Membuat Program Analisis Oli yang Ramping tapi Efektif
Baik itu masalah anggaran, dukungan manajemen, kekurangan individu, atau hanya perusahaan kecil dengan dana terbatas, ada cara untuk membuat program analisis oli yang efektif dengan biaya awal dan operasi minimal.
Dalam artikel ini, Anda akan membaca studi kasus tentang alternatif alat uji internal yang mahal, pemanfaatan laboratorium luar yang baik, solusi penyimpanan minyak, metode pelaporan temuan untuk memajukan program, menjual program ke manajemen tingkat atas serta ke operasi dan pemeliharaan, dan memulai dari awal lagi saat fasilitas Anda terjual.
Berikut adalah langkah-langkah yang saya alami dalam menyiapkan program analisis oli kami:
- Tujuan program analisis minyak
- Upaya kami untuk menyiapkan program canggih
- Tindakan saya setelah manajemen menolak rencana awal kami
- Peralatan yang digunakan dalam program analisis lean oil
- Program saat ini
Apa tujuan dari program analisis minyak?
Menurut saya, keandalan adalah alasan No. 1 kami melakukan pemeliharaan prediktif. Uptime adalah satu-satunya cara untuk bersaing di dunia yang sangat kompetitif saat ini. Mendeteksi masalah dan mencegah kegagalan adalah cara untuk mendapatkan waktu kerja semaksimal mungkin dari peralatan kami. Seiring dengan waktu aktif, pengurangan biaya juga penting untuk profitabilitas perusahaan mana pun.
Jika masalah peralatan dapat dideteksi lebih awal, masalah tersebut dapat dijadwalkan untuk diperbaiki atau diganti sebelum menyebabkan waktu henti yang mahal atau kerusakan peralatan. Tujuan akhirnya adalah menjalankan setiap komponen selama mungkin dan dapat memprediksi terlebih dahulu kapan komponen tersebut perlu diubah. Ini juga termasuk minyak. Semakin lama, oli menjadi komponen yang sangat mahal dari peralatan apa pun; mendapatkan masa pakai oli terpanjang yang Anda bisa tidak berbeda dengan bantalan atau roda gigi.
Biaya program pemeliharaan prediktif juga menambah biaya produksi dan diteliti lebih dari biaya lainnya, karena tidak dilihat secara langsung terkait dengan produksi. Tidak seperti getaran dan termografi, analisis oli biasanya memerlukan laboratorium luar untuk melakukan pengujian guna menganalisis sampel.
Sangat penting untuk menunjukkan keberhasilan sejak dini dan harus dikomunikasikan dengan cepat tidak hanya kepada manajemen tetapi juga kepada produksi dan pemeliharaan. Mendapatkan dukungan dari produksi dan pemeliharaan akan sangat membantu manajemen menjual uang yang dikeluarkan untuk program tersebut.
Jadi, jika Anda adalah perusahaan kecil dengan tidak banyak modal untuk bekerja, perusahaan besar yang berurusan dengan pengendalian biaya, tidak ada dukungan pemeliharaan prediktif oleh manajemen atau, dalam beberapa kasus, ada kombinasi masalah yang menghalangi Anda untuk memulai. atau mempertahankan program pemeliharaan prediktif, kesuksesan dapat dicapai dengan sedikit tekad dan sedikit pemikiran di luar kebiasaan.
Untuk memulainya, saya akan memberi Anda sedikit sejarah tentang bagaimana saya harus menyiapkan program analisis lean oil, apa yang menyebabkannya, bagaimana perkembangannya, dan keberhasilan yang dicapai.
Upaya kami untuk program kelas dunia
Dalam kasus saya, masalah terus berubah seiring pertumbuhan perusahaan kami dan kemudian dijual dua kali. Pada awalnya, kami dibentuk untuk menjadi pemeliharaan lintas-kerajinan penuh, dan setiap teknisi akan menjadi ahli dalam setiap aspek pemeliharaan, termasuk prediktif. Setiap orang diberikan beberapa pelatihan dasar tentang getaran, pelurusan, dan analisis oli. Sangat jelas bagi kami bahwa hanya teknisi tertentu yang tertarik pada masing-masing disiplin ilmu, tetapi setiap orang diharapkan untuk menyelesaikan perintah kerja apa pun yang diberikan kepada mereka.
Ini menghasilkan tren yang sangat tidak menentu dan bahkan analisis data yang lebih buruk. Banyak motor, bantalan, dan reduksi salah didiagnosis, membuang-buang tenaga, material, dan mengurangi keandalan. Manajemen masih ingin memiliki semua orang sebagai ahli dalam setiap disiplin pemeliharaan. Untuk mencapai ini, mereka berencana untuk mengirim dua teknisi sekaligus untuk pelatihan. Untungnya, dua yang pertama dikirim ke getaran serta dua yang dikirim ke pelatihan analisis oli sangat menyukai prosesnya.
Mereka mengambil kepemilikan atas setiap program dan mampu mencapai beberapa keberhasilan awal, tetapi tidak ada yang diizinkan untuk menjadi teknisi pemeliharaan prediktif khusus; kami masih memiliki setiap teknisi pemeliharaan mengumpulkan data dan melakukan analisis. Setiap kali ada kondisi alarm, jawabannya adalah, “Ganti oli”, “Ganti motor”, atau “Jalankan dan amati”.
Perubahan dimulai ketika dua orang memilih untuk pelatihan awal – satu analisis oli dan satu getaran – memutuskan untuk menangani sendiri masalah tersebut. Memikirkan kembali apa yang membuat kami melakukan ini di belakang manajemen, itu pasti karena hasrat untuk proses pemeliharaan prediktif, atau mungkin hanya sensasi lolos dari sesuatu.
Beberapa kelompok asli yang terlatih dalam analisis oli dan getaran kehilangan minat pada program karena manajemen tidak akan berinvestasi dalam peralatan yang dibutuhkan atau staf program secara penuh waktu. Bahkan setelah menyusun proposal yang menunjukkan semua manfaat dan imbalan dari program yang lengkap, manajemen mempertahankan filosofi mereka tentang departemen pemeliharaan lintas bidang penuh tanpa spesialis.
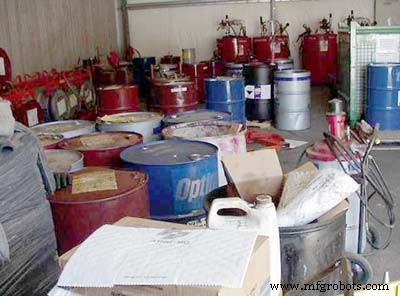
Gambar 1. Sebelum Gambar Ruang Minyak Clarion Boards
Perubahan rencana
Pola pikir lainnya adalah berjalan lambat dan meyakinkan manajemen melalui hasil. Metode yang digunakan sedikit berbeda dan memerlukan beberapa risiko, berada di belakang manajemen, tetapi metode tersebut telah mendorong kami untuk menjadi tenaga kerja mandiri. Semua teknisi di pabrik kami bekerja dalam shift dan bekerja dalam shift bergilir 12 jam. Manajemen bekerja hari lurus dan tidak ada akhir pekan, yang membuat kami harus mengatur sendiri malam dan akhir pekan.
Ini memberi kami peluang besar untuk menyiapkan program analisis minyak kami menggunakan cara non-tradisional. Saya akan menyelesaikan pekerjaan terjadwal saya secepat mungkin atau merekrut teknisi lain dalam shift saya untuk membantu pekerjaan terjadwal sehingga saya dapat meluangkan sedikit waktu setiap shift untuk menyiapkan program. Saya juga mengajukan diri untuk melakukan semua tugas pemeliharaan preventif (PM) penggantian oli pada hari-hari tidak aktif. Ini memberi saya kesempatan untuk merancang dan memasang port pengambilan sampel oli di semua peralatan kami.
Selama proses ini, kami menemukan beberapa dukungan dari kantor perusahaan kami. Kami mulai mengajukan pertanyaan kepada departemen pelatihan industri, yang memicu minat pada apa yang kami lakukan, dan pertanyaan diajukan kepada supervisor kami tentang kemajuan. Misalnya, mereka ingin mengetahui berapa banyak titik pengambilan sampel yang kami miliki untuk getaran kami dan berapa banyak port pengambilan sampel yang dipasang pada peralatan untuk analisis oli.
Ketika supervisor saya mendapat pujian karena memiliki 150 port pengambilan sampel yang dipasang di peralatan, dia terkejut dan bingung dan ingin tahu bagaimana hal ini dicapai tanpa dia sadari. Setelah melihat minat yang ditunjukkan perusahaan, ia memulai proses mendedikasikan beberapa teknisi untuk proses pemeliharaan prediktif. Dia menghadapi perlawanan yang sama dengan manajemen pabrik yang kami miliki di masa lalu (tidak ada spesialis), tetapi karena tekanan diterapkan dari perusahaan, proposalnya didorong, dengan beberapa perubahan.
Rencana yang disepakati oleh para manajer di fasilitas kami adalah tiga bulan, tim tiga orang untuk bekerja shift siang, untuk menyiapkan dan memulai program PdM. Setelah tiga bulan, tiga teknisi lagi akan diliburkan, dan mereka akan melanjutkan program tersebut. Rotasi ini akan berlanjut dengan seluruh staf pemeliharaan kami. Hanya tiga orang yang melamar posisi tersebut; sisanya tahu bahwa manajemen hanya melakukan ini karena tekanan perusahaan dan tidak akan memberikan dukungan program yang diperlukan untuk berhasil.
Setelah menerima posisi dan mendengarkan aturan dan batasan, kami mulai bekerja mengembangkan program dengan satu tujuan dalam pikiran – apa pun hambatan yang mereka berikan kepada kami, kami akan berhasil.
Kami langsung diberitahu bahwa tidak akan ada uang untuk program PdM. Kami harus menggunakan peralatan dan sumber daya yang sudah kami miliki. Tujuan pertama kami adalah menggunakan alat apa yang kami miliki untuk menunjukkan kesuksesan secepat mungkin. Bekerja dengan pemasok oli, yang memberi kami pengujian oli gratis (yang ternyata sepadan dengan apa yang kami bayar), saya menghabiskan waktu untuk menyempurnakan proses pengumpulan data.
Menjaga sampel tetap bersih dan membawanya ke lab dengan cepat memberi saya tren yang stabil pada sebagian besar peralatan. Memiliki satu orang yang mengumpulkan semua data memberi kami tren yang lebih stabil dibandingkan dengan meminta setiap teknisi pemeliharaan mengumpulkan data. Pada sebagian besar peralatan, saya bisa mendapatkan tren yang bagus kecuali penyimpangan lab – hal pengujian oli gratis. Saya akan membahasnya nanti.
Langkah saya selanjutnya adalah mengembangkan laporan di mana kami dapat menunjukkan semua kesuksesan dan tabungan kami untuk perusahaan. Saya menggunakan angka yang sangat konservatif saat memperkirakan uang yang dihemat atau waktu henti yang dapat dihindari. Saya akan memastikan laporan itu dikirim ke manajemen serta teknisi pemeliharaan dan proses. Untuk mempromosikan program, saya juga meneruskan laporan ke pusat pelatihan industri di kantor pusat perusahaan kami, yang, dengan bantuan mereka, naik tangga. Hal ini menimbulkan beberapa masalah dengan manajemen pabrik kami, tetapi ini mengamankan tempat kami karena mereka tidak dapat membenarkan penutupan kami.
Salah satu cara tercepat untuk menunjukkan penghematan ternyata adalah manfaat dari memiliki begitu banyak port pengambilan sampel yang dipasang di peralatan kami. Setiap peredam, dari yang terbesar hingga terkecil, serta setiap sistem hidraulik dan pelumas memiliki port pengambilan sampel yang terpasang. Sampel dapat diambil saat peralatan sedang berjalan. Saya dapat mengatur semua peralatan ini untuk penggantian oli berdasarkan kondisi. Penggantian oli yang direkomendasikan OEM untuk sebagian besar sistem hidraulik kami dilakukan pada waktu yang hampir bersamaan.
Dengan menggunakan hasil lab, saya dapat menunjukkan bahwa semua oli hidraulik dalam sistem sama baiknya dengan yang baru. Total minyak untuk sistem ini lebih dari 900 galon. Sampai hari ini, 11 tahun setelah startup, kami masih menggunakan pengisian asli pada sistem hidrolik. Mengganti oli berdasarkan kondisi mengurangi konsumsi oli sekitar 70 persen di tahun pertama.
Ruang penyimpanan minyak menjadi kamar saya karena tidak ada orang lain yang ingin mengambil alih kekacauan itu. Kami memiliki bangunan terpisah yang menempel di samping pabrik kami hanya untuk menyimpan minyak kami. Ruangan ini menjadi tempat persembunyian segala sesuatu yang berantakan. Beberapa sistem kami menghasilkan banyak limbah minyak yang terkontaminasi dengan serat kayu sebagai bagian dari proses. Limbah ini bersama dengan limbah minyak lainnya ada di mana-mana di gedung penyimpanan, bersama dengan oli baru kami dan wadah yang digunakan untuk sistem pengisian. Saya harus bertanggung jawab atas ruang minyak jika saya ingin berhasil dengan program analisis minyak.
Salah satu pabrik saudara kami memiliki sistem penyimpanan minyak yang terdiri dari tangki penyimpanan yang dibangun ke dalam sistem rak yang bagus dengan selang dan pompa untuk mentransfer dan menjaga minyak tetap bersih. Permintaan pembelian saya untuk sistem ini ditolak, jadi saya mulai menggunakan apa yang kami miliki dan, menggunakan beberapa ide dari pelatihan Noria, merancang sistem penyimpanan saya sendiri. Menambahkan kaki ke sistem rak drum yang kami miliki, saya mulai membersihkan ruang penyimpanan minyak.
Saya dapat membeli tangki limbah minyak baru serta beberapa lemari penyimpanan dan seiring waktu membeli wadah pemindahan minyak khusus. Ruang minyak yang sudah jadi (Gambar 2) akhirnya menjadi standar untuk seluruh perusahaan, termasuk pabrik saudara kami. Mereka harus melepaskan sistem penyimpanan mewah mereka dan menggantinya dengan sistem ini.
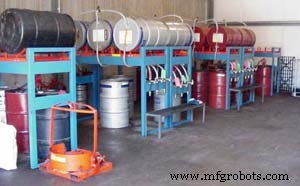
Gambar 2. Ruang Minyak Setelah Mengambil Kontrol
Selanjutnya, saya mengarahkan pandangan saya untuk meningkatkan pengambilan sampel, pengujian, dan analisis. Saya memiliki sekitar 100 sampel untuk diambil setiap bulan untuk mengawasi peralatan kami dan mengelola penggantian oli berdasarkan kondisi pada semua peralatan kami. Ini berarti kami akan kehabisan sampel gratis dalam waktu sekitar lima bulan. Saya memproyeksikan berapa biayanya untuk melanjutkan program selama tujuh bulan lainnya dalam setahun.
Pengujian jumlah partikel bukan bagian dari kesepakatan sampel gratis, dan akan ada biaya untuk pengujian ini yang ditambahkan ke paket untuk semua sampel. Seperti yang saya sebutkan sebelumnya, layanan lab gratis yang kami miliki dengan pemasok minyak kami sepadan dengan apa yang kami bayar untuk itu. Sekarang kami harus membayar untuk tes, jumlah partikel untuk 500 pertama dan kemudian harga penuh untuk semua sampel setelah itu. Saya perlu mencari tahu apakah layanan lab yang mereka tawarkan akan sepadan.
Setelah semua data dikumpulkan oleh satu orang, tren mulai naik, tetapi saya masih melihat hasil tes di waktu-waktu yang ada di mana-mana. Tidak dapat menghubungi lab, kecuali melalui perwakilan oli kami, saya memutuskan untuk menjalankan tes sederhana untuk melihat seberapa andal hasil yang kami peroleh dari lab. Setelah menarik cukup minyak dari drum minyak baru untuk membuat empat sampel, saya mengirimnya ke lab untuk pengujian.
Sebelum memisahkan minyak menjadi empat botol, saya mengaduk minyak secara menyeluruh. Hasil yang saya dapatkan semuanya berbeda. Jumlah partikel, viskositas dan hasil aditif ada di mana-mana. Saya menjalankan tes yang sama dalam kualifikasi laboratorium independen. Saya memilih lab dengan pengulangan terbaik.
Masih tidak memiliki anggaran untuk bekerja, saya menyusun proposal yang akan membuat kami melakukan beberapa pengujian internal, bersama dengan dukungan laboratorium independen dengan investasi yang sangat kecil. Saya membandingkan biaya:
- Laboratorium internal lengkap dengan semua peralatan yang diperlukan
- Laboratorium independen yang melakukan semua pekerjaan lab
- Sistem kami saat ini memproyeksikan fakta bahwa kami akan menjalankan sampel gratis kami di pertengahan tahun
Ini semua ternyata sangat mahal dan semuanya ditolak oleh manajemen. Saya mulai mencari alternatif.
Peralatan ramping
Jika saya dapat menemukan cara untuk melakukan pengujian internal dan hanya menggunakan lab luar untuk sampel yang sangat kritis dan meragukan, saya akan mendapatkan data yang lebih berguna dengan biaya lebih rendah. Kriteria yang saya tetapkan untuk peralatan pengujian internal saya adalah pengulangan, kemudahan penggunaan, dan kemampuan untuk melakukan pengujian dengan cepat. Pengulangan akan menjadi faktor terbesar. Mengetahui bahwa setiap tes akurat adalah suatu keharusan. Tiga tes yang saya rasa diperlukan untuk memiliki program internal yang efektif adalah viskositas, jumlah partikel, dan air.
Viskositas
Viskositas dapat diukur dengan menggunakan visgage, unit genggam dengan dua tabung masing-masing berisi bola baja. Salah satu tabung diisi dengan cairan referensi; yang lain dapat diisi dengan cairan yang akan diuji. Setelah memiringkan pengukur untuk membawa bola ke salah satu ujungnya, pengukur dipegang pada sudut 45 derajat sampai salah satu bola mencapai ujung skala pengukur; bola lainnya akan menunjukkan viskositas cairan.
Saat mengirimkan sampel ke lab, saya akan menggunakan tampilan dan merekam data dan membandingkannya dengan hasil tes dari lab. Saya terkejut betapa akurat tampilannya dengan sedikit latihan.
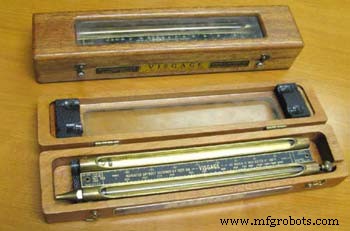
Gambar 3. Dua tampilan dibeli melalui lelang online – satu dalam centistoke dan yang lainnya dalam Saybolt detik.
Uji tempel
Setelah membaca artikel tentang tes tempel, saya memutuskan untuk melihat peralatan apa yang dibutuhkan, seberapa akurat tes itu dan apakah hasilnya dapat diulang. Saya juga membutuhkan cara agar data tren dilihat di tambalan. Saya menemukan mikroskop di Internet yang memiliki kamera digital yang terhubung ke komputer pribadi. Dengan lampiran kamera, saya dapat menyimpan gambar tambalan dan tren perubahan apa pun.
Saya juga menemukan bahwa cahaya atas diperlukan untuk melihat dan mengidentifikasi partikel pada patch. Magnet genggam kecil yang bergerak di samping mikroskop akan membuat logam besi menari. Menggunakan lampu atas dan bawah serta lensa 100 kali atau 400 kali membantu mengidentifikasi jenis keausan.
Sebelum menguji sampel, sampel harus diaduk. Saya menemukan sejak awal bahwa pengadukan sampel yang tepat membuat perbedaan besar dalam akurasi dan pengulangan tes. Saya memberi harga pada agitator komersial dan ternyata cukup mahal. Teknologi getaran kami membuat stasiun pelatihan getaran dari peredam bekas dan motor tua. Keluaran peredam berputar sangat lambat, memasang roda untuk menahan botol sampel; rotasi lambat mengaduk sampel serta pengocok bergetar apa pun.
Uji tempel menjadi tulang punggung program saya. Saya menggunakan tambalan untuk memeriksa sampel untuk kontaminasi, memakai puing-puing dan untuk melakukan penghitungan partikel yang belum sempurna. Menggunakan citra digital untuk menyimpan dan tren data yang dikumpulkan memudahkan untuk mendeteksi perubahan kondisi peralatan. Jika sesuatu yang tidak biasa diamati, maka sampel dapat dikirim ke laboratorium. Karena uji tempel menggunakan sedikit sampel, masih ada cukup sampel yang tersisa untuk dikirim ke laboratorium untuk pengujian dan analisis lebih lanjut.
Ada atlas uji tempel yang tersedia untuk membantu mengidentifikasi kontaminasi dan puing-puing keausan. Gambar sebenarnya dari berbagai jenis puing-puing aus dapat membantu Anda mengidentifikasi apa yang Anda lihat di mikroskop. Untuk merasakan perkiraan kandungan partikel suatu cairan, saya akan mengirim sampel ke lab dan membandingkan perkiraan saya dengan yang sebenarnya dari lab.
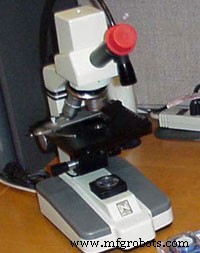
Gambar 4.
Saya menemukan dua metode untuk membuat tambalan. Satu terdiri dari pemegang patch berbentuk corong yang menggunakan gravitasi atau vakum untuk menjalankan cairan melalui patch. Ini bekerja dengan baik tetapi memiliki beberapa masalah:waktu, pembersihan, dan eksposur.
Menggunakan gravitasi untuk mengalirkan cairan melalui tambalan membutuhkan waktu dan sangat bergantung pada penambahan jumlah cairan pengencer yang tepat ke sampel agar cukup encer untuk melewati tambalan. Membersihkan corong di antara pengujian tidak hanya membutuhkan waktu tetapi juga dapat mempengaruhi sampel berikutnya jika ada residu yang tertinggal. Menuangkan, mencampur, dan waktu sampel terpapar ke udara dapat memengaruhi hasil tambalan.
Metode kedua, menggunakan jarum suntik dengan katup periksa dua arah, menyelesaikan semua masalah yang saya miliki dengan metode corong. Dengan katup periksa dua arah, saya dapat menarik jumlah minyak yang tepat dan kemudian cairan tipis dalam jarum suntik serta mendorongnya melalui patch dengan paparan minimal ke atmosfer. Membersihkan jarum suntik sangat mudah dan cepat, selain membersihkan semua cairan dan kontaminasi dengan cepat menggunakan metode yang sama. Hanya perlu beberapa menit untuk membuat tambalan yang siap dianalisis.
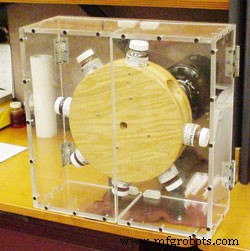
Gambar 5. Agitator botol ini dibuat sendiri dengan menggunakan bagian yang dibuang.
Uji kelembapan
Menguji minyak untuk air juga bisa dilakukan di rumah. Air dalam sistem yang saya uji di rumah tidak sepenting yang saya kirim ke lab. Pereduksi kecil yang berjalan di bawah beban normal dapat menangani sedikit kelembapan tanpa terlalu banyak kesulitan. Namun, untuk pemeriksaan keandalan guna memastikan kelembapan tidak menjadi masalah, saya menggunakan uji kresek.
Beberapa tetes minyak yang diletakkan di atas piring panas yang disetel ke suhu yang tepat akan memberi Anda pemeriksaan cepat untuk mengetahui keberadaan air. Memiliki lampu pembesar di atas hot plate tidak hanya melindungi Anda dari minyak panas tetapi juga memberi Anda pandangan yang lebih baik tentang pengujian. Saya juga telah menggunakan ini dalam pengujian darurat untuk peralatan penting kami untuk menguji kebocoran air pendingin.
Ujian internal
Sampel oli tipikal akan melalui langkah-langkah berikut setelah pengumpulan:
Tes visual: Lihatlah warna dan kejernihan minyak. Untuk tujuan ini, saya hanya menggunakan botol bening. Saya memiliki rak sampel oli baru yang berguna untuk perbandingan dan mencatat setiap perubahan warna. Hilangnya kejernihan dapat mengindikasikan kontaminasi oleh air, partikel aus, kotoran, atau oli pengisian yang salah.
Uji penciuman: Ini dapat mengungkapkan masalah dengan kontaminasi, oksidasi, dan pernis. Sampel oli baru juga berguna untuk pengujian ini.
Viskositas: Gunakan visgage untuk menguji viskositas dan merekam data.
Uji kresek: Taruh beberapa tetes dari visgage ke hot plate dan periksa apakah ada air di dalam oli.
Uji tempel: Hasilkan tambalan dan analisis. Periksa logam besi, menggunakan magnet, dan catat jumlah dan ukuran partikel. Cari dan catat jumlah kontaminan lain pada patch. Simpan gambar ke database untuk trending.
Laporan: Ini mungkin salah satu bagian terpenting dalam menjaga program tetap berjalan. Pelaporan temuan dan keberhasilan akan menghasilkan banyak minat dalam program ini. Jaga agar laporan tetap singkat dan to the point. Biasanya hanya halaman pertama laporan yang dibaca, jadi cobalah untuk menyimpannya di satu halaman dan menutupi kesuksesan Anda. Saya menemukan bahwa mengirimkan laporan ke manajemen untuk diproses membantu membuat semua orang sadar akan keberhasilan program.
Memulai dari awal
Tak lama setelah semuanya bekerja dengan baik dan mendapatkan pengalaman dengan peralatan, kami dimatikan. Masalah pasar menyebabkan penutupan, yang berlangsung selama 18 bulan. Ketika kami akhirnya dijual, setengah dari teknisi pemeliharaan tidak kembali. Pada bulan September 2004, kami memulai kembali pabrik; dan sampai hari ini, kami masih mencoba untuk membenahi departemen pemeliharaan kami. Sekali lagi, saya harus mulai menjual secara berlebihan pentingnya analisis minyak kepada manajemen.
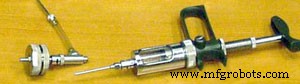
Gambar 6. Penahan Patch, Katup Dua Arah, dan Jarum Suntik untuk Membuat Tambalan yang Cepat dan Andal
Menemukan orang yang tepat untuk pekerjaan itu adalah kunci kesuksesan. Untuk membuatnya bekerja di lingkungan yang ramping membutuhkan seseorang yang berdedikasi dan memiliki semangat untuk proses analisis minyak. Saat ini, saya masih mencari orang yang tepat untuk mengisi posisi ini – seseorang yang bersedia mengambil alih kepemilikan penyimpanan minyak, mengambil alih pengaturan pengambilan sampel, pengujian dan pelaporan serta seseorang yang dapat berpikir di luar kotak.
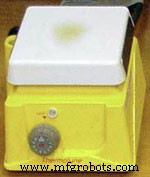
Gambar 7. Pelat Panas untuk Uji Kresek
Tentang penulis:
Dave Lander adalah supervisor pemeliharaan mekanik di Clarion Boards Inc. di Lucinda, Pa. Dave adalah penduduk seumur hidup, Lucinda, sebuah kota kecil di Pennsylvania barat, yang terletak di jantung industri kayu keras. Dave menghabiskan 22 tahun bekerja di pabrik penggergajian, di mana dia percaya bahwa serbuk gergaji adalah aditif minyak. 12 tahun terakhir telah dihabiskan di industri produk panel membuat papan serat kepadatan menengah di Clarion Boards. Dia memiliki sertifikasi Analis Pelumas Mesin Level II melalui Dewan Internasional untuk Pelumasan Mesin dan merupakan sukarelawan di komite penulisan tes ICML.