Keandalan &Ketersediaan:Cara Mencapainya dengan FMEA dan Kurva P-F
Untuk organisasi yang mengalami kegagalan tak terduga dan waktu henti yang tidak direncanakan, Mode Kegagalan dan Analisis Efek (FMEA) dapat membantu mencapai keandalan dan ketersediaan aset yang tinggi.
Anda mendapatkan keandalan dan ketersediaan dengan benar, dan Anda masih jauh di jalan menuju profitabilitas.
Tapi ini kejutannya.
Banyak organisasi dan produsen tidak pernah melakukan perjalanan ini dan dengan senang hati melanjutkan (jika produk yang dapat digunakan sampai ke pelanggan tepat waktu ) dalam spiral ke bawah.
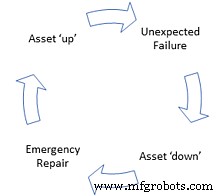
'Tapi perjalanan yang Anda bicarakan adalah RCM!' seru mereka. ‘Terlalu mahal untuk kami!’
Produsen yang sama sepertinya selalu punya waktu (dan uang) untuk membuang produk yang terbuang, membeli bantalan baru, membersihkan tumpahan oli, memperbaiki mesin, memanggil OEM (Original Equipment Manufacturer), dan membuat orang bekerja lembur. Dan setahun sekali – dengan banyak kemeriahan dan upacara - mereka memberikan penghargaan kepada 'pahlawan' pemeliharaan reaktif.
Hmm.
Anda berpikir:‘Orang-orang mendapatkan gambaran mereka di buletin perusahaan, jabat tangan dari VP untuk menjaga pabrik dalam pemeliharaan reaktif ?’.
Ya, benar. Tapi mari kita bergerak lebih dari itu.
Mendapatkan keandalan aset yang baik dan ketersediaan tinggi tidak memerlukan studi RCM lengkap. Tapi itu memang membutuhkan FMEA (Failure Mode &Effect Analysis) yang baik dengan output yang baik, dan penerapan kurva P-F (Potential Failure to Functional failure) untuk memastikan teknik pemantauan kondisi difokuskan pada mode kegagalan yang tepat pada frekuensi inspeksi yang tepat.
Mode Kegagalan &Analisis Efek:memahami hal-hal yang paling bawah (atau paling atas)
FMEA adalah alat analisis umum yang membantu desainer, teknisi, dan insinyur memahami bagaimana aset atau komponen penting dapat gagal, pengaruhnya terhadap sistem secara keseluruhan, dan apa yang mereka dapat dilakukan untuk mengurangi efeknya.
Inti dari FMEA adalah memahami mode kegagalan, seberapa besar kemungkinannya terjadi, dan menguranginya dengan tindakan pemeliharaan khusus, mendesain ulang, atau bahkan 'tidak melakukan apa pun' (jika risikonya cukup rendah).
FMEA hadir dalam dua tipe dasar.
Bottom up – FMEA ini dimulai dengan mendaftar setiap komponen dalam aset dan mendaftar semua kemungkinan kegagalannya. Ini sering dikenal sebagai 'pendekatan perangkat keras'. Jenis FMEA ini lebih melelahkan tetapi sering digunakan di sektor keselamatan dan konsekuensi lingkungan yang tinggi seperti penerbangan dan nuklir.
Kegagalan aset yang tidak terduga tidak dapat ditoleransi di sektor ini.
Top down – jenis FMEA ini (juga dikenal sebagai 'pendekatan fungsional') lebih umum dan – ya, Anda dapat menebaknya – mempertimbangkan fungsi aset terlebih dahulu. Ketika fungsi diketahui, kami bertanya 'bagaimana bisa gagal secara fungsional?' Ini membawa kita ke mode kegagalan dan mencari efek dan tindakan mitigasi.
FMEA top-down secara langsung hanya membahas kontributor paling penting untuk masalah potensial daripada setiap komponen individu.
Ada juga FMECA (C untuk kekritisan) yang menambahkan faktor risiko numerik.
Lihat contoh ini yang mencakup FMEA dan FMECA.
Kami akan membuatnya tetap sederhana dan mempertimbangkan wiper kaca depan mobil. Kami berasumsi bahwa kami tidak melakukan pemeriksaan apa pun pada awalnya dan kami membiarkannya gagal saat kami mengemudi.
Fungsi | Kegagalan Fungsional | Mode Kegagalan | Potensi Dampak | Keparahan | Potensi Penyebab | Kejadian | Mode Deteksi | Deteksi | RPN |
Apa fungsi dari aset atau komponen? |
Bagaimana ia gagal memenuhi fungsinya? |
Apa yang dapat menyebabkan kegagalan fungsional? |
Apa dampaknya? yaitu efeknya |
Seberapa parah efeknya? |
Apa yang menyebabkan mode kegagalan? |
Seberapa sering hal ini mungkin terjadi? |
Apa kontrol yang ada untuk pencegahan atau deteksi? |
Seberapa mudah untuk mendeteksi menggunakan metode saat ini? |
Nomor prioritas risiko =Sev x Occ x Det. |
Untuk membersihkan hujan dan kabut dari kaca depan (sesuai permintaan). |
Gagal memulai. |
Sekring putus. |
Mobil tidak bisa membersihkan kaca depan saat hujan deras. |
10 |
Puing-puing yang menghalangi wiper (menyebabkan arus berlebih &sekering putus) |
2 |
Temukan kegagalan (saat mengemudi) |
7 |
140 |
Tindakan yang Disarankan | Tanggung jawab | Tanggal Target | Tindakan Diambil | SEV | OCC | DET | RPN |
Bagaimana cara mengurangi kemunculan penyebab atau meningkatkan deteksi? | Siapa yang bertanggung jawab atas tindakan tersebut? | Berapa tanggal target tindakan? | Hitung ulang RPN untuk melihat apakah tindakan telah mengurangi risiko. | | | | RPN baru setelah tindakan. |
1. Periksa wiper kaca depan apakah ada penghalang sebelum setiap perjalanan. 2. Bawa sekering pengganti. | Pemilik mobil | Dengan efek langsung | Daftar periksa yang dibawa di mobil sebagai pengingat. Dan sekering pengganti. | 10 | 2 | 2 | 40 |
Seperti yang Anda lihat, setelah menerapkan tindakan, Nomor Prioritas Risiko Anda akan berkurang.
Setelah Anda melakukan FMEA atau FMECA di pabrik Anda, maka Anda memiliki strategi pemeliharaan.
Strategi pemeliharaan:ini membantu Anda mempertahankan keandalan bawaan.
Jadi, keluaran utama FMEA adalah strategi pemeliharaan, terutama dalam hal apa perlu Anda lakukan. Ini mungkin antara lain penggantian berdasarkan waktu, pemantauan kondisi, desain ulang peralatan, tugas menemukan kegagalan, inspeksi, atau overhaul.
Untuk lebih menyempurnakan - dan kemudian menerapkan - strategi pemeliharaan, Anda perlu memutuskan siapa yang akan melakukan pekerjaan, kapan, dan suku cadang apa yang diperlukan.
Ini yang perlu diingat:
Dengan melakukan perawatan yang tepat pada waktu yang tepat, Anda dapat mempertahankan inheren keandalan aset pada tingkat tinggi. Perawatan yang benar dan tepat saja tidak akan pernah meningkatkan keandalan yang melekat di luar kemampuan awalnya - karena ini adalah bawaan karakteristik.
Tetapi strategi pemeliharaan yang baik dapat menjaga keandalan bawaan tetap tinggi di tempatnya.
Pemantauan Kondisi &Pemeliharaan Berbasis Kondisi:ketersediaan adalah Raja.
Mari kita berkonsentrasi pada taktik pemantauan kondisi (juga dikenal sebagai Pemeliharaan Prediktif) sejenak. Ini bermanfaat karena sensor, data, dan informasinya memungkinkan kami memahami kesehatan aset. Mereka adalah kekuatan pendorong di balik industri internet of things (IIoT) dan industri 4.0.
Jika kami memahami kondisi aset setiap saat, maka kami dapat melakukan perawatan yang paling hemat biaya – perawatan berbasis kondisi (CBM) .
Ini yang perlu diingat:
Pemeliharaan Berbasis Kondisi tidak dan tidak akan meningkatkan keandalan aset , bawaan atau sebaliknya. Hal yang akan diberikannya kepada Anda dan yang sama pentingnya dengan tujuan organisasi Anda adalah ketersediaan aset . Dengan mengurangi waktu henti yang tidak direncanakan saja, Anda meningkatkan ketersediaan.
CBM melakukan tugas perbaikan atau penggantian hanya berdasarkan kesehatan aset yang diukur. Ini memberi kita sinyal peringatan dini tentang potensi atau kegagalan aset atau komponen yang akan datang.
Tetapi jika kita menggunakan teknik pemantauan kondisi, seberapa sering kita harus mengukur data?
Kurva dan Interval P-F
Pertama, apa kurva P-F yang kita bicarakan ini? Ini adalah kurva yang menunjukkan bagaimana kesehatan aset memburuk dari waktu ke waktu setelah mode kegagalan diaktifkan.
Diagram di sini mengilustrasikan konsepnya.
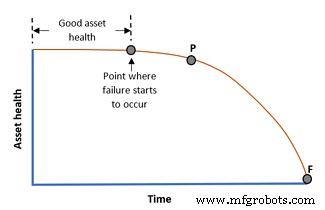
Bagian horizontal dari kurva adalah kesehatan aset yang baik. Bagian ini dapat diperpanjang dengan praktik terbaik pemeliharaan di:
- Pemasangan aset
- Pondasi dan struktur pendukung
- Pelumasan Aset
- Penyelarasan dan Penyeimbangan Aset
- Operasi yang tepat dalam kemampuan aset
Tetapi kemudian, ketika mode kegagalan muncul dengan sendirinya, kami memiliki titik di mana kegagalan telah dimulai. Tapi itu masih tidak terlihat selama pengumpulan data.
Kemudian waktu (atau siklus stres aset) bergerak ke titik P.
Titik P berarti Potensi Kegagalan . Di sinilah teknik pemantauan kondisi kami dapat mulai mendeteksi potensi kegagalan. Kemudian kesehatan aset secara bertahap (atau cepat) menurun hingga mencapai titik F, Kegagalan Fungsional .
Itu artinya selamat malam dan selamat tinggal untuk aset Anda.
Permainan sudah selesai dan Anda perlu memanggil 'pahlawan' pemeliharaan reaktif .
Perbedaan waktu antara P dan F dikenal sebagai interval P-F. Mungkin hitungan detik hingga puluhan tahun. Itu semua tergantung pada mode kegagalan dan aset yang bersangkutan.
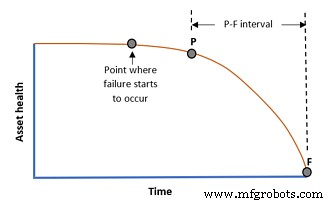
Anda sebaiknya mengingat bahwa interval P-F untuk mode kegagalan tertentu selalu rata-rata angka – hal-hal ini akan selalu memiliki variasi statistik.
Tetapi jika kita memiliki gagasan yang baik tentang apa itu – dari kegagalan masa lalu, RCA (Analisis Akar Penyebab), data OEM, dll. – maka kita dapat mengatur interval di mana kami melakukan inspeksi pemantauan kondisi. Aturan praktis yang baik untuk interval inspeksi biasanya setidaknya setengah dari interval P-F yang diharapkan.
Bayangkan Anda tahu saat bantalan ujung penggerak pompa kritis Anda bergetar pada 8 mm/dtk, kemungkinan hanya tersisa 3 bulan servis sebelum bekerja. Minimal, seberapa sering Anda harus mengukur getaran?
Interval pemeriksaan/pengukuran 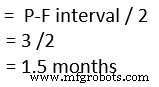
Ini memastikan Anda akan menangkap cacat tertentu dalam interval P-F yang diharapkan (meskipun sebagian besar ahli strategi di sini akan secara konservatif dan umum merekomendasikan interval inspeksi 1 bulan – ingat variasi statistik? ).
Sudah diterima secara luas bahwa teknik pemantauan kondisi yang berbeda dapat memberikan tingkat peringatan dini yang berbeda selama interval P-F. Lihat diagram di bawah ini untuk panduan kasarnya. Tidak ada teknik yang cocok untuk semua mode kegagalan.
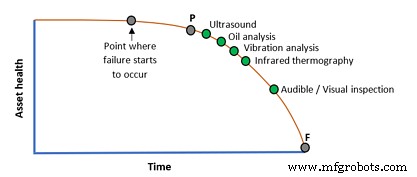
Strategi terbaik memanfaatkan kombinasi teknologi pemantauan kondisi.
Perjalanan menuju pemeliharaan preskriptif
Sebagai catatan terakhir, dengan mempertimbangkan kemajuan IIoT dan industri 4.0, kita harus mempertimbangkan perjalanan menuju pemeliharaan preskriptif.
Pemeliharaan preskriptif (Rx) unik karena alih-alih hanya memprediksi kegagalan yang akan datang, seperti halnya pemeliharaan prediktif (PdM), ia berupaya menghasilkan rekomendasi yang berfokus pada hasil untuk operasi dan pemeliharaan dari analitik Rx. Meskipun RxM masih dalam masa pertumbuhan, banyak pemimpin pemikiran mempertimbangkan potensinya untuk menjadi praktik terbaik keandalan dan pemeliharaan tingkat berikutnya.
www.plantservices.com (Sheila Kennedy) |
'Tapi apa itu ?’ kami mendengar Anda bertanya.
Jadi, batasan berikutnya di luar pemeliharaan prediktif adalah pemeliharaan preskriptif.
Dapatkah Anda bayangkan itu?
Sensor, jaringan, algoritme, pembelajaran mesin, dan penggabungan AI untuk memberi tahu tim pemeliharaan Anda apa yang harus mereka lakukan dan kapan mereka perlu melakukannya untuk menjaga keandalan dan meningkatkan ketersediaan. Atau bahkan bagaimana mengelola aset (kecepatan dan beban) untuk memperpanjang masa manfaat yang tersisa setelah potensi kegagalan terdeteksi.
Strategi pemeliharaan di masa depan akan lancar, dapat diubah, dan diinformasikan secara cerdas oleh teknologi dan FMEA buatan manusia, interval P-F, dan panduan pemecahan masalah OEM.
Kami belum sampai, tapi akan datang...
Baca selanjutnya:Panduan komprehensif untuk IIoT dalam Pemeliharaan