Lapisan tahan api dari Tungku Oksigen Dasar
Lapisan tahan api Tungku Oksigen Dasar
Tujuan lapisan refraktori dalam tungku oksigen dasar (BOF) adalah untuk menyediakan ketersediaan tungku maksimum selama pengoperasian konverter untuk memenuhi persyaratan produksi dan untuk memastikan konsumsi refraktori spesifik serendah mungkin. Untuk mencapai hal ini, penting untuk (i) mengoptimalkan desain pelapis, (ii) mengoptimalkan praktik perawatan pelapis, dan (iii) memiliki disiplin teknologi yang baik selama pengoperasian konverter. Lapisan refraktori tipikal ditunjukkan pada penampang konverter pada Gambar 1.
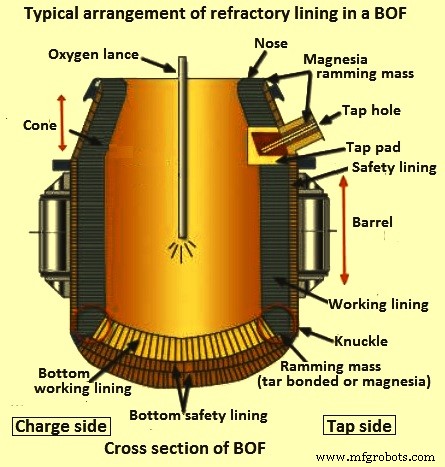
Gbr 1 Susunan tipikal lapisan refraktori dalam BOF
Desain lapisan
Keausan lapisan refraktori BOF disebabkan oleh efek individu atau gabungan dari beberapa agen yang memiliki pengaruhnya terhadap mekanisme keausan. Agen-agen ini adalah (i) durasi panas yang menentukan waktu tinggal terak dan logam dalam konverter, (ii) korosi karena serangan kimia terak karena kimianya, (iii) suhu baja cair dan terak, (iv) korosi karena keadaan oksidasi lelehan, (v) erosi karena terak dan logam selama penghembusan oksigen (O2) dan selama kemiringan BOF, (vi) benturan dan abrasi debu dan gas, (vii) dampak dari potongan dan logam selama pengisian, (viii) dampak dan penetrasi jet O2, (ix) siklus termal selama panas, dan (x) kerusakan mekanis selama deskulling konverter. Karena berbagai tindakan agen ini, ada banyak area keausan di konverter.
Operasi konverter serta konfigurasi lapisan memiliki pengaruh besar pada umur lapisan konverter. Temperatur sadapan baja cair bervariasi secara signifikan dengan superheat yang dibutuhkan untuk mencor baja dengan grade tertentu, dan fasilitas pembuatan baja sekunder yang tersedia untuk pabrik tertentu. Keadaan oksidasi lelehan dalam konverter sangat signifikan dalam hal keausan lapisan BOF dan diperparah oleh suhu tinggi. Kimia terak penting dalam beberapa cara. Batu bata Magnesia-karbon (Mag-C) adalah refraktori dasar yang membutuhkan terak dasar. Terak dasar yang terbentuk juga berusaha untuk melarutkan magnesia (MgO) dari batu bata sampai tingkat kejenuhannya. Kejenuhan MgO khas terjadi sekitar 8% lagi tergantung pada suhu dan keadaan oksidasi, jadi jika MgO tidak ditambahkan, biasanya dalam bentuk dolomit terkalsinasi, terak melarutkan lapisan secara istimewa dan dengan demikian meningkatkan keausan lapisan. Kimia terak sekali lagi terkait dengan keadaan oksidasi dan suhu karena kebasaan dan kandungan MgO diencerkan oleh FeO tingkat tinggi dan suhu meningkatkan laju reaksi kinetik. Erosi dan efek abrasi sangat terkait dengan praktik yang diterapkan selama pembuatan baja.
Secara teoritis lapisan refraktori dari sebuah konverter dirancang dengan jenis refraktori dan ketebalan yang berbeda sehingga tidak ada material yang terbuang pada akhir kampanye konverter. Ini berarti bahwa semua zona (Gbr. 2) dari lapisan konverter akan aus sampai ketebalan penghentian pada waktu yang sama. Namun dalam praktiknya hal ini tidak terjadi dan refraktori di beberapa zona lebih cepat aus dibandingkan refraktori di zona lain. Desain lapisan yang seimbang selalu ditujukan untuk meningkatkan umur lapisan dengan biaya refraktori yang optimal. Lapisan yang seimbang adalah lapisan di mana kualitas dan ketebalan yang berbeda dari refraktori digunakan di zona yang berbeda dari konverter setelah mempelajari dengan cermat pola keausan dari refraktori dalam konverter. Jenis lapisan ini juga disebut lapisan zonal karena dalam jenis lapisan tersebut refraktori diberi zona sedemikian rupa sehingga segmen lapisan tertentu yang memiliki keausan lebih rendah diberi kualitas tahan api yang lebih rendah atau ketebalan yang lebih rendah. Demikian pula refraktori dengan ketahanan aus yang lebih besar dan biasanya memiliki biaya lebih tinggi ditempatkan pada segmen lapisan konverter yang memiliki pola keausan yang lebih tinggi sehingga memiliki masa pakai yang lebih lama pada area keausan yang parah ini.
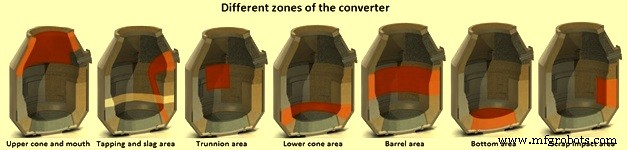
Gbr 2 Zona konverter yang berbeda
Kualitas refraktori yang biasanya digunakan untuk lapisan konverter berkisar dari dolomit berikat tar, dolomit berikat pitch, dan magnesia berikat pitch hingga refraktori canggih yang dibuat dengan ikatan resin, logam, grafit dan MgO yang disinter dan/atau menyatu yang 99% murni. Refraktori dibuat memiliki kombinasi sifat untuk menahan suhu tinggi dan perubahan kondisi lingkungan yang cepat selama panas dalam konverter. Keseimbangan sifat seperti kekuatan panas, ketahanan oksidasi, dan ketahanan terak diharapkan dari refraktori konverter. Saat ini refraktori Mag-C adalah refraktori paling populer untuk lapisan konverter.
Refraktori Mag-C
Variabel yang berbeda terkait dengan refraktori Mag-C untuk meningkatkan kualitas agar memiliki umur lapisan yang lebih baik dari konverter adalah (i) jenis butir magnesia yang digunakan seperti kimia, ukuran kristal, dan densitas, (ii) jenis ikatan dan ukuran bata press (gesekan / hidrolik), (iii) bonding agent seperti pitch, resin, quantity, dan re-impregnation, (iv) jenis grafit yang digunakan seperti kemurnian, sizing, dan quantity, (v) anti-oksidan seperti jenis, jumlah, dan ukuran, (vi) sifat fisik bata seperti densitas, porositas, dan kekuatan (panas dan dingin). Jenis dan ukuran press baik itu gesekan atau hidrolik memiliki pengaruh pada sifat bata.
Butir magnesium – Karena komponen terbesar dari batu bata Mag-C adalah butiran MgO, komposisi dan sifat butiran memainkan peran penting dalam karakteristik batu bata. Ada beberapa jenis butir MgO yang tersedia. Kualitas butir MgO yang lebih tinggi diperlukan untuk menahan terak dasar, erosi, abrasi, dan suhu dll. Kepadatan butir, ukuran, dan kimia sangat penting. Dalam hal kimia, rasio kapur (CaO) / silika (SiO2) dari biji-bijian adalah penting. Rasio CaO/SiO2 harus nol atau lebih dari 2:1 untuk memastikan pembentukan di-kalsium silikat, fase titik leleh yang tinggi. Beberapa butir MgO memiliki rasio CaO/SiO2 setinggi 6:1 tetapi kemudian butir-butir ini menjadi lebih rentan terhadap hidrasi. Rasio CaO/SiO2 yang rendah menghasilkan fase titik leleh yang rendah dan hilangnya kekuatan panas dapat menjadi bencana besar. Jumlah mineral sekunder yang terbentuk dalam butiran juga penting dan karenanya, kandungan SiO2 harus serendah mungkin (kurang dari 0,3%). Kandungan boron (B) yang tinggi juga sangat penting karena merusak kekuatan panas biji-bijian.
Kepadatan butir – Kepadatan butir dapat bervariasi dari 3,2 gram per sentimeter kubik (g/cc) hingga lebih tinggi dari 3,5 g/cc. Kepadatan butir rendah berarti porositas tinggi membuat butir rentan terhadap penetrasi terak.
Ukuran kristal – Kristal berbutir besar biasanya mengungguli butiran dengan ukuran kristal rendah karena pengurangan porositas interstisial sehingga mengurangi kemungkinan penetrasi terak ke batas butir dan dengan menurunkan kerentanan MgO terhadap reduksi oleh C yang ada di batu bata selama layanan suhu tinggi. Proses reduksi menghancurkan baik C dalam batu bata dan MgO dalam biji-bijian yang menghasilkan uap logam magnesium (Mg) dan gas CO. Ukuran kristal biasanya dianggap besar bila lebih tinggi dari 140 mikron. Ukuran butir MgO yang menyatu dapat melebihi 1000 mikron. Namun bahan butiran yang menyatu dapat memiliki variasi dalam kimia, dan ukuran kristal.
Agen pengikat – Bata Mag-C adalah bata ikat C dengan sisa C yang telah dibelah halus yang tersisa setelah pengikatan pengikat. Residu ini menyatukan bata.
Jenis grafit yang digunakan – Grafit tidak membasahi terak pembuatan baja dan karenanya mencegah penetrasi terak ke dalam batu bata dan pembubaran butir MgO selanjutnya. Grafit juga sangat konduktif termal mentransfer panas dari permukaan bata sehingga mengurangi kinetika reaksi agresif. Secara kimia, semua grafit adalah C murni tetapi semuanya mengandung beberapa abu (mineral lempung yang ditemukan dalam endapan grafit). Grafit tidak murni menambahkan fluks seperti SiO2 dan Al2O3 (alumina) ke batu bata yang hanya menghasilkan efek negatif. Grafit serpihan biasanya digunakan karena memiliki ketahanan yang lebih tinggi terhadap oksidasi daripada grafit amorf dan konduktivitas termal yang lebih tinggi. Umumnya jumlah grafit yang digunakan dapat bervariasi dari 5% hingga 25% dan jika semuanya sama maka semakin tinggi kandungan grafit semakin tinggi pula ketahanan terak dan konduktivitas termal batu bata.
Anti-oksidan – Serbuk logam ditambahkan ke batu bata Mag-C karena mereka bertindak sebagai pemulung O2 yang menunda oksidasi grafit dan ikatan-C. Serbuk meningkatkan kekuatan panas secara nyata dengan membentuk ikatan logam-karbida-oksida kompleks di dalam batu bata.
Desain lapisan BOF bervariasi dari pabrik ke pabrik masing-masing dengan tujuan menghasilkan lapisan yang mencapai umur dan ketersediaan yang diinginkan, dan dengan upaya untuk menyamakan keausan dari mekanisme keausan yang berbeda di berbagai area BOF. Lapisan zona khas dari konverter diberikan pada Gambar 3.

Gbr 3 Lapisan zona khas konverter
Praktik pemeliharaan lapisan
Beberapa praktik perawatan lapisan digunakan untuk meningkatkan masa pakai lapisan tahan api dalam konverter. Ini diberikan di bawah ini.
Pengukuran keausan tahan api oleh sinar laser – Ini adalah teknik yang digunakan untuk pengukuran ketebalan lapisan dengan bantuan sinar laser (Gbr 4). Saat ini merupakan metode yang banyak digunakan. Dalam teknik ini, sinar laser dipantulkan kembali dari titik-titik yang dikalibrasi pada konverter yang tepat dan dibandingkan dengan titik-titik pada lapisan yang aus. Analisis komputer kemudian digunakan untuk memplot ketebalan lapisan yang tersisa. Informasi ini juga berguna dalam membandingkan tingkat keausan untuk berbagai refraktori dan menghindari kerusakan cangkang. Kegunaan teknik ini adalah dalam menentukan dan mengontrol kebutuhan perawatan tungku dengan cara menembak. Dengan menggunakan sinar laser, area yang benar-benar membutuhkan perawatan penembakan dapat diidentifikasi untuk melakukan perawatan penembakan yang diperlukan. Jumlah material senjata yang dibutuhkan juga dapat dikontrol.

Gbr 4 Pengukuran keausan refraktori dengan sinar laser
Tingkat magnesium – Tingkat MgO terak merupakan faktor yang sangat penting untuk meningkatkan umur lapisan. Tujuannya adalah untuk mengisi lebih banyak MgO daripada tingkat kejenuhan terak pada suhu operasi. MgO yang lebih tinggi dalam terak juga meningkatkan karakteristik pelapisan terak selama pelapisan terak serta karakteristik lengketnya terak selama percikan terak. Sumber MgO biasanya merupakan sumber magnesium berbiaya rendah. Bahan pelapis dasar bekas juga dapat digunakan untuk tujuan ini. Kadar MgO dalam terak harus didasarkan pada suhu penyadapan.
Lapisan terak – Ini pada dasarnya adalah teknik mengayunkan konverter untuk membuat lapisan terak yang berfungsi. Ini adalah seni yang membutuhkan perhatian yang cukup besar selama operasi konverter. Persyaratan agar praktik pelapisan terak berhasil adalah (i) pemilihan jenis terak yang tepat, (ii) pengkondisian terak dengan jumlah penambahan yang tepat dan tepat, (iii) goyangan konverter yang benar, (iv) pembuangan terak bila perlu, (v) pelapisan pada waktu terbaik. Barang-barang ini harus direncanakan dengan baik dan dilaksanakan dengan benar untuk pelapisan terak yang tepat.
Percikan terak – Teknik percikan terak berkontribusi pada peningkatan besar dalam masa pakai lapisan konverter. Percikan terak seperti namanya, memanfaatkan sisa terak dari proses pembuatan baja, yang dikondisikan, untuk memberikan lapisan pada permukaan tahan api untuk bertindak sebagai lapisan keausan pada panas berikutnya. Terak kental cair dihembuskan dengan menggunakan nitrogen bertekanan tinggi (N2) ke berbagai bagian konverter di mana ia menempel pada lapisan kerja konverter. Teknik percikan terak membutuhkan beberapa menit waktu konverter setelah penyadapan panas sebelumnya dan sebelum dimulainya panas berikutnya. Teknik percikan terak telah dikembangkan untuk melawan erosi dan menghasilkan lapisan beku dalam konverter. Splashed slag bertindak sebagai lapisan kerja selama panas berikutnya. Ini telah menjadi alat yang ampuh untuk meningkatkan umur lapisan konverter. Ini memerlukan penggunaan tombak O2 untuk meniup N2 pada sisa terak. Percikan terak membutuhkan waktu 2 menit sampai 3 menit dan dilakukan dengan konverter dalam kondisi vertikal. Aliran N2 dikendalikan berdasarkan ketinggian tombak dan biasanya otomatis.
Menembak – Teknik ini membantu untuk mencapai umur panjang pada lapisan. Ini terdiri dari menembakkan bahan tahan api yang biasanya monolitik di area yang mengalami keausan parah seperti trunnion, dan garis terak. Penembakan biasanya dilakukan hanya pada area tertentu. Jenis senjata penembak digunakan untuk proses penembakan untuk menghadapi lingkungan proses yang tidak bersahabat. Bahan gunning biasanya berbahan dasar air. Banyak penelitian telah dilakukan pada bahan senjata dan kualitasnya terus ditingkatkan. Karena bahan tembak memiliki biaya, jumlah penembakan harus diimbangi dengan biaya spesifik bahan tahan api selama pembuatan baja.
Pelapis konverter dan bahan pelapis
Dalam lapisan konverter biasanya dua lapisan batu bata tahan api digunakan. Ini terdiri dari lapisan pengaman yang lebih tipis untuk melindungi cangkang yang biasanya memiliki ketebalan mulai dari 150 mm hingga 225 mm dan lapisan kerja yang lebih tebal biasanya dengan ketebalan mulai dari 450 mm hingga 750 mm. Sebagian besar lapisan pengaman biasanya bertahan selama beberapa kampanye lapisan kerja. Lapisan pengaman ditahan di tempatnya dengan cincin penahan baja dan mortar. Lapisan konverter sederhana dan terdiri dari langkah-langkah berikut.
- Lapisan konverter didinginkan setelah kampanye selesai dan pelapis kerja yang tersisa dihilangkan dengan cara mekanis umumnya menggunakan mesin de-bricking. Refraktori yang dilepas dibiarkan jatuh dengan memutar konverter ke posisi terbalik.
- Perbaikan bagian yang rusak dari lapisan pengaman dilakukan dan lapisan kerja dipasang tanpa mortar.
- Pada prinsipnya lapisan kerja dipasang dengan pemotongan batu bata minimum dalam konstruksi kunci bercincin di mana batu bata ditahan pada tempatnya oleh lancip bata (muka panas lebih kecil daripada muka dingin)
Kondisi keausan di berbagai zona konverter dan jenis refraktori yang direkomendasikan untuk digunakan diberikan di bawah ini.
Bawah – Erosi refraktori di area ini oleh logam cair, terak dan gas. Tegangan termo-mekanis dikembangkan dalam kasus konverter tiup gabungan sebagai akibat dari gradien termal antara tuyer yang didinginkan oleh gas dan lapisan bawah. Lapisan Mag-C tidak memberikan peningkatan kinerja di area dasar konverter. Dalam kasus tiupan dalam selama panas, bagian bawah lebih cepat aus. Perbaikan bagian bawah selama kampanye biasanya dilakukan dengan membangun bagian bawah dengan terak kental yang diperkaya dolomit atau menambal bagian bawah dengan campuran terak cair dan batu bata dasar yang rusak. Penggabungan operasi peniupan dalam konverter menyebabkan tegangan tinggi di bagian bawah dan karena alasan ini, blok refraktori MgO yang ditembakkan dengan pengubah dan impregnasi pitch biasanya digunakan di area ini.
Tuyeres bawah dan sekitarnya – Blow blowing dan bath agitasi melalui tuyeres berkontribusi terhadap keausan lokal dari bahan tahan api di area sekitarnya. Keausan ini disebabkan oleh aliran turbulen baja cair yang menimbulkan erosi refraktori dan juga karena tegangan termal yang disebabkan oleh aliran gas dingin. Blok refraktori Mag-C yang direkatkan dengan densitas tinggi dan porositas rendah serta diresapi berdasarkan MgO leburan lebih disukai untuk aplikasi ini.
Bantalan pengisi daya – Bantalan pengisi daya di konverter biasanya berhadapan langsung dengan lubang keran. Bantalan pengisi dikenai beban tumbukan oleh potongan yang jatuh, terkadang bersifat berat seperti ujung yang mekar. Baja cair juga menyebabkan erosi bantalan muatan. Selain itu, probe pengambilan sampel dan probe suhu dimasukkan dari sisi bejana yang dimiringkan ini dan ini menyebabkan terak pada suhu tinggi yang melakukan pencucian area bantalan pengisi daya. Solusi refraktori awal untuk bantalan muatan ditemukan dengan batu bata MgO yang diresapi dengan pitch. Karena masa pakai konverter telah meningkat karena penggunaan bahan Mag-C, bantalan pengisi daya menjadi area keausan utama, dan Mag-C berikat resin dengan tambahan logam digunakan untuk mendapatkan kinerja yang baik. Bahan-bahan ini menawarkan ketahanan yang baik terhadap benturan, memberikan ketahanan yang digabungkan dengan kekuatan, dan ketahanan terhadap masuknya terak karena adanya grafit.
Area penyadapan – Area sadapan mengalami erosi oleh baja cair pada suhu tinggi dan mengalami korosi oleh terak cair. Perkembangan refraktori di daerah sadap telah sejalan dengan perkembangan daerah bantalan muatan. Bahan sebelumnya sedang diganti dengan Mag-C terikat dan diresapi dengan penambahan logam. Karena proses keausan dominan di area sadapan melibatkan serangan terak suhu tinggi, blok tahan api yang dibuat dari MgO berukuran kristal besar dengan cepat menjadi standar. Pitch bonded dan refraktori impregnasi telah ditemukan memberikan kinerja yang unggul di area sadapan karena pengurangan penetrasi slag oksida oleh aksi C dalam porositas blok refraktori.
Perlintasan zona terak – Area lapisan konverter ini, yang terletak di persimpangan antara area sadapan bawah dan tingkat atas dari rendaman statis, sangat kompleks karena mengalami beberapa mode serangan seperti serangan terak, suhu tinggi, dan erosi. Semua serangan ini terjadi selama penyadapan konverter. Bahan tahan api dengan ketahanan terhadap serangan terak suhu tinggi bersama dengan ketahanan oksidasi diperlukan untuk lapisan area ini. Pitch bonded, impregnasi Mag-C berdasarkan MgO ukuran kristal besar, grafit serpihan kemurnian tinggi dan mengandung penambahan logam telah memberikan hasil yang baik. Penggunaan serpihan grafit kemurnian tinggi sangat berguna karena membatasi 'oksidasi sendiri' oleh oksida pengotor yang secara inheren ada dalam serpihan grafit.
Zona trunnion – Zona trunnion konverter adalah yang paling sulit dipelihara karena berada pada sumbu rotasi dan karenanya tidak mampu mencuci terak. Keausan bahan tahan api terutama disebabkan oleh hilangnya permukaan kerja oleh oksidasi ikatan C. Menembak area konverter ini adalah satu-satunya metode praktis untuk mempertahankan area ini dan blok tahan api dengan ketahanan tinggi terhadap oksidasi lebih disukai.
Laras utama – Laras utama konverter dapat dengan mudah dibagi menjadi dua area yaitu (i) buku jari, dan (ii) dinding samping atas.
Area buku jari di konverter sering kali merupakan area keausan utama, meskipun perubahan desain sering kali efektif dalam meningkatkan kinerja. Area buku jari sebagian besar mengalami serangan terak yang parah, terutama ketika konverter tidak ditiup. Ini membutuhkan bahan tahan api dengan ketahanan yang sangat baik terhadap korosi dan erosi terak.
Dinding samping atas konverter terkena serangan terak, tetapi juga terhadap siklus suhu yang ekstrem. Bahan yang memiliki ketahanan terak yang baik digunakan di area ini. Namun, lapisan tahan api di area ini juga harus mampu mengambil dan menahan lapisan terak.
Mengambil sampel garis terak – Area kerucut yang terdistribusi di kedua sisi bantalan muatan dikenai serangan preferensial oleh terak ketika bejana dimiringkan untuk pengukuran suhu dan untuk sampel probe dips. Mag-C yang diresapi dengan pitch bonded memberikan kinerja yang baik di area konverter ini.
Kerucut – Daerah kerucut mengalami erosi suhu tinggi oleh gas berkecepatan tinggi yang membawa serta partikel yang terperangkap. Ada atmosfer pengoksidasi. Bahan Mag-C yang direkatkan dengan resin memberikan kinerja yang baik di area kerucut.
Kerucut atas – Di kerucut atas, enam hingga sepuluh cincin teratas, mekanisme keausan dimodifikasi dengan hilangnya bahan tahan api selama pelepasan tengkorak. Kerusakan pada batu bata tahan api di kerucut atas terjadi selama deskulling mekanis baik secara progresif dengan hilangnya ujung batu bata atau dengan terlepasnya seluruh batu bata.
Bahan tahan api dengan ketahanan tinggi yang dikombinasikan dengan kekuatan dan ketahanan oksidasi merupakan prasyarat untuk area konverter ini . Pitch bonded impregnated MgO, terkadang dilengkapi dengan pelat logam co-moulded, yang mengembang selama oksidasi dan mengencangkan cincin bata, adalah bahan refraktori yang paling sukses di area ini.