Utilitas diuntungkan dari pemantauan kondisi, peningkatan sistem kontrol
Tahun ini, Amerika Serikat akan mengkonsumsi sekitar 3,3 terawatt – sedikit lebih dari 20 persen dari daya yang digunakan di seluruh dunia, menurut Badan Energi Internasional (IEA). Penggunaan listrik global sedang meningkat dan bisa berlipat ganda pada tahun 2050, menurut proyeksi IEA, karena pertumbuhan populasi global dan peningkatan standar hidup di negara-negara berkembang. Karena penggunaan listrik terus meningkat dan jaringan listrik didorong hingga batasnya, perusahaan utilitas mencari cara tambahan produksi listrik untuk memastikan mereka dapat memenuhi permintaan secara memadai.
Untuk utilitas Selatan besar yang menghasilkan listrik untuk sekitar 600.000 pelanggan eceran dan grosir, tinjauan tentang teknik yang diterapkan sebelumnya membantu meningkatkan pembangkitan listrik sekarang dan untuk tahun-tahun mendatang.
Utilitas membersihkan armada mesin turbin gas pembakaran yang tidak terpakai dan ingin memodernkannya untuk menghasilkan listrik cadangan selama periode konsumsi energi puncak. Ditugaskan untuk mengganti sistem kontrol penuaan pada mesin adalah HPI LLC, pengembang proyek yang mengkhususkan diri dalam menyediakan kontrol retrofit untuk pembangkit listrik turbin gas dan uap, kompresor dan sistem penggerak mekanis. HPI, yang berkantor pusat di Houston, membuka pintunya pada tahun 2002 dan sejak itu telah menyelesaikan lebih dari 70 model turbin gas yang berbeda untuk lebih dari 20 produsen. Perusahaan merancang, merakit, menguji, dan mengemas sistem penggantian menggunakan pengontrol terprogram yang dapat diprogram dan berkecepatan tinggi.
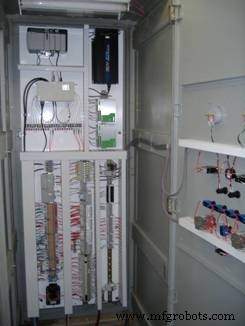
Pengontrol ControlLogix dan modul XM menawarkan keandalan dan kontrol turbin yang ditingkatkan.
Tantangan
Ketika pelanggan memutuskan untuk memperbarui empat paket generator turbo General Electric MS5001 (Frame 5), pelanggan menginginkan mesin online secepat mungkin. Kendala utama adalah sistem kontrol yang usang di mesin.
Selain teknologi pengontrol yang sudah ketinggalan zaman dan kabel yang sudah tua, sistem kontrol yang ada sangat membutuhkan pemantauan kondisi dan perlindungan getaran yang diperbarui. Kontroler untuk mesin turbin gas memastikan bahwa turbin mulai dan berhenti saat dipanggil, sedangkan sistem pemantauan dan perlindungan kondisi membantu mesin berjalan dengan aman dan efisien.
Kegagalan pengontrol atau proteksi sistem pada turbin gas adalah proposisi yang mahal dan berbahaya. Sistem perlindungan getaran utilitas yang ada terdiri dari kombinasi sistem General Electric Speedtronic, dan sistem getaran dan pemantauan Bently Nevada 3300. Untuk mengurangi biaya, pelanggan ingin mempertahankan probe getaran General Electric yang ada, tetapi karena getaran dan sistem pemantauan Bently tidak akan berinteraksi langsung dengan probe yang ada, HPI perlu mencari solusi lain.
Selain sistem pemantauan kondisi dan getaran, HPI perlu memperbarui sirkuit pelindung kritis lainnya – sistem perlindungan kecepatan berlebih. Dalam situasi retrofit, pelanggan HPI biasanya memiliki sistem perlindungan overspeed yang sudah usang atau hidrolik, yang membuat sistem sulit untuk diuji dan dirawat. Ini adalah kasus untuk proyek utilitas Selatan, dan HPI membutuhkan sistem penggantian yang andal dan mudah diservis.
“Jika perlindungan overspeed gagal, seluruh unit kemungkinan besar akan hancur, ” kata Tukang Roda. “Untuk pelanggan seperti ini, itu berarti jutaan dolar untuk membeli unit baru dan berbulan-bulan, jika bukan setahun penuh, untuk berdiri dan berjalan kembali.”
Solusi
yang disediakan HPI solusi sistem kontrol digital standar untuk utilitas yang menawarkan peningkatan keandalan, kontrol turbin dan informasi diagnostik yang ditingkatkan, dan kemampuan start jarak jauh.
Keberhasilan sistem baru berkisar pada penggunaan kontrol pelengkap, jaringan dan teknologi visualisasi – inti dari Rockwell Automation Integrated Architecture. Dirancang untuk memfasilitasi integrasi perusahaan yang mulus, kontrol produksi dan sistem informasi Arsitektur Terintegrasi terdiri dari Logix Control Platform dan rangkaian produksi dan kinerja terintegrasi FactoryTalk.
Memanfaatkan Allen-Bradley ControlLogix Programmable Automation Controller (PAC) , ControlNet dan jaringan EtherNet/IP dan perangkat lunak antarmuka manusia-mesin (HMI) FactoryTalk View SE, pelanggan memiliki sistem kontrol turbin yang kohesif. Ini berarti aktivitas yang terkoordinasi secara ketat dan berbagi informasi yang lebih baik.
HPI memilih ControlLogix karena kemampuannya untuk mengintegrasikan berbagai disiplin otomatisasi termasuk diskrit, gerak, kontrol proses, batch, sistem penggerak, dan keselamatan menggunakan lingkungan pengembangan tunggal dan satu protokol komunikasi terbuka.
“Kami dulu membeli pengontrol terpisah dan menyambungkannya, tetapi pengontrol Rockwell Automation Logix memungkinkan kami menyediakan solusi siap pakai yang melampaui hanya gas kontrol turbin,” kata Jerry Wheelwright, wakil presiden bidang teknik, HPI.
Manfaat penting lainnya dari penggantian bagi pelanggan datang dengan skema jaringan dan solusi visualisasi. HPI menghubungkan modul Allen-Bradley FLEX I/O dengan tembaga dan serat optik ControlNet dan komunikasi jaringan EtherNet/IP menggunakan modul 1756-ENTB dan modul 1756-CNB. Dengan menggunakan skema jaringan ini, mereka membangun PAC jarak jauh yang dipasang di panel yang mencakup modul FLEX I/O digital, analog, dan pemantau suhu. Untuk mengurangi jumlah pemasangan kabel di lokasi yang diperlukan, semua terminal, sekering, relai, dan saluran telah dipasang sebelumnya di subpanel.
Menggunakan jaringan ControlNet dan EtherNet/IP, pelanggan memanfaatkan komunikasi asli ControlLogix melalui topologi jaringan standar industri. EtherNet/IP memperluas Ethernet komersial dan siap pakai dengan protokol industri terbuka untuk tujuan otomatisasi – protokol yang sama yang digunakan dalam jaringan ControlNet.
Sistem kontrol yang diaktifkan informasi memungkinkan pelanggan untuk beroperasi sistem, yang digerakkan oleh pengontrol ControlLogix dari lokasi yang berjarak lima mil dari turbin fisik.
“Kemampuan untuk memantau dan mengontrol turbin setiap saat sepanjang hari dari lokasi yang jauh adalah manfaat yang signifikan bagi pelanggan ini,” kata Wheelwright. “Utilitas dapat memiliki turbin gas yang tersebar di seluruh negara bagian dan menjalankan kontrol melalui pembangkit turbin uap yang lebih besar yang diawaki 24 jam sehari, menghilangkan kebutuhan mereka untuk mengelola setiap lokasi.”
Karena HPI menggunakan Logix Control Platform untuk menstandarisasi panel kontrol, menggabungkan modul seri XM dari Rockwell Automation untuk pemantauan kondisi adalah hal yang wajar. HPI menggunakan modul pengukuran dinamis XM-120 untuk perlindungan getaran. Modul XM-120 adalah monitor tujuan umum dua saluran yang cerdas yang memungkinkan pelanggan menggunakan probe getaran yang ada.
HPI menggunakan dua modul pada masing-masing dari empat turbin. Modul ini mendukung pemantauan getaran poros, selubung atau tumpuan pada peralatan yang berputar, seperti turbin, di mana pemantauan atau perlindungan kondisi waktu nyata diperlukan. Modul XM-120 berinteraksi dengan peralatan melalui ControlNet ke modul antarmuka DeviceNet.
Penggantian sistem perlindungan overspeed juga disederhanakan menggunakan Logix Control Platform. HPI mengganti sistem perlindungan kecepatan berlebih yang sudah usang dengan modul kecepatan ganda XM-220. Modul XM-220 adalah modul pengukuran dua saluran yang cerdas yang menerima input dari dua takometer. Modul ini mengukur kecepatan, akselerasi rotor, dan kecepatan puncak, serta mampu mendeteksi kecepatan nol, rotor terkunci, dan rotasi balik.
Sebagai sistem pemantauan dan perlindungan mesin pertama di industri yang berhasil menghubungkan alat perawatan ke dalam arsitektur kontrol, modul XM-220 dapat digunakan pada bus industri standar terbuka, memungkinkan pemantauan dan perlindungan aset penting yang berkelanjutan dan hemat biaya.
Hasil
Sistem kontrol pengganti HPI menyediakan pelanggan dengan kinerja yang konsisten, berulang, dan andal. Turbin utilitas tidak mengalami kegagalan start sejak peningkatan kontrol. HPI sangat senang dengan fleksibilitas seri XM, kemudahan konfigurasi dan kemampuan untuk melihat bahwa sirkuit pelindung bekerja, perusahaan memutuskan untuk menstandarisasi peralatan untuk peningkatan di masa mendatang.
“Kami memilih seri XM karena dua alasan,” kata Wheelwright. “Salah satunya adalah ketersediaan. Itu ada di rak ketika kami membutuhkannya. Alasan kedua adalah kemampuannya untuk berinteraksi dengan probe lain dan sistem lainnya.”
Karena kesederhanaan Logix Control Platform, HPI dapat membangun subpanel modular atau membuat kabinet yang sama sekali baru yang memenuhi kebutuhan ruang khusus tanaman.
HPI menawarkan layanan 24 jam dan bantuan teknis. Dengan menggunakan platform ControlLogix dan produk Allen-Bradley, pelanggannya dapat memperoleh perangkat keras yang mereka butuhkan di lokasi distributor Rockwell Automation di seluruh dunia. Pelanggan kemudian dapat menginstal perangkat keras itu sendiri. Dari kantor pusatnya di Houston, HPI akan mengirimkan patch perangkat lunak melalui email, mengerjakan sistem kontrol, dan memastikan model I/O terintegrasi.
Untuk mengurangi jumlah pemasangan kabel di lokasi yang diperlukan, HPI telah diinstal sebelumnya semua terminal, sekering, relai, dan saluran di subpanel.