Proses Rotary Kiln Pengurangan Langsung Berbasis Batubara
Proses Rotary Kiln Pengurangan Langsung Berbasis Batubara
Proses rotary kiln reduksi langsung berbasis batubara dikembangkan untuk mengubah bijih besi secara langsung menjadi besi metalik tanpa peleburan material. Proses ini memiliki keuntungan dari pengeluaran modal yang rendah dan tidak memerlukan batubara kokas. Besi metalik dalam proses ini diproduksi dengan reduksi oksida besi di bawah suhu fusi bijih besi (1535 derajat C) dengan memanfaatkan bahan karbon yang ada dalam batubara non-coking. Karena bijih besi bersentuhan langsung dengan zat pereduksi selama proses reduksi, ini sering disebut sebagai besi tereduksi langsung (DRI). Produk tereduksi yang memiliki tingkat metalisasi tinggi menunjukkan 'struktur sarang lebah', karena itu sering disebut besi spons.
Pembangkit DRI berbasis batubara fleksibel terhadap lokasi pembangkit karena batubara non-coking tersebar luas dalam deposit besar dan mudah diangkut. Sebagian besar pabrik menggunakan proses reduksi yang dilakukan dalam rotary kiln. Pabrik-pabrik ini menggunakan berbagai bahan baku dan batubara non-coking. Kualitas bahan-bahan ini memiliki pengaruh langsung pada proses serta produk. Beberapa tanaman tidak menggunakan bijih besi secara langsung. Tanaman ini menggunakan pelet bijih besi di rotary kiln. Campuran bahan baku yang terdiri dari bijih besi, dolomit dan batubara non-coklat diumpankan di salah satu ujung rotary kiln dan dipanaskan oleh pembakar batubara untuk menghasilkan DRI. Produk DRI bersama dengan char (kadang-kadang disebut dolo char) dikeluarkan dari ujung kiln yang lain. Selain itu, udara primer dan udara sekunder dipasok ke kiln untuk memulai pembakaran dan mempertahankan proses reaksi di kiln.
Bahan mentah
Bahan baku utama untuk produksi DRI dengan proses rotary kiln adalah (i) bijih besi gradasi ukuran atau pelet bijih besi, (ii) batubara non-coking, dan (iii) dolomit dalam jumlah kecil untuk mengais belerang.
Bijih besi dengan kualitas yang tepat merupakan input dasar untuk proses reduksi langsung berbasis batubara. Sebagian besar pabrik reduksi langsung berbasis batubara menggunakan bijih besi lump. Persyaratan kualitas utama adalah (i) kandungan Fe tinggi dengan sedikit gangue dan elemen merusak seperti fosfor dan belerang, (ii) sifat penanganan yang baik (indeks gelas dan indeks abrasi), (iii) dikalibrasi dengan ukuran dengan butiran yang lebih sedikit, (iv) tinggi reducibility, (v) decrepitation rendah selama reduksi, dan (vi) kompatibilitas yang baik dengan batubara reduktor yang digunakan.
Persyaratan mutu bijih besi berukuran memenuhi persyaratan fisik, metalurgi, dan kimia. Persyaratan fisik adalah kekuatan dan granulometri. Bijihnya harus keras, dan memiliki kekuatan tinggi. Kekuatan tumbler optimum dari bijih harus minimal 90%. Tergantung pada reducibility, bijih dikalibrasi dalam kisaran ukuran 5 mm sampai 20 mm umumnya digunakan. Persyaratan metalurgi bijih termasuk reducibility tinggi, stabilitas termal, dan kecenderungan rendah untuk menempel dan disintegrasi selama pemanasan dan reduksi. Persyaratan kimia bijih merupakan karakteristik penting karena selain penghilangan oksigen, tidak ada perubahan kimia lain yang terjadi selama proses reduksi langsung. Bahan gangue di DRI, yang berasal dari bijih besi, yaitu silika dan alumina bersama dengan kandungan belerang dan fosfor mempengaruhi ekonomi dalam operasi pembuatan baja selanjutnya. Oleh karena itu, bijih harus tinggi kandungan besi dan rendah gangue. Spesifikasi fisik dan kimia bijih yang diinginkan adalah sebagai berikut.
Ukuran – 5 mm -20 mm
Oversize dan undersize – masing-masing maksimal kurang dari 5%
Indeks Tumbler – lebih dari 90%
Kontaminasi (laterit dll.) – kurang dari 5%
Total Fe – minimum 65%
Silika – kurang dari 3%
Silika + alumina – maksimum 5%
Sulfur – maksimum 0,01%
Fosfor – maksimum 0,05%
Kelembaban – maksimum 1%
Batubara non-coking yang digunakan dalam rotary kiln memiliki peran ganda. Ini memasok panas untuk proses dan juga bertindak sebagai agen pereduksi. Persyaratan kualitas utama dari batubara non-coking adalah (i) karakteristik non-coking, (ii) kadar abu rendah, (iii) kadar sulfur rendah, (iv) reaktivitas yang baik, (v) suhu fusi abu yang tinggi, dan (vi ) bahan volatil sedang. Karakter non-coking dari batubara diperlukan karena reaksi kokas menyebabkan pembentukan cincin di dalam kiln. Batas indeks caking yang diperbolehkan secara praktis untuk proses rotary kiln adalah maksimal 3 buah. Kadar abu batubara yang rendah diperlukan karena kadar abu yang tinggi menyebabkan penggunaan volume kiln yang tersedia untuk reduksi menjadi kurang dimanfaatkan. Ini juga meningkatkan konsumsi karbon tetap karena energi tambahan dikonsumsi dalam memanaskan massa abu inert ke suhu reaksi. Kadar abu maksimum 20% adalah batas praktis untuk operasi yang efisien. Kandungan belerang yang rendah diperlukan untuk mengontrol belerang dalam DRI. Sulfur dalam batubara harus maksimum 0,01%. Reaktivitas batubara yang baik diperlukan karena langkah penting dalam proses reduksi solid state adalah reaksi maju, dimana karbon dioksida yang dihasilkan dari pembakaran batubara bereaksi dengan batubara untuk meregenerasi karbon monoksida (reaksi Boudouard). Oleh karena itu, batubara harus memiliki reaktivitas yang cukup sehingga reaksi Boudouard berlangsung pada laju yang diinginkan. Batubara bituminous dan sub-bituminous biasanya menunjukkan reaktivitas yang baik yang cocok untuk produksi DRI. Suhu fusi abu adalah karakteristik penting lainnya. Batubara yang memiliki suhu fusi abu yang rendah menyebabkan massa lengket yang mengakibatkan operasi kiln tidak stabil karena pembentukan akresi di dalam kiln yang mengurangi laju reduksi dengan pembentukan lapisan terak di permukaan bijih. Oleh karena itu batubara dengan suhu fusi abu lebih tinggi dari 1400 derajat C diinginkan untuk operasi tanur putar. Volatile matter dari batubara harus optimal untuk proses rotary kiln berbasis batubara. Batubara dengan bahan volatil yang sangat rendah menghasilkan reaktivitas arang yang sangat rendah, dan dengan demikian menimbulkan produk logam yang buruk. Batubara volatil yang sangat tinggi, meskipun menghasilkan arang yang sangat reaktif, juga tidak disukai karena meningkatkan volume gas di kiln. Biasanya untuk proses tanur putar, zat yang mudah menguap berada dalam kisaran 25% hingga 30%. Batubara untuk reduksi langsung di rotary kiln harus memiliki indeks pengembangan yang rendah. Biasanya indeks pembengkakan kurang dari 1. Spesifikasi fisik dan kimia dari batubara non-coking adalah sebagai berikut.
Ukuran gumpalan – 5 mm hingga 20 mm
Ukuran denda – kurang dari 5 mm
Kontaminasi (serpih, batu, dll.) – kurang dari 3%
Karbon tetap – minimum 45%
Materi yang mudah menguap – 25% hingga 30%
Abu – maksimum 20%
Kelembaban – maksimum 8%
Dolomit digunakan untuk desulfurisasi dalam proses produksi DRI. Spesifikasi khas dolomit diberikan di bawah ini.
MgO – minimum 22 %
CaO – maksimum 28%
LOI – saldo
Reaksi kimia
Reaksi kimia berlangsung di dalam rotary kiln. Penampang kiln putar ada di Gambar 1.
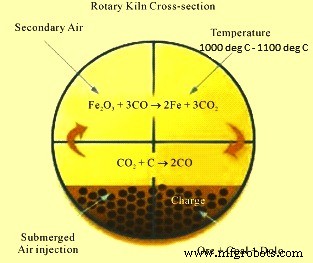
Gbr 1 Penampang rotary kiln
Proses reduksi langsung berbasis batubara didasarkan pada zat pereduksi padat yaitu batubara non-coking. Reaksi berlangsung pada suhu tinggi (1000 derajat C sampai 1100 derajat C). Batubara memainkan peran ganda dalam kiln. Sebagian batubara digunakan sebagai bahan bakar untuk memasok panas yang diinginkan sehingga dapat membawa bahan baku ke suhu yang diinginkan. Namun peran utama batubara adalah sebagai pemasok karbon untuk proses reduksi. Dolomit digunakan sebagai pemulung belerang yang akhirnya keluar bersama arang. Char mengandung abu batubara dan kotoran lain dari bijih besi. Reaksi di dalam kiln berlangsung dalam beberapa tahap selama reduksi bijih besi menjadi DRI. Bijih besi mengalami reaksi reduksi akhir berikut.
Fe2O3 + 3CO =2 Fe + 3CO2
Reaksi menunjukkan bahwa karbon monoksida (CO) adalah gas pereduksi yang diperoleh dengan pembakaran batubara yang terkontrol, menurut reaksi Boudouard seperti yang diberikan di bawah ini.
C + O2 =CO2
C + CO2 =2CO
Karbon monoksida yang dihasilkan seperti di atas mereduksi oksida besi dari bijih besi menjadi besi metalik sesuai dengan reaksi yang diberikan di atas. Namun, reduksi dari oksida menjadi logam tidak terjadi dalam satu langkah, tetapi dengan penghilangan bertahap pemberian oksigen, menimbulkan berbagai oksida antara. Urutan reduksi dapat dinyatakan sebagai Fe2O3 menjadi Fe3O4 menjadi FeO menjadi Fe.
Reaksi yang terjadi di dalam lapisan bijih besi dan batubara bersifat heterogen. Dua set reaksi berlangsung. Set pertama reaksi terjadi antara batubara, karbon dioksida dan oksigen sedangkan di set kedua reaksi antara partikel bijih besi dan CO. Karena oksigen dari bijih besi dihilangkan sebagai CO2, pelepasan gas CO2 membuat produk DRI berpori. Reaksi antara partikel bijih dan reduktor gas dapat divisualisasikan terjadi dalam lima tahap berturut-turut berikut.
- Tahap 1 – Pada tahap ini difusi gas reaktan terjadi melalui film yang mengelilingi partikel bijih ke permukaan padatan.
- Tahap 2 – Pada tahap ini, penetrasi dan difusi reaktan melalui selimut lapisan luar yang bereaksi terjadi ke permukaan inti yang tidak bereaksi.
- Tahap 3 – Pada tahap ini, reaksi reaktan gas terjadi dengan padatan di permukaan reaksi.
- Tahap 4 – Pada tahap ini difusi produk gas terjadi melalui lapisan yang bereaksi ke permukaan luar padatan.
- Tahap 5 – Pada tahap ini difusi produk gas melalui film gas kembali ke badan utama gas.
Karena reaksi berlangsung dalam beberapa tahap dan setiap tahap berturut-turut, tahap dengan laju paling sedikit mengontrol laju reaksi. Laju difusi dan laju reaksi terutama merupakan fungsi dari tiga parameter yaitu (i) konsentrasi reaktan, (ii) suhu antarmuka aktif, dan (iii) area aktif reaksi.
Proses reduksi langsung
Proses reduksi langsung dilakukan dalam rotary kiln dimana temperatur operasi dijaga pada kisaran 1.000 derajat C sampai 1.100 derajat C. Produk dari kiln (DRI dan campuran arang) kemudian didinginkan dalam rotary cooler dengan eksternal sistem pendingin air. Produk kiln disaring dan dipisahkan secara magnetis. DRI yang bersifat magnetis tertarik dan terpisah dari arang non-magnetik.
Bijih besi dan batubara yang dihancurkan dan disaring ke ukuran masing-masing diumpankan ke rotary kiln melalui tabung umpan dalam rasio yang telah ditentukan. Rotary kiln sedikit miring pada sudut 2,5 derajat dan diputar oleh motor kecepatan variabel AC pada kecepatan variabel mulai dari 0,2 rpm (putaran per menit) hingga 1,0 rpm. Karena kemiringan dan gerakan putar kiln, material berpindah dari ujung umpan ke ujung pembuangan kiln dalam waktu sekitar 7 jam hingga 8 jam.
Denda batubara dihembuskan dari ujung pembuangan untuk mempertahankan suhu yang diperlukan dan konsentrasi karbon di lapisan. Kiln memiliki beberapa kipas udara shell yang dipasang di bagian atas yang meniupkan udara di zona masing-masing untuk mempertahankan profil suhu yang diperlukan. Material dan gas panas bergerak berlawanan arah, akibatnya bijih besi dipanaskan terlebih dahulu dan secara bertahap berkurang saat mencapai ujung yang dibuang.
Rotary kiln secara garis besar dibagi menjadi dua zona yaitu zona pra-pemanasan dan zona reduksi (Gbr 2). Zona pra-pemanasan meluas lebih dari 40 hingga 50 persen dari panjang kiln. Di zona ini, uap air dalam muatan dihilangkan, dan zat yang mudah menguap dalam batubara, yang dibebaskan pada kisaran suhu 600 derajat C hingga 800 derajat C, dibakar dengan udara pembakaran yang disuplai melalui tabung udara di ruang bebas. di atas biaya. Panas dari pembakaran menaikkan suhu lapisan dan permukaan tempat tidur. Saat kiln berputar, lapisan mentransfer panas ke muatan. Bahan pengisi daya, yang dipanaskan sebelumnya hingga sekitar 950 derajat C memasuki zona reduksi. Suhu orde 1000 derajat C hingga 1100 derajat C dipertahankan di zona reduksi, yang merupakan suhu yang sesuai untuk reduksi keadaan padat dari oksida besi menjadi besi logam. Termokopel yang dipasang di sepanjang cangkang tungku menentukan profil termal tungku. Temperatur di dalam kiln dikendalikan dengan mengatur jumlah udara pembakaran yang masuk ke dalam kiln melalui port dengan bantuan kipas yang dipasang pada cangkang kiln dan dengan injeksi batubara yang terkontrol. Oksida besi dari bijih direduksi menjadi besi metalik oleh karbon monoksida yang dihasilkan dalam kiln dari batubara.
Bahan tereduksi panas dari kiln kemudian diteruskan ke pendingin putar melalui saluran transfer untuk pendinginan. Pendingin juga dimiringkan pada 2,5 derajat dan diputar dengan kecepatan variabel 0,3 rpm hingga 1,2 rpm yang digerakkan oleh motor kecepatan variabel AC. Air disemprotkan di atas cangkang untuk mendinginkan secara tidak langsung bahan panas di dalam cangkang. Bahan didinginkan hingga sekitar 100 derajat C dan dikeluarkan pada konveyor sabuk melalui katup pendulum ganda, yang berfungsi sebagai segel dan mencegah udara atmosfer masuk ke pendingin putar.
Produk kiln yang didinginkan setelah dikeluarkan dari rotary kiln dikirim ke area pemisahan produk di mana DRI dipisahkan secara magnetis dari arang dan disaring ke berbagai fraksi ukuran.
Gas yang mengalir berlawanan arah dengan material di kiln menuju ke dust settling chamber (DSC) di mana partikel yang lebih berat mengendap. Partikel-partikel ini terus-menerus dihilangkan oleh sistem scrapper basah. Gas-gas tersebut kemudian mengalir ke after burner chamber (ABC) di mana sisa karbon atau CO dibakar oleh udara berlebih yang tersedia. Setelah ABC, gas-gas tersebut berada pada temperatur tinggi dan memiliki banyak energi panas yang biasanya dimanfaatkan untuk pembangkitan uap melalui waste heat recovery boiler (WHRB). Uap ini umumnya digunakan untuk pembangkit listrik. Gas yang didinginkan hingga sekitar 200 derajat C pada pelepasan WHRB mengalir ke peralatan pengendalian polusi seperti bag filter, scrubber, atau electro static precipitator (ESP) untuk menghilangkan partikel debu yang lebih halus. Gas bersih dilepaskan ke atmosfer pada suhu sekitar 80 derajat C melalui cerobong asap.
Untuk menghindari pembentukan cincin kiln yang signifikan, suhu operasi di kiln harus dijaga dalam suhu 1.100 derajat C.
Karena proses rotary kiln membutuhkan waktu reduksi sekitar 7 jam hingga 8 jam, produktivitas prosesnya terbatas dan biasanya berkisar antara 30.000 ton/tahun hingga 150.000 ton/tahun tergantung pada ukuran kiln. Tahapan penting dari proses dan konsep proses ditunjukkan pada Gambar 2.
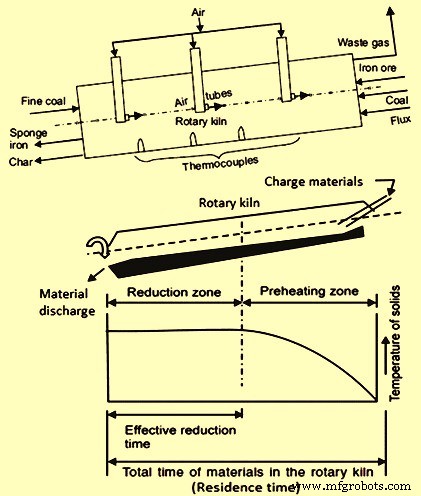
Gbr 2 Tahapan penting dan konsep proses proses rotary kiln
Selanjutnya dalam proses reduksi rotary kiln berbasis batubara dibutuhkan sekitar 6 GCal energi bahan bakar. Lebih dari 2 GCal energi dikeluarkan dari kiln sebagai gas buang. Sebagian dari energi ini dipulihkan di WHRB.
Lembar aliran skematik khas dari proses reduksi langsung berbasis batubara ada di Gambar 3.
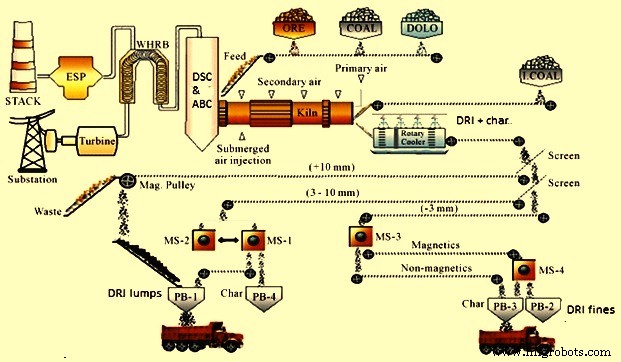
Gbr 3 Skema flow sheet proses reduksi langsung berbasis batubara
Ada beberapa proses dan konsep proses yang telah dikembangkan di bidang ini selama paruh kedua abad kedua puluh. Beberapa dari mereka selamat sementara yang lain tidak. Proses dan konsep proses yang bertahan memiliki beberapa fitur umum atau sedikit berbeda seperti yang diberikan di bawah ini.
- Metode penyegelan untuk menghindari masuknya udara ke dalam rotary kiln.
- Metode melempar atau melempar batu bara non-coking dari ujung pembuangan tanur putar.
- Metode penimbangan, penimbangan, dan pengisian bahan baku.
- Metode memasukkan udara dalam jumlah terkontrol secara berkala di sepanjang kiln sedemikian rupa sehingga tidak mengoksidasi produk tereduksi di tempat tidur.
- Metode pengukuran dan pencatatan suhu secara berkala di sepanjang kiln.
- Metode pendinginan tidak langsung campuran DRI – arang dalam cangkang silinder baja putar dengan menyemprotkan air pada permukaan luar cangkang.
- Metode pemisahan DRI dari campuran DRI-char.
- Metode pengolahan gas buangan dan mempertahankan profil aliran yang diinginkan melalui kontrol tekanan.
- Metode pemulihan energi dari limbah gas
Peralatan dan fasilitas
Peralatan dan fasilitas berikut diperlukan untuk proses tanur putar reduksi langsung berbasis batubara.
- Bagian persiapan bahan baku – Bagian ini berisi peralatan seperti vibro-feeder, crusher, dan screen. Penghancuran bijih besi biasanya tidak diperlukan karena bahan berukuran (5 mm sampai 20 mm) umumnya diperoleh. Bijih besi biasanya dibawa ke hopper tanah, dari mana ia dibawa ke layar dengan bantuan vibro-feeder, di mana oversize (+ 20 mm) dan undersize (- 5 mm) dipisahkan dengan penyaringan. Material oversize dikirim ke oversize crusher untuk mendapatkan material berukuran besar. Dalam hal batubara non-coking, ukuran yang diterima biasanya -200 mm yang dihancurkan dengan penghancur primer dan sekunder di sirkuit tertutup dengan saringan primer dan sekunder. Penyaringan memisahkan dua fraksi yaitu gumpalan batubara untuk batubara umpan (5 mm hingga 20 mm) dan butiran halus (-5 mm) untuk batubara injeksi yang diperlukan untuk proses tersebut. Penghancuran dan penyaringan dolomit umumnya tidak diperlukan karena material berukuran (3 mm hingga 8 mm) umumnya diperoleh dan langsung diumpankan ke day bin melalui konveyor. Semua bahan mentah dari titik pembuangannya diumpankan ke day bin melalui konveyor.
- Bagian penyimpanan bahan baku – Terdiri dari tempat penyimpanan (day bins). Untuk bahan baku yang berbeda, tempat penyimpanan terpisah disediakan. Tempat sampah biasanya dirancang untuk penyimpanan bahan mentah untuk konsumsi minimal satu hari.
- Sistem pengumpanan bahan baku – Ini terdiri dari pengumpan timbangan yang disediakan di bawah setiap wadah untuk menarik berbagai bahan mentah dalam proporsi yang diperlukan dari wadah dan dikirim ke konveyor untuk dimasukkan ke dalam kiln.
- Rotary kiln – Ini adalah inti dari proses reduksi berbasis batubara karena reaksi reduksi berlangsung di reaktor ini. Diameter dan panjang tungku tergantung pada kapasitasnya. Kiln umumnya dilapisi dengan refraktori castable alumina tinggi sepanjang panjangnya dengan bendungan di ujung umpan dan ujung pembuangan. Kiln biasanya miring pada kemiringan 2,5 derajat ke bawah dan bertumpu pada dua hingga empat stasiun pendukung, tergantung pada ukuran kiln. Laju pengangkutan material melalui kiln dapat dikontrol dengan memvariasikan kemiringan dan kecepatan putarannya. Ada kerucut inlet dan outlet di ujung yang berlawanan dari kiln yang didinginkan oleh masing-masing kipasnya. Cangkang kiln dilengkapi dengan port pengambilan sampel kecil. Posisi memanjang kiln pada cincin pengendaraannya dikendalikan oleh sistem hidraulik. Batubara dan bijih besi diukur ke bagian atas tanur miring. Sebagian batubara juga disuntikkan secara pneumatik dari ujung pembuangan kiln. Beban pertama melewati zona pra-pemanasan di mana de-volatilisasi batubara terjadi dan bijih besi dipanaskan sampai suhu pra-pemanasan untuk reduksi. Kontrol suhu dan proses di kiln dilakukan dengan memasang sejumlah tabung injeksi udara yang terbuat dari baja tahan panas yang ditempatkan secara merata di sepanjang kiln dan berlawanan arah dengan aliran bijih besi. Ujung tabung udara dilengkapi dengan pusaran internal khusus untuk meningkatkan keseragaman pembakaran. Pembakar sentral yang terletak di ujung pembuangan kiln digunakan dengan LDO (minyak diesel ringan) untuk memanaskan tanur dingin. Setelah pemanasan awal, pasokan bahan bakar dimatikan dan burner digunakan untuk menyuntikkan udara untuk pembakaran batubara. Suhu tanur diukur dengan termokopel tetap dan port 'termokopel respons cepat' (QRT). Termokopel tetap terletak di sepanjang kiln sehingga suhu di berbagai bagian kiln dapat dipantau. Termokopel tetap, kadang-kadang dapat memberikan pembacaan yang tidak menentu jika dilapisi dengan abu, bijih, atau akresi. Dalam kasus seperti itu, QRT digunakan untuk memantau suhu tungku.
- Pendingin putar – Produk (DRI) bersama dengan abu batubara, dolomit terkalsinasi, dan arang sisa dikeluarkan dari kiln pada suhu sekitar 1000 derajat C. Parasut tertutup di ujung pembuangan kiln dilengkapi dengan pemisah gumpalan dan pintu akses untuk menghilangkan gumpalan memindahkan DRI panas ke pendingin putar. Pendingin adalah silinder berputar dengan ukuran yang sesuai yang miring pada 2,5 derajat. DRI didinginkan secara tidak langsung dengan semprotan air pada permukaan atas yang lebih dingin. Air pendingin dikumpulkan dalam bak di bawah pendingin dan dipompa ke menara pendingin untuk didaur ulang bersama dengan air make-up. Padatan yang dibuang ke pendingin melalui saluran tertutup didinginkan hingga sekitar 100 derajat C tanpa kontak udara. Grizzly di saluran menghilangkan akresi yang besar (lebih besar dari 50 mm) untuk menyumbat atau merusak mekanisme pelepasan yang lebih dingin. Benjolan akresi ini dibuang secara terpisah melalui gerbang benjolan. Sisa material dibuang pada konveyor melalui katup penutup ganda. Produk kemudian dikirim ke sistem pemisahan produk melalui konveyor.
- Bagian pemisahan produk – Terdiri dari layar getar dan pemisah magnetik. Produk yang didinginkan dikirim ke bagian pemisahan produk dengan konveyor sabuk. Produk dari cooler discharge mengandung DRI, char dan abu batubara. Di gedung pemisahan produk, produk pertama kali disaring dalam layar dek ganda yang memiliki layar 3 mm dan 20 mm. Produk yang disaring diumpankan ke pemisah magnetik untuk pemisahan bagian magnetik dan non-magnetik. Produk disaring terlebih dahulu untuk menghilangkan DRI plus 20 mm. Undersize (campuran DRI, arang dan abu batubara) disaring menjadi fraksi +/- 3 mm. Setiap fraksi melewati pemisah magnetik. Bagian non-magnetik dari fraksi plus 3 mm sebagian besar adalah arang yang dapat didaur ulang ke kiln jika diinginkan atau dapat digunakan dalam boiler pembangkit listrik sebagai bahan bakar. Bagian nonmagnetik fraksi -3 mm yang sebagian besar habis dikalsinasi dolomit, abu dan arang halus dibuang. Bagian magnetik dari setiap fraksi adalah DRI. Fraksi plus 3 mm dapat digunakan langsung untuk pembuatan baja dan fraksi yang lebih halus dapat dibriket dan dikumpulkan dalam kantong.
- Bagian penyimpanan produk – Terdiri dari tempat penyimpanan. Gumpalan DRI (3 mm hingga 20 mm) dan butiran DRI (-3 mm) disimpan di tempat penyimpanan yang berbeda. Tempat sampah biasanya dirancang untuk memiliki penyimpanan minimal 1 hari produksi. Arang yang dihasilkan di pembangkit disimpan secara terpisah untuk digunakan sebagai bahan bakar di pembangkit listrik.
- Sistem gas limbah – Gas limbah kiln pada suhu sekitar 850 derajat C hingga 900 derajat C melewati ruang pengendapan debu tempat partikel debu yang lebih berat mengendap karena penurunan kecepatan gas secara tiba-tiba. Gas buang kemudian melewati ruang setelah pembakaran di mana bahan mudah terbakar yang tidak terbakar dibakar dengan meniupkan udara berlebih. Suhu ruang after burner, kadang-kadang, dikendalikan oleh semprotan air. Gas yang terbakar kemudian melewati down duct ke dalam evaporator cooler dimana temperatur diturunkan dan melalui alat pengontrol polusi yaitu ESP/bag filter/scrubber dimana balance partikel debu dipisahkan. Kemudian gas dibiarkan keluar ke atmosfer melalui stack melalui induced draft (ID) fan. Namun, diinginkan untuk melengkapi sistem gas limbah dengan boiler pemulihan panas limbah (waste heat recovery boiler/WHRB) untuk pemulihan energi sensibel yang dibawa oleh gas limbah. Dalam hal ini gas buang setelah ruang pembakaran melewati saluran siku ke WHRB di mana panas yang masuk akal dari gas diekstraksi. Gas tersebut kemudian dilepaskan ke atmosfer setelah melewati peralatan pengendalian polusi seperti ESP /bag filter / scrubber, ID fan dan stack.
- Pasokan utilitas – Udara bertekanan dan air pendingin adalah dua utilitas yang dibutuhkan untuk proses tersebut. Kompresor udara biasanya dipasang untuk memasok udara tekan sedangkan untuk sistem air pendingin terdiri dari rumah pompa dan menara pendingin.
Pembentukan akresi di tanur putar
Bahan di dalam kiln jatuh dan meluncur, dan lapisan tipis debu selalu terbentuk di permukaan lapisan tahan api. Beberapa zona kiln mungkin secara khusus rentan terhadap akumulasi partikel dan efek gabungan dari kondisi termal dan aliran menghasilkan pembentukan endapan silinder, atau cincin karena gerakannya yang berputar. Saat ring menjadi lebih tebal, bukaan kiln yang tersedia berkurang, yaitu volume kerja kiln berkurang, yang mengakibatkan terhambatnya aliran produk dan gas buang melalui kiln. Cincin umumnya terletak dekat dengan zona reduksi atau burner dan disebabkan oleh suhu yang sangat tinggi di area ini, terutama ketika lapisan refraktori terlalu panas karena pelampiasan langsung dari api burner. Ini adalah jenis cincin yang paling umum dan juga yang paling merepotkan.
Alasan utama pembentukan akresi pada rotary kiln adalah karena terbentuknya senyawa kompleks dengan titik leleh rendah dalam sistem FeO-SiO2-Al2O3, seperti wustite, fayalite, iron cordierite, hercynite, dan dalam CaO-MgO-FeO-SiO2- Sistem Al2O3, seperti melilite atau anorthite, akermanite, iron-magnesium cordierite, spinel, dan iron-magnesium silikat. Koeksistensi senyawa kompleks ini menurunkan suhu fusi muatan kiln, yang pada gilirannya melekat pada dinding refraktori. Beberapa akresi juga terbentuk karena aglomerasi butiran halus lebih dekat ke ujung pengisian atau karena sintering DRI karena suhu yang berlebihan dan/atau rasio karbon/besi yang lebih rendah pada ujung pelepasan tanur putar.
Karena cincin-cincin ini tidak dapat dicapai dari luar kiln, oleh karena itu cincin-cincin tersebut tidak mungkin dilepas selama pengerjaan kiln. Dalam beberapa kasus, cincin tumbuh dengan cepat dan menyebabkan pemadaman kiln yang tidak terjadwal. Telah diamati bahwa sebagian besar penghentian kiln hanya karena pembentukan akresi.
Istilah yang terkait dengan produksi DRI
Beberapa istilah yang terkait dengan pengukuran efektivitas reaksi reduksi untuk DRI didefinisikan sebagai berikut.
Persen besi total 'Fe T' adalah besi total dalam sampel, termasuk besi metalik dan besi yang secara kimiawi digabungkan dengan elemen lain seperti oksigen.
Fe T =(berat besi/berat sampel)*100
Persen besi metalik 'Fe M' adalah besi yang secara kimiawi tidak bergabung dan sebagai sementit (Fe3C).
Fe M =(berat besi metalik/berat sampel)*100
Oksida besi sisa adalah sisa oksida besi yang ada di DRI baik dalam bentuk FeO, Fe3O4 atau Fe2O3, meskipun biasanya FeO biasanya merupakan satu-satunya oksida sisa yang ada.
Total karbon adalah total karbon yang ada dalam DRI dan sama dengan jumlah karbon bebas dan karbon gabungan (sebagai sementit).
Kotoran adalah elemen/senyawa yang tidak diinginkan dalam DRI, sulfur dan fosfor adalah yang paling umum di antara mereka.
Metalisasi adalah ukuran konversi oksida besi menjadi besi metalik (baik bebas, atau dalam kombinasi dengan karbon sebagai sementit) dengan menghilangkan oksigen karena aksi reduktor yang digunakan.
Derajat metalisasi mengacu pada bagian dari total besi yang ada sebagai besi metalik.
Derajat metalisasi =(berat besi metalik/berat besi total)* 100 =(Fe M/Fe T)*100
Metalisasi setara – Kandungan karbon dalam besi spons pada tingkat metalisasi tertentu adalah penting. Ini memiliki kapasitas untuk menghilangkan oksigen dari oksida besi yang tersisa selama pembuatan baja. Ini mengarah pada konsep metalisasi ekivalen, yang didefinisikan sebagai berikut.
Metalisasi ekivalen dalam % =Derajat metalisasi (%) + 5 kali % total karbon dalam DRI
Persen pengurangan mengacu pada oksigen yang telah dihilangkan dalam memproduksi DRI dengan mengacu pada Fe awal sebagai Fe2O3.
% reduksi ={[(%O/% Fe T) dalam Fe2O3 – (%O/% Fe M) dalam DRI]/(%O/%Fe T) dalam Fe2O3}*100
% reduksi =[1- 2,327* (%O/%Fe T) dalam DRI]*100
Definisi ini memberikan keadaan besi yang terkandung dalam DRI. Kebingungan dapat muncul karena beberapa orang mendefinisikan persen pengurangan mengacu pada keadaan oksida awal bijih yang mungkin termasuk Fe3O4 dan FeO. Dalam hal ini, pengurangan persen menentukan jumlah pengurangan yang dilakukan dalam proses DRI.
Persen gangue mengacu pada senyawa non-besi (SiO2, Al2O3, CaO, MgO, dll.) dalam DRI.
Gangue =100 – %O dengan Fe – %Fe M – %C
Dasar kuarterner adalah rasio CaO, MgO, dan Al2O3, SiO2, dan dinyatakan sebagai rasio (% CaO + % MgO)/(% Al2O3 + % SiO2).