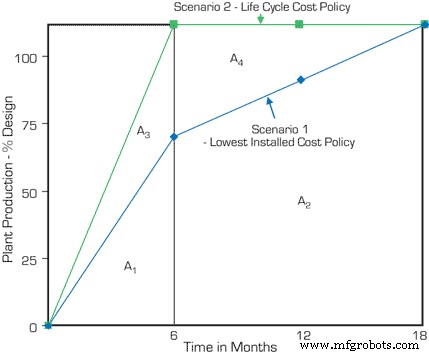
Gambar 3. Startup loss - dua skenario.
RINGKASAN
Anda harus mengembangkan skenario perusahaan Anda dan menggunakan penilaian Anda tentang nilai penerapan prinsip biaya siklus hidup. Anda bahkan dapat menyusun strategi untuk menerapkan prinsip-prinsip ini pada lima proyek besar Anda berikutnya untuk menentukan apakah mereka, pada kenyataannya, berhasil. Perhatikan bahwa ini mungkin membutuhkan waktu lima tahun atau lebih untuk menentukannya. Pendapat saya adalah bahwa biaya awal tambahan 10 persen pada sebuah proyek, mengingat bahwa itu dihabiskan untuk meminimalkan kesalahan desain dan dengan demikian meminimalkan biaya siklus hidup, adalah uang yang dihabiskan dengan baik. Ini memiliki pengembalian nosional 18 bulan dan akan sangat membantu mengatasi risiko kerugian di masa depan - produksi, biaya, dan cedera. Akhirnya, tambahan 10 persen pada anggaran modal tampaknya masuk akal untuk menerapkan prinsip-prinsip biaya siklus hidup. Dalam contoh ini, Anda mendapatkannya kembali hanya dalam 18 bulan!
Ron Moore adalah mitra pengelola The RM Group dan penulis “Praktik Umum yang Masuk Akal Sehat:Model untuk Keunggulan Manufaktur” (sekarang dalam edisi ketiganya) dan “Memilih Alat Peningkatan Manufaktur yang Tepat – Alat Apa? Kapan?”, keduanya dari Elsevier Books, Butterworth-Heinemann imprints. Dia dapat dihubungi di 865-675-7647 atau [email protected] .