Apakah Konvergensi IT/OT Hanya Istilah Buzz?
Jadi, apakah "konvergensi TI/OT" hanyalah istilah buzz yang menarik perhatian?
Anda dapat berargumen bahwa memang demikian. Setiap kali seseorang menangkap ide baru, ada upaya untuk membuatnya mudah diingat dan membuatnya terdengar seperti "hal baru terbaik sejak irisan roti." Jadi, tentu saja, seseorang akan menemukan frasa menarik yang diharapkan dapat menginspirasi perubahan, dan dapat mereka gunakan untuk pemasaran.
Masalahnya adalah, bagaimanapun, "konvergensi" TI dan PL ini benar-benar hanya perpanjangan berikutnya dari membuat data dapat digunakan.
Apa itu Konvergensi TI/OT?
Beberapa waktu lalu, kita melihat dimulainya otomatisasi di bidang manufaktur. Peralatan otomatis dirancang untuk melakukan fungsi tertentu yang perlu dilakukan pada kecepatan atau tingkat daya yang tidak dapat dicapai manusia. Tetapi ketika peralatan otomatis gagal, insinyur kontrol perlu masuk ke sistem untuk menentukan apa yang salah. Ini diperlukan untuk masuk ke register sistem PLC untuk mencari petunjuk kegagalan. Ini adalah awal dari penggunaan data teknologi operasional (OT) .
Memiliki beberapa data yang mengarah ke titik kegagalan baik untuk diagnostik—untuk melihat apa yang terjadi sebelumnya. Akibatnya, sistem PLC mulai menggunakan sejarawan untuk menyimpan aliran data yang lebih lama dari sensor, pemanas, dan aktuator otomatisasi—menggunakan data PL dalam jumlah besar.
Dengan memantau data PL dari sejarawan, fungsi SCADA dapat memberikan beberapa wawasan kepada operator tentang bagaimana peralatan itu beroperasi. Ketika kegagalan sudah dekat, fungsi SCADA akan memungkinkan operator (atau supervisor) kesempatan untuk mengambil tindakan sebelum kegagalan terjadi. Ini membutuhkan sistem SCADA untuk memiliki akses ke data dari sejarawan, dan menggunakan komunikasi kepemilikan seperti MODBUS atau PROFIBUS untuk membuat data tersebut tersedia bagi operator melalui antarmuka manusia-mesin (HMI). Tetapi pemantauan itu eksklusif untuk kinerja peralatan, yang semakin memperluas penggunaan data OT.
Melalui pengamatan aliran data ini (pengukur, layar operator, dan sebagainya) dan melalui pemahaman lebih lanjut tentang penyimpangan data, seseorang dapat mengenali—melalui sistem SCADA—tidak hanya ketika kegagalan peralatan akan segera terjadi, tetapi bahwa data juga dapat digunakan untuk menganalisis kegagalan kualitas produk pada pengujian dan inspeksi—operasi yang mungkin beberapa langkah kemudian dalam proses.
Ini menciptakan kebutuhan untuk memiliki data PL yang terkait dengan data TI. Ini menghasilkan penciptaan antarmuka yang kompleks dari PLC dan SCADA ke sistem teknologi informasi (TI) seperti MES, yang memungkinkan data relasional dari kegagalan produk dihubungkan ke data operasional peralatan yang membuat produk. Beberapa mencobanya langsung ke ERP juga (dan masih mencoba), tetapi sistem ERP tidak dilengkapi untuk memproses dan menyajikan data itu dengan cukup cepat dan cukup detail dalam kaitannya dengan peristiwa lain selama proses manufaktur.
Masalah dengan antarmuka ke MES adalah bahwa mereka sangat disesuaikan dan mahal, kadang-kadang menambahkan sebanyak 40-50% dari biaya implementasi untuk sebuah proyek. Langkah selanjutnya dalam peningkatan akses data adalah membuat data PLC lebih mudah diakses oleh MES dan database relasional lainnya. Ketika kebutuhan akan akses ini digabungkan dengan biaya komputasi dan memori komputer menjadi lebih murah dan komunikasi jaringan menjadi lebih stabil (masuk ke jaringan 5G), masuk akal untuk menghubungkan sensor dan aktuator PLC langsung ke jaringan TI (yang kami sebut IIoT) dan membuat data mereka tersedia untuk...siapa pun yang membutuhkannya.
Semua latar belakang ini untuk menyoroti bahwa membuat data PL lebih mudah tersedia untuk sistem TI hanya langkah berikutnya dalam proses yang lebih lama evolusi teknologi yang membawa kita ke Industri 4.0.
Bagaimana Konvergensi TI/OT Digunakan?
Antarmuka data PL ke sistem TI sekarang menghadapi masalah baru.
Sistem PLC/SCADA yang memantau sensor dalam sejarah dapat membuat aliran data yang besar (berukuran hingga megabita) dalam hitungan detik. Namun, dari perspektif pemahaman karakterisasi suatu peristiwa kembali ke sistem TI, aliran data ini—bahkan dalam kerangka waktu yang kecil—terlalu banyak untuk ditangani oleh basis data relasional sistem TI seperti MES. Banyak implementasi telah mencoba untuk merekam contoh data sensor (diambil dari aliran data) untuk menangkap elemen data tunggal, untuk mencoba beberapa representasi peristiwa PL di tingkat TI. Banyak yang telah menemukan, bagaimanapun, bahwa menghubungkan contoh data PL ke peristiwa kualitas produk selama manufaktur tidak terlalu efektif untuk memantau kualitas proses secara umum.
Sekarang kita perlu menentukan cara untuk menggabungkan aliran data dari sistem PL dengan cara yang memegang ke karakteristik penting dari acara produksi. Pelaporan OEE adalah salah satu upaya agregasi ini. Penting untuk diketahui bahwa saat menggunakan segala bentuk agregasi data, akan ada beberapa kehilangan detail penting dari peristiwa yang berkualitas. Itulah mengapa OEE digunakan sebagai objek data level monitoring dan bukan objek level analisis. Namun, dengan memantau nilai perubahan OEE secara real-time, sistem TI dapat mengenali laju dan besarnya perubahan dan membuat alarm untuk memperingatkan adanya masalah.
Untuk menganalisis masalah yang sebenarnya, Anda harus kembali ke aliran data asli yang digunakan untuk membuat nilai OEE. Setidaknya dengan nilai OEE yang diberikan secara real time, insinyur manufaktur dan kontrol mendapatkan visibilitas ke dalam masalah cukup awal sehingga mereka dapat kembali ke sejarawan untuk analisis sebelum peristiwa tersebut terkubur oleh lebih banyak data dari aliran data PL.
Masalahnya adalah, bagaimana Anda mengumpulkan data?
Jawabannya, seperti biasa, adalah...itu tergantung!
Cara menggabungkan data akan bergantung pada data apa yang Anda kumpulkan dan apa yang Anda coba pantau dalam prosesnya. Ini juga akan bergantung pada kemampuan untuk menginterpretasikan perubahan dalam model agregasi data.
Di bagian ini, saya akan melihat salah satu metode agregasi tersebut dan menyajikan beberapa cara untuk menginterpretasikan perubahan dalam kumpulan data ini.
"Kurva distribusi alami" atau histogram adalah salah satu representasi grafis paling umum dari data dari perangkat seperti sensor. Premis utama dari kurva adalah, jika hanya ada variasi acak normal dalam suatu proses, distribusi contoh data akan jatuh ke dalam pola yang menyerupai kurva distribusi alami.
Gambar 1 menggambarkan seperti apa distribusi pembacaan dari sensor oven dengan variasi normal saat diplot dalam histogram.
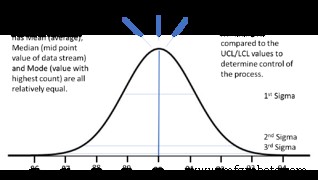
Gambar 1:Kurva distribusi suhu oven menunjukkan mean, median, dan modus. Atas perkenan penulis.
Karakteristik utama kurva adalah mean (rata-rata), median (nilai tengah aliran data), dan mode (nilai dengan kemunculan terbanyak) semuanya kira-kira sama . Hal ini dapat dijadikan acuan untuk mengetahui apakah proses tersebut mengalami kendala. Selama ada indikasi bahwa proses dalam kendali, ada nilai dalam menentukan nilai sigma +/-3 dan membandingkannya dengan batas kendali atas dan bawah serta batas spesifikasi produk.
Contoh Skenario
Untuk memantau proses unit produksi yang melalui proses curing oven, sistem MES akan mencatat waktu unit masuk dan keluar dari oven. Selama waktu ini, sistem PLC (menggunakan sensor pintar) akan membuat aliran data sensor suhu yang konstan yang akan disimpan dalam database sejarawan lokal di perangkat penginderaan. Ketika unit produksi keluar dari oven, MES akan membuat permintaan ke perangkat untuk agregat data suhu selama periode waktu yang ditentukan. Bahkan dengan daya komputasi terbatas yang tersedia di tingkat perangkat, perangkat dapat mengambil ratusan (atau bahkan ribuan) titik data dan memberikan satu set data agregat kembali ke MES—alih-alih memberikan satu contoh data sensor, seperti biasanya. , atau mencoba memproses seluruh aliran data.
Berikut ini adalah kumpulan nilai data gabungan untuk unit produksi ini:
- Rata-rata:90.0
- Median:akan sangat mendekati 90,0
- Mode:sekitar 90,0 derajat juga
- +/- Distribusi 3 Sigma:87.0, 93.0 (akan diverifikasi dengan UCL dan LCL)
Dengan melakukan analisis cepat terhadap perbedaan antara mean, median, dan mode, MES dapat mencari pemantauan kontrol proses yang dapat diterima serta perubahan tren dari unit produksi sebelumnya yang telah melewati oven. Jika nilai +/- 3 sigma berada di luar batas yang dapat diterima, MES akan secara otomatis menandai unit produksi sebagai tersangka, demikian juga jika mean, median, atau mode berbeda secara signifikan satu sama lain atau dari produk sebelumnya.
Gambar 2 menyajikan contoh bagaimana nilai-nilai yang sama akan menunjukkan proses yang tidak terkendali. Namun, dalam kasus ini, nilai sigma +/- 3 masih mungkin berada dalam batas.
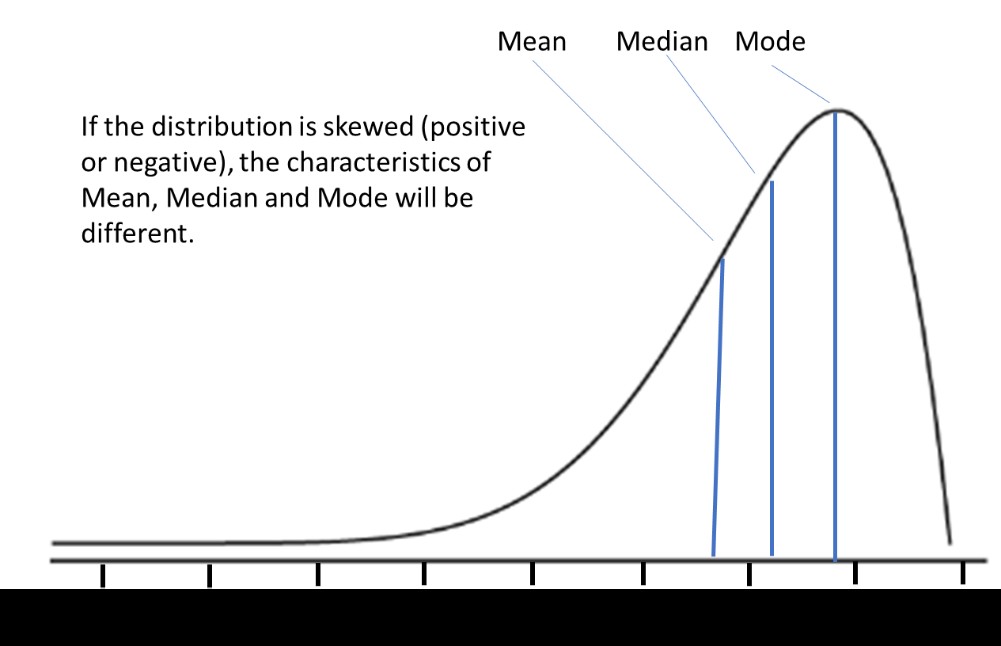
Gambar 2:Contoh perbedaan mean, median, dan modus dalam proses miring. Atas perkenan penulis.
Sekarang, secara teknis, jika distribusi miring seperti yang ditunjukkan, nilai sigma +/- 3 mungkin tidak dianggap valid karena sifat kumpulan data yang miring. Tetapi analisis langsung oleh perangkat masih dapat digunakan untuk menentukan apakah batas kendali telah dilanggar.
Poin kuncinya:jika ini adalah jenis kumpulan data yang disediakan oleh sensor pintar, ini merupakan indikasi bagi teknik manufaktur bahwa oven tidak beroperasi dengan hanya varians acak-dan karena itu harus diselidiki.
Perbedaan lain dalam mean, median, dan modus (misalnya, mean dan median adalah sama, tetapi modusnya berbeda) juga dapat menunjukkan kondisi seperti distribusi bi-modal yang menunjukkan beberapa pengaruh proses yang dimainkan. Sekali lagi, teknik manufaktur harus melihat ke dalam prosesnya.
Ketika kumpulan data di atas dihubungkan langsung ke unit produksi di tingkat MES, data ini dapat digunakan—dengan hasil pengujian dan inspeksi—untuk menunjukkan apakah ada hubungan antara variasi suhu oven dan kegagalan unit produksi.
Apakah produk gagal sebagai akibat dari masalah proses atau tidak, melihat nilai data melayang selama proses produksi juga dapat menunjukkan masalah manajemen proses mendasar yang perlu diselidiki.
Ringkasan
Contoh agregasi data sebelumnya hanya mencerminkan skenario tertentu, tetapi dimaksudkan untuk memberikan gambaran tentang alasan untuk konvergensi data PL dan TI serta nilai potensial konvergensi ini . Dalam setiap skenario produksi, metode agregasi data yang benar perlu dievaluasi, dan pemrograman perangkat pintar perlu membuat fungsi ini tersedia. Atau, sebagai alternatif, sistem komputasi tepi akan diprogram untuk menggantikan fungsi yang dijelaskan untuk perangkat pintar.
Intinya adalah bahwa, meskipun industri banyak menggunakan “konvergensi TI/OT” sebagai istilah umum untuk menggambarkan perubahan teknologi, ada perubahan yang sah dalam pemrosesan data bahwa teknologi di balik istilah buzz memberikan. Perusahaan yang memanfaatkan teknologi konvergensi, dan yang belajar untuk mengumpulkan dan menginterpretasikan data yang disajikan melalui konvergensi dengan benar, dapat memperoleh keuntungan praktis dalam efektivitas program manajemen kualitas dan fasilitas. Dalam lingkungan global yang kompetitif saat ini, menggunakan keuntungan apa pun baik untuk keuntungan.
Jadi, jawabannya adalah tidak. Konvergensi TI/OT bukan hanya istilah buzz. Ini adalah alat yang berharga dalam evolusi akuisisi data dan teknologi manajemen yang dapat sangat bermanfaat bagi perusahaan manufaktur. Mempelajari cara menggabungkan data dari tingkat PL sehingga sistem di tingkat TI dapat menanganinya adalah bagian penting dari konvergensi.