Sistem Otomasi dan Kontrol Pabrik Sinter
Sistem Otomasi dan Kontrol Pabrik Sinter
Proses sintering (Gambar 1) merupakan proses metalurgi yang dilakukan pada mesin sintering. Ini adalah proses aglomerasi termal. Proses sintering adalah proses intensif energi, di mana sejumlah parameter harus diperhitungkan. Prosesnya kompleks dan melibatkan berbagai fenomena fisik dan kimia seperti perpindahan panas, massa, dan momentum yang digabungkan dengan reaksi kimia. Fenomena ini terjadi secara bersamaan yang meningkatkan kompleksitas proses secara signifikan. Kompleksitas proses sintering mengakibatkan kompleksitas sistem kontrolnya.
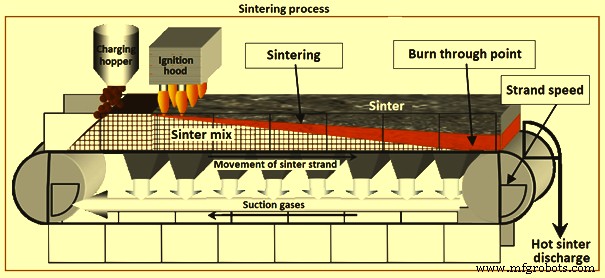
Gbr 1 Proses sintering
Proses sintering pada dasarnya merupakan tahapan proses pre-treatment pada saat pembuatan besi yang digunakan untuk menggumpalkan campuran fine ore ore, return fine, flux, dan coke wind, dengan ukuran partikel kurang dari 10 mm, sehingga dihasilkan sinter, dengan ukuran partikel kurang dari 10 mm. ukuran tersaring 5 mm sampai 30 mm, dapat menahan tekanan dan kondisi suhu di tanur tinggi. Aglomerasi dalam proses sintering dicapai melalui pembakaran. Dalam proses ini udara tersedot pada untai sinter melalui lapisan campuran sinter. Partikel bahan bakar pada lapisan permukaan atas pertama-tama dinyalakan dalam tungku dan saat untaian bergerak maju, bagian depan yang tersulut atau pembakaran berjalan secara bertahap ke bawah melalui dasar sampai akhir tercapai.
Proses sintering merupakan langkah penting dalam persiapan pengisian tanur sembur di mana bahan aglomerat (sinter) diperlukan untuk memiliki sifat yang sesuai untuk produksi logam panas yang optimal di tanur sembur. Selanjutnya, sangat penting juga untuk mengontrol emisi gas pabrik sinter, yang diproduksi dalam volume besar dan mengandung sejumlah besar zat pencemar dengan tingkat toksisitas yang berbeda.
Proses sintering melibatkan sejumlah besar parameter, lebih dari 500, yang masing-masing memberikan pengaruh yang lebih besar atau lebih kecil dan perlu dikontrol, dalam batas yang mungkin, untuk mengoptimalkan produktivitas, stabilitas proses, dan menstandarisasi komposisi dan kualitas. dari sinter yang dihasilkan. Juga untuk memenuhi persyaratan lingkungan menurut undang-undang, sistem pengendalian polusi diperlukan untuk memantau materi partikulat dan gas yang dihasilkan dan dipancarkan ke atmosfer oleh pabrik sinter. Apalagi proses sintering memiliki karakteristik kontinuitas, nonlinier, time-variying, dan ketidakpastian disamping kompleksitas dan histeresis yang besar. Selanjutnya, dari tahun ke tahun, perbaikan sedang dilakukan pada proses sintering di setiap pabrik sinter karena akumulasi pengalaman operator pabrik dan evolusi serta kemajuan dalam pengetahuan sintering.
Untuk waktu yang lama, proses sintering sebagian besar dikendalikan dengan pengalaman operator. Karena itu, fluktuasi terjadi dalam mengendalikan proses. Fluktuasi yang tidak diinginkan dalam pengendalian proses tidak dapat dihindari karena histeresis, fluktuasi dalam akuisisi data dan deteksi penyimpangan proses, perbedaan pengetahuan operator dan kemampuan pengambilan keputusan mereka, distribusi tanggung jawab di antara operator, dan faktor lain seperti faktor fisiologis, psikologis faktor lingkungan dan faktor lingkungan yang mempengaruhi proses tersebut. Dampak dari faktor-faktor ini meningkat seiring dengan peningkatan kapasitas mesin sintering. Hal ini menciptakan kebutuhan untuk pengembangan otomatisasi dan sistem kontrol untuk proses sintering.
Sistem otomasi dan kontrol di pabrik sinter diperlukan untuk memenuhi persyaratan di atas. Hal ini diperlukan untuk memastikan pengendalian subsistem yang efektif, pasokan informasi proses yang tepat waktu, dan minimalisasi biaya total, sambil memenuhi persyaratan produksi dan kualitas. Selanjutnya, sistem otomatisasi dan kontrol diperlukan untuk membangun basis data yang diperlukan untuk analisis data dan untuk menggabungkan alat analisis untuk tujuan ini.
Sistem kontrol otomatisasi dasar yang andal dan terbukti dengan baik adalah tulang punggung operasi pabrik sinter modern. Tujuan utama dari sistem kontrol proses pabrik sinter adalah (i) meminimalkan konsumsi bahan bakar karena laju bahan bakar merupakan faktor kunci dalam biaya produksi, (ii) menghindari tindakan kontrol berat karena jika hanya tindakan kontrol kecil yang diperlukan, kinerja mesin sinter sangat stabil, (iii) menghindari situasi proses kritis karena semakin cepat sistem bereaksi terhadap situasi proses kritis, seperti campuran yang tidak homogen, pengapian permukaan yang buruk, atau pembakaran yang tidak sempurna dari campuran sinter, semakin halus proses sintering secara keseluruhan, menghasilkan kualitas produk yang lebih seragam, (iv) keputusan operasional yang terkoordinasi di seluruh shift menghasilkan kondisi operasi yang konstan di semua shift yang meningkatkan masa pakai peralatan dan mengurangi biaya produksi, dan (v) pengurangan emisi sejak dengan penutupan -mode operasi loop dari sistem kontrol proses, parameter produksi dapat dioptimalkan dalam emisi lingkungan batas sion, khususnya, emisi SO2.
Sistem otomatisasi dan kontrol pabrik sinter adalah alat modern yang ramah pengguna yang membantu meningkatkan produktivitas dan stabilitas pabrik sinter. Ini membantu dalam meningkatkan kinerja pabrik sinter dengan memenuhi kebutuhan pabrik. Ini menstabilkan produksi sinter, membantu dalam mencapai hasil yang diantisipasi dan memiliki nilai praktis yang sangat besar. Manfaatnya antara lain (i) produktivitas tinggi karena menjaga pabrik sinter berjalan pada kinerja puncak sambil meminimalkan konsumsi energi listrik dan bahan bakar, (ii) kualitas produk yang berarti sinter mempertahankan sifat kimia, fisik, dan mekanik sinter pada yang diinginkan. tingkat, (iii) pengurangan konsumsi bahan bakar yang disebabkan oleh hasil pencampuran yang tepat dari bahan yang diisi dan kontrol yang ideal dari jumlah denda yang kembali dengan mempertimbangkan kondisi termal sinter pada untai, (iv) stabil dan bergeser -operasi independen sehingga memastikan produksi yang efisien, (v) integrasi yang mudah dari berbagai model metalurgi yang komprehensif ke dalam sistem otomasi dan kontrol, (vi) respons cepat terhadap permintaan tanur tinggi, dan (vii) amortisasi cepat dengan periode standar diperkirakan kurang dari satu tahun.
Dalam proses sintering, parameter kimia dan fisik seperti kebasaan dan ukuran produk harus memenuhi nilai target yang telah ditentukan sebelumnya dalam standar deviasi yang ditentukan untuk memenuhi persyaratan kualitas tanur sembur. Kualitas sinter dimulai dengan pemilihan dan pencampuran bahan baku di blending yard dan dosing plant yang terintegrasi dalam model kendali umum proses sinter. Sifat kimia harus dihomogenkan dengan adaptasi otomatis dari campuran bahan baku. Sistem kontrol 'titik bakar' (BTP) yang disempurnakan yang memperhitungkan sifat fisik dan kimia campuran sinter harus dimasukkan ke dalam sistem. Sistem harus melawan perubahan yang disebabkan oleh fluktuasi, yang dicapai dengan kontrol loop tertutup dari proses.
Optimalisasi proses sinter membutuhkan sistem kontrol proses inovatif yang meningkatkan otomatisasi pabrik ke tingkat yang benar-benar baru. Ini harus didasarkan pada sistem dasar yang teruji dengan baik dan terbukti yang memastikan ketersediaan tinggi dan menggabungkan akuisisi data, pemrosesan data, dan visualisasi data secara efisien. Spektrum yang luas dari sumber data mentah (sinyal front-end, jumlah bahan yang dibebankan, data laboratorium, kejadian, hasil model, dan data biaya) harus disimpan selama masa pakai pabrik secara keseluruhan. Alat khusus harus disediakan di mana informasi proses dapat dikaitkan dengan data analisis dan resep campuran mentah.
Sistem otomasi dan kontrol pabrik sinter dikembangkan dengan tujuan untuk meningkatkan produktivitas tenaga kerja, meningkatkan rendemen sinter, mendapatkan kualitas sinter yang optimal (fisik, mekanik, kimia, dan metalurgi), dan mengurangi konsumsi energi. Ini adalah sistem vital yang membantu operator pabrik dalam memantau setiap tahap proses produksi sinter.
Karena karakteristik bahan baku sintering, seperti komposisi kimia dan ukuran butir, memiliki elemen intrinsik yang menyebabkan fluktuasi, maka perlu menggunakan metode statistik untuk evaluasi data proses. Ini membutuhkan pengembangan beberapa model. Pengembangan model di pabrik sinter rumit karena sifat kompleks dari proses sinter. Namun, perlu dikembangkan model yang dapat digunakan secara praktis secara online. Lebih lanjut, operasi pabrik sinter harus memiliki fleksibilitas untuk memenuhi persyaratan minimalisasi biaya melalui penghematan energi dll., sambil mengakomodasi fluktuasi bahan baku, memenuhi persyaratan proses pembuatan besi yang terus ditingkatkan di tanur tinggi.
Sistem otomasi dan kontrol pabrik sinter memastikan operasi yang optimal dan stabil selama proses sintering. Ini membantu dalam meningkatkan produktivitas dan menurunkan biaya operasional. Untuk memastikan proses sintering yang optimal dan stabil, perlu untuk memahami fenomena di tempat tidur dan mengarahkan proses ke arah operasi yang optimal. Teknik kontrol utama dalam sintering adalah kontrol densitas muatan untuk mencapai sintering yang seragam di seluruh lebar untaian dan kontrol kecepatan palet untuk mempertahankan produktivitas dan kualitas sinter yang optimal.
Efisiensi otomatisasi sangat tergantung pada instrumentasi yang tepat. Instrumen yang tepat harus disediakan di tempat yang tepat dan harus dipasang dengan mulus untuk sistem otomatisasi dan kontrol yang efisien. Selanjutnya, teknik yang mapan dan efisien seperti virtualisasi server meningkatkan fleksibilitas dan ketersediaan sistem serta membantu menghemat biaya perangkat keras dan pemeliharaan. Teknologi Ethernet industri terbaru dan arsitektur perangkat keras yang telah terbukti memungkinkan kinerja maksimum sekaligus menjaga tingkat keamanan TI (teknologi informasi) yang tinggi.
Dengan tujuan akhir untuk menstabilkan proses sintering, meningkatkan produktivitas, dan menurunkan biaya produksi, sistem otomasi dan kontrol diperlukan di pabrik sinter untuk memastikan operasi yang optimal dan stabil selama proses sintering. Untuk tujuan ini, beberapa upaya telah dilakukan untuk memahami fenomena di tempat tidur dan mengarahkan proses menuju operasi yang optimal. Teknik kontrol utama dalam sintering adalah kontrol kerapatan muatan untuk mencapai sintering yang seragam di seluruh lebar untaian dan kontrol kecepatan palet untuk menjaga produktivitas dan kualitas sinter yang optimal. Desain otomatisasi pabrik sinter biasanya dibagi menjadi enam lapisan peralatan dasar. Gambar 2 menunjukkan hierarki sistem otomasi pabrik sinter.
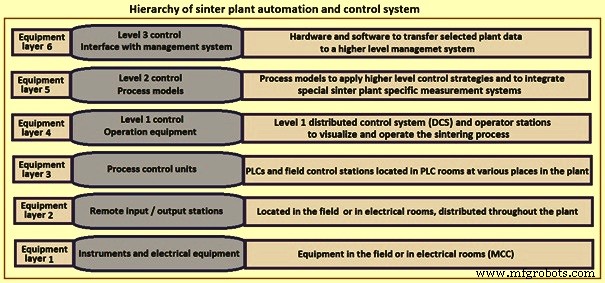
Gbr 2 Hirarki sistem kontrol dan otomatisasi pabrik sinter
Teknologi otomasi dan kontrol untuk proses sintering dikembangkan bersama dengan teknologi sinter untuk memenuhi persyaratan kualitas sinter yang diperlukan untuk kebutuhan kinerja tanur sembur yang terus meningkat. Komputer pertama kali diperkenalkan di pabrik sinter untuk mendeteksi, mengkhawatirkan, merekam, dan mencetak persyaratan proses sintering selama awal 1960-an di AS dan Eropa (terutama di Prancis dan Belgia). Kemudian, komputer digunakan untuk kontrol loop terbuka dan tertutup langkah demi langkah. Saat itu pada tahun 1970-an ketika Jepang menjadi pusat pengembangan otomatisasi dan kontrol untuk proses sintering. Organisasi baja Jepang seperti Kawasaki Steel Corporation (KSC), Sumitomo Metal Industries Corporation (SMI), Kobe Steel, Nippon Steel Corporation (NSC) dan Nippon Kokan Keihin (NKK) melaksanakan proyek penting di bidang sistem otomasi dan kontrol. Daftar berikut mencakup beberapa contoh pekerjaan yang dilakukan oleh berbagai organisasi Jepang di bidang otomasi dan kontrol pabrik sinter. Dari tahun 1980-an kecerdasan buatan sedang dipelajari untuk proses sintering. Oleh karena itu, keandalan dan presisi kontrol telah ditingkatkan.
Sistem kontrol energi sintering (SECOS) dikembangkan oleh KSC. SECOS dapat mendeteksi dan mengontrol tingkat energi termal dengan cepat dalam kisaran yang diizinkan. Dua parameter dipertimbangkan oleh sistem kontrol ini yaitu (i) jumlah karbon dari campuran sinter yang dibakar pada palet (dihitung melalui keseimbangan karbon dengan mendeteksi volume dan komposisi gas buang), dan (ii) rasio zona panas kue sinter penampang di ujung debit diukur dengan kamera. Setelah dievaluasi tingkat energi termal dengan menggunakan dua parameter ini, rasio campuran kokas disesuaikan. Penerapan sistem ini telah menghasilkan Peningkatan kualitas dan produktivitas sinter.
Sistem panduan operasi (OGS) dikembangkan oleh KSC dengan tujuan untuk mencapai permeabilitas sinter bed yang stabil untuk mencapai kualitas sinter yang optimal. Setelah memasukkan data produksi proses sintering, sistem utama mengevaluasi permeabilitas, kualitas sinter, dan produktivitas. Ini memiliki dua sub-sistem. Salah satu sub-sistem digunakan untuk menilai permeabilitas, sementara yang lain digunakan untuk menyesuaikan otomatis nilai standar untuk penilaian.
Sistem lain di mana pekerjaan ekstensif dilakukan adalah 'kontrol operasi sub-gerbang' oleh Kobe Steel, NKK, dan KSC), 'kontrol BTP baru pada kecepatan untai' oleh NKK, 'sistem tangkas buatan buatan' (ADONIS) oleh NSC, ' Kawasaki sinter automatic control' (K-SAC) oleh KSC, dan 'sistem operasi tak berawak' oleh NKK.
Sistem otomasi dan kontrol pabrik sinter disusun dalam level klasik, dari Level 0 (Level lapangan) hingga Level 3 (Level manajemen). Ini adalah sistem hierarki tiga tingkat yang menggunakan sistem kontrol terdistribusi (DCS), sistem komputer proses terpusat (PCS), dan sistem komputer pusat (CCS) dari pabrik baja. DCS melakukan fungsi seperti mengukur distribusi kecepatan angin dan distribusi suhu gas di sepanjang untai sinter, dan juga 'kontrol digital langsung' (DDC). PCS melakukan fungsi seperti kontrol proses untuk mengoptimalkan operasi pabrik sinter, dan layanan informasi kepada operator. Model proses untuk menerapkan strategi kontrol tingkat yang lebih tinggi terintegrasi dengan sistem pengukuran pabrik sinter khusus. CCS melakukan fungsi seperti perencanaan, pengelolaan, dan analisis data produksi dan operasi berdasarkan basis data tujuan umum. Penerapan sistem kontrol tiga tingkat meningkatkan fleksibilitas, memfasilitasi ekspansi, dan meningkatkan keandalan proses.
Tiga tingkat sistem kontrol terdiri dari (i) sistem kontrol digital (DCS) yang merupakan sistem pemantauan dan kontrol terintegrasi yang mencakup komputer kontrol digital, sensor, dan perangkat transmisi, memberikan kontrol loop lokal dan kontrol lanjutan dari proses dengan standar nilai yang ditetapkan dari komputer proses, (ii) sistem komputer proses yang memiliki fungsi mengumpulkan dan memproses data yang dikirim oleh DCS, mewujudkan kontrol nilai yang ditetapkan dan panduan operasi yang komprehensif dari proses sesuai dengan instruksi yang memberikan 'sistem komputer pusat' (CCS), dan (iii) CCS yang merupakan sistem kontrol tingkat atas dan memiliki database sistem pembuatan besi, yang diperoleh dengan mengumpulkan dan menyimpan informasi komputer bawahan, dan digunakan dalam penjabaran perencanaan pembelian bahan dan produksi, tetapi juga menggunakan dalam laporan produksi dan analisis teknis dari data produksi. Dengan cara ini, sumber daya manusia dihemat, biaya operasi berkurang, dan manajemen operasi ditingkatkan. Selain itu, sistem cerdas membuat proses sintering tidak terlalu bergantung pada pengalaman operator. Gambar 3 menunjukkan sistem otomatisasi dan kontrol untuk pabrik sinter.
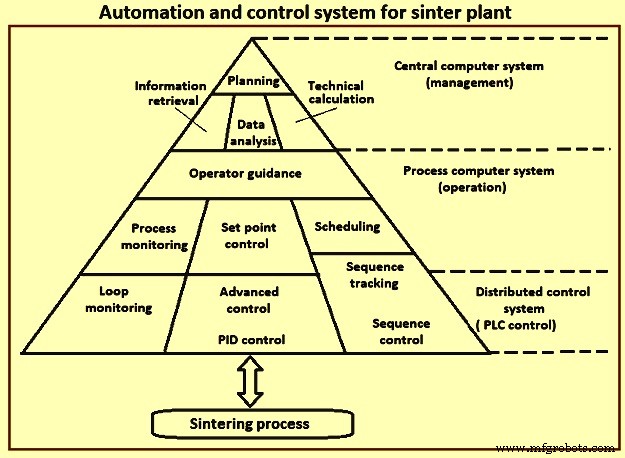
Gbr 3 Sistem otomasi dan kontrol untuk pabrik sinter
Penerapan model matematis untuk kontrol proses dari proses total terbatas karena kompleksitas proses sintering. Oleh karena itu pengembangan model telah mendahului area bijaksana di pabrik sinter. Model area bijaksana menghasilkan pendekatan modular untuk otomatisasi dan sistem kontrol pabrik sinter.
Sistem otomatisasi dan kontrol pabrik sinter biasanya dicirikan oleh struktur sistem modular. Selain fungsi dasar seperti akuisisi data dan eksekusi set-point, kontrol teknologi (loop kontrol utama) diimplementasikan dalam sistem otomasi dasar. Ini termasuk kontrol rasio campuran mentah, kontrol umpan campuran mentah, kontrol kelembaban, kontrol level hopper lonjakan, kontrol pengumpan drum, kontrol kap pengapian, kontrol pendingin gas buang, dan kontrol pendingin sinter. Fokus dari fungsi kontrol dasar ini adalah untuk memastikan proses sintering yang lancar dan andal serta memungkinkan pengoptimalan proses yang berkelanjutan.
Antarmuka yang fleksibel, modularisasi dan arsitektur perangkat lunak modern menyediakan sarana untuk dengan mudah beradaptasi dan memelihara sistem dalam lingkungan yang terus berubah sehubungan dengan bahan baku, filosofi operasi, dan konektivitas ke sistem pihak ketiga. Seiring dengan sistem dasar yang kuat, banyak model proses yang saling berinteraksi mendukung operator dan insinyur metalurgi dalam keputusan sehari-hari mereka. Kebutuhan khusus tanaman dimasukkan ke dalam model proses metalurgi ini. Transparansi menyeluruh secara real-time melalui visualisasi data terkini dan model proses metalurgi menghasilkan kolaborasi yang lebih baik, meningkatkan alur kerja, dan mengurangi kesalahan sekaligus mendukung pengambilan keputusan.
Contoh spesifik selama pengembangan sistem kontrol dan otomatisasi pabrik sinter
KSC telah mengembangkan sensor yang memantau indeks pola panas di tempat tidur sinter. Sensor ini memungkinkan kontrol operasi yang lebih rumit, tidak hanya dengan mengevaluasi kondisi operasi dari transisi permeabilitas, kualitas, hasil, dan data deret waktu konvensional lainnya, tetapi juga dengan memperkirakan secara lebih langsung perubahan kondisi lapisan dan mengontrol distribusi volume angin dan kokas. distribusi di tempat tidur. Gambar 4 menunjukkan contoh pola panas yang dicapai dengan sistem pengukuran di pabrik sinter.
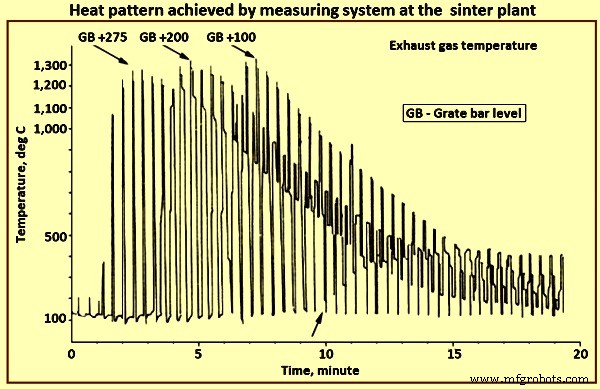
Gbr 4 Pola panas dicapai dengan sistem pengukuran di pabrik sinter
ArcelorMittal bekerja sama dengan Center de Recherches Metallurgiques (Belgia) mengembangkan pada tahun 1992 sistem pakar dengan perangkat lunak Nexpert Object dan perangkat keras VAX VMS yang mengontrol 200 parameter operasi setiap 15 detik. Manfaat yang telah dicapai antara lain menurunkan standar deviasi kandungan FeO, meningkatkan RDI (reduksi indeks degradasi), meningkatkan pengendalian BTP (didefinisikan sebagai titik di mana suhu gas buang mencapai nilai tertinggi, yang terjadi ketika api depan mencapai bagian bawah tempat tidur sinter), dan profil suhu di kotak angin.
Pada tahun 1994 ArcelorMittal memasang sistem kontrol untai sinter berdasarkan analisis kandungan CO (karbon mono-oksida), CO2 (karbon di-oksida), dan O2 (oksigen) dalam gas buang kotak angin, ditambah dengan model keseimbangan panas bertahap dikembangkan oleh IRSID (Institut de recherche de la siderurgie). Pengalaman yang diperoleh dengan penggunaan sistem kontrol telah menunjukkan variasi dalam produktivitas, BTP, suhu depan nyala api maksimum dan fraksi lelehan yang terbentuk di unggun pada suhu maksimum, sebagai fungsi dari variasi serangkaian parameter. Produktivitas teoretis tergantung terutama pada keseimbangan pengembalian halus dan aliran campuran mentah. Penilaian atas perbedaan antara produktivitas nyata dan produktivitas terukur telah menunjukkan bahwa pengaruh keseimbangan pengembalian denda dapat ditelusuri dengan baik.
BTP yang dihitung tergantung pada aliran dan komposisi kimia campuran mentah (melalui kandungan karbon dalam campuran mineral dan kadar air dalam bahan bakar) dan CO2 dalam gas buang. Penilaian perbedaan antara BTP yang dihitung dan yang dihasilkan dari pengukuran suhu di bawah jeruji telah menunjukkan variasi di kedua sisi deviasi rata-rata dari orde 1 m hingga 2 m. Peningkatan nilai ini merupakan pemanasan. Perhitungan suhu depan nyala api maksimum yang dicapai pada bagian depan nyala api dan fraksi lelehan bergantung pada masukan panas dan persyaratan yang terkait dengan komposisi kimia campuran mentah.
British Steel Corporation (BSC) telah memasang pada tahun 1994, sebuah komputer pusat VAX 4000/500 untuk mencatat data dari 4500 sinyal bersama dengan dua MicroVAX 3100 Model 80 untuk bertindak sebagai mesin bantu untuk menggerakkan terminal dan printer. Penggunaan komputer telah meningkatkan penentuan kelembaban campuran mentah yang optimal setelah perubahan unggun sinter. Dengan mampu memantau data operasi secara konstan, dimungkinkan untuk menghitung permeabilitas secara terus menerus, berdasarkan aliran gas dan udara ke tungku pengapian. Gambar 5 menunjukkan hubungan antara kadar air campuran dan permeabilitas. Dapat dilihat bahwa kelembaban optimum dapat dengan mudah diamati. Hal ini juga memungkinkan untuk melihat pengaruh kuat kelembaban yang diketahui terhadap permeabilitas.
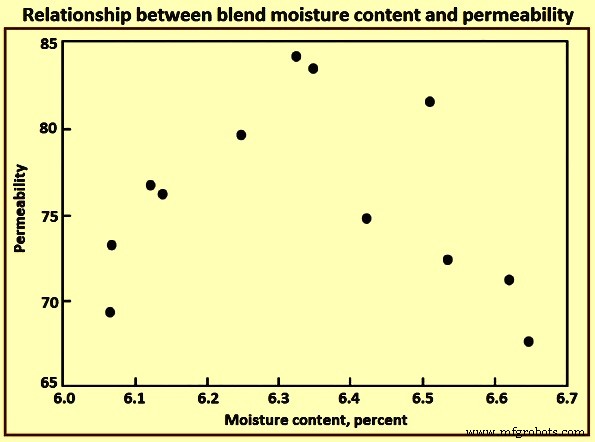
Gbr 5 Hubungan antara kadar air campuran dan permeabilitas
Untuk pengukuran kandungan FeO di dalam sinter, sistem belt coil telah ditempatkan di sekitar belt conveyor produk. Kontrol FeO yang ditingkatkan memungkinkan penghematan kokas sebesar 1 kg per ton sinter. Juga dimungkinkan untuk meningkatkan kontrol proses dan mencapai efisiensi penggunaan untai yang lebih tinggi dengan mengukur dan mengontrol BTP, di mana suhu maksimum terjadi. Model BTP telah dipasang pada komputer pabrik untuk menghitung dan mendeteksi BTP di sepanjang untai sinter dengan mengukur suhu di bawah untai untuk delapan kotak angin terakhir. Model menghitung kecepatan untai yang diusulkan untuk membawa BTP aktual sesuai dengan pengaturan yang ditentukan pengguna, dan ini diberitahukan kepada operator yang mengendalikan untaian. Ketika kecepatan untai dikendalikan menggunakan model ini, pemanfaatan untaian meningkat sekitar 1%.
Perusahaan Besi dan Baja Wuhan (WISCO) di Cina bekerja sama dengan Voest-Alpine Industrieanlagenbau (VAI) dari Austria memasang model yang menghitung 700 nilai pada dua tingkat otomatisasi dan satu set modul pengoptimalan proses. Terlepas dari kompleksitas besar parameter proses, tujuan utamanya adalah (i) peningkatan output sebesar 5%, (ii) pengurangan konsumsi kokas lebih dari 2%, dan (iii) memastikan ketersediaan sistem lebih tinggi dari 99,5% .
Tingkat pertama model mencakup semua data utama dari berbagai sumber, seperti analisis bahan baku dan sinter. Data ini disajikan kepada operator dengan cara yang sangat efisien, biasanya dalam bentuk grafik. Data ini dianalisis oleh operator dalam format grafik. Model level 2 menyediakan kontrol loop tertutup dari proses (tanpa interaksi manusia). Beberapa titik setel dihitung oleh model setiap saat dan secara bersamaan diverifikasi jika titik setel ini dapat diterapkan. Titik setel ini meliputi aliran campuran mentah, rasio material, penambahan air, dan kecepatan untai sinter untuk mengontrol BTP. Sistem dapat beralih dari level 1 ke level 2, dan jika kontrol level 2 tidak memungkinkan karena alasan apa pun, kontrol kembali diambil alih oleh level 1.
Ketika tidak mungkin untuk mengatur kecepatan untai dengan cara yang ideal, variasi kecepatan dapat diperkirakan menyebabkan operasi yang tidak stabil. Untuk mengendalikan proses, perlu untuk memastikan sintering lengkap dari campuran sebelum mencapai ujung untai, dan memastikan bahwa titik BTP sedekat mungkin dengan ujung untaian untuk mencapai output maksimum. Gambar 6 menunjukkan ikhtisar kontrol produktivitas pabrik sinter.
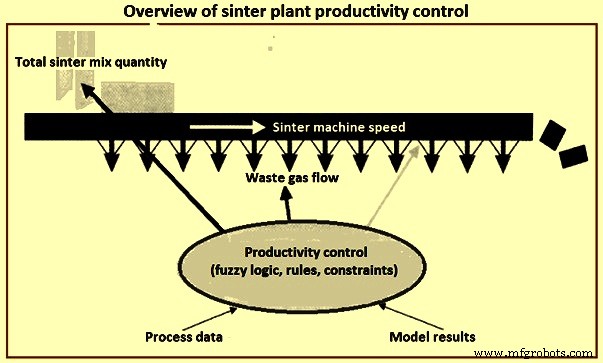
Gbr 6 Ikhtisar kontrol produktivitas pabrik sinter
Pohang Iron and Steel Company (POSCO) telah memasang di Pohang sistem pemandu dan pemantauan visual terintegrasi di pabrik sinter yang terdiri dari lima puluh termokopel, 5 pengukur aliran di tempat tidur, perangkat pencitraan termal, dan sistem kontrol pembukaan sub-gerbang. Gambar 7 menunjukkan tata letak sistem pemantauan visual ini. Termokopel ditempatkan di bawah kotak angin 15 hingga 25 dan 5 flow meter berada di kotak tempat tidur 6. Dengan menggunakan sistem ini, operator dapat mempertahankan proses dalam kondisi optimal dan stabil. Visualisasi status untaian memberikan informasi tentang kecepatan palet, kepadatan pengisian, dan kandungan bahan bakar kepada operator. Akibatnya, fluktuasi suhu off-gas di bawah palet sinter sangat berkurang. Juga, setelah kontrol otomatis pembukaan sub-gerbang, dan karenanya, jumlah denda pengembalian yang dihasilkan lebih rendah dan hasil produk yang lebih tinggi tercapai.
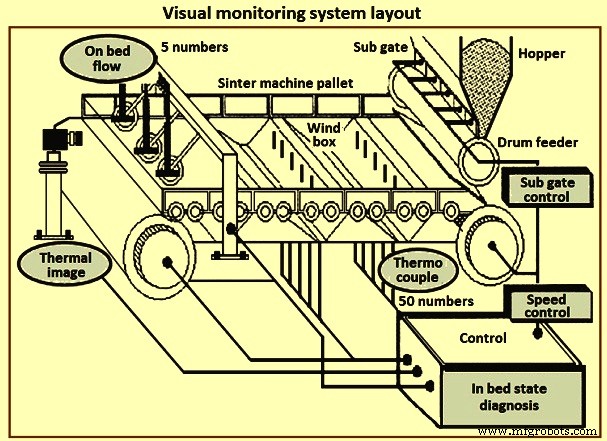
Gbr 7 Tata letak sistem pemantauan visual
POSCO telah memasang sistem pengukuran on-line di pabrik Gwangyang untuk memeriksa kadar air dalam bijih besi dan kokas yang dikirim ke hopper mixer drum. Sistem ini didasarkan pada sumber neutron cepat. Ketika neutron cepat bertabrakan dengan atom hidrogen dalam air mineral, mereka kehilangan energi sebanding dengan jumlah atom hidrogen, dan kadar air dapat ditentukan dengan menggunakan sensor yang mendeteksi neutron lambat yang dihasilkan dari tumbukan (Gambar 8). Sistem dikalibrasi untuk memperhitungkan variasi suhu dan kelembapan sekitar sepanjang tahun.
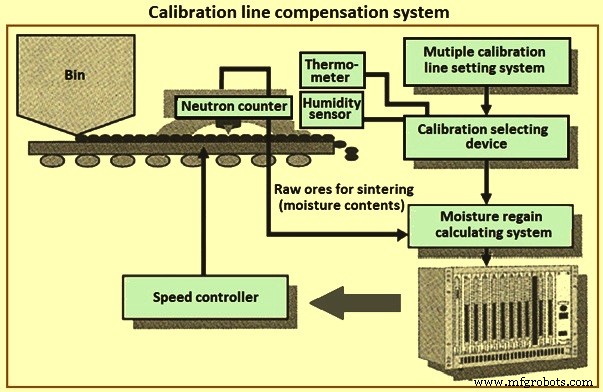
Gbr 8 Sistem kompensasi garis kalibrasi
Pengembangan model untuk proses sintering
Selama proses sintering, beberapa reaksi kimia dan transformasi fasa terjadi, tidak hanya karena perubahan panas depan, tetapi juga karena modifikasi komposisi gas lokal dan suhu leleh awal campuran bahan baku. Ketika suhu lokal dan komposisi padatan tercapai, sebagian besar transformasi fase didorong oleh suplai panas dan difusi yang terjadi di dalam lapisan partikel dengan mekanisme pembentukan cairan memainkan peran utama. Bahan sebagian meleleh ketika suhu lokal mencapai suhu leleh dan saat bergerak, kontak dengan gas dingin mendorong pemadatan ulang dan dengan demikian, aglomerasi partikel membentuk kue sinter berpori yang terus menerus. Sifat kue sinter akhir sangat bergantung pada siklus termal, komposisi kimia awal bahan baku, dan sifat termo-fisik yang dikembangkan selama sintering. Model matematika dari proses sintering mensimulasikan fenomena yang terjadi di dalam mesin sinter.
Metode untuk memodelkan proses sintering didasarkan pada persamaan transpor momentum, massa, dan energi multi-fasa, dan multi-komponen untuk fase gas, padat, dan cair dengan mempertimbangkan fenomena lokal pembentukan sinter berpori (Gambar 9). Model mempertimbangkan fase berinteraksi secara bersamaan dan spesies kimia dari setiap fase dihitung berdasarkan persamaan konservasi spesies kimia. Deskripsi akurat dari laju pertukaran untuk momentum, energi, dan reaksi kimia sangat penting untuk akurasi model yang lengkap.
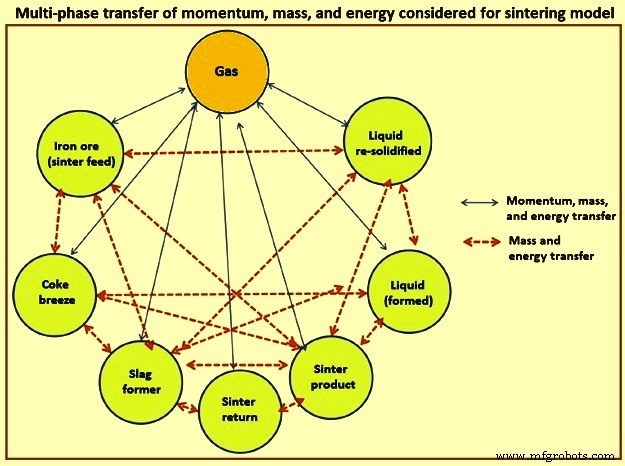
Gbr 9 Transfer multifase momentum, massa, dan energi dipertimbangkan untuk model sintering
Spesies kimia secara individual diperhitungkan dengan memecahkan persamaan transportasi setiap spesies kimia dari fase gas dan padat. Fase padat menyumbang campuran umpan sinter bijih besi, sinter halus (sinter halus yang dikembalikan), angin kokas (atau bahan bakar padat lainnya), kerak (halus dari pabrik baja), dan fluks. Fase cair terdiri dari komponen-komponen yang meleleh dan terbentuk dalam fase cair. Fase re-solidifikasi terdiri dari cairan yang dipadatkan kembali dan fase yang terbentuk selama proses re-solidifikasi dan sangat bergantung pada komposisi cairan lokal dan pertukaran panas. Kue sinter akhir dibentuk oleh campuran bahan-bahan ini dan kualitasnya tergantung pada komposisi akhir dan fraksi volume masing-masing bahan ini dan distribusinya dalam struktur sinter mosaik.
Dalam model proses sinter, diasumsikan bahwa fase cair yang terbentuk bergerak bersama dengan fase padat yang tersisa karena viskositas dan mengingat bahwa cairan yang terbentuk melekat pada permukaan partikel yang tidak meleleh, dengan demikian, persamaan untuk perpindahan momentum dan entalpi akun padatan untuk campuran cairan kental dan bahan padat ini. Dalam model, sifat termo-fisika yang bergantung pada suhu-komposisi diasumsikan mengikuti aturan campuran untuk memperhitungkan sifat fasa individu yang dipertimbangkan oleh fraksi volume fasanya.
Selama 2012, model prediksi dikembangkan oleh Hauck et al untuk profil suhu kotak angin dan posisi titik bakar dan suhu, yang diintegrasikan ke dalam sistem kontrol stabilisasi proses. Dengan cara ini, stabilisasi parameter kualitas, peningkatan produktivitas dan pengurangan dosis bahan bakar tercapai.
Pada tahun 2012, telah dikembangkan simulasi komputasi proses sinter yang mampu memprediksi fenomena terpenting di dalam sintering bed. Model didasarkan pada konsep multi fase dengan beberapa komponen yang dijelaskan oleh persamaan konservasi masing-masing komponen ditambah dengan momentum, reaksi kimia dan perpindahan panas. Validasi model dilakukan membandingkan prediksi model dengan data industri rata-rata dan pengukuran suhu lokal dalam untai sinter. Prediksi model menunjukkan kesesuaian yang baik dengan nilai rata-rata yang diukur pada proses sinter industri.
Pada tahun 2013 model matematika sinter dikembangkan oleh Saiz dan Posada dengan tujuan untuk mengontrol BTP pada plant sintering (posisi dan temperatur). BTP yang stabil mengarah pada proses sintering yang stabil dan peningkatan kualitas dan produktivitas. This mathematical model has been applied to the sinter plant of ArcelorMittal at Asturias (strand speed and coke consumption as control variables, BTP position, and temperature have been used in the control algorithm). By applying the model, an improvement in the productivity of 4 % to 5 %, reduction in coke consumption from 5.2 % to 5.5 % and decrease in return fines from 37 % to 45 % have been achieved.
Fuzzy logic allows for the coordination among the objective knowledge (e.g. mathematical models) and the subjective knowledge (e.g. linguistic information which cannot be quantified by means of the traditional mathematics, as the plant operators’ information). In this way, fuzzy logic has been recently used. A new approach based on fuzzy inference to control the charging gates of the sinter plant has been studied in 2014. Two strategies have been established. One which is more invasive within process operational conditions, used in sinter plants with low productivity (for example when the plant is restarted after a stoppage) with the purpose of maximizing the productivity and the second which is more conservative, also aims to maximize the productivity but the machine shows high sensitivity to changes on the gates.
During 2016, software for sinter cost optimization based on the sinter quality characteristics has been developed. Moreover, Tumbler and RDI indexes have been estimated by means of a Sugeno-type fuzzy inference system. Historical data of 6 years has been used in the multivariate statistics studies, and thus, software which gives the least expensive blend mix to be used in the sintering process and satisfies the quality requirements has been developed. Economic savings have been achieved and sinter quality has improved.
Modelling and simulation knowledge has allowed the possibility of evaluating the effect of different variables in processes, concretely in the sintering process without using directly the real sinter plant. The effect of coke combustion rate on the temperature distribution in iron ore sintering process and the growth of voids and cracks in the sinter cake by using simulation techniques have been studies. During 2015, the recovery of waste heat from sinter cooling process has been simulated and optimized.