Pengembangan Teknologi Pembuatan Baja Tungku Busur Listrik
Pengembangan Teknologi Pembuatan Baja Tungku Busur Listrik
Pengembangan teknologi pembuatan baja dilakukan untuk memenuhi sejumlah persyaratan. Persyaratan ini dapat diklasifikasikan ke dalam empat kelompok seperti yang diberikan di bawah ini.
- Teknologi ini harus memenuhi persyaratan proses yang diperlukan untuk menghasilkan mutu baja yang berbeda dengan kualitas yang dibutuhkan.
- Teknologi tersebut untuk memenuhi kebutuhan ekonomi yang diperlukan untuk mengendalikan biaya produksi sehingga produk baja yang dihasilkan berdaya saing.
- Teknologi ini untuk memenuhi tingkat emisi yang ditetapkan oleh badan pengatur.
- Teknologi ini memenuhi persyaratan kesehatan dan keselamatan sehingga operator bekerja di area tersebut tanpa bahaya, stres, dan noda.
Untuk memahami tungku busur listrik (EAF), perlu dipahami apa itu busur listrik. Busur listrik adalah bentuk pelepasan listrik antara dua elektroda, dipisahkan oleh celah kecil (biasanya, udara normal). Contoh paling terkenal dari hal ini adalah petir. Siapa pun yang pernah melakukan pengelasan busur juga akrab dengan busur listrik. Jika salah satu menghubungkan benda kerja ke sisi negatif dari sumber listrik DC dan elektroda ke sisi positif, sentuh elektroda sebentar dan tarik agak jauh dari benda kerja, maka busur listrik yang stabil terbentuk antara elektroda dan benda kerja dan panas dari busur ini cukup untuk melelehkan elektroda dan mengelas benda kerja menjadi satu. Ide yang sama digunakan dalam skala yang lebih besar dalam tungku busur listrik.
Sejarah pembuatan baja tanur busur listrik (EAF) tidak terlalu tua. Hanya sedikit lebih dari satu abad ketika tungku pertama ditugaskan untuk melelehkan baja dengan memanfaatkan tenaga listrik. Perkembangan awal teknologi terjadi, karena unit-unit ini memungkinkan untuk dengan mudah mencapai suhu tertinggi dan memastikan kondisi terbaik untuk memproduksi nilai baja paduan dan paduan berkualitas tinggi. Sejak saat itu, kemajuan besar telah dibuat dalam peralatan tungku, teknologi EAF, praktik peleburan, bahan baku, dan produk baja. Kemajuan dalam teknologi EAF telah memungkinkan EAF untuk lebih berhasil bersaing dengan pabrik terintegrasi yang menggunakan teknologi tungku oksigen dasar (BOF) dalam pembuatan baja. Saat ini pembuatan baja EAF memiliki kontribusi besar dalam produksi baja dunia meskipun masih jauh di belakang kontribusi produksi baja yang dibuat oleh teknologi pembuatan baja dominan BOF.
Perkembangan awal
Pada abad ke-19, sejumlah percobaan dilakukan untuk menggunakan busur listrik untuk peleburan besi. Sir Humphry Davy melakukan demonstrasi eksperimental pada tahun 1810, pengelasan diselidiki oleh Pepys pada tahun 1815, Pinchon mencoba membuat tungku elektro-termik pada tahun 1853, dan pada tahun 1878 – 79, Carl Wilhelm Siemens mengeluarkan paten untuk tungku listrik jenis busur.
De Laval telah mematenkan tungku listrik untuk peleburan dan pemurnian besi pada tahun 1892 dan Paul Heroult telah mendemonstrasikan peleburan busur listrik dari paduan ferro antara tahun 1888 dan 1892. Teknologi baru yang muncul digunakan secara komersial pada awal abad kedua puluh ketika berbagai pembangkitan energi listrik yang relatif murah dimulai pada saat itu. Pada tahun 1906, tungku peleburan busur listrik pertama di Amerika Serikat dipasang di pabrik Halcomb. Tungku busur listrik Heroult 'No. 1 Lama' ini sekarang berdiri sebagai monumen bersejarah ASM (American Society for Materials) yang ditunjuk di Station Square di Pittsburgh, Pennsylvania (Gbr 1).
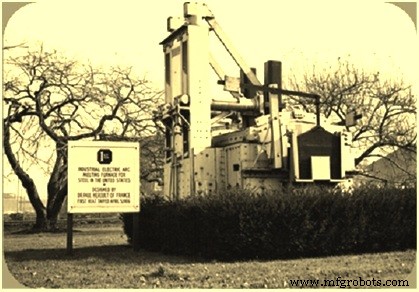
Gbr 1 Tungku busur listrik Heroult pertama
Awalnya, pembuatan baja EAF dikembangkan untuk memproduksi baja dengan grade khusus menggunakan bentuk umpan padat seperti scrap dan paduan besi. Bahan padat pertama-tama dilebur melalui peleburan busur langsung, disempurnakan melalui penambahan fluks yang sesuai dan disadap untuk diproses lebih lanjut. Tungku busur listrik juga digunakan untuk menyiapkan kalsium karbida untuk digunakan dalam gumpalan karbida. Teknologi pembuatan baja EAF kini telah berkembang dari proses lambat ke proses peleburan cepat yang bekerja pada tingkat yang mendekati tingkat produktivitas BOF.
Penampang melintang skema melalui tungku pemurnian busur Heroult ditunjukkan pada Gambar 2. Pada Gambar ini, E adalah elektroda (hanya satu yang ditunjukkan), dinaikkan dan diturunkan oleh drive rak dan pinion R dan S. Bagian dalam dilapisi dengan bata tahan api H, dan K menunjukkan lapisan bawah. Sebuah pintu di A memungkinkan akses ke interior. Cangkang tungku diletakkan di atas rocker agar dapat dimiringkan untuk penyadapan.
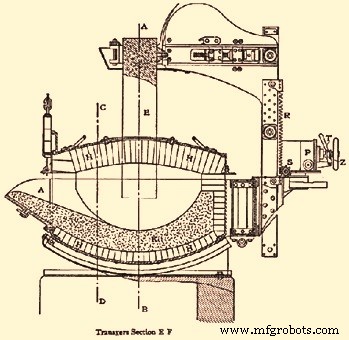
Gbr 2 Tungku pemurnian busur Heroult
Evolusi teknologi pembuatan baja EAF
Sejak EAF industri pertama untuk pembuatan baja mulai beroperasi, perkembangannya pesat dan ada peningkatan produksi sepuluh kali lipat dari tahun 1910 hingga 1920, dengan lebih dari 500.000 ton baja diproduksi oleh EAF pada tahun 1920, meskipun ini hanya mewakili persentase yang sangat kecil dari produksi baja global pada waktu itu. Tungku generasi pertama memiliki kapasitas antara 1 ton dan 15 ton. EAF memiliki konverter Bessemer/Thomas dan tungku Siemens Martin (perapian terbuka) sebagai pesaing kuat, pada awalnya. Tapi ceruknya adalah produksi baja khusus yang membutuhkan suhu tinggi, peleburan paduan besi, dan waktu pemurnian yang lama.
EAF adalah fase default dalam proses pembuatan baja. Selama bertahun-tahun EAF telah berkembang secara dinamis dan mengadopsi metode yang efisien, kompetitif dan berkelanjutan dalam proses dan output baja global dari EAF meningkat. Banyak negara yang tidak dapat membuat besi dengan jalur tradisional, yaitu jalur BF-BOF) mengadaptasi jalur pembuatan baja EAF. Salah satu alasan utama negara-negara ini untuk mengadaptasi rute pembuatan baja EAF adalah tidak tersedianya batu bara kokas dan mudahnya ketersediaan listrik berbiaya rendah karena aksesibilitas bahan bakar yang murah. Pabrik baja yang menggunakan teknologi EAF untuk produksi baja dikenal sebagai pabrik mini dan industri ini merupakan pendaur ulang skrap baja terbesar.
Sementara EAF secara luas digunakan dalam Perang Dunia II untuk produksi baja paduan, baru kemudian pembuatan baja listrik mulai berkembang. Biaya modal yang rendah untuk pabrik mini memungkinkan pabrik didirikan dengan cepat dalam skenario global yang dilanda perang, dan juga memungkinkan mereka untuk berhasil bersaing dengan pembuat baja besar untuk 'produk panjang' baja karbon berbiaya rendah (baja struktural, batang dan batang, dan batang kawat) di pasaran.
Ketika Nucor, sekarang salah satu produsen baja terbesar di AS memutuskan untuk memasuki pasar produk lama pada tahun 1969, mereka memilih untuk memulai pabrik mini, dengan EAF sebagai tungku pembuatan bajanya, segera diikuti oleh produsen lain. Sementara Nucor berkembang pesat di Amerika Serikat bagian timur, organisasi yang mengikuti mereka ke operasi pabrik mini terkonsentrasi di pasar lokal untuk produk lama, di mana penggunaan EAF memungkinkan pabrik untuk memvariasikan produksi sesuai dengan permintaan lokal. Pola ini juga diikuti secara global, dengan produksi baja EAF terutama digunakan untuk produk panjang, sedangkan pabrik terintegrasi, menggunakan rute produksi BF – BOF, terkonsentrasi pada pasar untuk 'produk datar' (lembaran baja, strip, dan pelat baja yang lebih berat, dll. .). Pada tahun 1987, Nucor membuat keputusan untuk memperluas ke pasar produk datar, masih menggunakan metode produksi EAF.
Peningkatan produksi dan teknologi EAF di seluruh dunia disebabkan oleh alasan berikut.
- Penghentian proses perapian terbuka sebagai proses pembuatan baja yang kompetitif.
- Keinginan untuk beralih dari modal besar dan biaya operasi yang terkait dengan pembuatan baja terintegrasi skala besar menuju pabrik baja mini yang lebih kecil dan kurang padat modal.
- Peningkatan yang sangat cepat dalam teknologi kelistrikan, menurunkan biaya peralatan listrik skala besar dan juga memungkinkan kontrol perangkat listrik yang jauh lebih baik.
- Tersedianya skrap di banyak negara dikombinasikan dengan tekanan sosial yang kuat terhadap daur ulang logam.
- Meningkatnya ketersediaan sumber zat besi alternatif, terutama dari negara berkembang.
- Penggunaan logam panas dan bahan bakar oxy di tungku busur listrik
- Peningkatan besar dalam operasi, kontrol, efisiensi, dan kualitas produk dari teknologi pembuatan baja berbasis EAF.
Pertumbuhan dalam pembuatan baja EAF telah disertai dengan beberapa peningkatan teknologi yang memungkinkan penurunan besar dalam kebutuhan daya dan peningkatan efisiensi energi, produktivitas tungku dan lingkungan kerja di bengkel peleburan baja. Peningkatan teknologi ini telah memberikan beberapa keuntungan pada operasi EAF yang mencakup antara lain, operasi busur listrik yang stabil, konsumsi energi yang rendah, konsumsi elektroda yang rendah, kerusakan elektroda yang lebih sedikit, gaya yang diterapkan pada elektroda dan lengan bantalan elektroda yang lebih rendah, dan gangguan jaringan yang lebih rendah.
Proses pembuatan baja EAF hanya bergantung pada daya listrik sampai energi kimia berubah sebagai tambahan untuk mengurangi biaya konversi melalui peningkatan produktivitas EAF. Namun, pengelolaan energi listrik dan kimia yang efisien adalah dengan menggabungkan kontrol dinamis busur listrik yang efisien dengan injeksi oksigen dan karbon yang seimbang untuk meningkatkan produktivitas EAF. Pabrik EAF sering menggunakan campuran besi tereduksi langsung (DRI) / besi briket panas (HBI) / DRI panas dan umpan baja daur ulang dan bahan berbasis karbon sebagai agen pembusa terak dan sebagai karburator. Sesuai persyaratan pengurangan konsumsi energi dan emisi gas rumah kaca, antrasit tradisional dan kokas metalurgi diganti dengan bahan berbasis karbon dan sekarang sumber karbon alternatif seperti ban karet akhir masa pakai dan plastik daur ulang juga sebagian menggantikan bahan karbon konvensional.
Peningkatan dalam desain EAF
Banyak peningkatan teknologi dalam desain EAF dibuat untuk mengurangi waktu ketuk-ke-tap. Peningkatan ini termasuk yang berikut.
- Tungku busur listrik dengan desain daya ultra tinggi (UHP), dengan tegangan sekunder tinggi dan busur lebih panjang. Inovasi ini memainkan peran yang menentukan dalam mempersingkat waktu tap to tap secara tajam dan meningkatkan produktivitas EAF per jam. Tungku UHP pertama dipasang di Amerika Serikat pada tahun 1963. Tungku 135 ton ini dilengkapi dengan trafo 70-80 MVA yang berarti daya spesifik sebesar 520-600 kVA/ton. Karena operasinya yang sukses, tungku UHP menjadi populer dengan cepat dan daya spesifiknya juga ditingkatkan menjadi 1000 kVA/ton.
- Lengan elektroda penghantar arus tinggi dalam desain kotak berlapis tembaga.
- Sistem kontrol elektroda tercanggih.
- berbagai bukaan di tungku untuk penggunaan sumber energi alternatif secara ekstensif
- Desain konstruksi berat untuk mempertahankan kondisi kerja keras yang memungkinkan pergerakan sangat cepat dan pengoperasian yang aman.
- Desain cangkang terpisah dari EAF untuk kemudahan perawatan dan pengurangan waktu perawatan.
- Panel pendingin tembaga atau kombinasi dengan aliran air pendingin berkecepatan tinggi.
- Sistem pengumpanan kontinu untuk DRI/HBI/DRI panas menghasilkan pengurangan waktu pengisian tungku.
- Lebih banyak masukan panas di area EBT (penyadapan bawah eksentrik) dingin karena desain khusus sistem burner EBT.
- Fleksibilitas tinggi dan efisiensi tinggi operasi tungku dengan aplikasi pintu terak tertutup.
- Pengoperasian perawatan yang mudah untuk desain khusus seperti sistem pengangkatan atap, sistem penguncian tungku.
- Masukan energi kimia tambahan berbasis karbon, bahan bakar dan oksigen yang digunakan sebagai pengganti tenaga listrik.
- Desain regulasi untuk elektroda – Biasanya, rakitan elektroda / lengan / tiang / kabel memiliki berat dalam kisaran 20 ton. Ini dipindahkan secara vertikal untuk tujuan kontrol oleh silinder hidrolik yang tergabung dalam tiang. Karena panjang busur bergantung, antara lain, pada tingkat sisa atau cairan yang terus berubah di bawah elektroda, maka diperlukan kontrol otomatis atas posisi elektroda (sistem pengaturan). Sistem regulasi mempengaruhi banyak aspek penting dari kinerja tungku, seperti masukan energi, arus rata-rata, stabilitas busur, pola peleburan skrap, kehilangan energi pada panel berpendingin air, energi, elektroda, dan konsumsi refraktori. Semua parameter ini saling terkait secara kompleks dan ada banyak perbedaan pendapat tentang strategi pengendalian yang 'optimal'.
- Mencapai keseimbangan energi dan termal yang lebih baik di dalam tungku karena injeksi multiunit.
Perkembangan besar dalam teknologi EAF
Beberapa peningkatan teknologi utama selama empat puluh tahun terakhir diberikan di bawah ini.
- Praktek terak berbusa – Dalam pembuatan baja EAF, pencairan skrap secara progresif meningkatkan perpindahan panas iradiatif dari busur ke dinding samping tungku. Dengan menutupi busur di lapisan terak, busur terlindung dan lebih banyak energi ditransfer ke bak mandi. Terak berbusa selama periode ini bermanfaat. Efektivitas pembusaan terak tergantung pada kebasaan terak, kandungan FeO terak, suhu terak dan ketersediaan karbon untuk bereaksi dengan oksigen atau FeO terak. Terak berbusa mengurangi kerusakan refraktori dan kehilangan panas dari daerah busur. Penghematan energi bersih diperkirakan mencapai 6-8 kWh/ton baja.
- Meniup oksigen dalam lelehan – Meniup oksigen dalam baja cair melepaskan panas, karena reaksi oksigen dengan karbon, silikon, besi dalam logam cair bersifat eksotermis dan menghasilkan panas. Pada kondisi ini, waktu peleburan berkurang dan produktivitas meningkat. Karena pelepasan panas, konsumsi listrik berkurang serta konsumsi elektroda seiring dengan konsumsi refraktori. Di masa lalu, ketika konsumsi oksigen kurang dari 10 cu m per ton baja biasa terjadi, operasi lancing dilakukan secara manual menggunakan tombak pipa habis pakai. Sebagian besar operasi modern sekarang menggunakan tombak otomatis dan sebagian besar fasilitas sekarang menggunakan tombak berpendingin air yang tidak dapat dikonsumsi untuk menyuntikkan oksigen ke dalam baja. Banyak dari tombak ini juga memiliki kemampuan untuk menyuntikkan karbon.
- Pengoperasian tumit panas – Dalam pengoperasian tumit panas, sekitar 15% hingga 20% logam dan sejumlah terak tertinggal di dasar tungku setelah setiap penyadapan. Sisa terak dikeluarkan dari tungku di atas ambang jendela. Ini membantu dalam pelelehan umpan padat segar yang memasuki tungku dan memungkinkan penyadapan bebas terak secara praktis. Pengoperasian tumit panas menghasilkan penghematan paduan besi dan efisiensi energi.
- Penyadapan bawah eksentrik – Penyadapan bawah eksentrik (EBT) mengurangi waktu ketukan, kehilangan suhu, dan terbawanya terak ke dalam ladle. Penghematan listrik 12-15 kWh/ton baja diperkirakan dengan menggunakan teknologi ini. Hasil penyadapan bebas terak EBT menjadi aditif paduan hasil tinggi dan masa pakai refraktori sendok yang tinggi.
- Praktek pasca pembakaran – Gas karbon mono oksida (CO) yang dihasilkan selama dekarburisasi dibakar dengan injeksi oksigen dari tombak di dalam tungku. Energi yang dibebaskan digunakan untuk memanaskan bak mandi secara langsung atau memanaskan bahan umpan yang masuk. Sistem kontrol pasca pembakaran khusus yang dipasang di dua pabrik di Meksiko dan Amerika Serikat menghasilkan pengurangan masing-masing 2% dan 4% dalam konsumsi listrik, 8% dan 16% dalam konsumsi gas alam, 5% dan 16% dalam penggunaan oksigen, dan 18% dan 18% karbon diisi dan disuntikkan.
- Injeksi karbon – Injeksi karbon membawa manfaat dari (i) untuk praktik skrap 100% atau ketika kandungan karbon dalam bak tidak cukup untuk menghasilkan gas CO untuk pembusaan terak, injeksi karbon bermanfaat, dan (ii) menghasilkan oksidasi karbon Gas CO yang pada pasca pembakaran menghasilkan energi panas. Perlu dicatat bahwa injeksi karbon memerlukan injeksi oksigen untuk memulai oksidasi karbon.
- Pemantauan dan kontrol gas buang – Tingkat pemulihan energi kimia dari gas buang dapat ditingkatkan sebesar 50% dengan menyesuaikan tingkat injeksi oksigen untuk pasca pembakaran berdasarkan pembacaan CO dan CO2 waktu nyata dalam gas buang, alih-alih menggunakan nilai yang telah ditetapkan sebelumnya. Penghematan listrik 12-15 kWh/ton baja diperkirakan dengan menggunakan teknologi ini.
- Oxy fuel burner – Oxy-fuel burner/lancing dapat dipasang di EAF untuk mengurangi konsumsi listrik dengan mengganti listrik dengan oksigen dan bahan bakar hidrokarbon. Teknologi ini telah diperkenalkan untuk meningkatkan laju leleh dan untuk memberikan distribusi panas yang lebih merata di seluruh tungku. Ini mengurangi konsumsi energi total karena pengurangan waktu panas, meningkatkan perpindahan panas selama periode pemurnian, dan memfasilitasi pembusaan terak, yang meningkatkan efisiensi penggunaan oksigen dan karbon yang disuntikkan. Penggunaan pembakar oxy-fuel harus hati-hati, jika tidak, ada risiko peningkatan konsumsi energi total dan pembangkitan gas rumah kaca. Energi 2-3 kWh/ton baja dapat dihemat untuk setiap menit waktu pemanasan yang dikurangi. Penghematan listrik 35-40 kWh/ton baja dapat dicapai dengan laju injeksi oksigen tipikal 18 N cum /ton baja.
- Pemanasan awal skrap – Sejumlah sistem pemanasan awal skrap yang memanfaatkan panas yang terkait dengan gas lepas telah dikembangkan, beberapa didasarkan pada sistem ember batch dan lainnya pada sistem poros kontinu. Dengan sistem poros tunggal hingga 77 kWh/ton baja energi listrik dapat dihemat. Sistem poros jari memungkinkan penghematan hingga 110 kWh/ton baja, yang merupakan sekitar 25% dari input listrik.
- Penghapusan sumber radiasi di skrap yang bertanggung jawab – skrap yang dibeli harus menjalani deteksi radiasi untuk menghindari baja yang diproduksi menjadi rawan radiasi. Semua skrap yang masuk ke fasilitas harus melewati peralatan deteksi 'Exploranium'. Memo yang ditandai sebagai berisiko tinggi menjalani pemindaian tambahan dari detektor tangan. Pemindaian kedua dengan peralatan deteksi 'Exploranium' dilakukan sebelum pengiriman di toko lelehan dan pemindaian terakhir dilakukan pada setiap beban magnet saat ember pengisian diisi. Detektor bag house EAF menentukan kapan, jika ada, bahan radioaktif telah meleleh.
- Pengisian DRI panas- Pengisian DRI panas pada suhu hingga 600 derajat C daripada DRI dingin menghasilkan pengurangan energi leleh 150 kWh/ton baja. Manfaat lainnya adalah peningkatan produktivitas, penurunan kandungan elemen tramp, peningkatan pembusaan terak, dan peningkatan kandungan karbon dalam muatan.
- Pengisian logam panas – Pengisian logam panas di EAF bersama dengan injeksi oksigen mengurangi konsumsi energi listrik karena pemanfaatan energi kimia. Hal ini mengurangi waktu ketuk untuk mengetuk, konsumsi karbon, dan konsumsi listrik.
- Transformator daya ultra tinggi – Penghematan listrik diperkirakan sebesar 1,1 kWh/ton baja untuk setiap peningkatan daya MW. Konsumsi daya turun masing-masing sebesar 11 kWh/t dan 22 kWh/t untuk 2 saluran tungku saat tegangan pengoperasian meningkat dari 600 V menjadi 660 V dalam satu tungku dan dari 400 V menjadi 538 V di tungku lain.
- Listrik tungku – Peningkatan besar dalam kontrol dan efisiensi energi telah dicapai karena pengembangan pasokan listrik dengan tegangan operasi yang lebih tinggi.
- Kontrol tungku -Teknologi ini menghasilkan pengurangan konsumsi listrik sebesar 14%. Selain itu, pengurangan konsumsi gas alam sebesar 6% dapat dicapai secara bersamaan.
- Kontrol proses yang ditingkatkan ( jaringan saraf) – Kontrol proses yang ditingkatkan (jaringan saraf) dapat membantu mengurangi konsumsi listrik di luar yang dicapai melalui sistem kontrol klasik. Misalnya, jaringan saraf atau sistem 'logika fuzzy' menganalisis data dan meniru pengontrol terbaik. Untuk EAF, sistem kontrol 'logika fuzzy' pertama telah dikembangkan menggunakan faktor daya saat ini dan penggunaan daya untuk mengontrol elektroda di bak mandi. Penghematan listrik sebesar 30 kWh/ton baja diperkirakan dapat dicapai, dan nilainya dapat berubah berdasarkan karakteristik skrap dan tungku.
- Injeksi gas pengadukan/pengadukan bawah – Dalam tungku busur konvensional ada sedikit turbulensi listrik alami di dalam bak. Karena tidak adanya pengadukan, potongan besar dapat membutuhkan waktu lama untuk meleleh dan mungkin memerlukan oksigen lancing. Pengadukan argon atau nitrogen menghilangkan gradien suhu dan konsentrasi, mempersingkat waktu ketuk-ke-tap, mengurangi refraktori, elektroda dan konsumsi daya, dan meningkatkan hasil besi dan paduan. Dengan diperkenalkannya teknologi pengadukan di bak mandi, ada penghematan listrik. Penghematan listrik ini dapat bervariasi antara 12 hingga 24 kWh per ton baja.
- Tungku busur arus searah – Tungku busur arus searah (DC) mewakili konsep yang berbeda dalam desain tungku busur. Kebanyakan tungku DC dengan elektroda tunggal di mana arus mengalir dari elektroda karbon ke anoda dipasang di bagian bawah tungku. Pengurangan konsumsi elektroda dari urutan 50% sampai 60% adalah keuntungan utama dari tungku DC dibandingkan dengan tungku busur tiga fase konvensional. Tingkat kebisingan untuk tungku DC lebih rendah. Biaya perawatan yang lebih rendah diklaim dan biaya refraktori lebih sedikit untuk dinding samping tetapi lebih untuk bagian bawah tungku. Tungku busur DC memerlukan penambahan elektroda bawah (anoda), reaktor DC, dan thyristor yang semuanya menambah biaya tungku DC. Tungku DC terlepas dari konsumsi energi dan elektrodanya yang rendah memastikan homogenisasi termal dan metalurgi yang sangat baik dari baja cair. Juga ada efek pengadukan yang meningkat dari busur arus searah yang mendukung proses ini. Dibandingkan dengan tungku busur listrik AC, tungku DC menyebabkan lebih sedikit gangguan jaringan dan karenanya dapat dihubungkan bahkan ke jaringan listrik yang lemah. Penghematan energi bersih dibandingkan tungku AC lama diperkirakan 85-90 kWh/ton baja. Dibandingkan dengan tungku AC baru, penghematannya terbatas pada 10 -20 kWh/ton baja.
- Pemulihan panas limbah untuk EAF – Untuk peleburan EAF 150 t/pengisian DRI dengan waktu ketuk-ke-tap 49 menit dan waktu penyalaan 40 menit, sekitar 130 kWh/ton energi baja dapat diperoleh kembali ( efisiensi 30%). Jika energi yang dipulihkan digunakan untuk pembangkit listrik dengan uap jenuh 2,8 MWh/tahun listrik dapat dihasilkan. Jika energi yang diperoleh kembali digunakan untuk pembangkit listrik dengan uap super panas, energi 15,1 MWh/tahun dapat dihasilkan.
- Drive frekuensi variabel atau drive kecepatan yang dapat disesuaikan – Total konsumsi energi kipas dapat dikurangi hingga 67%. Penghematan listrik diperkirakan mencapai 16,5 kWh per ton baja.
- Tungku busur DC cangkang kembar – Dapat menghasilkan penghematan listrik sebesar 15 -20 kWh/ton baja.
- Tungku CONARC- Tungku ini menggabungkan keunggulan teknologi tungku busur listrik dengan proses blowing konvensional. CONARC mencerminkan kombinasi CONverter dan ARCing. Prosesnya dibagi menjadi dua fase. Fase konverter yang melibatkan peniupan oksigen ke lelehan melalui tombak atas untuk mendekarburasinya dan fase tungku busur listrik di mana tenaga listrik diterapkan untuk melelehkan bahan padat dan memanaskan bak mandi terlalu panas hingga suhu penyadapan.
- Teknologi injeksi polimer – Ini adalah proses paten baru yang menarik, yang menggantikan sebagian penggunaan kokas dengan polimer, termasuk karet (ban bekas), sebagai injektor karbon alternatif untuk menghasilkan terak berbusa dalam pembuatan baja EAF. Manfaatnya antara lain (i) pengurangan konsumsi energi listrik spesifik sekitar 3%, (ii) pengurangan injektor karbon sekitar 12%, (iii) peningkatan produktivitas tungku (ton per menit) sebesar 4%, (iv) kadar terak FeO dipertahankan dalam kisaran yang disyaratkan, dan (v) pengurangan tingkat emisi untuk NOx, CO, dan SO2.
EAF dengan ban karet dan plastik
Sebuah studi yang dilakukan oleh One Steel's Sydney Steel Mill bekerja sama dengan UNSW dalam pengujian laboratorium tentang penggunaan ban karet dalam pembuatan baja EAF untuk optimalisasi terak berbusa telah mengembangkan dan mengkomersialkan sistem rekayasa melalui uji coba pabrik untuk EAF untuk menyuntikkan campuran karet dari ban yang habis masa pakainya. dan kokas menjadi EAF sebagai bahan pembusa terak. Metode tersebut menghasilkan manfaat seperti, peningkatan volume dan busa terak termasuk peningkatan efisiensi energi listrik karena busur yang lebih panjang dan peningkatan perpindahan panas dari busur ke baja, serta penurunan kehilangan panas melalui terak dan dinding samping. Sementara, pembuat baja EAF yang menggunakan teknologi injeksi polimer (PIT) juga dapat mengharapkan untuk melihat peningkatan hasil, konsumsi oksigen injeksi, konsumsi refraktori dan elektroda, dan keausan sistem injeksi. Teknologi injeksi karet (RIT) telah menjadi proses standar di One Steel's Sydney dan Laverton EAF Steel Mills dan telah mencapai tonggak penting dengan 40.720 panas yang disadap dengan injeksi karet, 13.721 ton kokas berkurang karena – tersubstitusi dan pengurangan injeksi karena Kontrol FeO dan ukuran yang konsisten, dan 1.128.486 ban penumpang setara yang digunakan. Baja hijau yang dihasilkan dari ban karet dan plastik bekas tidak menghasilkan limbah atau asap beracun.