Merasionalkan investasi keandalan Anda
Berapa biaya sebenarnya dari sebuah kegagalan? Sayangnya, kita tidak tahu sampai setelah kegagalan terjadi - dan keandalan adalah tentang menghindari kegagalan. Jadi, inilah kebingungan kami:Berapa nilai non-acara? Dunia rekayasa keandalan manufaktur penuh dengan orang-orang yang sangat kompeten dan terlatih yang terbiasa mendefinisikan dunia mereka dalam istilah parametrik dan deterministik.
Agar nyaman dengan proses memprediksi masa depan dalam kondisi saat ini dan kemudian membenarkan perubahan untuk menciptakan masa depan yang baru dan lebih menguntungkan, profesional keandalan manufaktur harus merasa nyaman dengan proses mendefinisikan dunia mereka dalam istilah probabilistik dan non-parametrik.
Kami tahu dua hal - setiap proses manufaktur akan gagal dan kegagalan tersebut akan berdampak pada organisasi. Demikian pula, ada dua hal yang tidak kita ketahui:kapan prosesnya akan gagal dan seberapa parah dampaknya bagi organisasi.
Dalam pengalaman saya, ahli keandalan cenderung condong ke salah satu dari dua ekstrem ketika mendefinisikan dampak kegagalan. Di satu sisi, insinyur keandalan konservatif hanya mengklaim biaya yang dihindari untuk suku cadang, menganggap bahwa biaya tenaga kerja tenggelam; tidak ada biaya downtime karena kami tidak dapat berasumsi bahwa kapasitas produksi pabrik akan terjual habis; dan kami tidak dapat menanggung biaya berbasis risiko, seperti cedera pribadi, dampak lingkungan, dll. Di sisi lain, insinyur keandalan yang terlalu bersemangat mengklaim bahwa jika mereka tidak mendeteksi potensi kegagalan bantalan dan menjadwalkannya untuk diperbaiki, pompa akan gagal, menciptakan kerugian total dari produksi yang terjual habis dan menyebabkan kebakaran yang meledakkan pabrik, membunuh semua orang, menciptakan zona limbah lingkungan utama dan menyebabkan bumi berhenti berputar pada porosnya! Aku bercanda, tapi intinya adalah bahwa kebenaran ada di antara keduanya.
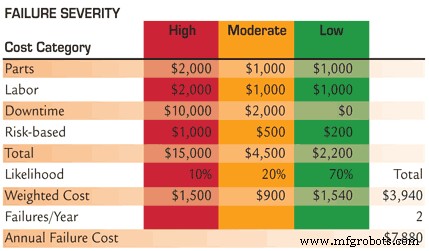
Gambar 1. Biaya sebenarnya dari kegagalan tidak dapat diperkirakan secara deterministik sampai setelah kejadian. Untuk tujuan perencanaan, pendekatan probabilistik harus digunakan.
Pada intinya, keandalan mirip dengan manajemen risiko. Manajer risiko memandang dunia dengan cara probabilistik, non-parametrik karena itulah satu-satunya cara yang masuk akal untuk mencoba memprediksi masa depan. Meminjam bab dari manajemen risiko 101 dan beberapa standar terkait yang berkaitan dengan topik tersebut, saya telah membuat model untuk mengilustrasikan kepada Anda bagaimana memperkirakan biaya kegagalan fungsional dari proses manufaktur. Model ini diilustrasikan pada Gambar 1. Berikut adalah petunjuk langkah demi langkah untuk membuat dan menggunakan model biaya kegagalan yang disesuaikan dengan risiko.
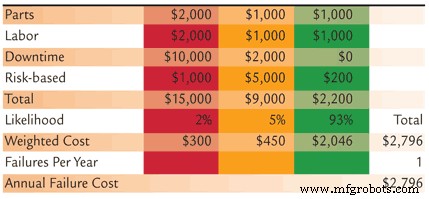
Gambar 2. Perkiraan biaya kegagalan tahunan setelah menerapkan pemantauan, perencanaan, dan peningkatan keandalan
1) Buat perkiraan biaya berdasarkan tingkat keparahan kegagalan: Seperti yang diilustrasikan Gambar 1, setiap kegagalan fungsional memiliki biaya terkait. Ini mungkin termasuk suku cadang, tenaga kerja, waktu henti, biaya berbasis risiko, dll. Kuncinya adalah membuat model biaya berbasis tingkat keparahan kegagalan. Peristiwa dengan tingkat keparahan tinggi dapat menyebabkan Anda mengeluarkan biaya waktu henti yang signifikan dan/atau biaya tambahan, sedangkan peristiwa sedang dan kecil menghasilkan dampak yang lebih kecil pada organisasi. Dalam model contoh saya, kegagalan tingkat tinggi biaya $15.000 per peristiwa, tingkat kerusakan sedang biaya $4.500 dan tingkat kerusakan rendah $2.200. Ini bukan untuk mengatakan bahwa setiap peristiwa yang dinilai berdampak sedang akan menelan biaya persis $4.500 (ingat, kami memiliki batasan pemikiran non-parametrik); ini adalah rata-rata tertimbang dalam kategori keparahan kegagalan tersebut.
Saya telah memilih tiga klasifikasi keparahan, yang merupakan pendekatan khas saya dalam bekerja dengan klien. Anda dapat membuat kategori sebanyak yang Anda inginkan. Namun, ada pengembalian marjinal yang semakin berkurang dalam kegunaan untuk setiap kategori tambahan. Juga, saya sarankan Anda menahan godaan untuk mendiskon biaya tenaga kerja berdasarkan logika bahwa mereka tenggelam. Yang benar adalah bahwa tenaga kerja adalah biaya variabel. Jika proses manufaktur menjadi lebih otomatis dan andal, kami hanya membutuhkan lebih sedikit orang untuk mengoperasikan dan memeliharanya, titik.
2) Buat faktor pembobotan probabilitas: Dalam contoh saya, saya berasumsi bahwa 10 persen dari peristiwa kegagalan saya adalah tingkat keparahan tinggi, 20 persen tingkat keparahan sedang dan 70 persen tingkat keparahan rendah. Kalikan total biaya kegagalan untuk setiap kategori keparahan dengan perkiraan kemungkinan yang terkait dan jumlahkan produk untuk menghasilkan biaya total rata-rata tertimbang untuk peristiwa kegagalan. Dalam contoh saya, peristiwa dengan tingkat keparahan tinggi menyumbang $1.500 ke rata-rata tertimbang, sementara peristiwa dengan tingkat keparahan sedang dan rendah masing-masing menyumbang $900 dan $1.540, dengan total $3.940 per peristiwa. Apakah ini menunjukkan bahwa kegagalan kita berikutnya akan menelan biaya tepat $3.940? Tentu saja tidak. Sekali lagi, kami berpikir secara probabilistik dan non-parametrik.
3) Perkirakan jumlah acara per tahun: Dalam dunia keuangan, analisis biaya manfaat didasarkan pada biaya dan manfaat yang disetahunkan. Jadi, kita perlu memperkirakan berapa banyak kejadian kegagalan jenis ini yang mungkin kita harapkan dalam setahun. Dalam contoh saya, kami mengharapkan dua acara per tahun. Jadi, perkiraan biaya kegagalan tahunan rata-rata kami untuk mode kegagalan fungsional ini adalah $7.880. Tindakan mitigasi apa pun yang Anda ambil akan memengaruhi distribusi keparahan dan/atau mengurangi jumlah kejadian kegagalan per tahun (meningkatkan waktu rata-rata antara kegagalan [MTBF] atau waktu rata-rata hingga kegagalan [MTTF]).
4) Mengubah distribusi kemungkinan: Pada umumnya, alat perencanaan cenderung memodifikasi distribusi kemungkinan. Misalnya, pemantauan protektif, inspeksi, dan pemantauan prediktif membantu kami mendeteksi masalah pada tahap awal, sebelum diberi kesempatan untuk meningkat ke tingkat yang parah atau bencana. Demikian juga, proses perencanaan, penjadwalan, dan manajemen kerja yang efektif memastikan bahwa masalah yang terdeteksi ditangani. Langkah-langkah ini tidak memengaruhi tingkat kegagalan dasar, tetapi cenderung memengaruhi distribusi kemungkinan, mengurangi kemungkinan bahwa suatu peristiwa akan memiliki tingkat keparahan yang tinggi sekaligus meningkatkan kemungkinan bahwa itu akan menjadi peristiwa dengan tingkat keparahan yang rendah.
Dalam contoh kami, jika kami meningkatkan kemampuan kami untuk mendeteksi dan mengelola kegagalan, kami memperkirakan bahwa kemungkinan peristiwa dengan tingkat keparahan tinggi berkurang dari 10 persen menjadi 2 persen, kemungkinan peristiwa dengan tingkat keparahan sedang berkurang dari 20 persen menjadi 5 persen, sedangkan kemungkinan kejadian dengan tingkat keparahan rendah meningkat dari 70 persen menjadi 93 persen. Mendistribusikan ulang kemungkinan keparahan mengurangi perkiraan biaya rata-rata tertimbang per peristiwa dari $3.940 menjadi $2.796 (Gambar 2).
5) Mengubah tingkat kegagalan: Langkah-langkah proaktif, di sisi lain, mempengaruhi keandalan proses manufaktur, mengurangi tingkat kegagalan. Kontrol dan pemantauan kondisi proaktif untuk meningkatkan pelumasan, kontrol kontaminasi, keseimbangan dan penyelarasan, serta tindakan operasi dan perawatan presisi yang dipandu oleh prosedur operasi standar (SOP) dan prosedur perawatan standar (SMP) yang terdokumentasi mengurangi tingkat kegagalan yang terjadi. Dalam contoh kami, kami memperkirakan bahwa kami dapat mengurangi dari dua kegagalan per tahun menjadi satu. Dengan asumsi kami mengurangi biaya per peristiwa dengan meningkatkan kemampuan kami untuk mendeteksi dan mengelola masalah yang dikombinasikan dengan inisiatif peningkatan keandalan kami, kami berharap dapat mengurangi biaya kegagalan tahunan kami dari $7.880 menjadi $2.796 (gambar 1 dan 2).
Jadi, dalam contoh kita, meningkatkan kemampuan kita untuk mendeteksi dan mengelola kegagalan menghasilkan keuntungan bersih sebesar $1,144 per tahun untuk mode kegagalan fungsional yang ditentukan. Dikombinasikan dengan inisiatif peningkatan keandalan kami, keuntungan bersihnya adalah $5,084. Selama investasi keandalan yang diperlukan untuk membuat perubahan menghasilkan tingkat pengembalian yang sesuai bagi organisasi, inisiatif harus dilakukan.
Di kolom ini, kami telah mengadopsi model manajemen risiko untuk membantu kami menghitung biaya mode kegagalan fungsional. Dalam edisi mendatang, kami akan terjun ke bidang pengambilan keputusan di bawah ketidakpastian untuk membahas model untuk membuat perkiraan ketika hanya ada sedikit data empiris yang tersedia, kemudian kami akan menyatukannya untuk menunjukkan kepada Anda bagaimana melakukan analisis biaya manfaat dan menyajikan usulan Anda proyek peningkatan keandalan dalam bentuk yang akan menyebabkan peringkat persetujuan Anda meningkat secara dramatis.