Otomatisasi, Pengukuran, dan Sistem Kontrol Proses Tungku Ledakan
Otomasi, Pengukuran, dan Sistem Kontrol Proses Blast Furnace
Pengoperasian tanur sembur modern yang efisien membutuhkan otomatisasi tingkat tinggi dalam hubungannya dengan sistem pengukuran dan sistem pemantauan dan kontrol. Sistem kontrol proses tanur sembur yang dikombinasikan dengan sistem optimasi tanur sembur menciptakan tingkat tinggi dalam otomatisasi tanur sembur cerdas. Interaksi optimal antara model canggih dan sistem pakar memberikan bantuan komprehensif kepada operator instalasi dan meminimalkan risiko kesalahan manusia.
Masalah yang berkaitan dengan otomatisasi proses tanur tinggi, sistem pengukuran dan kontrol yang akan ditangani berkisar dari masalah teori kontrol klasik sistem linier dan nonlinier, tunggal, dan multivariabel dalam kontrol proses, hingga pertanyaan tentang kontrol operasional dan produksi. Untuk ini, sistem operasi yang kompleks harus diterapkan. Sistem ini harus memulai dan menghentikan modul program khusus ('tugas') secara otomatis, tanpa operator sehingga untuk memenuhi apa yang disebut 'kondisi waktu nyata' dengan komputer harus bereaksi sepenuhnya dalam waktu maksimum yang ditentukan dengan jelas (tenggat waktu) untuk suatu peristiwa dalam proses. Tenggat waktu berkisar dari beberapa menit hingga beberapa detik.
Sistem otomatisasi, pengukuran, dan kontrol proses tanur sembur adalah salah satu kontributor utama keberhasilan operasi tanur sembur dan termasuk dalam faktor kunci efektivitas ekonominya. Kompleksitas proses tanur sembur dikombinasikan dengan meningkatnya permintaan akan efektivitas dan pengurangan dampak lingkungan telah mengharuskan perubahan dalam strategi pengendalian proses. Di masa lalu, perhitungan statis berdasarkan prinsip kotak hitam digunakan untuk menentukan beberapa titik setel mendasar dengan umpan balik terbatas dari proses. Jenis kontrol ini dapat memberikan hasil yang dapat diterima hanya jika proses memiliki penyimpangan kecil dari titik operasi stasioner. Karena ketidakstabilan proses, gangguan kecil dapat menyebabkan penyimpangan yang cukup besar dari titik operasi yang memerlukan koreksi titik setel yang biasanya digunakan metode AI (kecerdasan buatan).
Dengan variasi dalam komposisi muatan dan berbagai praktik operasi, dinamika proses harus diperhitungkan dengan menyediakan penghitungan ulang titik setel dan umpan balik langsung secara real-time. Salah satu prasyarat untuk kontrol proses dinamis adalah pengembangan sensor dan teknik pengukuran yang memberikan informasi waktu nyata tentang status proses. Evaluasi model dinamis memungkinkan untuk beralih dari pengawasan proses ke kontrol waktu nyata proaktif. Pendekatan yang berbeda mencerminkan situasi tertentu dan filosofi kontrol. Saat ini sistem kontrol proses tanur sembur didasarkan pada model dinamis dan memungkinkan kontrol on-line. Pendekatan dasarnya adalah mempertimbangkan tanur sembur sebagai suatu sistem yang mencakup pendinginan air, di mana material dan energi disuplai, reaksi kimia eksotermik dan endotermik berlangsung, dan energi dihamburkan dalam bentuk kehilangan panas ke permukaan yang didinginkan dengan air dan sebagai panas sensibel yang masuk. bensin.
Pengoperasian dengan biaya yang dioptimalkan, peningkatan proses yang tidak berkompromi dengan pemilihan material beban, kualitas produk tertinggi, dan pencapaian serta pemeliharaan produktivitas yang diinginkan adalah tantangan utama untuk otomatisasi, pengukuran, dan sistem kontrol proses tanur sembur tingkat lanjut. Perhitungan beban yang dioptimalkan dengan target kimia yang tepat dan kontrol loop tertutup berikutnya membentuk dasar untuk memproduksi logam panas dan terak berkualitas tinggi, sekaligus mengurangi konsumsi energi. Sistem optimasi menyediakan akses mudah ke semua parameter proses, sifat material, dan data produktivitas yang mencakup informasi pengisian, material beban kimia dan fisik, dan pengukuran proses sehingga kondisi optimal untuk memproduksi logam panas dan terak pada tingkat kualitas terbaik dapat ditentukan. .
Sistem otomatisasi, pengukuran, dan kontrol proses tanur sembur adalah kontrol proses dengan akurasi tinggi dengan informasi grafis online yang cepat. Ini memberikan operasi blast furnace yang stabil dan dapat direproduksi dengan kualitas logam panas yang konstan. Ini memastikan operasi pabrik independen shift di mana interaksi manual dikurangi seminimal mungkin. Hasilnya adalah pengoperasian tanur sembur yang lancar sepanjang waktu, peningkatan masa pakai peralatan, dan pengurangan biaya produksi. Gambar 1 menunjukkan gambaran umum tentang otomatisasi, pengukuran, dan sistem kontrol proses tanur sembur.
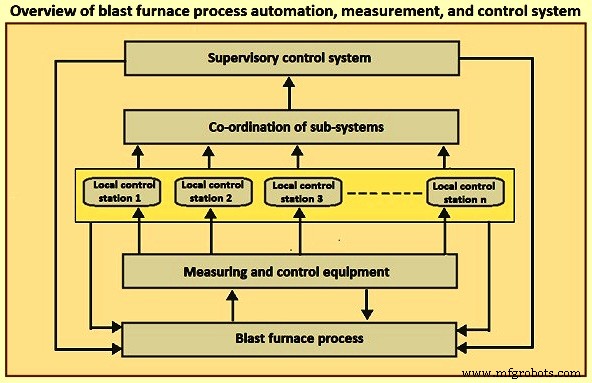
Gbr 1 Ikhtisar otomatisasi, pengukuran, dan sistem kontrol proses tanur tinggi
Keuntungan dari sistem otomatisasi, pengukuran, dan kontrol proses tanur sembur meliputi (i) produktivitas tinggi yang berarti mempertahankan kinerja tanur sembur pada kinerja puncak sambil meminimalkan konsumsi energi listrik dan bahan bakar, (ii) kualitas produk yang tinggi dan seragam yang berarti pemeliharaan sifat kimia logam panas dan terak pada tingkat yang diinginkan, (iii) pengurangan konsumsi bahan bakar sambil menjaga suhu logam panas konstan melalui modifikasi kecil laju bahan bakar, berdasarkan kondisi termal tanur tinggi, ( iv) operasi tanur sembur yang stabil, tidak bergantung pada shift, dan praktik terbaik sepanjang hari untuk memastikan produksi yang efisien, (v) integrasi yang mudah dari berbagai model dan paket metalurgi dengan sistem otomatisasi, pengukuran, dan kontrol, (vi) reaksi cepat dan fleksibel terhadap perubahan persyaratan, (vii) kemungkinan untuk perluasan sistem di masa mendatang, dan (viii) pengembalian yang sangat cepat pada i investasi.
Otomatisasi, pengukuran, dan kontrol proses tanur sembur biasanya terdiri dari sistem PLC (pengontrol logika yang dapat diprogram) dan HMI (antarmuka mesin manusia) pada otomatisasi Level-1 yang merupakan kontrol untuk semua proses kritis. Sarana kontrol ini dilengkapi dengan solusi Level-2 (model proses, sistem pakar, dan alat program), yang mencakup keseluruhan operasi BF atau bagian tertentu dari proses pembuatan besi (kompor sembur panas, dan pengisian tanur sembur, dll.). Sistem pakar digunakan untuk solusi Level-2 terintegrasi untuk tanur sembur. Sistem bantuan proses lanjutan ini mencakup kontrol tanur sembur dan analisis data waktu nyata dan optimalisasi proses serta analisis data tanur sembur yang ditangguhkan. Hal ini memungkinkan operator untuk mengoptimalkan produksi logam panas, dibantu oleh sistem berbasis pengetahuan dan melaporkan indikator kinerja dan angka produksi.
Dalam keseluruhan proses otomatisasi, pengukuran, dan sistem kontrol, komputer, pengontrol yang dapat diprogram, dan pengontrol mikro digunakan yang terhubung dalam bentuk jaringan kontrol area lokal untuk melakukan semua komunikasi dari tingkat perusahaan ke bawah ke pabrik dan sebaliknya dalam cara yang optimal. Sistem kontrol motor cerdas, terintegrasi dengan sistem kontrol, menyediakan kontrol terdistribusi dan data perawatan tambahan untuk meningkatkan diagnostik dan kinerja peralatan lapangan.
Sistem otomatisasi, pengukuran, dan kontrol proses tanur sembur memiliki (i) jaringan berkemampuan tinggi, terbuka, dan redundan, (ii) pemasangan kabel lapangan I/O (input/output) yang lengkap dan pertimbangan desain untuk mengurangi biaya pemasangan, (iii) minimal, instrumentasi HART (Highway Addressable Remote Transducer protocol) dengan kemampuan antarmuka HART dalam sistem kontrol, (iv) sistem manajemen aset yang mampu memelihara semua aset pabrik termasuk sistem kontrol, (v) antarmuka mulus ke aplikasi Level 2 untuk optimasi proses (jika belum dilakukan di Level 1) dan data historis dengan Level 2 yang mudah berkembang dengan platform kontrol Level 1, (vi) data Level 0/1 disimpan di file riwayat, untuk digunakan di HMI, atau di Level 2/3, (vi) proses dan laporan operasional, dan (vii) data operator dan pemeliharaan/sistem diagnostik. Protokol komunikasi HART adalah protokol terbuka otomasi industri analog + digital hibrida. Keuntungannya yang paling menonjol adalah ia dapat berkomunikasi melalui loop arus instrumentasi analog 4–20 mA lama, berbagi pasangan kabel yang digunakan oleh sistem host khusus analog.
Sistem otomatisasi tanur sembur tipikal menggunakan pengontrol proses, stasiun operasi yang terintegrasi di seluruh jaringan peer-to-peer 'Modbus plus' berkecepatan tinggi. Ini menghasilkan kontrol proses akurasi tinggi dengan informasi grafis online yang cepat. Terutama kompor sembur panas dan optimasi beban dengan interlock bukti bodoh untuk pengisian tanur sembur yang andal dan aman dan hasil distribusi beban menjadi operasi tanur sembur yang stabil dan dapat direproduksi dengan kualitas logam panas yang konstan
Karena tanur sembur adalah bejana reaksi yang sangat sederhana, sulit untuk mengontrol kondisi di dalamnya secara langsung dan hati-hati. Selain itu, karena proses dalam tanur sembur berubah sangat lambat, sekali operasi tanur yang stabil terganggu, sangat sulit untuk memulihkan keadaan normal. Oleh karena itu, penting untuk mempertahankan operasi yang stabil untuk memantau perubahan yang sangat kecil dalam kondisi di dalam tungku dan mengambil tindakan tepat waktu yang tepat. Untuk mencapai tujuan ini, komputer proses mengumpulkan dan menghitung data dari sensor yang disediakan di berbagai posisi tanur sembur, dan dengan demikian memantau kondisi tanur secara real time. Saat mendeteksi perubahan apa pun yang dapat berdampak buruk pada operasi stabil tanur tinggi, alat ini mengeluarkan panduan tindakan untuk operator tanur.
Lebih khusus lagi, fungsi pemantauan dan pengendalian sistem kendali proses tanur tinggi meliputi (i) kendali pengisian bijih dan kokas dengan melakukan perhitungan rasio pengisian bijih besi dan kokas serta urutan pengisiannya, (ii) kontrol operasi pengisian dengan pengaturan mode operasi saluran pengisian berputar sedemikian rupa sehingga distribusi melingkar yang memadai dari bijih dan kokas diwujudkan, (iii) kontrol kompor ledakan panas dengan kontrol pembakaran di kompor panas sehingga ledakan panas disuplai secara stabil , (iv) kontrol tungku dengan memperkirakan kondisi di dalam tungku berdasarkan informasi dari berbagai sensor, dan (v) kontrol penyadapan logam panas dan terak cair dengan kontrol jumlah dan kualitas logam panas yang disadap.Seperti yang terlihat di atas, otomatisasi, pengukuran, dan sistem kontrol proses tanur sembur memiliki peran yang sangat penting dalam pengoperasian tanur sembur.
Tungku sembur saat ini memiliki hampir seribu sensor yang terpasang di dalamnya. Sejumlah besar sensor dalam instrumentasi analog konvensional ini sulit dipasang di area pembuatan besi yang luas. Kemajuan mikro-elektronik dan sistem komunikasi data seperti jalan raya data memungkinkan untuk memperkenalkan instrumentasi digital terdistribusi. Ada beberapa keunggulan instrumentasi digital dibandingkan instrumentasi analog konvensional seperti (i) mampu membangun sistem bebas noise, terutama noise elektromagnetik, (ii) dapat menggunakan pemrosesan sinyal canggih dan fungsi kontrol lanjutan, (iii) keandalan sistem dapat ditingkatkan dengan penggunaan fungsi ganda, (iv) dengan menggunakan tampilan CRT (tabung sinar katoda) dimungkinkan untuk menerima lebih banyak informasi dari meja kontrol yang ringkas daripada panel instrumen analog besar sebelumnya, (v) jauh lebih mudah untuk mengubah atau meningkatkan sistem atau fungsi, (vi) lebih mudah untuk bertukar informasi dengan sistem komputer host, dan (vii) biaya instalasi jauh lebih murah daripada instrumentasi analog konvensional dari sudut pandang peningkatan fungsi. Untuk alasan ini, instrumentasi digital biasanya digunakan untuk otomatisasi, pengukuran, dan sistem kontrol proses tanur tinggi.
Kontrol tanur sembur yang efisien membutuhkan pengukuran yang andal terhadap kondisi di dalam tungku. Suhu di bagian bawah tungku dapat meningkat hingga lebih dari 2.000 derajat C, di mana sebagian besar teknologi pengukuran intrusif tidak dapat diandalkan, sehingga sebagian besar pengukuran dalam tungku dilakukan di atas atau di dekat permukaan beban. Operasi probe yang andal penting untuk mendukung, secara teratur, pemrosesan data, model proses tungku, dan sistem pengawasan operasi tungku. Probe yang andal membantu operator tanur sembur untuk menetapkan (i) profil suhu gas atas dan kimia gas atas, (ii) lintasan jatuh material, level dan profil garis stok, (iii) pembentukan lapisan beban, perilaku pencampuran dan penurunan, ( iv) profil gas dan suhu di kolom beban, (v) kondisi raceway dan coke bed, dan (vi) kualitas logam panas dan operasi sadap. Teknik yang paling penting untuk kuantifikasi langsung atau tidak langsung dari distribusi beban meliputi (i) probe di atas beban, (ii) probe di dalam beban, (iii) detektor garis stok, (iv) pengukur profil, (v) probe vertikal, (vi) termokopel, (vii) pengukur tekanan di dinding tungku, dan (viii) pengukuran lain-lain. Gambar 2 menunjukkan tata letak khas dari beberapa probe yang digunakan dalam tanur tinggi.
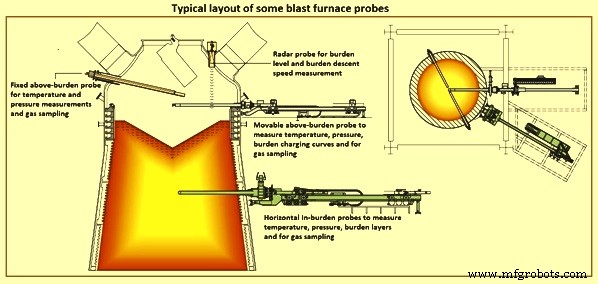
Gbr 2 Tata letak tipikal beberapa probe tanur sembur
Penyelidikan di atas beban – Probe di atas beban memiliki sejumlah termokopel yang terpasang pada perangkat untuk mengukur suhu gas pada posisi radial yang berbeda di atas permukaan beban. Ini memberikan informasi tentang kondisi aliran gas di tungku. Daerah dengan permeabilitas yang lebih rendah memungkinkan lebih sedikit gas mengalir yang mengurangi suhu gas dibandingkan dengan daerah dengan permeabilitas yang lebih tinggi. Oleh karena itu, pembacaan suhu memberikan informasi tentang kondisi permeabilitas dalam tungku.
Masalah dengan probe beban di atas adalah bahwa gas yang keluar dari permukaan beban bercampur sebelum mencapai probe. Oleh karena itu, beberapa suhu dapat diremehkan atau ditaksir terlalu tinggi. Oleh karena itu, probe dipasang lebih dekat ke permukaan beban, yang sulit diwujudkan karena permukaan beban dapat berubah selama proses dan dengan laju produksi. Selain itu, peningkatan stok-line yang tiba-tiba yang disebabkan oleh fluidisasi dapat merusak probe.
Penyelidikan terbebani – Probe dalam beban biasanya dipasang pada ketinggian berapa pun di bawah permukaan beban dan di atas zona kohesif. Oleh karena itu, probe ini harus bertahan pada suhu dan abrasi yang lebih tinggi dibandingkan dengan probe di atas beban. Inilah alasan mengapa mereka biasanya ditarik dan hanya dimasukkan ketika pengambilan sampel dilakukan. Probe in-burden mengukur suhu gas dan komposisi pada titik radial yang berbeda. Pengukuran secara umum lebih akurat daripada sinyal dari probe beban di atas karena pencampuran tidak terjadi pada tingkat yang sama. Namun, sebenarnya, hasilnya tergantung pada lapisan di mana titik pengambilan sampel berada pada saat pengukuran.
Detektor garis stok – Detektor jalur stok digunakan untuk memperoleh informasi tentang ketinggian permukaan beban, yang dikenal sebagai ‘jalur stok’, setelah mengisi setiap pembuangan ke tungku. Blast Furnace diprogram sehingga dump diisikan ke dalam Furnace hanya ketika permukaan beban telah turun melampaui level vertikal tertentu. Detektor garis stok dapat berupa perangkat mekanis (batang stok) di mana beban di ujung rantai atau kawat diturunkan sampai tercapai resistensi dalam bentuk permukaan beban. Tungku masa kini menggunakan teknik non-kontak, seperti sistem radar yang menghilangkan hilangnya waktu sambil menurunkan berat ke dalam tungku. Penurunan stok secara tiba-tiba merupakan indikasi slip, yang dapat menjadi perhatian operator tungku.
Pengukur profil – Pengukur profil pada awalnya merupakan perangkat mekanis tetapi sekarang telah digantikan oleh metode non-kontak, misalnya radar bergerak (probe bergerak) di sepanjang saluran horizontal yang mengukur ketinggian permukaan beban pada berbagai titik radial. Pengukur profil juga dapat memperkirakan kecepatan penurunan beban. Pengukur profil saat ini memiliki radar yang dipasang pada sambungan putar dan permukaan beban 3D dapat diperkirakan, yang memberikan pemahaman yang jauh lebih baik daripada dengan pengukuran sepanjang satu arah. Pengukuran level non-kontak dengan radar di tanur sembur memiliki beberapa keunggulan yang meliputi (i) pengukuran yang andal, tidak bergantung pada debu, komposisi material dan suhu tinggi, (ii) kepastian pengukuran yang tinggi bahkan selama pengisian, dan (iii) bebas aus dan perawatan operasi.
Penyelidikan vertikal – Probe vertikal digunakan untuk memberikan suhu dan komposisi gas di sepanjang ketinggian tanur sembur. Probe ini dapat terdiri dari kabel pada posisi radial yang berbeda yang diturunkan ke permukaan beban dan diseret ke bawah dengan menggerakkan padatan sampai ujungnya rusak, karena kabel mencapai suhu tinggi di bagian bawah tungku. Probe biasanya mengukur suhu dan tekanan dan dapat mengambil sampel gas untuk komposisi. Probe ini dapat dilengkapi dengan kamera untuk distribusi ukuran partikel. Panjang probe yang terkikis juga menunjukkan lokasi zona kohesif di tungku. Meskipun probe vertikal memberikan informasi maksimum tentang tungku, mereka jarang digunakan karena mahal dan membutuhkan peralatan makan yang rumit.
Termokopel – Dinding tanur sembur dilapisi dengan termokopel yang juga memberikan informasi penting tentang operasi tungku. Misalnya, perubahan mendadak dalam pembacaan termokopel dapat mengindikasikan jatuhnya tengkorak, yang merupakan massa padat yang stagnan yang terbentuk di dinding tungku.
Lingkungan yang keras yang disebabkan oleh suhu tinggi dan tekanan tinggi yang ditemui di kompor sangat mengurangi masa pakai termokopel, karena kontaminasi dan migrasi bahan ujung. Selubung logam yang digunakan untuk melindungi termokopel konvensional tidak dapat bertahan di atas 1.200 derajat C. Selubung alternatif mudah pecah atau rusak oleh ekspansi dan kontraksi bata keramik selama siklus pemanasan. Selain itu, pelepasan tekanan mendadak (atau 'mendengus') dapat menyebabkan penurunan pembacaan suhu antara 20 derajat C hingga 30 derajat C selama sekitar 30 detik. Hal ini membuat sinyal termokopel tidak cocok untuk digunakan dalam sistem kontrol pembalikan kompor otomatis. Dipasang dengan benar, sistem pirometer inframerah memberikan pengukuran suhu yang akurat untuk aplikasi kompor sekaligus mengatasi beberapa masalah yang dihadapi dengan penggunaan termokopel.
Pengukur tekanan di dinding tungku – Tekanan gas diukur pada titik yang berbeda di dinding. Saat gas mengalir melalui celah kokas arahnya horizontal, sehingga mempengaruhi tekanan di dinding. Oleh karena itu, informasi tekanan dapat digunakan untuk memperkirakan bentuk zona kohesif.
Pengukuran lainnya – Beberapa pengukuran lain di tanur sembur meliputi (i) tekanan, suhu, dan komposisi gas atas, (ii) laju aliran dan kenaikan suhu air pendingin, (iii) kondisi ledakan, (iv) logam panas dan variabel terak, (v) penggunaan probe perut, dll. (vi) kamera inframerah untuk mengukur suhu permukaan beban, dan (vii) termokopel aliran kulit (atau probe mini). Pengukuran ini secara tidak langsung dipengaruhi oleh distribusi beban.
Beberapa probe pengukuran tambahan yang digunakan dalam blast furnace adalah (i) probe pemindaian material (ii) probe tuyere, (iii) sampler inti, (iv) probe benturan (v) probe radar tingkat sendok torpedo, dan (vi) pengukuran resistansi dalam cangkang tungku.
Fungsi inti untuk pengoptimalan tanur tinggi
Optimalisasi tanur sembur adalah sistem optimasi proses inovatif yang mengangkat otomatisasi, pengukuran, dan sistem kontrol proses tanur sembur ke tingkat yang benar-benar baru. Solusi khas berdasarkan sistem dasar yang teruji dan terbukti memastikan ketersediaan tertinggi dan menggabungkan akuisisi, pemrosesan, dan visualisasi data secara efisien. Sistem menunjukkan keandalan dan penghematan biaya.
Spektrum yang luas dari sumber data mentah (termasuk sinyal ujung depan, jumlah bahan yang dibebankan, data laboratorium, kejadian, hasil model, dan data biaya) disimpan sepanjang masa pakai pabrik. Alat khusus disediakan yang memungkinkan informasi proses dihubungkan dengan data analisis dan matriks beban. Antarmuka yang fleksibel, modularisasi, dan arsitektur perangkat lunak yang andal menyediakan sarana untuk dengan mudah beradaptasi dan memelihara sistem dalam lingkungan bahan mentah yang terus berubah, filosofi operasi, dan konektivitas ke sistem pihak ketiga.
Selain sistem dasar yang kuat, sejumlah model proses yang saling berinteraksi mendukung operator dan manajer lini dalam keputusan harian mereka. Model proses metalurgi membuat proses tanur sembur menjadi transparan. Persyaratan khusus pabrik biasanya dimasukkan ke dalam model proses metalurgi ini.
Tujuan dari model dinamis adalah untuk terus menampilkan dan memprediksi status proses. Hal ini juga memungkinkan pengendalian berbagai parameter proses dengan strategi proses yang berlaku. Penentuan status proses didasarkan pada informasi yang diperoleh dari instrumen lapangan. Beberapa contoh model yang telah dikembangkan adalah (i) distribusi material dan posisi zona material tertentu, (ii) distribusi gas, (iii) distribusi suhu, (iv) keadaan termal tungku dan bagian-bagiannya, (v ) komposisi kimia logam panas dan terak di zona jatuh, (vi) ketinggian cairan perapian, (vii) geometri zona material (zona kohesif, zona jatuh, orang mati, dan ketahanan termal jangka panjang), dan (viii) geometri poros ( perancah). Model yang dikembangkan bersifat analitis, empiris, dan heuristik. Perhitungan berjalan secara siklis dan keluaran dari model ini adalah keadaan geometris, termal, dan material tungku serta karakteristiknya.
Model prediktif membuat simulasi real-time berdasarkan data aktual tentang input tungku. Model adalah tipe zonal. Proses yang dimodelkan adalah aliran gas, aliran material, proses termal, proses kimia, proses fisik, dan proses geometris. Keadaan tungku ditentukan untuk setiap elemen dengan keseimbangan panas dan material. Perhitungan didasarkan pada informasi yang diambil dari laboratorium dan instrumentasi lapangan yang memungkinkan penutupan saldo. Reaksi kimia dasar digunakan dalam model.
Transparansi ujung-ke-ujung secara real time melalui visualisasi data terkini dan model proses metalurgi menghasilkan kolaborasi yang lebih baik, alur kerja yang lebih baik, dan pengurangan kesalahan sekaligus mendukung pengambilan keputusan. Bahkan parameter proses penting seperti suhu nyala dan persentase reduksi tidak langsung diimplementasikan sebagai sensor lunak, yang membuatnya tidak dapat dibedakan dari pengukuran konvensional.
Teknologi informasi industri besi dan baja sedang bergeser, dan akses seluler diperkirakan akan melampaui akses berbasis desktop. HMI dirancang agar responsif dan fleksibel, baik itu desktop atau antarmuka multi-sentuh baru. Ini harus sederhana untuk memungkinkan operator bekerja lebih efisien dan efektif.
Dengan menggunakan pengukuran yang berbeda bersama-sama dan dengan pengalaman masa lalu, operator dapat memperoleh pandangan holistik tentang kondisi di tanur tinggi dan mengidentifikasi penyebab kondisi tanur yang tidak tepat. Otomatisasi proses, pengukuran, dan kontrol berbagai area tanur sembur dijelaskan secara singkat di bawah ini.
Otomasi pengisian gudang dan tungku penyimpanan – Otomatisasi pengisian gudang dan tungku dapat diimplementasikan mulai dari sistem mobil skala hingga sistem konveyor/penyaring/pengumpan otomatis penuh, menyediakan bijih kokas dan bahan lain-lain untuk dilewati atau tungku yang diberi sabuk. Ini termasuk kemampuan untuk membuat resep batch dari jarak jauh atau melalui HMI dengan program 'charge master' yang sepenuhnya otomatis. Program ini melacak aliran material dari tempat penyimpanan gudang penyimpanan hingga pengiriman ke bagian atas tungku, lengkap dengan koreksi kesalahan berat kering dan kompensasi kesalahan penimbangan, untuk mempertahankan komposisi dan level beban yang benar. Komponen penting untuk sistem yang sepenuhnya otomatis adalah penambahan sistem pengumpulan debu untuk menghilangkan dan mengekstrak emisi yang dihasilkan oleh proses penanganan material.
Sistem pengisian berbasis material memungkinkan penugasan dinamis berbagai material ke bunker gudang penyimpanan. Matriks pengisian hanya terkait dengan bahan yang tersedia dan tidak terkait dengan bunker. Efeknya adalah operasi pabrik yang lebih fleksibel tanpa perlu penyesuaian program. Sebagai alternatif, versi yang lebih rumit dari matriks pengisian berbasis bunker konvensional juga dapat digunakan. Terlepas dari jenis matriks pengisian, kompensasi cerdas dari penyimpangan dosis dianggap sebagai hal yang biasa. Kontrol rumah stok menghitung semua kemungkinan material yang tumpang tindih pada sabuk konveyor pengisian dalam kasus tungku diumpankan sabuk. Seiring dengan fungsi pelacakan material yang komprehensif dari gudang penyimpanan hingga tungku, operasi yang lancar dan efisien dapat dicapai.
Otomasi pengisian atas tungku – Otomatisasi untuk pengisian atas tungku mencakup (i) pemrograman sistem kontrol pengiriman material lonceng kecil / lonceng besar serta kontrol untuk sistem tanpa lonceng, (ii) pemantauan dan kontrol level jalur stok, (iii) tekanan atas tungku dan sistem bantuan, (iv) sistem pelumasan, (v) minimal, instrumentasi HART dengan kemampuan antarmuka HART dalam sistem kontrol, dan (vi) desain yang aman dan aman untuk kontrol katup pembuangan tekanan atas tungku, termasuk yang terkait sistem hidrolik.
Peralatan pengisian yang berbeda memberikan tingkat kontrol yang berbeda atas proses pengisian, yang pada akhirnya menentukan distribusi beban. Meskipun dengan beberapa opsi, proses pengisian daya bisa menjadi sangat rumit dan terkadang kontra-intuitif.
Solusi distribusi cerdas untuk semua jenis standar sistem distribusi material biasanya disediakan jika pengisian daya tanpa bel. Versi cerdas dari logika distribusi dering yang paling umum ditingkatkan dengan opsi untuk mengaktifkan pengisian spiral, dering penuh, dan distribusi berat atau waktu. Akibatnya, modifikasi distribusi yang fleksibel dan marjinal antara batch individu dimungkinkan. Pengisian spot dan sektor menawarkan kesempatan yang fleksibel dan mudah untuk bereaksi terhadap status tungku aktual di bawah kondisi tanur tinggi yang menuntut. Distribusi bentuk bebas yang mulus adalah kombinasi dari distribusi ring dan spot yang menerapkan variasi kecepatan ke perangkat distribusi. Mode ini menggabungkan distribusi mode dering yang stabil dengan fleksibilitas distribusi bentuk bebas.
Kontrol distribusi beban loop tertutup adalah fitur unik dari sistem otomatisasi untuk stabilisasi proses tanur tinggi dan pengurangan konsumsi bahan bakar. Berdasarkan pengukuran suhu radial di poros tanur sembur, model menghitung modifikasi pola distribusi untuk mencapai profil suhu target. Sistem ini mendukung baik probe dalam-beban atau pengukuran suhu di atas-beban berdasarkan teknik konvensional dan akustik.
Otomasi tungku dan perapian yang tepat – Otomatisasi tungku dan perapian yang tepat mencakup kontrol untuk pemantauan suhu proses, tren dan alarm, analisis off-gas, dan sistem probe di atas beban dan di dalam beban. Sebagai bagian dari sistem pemantauan, perhitungan proses dan produksi serta model pihak ketiga digunakan untuk memberikan pedoman operasional. Beberapa data ini meliputi (i) isoterm perapian dan dinding samping, (ii) distribusi beban, (iii) penggilingan batubara dan injeksi batubara bubuk, (iv) deteksi kebocoran tuyere dan kehilangan panas, (v) perhitungan proses seperti suhu nyala adiabatik, permeabilitas, dan kecepatan tuyere, dan (vi) data ke / dari sistem Level 2 (file data riwayat dan model proses).
Pengoperasian tanur sembur yang dioptimalkan membutuhkan pengisian bahan baku yang akurat, termasuk sinter, pelet, bijih, kokas, fluks, dan aditif. Untuk memodifikasi titik setel pengisian, laju kokas, kebasaan terak, dan analisis bahan baku aktual serta pengaruhnya terhadap parameter tanur sembur harus dipertimbangkan. Prosedur ini rumit dan membutuhkan bantuan model komputer. Model kontrol beban menghitung matriks pengisian berdasarkan komposisi beban yang dioptimalkan sementara model distribusi beban meningkatkan pemanfaatan gas melalui distribusi material yang tepat.
Dengan sistem pengoptimalan tanur sembur, operator memiliki transparansi data yang lengkap di seluruh proses. Berbagai macam proses dan meta-data (misalnya, shift, alarm, dan material) dibuat transparan, dapat diakses, dan dimengerti melalui laporan ringkas yang dihasilkan oleh sistem. Ubin pintar berfungsi sebagai pintu kaca yang secara otomatis menampilkan informasi langsung dari aplikasi favorit operator, bahkan jika aplikasi tidak berjalan. Jika terjadi penyimpangan signifikan dari parameter proses normal, data produksi terkait menjadi hidup di layar beranda, memungkinkan operator membuat keputusan penting dan mengambil tindakan korektif untuk situasi tersebut.
Tujuan dari model kontrol beban adalah untuk menetapkan komposisi beban yang tepat yang memenuhi nilai target yang ditetapkan untuk laju coke dan injeksi bahan bakar, kebasaan terak, kualitas logam panas, dan laju umpan beban. Hasil akhir dari model kontrol beban adalah matriks pengisian yang dapat ditransfer ke sistem otomasi dasar untuk dieksekusi dengan satu klik mouse. Dikombinasikan dengan sistem pakar, model kontrol beban adalah bagian utama dari optimasi komposisi beban yang sepenuhnya otomatis dalam pengoperasian tanur sembur.
Manfaat dari model kontrol beban meliputi (i) kualitas produk konstan yang berarti menjaga komposisi kimia logam panas dan terak pada tingkat yang diinginkan, (ii) modifikasi beban bebas pergeseran karena perhitungan komposisi beban baru dilakukan secara otomatis menggunakan analisis bahan baku terbaru dan prosedur perhitungan standar, dan (iii) tidak diperlukan interaksi operator manual untuk menghitung dan mengaktifkan matriks pengisian baru.
Peluncuran pengisian tanpa lonceng serta perangkat pengisi daya tipe lonceng dengan pelindung yang dapat dipindahkan memungkinkan distribusi yang tepat dari lapisan bijih dan kokas ke dalam tanur tinggi. Model distribusi beban membantu operator dan / atau manajer lini untuk memodifikasi distribusi aktual untuk meningkatkan pola aliran gas dan permeabilitas beban sesuai dengan persyaratan proses yang sebenarnya. The model simulates the burden descent through the blast furnace shaft and calculates the actual shape of the material layers in the upper part of the shaft. It also computes the radial volume, chemical properties, and particle size distribution, taking into account material segregation.
The on-line burden distribution model performs the calculation based on actual charging data and actual measurements of the stock-line and calculates the current burden distribution in the upper shaft of the furnace. This gives the operator the opportunity to detect irregularities in the burden distribution in a timely manner. In the off-line mode, the model calculation is based on a charging matrix and a pre-defined stock-line. The off-line burden distribution model is a valuable tool for the design of new distribution matrices for optimized gas-flow patterns and burden permeability.
3D hearth lining monitoring – 3D hearth lining monitoring is for safe, durable, reliable production at the blast furnace. The campaign duration of a blast furnace is mainly determined by the lifetime of its hearth. Hence, it is clear that monitoring the refractory thickness in the hearth wall and bottom areas is important for estimating the lifetime of the hearth lining.
The hearth wear model includes mathematical algorithms which solve the inverse heat transfer problem in 3 spatial dimensions based on the statistical evaluations of the thermocouple measurements and the heat conductivities of the refractories. The model calculates the erosion profile and the formation of the solidified skull layer. The computed wear velocity together with the remaining wall thickness allows the blast furnace operators and line managers to predict the lifetime of the hearth refractory.
The 3D hearth lining monitoring model includes user interfaces and reports for visualizing the results of the model over the entire life of the blast furnace. For every calculation, the HMI screens show 3D graphs of the actual and maximum wear lines. This means that the contour can be efficiently compared with the original lining, a single isothermal area with configurable temperature (e.g. 1,150 deg C) can be displayed, and horizontal and vertical angle ranges can be selected.
Thermal index calculation model – The energy consumption and productivity of the blast furnace are reflected by the thermal index, which can subsequently be used to predict the development of the hot metal temperature and silicon content. The model result is used as an input to the blast furnace expert system for controlling the thermal state of the blast furnace process.
Shaft calculation model – The model performs a mass-balance calculation based on actual charging data using the materials of one charge, consisting of one coke and one burden layer. These individual charges are tracked from the furnace top down to the tuyere area. The results are displayed graphically and allow the operator to track burden composition and burden distribution changes. The model also computes the time when burden changes become effective on hot metal and slag.
Mass and energy balance plausibility model – This model automatically generates reports based on actual charging, process, and production data over a pre-defined time period, taking into account the material retention time in the blast furnace. The mass and energy balance calculation is used to detect the build up of alkaline and zinc circuits or to identify systematic measurement inaccuracies. The subsequent balance plausibility algorithm indicates the most probable sources of measurement faults.
Automation of cast house – Stable and reproducible tapping operations are necessary for both the hot metal quality and the establishment of a smooth, efficient blast furnace process. Further, a clean and safe working environment in the cast house is achievable with good layout, accessibility and ergonomics. The cast house machines are to work together to provide this environment. Cast house automation provides for consistent, safe, operation of the cast house. It includes (i) control of mud gun and tap hole drill equipment, (ii) trough and runner temperature monitoring, (iii) tilting runner operation and monitoring of the level of hot metal in the ladle, (iv) process parameters of slag granulation, (v) monitoring of the cast house fume collection systems, and (vi) control schemes include radio operated belly box designs to fully automated gun-up and automated drilling logic.
The tapping management model calculates the actual hot metal and slag production rates as well as the drainage rates through the open tap holes. This allows it to continuously compute the actual amount and level of hot metal and slag in the hearth. The model result is used as an input to the blast furnace expert system, which makes a recommendation on opening a tap hole.
Automation of furnace cooling system – From shell plate spray cooling to closed loop stave cooling, the various options for furnace cooling and temperature monitoring and control are managed through a well instrumented and integrated control system. Heat flux monitoring and water treatment systems are integral to proper furnace cooling operations and longevity.
Leakage detection system for critical cooling circuits – Leakage detection system is essential from the point of view of safety. There is risk involved if there is no quick detection of the leakages. Expanding cracks or small water leaks in cooling system pipes can affect the quality of hot metal, lead to stoppage of production, damage to furnace, or in the worst case, loss of life.
A system which effectively detects leakage is hence not just one of the most important parts of the blast furnace process automation and control system, but more importantly, an integral part of the at the blast furnace. For this reason, the leakage detection is designed so as to meet the requirements of the safety standard for the instrumented systems for process industries sector.
Automation of stoves and hot blast delivery – Stove automation is for providing automatic cycling of stove valves to supply uninterrupted and consistent hot blast to the blast furnace. Stove cycling systems is designed for 2, 3, and 4 stove operation. Stove automation includes control of the process gasses and firing strategies, including Level 1 control optimization, and burner management capabilities. In addition, preheated air and gas supplies are used to reduce the amount of enrichment gas used in the stove heating cycle. Cold blast monitoring and control and hot blast temperature control, fuel injection control is included within the hot blast delivery system.
Present day blast furnaces are typically operated very close to the maximum hot blast temperature which the stoves can sustain. If the dome temperature does not increase rapidly enough, sophisticated controls are provided to enrich the blast furnace gas with a fuel of higher calorific value to achieve a faster heating rate. The use of the optimized combustion control consists of a number of features such as (i) control of excess air, (ii) consideration of flue gas oxygen or chemical combustibles analysis, or both, (iii) dome temperature influences on the gas enrichment ratio, and (iv) sequencing for either three or four stoves.
Optimization of hot stove is needed for achieving high efficiency, flexibility, and energy saving. The blast heating process offers considerable energy saving potentials. The challenge for the plant operators and the line managers is to optimize the energy input to the hot blast stoves while keeping the blast temperature at given targets of the blast flow rate and the blast time. The stove model ensures stoves optimization, and energy savings by increasing stove efficiency.
The hot stoves control model combines short term direct control and longer self-tuning algorithms. Rapid control is used to correct the firing rate for maintaining the proper stoves operation parameters. The fast controls reduce carbon di-oxide (CO2) emissions and maximize stove efficiency. Artificial intelligence algorithms are used to optimize the efficiency performance of the hot blast stoves. These self-learning algorithms enable operators to identify and correct measurement errors.
The hot blast stoves control model supports all operation modes in combination with various rich gas types. All the types of stoves (such as Cowper or Kalugin) as well as pre-heating and heat-recovery systems are normally covered in the model.
Automation of gas cleaning plant – Blast furnace gas is cleaned using a variety of methods including a cyclone or dust catcher to remove large particles and either annular gap water sprays or electrostatic precipitators. Semi-cleaned gas has also been used to drive a TRT (top gas recovery turbine) system for energy recovery. In either case, gas cleaning systems provide furnace top pressure control, as well as cleaned gas to be re-used for various processes including stove heating, and for use in the boiler house of the power plant.
Closed loop blast furnace expert system
The closed-loop blast furnace expert system is normally designed according to the principle ‘as few actions as possible, as many as essential’. The objective is to optimize blast furnace operation and reduce operator interactions to a minimum. The expert system, which is normally designed as a rule-based decision system, counteracts process fluctuations caused by changes in burden material composition and quality, human factors, and process conditions. The sooner the system responds to an abnormal or changing process situation, the smoother is the overall blast furnace operation. Timing control activities accurately and anticipating disturbances are both of the utmost importance in order to avoid critical process conditions and to maintain a high production rate at low costs. The closed-loop blast furnace expert system ensures considerable improvements to product quality and reduced fuel consumption with the available burden materials.
The expert system recommends operational changes in a two-step process. The first step is an analysis of the current situation, called process diagnosis. The expert system studies the occurrence of phenomena in the blast furnace using a variety of technical calculations based on a huge amount of process measurements and analysis data which are collected continuously. In the second step, corrective actions are proposed if needed. An extensive rule set forged by experienced blast furnace process experts and operators on the basis of cause-and-cure relationships results in recommendations for the best-practice and shift independent operation. Corrective actions to achieve and maintain the smooth operation of the blast furnace are reported to the operators. The actions can be executed either in closed-loop mode or after operator confirmation.
There are a set of major corrective actions which results in a continuous, shift-independent blast furnace operation. The guidance of the expert system, especially during start-up and shut-down periods, leads to energy savings and minimized production losses. This uniform operation contributes to prolonging the lifetime of the blast furnace. The set of major corrective actions are described below.
Fuel rate and injection control – The expert system observes the thermal state of the blast furnace hearth and suggests a change of the fuel rate as soon as significant deviations from optimal conditions are recognized. According to the rules defined in the knowledge base, either a change of injected fuel or coke rate is suggested and can be executed fully automatically.
Slag basicity control – On the basis of recent slag analyses and hot metal temperature data, the expert system recommends changes in the burden composition as soon as a deviation from the target slag basicity is detected. Working with the burden control model, a new charging matrix is calculated automatically which can be transferred to the process control system for execution.
Control of oxygen enrichment and steam addition – The oxygen enrichment control calculates an optimized oxygen addition rate to achieve the target hot metal production. Critical situations caused by rapidly increasing production rates can be avoided. The expert system uses steam addition to maintain the burden permeability at the targeted level. Because of the fast control cycles, it is possible to precisely adjust the addition of steam to the amount needed by the process. In this way the steam input is reduced whenever possible directly leading to energy-savings.