Proses Pembuatan Besi FASTMET dan FASTMELT
Proses Pembuatan Besi FASTMET dan FASTMELT
Proses FASTMET adalah proses pembuatan besi berbasis batubara. Hal ini memungkinkan konversi oksida logam baik dari bijih besi halus atau limbah metalurgi pabrik baja, menjadi besi metalisasi. Proses FASTMELT adalah proses FASTMET dengan penambahan 'electric iron melting furnace' (EIF) untuk menghasilkan besi cair atau logam panas. Kobe Steel bekerja sama dengan Midrex Technologies, Inc., anak perusahaan Kobe Steel di AS, telah mengembangkan proses ini. FASTMET adalah proses unik yang menggunakan rotary hearth furnace (RHF) untuk mereduksi aglomerat yang mengandung batubara dengan rasio reduksi tinggi dan produktivitas tinggi. Gambar 1 menunjukkan penampang yang disederhanakan dan tampilan denah dari RHF.
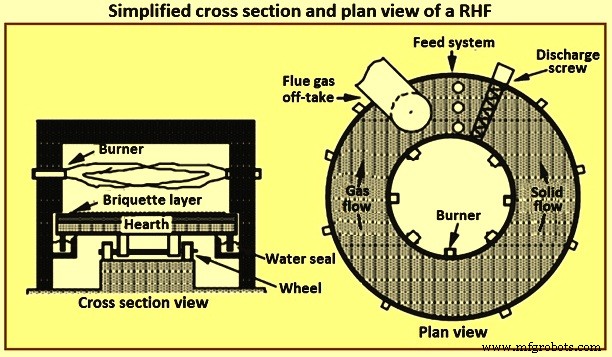
Gbr 1 Penampang melintang yang disederhanakan dan tampilan denah RHF
Proses FASTMET mengubah umpan pelet bijih besi, butiran halus bijih besi dan/atau limbah metalurgi pabrik baja menjadi besi tereduksi langsung (DRI) dengan menggunakan pulverized non-coking coal sebagai reduktor. Produk akhir DRI dapat berupa briket panas untuk menghasilkan besi briket panas (HBI), atau dibuang sebagai DRI panas ke dalam wadah transfer, atau didinginkan jika DRI dingin diperlukan. DRI panas langsung dibuang dari RHF ke EIF dan dilebur untuk menghasilkan logam panas. Logam panas dapat dicor menjadi pig iron. Besi / logam panas yang direduksi dapat dimasukkan ke dalam tungku pembuatan baja utama.
Selain memfasilitasi daur ulang limbah metalurgi ke tungku oksigen dasar / umpan tungku busur listrik, ada dua target utama dari proses tersebut. Salah satunya adalah metalisasi oksida besi yang lebih tinggi, yang mengurangi beban proses peleburan. Yang lainnya adalah rasio penghilangan seng yang tinggi, yang mengurangi konsentrasi seng dalam lingkaran daur ulang. Untuk umpan tanur sembur, diperlukan kekuatan kompresi yang tinggi, yang juga dicapai dengan menyesuaikan pengikat dan rasio pencampuran bahan baku dengan proses FASTMET.
Perkembangan bersejarah
Pengurangan bijih besi di RHF pertama kali dicoba oleh Midland Ross Co., pelopor Midrex Technologies, Inc. Prosesnya, yang disebut 'Heat Fast', unik karena melibatkan pelet komposit, yang terdiri dari bijih besi dan material karbon, yang pra-dipanaskan di perapian, pra-dikurangi dalam RHF dan didinginkan dalam pendingin poros. Proses 'Heat Fast' berhasil diuji di pabrik percontohan 2 ton per jam (tph) di Cooley, Minnesota, dari tahun 1965 hingga 1966.
Bersamaan dengan pengembangan 'Heat Fast', proses DRI Midrex berbasis gas alam, yang menawarkan produk berkualitas lebih tinggi daripada 'Heat Fast' dan biaya operasi yang lebih rendah (gas alam dihargai sangat rendah pada waktu itu) juga sedang dikembangkan. Karena biaya operasi proses gas alam yang saat itu rendah, pekerjaan proses 'Heat Fast' dihentikan dan pengembangan komersial tidak pernah dilakukan.
Midrex menghidupkan kembali minatnya dalam menggunakan RHF untuk pengurangan langsung pada awal 1980-an. Beberapa penelitian telah dilakukan yang menunjukkan bahwa proses berbasis RHF dapat dikembangkan untuk menghasilkan besi tereduksi langsung dengan harga yang menarik. Pada 1990-an, harga gas alam naik dan kemudian pabrik percontohan FASTMET dibangun dan ditugaskan di pusat teknis Midrex dengan RHF berdiameter 2,75 m yang memiliki kapasitas produksi 160 kilogram per jam. Lebih dari 100 kampanye dijalankan dari tahun 1992 hingga 1994.
Kobe Steel dan Midrex Technologies, Inc. berkolaborasi untuk memulai kembali pengembangan proses berbasis batubara RHF dengan tujuan mengkomersialkan teknologi tersebut. Dibangun di atas pabrik percontohan 'Heat Fast' sejak tahun 1960-an, perbaikan dilakukan pada teknologi yang menghasilkan produktivitas yang lebih tinggi, peningkatan kualitas produk, fleksibilitas proses yang lebih besar, dan peningkatan efisiensi proses. Hasil akhirnya adalah pengembangan proses FASTMET. Kobe Steel dan Midrex telah mengambil proses FASTMET satu langkah lebih jauh dalam mengembangkan proses FASTMELT yang membutuhkan pelepasan panas DRI dari RHF dan pengisian secara gravitasi ke dalam EIF, tungku peleburan yang dirancang khusus untuk melelehkan DRI panas FASTMET untuk menghasilkan logam panas.
Sebuah pabrik percontohan demonstrasi dibangun pada tahun 1995 di karya Kakogawa dari Kobe Steel Limited (KSL). Pabrik tersebut memiliki diameter RHF 8,5 m dan kapasitas produksi 2,5 tph. Pabrik tersebut terus beroperasi dari tahun 1995 hingga 1998. Melalui berbagai operasi demonstrasi yang dilakukan di sana, Kobe Steel dan Midrex Technologies, Inc. telah menetapkan proses FASTMET untuk komersialisasi. Pada tahun 2000, pabrik FASTMET komersial pertama dipasok ke pekerjaan Hirohata dari Nippon Steel Company (NSC) untuk mengurangi 190.000 ton per tahun (tpa) limbah pabrik baja. Proses FASTMET dikenal karena kemampuannya mendaur ulang debu besi secara efisien. Rincian lima pabrik pertama yang telah ditugaskan diberikan di Tab 1.
Tab 1 pabrik komersial FASTMET |
| Satuan | NSC Hirohata no. 1 | NSC Hirohata no. 2 | NSC Hirohata no. 3 | JFE Steel, Fukuyama | KSL Kakogawa |
Rasio umpan RHF | tpa | 190.000 | 190.000 | 190.000 | 190.000 | 16.000 |
Bahan baku | | Debu BOF | Debu BOF | Debu BOF | Debu BF, debu BOF | Debu BF, Debu BOF, Debu EAF |
Aplikasi produk | | Umpan BOF, DRI | Umpan BOF, DRI | Umpan BOF, HBI | Umpan BOF, DRI | Umpan BF &BOF, DRI |
Diameter luar RHF | m | 21.5 | 21.5 | 21.5 | 27 | 8.5 |
Tanggal komisioning | | April, 2000 | Januari, 2005 | Desember, 2008 | April, 2009 | April, 2001 |
Dapat dilihat bahwa proses ini sedang digunakan saat ini untuk pemanfaatan limbah metalurgi dari pabrik baja. Selain limbah metalurgi, proses ini juga dapat menggunakan butiran bijih besi yang berukuran sama dengan ukuran pakan pelet (kurang dari 45 mikrometer). Ini karena prosesnya memiliki langkah-langkah aglomerasi bawaan. Proses FASTMET/FASTMELT menghadirkan rute alternatif untuk pembuatan besi dalam kapasitas mulai dari 100.000 tpa hingga 500.000 tpa. Proses FASTMELT menawarkan alternatif untuk teknologi mini blast furnace (BF). Refraktori yang digunakan dalam RHF dan EIF adalah spesifikasi standar yang biasanya digunakan dalam pembuatan besi. Desain EIF didasarkan pada desain teknologi EAF (tungku busur listrik) dan LF (tungku sendok) yang telah terbukti.
Fitur proses FASTMET
Proses FASTMET jelas berbeda dari proses reduksi berbasis gas menggunakan gas reformed yang dihasilkan dari gas alam, dalam hal ini memanaskan dan mereduksi aglomerat komposit, masing-masing terdiri dari bijih besi, atau limbah metalurgi pabrik baja, dan batu bara. Proses sederhana dan unik yang melibatkan pemanasan cepat ini menghasilkan reaksi reduksi yang cepat. Aglomerat ditempatkan dalam satu atau dua lapisan rata di atas perapian dan dipanaskan menggunakan panas radiasi. Hal ini mencegah oksidasi aglomerat, meskipun gas buang pembakaran dalam kondisi tungku, yang memiliki potensi oksidasi yang cukup besar.
Proses ini dapat mencapai pemanasan dan pengurangan aglomerat secara bersamaan dan efektif pada rasio udara-gas yang ideal di RHF. Selain itu, gas mudah terbakar yang dihasilkan dari karbon dalam aglomerat terbakar dalam pembakaran sekunder di atasnya. Ini sangat menekan emisi NOx, meskipun faktanya RHF adalah tungku yang memiliki lingkungan suhu tinggi. Ini adalah fitur lain dari proses FASTMET.
Saat perapian RHF berputar, pelet atau briket melewati tiga zona dan dipanaskan dengan cepat. Setiap zona memiliki tiga pembakar berbahan bakar gas, yang jatah udara / bahan bakarnya dapat disesuaikan untuk mencapai pembakaran ramping atau kaya yang diinginkan di setiap zona. Di ujung zona 3, material lewat di bawah dinding pemisah yang memisahkan zona pembakaran akhir dari zona pelepasan. Sekrup heliks membawa produk DRI panas dari perapian ke saluran pengalih dan kemudian secara gravitasi ke dalam wadah produk DRI yang dibersihkan dengan nitrogen atau ke dalam EIF.
Sebuah penukar panas dipasang pada peralatan pengolahan gas buang mengubah energi yang terkandung dalam gas buang suhu tinggi menjadi energi untuk memanaskan udara yang digunakan baik untuk pembakaran atau pengeringan bahan baku. Ini mengurangi konsumsi energi secara keseluruhan.
Bahan mentah seperti debu pabrik baja terkadang dapat menghasilkan dioksin saat terbakar. Namun, dalam proses FASTMET, suhu RHF adalah 1.300 derajat C atau lebih tinggi, yang cukup tinggi untuk menekan pembentukan dioksin. Gas buang dari RHF didinginkan dengan cepat melalui daerah suhu di mana dioksin dapat bergabung kembali, sehingga mencegahnya dari pengomposan ulang. Gambar 2 menunjukkan lembar aliran khas dari proses FASTMET / FASTMELT.
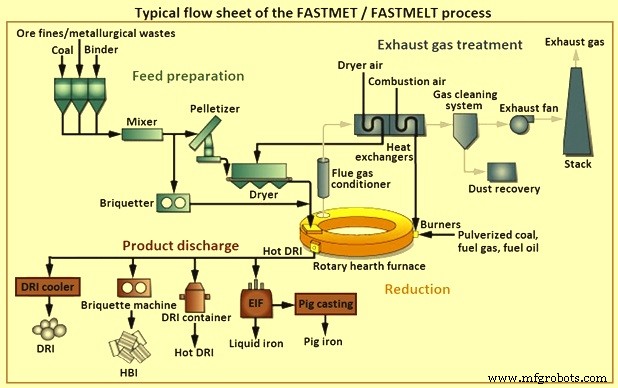
Gbr 2 Flow sheet khas dari proses FASTMET / FASTMELT
Gas panas yang keluar dari RHF didinginkan melalui pendingin evaporatif sebelum memasuki penukar panas. Panas sensibel dalam gas buang digunakan untuk memanaskan awal udara pembakaran RHF dan udara pengering bola hijau hingga sekitar 350 derajat C. Gas buang yang meninggalkan pra-pemanas selanjutnya didinginkan oleh pendingin evaporatif kedua sebelum memasuki bag house, di mana seng oksida dipulihkan dan dikirim ke silo debu untuk disimpan. Kipas angin yang diinduksi ditempatkan pada outlet bag house untuk mencapai penurunan tekanan yang diperlukan untuk sistem gas buang dan mengontrol RHF di bawah tekanan yang sedikit negatif.
Utilitas yang dibutuhkan adalah plant air, nitrogen, steam, instrument air, make-up water, dan liquefied natural gas. Pabrik juga membutuhkan sirkuit air proses resirkulasi terbuka serta sirkuit air pendingin mesin tertutup.
DRI panas, dikeluarkan dari RHF, memiliki tiga opsi pelepasan yaitu (i) didinginkan untuk menghasilkan DRI dingin, (ii) dibriket dalam mesin briket untuk menghasilkan HBI, (iii) dilebur dalam EIF untuk menghasilkan besi cair. Besi cair ini dapat dicor dalam pig caster untuk menghasilkan pig iron.
DRI memiliki banyak pori-pori yang tersisa setelah proses reduksi. Jika terkena udara untuk waktu yang lama, besi logam teroksidasi kembali menjadi oksida besi, menurunkan kualitasnya. Jika DRI tidak segera digunakan sebagai bahan baku untuk tungku peleburan atau tanur sembur, pemadatan dan pemadatan DRI menjadi besi briket panas (HBI) mencegah reoksidasi. Hal ini memungkinkan penyimpanan besi tereduksi untuk jangka waktu yang lama tanpa penurunan kualitas. HBI yang disimpan dapat diumpankan ke tungku pembuatan baja primer atau ke tanur tinggi. Apakah besi tereduksi yang dihasilkan proses FASTMET digunakan sebagai DRI dalam bentuk pelet/briket atau dibentuk menjadi HBI menggunakan peralatan HBI tergantung pada aplikasi produk (sumber besi) dan masa penyimpanannya.
Limbah metalurgi (debu) yang dihasilkan di pabrik baja secara konvensional telah dibuat pelet atau disinter di rumah untuk mendaur ulang debu sebagai bahan baku untuk tanur sembur. Bahan baku tanur sembur, bagaimanapun, mengandung komponen yang mudah menguap, khususnya seng, yang menguap di zona suhu tinggi tanur sembur. Namun, tidak semua uap keluar dari tanur sembur. Beberapa bagian dari uap didinginkan dan terperangkap oleh bahan yang baru diisi, tetap berada di tungku. Akumulasi komponen volatil menurunkan permeabilitas tanur sembur, dan sangat mengganggu produktivitasnya.
Proses FASTMET menguapkan logam berat seperti seng dan timbal, yang telah menghambat daur ulang besi tua, dan mengubahnya menjadi seng oksida mentah dan sejenisnya. Hal ini memungkinkan pelepasan elemen-elemen ini ke saluran pembuangan tanpa mengedarkannya dalam proses. Fasilitas pengolahan gas buang dilengkapi dengan sistem pendingin dan pengumpulan debu, yang dikombinasikan dengan pendingin udara dan pendingin air, mencegah komponen yang mudah menguap menempel pada dinding peralatan. Hal ini memungkinkan operasi yang stabil dan berkelanjutan untuk jangka waktu yang lama dan pengumpulan oksida seng mentah dan sejenisnya, menggunakan bag filter. Seng oksida mentah yang dikumpulkan adalah sumber daya yang berharga dan didaur ulang bersama dengan besi yang tereduksi.
Proses dan prinsip reaksi
Proses FASTMET dimulai dengan pencampuran butiran halus bijih besi atau limbah metalurgi pabrik baja (mengandung oksida besi dalam persentase tinggi) dengan bubuk batubara, aglomerasi campuran menjadi pelet atau briket menggunakan pelletizer atau briket, pengeringan aglomerat dalam pengering, dan menempatkan aglomerat di atas perapian RHF dalam satu atau dua lapisan yang rata.
Pelet atau briket harus diisolasi dari udara saat memasuki tungku. Tingkat umpan mereka dikontrol secara tepat pada waktu yang sama. Proses FASTMET berisi sistem pipa umpan yang memungkinkan penyesuaian jumlah pipa sesuai dengan ukuran tungku, sehingga secara bersamaan mencapai isolasi dari udara dan kontrol volume. Sistem levelling tipe sekrup diadopsi untuk menempatkan aglomerat dalam satu atau dua lapisan genap.
Saat perapian berputar, briket dipanaskan oleh radiasi dari suhu zona RHF lebih dari 1.300 derajat C dan oksida besi direduksi menjadi besi metalik. Reduksi oksida besi dilakukan terutama dengan mereaksikan karbon unsur tetap dengan magnetit (Fe3O4) atau hematit (Fe2O3) untuk membentuk besi logam (Fe) dan wustit dalam bentuk padat sambil mengembangkan gas karbon monoksida (CO) dan karbon dioksida (CO2). . Beberapa karbon masuk ke dalam larutan padat dengan besi logam untuk membentuk besi karbida (Fe3C).
Seng oksida, oksida timbal, dan oksida logam mudah menguap lainnya yang terkandung dalam umpan limbah metalurgi juga direduksi menjadi bentuk logam dan diuapkan. Uap logam ini dioksidasi ulang dalam gas buang sebelum meninggalkan tungku melalui pengambilan.
Metode pemanasan cepat, teknologi eksklusif Kobe Steel diadopsi untuk memanaskan pelet atau briket yang diletakkan di atas perapian, dengan cepat mencapai suhu tinggi 1.350 derajat C. Pemanasan ini menghasilkan reaksi oksida dan karbon. Berdiam selama 8 menit sampai 16 menit, aglomerat diubah menjadi DRI, yang dikeluarkan dari tungku atau disuplai ke proses hilir, pada suhu 1.000 derajat C sampai 1.200 derajat C. Reaksi yang berbeda yang terjadi antara oksida dan karbon adalah (i) Fe2O3+3C =2Fe+3CO, (ii) Fe3O4 4C =3Fe+4CO, (iii) Fe2O3 +3CO =2Fe+3CO2, (iv) Fe3O4 4CO =3Fe 4CO2, (v) FeO +CO =Fe+CO2, dan (vi) ZnO =.
Gas pembakaran (gas CO) yang dikeluarkan dari pelet / briket sebagai hasil dari reaksi reduksi dapat digunakan sebagai bahan bakar untuk RHF, yang secara signifikan mengurangi jumlah bahan bakar yang dipasok ke burner.
Atmosfer dalam EIF proses FASTMELT pada dasarnya terdiri dari gas CO dan karenanya sangat tereduksi. Atmosfer yang berkurang ini mendorong pengurangan silikon dan penghilangan belerang.
Pelepasan DRI yang stabil dan berkelanjutan dari RHF pada suhu tinggi dicapai dengan teknologi eksklusif KSL seperti meninggikan perapian tungku reduksi. Tidak seperti tanur tinggi, FASTMET dapat memulai dan menghentikan pengoperasian dengan relatif mudah bergantung pada jumlah produksi, yang memungkinkan produksi untuk merespons permintaan.
Mekanisme pengurangan
Kinematika reaksi reduksi dalam tungku reduksi langsung biasanya dikendalikan oleh difusi gas reduksi dari luar. Pada proses FASTMET, reaksi reduksi terjadi di dalam pelet/briket komposit karbon yang terdiri dari butiran halus bijih besi dan batu bara yang dihaluskan. Setelah pelet / briket komposit dipanaskan, gas CO di dalamnya, mempromosikan pengurangan oksida besi. Oleh karena itu reaksi reduksi berlangsung lebih cepat dalam pelet / briket komposit karbon daripada reaksi reduksi yang terjadi pada proses reduksi langsung konvensional. Reaksi reduksi dasar yang dianggap terjadi selama proses FASTMET adalah (i) FexOy + yC =xFe + y CO (reaksi endoterm), (ii) CO2 + C =2CO (reaksi endoterm), dan (iii) FexOy + yCO =xFe + yCO2 (reaksi eksotermik).
Pada suhu di bawah titik leleh besi, hampir tidak ada reaksi langsung dengan karbon padat dari bubuk batu bara dan oleh karena itu reaksi seperti yang diberikan dalam persamaan (i) mendominasi kinematika reaksi. Pada suhu yang lebih tinggi dari 1.000 derajat C dan lebih, reaksi pembentukan gas CO dengan kehilangan larutan karbon sesuai persamaan (ii) dan reaksi oksida besi oleh gas CO sesuai persamaan (iii) berlangsung secara seri di dalam karbon komposit pelet/briket. Dalam reaksi ini, pembentukan gas CO mengontrol kinematika reaksi dengan sifatnya yang sangat endotermik. Oleh karena itu untuk mendorong reaksi, perlu untuk memasok panas yang dibutuhkan untuk reaksi ke bagian dalam pelet / briket komposit karbon pada suhu yang lebih tinggi dari 1.000 derajat atau lebih. Ini berarti panas dipindahkan secara efisien melalui radiasi dari atmosfer ke permukaan pelet/briket, dan dengan konduksi dari permukaan pelet/briket ke bagian dalamnya. Gambar 3 menunjukkan mekanisme reduksi pelet/briket komposit karbon
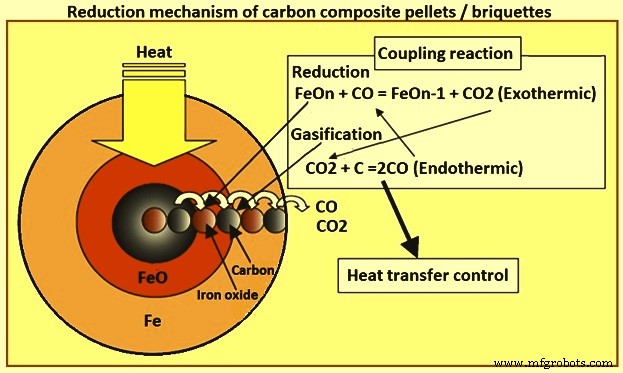
Gbr 3 Mekanisme reduksi pelet / briket komposit karbon
Di RHF, pelet / briket biasanya dipanaskan dengan suhu zona lebih dari 1.300 derajat C dan direduksi menjadi besi logam. Waktu tinggal di perapian biasanya 8 menit sampai 16 menit. Ini bervariasi tergantung pada bahan yang diproses, ukuran pelet / briket, dan faktor lainnya. Laju reduksi cepat yang dicapai dalam proses FASTMET disebabkan oleh suhu reduksi yang tinggi, laju perpindahan panas yang tinggi, dan kontak yang erat antara karbon yang terkandung di dalam briket dengan oksida besi. Perpindahan panas dan reaksi reduksi yang berbeda yang terjadi di RHF secara skematis ditunjukkan pada Gambar 4.
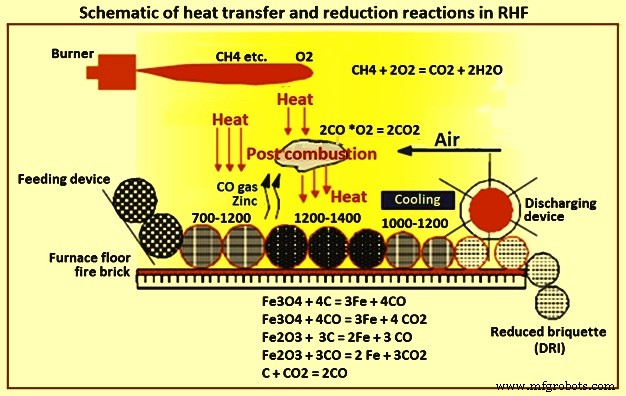
Gbr 4 Skema perpindahan panas dan reaksi reduksi di RHF
Produk
Produk akhir dari proses FASTMET/FASTMELT dapat berupa HBI, DRI panas yang dibuang langsung ke wadah transfer, DRI dingin, atau besi cair (hot metal). Metalisasi yang dicapai selama proses lebih dari 85%. Suhu logam panas yang dihasilkan oleh proses FASTMELT berkisar antara 1.450 derajat C hingga 1.550 derajat C dan memiliki komposisi khas karbon – 3% hingga 5%, silikon – 0,3% hingga 0,6%, mangan – 0,6% hingga 1,2% , belerang – kurang dari 0,05%, dan fosfor – kurang dari 0,03 %.
Perlakuan gas buang dan kontrol lingkungan
Gas buang yang meninggalkan RHF sepenuhnya terbakar, mengandung sekitar 2% oksigen. Penukar panas menggunakan energi panas dalam gas buang untuk memanaskan awal udara pembakaran untuk pembakar RHF dan pengering persiapan bahan baku. Gas buang meninggalkan tungku perapian putar melalui atap dan mengalir melalui saluran pembuangan yang dilapisi refraktori ke saluran gas buang. Lokasi yang tepat dari pengambilan gas buang relatif terhadap zona pembakaran RHF ditentukan oleh analisis bahan umpan, kinetika reduksi, dan diverifikasi oleh 'Computational Fluid Dynamics'. Udara pengenceran disuntikkan ke saluran gas buang untuk mendinginkan dan membakar sisa bahan mudah terbakar (hidrogen dan CO) dalam aliran gas buang.
Semprotan air ditambahkan ke pendingin utama untuk mendinginkan gas dari lebih dari 1.400 derajat C ke 1.000 derajat C untuk meminimalkan pembentukan NOx dan untuk memberikan suhu masuk yang dapat diterima untuk recuperator. Dari pendingin primer gas buang dialirkan melalui udara pembakaran dan preheater udara pengering dimana panas dari gas buang digunakan untuk memanaskan udara pembakaran untuk rotary hearth burner dan rotary dryer. Gas buang keluar dari pemanas awal pembakaran ke pendingin sekunder. Semprotan air ditambahkan ke pendingin sekunder untuk mendinginkan gas dari sekitar 800 derajat C hingga 120 derajat C untuk memberikan suhu masuk yang dapat diterima untuk sistem bag filter. Gas buang kemudian mengalir ke rumah bag filter kain jet tempat oksida seng mentah dikumpulkan dan kemudian ke kipas ID di mana ia dibuang melalui tumpukan ke atmosfer.
Kontrol SO2 biasanya tidak diperlukan dalam proses FASTMET karena sebagian besar SO2 bereaksi dengan dan diserap oleh oksida logam dalam aliran gas buang. Injeksi kapur dapat digunakan untuk mengontrol SO2 lebih lanjut. NOx dikendalikan oleh penggunaan pembakar NOx rendah dan kontrol operasional yang ketat dari rasio udara terhadap bahan bakar dan suhu pembakaran. Dioksin dan Furan dihancurkan oleh suhu tinggi dan waktu tinggal yang lama di dalam RHF. Laju pendinginan gas buang dikontrol untuk meminimalkan pembentukan Dioksin dan Furan. Partikulat dikeluarkan dari gas buang dengan sistem bag filter. Seng oksida mentah dikumpulkan oleh sistem bag filter dan disimpan dalam silo.
Proses FASTMET adalah proses yang ramah lingkungan. Emisi CO2 dari proses FASTMELT adalah sekitar 1,6 ton per ton logam panas (t/tHM) dibandingkan sekitar 2,1 t/tHM emisi CO2 dalam kasus tanur sembur mini. Emisi NOx berkisar antara 0,3 kilogram per ton logam panas (kg/tHM) hingga 1,5 kg/tHM dan emisi SOx sekitar 2,4 kg/tHM.
Manfaat dari proses FASTMET
Proses FASTMET memberikan pilihan lain untuk penanganan limbah metalurgi pabrik baja. Pabrik FASTMET yang berlokasi di pabrik baja dapat memproses debu dan membuat dua produk utama, DRI untuk umpan balik ke tungku pembuatan baja utama, dan seng oksida mentah untuk dijual ke prosesor seng. Itu membuat kewajiban menjadi aset. Biaya pembuangan yang tinggi dihilangkan dan pasokan unit besi yang murah tersedia.
Manfaat proses meliputi (i) pembentukan butiran halus yang sangat rendah dalam proses menghasilkan kandungan seng yang tinggi dan kandungan besi yang sangat rendah dari debu sekunder, (ii) metalisasi yang tinggi dan penghilangan seng yang tinggi membuat produk besi tereduksi dapat didaur ulang ke tungku pembuatan baja primer, ( iii) tidak ada limbah yang dihasilkan untuk dibuang, (iv) perlakuan suhu tinggi menguraikan dioksin, dan (v) debu seng dapat diolah secara ekonomis dan menjadi produk, bukan limbah.