Penggunaan Logam Panas untuk Pembuatan Baja di Tungku Busur Listrik
Penggunaan Logam Panas untuk Pembuatan Baja di Tungku Busur Listrik
Pembuatan baja oleh tungku busur listrik (EAF) memiliki fleksibilitas yang sangat baik sehubungan dengan pemilihan bahan muatan. Bahan pengisi tradisional untuk proses EAF adalah 100% skrap dingin tetapi karena masalah terkait skrap seperti ketersediaan dan kualitasnya, fluktuasi harga pasar, dan pembatasan yang diberlakukan oleh skrap dalam membuat beberapa nilai baja karena elemen residu dan tingkat nitrogen, dll. bahan muatan alternatif telah berhasil digunakan dalam berbagai persentase oleh operator EAF. Bahan pengisi alternatif adalah besi tereduksi langsung (DRI), besi briket panas (HBI), besi kasar, atau logam panas.
Penggunaan logam panas lebih populer di daerah-daerah di mana ada kekurangan skrap dan/atau tenaga listrik atau tenaga listrik berbiaya tinggi. Sumber logam panas yang populer adalah tanur sembur sehingga logam panas dapat digunakan di EAF yang berada di dekat tanur sembur, jika tidak, operator EAF harus menggunakan pig iron. Pig iron membutuhkan energi ekstra untuk melelehkannya. Berbagai variasi dalam proporsi logam panas dan skrap dimungkinkan dalam pembuatan baja EAF. Dengan operasi skrap 100% di salah satu ujung timbangan; FAF juga dapat dioperasikan dengan muatan hanya 20% skrap dan 80% logam panas. Saat ini ada banyak EAF yang telah dirancang untuk menggunakan 80% logam panas dalam pengisian daya.
Menggabungkan muatan logam panas dan skrap ke EAF membantu meningkatkan kinerja operasi proses. Logam panas memiliki karbon terlarut dan silikon yang merupakan sumber panas penting yang tersedia dengan oksidasinya. Panas oksidasi elemen-elemen ini bersama dengan panas sensibel yang tersedia dalam logam panas membantu dalam pengurangan substansial dalam konsumsi daya selama pembuatan baja di EAF. Selanjutnya, logam panas bebas dari bahan non-logam asing yang telah dihilangkan sebagai terak selama proses pembuatan besi. Namun, operator EAF diharuskan untuk menjaga reaksi kuat yang terjadi di tungku karena karbon dalam logam panas. Logam panas dapat diisi dengan cara yang terkendali untuk menjaga kandungan karbon dalam penangas logam cair di tungku.
Manfaat utama yang terkait dengan pengisian logam panas di EAF termasuk peningkatan produktivitas, peningkatan pembusaan terak, dan peningkatan kandungan karbon dalam pengisian. Kemurnian tinggi, kandungan gangue rendah dari logam panas memungkinkan produksi produk baja yang membutuhkan kandungan residu rendah. Lebih lanjut, logam panas tersebut telah dikenal dan konsisten secara kimia yang disertifikasi oleh analisis dan ini mengimbangi fluktuasi kimia yang luas yang umum terjadi dengan penggunaan skrap usang.
Energi kimia yang terkandung dalam logam panas dikirim secara efisien oleh karbon yang terkandung, yang mendorong pencairan lebih cepat dan peningkatan produktivitas. Logam panas sangat bermanfaat untuk meningkatkan produktivitas EAF dan mencapai waktu tap-to-tap yang singkat asalkan desain tungku tidak membatasi laju dekarburisasi. Logam panas juga memungkinkan fleksibilitas yang cukup besar dalam pemilihan skrap. Karena kandungan residu logam panas yang rendah, dimungkinkan untuk memanfaatkan skrap bermutu rendah ketika proporsi logam panas yang lebih tinggi digunakan di EAF.
Hot metal memberikan manfaat yang mirip dengan pig iron, dengan manfaat tambahan bahwa material sudah berada pada suhu sekitar 1.300 derajat C atau lebih. Dengan demikian, sebagian besar kebutuhan energi dalam EAF (diperlukan untuk peleburan Fe) sudah tersedia. Satu ton logam panas pada 1.430 derajat C memasok sekitar 250 kWh dalam bentuk panas sensibel, hanya berdasarkan kandungan Fe. Untuk penggunaan pig iron di EAF, penghematan energi tipikal biasanya berkisar antara 3,1 kWh/persen pig iron hingga 3,6 kWh/persen pig iron. Menggunakan logam panas meningkatkan penghematan menjadi 4,8 kWh/persen logam panas. Menggunakan logam panas dalam jumlah besar dapat mengurangi konsumsi daya hingga ke tingkat 200 kWh per ton logam panas ke bawah dan dengan demikian dapat sangat bermanfaat untuk lokasi yang memiliki jaringan listrik yang lemah.
Pengaruh HM pada parameter kunci proses EAF
Belakangan ini, penekanan utama dalam pembuatan baja EAF berkaitan dengan pencapaian efisiensi energi maksimum. Selanjutnya, bahan pengisi umpan mempengaruhi desain EAF dan praktik pengoperasiannya. Pengaruh HM sebagai bahan pengisi pada berbagai parameter kunci dari proses EAF pembuatan baja dirinci di bawah ini.
Elemen sisa – Elemen sisa yang juga dikenal sebagai elemen gelandangan tidak dapat dihilangkan dari baja selama pemrosesan. Oleh karena itu, jumlah unsur-unsur ini dalam produk adalah fungsi langsung dari jumlah unsur-unsur ini yang dibebankan pada proses pembuatan baja melalui bahan pengisi. Tingkat elemen residu yang tinggi dapat mempengaruhi operasi pengecoran dan pengerolan selain mempengaruhi kualitas produk. Dengan menambahkan HM, yang merupakan unit besi bersih, dalam campuran muatan, tingkat elemen sisa dalam baja cair dapat dikurangi ke tingkat yang dapat diterima melalui proses pengenceran.
Tingkat nitrogen dalam baja – Nitrogen umumnya dianggap sebagai pengotor yang tidak diinginkan yang menyebabkan penggetasan pada baja dan mempengaruhi penuaan regangan. Nitrogen dalam baja cair hadir dalam bentuk larutan. Selama pemadatan baja dalam pengecoran kontinu, nitrogen adalah alasan utama pembentukan lubang tiup. Logam panas karena kadar nitrogennya yang lebih rendah memberikan efek pengenceran dan juga menghasilkan gas karbon mono oksida (CO) di dalam penangas baja melalui pendidihan C yang selanjutnya mengarah pada penurunan kandungan nitrogen dalam baja.
Penghilangan hidrogen – Gas CO berevolusi selama proses dekarburisasi membantu menghilangkan hidrogen. Telah ditunjukkan bahwa dekarburisasi pada laju 1% per jam dapat menurunkan kadar hidrogen dalam baja dari 8 ppm menjadi 2 ppm dalam 10 menit.
Pengaruh pada produktivitas dan parameter operasi lainnya – Dengan penggunaan HM dalam campuran muatan, terdapat konsumsi oksigen yang lebih besar yang membantu dalam peningkatan produktivitas EAF, dalam waktu ketuk ke ketuk yang lebih singkat, peningkatan hasil Fe, dan pengurangan konsumsi daya spesifik. Dengan penggunaan HM dalam campuran muatan, penghematan berada dalam kisaran 4 kWh per persen logam panas hingga 8 kWh per persen logam panas dalam muatan. Gambar 1 menunjukkan hubungan produktivitas dan konsumsi daya spesifik dengan persentase logam panas dalam muatan EAF.
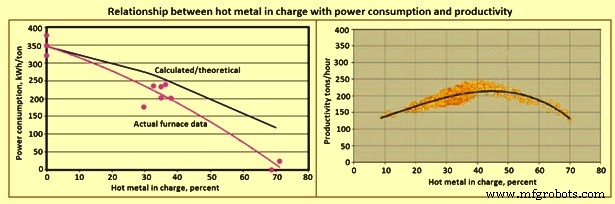
Gbr 1 Hubungan antara logam panas yang bertanggung jawab dengan konsumsi daya dan produktivitas
Peran karbon – Selama pembuatan baja di EAF, karbon diperlukan untuk bereaksi dengan oksigen dan oksida besi untuk membantu pembentukan terak. Beberapa karbon juga diperlukan untuk memenuhi kebutuhan produk. Karbon juga dibebankan di EAF untuk bereaksi dengan di bak mandi dengan oksigen yang disuntikkan untuk menghasilkan gas CO serta memberikan masukan energi kimia yang cukup untuk menghemat konsumsi energi listrik. Pembentukan gas CO dalam bak membantu dalam mencapai konsentrasi rendah dari gas terlarut dalam baja. Gelembung gas CO juga membantu dalam pembusaan terak (membuat emulsi) yang membantu menahan busur listrik dan meningkatkan transfer energi ke penangas baja alih-alih ke cangkang tungku dan transfer ke penangas dengan energi radiasi. Efisiensi transfer di bawah berbagai kondisi terak diberikan di Tab 1.
Tab1 Jenis busur dan efisiensi transfer energi listrik |
No. sl. | Jenis busur | % efisiensi energi listrik |
1 | Pembakaran gratis | 26 |
2 | Sebagian dikelilingi oleh terak berbusa | 65 |
3 | Benar-benar dikelilingi oleh terak berbusa | 93 |
4 | Pemanasan resistensi sebagian | 97 |
5 | Total resistensi pemanasan | 100 |
Dapat dilihat bahwa merendam busur listrik secara total dalam terak berbusa memiliki efek positif yang sangat besar pada transfer energi. Dengan demikian kehilangan panas melalui radiasi dapat dikurangi. Jumlah total penambahan karbon yang dibutuhkan dalam pengoperasian EAF tergantung pada beberapa faktor yaitu (i) kandungan karbon bahan pakan (ii) tingkat konsumsi oksigen yang direncanakan (iii) tingkat karbon tap yang diinginkan (iv) keekonomian hasil Fe dibandingkan dengan biaya karbon dan (v) kapasitas sistem gas buang. Karbon biasanya ditambahkan dalam EAF dalam bentuk batubara atau kokas yang memiliki kadar abu yang merupakan bahan yang tidak diinginkan dalam pembuatan baja. Logam panas memiliki karbon dalam kisaran 3,8% hingga 4,5%. Oleh karena itu penggunaan logam panas menghemat banyak biaya jika dibandingkan dengan penambahan karbon ke bak mandi dari sumber eksternal.
Karena pemulihan karbon muatan yang tidak menentu di EAF, banyak operator EAF telah beralih ke bahan umpan karbon tinggi seperti besi kasar atau logam panas dll. sebagai cara untuk mengurangi variasi dalam operasi pembuatan baja. Bila besi kasar atau logam panas digunakan dalam jumlah besar, tidak perlu menambahkan karbon muatan sama sekali. Setiap 1% logam panas dalam muatan memasok 0,435 kg per ton karbon muatan (mengasumsikan 4% C dalam logam panas, dan hasil sisa 92%). Jadi, 20% logam panas dalam muatan memasok setara dengan hampir 9 kg per ton muatan karbon. Pemulihan karbon yang terkandung dalam bahan umpan logam sangat tinggi (biasanya 90% hingga 100%). Jika peningkatan pemulihan karbon diperhitungkan, jumlah logam panas ini dapat menggantikan 10 kg per ton karbon bermuatan menjadi 60 kg per ton karbon bermuatan.
Fitur desain – Masalah utama EAF adalah kapasitas dekarburisasinya. Kandungan karbon yang tinggi dalam pengisian membutuhkan waktu tambahan untuk dekarburisasi. EAF tidak dapat memanfaatkan laju injeksi oksigen yang khas untuk praktik pembuatan baja BOF. Bagian logam panas yang melebihi 40% telah dianggap sebagai batas maksimum di mana produktivitas EAF berkurang karena kapasitas injeksi oksigen yang tidak mencukupi. Namun, saat ini tersedia EAF yang dirancang untuk menggunakan hingga 80% logam panas.
Batas injeksi oksigen dalam EAF yang dirancang normal biasanya terkait dengan masalah dengan fenomena percikan yang luas, serangan balik, peningkatan konsumsi elektroda dan erosi lapisan refraktori serta pengurangan masa pakai panel atap dan bagian tengah delta refraktori. Tingkat dekarburisasi tipikal dalam EAF yang dirancang normal berkisar dari 0,06% hingga 0,1%. Tingkat karbon yang terlalu tinggi dalam bahan pengisi umpan di EAF semacam itu dapat meningkatkan waktu ketuk ke ketuk karena keterbatasan ini. Hubungan khas antara laju dekarburisasi dan muatan logam panas dalam bahan muatan EAF ditunjukkan pada Gambar 2.
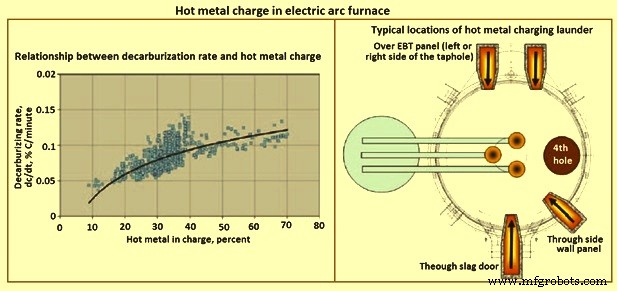
Gbr 2 Muatan logam panas dalam tungku busur listrik
Perbandingan dengan kandungan karbon DRI dan/atau HBI – Selanjutnya dalam kasus DRI/HBI (bahan umpan EAF) karbon juga diperlukan untuk mereduksi oksida besi yang ada dalam DRI dan/atau HBI. Hal ini meningkatkan kebutuhan karbon muatan. Dalam hal logam panas, persyaratan tersebut tidak ada karena logam panas memiliki 100% metalisasi.
Kandungan silikon dan mangan dari logam panas – Logam panas mengandung sejumlah besar silikon dan mangan. Unsur-unsur ini ketika mereka teroksidasi memberikan energi kimia yang selanjutnya mengurangi konsumsi energi listrik. Juga oksida-oksida ini yang bersifat asam meningkatkan konsumsi fluks (CaO dan MgO) untuk menjaga tingkat kebasaan terak yang diperlukan dalam rendaman tungku.
Pengisian logam panas
Pengisian logam panas ke EAF terdengar seperti proposisi sederhana meskipun sebenarnya cukup rumit. Pengisian logam panas dalam EAF membutuhkan perawatan ekstra karena kontak dengan terak tungku yang sangat teroksidasi atau skrap dingin dapat mengakibatkan reaksi yang hebat. Hilangnya kontrol selama pengisian logam panas dapat mengakibatkan luapan terak dan logam dari EAF. Reaksi kekerasan yang serupa biasanya terjadi ketika gradien konsentrasi karbon yang besar berkembang dalam penangas cairan selama fase superheating. Kehilangan kendali selama pengisian logam panas berakhir dengan luapan terak dan baja dari tungku. Dalam kasus ekstrim, kerusakan lengan elektroda juga diamati selama letusan hebat di tungku.
Pengisian logam panas dapat dilakukan di dua lokasi yaitu melalui atap atau pintu terak. Beberapa pabrik mengisi logam panas ke EAF dengan mengayunkan atap dan menuangkannya ke dalam tungku. Hal ini menyebabkan pencampuran yang sangat cepat dari logam panas dengan terak yang sangat teroksidasi di EAF dan terkadang karena ledakan ini memang terjadi. Oleh karena itu, untuk mode operasi ini, direkomendasikan bahwa deoksidasi terak ditambahkan sebelum penambahan logam panas. Deoxidizer yang umum adalah bahan halus silikon, bahan halus aluminium, dan kalsium karbida.
Hal-hal yang penting selama pengisian logam panas di EAF adalah (i) pengisian logam panas harus dilakukan dengan daya untuk menghindari kerugian produktivitas, (ii) kontrol kemiringan sendok logam panas harus cukup tepat untuk memastikan laju penuangan yang stabil , (iii) runner logam panas harus sesingkat mungkin untuk menghindari pembekuan logam panas, dan (iv) runner harus dipanaskan terlebih dahulu di antara operasi penuangan.
Untuk memanfaatkan keuntungan suhu logam panas, pengisiannya ke dalam tungku harus dilakukan dengan atap tertutup. Metode alternatif pengisian logam panas ke EAF adalah dengan menuangkannya ke mesin cuci yang dimasukkan ke sisi EAF. Metode ini membutuhkan lebih banyak waktu untuk mengisi daya logam panas tetapi menghasilkan operasi yang jauh lebih aman.
Biasanya, masalah keterbatasan logistik dan tata letak tidak memberikan terlalu banyak kebebasan untuk memilih tempat di mana sendok logam panas dapat dikirim ke toko EAF, yaitu di sisi pengisian atau penyadapan tungku. Desain EAF sendiri memberlakukan batasan tambahan. Posisi trafo, pembuangan gas, dll. sangat membatasi ruang yang tersedia, di mana runner logam panas dapat dimasukkan ke dalam tungku dan posisi runner yang sebenarnya merupakan kompromi di antara berbagai pertimbangan. Solusi khas diberikan pada Gambar2. Pelari yang dimasukkan melalui pintu terak harus dapat digerakkan (melalui mobil pengisi daya logam panas khusus). Di posisi lain, pelari dapat dipasang pada cangkang tungku atau pada mobil pengisi daya.
Kerugian paling serius dari pengisian terak pintu adalah menuangkan logam panas melawan aliran terak. Dalam beberapa kasus, hal ini dapat mengakibatkan pembuangan fosfor yang buruk dari bak mandi. Selain itu, penuangan dapat dimulai hanya setelah area di belakang pintu terak bebas dari terak. Posisi dinding samping runner bermasalah jika terjadi luapan logam panas. Di tempat itu, sulit untuk mengumpulkan logam yang tumpah. Selain itu, luapan apa pun menimbulkan risiko bagi semua pipa yang dipasang di area sekitarnya. Pelari yang terletak di balkon EBT tampaknya paling menguntungkan. Karena keberadaan skrap terbatas di area itu, pengisian logam panas dapat dimulai sangat awal. Jika terjadi luapan, logam panas dapat dikumpulkan di lubang sadapan di bawah tungku.
Sebagian besar operasi modern menyuntikkan oksigen di beberapa lokasi alih-alih menggunakan tombak pintu terak tunggal. Di bawah kondisi ini, telah ditetapkan bahwa muatan logam panas 30% hingga 40% lebih cocok untuk EAF. Pengisian logam panas hingga 50% telah berhasil digunakan di beberapa EAF. Namun, pengisian logam panas lebih dari 50% mengakibatkan masalah operasional karena panas yang berlebihan dihasilkan melalui oksidasi elemen, seperti karbon, mangan, dan silikon, yang dapat menyebabkan tungku terlalu panas.
Dengan kemajuan baru dalam EAF dan teknologi proses, penghilangan karbon berkecepatan tinggi dari logam panas dapat dicapai di EAF tanpa kehilangan hasil atau membebani sistem off gas. Seiring dengan berkembangnya teknologi EAF, pemanfaatan ekonomis logam panas di EAF telah meningkat dari maksimum 50% menjadi setinggi 80%. Pemanfaatan penuh kandungan energi logam panas sekarang dapat dicapai.