Inklusi dalam Baja dan Pembuatan Baja Sekunder
Inklusi dalam Pembuatan Baja dan Baja Sekunder
Inklusi non-logam, (selanjutnya disebut sebagai 'inklusi'), adalah senyawa kimia yang terdiri dari setidaknya satu komponen non-logam, seperti belerang atau oksigen. Dalam baja, inklusi adalah fase yang tidak diinginkan tetapi terutama tidak dapat dihindari yang disebabkan oleh kandungan zat pengoksidasi dalam baja cair karena bahan baku atau diperkenalkan selama pembuatan baja. Inklusi dibentuk menjadi berbagai jenis tergantung pada kondisi termodinamika yang menguntungkan di hampir semua praktik perawatan yang melibatkan baja cair.
Efek berbahaya dari inklusi sangat tergantung pada komposisi kimianya, fraksi volume, dispersi, dan morfologinya. Biasanya inklusi besar dan tidak dapat dipecahkan dengan titik leleh tinggi adalah yang paling tidak diinginkan. Namun dibandingkan dengan inklusi ini, yang kecil dan mudah pecah atau yang memiliki titik leleh lebih rendah lebih disukai. Alasan untuk preferensi ini adalah bahwa inklusi yang memiliki titik leleh lebih rendah atau mudah pecah cenderung berubah bentuk, dihancurkan menjadi inklusi yang lebih kecil, atau menghilang dalam proses pembentukan panas atau dingin (efek proses pembentukan dan rasio reduksi) atau perlakuan panas yang baja dapat memiliki setelah pengecoran berkelanjutan dan proses pemadatan.
Inklusi utama dalam pembuatan baja adalah oksida dan sulfida. Mereka terbentuk sebagai hasil dari proses pembuatan baja dan karenanya merupakan bagian integral dari baja. Sedangkan oksida biasanya dianggap berbahaya, sulfida memainkan peran rumit dalam menentukan sifat baja seperti kemampuan mesin.
Terlepas dari beberapa aplikasi di mana inklusi seharusnya dituntut, seperti sulfida untuk meningkatkan kemampuan mesin, mereka biasanya menurunkan sifat mekanik dan kualitas permukaan produk baja dan dapat menyebabkan penyumbatan nosel dan gangguan proses pembuatan dan pembentukan baja. Dipercaya secara luas bahwa karena adanya inklusi sulfida dan oksida, beberapa sifat mekanik baja seperti keuletan, ketangguhan, anisotropi, dan kemampuan bentuk dapat terpengaruh secara negatif. Sisa inklusi di dalam matriks baja merusak sifat mekanik dan mengakibatkan kegagalan material.
Persyaratan kualitas yang diminta untuk produk baja cor terus-menerus semakin ketat dalam beberapa tahun terakhir untuk memenuhi permintaan pelanggan berdasarkan kebutuhan untuk meningkatkan produktivitas dan efisiensi melalui produksi produk tanpa cacat dan peningkatan kinerja pemrosesan.
Adanya inklusi dalam baja cair secara umum merupakan salah satu faktor utama yang menyebabkan cacat kualitas yang disebabkan oleh pembuatan baja, dan hal tersebut tidak hanya secara langsung menyebabkan cacat produk tetapi juga menyumbat nozel, sehingga menyebabkan kelainan pengoperasian seperti pergeseran baja cair dalam cetakan dan jebakan bubuk, sehingga secara tidak langsung menyebabkan cacat produk juga.
'Baja dengan kebersihan tinggi' tidak dapat dinyatakan secara sederhana karena persyaratan karakteristik kualitas bervariasi tergantung pada penggunaannya, dan karenanya, ukuran inklusi, komposisi, dan jumlah yang dapat diterima juga bervariasi tergantung pada penggunaan baja tersebut. Istilah 'baja bersih' digunakan dengan hati-hati. Hal ini karena (i) berbagai tuntutan kebersihan baja untuk aplikasi yang berbeda, (ii) berbagai kebersihan dalam baja yang diproduksi dalam operasi yang berbeda, dan (iii) pemahaman yang normal dari kata 'baja bersih', yang beberapa orang mengartikannya secara harfiah berarti tidak adanya inklusi dalam baja.
Definisi 'bersih' tidak mutlak, tetapi tergantung pada proses produksi baja individu dan penggunaan produk akhir dalam layanannya. Istilah 'baja bersih' karenanya bervariasi tergantung pada produsen baja dan aplikasi baja. Karena sifat variabel dari istilah 'baja bersih', kadang-kadang diusulkan untuk berbicara lebih akurat tentang (i) baja kemurnian tinggi sebagai baja dalam kasus tingkat zat terlarut yang rendah (sulfur, fosfor, nitrogen, oksigen, dan hidrogen) dan (ii) baja sisa rendah sebagai baja dengan tingkat pengotor yang rendah (tembaga, timbal, seng, nikel, dan kromium untuk beberapa nama) sebagian besar berasal dari skrap.
Kebersihan baja memiliki implikasi baik dari sudut pandang operasional dan kinerja produk. Istilah 'baja bersih' biasanya digunakan untuk menggambarkan baja yang memiliki (i) elemen terlarut tingkat rendah, (ii) tingkat elemen residu yang terkontrol, dan (iii) frekuensi rendah oksida yang dibuat selama pembuatan baja, metalurgi sendok, pengecoran, dan bergulir.
Baja bersih adalah baja dengan frekuensi cacat produk yang rendah yang dapat dikorelasikan dengan inklusi oksida. Selain itu, baja bersih semakin dipahami sebagai baja yang komposisinya dikontrol ketat oleh elemen paduan untuk meningkatkan sifat produk dan konsistensi sifat. Ada satu konstanta dalam memproduksi baja dengan kemurnian tinggi, residu rendah, dan bersih , yang merupakan upaya terus-menerus untuk mengurangi elemen terlarut dan residu dalam baja dan mengontrol frekuensi, distribusi, dan ukuran inklusi.
Penilaian kebersihan pada baja mengalami masalah. Hanya ada sedikit inklusi besar (makro), yang sulit dideteksi karena jumlahnya kecil. Sebaliknya, jumlah inklusi yang sangat kecil (mikro) hampir sangat kecil dan ukurannya membuat mereka hampir tidak terdeteksi. Tampaknya 5 mikrometer (0,005 mm) mewakili batas antara inklusi mikro yang dapat ditoleransi dan inklusi makro yang berpotensi berbahaya. Inklusi besar yang sporadis ini mewakili masalah kualitas utama bagi pabrik baja dalam memproduksi baja bersih.
Baja bersih, selain menurunkan inklusi oksida dan sulfida, dan mengontrol komposisi dan morfologinya, perlu menurunkan sisa pengotor lainnya seperti kandungan fosfor, hidrogen, dan nitrogen serta elemen jejak lainnya dalam baja. Terkadang konsep baja bersih diperdebatkan sebagai konsep yang bisa diperdebatkan. Karena istilah baja bersih itu relatif, dan memang benar untuk mengatakan bahwa 'kebersihan baja, seperti keindahan, sangat diperhatikan oleh yang melihatnya'. Lebih lanjut, sesuai argumen, konsep tersebut mengarah pada kesan bahwa baja dengan jumlah inklusi yang lebih sedikit lebih unggul dalam kinerja yang tidak selalu demikian.
Ada nilai baja yang berbeda yang diproduksi untuk tujuan yang berbeda. Tingkat kebersihan baja untuk setiap tujuan tergantung pada jumlah inklusi, morfologi, komposisi dan distribusi ukuran setiap kelas baja. Misalnya, dalam pemesinan bebas atau baja yang disulfurisasi, desainnya tidak sepenuhnya menghilangkan inklusi tetapi memodifikasinya untuk meningkatkan kemampuan pemesinan. Oleh karena itu, pendapat yang seimbang mengenai tingkat penyertaan atau kebersihan yang diizinkan untuk setiap grade baja benar-benar sangat penting secara teknis dan ekonomis baik bagi pembuat baja maupun pengguna. Untuk sebagian besar, baja bersih diperlukan untuk memenuhi spesifikasi dan persyaratan pelanggan untuk aplikasi yang berkaitan dengan karakteristik penyertaan.
Adanya inklusi pada baja tidak terlepas dari proses pembuatan baja. Kehadiran mereka sering dianggap berbahaya, tetapi terkadang sama-sama menguntungkan. Apapun efeknya, keberadaannya dalam baja merupakan bagian dari proses pembuatan baja dan harus dimanfaatkan untuk keuntungan sifat baja akhir.
Komposisi kimia inklusi dan fraksi volumenya ditentukan oleh pengelolaan berbagai langkah yang terlibat dalam proses produksi baja yaitu (i) pembuatan baja primer, (ii) pembuatan baja sekunder, dan (iii) operasi pengecoran kontinu. Oleh karena itu, populasi inklusi bergantung pada hubungan yang ada antara parameter operasi yang diterapkan dan fitur grade baja yang diproduksi.
Berdasarkan asalnya, inklusi dapat berupa partikel oksidasi, fragmen refraktori, entrainment terak atas, dan produk reoksidasi, dll. Berbagai metode diterapkan untuk menghilangkan inklusi, seperti pengadukan sendok, pemurnian terak, operasi tundish, dan cetakan pengecoran kontinu. Penghapusan inklusi dalam cetakan pengecoran kontinyu sulit karena baja cair menjadi padat dan inklusi memiliki sedikit kesempatan untuk mengapung keluar. Penghapusan inklusi dan distribusi akhir inklusi dalam produk baja sangat bergantung pada sifat inklusi, pengangkutan inklusi dalam baja cair dan interaksi antara inklusi dan cangkang pemadatan. Oleh karena itu, pemahaman tentang jebakan inklusi dan distribusi akhir mereka dalam produk baja penting untuk pengendalian kebersihan dan kualitas produk baja.
Salah satu fungsi dari pembuatan baja sekunder adalah untuk menghilangkan inklusi yang dihasilkan melalui deoksidasi rendaman baja selama proses tersebut. Pada dasarnya, setelah dimasukkan ke dalam baja cair, inklusi menjalani tiga tahap untuk dihilangkan. Tahapan tersebut adalah (i) flotasi, (ii) pemisahan, dan (iii) pelarutan. Langkah pertama melibatkan pengangkutan inklusi ke antarmuka baja / terak dan selama pemisahan kedua, tegangan permukaan baja pecah, memungkinkan inklusi stabil pada antarmuka baja / terak. Pada tahap akhir, pembubaran, kembalinya inklusi ke bak baja dihilangkan ketika sepenuhnya dimasukkan ke dalam terak. Jika dua langkah terakhir gagal dilakukan, penyertaan akan dikenakan re-entrainment ke dalam penangas baja cair melalui jebakan, tergantung pada pola aliran di sendok atau tundish.
Studi menunjukkan bahwa fase pemisahan untuk inklusi padat berlangsung sangat cepat. Dihitung bahwa, ketika diserahkan ke terak standar dalam pembuatan baja sekunder, inklusi padat membutuhkan waktu kurang dari 0,0007 detik untuk mematahkan tegangan permukaan baja setelah flotasi. Namun, dibutuhkan waktu yang cukup lama hingga 7 detik untuk inklusi mencapai antarmuka baja / terak. Perbedaan waktu ini disebabkan oleh sudut kontak yang lebih kecil antara partikel cair dan baja cair. Sebaliknya, waktu pelarutan untuk inklusi cair dapat diabaikan karena mereka larut dalam terak. Oleh karena itu, langkah ketiga dalam penghapusan inklusi adalah yang paling menonjol untuk inklusi padat. Inklusi ini memiliki kelarutan terbatas dalam terak dan karenanya sensitif terhadap karakteristik fisik dan kimia, gradien suhu, dan volume terak yang bersangkutan. Dengan demikian, perilaku penghapusan inklusi padat tunduk pada kontrol oleh perpindahan massa, kinetika reaksi dan interaksi kimia dengan terak. Pembubaran karenanya menjadi langkah pengontrol untuk menghilangkan inklusi padat dan menganalisis faktor-faktor yang berperan selama fase ini sangat penting untuk menjelaskan kapasitas penyerapan inklusi terak.
Dalam proses pembuatan baja sekunder, terak, baja dan sendok terlibat. Oleh karena itu komposisi terak, baja, dan sendok merupakan faktor yang sangat penting untuk mencapai sifat baja akhir yang diinginkan, dan mereka memiliki efek penting pada komposisi kimia, fraksi volume, dispersi, dan morfologi inklusi. Beberapa faktor terpenting yang dapat mempengaruhi sifat fisiko-kimia inklusi ditunjukkan pada Gambar 1.
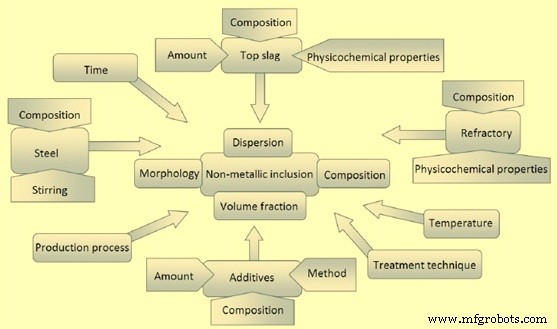
Gambar 1 Faktor yang mempengaruhi berbagai karakteristik inklusi selama pembuatan baja
Evolusi populasi inklusi dari waktu ke waktu selama perawatan sendok bisa menjadi kompleks. Mengingat bahwa efektivitas penghilangan inklusi dengan koagulasi, perlekatan gelembung, dan penangkapan antarmuka sangat tergantung pada komposisi, fase, dan morfologi populasi inklusi yang dikembangkan selama praktik perawatan sendok, terbukti bahwa ada periode waktu selama perawatan sendok di mana pembilasan dan perawatan flotasi lebih efektif daripada yang lain. Kemampuan untuk mengembangkan strategi perawatan sendok untuk memanfaatkan waktu perawatan yang disukai ini di mana tingkat pengasaran dan penghilangan inklusi adalah yang paling cepat pada akhirnya tergantung pada kebersihan penambahan perawatan pasca-flotasi, kontrol reoksidasi, dan masuknya terak selama pengadukan dan efektivitas perlindungan reoksidasi selama pemindahan baja.
Proses pengolahan sendok adalah proses kunci untuk produksi baja dengan kandungan inklusi rendah dan komposisi inklusi dan morfologi yang tidak merugikan produk atau proses pembuatannya. Namun, proses perawatan sendok juga melayani beberapa fungsi lain yang terkadang dapat bertentangan dengan produksi baja bersih. Langkah-langkah perawatan sendok yang paling umum termasuk deoksidasi baja dan terak, desulfurisasi baja, paduan baja, menyesuaikan suhu baja untuk transfer ke mesin pengecoran kontinu, kontrol gas terlarut seperti nitrogen dan hidrogen, modifikasi inklusi, dan penghapusan inklusi, seperti yang ditunjukkan pada Gambar 2.
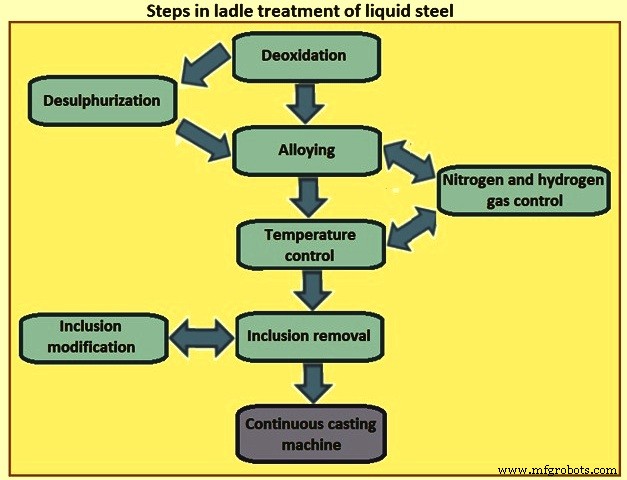
Gbr 2 Langkah perawatan sendok baja cair
Jenis praktik deoksidasi yang digunakan dalam proses pembuatan baja memainkan peran penting dalam jenis inklusi yang terbentuk selama perawatan sendok. Untuk banyak produk batangan dan struktur, baja dideoksidasi dengan silikon dan mangan (Si-Mn terbunuh) sedangkan untuk produk lembaran, pelat dan batangan berkualitas, baja dideoksidasi dengan aluminium (Al terbunuh). Beberapa baja aluminium yang terbunuh juga diperlakukan dengan kalsium untuk memodifikasi inklusi alumina dan inklusi yang mengandung belerang untuk meningkatkan kemampuan cor baja dan sifat mekanik produk. Inklusi yang berkembang selama perawatan sendok dapat sepenuhnya padat, sepenuhnya cair, atau campuran padat dan cair.
Teknologi pembuatan baja sekunder seperti metalurgi sendok dan degassing vakum sangat mengontrol inklusi dalam baja. Penggunaan metalurgi sendok untuk reaksi logam terak terkontrol, paduan mikro, dan kontrol bentuk inklusi telah menghasilkan peningkatan besar dalam proses pembuatan baja. Peningkatan lain yang dicapai dalam pembuatan baja bersih saat ini mencakup peningkatan praktik deoksidasi, pengadukan, penghilangan gas vakum, dan peleburan kembali terak elektro. Selain itu, prosedur penimbunan yang lebih efektif dan ketat serta penggunaan penimbunan yang menanjak dengan selubung padat yang efektif telah sangat berkontribusi pada pengurangan reoksidasi, dan karenanya sangat mengurangi pemasukan oksida dalam baja.
Biasanya setelah menyelesaikan proses pembuatan baja sekunder karena kurangnya pengadukan terak-baja yang cukup dan dengan sedikit kemungkinan menambahkan bahan tambahan, tidak mudah untuk membuat perubahan apa pun pada sistem dan karenanya morfologi, fraksi volume, komposisi, dan dispersi non -Inklusi logam pada akhir proses pembuatan baja sekunder tidak dapat dengan mudah diubah. Namun, ada kemungkinan efek kecil dari serbuk tuang dalam cetakan dan lapisan tundish selama pengecoran kontinu dan proses pemadatan. Proses deoksidasi yang digunakan dalam praktik pembuatan baja sekunder dijelaskan di bawah ini.
Proses deoksidasi Si-Mn – Kombinasi deoxidizers (silico-mangan, ferro-silicon, dan ferro-manganese) biasanya digunakan untuk hasil yang lebih baik. Deoksidasi parsial biasanya digunakan selama proses peleburan dan proses deoksidasi akhir dicapai dalam sendok. Praktek ini mempromosikan pembentukan produk deoksidasi titik leleh rendah yang mudah dihilangkan dari baja cair. Deoksidasi Si-Mn-Si (silikon-mangan) sering membentuk inklusi silika padat dan silikat mangan cair. Terdapat rasio kritis [%Si] / [%Mn] pada suhu tertentu yang mempengaruhi jenis produk deoksidasi yang terbentuk seperti yang ditunjukkan pada Gambar 3. Untuk komposisi ke sisi kiri kurva pada Gambar 3, silika padat cenderung terbentuk sedangkan silikat mangan cair cenderung terbentuk di sebelah kanan kurva di mana kandungan mangan lebih tinggi. Reaksi kesetimbangan reaksi deoksidasi Si-Mn diberikan oleh persamaan [Si] + 2MnO =2[Mn] + SiO2.
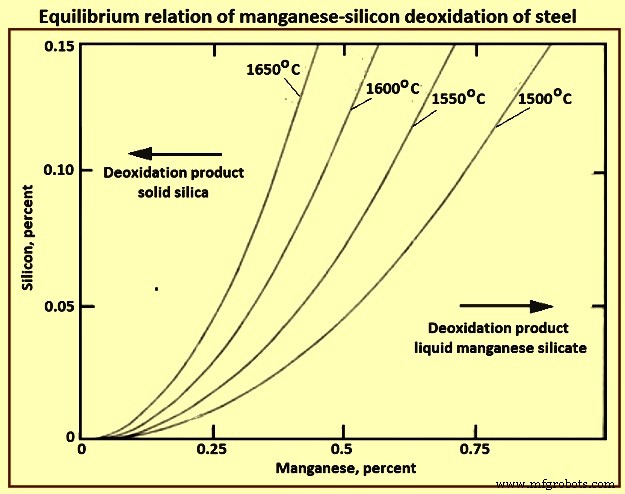
Gbr 3 Hubungan kesetimbangan deoksidasi silikon-mangan baja
Oleh karena itu, penurunan rasio Si / Mn menghasilkan inklusi silikat mangan cair. Inklusi silikat mangan cair lebih kaca dan plastis dalam deformasi ketika digulung panas. Namun, indeks plastisitas dari jenis inklusi ini menurun dan menjadi lebih rapuh saat digulung dingin. Ketika kombinasi silikon-mangan, dan aluminium digunakan untuk deoksidasi, mangan dan silikon diisi dalam bentuk paduan besi selama proses peleburan dan aluminium digunakan dalam sendok untuk deoksidasi akhir. Inklusi dalam sistem ini terutama terdiri dari alumina, silika dan mullite ketika kandungan mangan rendah. Namun, silikat mangan cair terbentuk dengan meningkatnya suhu ketika kandungan mangan dari baja tinggi. Salah satu studi menunjukkan bahwa, untuk membentuk inklusi cair pada suhu pembuatan baja, area komposisi (untuk garis L1 dan L2, dan garis ketiga yang mewakili 40% alumina maksimum) dibatasi oleh rasio SiO2 / MnO 17-1,9 dengan masing-masing Si / Rasio Mn 0,47-1,7 dalam konten inklusi masing-masing (Gambar 4).
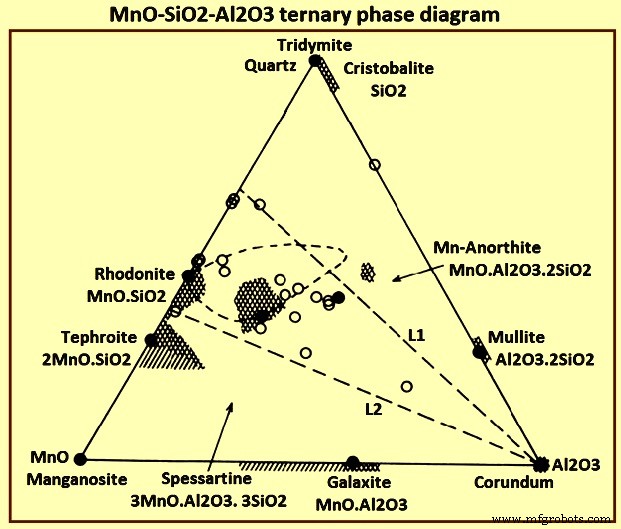
Gambar 4 diagram fase terner MnO-SiO2-Al2O3
Deoksidasi aluminium – Aluminium adalah salah satu deoxidizer yang paling efektif digunakan dalam pembuatan baja. Baja yang dideoksidasi dengan aluminium biasanya mengandung inklusi alumina seperti korundum. Inklusi alumina padat dilaporkan menyebabkan penyumbatan nosel selama pengecoran kontinyu baja cair. Mereka lebih merugikan dan tidak diinginkan dalam baja. Inklusi alumina memiliki suhu leleh yang tinggi dan tetap padat pada suhu pembuatan baja. Selain itu, inklusi alumina bersifat keras dan tidak terdeformasi atau terdeformasi dengan cara getas saat digulung. Reaksi kesetimbangan deoksidasi aluminium adalah 2[Al] + 3[O] =Al2O3. Batang aluminium biasanya ditambahkan ke baja cair untuk deoksidasi.
Perlakuan kalsium pada baja – Kalsium memiliki afinitas yang kuat untuk oksigen dan karenanya dapat digunakan sebagai deoxidizers. Namun, penggunaan kalsium sebagai deoxidizer ditantang oleh titik didihnya yang rendah yaitu 1.439 derajat C, kelarutan kalsium yang terbatas (0,032 %) dalam baja pada 1.600 derajat C, dan tekanan uap yang tinggi sebesar 0,183 MPa pada 1.600 derajat C. Sifat-sifat ini membuat sulit dan tidak ekonomis untuk menggunakan kalsium sebagai deoxidizers. Namun, kombinasi deoksidasi Ca dan Al atau Si / Mn membentuk inklusi primer yang dimodifikasi dengan aktivitas dan suhu leleh yang lebih rendah. Untuk alasan ini, dalam praktek pembuatan baja biasanya kalsium ditambahkan ke baja lebih sebagai pengubah inklusi daripada deoxidizer. Mayoritas nilai baja diperlakukan dengan kalsium menggunakan paduan Ca-Si atau campuran Ca-Fe(Ni) tergantung pada spesifikasi paduan. Biasanya perawatan ini efektif dilakukan setelah penambahan trim dan pembilasan argon. Kawat paduan Ca-Si biasanya disuntikkan ke dalam baja cair setelah proses deoksidasi aluminium. Gambar 5 menunjukkan skema modifikasi inklusi oleh kalsium dengan perlakuan kalsium baja.
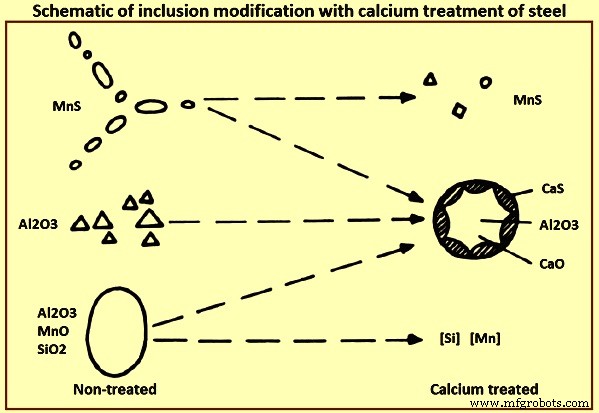
Gbr 5 Skema modifikasi inklusi dengan perlakuan kalsium pada baja
Setelah perawatan kalsium yang efektif, semua inklusi oksida biasanya mengandung sejumlah kalsium. Modifikasi efektif inklusi oksida dalam baja tergantung pada aluminium terlarut dan kandungan oksigen dari baja cair sebelum perlakuan kalsium. Untuk modifikasi inklusi penting, diperlukan batas bawah kalsium dari 15 ppm (bagian per juta) hingga 20 ppm. Inklusi kalsium aluminat dibentuk dengan rasio CaO-Al2O3 12:7, dan titik leleh rendah 1.455 derajat C kalsium aluminat. Inklusi ini ada dalam keadaan cair pada suhu pembuatan baja. Kalsium aluminat 12CaO.7Al2O3, 3CaO.Al2O3, dan CaO.Al2O3 berada dalam keadaan cair, sedangkan CaO.2Al2O3 dan CaO.6Al2O3 berbentuk padat pada suhu pembuatan baja.
Efek umum dari perlakuan kalsium pada modifikasi inklusi diringkas sebagai (i) mangan sulfida berkurang jumlah dan ukurannya, dan diubah menjadi Ca-Mn sulfida dengan berbagai sifat, (ii) aluminium oksida, yang biasanya keras, bersudut dan sering muncul dalam kelompok berkurang jumlahnya atau dihilangkan sama sekali dan diganti dengan inklusi CaO-Al2O3 atau CaO-Al2O3-SiO2 kompleks, (iii) silikat dihilangkan dan digantikan oleh inklusi CaO-Al2O3-SiO2, dan (iv) kompleks CaO- globular Inklusi Al2O3-SiO2 sering terbentuk dikelilingi oleh tepi sulfida.
Modifikasi sulfida dengan penambahan kalsium – Sulfur memiliki kelarutan yang hampir tak terbatas dalam baja cair. Namun, kelarutan belerang dalam baja padat mendekati nol. Selama pemadatan, sulfida mengendap dalam berbagai bentuk pada batas butir yang menghasilkan cacat baja yang khas. Afinitas kimia kalsium terhadap oksigen lebih tinggi daripada belerang. Diperkirakan bahwa kalsium bereaksi dengan belerang, aktivitas belerang sekitar 19 kali lebih tinggi dari aktivitas oksigen dalam baja, suatu kondisi yang sulit dicapai. Oleh karena itu, tujuan memasukkan kalsium untuk modifikasi belerang adalah untuk mengubah mekanisme pelepasan belerang sedemikian rupa sehingga belerang terikat atau diendapkan di sekitar oksida yang mengandung kalsium dan tidak mengendap pada batas butir sebagai sulfida bebas selama pemadatan. Dalam baja yang diperlakukan bebas kalsium, belerang mengendap sebagai partikel kecil MnS dalam cairan terakhir yang membeku. Partikel MnS berubah bentuk menjadi stringer saat digulung panas. Namun, inklusi sulfida yang mengandung kalsium memiliki bentuk bulat yang tidak berubah bentuk selama pengerolan panas.
Tingkat modifikasi inklusi dalam baja merupakan fitur penting dalam pembuatan baja sekunder dengan perlakuan kalsium. Bagian dari kalsium yang ditambahkan ke dalam cairan mengalami reaksi dan tetap berada dalam cairan sebagai kalsium terlarut dalam bentuk inklusi atau masuk ke terak sebagai penyusun terak. Sisanya keluar dari sistem dalam bentuk uap. Sangat penting bahwa kalsium yang ditambahkan harus dikonsumsi oleh baja cair semaksimal mungkin untuk membuat injeksi kalsium menjadi efisien dan hemat biaya. Dalam hal ini, studi pemulihan kalsium merupakan faktor penting untuk optimasi proses.
Sifat baja meningkat dengan perlakuan kalsium pada baja cair. Perbaikan sifat tersebut meliputi (i) peningkatan sifat mekanik terutama pada arah melintang dan melalui ketebalan dengan memodifikasi MnS menjadi globular (Ca-Mn)S atau CaS yang tidak terdeformasi, (ii) peningkatan kemampuan mesin baja pada pemotongan tinggi dengan membentuk lapisan pelindung pada permukaan pahat yang memperpanjang umur pahat karbida, (iii) peningkatan kualitas permukaan dan kemampuan pemolesan, (iv) meminimalkan robekan lamellar pada struktur las dengan tahanan besar dan kerentanan baja untuk memanaskan ulang retak seperti pada zona las yang terpengaruh panas, dan (iv) peningkatan castability baja dengan mencegah atau meminimalkan penyumbatan nozzle.
Inklusi juga bisa ada sebagai fase tunggal atau sebagai inklusi multifase. Biasanya, inklusi cair cenderung menyebabkan penyumbatan daripada inklusi padat selama proses pengecoran kontinu. Namun, kecenderungan inklusi untuk menggumpal dan menyumbat sangat bergantung pada energi antarmuka dan sudut kontak antara sistem refraktori inklusi-logam-gas-gas.
Selama operasi di pabrik besi dan baja terintegrasi, belerang dapat dihilangkan dengan perlakuan awal logam panas saat aktivitas oksigen rendah. Dengan demikian, penghilangan belerang selama perawatan sendok dalam proses pembuatan baja terintegrasi menjadi lebih sedikit. Dalam pembuatan baja tungku listrik, bagaimanapun, penghilangan belerang harus dilakukan selama perawatan sendok setelah baja dan terak sepenuhnya dideoksidasi. Penghilangan belerang ini biasanya membutuhkan praktik deoksidasi yang lebih agresif dan pengadukan yang kuat untuk mencapai kadar belerang yang rendah dalam baja. Persyaratan pemrosesan untuk desulfurisasi dalam ladle dapat mempengaruhi komposisi dan morfologi inklusi yang terbentuk dalam proses. Misalnya, inklusi spinel Al2MgO4 mudah terbentuk pada baja yang dibunuh dengan aluminium yang mengalami perlakuan desulfurisasi kuat, sedangkan inklusi alumina (Al2O3) lebih umum pada baja yang tidak mengalami perlakuan deoksidasi dan desulfurisasi yang kuat.
Laju aglomerasi inklusi, flotasi, penangkapan dan retensi dalam lapisan terak merupakan fungsi yang kuat dari komposisi, morfologi dan fase (padat atau cair) populasi inklusi dalam ladle. Sementara inklusi cair mudah larut dalam terak begitu mereka melewati antarmuka logam terak, mereka juga cenderung tidak menggumpal, mengapung dan lolos ke lapisan terak daripada inklusi padat saat berada di penangas baja. Perilaku ini, secara umum, menyebabkan tingkat pengkasaran dan pengapungan yang lebih rendah untuk inklusi cair daripada inklusi padat dan, karenanya, tingkat penyisihan inklusi keseluruhan yang lebih rendah untuk inklusi cair dibandingkan dengan inklusi padat.
Pembentukan inklusi selama deoksidasi
Agar baja cair dapat dicor dalam mesin pengecoran kontinyu, oksigen terlarut dalam baja cair harus cukup dikurangi untuk menghindari evolusi gas CO (karbon mono-oksida) selama pemadatan. Elemen yang paling umum digunakan dalam deoksidasi baja adalah mangan, silikon, aluminium, dan kalsium. Praktek deoksidasi kompleks dapat digunakan yang menggabungkan deoksidan ini. Dalam beberapa kasus, titanium, zirkonium, dan tanah jarang juga dapat digunakan untuk deoksidasi.
Kesetimbangan antara berbagai penambahan deoksidan dan oksigen dalam baja juga dapat dihitung untuk berbagai elemen dan pada berbagai konsentrasi dan suhu menggunakan perangkat lunak termodinamika. Perangkat lunak ini mampu menghitung kondisi kesetimbangan untuk deoksidasi kompleks dan juga dapat menjelaskan interaksi atom terlarut orde tinggi dalam baja yang mengarah pada kelarutan oksigen retrograde yang diamati dengan deoksidan kuat. Seperti yang ditunjukkan pada Gambar 6, diperlukan beberapa waktu untuk mendekati konsentrasi kesetimbangan dalam komposisi baja curah karena dibutuhkan beberapa waktu untuk inklusi untuk menggumpal dan mengapung dari baja. Kandungan oksigen baja dapat sangat bervariasi sebelum deoksidasi. Tingkat oksigen khas BOF (tungku oksigen dasar) dan EAF (tungku busur listrik) pada penyadapan tungku dapat berkisar dari 200 ppm hingga 800 ppm oksigen. Selain itu, deoksidasi parsial terkadang dilakukan selama penyadapan menggunakan mangan, silikon dan / atau aluminium. Ketika deoksidan ditambahkan ke baja cair, oksigen terlarut dalam baja bereaksi dengan penambahan deoksidan untuk membentuk oksida sesuai persamaan xM (dalam baja) + yO (dalam baja) =MxOy (inklusi.
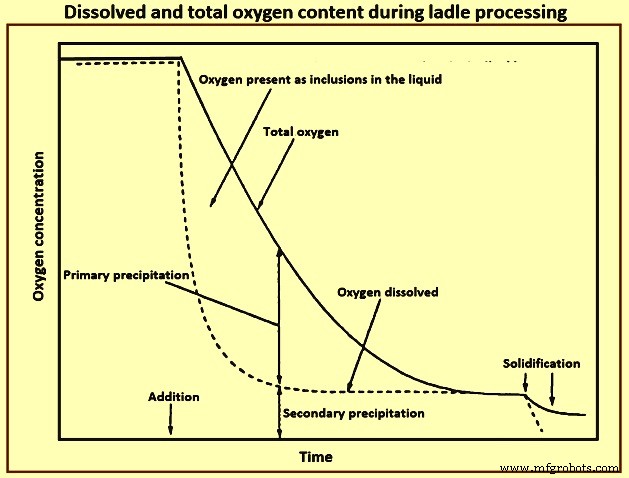
Gbr 6 Kandungan oksigen terlarut dan total selama pemrosesan sendok
Nukleasi oksida dapat terjadi dengan nukleasi homogen, terutama (i) ketika tingkat supersaturasi logam terlarut dan oksigen tinggi, atau (ii) dapat terjadi dengan nukleasi heterogen pada inklusi yang terbentuk lebih awal selama proses pembuatan baja, atau ( iii) pada gelembung argon yang digunakan untuk mengaduk sendok atau (iv) pada dinding tahan api sendok. Laju nukleasi dipengaruhi oleh tingkat supersaturasi dan energi antarmuka produk deoksidasi yang kontak dengan baja. Rasio super-saturasi dan energi antarmuka antara baja dan oksida keduanya mempengaruhi jari-jari kritis untuk nukleasi, dan karenanya mempengaruhi ukuran dan jumlah inklusi yang awalnya terbentuk pada awal deoksidasi.
Biasanya diterima bahwa nukleasi terjadi sangat cepat pada penambahan awal deoksidan dan bahwa nukleasi homogen dan heterogen dapat terjadi. Telah ditemukan bahwa ada hubungan yang kuat antara tingkat oksigen dan ukuran inklusi yang terbentuk dan bahwa tahap awal pembentukan inklusi dikendalikan oleh difusi oksigen dalam baja cair.
Sangat menarik untuk dicatat bahwa waktu yang dibutuhkan untuk mencapai komposisi yang seragam dalam sendok yang diaduk dengan argon adalah dalam orde menit, sedangkan waktu untuk nukleasi biasanya dalam orde 0,1 detik atau kurang. Ini menyiratkan bahwa berbagai tingkat penambahan deoksidan dicampur dan tersebar di sendok. Hal ini dapat mengarah pada pembentukan berbagai kemungkinan morfologi inklusi dalam rendaman baja, tergantung pada konsentrasi deoksidan lokal dan tingkat kejenuhan oksigen yang ada di berbagai daerah di dalam sendok.
Nukleasi dapat terus terjadi sampai supersaturasi tidak ada lagi. Pada titik ini, nukleasi lebih lanjut hanya dapat terjadi ketika suhu baja menurun, ketika elemen paduan ditambahkan ke baja atau ketika oksigen dimasukkan kembali ke dalam baja selama peristiwa reoksidasi. Dalam kondisi ini, tingkat super-saturasi biasanya jauh lebih rendah dan nukleasi heterogen dari oksida baru ke inklusi yang sudah ada biasanya lebih menguntungkan.
Evolusi penyertaan setelah deoksidasi
Pengarasan, aglomerasi, dan penghapusan inklusi – Setelah populasi inklusi berinti, inklusi dapat tumbuh dengan berbagai mekanisme. Ukuran partikel rata-rata dari populasi inklusi dapat meningkat melalui pematangan Ostwald, melanjutkan nukleasi heterogen pada inklusi yang sebelumnya berinti, dan melalui aglomerasi partikel. Tumbukan partikel yang mengarah pada aglomerasi dapat terjadi melalui gerak Brown, gerak turbulen, gradien kecepatan, dan tumbukan Stokes. Jembatan rongga juga dapat mempromosikan daya tarik dan aglomerasi partikel non-pembasahan. Gambar 7 menunjukkan mekanisme jembatan rongga dari aglomerasi partikel berdasarkan percobaan laboratorium yang secara langsung mengukur gaya tarik menarik antar oksida dalam baja cair.
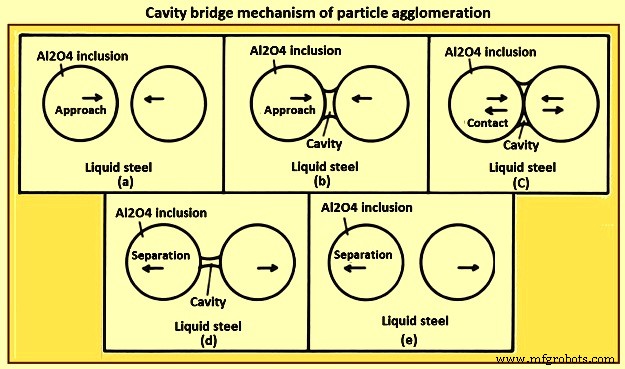
Gambar 7 Mekanisme jembatan rongga aglomerasi partikel
Ukuran inklusi dan kepadatannya mendorong penghapusan inklusi dari baja dengan flotasi. Hukum Stokes memberikan perkiraan kasar tentang efek diameter inklusi dan kepadatan partikel pada laju flotasi. The flotation rate is strongly favoured by a large inclusion diameter and a low inclusion density relative to the liquid steel density.
Rising bubbles from argon stirring also promote the removal of inclusions if wetting between the inclusion and the argon bubble is favourable for attachment. The fluid flows induced by argon stirring or electromagnetic stirring can also promote inclusion transport and removal to the slag layer or to the ladle wall. Fig 8 shows an overview of these mechanisms for inclusion growth and removal from the ladle.
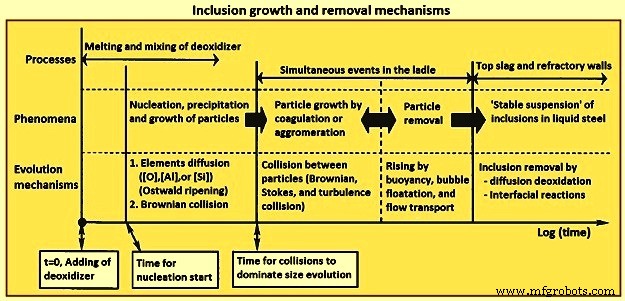
Fig 8 Inclusion growth and removal mechanisms
The effectiveness of argon stirring on inclusion removal depends on several factors which include porous plug location, number of plugs, the size of the ladle, the intensity of the stirring, and the contact angle of the inclusion with the steel and stirring gas. In general, liquid oxide inclusions tend to have much lower contact angles than solid oxide inclusions and normally have less than a 90 degree wetting angle. This has implications for particle agglomeration and bubble attachment mechanisms which influence the rate of inclusion removal from the ladle.
One of the studies has demonstrated that the rate of removal of particles from a fluid by gas bubbling is very dependent on the wetting angle of the particle-fluid-gas in a water model system, and that the removal rate drops sharply when the wetting angle drops to below 90 degrees. Steel systems also have similar effects. Argon bubbling has also been shown to selectively remove under-modified solid calcium aluminate inclusions from an inclusion population in the continuous casting machine tundish and argon stirring prior to calcium treatment has been seen to be more effective at removing inclusions than the argon stirring after calcium treatment.
Both inclusion agglomeration and bubble attachment mechanisms depend upon the interfacial energy and wetting angle between inclusions and the liquid steel and mechanisms which promote inclusion agglomeration and growth. Bubble attachment and cavity bridge agglomeration are both favoured by a large contact angle, suggesting that several solid inclusions are easier to remove from the ladle than liquid inclusions. The morphology of the solid inclusions can also influence agglomeration and flotation.
Macroscopically, the inclusion removal from the ladle can be observed by monitoring the total oxygen content of the steel or by evaluating the number or area density of the inclusions. For a given stirring intensity, stir configuration and inclusion population, longer rinse stir times normally result in progressively more inclusion removal. This is true both for argon stirring and stirring by other methods such as electromagnetic stirring.
Control of intensity of stirring in the ladle is important. While the increase of the stirring intensity leads to increased rates of inclusion removal, excessively increased stirring intensities can induce reoxidation by exposing the steel to air through the slag ‘eye’ where the slag is pushed back by the rising bubble plume or strong upward recirculating flow during the stirring. This condition can lead to a higher final inclusion content.
Recently, SEM-AFA (scanning electron microscopy – automated feature analysis) analysis has made it possible to analyze a large number of inclusions in a sample in a reasonable time. This has allowed the observation of the size distribution and population number density of inclusion populations at various stages in the process. It has been shown in a study that the shape of the inclusion size distribution changes with time, forming a log normal distribution early in the inclusion population’s life cycle and evolving to a power law or fractal size distribution later in the population’s life cycle when active nucleation is no longer taking place.
Several studies have reported similar trends in the evolution of the shape of the inclusion population in ladle deoxidation using models for nucleation and growth of inclusions during deoxidation in the ladle and by direct experimental observation. Observations of the shape of inclusion size distributions have been used successfully to identify reoxidation events, where oxygen from the air generates a new population of reoxidation inclusions which have a log normal distribution. On a log-log plot, this new population of reoxidation inclusions deviate from linearity for conditions of a tundish first fill and eventually subsiding and re-establishing a linear distribution. Similar observations have been there in the ladle after additions are made.
The type of deoxidant and the conditions of super-saturation employed in the deoxidation process have a strong influence on the rate at which the inclusion population changes over time. It has been observed that there is a rapid increase in diameter and reduction of the number of inclusions with time in aluminum deoxidized steels and little change in diameter and number with time in titanium and complex titanium-aluminum deoxidized steels. Also, there are large differences in the agglomeration rate of different inclusions in steel.
The size distribution of alumina clusters is observed to shift to progressively larger diameters and lower inclusion counts with time. By comparison, the size distribution of the titanium / aluminum complex deoxidant, which is liquid with a low wetting angle, does not increase in diameter with time and the inclusion count drops much more slowly with time because of the smaller overall diameter of the population.
Once the inclusions are transported to the slag layer in the ladle, the inclusions are to contact and become incorporated into the slag layer to be removed from the system. The rate of passage of inclusions through the slag-metal interface and the rate of dissolution of inclusions in a CaO-Al2O3 (lime-alumina) slag have been studied. During the study, it has been observed that alumina inclusions pass through the slag metal interface quickly, but that liquid MnO-SiO2-Al2O3 inclusions take much more time to pass through the interface and, in some cases, are not captured by the slag at all. It has also been found that the rate of inclusion dissolution in the slag is diffusion controlled for alumina inclusions dissolving in the slag.
The rate of dissolution of Al2O3 and MgO (magnesia) inclusions in various slags has also been studied. During the study, it has been found that in some slag systems, intermediate reaction products such as CaAl12O19 and Ca2Al2SiO7 formed on the inclusion surface and slowed the dissolution rate of the inclusion into slag.
The rate of dissolution of Al2MgO4 oxide spinel in slags of various compositions has also been studied. During the study, it has been found that the rate of dissolution is controlled by diffusion in the slag and is inversely related to the viscosity of the slag. If the time for passage through the slag–metal interface or the dissolution rate in the slag is slow, the slag-metal interface can become a site for solid inclusion agglomeration and re-emulsification of inclusions is possible.
Changes in inclusion composition during ladle treatment – The composition and morphology of inclusions can change considerably during the course of ladle treatment. The alloying additions made during ladle treatment can introduce elements which influence the overall composition and number of inclusions which are present. Also, additions such as calcium are used specifically for the purpose of modifying inclusion composition and morphology. Even in the absence of these additions, the inclusions present in a ladle after deoxidation can change composition over time through interactions with the slag and refractories used in the ladle, or with the atmosphere if the ladle stirring is aggressive.
Mini steel plants which produce aluminum killed steels with restricted sulphur levels frequently experience a shift in the inclusion chemistry during desulphurization. Under low oxygen conditions after the aluminum killing, argon stirring can promote the transfer of magnesium from the slag and the ladle refractory lining to the steel. During this process, the alumina inclusions gradually pick up magnesium and the inclusion population gradually shifts from Al2O3 to Al2MgO4 spinel. This exchange is influenced by the oxygen potential of the system and the composition of the slag. It has been found that MgO in slag and in the refractory both contribute to magnesium pickup and spinel formation, but that slag has a higher contribution to the pickup than the refractory.
While calcium treatment is used normally to convert solid alumina inclusions to liquid calcium aluminate inclusions to improve castability, calcium treatment is also quite successful at modifying solid spinel inclusions. Different studies have shown that spinel modification with calcium treatment reduces the magnesium content of the inclusion population and drives magnesium back into solution in the liquid steel. Subsequent exposure to reoxidation can result in the reformation of spinel inclusions through the reoxidation of magnesium in solution in the steel later in the process. These studies have also shown that CaS formed during calcium treatment can serve to suppress the reformation spinels during reoxidation by acting as a reservoir for calcium which can be released during reoxidation to further modify newly formed alumina. Under these conditions, the presence of some CaS in the inclusion population can be beneficial as long as it does not contribute to nozzle clogging during the continuous casting of steel.
It has also been shown that if the spinel inclusion population is high enough before calcium treatment, solid MgO inclusions can also form along with liquid calcium aluminate inclusions after the calcium treatment. This type of inclusion has been found to be very detrimental in high performance steel such as line-pipe steels. Such conditions can arise when aluminum killed steels are heavily aluminum deoxidized and held in contact with high MgO slags and refractories for extended periods.
Impurities in alloy additives also have a strong influence on the inclusion population and the efficiency of inclusion removal. For example, the effects of calcium content of ferro-silicon on inclusion composition and the tundish clogging sensitivity has been cited. In some steel melting shops, calcium in ferro-silicon is managed to modify inclusions directly without additional calcium treatment while in other operations calcium in ferrosilicon is to be restricted to avoid changes in alumina morphology which promotes clogging. The stage in the ladle furnace processing where inclusions are modified in relation to the application of soft argon stirring to remove inclusions can have a pronounced effect on the inclusion removal efficiency. Argon rinse stirring prior to calcium treatment, when solid inclusions are present, has been shown to be more effective at removing inclusions than argon rinse stirring after the calcium treatment, when the inclusions have been modified to liquid calcium aluminates.
In short, the evolution of the inclusion population over time during ladle treatment can be complex. Given that the effectiveness of inclusion removal by coagulation, bubble attachment and interface capture is highly dependent upon the composition, phase, and morphology of the inclusion population developed during the ladle treatment practice. It is obvious that there are time periods during ladle treatment where rinsing and flotation treatments are more effective than others. The ability to develop ladle treatment strategies to take advantage of these preferred treatment times where inclusion coarsening and removal rates are the most rapid ultimately is dependent upon the cleanliness of post-flotation-treatment additions, control of reoxidation, and slag entrainment during stirring and the effectiveness of reoxidation protection during steel transfer.