5 penyebab kegagalan peralatan (dan apa yang dapat Anda lakukan untuk mencegahnya)
Pos ini awalnya ditulis sebagai blog tamu oleh Nicole Pontius dari Camcode. Diedit dan diperbarui oleh tim Fiix pada Juni 2019.
- 5 penyebab umum kegagalan peralatan
- Penyebab #1:Pengoperasian yang tidak benar
- Penyebab #2:Kegagalan melakukan pemeliharaan preventif
- Penyebab #3:Terlalu banyak perawatan preventif
- Penyebab #4:Kegagalan untuk terus memantau peralatan
- Penyebab #5:Budaya keandalan yang buruk (atau tidak!)
- Intinya
Kegagalan peralatan terjadi. Dampaknya dapat berjalan secara keseluruhan dari yang mudah diperbaiki dengan kerugian minimal hingga bencana, tergantung pada faktor-faktor seperti biaya perbaikan, waktu henti total, implikasi kesehatan dan keselamatan, serta dampak pada produksi dan penyampaian layanan.
Ada beberapa alasan umum peralatan dapat rusak, dan memahami mengapa peralatan Anda mungkin gagal adalah garis pertahanan pertama Anda terhadap konsekuensi serius dari waktu henti yang tidak direncanakan.
Gunakan tujuh rahasia ini untuk mengurangi waktu henti dan menang melawan kegagalan
Mengalahkan kegagalan peralatan
5 penyebab umum kegagalan peralatan
Penyebab #1:Pengoperasian yang tidak benar
Ada banyak orang yang mungkin berada di dalam dan di sekitar peralatan setiap hari yang dapat memberikan dampak signifikan pada kondisi pengoperasiannya secara keseluruhan.
Operator peralatan adalah salah satu kelompok tersebut. Mereka biasanya menerima pelatihan mendalam tentang prosedur operasi yang sesuai, pemecahan masalah dasar, dan praktik terbaik untuk penggunaan peralatan yang aman yang relevan dengan mesin yang akan mereka gunakan. Namun, suatu hari mungkin akan tiba ketika seorang operator akhirnya mengerjakan mesin yang belum dilatih secara memadai. Terkadang situasi ini muncul sebagai akibat dari kekurangan staf atau ketidakhadiran yang tidak terduga. Di lain waktu, keadaan darurat muncul yang memerlukan perbaikan cepat dengan staf yang tersedia yang mungkin belum tentu memiliki tingkat keahlian yang dimiliki operator Anda yang paling berpengalaman.
Salah satu solusi untuk masalah ini adalah memastikan bahwa Anda memiliki operator terlatih yang cukup untuk memungkinkan fleksibilitas dan rencana darurat untuk keadaan darurat kekurangan staf. Jika memungkinkan, semua operator Anda harus mendapatkan pelatihan tentang setiap peralatan—bahkan aset yang biasanya tidak mereka gunakan.
Yang terpenting, jangan pernah mengizinkan operator menggunakan peralatan yang tidak memenuhi syarat untuk dijalankan. Ini tidak hanya akan membantu mengurangi kesalahan operasional, tetapi di beberapa industri, sangat penting untuk kepatuhan terhadap peraturan. Administrasi Keselamatan dan Kesehatan Kerja (OSHA) menetapkan peraturan untuk persyaratan pelatihan operator untuk jenis peralatan tertentu dan untuk keselamatan kerja secara umum. Namun, terserah Anda untuk mengetahui peraturan yang berlaku untuk industri Anda dan memastikan bahwa Anda memiliki prosedur kepatuhan yang memadai.
Penyebab #2:Kegagalan melakukan pemeliharaan preventif
Sebagian besar peralatan memerlukan perawatan rutin untuk kinerja yang optimal, tetapi terlalu sering, perawatan preventif adalah tugas pertama yang harus dilakukan ketika Anda kekurangan staf dan kewalahan. Sangat mudah untuk mengabaikan perawatan rutin ketika segala sesuatunya tampak berjalan baik-baik saja, dan banyak perusahaan bekerja dengan asumsi bahwa pekerja berpengalaman akan mengidentifikasi masalah yang akan datang sebelum peralatan gagal total.
Meskipun demikian, banyak dari tanda-tanda halus dari kinerja yang melambat atau tahap awal kegagalan tidak mudah dideteksi dan sering tidak diperhatikan. Dalam kasus lain, perusahaan hanya kekurangan metode perencanaan yang efisien untuk memastikan bahwa pemeliharaan berkelanjutan dilakukan. Peralatan dan mesin pelacak dengan tag aset dapat membantu menjaga jadwal perawatan tetap pada jalurnya dan peralatan beroperasi pada efisiensi operasional maksimum.
Pemeliharaan preventif adalah salah satu fungsi berkelanjutan yang tidak boleh dibiarkan begitu saja. Merawat peralatan Anda dengan penyetelan rutin akan memperpanjang masa pakai peralatan Anda, yang pada akhirnya memberi Anda lebih banyak untuk setiap dolar. Selain itu, pemeliharaan preventif dapat mengidentifikasi masalah kecil dengan solusi murah sebelum menjadi kerusakan besar dan mahal. Ketika Anda menggunakan strategi pengendalian inventaris yang efektif untuk memastikan bahwa Anda memiliki persediaan suku cadang yang tepat untuk tugas pemeliharaan dan malfungsi yang paling umum, waktu henti untuk pemeliharaan dan perbaikan rutin menjadi minimal. Faktanya, Departemen Energi A.S. memperkirakan bahwa pemeliharaan preventif menghasilkan:
- Pengurangan biaya energi dan pemeliharaan hingga 30%
- 35% hingga 45% lebih sedikit kerusakan
- Pengurangan waktu henti hingga 75%
Berhenti memadamkan api sepanjang hari dengan templat jadwal pemeliharaan preventif gratis ini
Penyebab #3:Terlalu banyak pemeliharaan preventif
“Tentunya ini kesalahan,” Anda berpikir. “Anda baru saja mengatakan kepada saya bahwa TIDAK melakukan pemeliharaan preventif akan menyebabkan kerusakan.” Memang benar— ada sedikit situasi Goldilocks yang terjadi dalam hal pemeliharaan preventif. Tidak cukup bisa menjadi masalah karena alasan yang kami uraikan di atas, tetapi terlalu banyak juga merupakan penyebab utama kekhawatiran.
Kami telah menulis tentang ini secara mendalam sebelumnya, jadi periksa blog ini jika Anda ingin mempelajari lebih dalam konsep kerusakan pasca-pemeliharaan. Tapi inilah Catatan Coles:Setiap kali Anda masuk ke mesin untuk merawatnya, Anda membuka peralatan itu ke seluruh rangkaian risiko, dan seiring waktu risiko tersebut dapat bertambah dan menyebabkan kegagalan.
PM tidak cukup
Tanda-tanda kegagalan awal terlewatkan
Jadwal pemeliharaan terganggu
Mengurangi efisiensi peralatan
Masa pakai aset menyusut
Kerusakan dan kenaikan waktu henti
Biaya meroket
PM secukupnya
Biaya dikendalikan
Pengiriman tepat waktu tercapai
Waktu henti terputus
Efisiensi teknisi ditingkatkan
Keamanan meningkat
Produktivitas aset penting dioptimalkan
Terlalu banyak PM
Peningkatan pengeluaran yang berlebihan
Keausan pada aset yang melonjak
Waktu teknisi terbuang percuma
Inventaris yang tidak perlu digunakan
Informasi yang tidak akurat dikumpulkan
Pastikan Anda tidak melakukan terlalu banyak PM dengan template log pemeliharaan ini
Anggap saja dalam hal operasi— bypass tiga kali lipat adalah operasi yang menyelamatkan jiwa. Tetapi Anda tidak ingin menjalani operasi jantung terbuka secara teratur hanya karena beberapa tahun telah berlalu, atau jantung Anda telah berdetak beberapa juta kali. Namun seringkali, itulah cara kami melakukan pemeliharaan preventif. Ini dilakukan pada jadwal yang telah ditentukan (umumnya berdasarkan waktu atau penggunaan) tanpa mempertimbangkan kondisi pengoperasian aset yang sebenarnya.
Yang membawa kita ke…
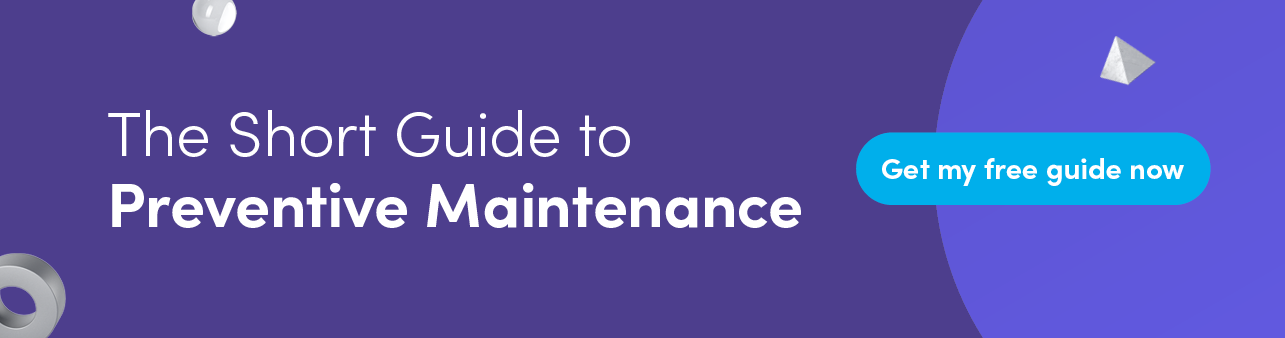
Penyebab #4:Kegagalan untuk terus memantau peralatan
Jadi bagaimana Anda menemukan keseimbangan yang tepat dari pemeliharaan preventif? Penyembuhan di sini sederhana dalam konsep tetapi sedikit lebih rumit dalam pelaksanaannya:pemeliharaan berbasis kondisi. Ini adalah perawatan yang dilakukan berdasarkan kondisi operasi suatu peralatan, bukan hanya jadwal 'setel dan lupakan saja'. Ini mempertimbangkan banyak hal, mulai dari riwayat peralatan informasi pabrikan hingga data waktu nyata seperti analisis getaran.
Pemantauan berkelanjutan bergantung pada data sensor untuk menetapkan garis dasar seperti apa kondisi peralatan yang baik untuk mendeteksi perubahan halus, yang dapat digunakan untuk memprediksi kerusakan dan kegagalan. Hal ini memungkinkan lebih banyak waktu untuk perencanaan kontinjensi dan penjadwalan waktu henti guna meminimalkan gangguan produksi. Jenis pemantauan dan data yang dikumpulkan dalam proses ini dapat membantu perusahaan mengidentifikasi penyebab peningkatan tekanan pada mesin dan menyesuaikan beban kerja dan jadwal untuk mengurangi beban pada peralatan yang menunjukkan indikator awal kegagalan yang akan datang.
Bersiaplah untuk setiap kegagalan pada aset penting Anda dengan template FMEA ini
Tangkapannya di sini adalah bahwa ini sebenarnya sangat sulit dilakukan jika Anda mengelola pemeliharaan dengan pena dan kertas atau Excel. Jika ini adalah tujuan operasi pemeliharaan Anda, mungkin ini saatnya untuk mempertimbangkan untuk beralih ke solusi pemeliharaan digital.
Kapan menggunakan pemantauan berbasis kondisi
Penyebab #5:Budaya keandalan yang buruk (atau tidak!)
Semua orang pernah ke sana— tekanan besar dari atas berarti tidak ada waktu luang jika Anda memiliki harapan untuk mencapai tujuan produksi Anda. Dalam keadaan ini, bisa jadi sangat menggoda (dan sangat mudah) bagi operator atau pekerja pemeliharaan untuk melihat sesuatu tidak bekerja pada 100%, menampar solusi band-aid di atasnya dan berkata, “Saya akan mencari tahu ini ketika keadaan tenang. turun". Masalahnya adalah bahwa secara realistis, segala sesuatunya tidak pernah tenang sejauh Anda punya waktu untuk meninjau kembali pekerjaan itu. Yang berarti bahwa solusi plester menjadi solusi semi-permanen sampai berhenti bekerja dan menjadi kegagalan total.
Contoh yang sangat bagus untuk ini adalah Boeing. Anda mungkin akrab dengan dua kecelakaan maut yang melibatkan pesawat 737 Max perusahaan, yang menimbulkan pertanyaan tentang apakah terburu-buru Boeing untuk menyelesaikan produksi membuat perusahaan mengambil risiko keselamatan yang pada akhirnya mengakibatkan kecelakaan.
Tapi cerita yang lebih tenang menyangkut model pesawat yang berbeda— 787 Dreamliner. Beberapa pelapor telah maju untuk meningkatkan alarm tentang Dreamliners, yang diproduksi pada tahun 2009 di pabrik baru di dekat Charleston, Carolina Selatan. Sejak awal, produksi yang ceroboh adalah masalah yang secara konsisten tersapu oleh jadwal produksi yang agresif.
Jika Anda ingin cerita lengkapnya, lihat artikel lengkap New York Times di sini (atau podcast terkait dari Daily jika Anda lebih menyukai audio). Tapi singkat cerita, masalah di Boeing adalah contoh yang sangat baik dari tekanan persaingan di tingkat tertinggi bisnis yang memiliki efek riak sepanjang rantai komando, sampai ke lantai pabrik. Budaya buruk di atas menciptakan mentalitas "selesaikan dengan cepat" yang dapat mengakibatkan kelalaian yang menghancurkan, solusi plester, dan kesalahan.
Jadi bagaimana jika budaya buruk adalah akar dari kegagalan peralatan Anda? Apa yang bisa kau lakukan? Kami telah membahas topik tentang cara mulai membangun budaya yang berfokus pada keandalan, jadi lanjutkan dan periksa satu (atau semua!) dari bagian ini untuk memberi Anda dasar yang kuat dalam keandalan.
Intinya:Operator terlatih, jadwal PM yang padat, dan fokus pada budaya keandalan adalah tiket Anda menuju masa depan yang bebas kegagalan (atau setidaknya lebih sedikit kegagalan)
Peralatan bisa tidak terduga, dan kegagalan terjadi. Orang membuat kesalahan, suku cadang menjadi tua, dan terkadang pemeliharaan preventif hanyalah satu hal yang terlalu banyak dilakukan di hari yang sudah sibuk. Namun dengan memastikan pelatihan operator yang memadai, menjalankan pemeliharaan preventif atau berdasarkan kondisi pada waktu yang tepat, dan bekerja menuju budaya keseluruhan yang lebih baik, Anda akan memiliki kesempatan yang jauh lebih baik untuk menjaga peralatan Anda tetap dalam kondisi prima.