Sendok Baja Penuh dan Lapisan Tahan Apinya
Sendok Baja Penuh dan Lapisan Tahan Apinya
Steel teeming ladle (STL) diperlukan di pabrik baja untuk menampung dan mengangkut baja cair dari tungku pembuatan baja ke fasilitas pengecoran. Saat ini STL digunakan dengan cara yang jauh lebih kompleks daripada toko peleburan baja tua di mana sendok digunakan hanya untuk mengangkut baja cair dari tungku pembuatan baja ke cetakan ingot.
Fungsi lain yang dilakukan dalam STL adalah kontrol suhu, deoksidasi, penambahan karburator dan paduan besi, serta pengapungan inklusi. Di masa lalu, permintaan untuk berbagai kelas baja dengan spesifikasi yang ketat telah meningkat pesat. Baja ini diproduksi menggunakan proses pemurnian sekunder. Lapisan STL harus tahan terhadap kondisi layanan yang semakin parah terkait dengan proses pemurnian sekunder. Kondisi parah ini adalah waktu penahanan yang lebih lama, suhu cairan yang lebih tinggi dan pemanasan busur/kimia. Pembilasan dengan gas inert dan degassing baja cair, paduan dan penggunaan terak sintetis juga mempercepat keausan lapisan. Karena kegiatan ini, permintaan kualitas refraktori STL telah meningkat sangat banyak.
Di toko peleburan baja saat ini, STL berfungsi sebagai komponen perjalanan dari proses skimming, pembilasan, pemanasan ulang, dan penghilangan gas. Waktu pemaparan untuk panas tertentu di toko-toko ini telah diperluas dari dua menjadi lima kali lipat dari waktu yang diperlukan sebelumnya untuk penumpukan ingot.
STL juga diperlukan untuk menghemat panas dengan meminimalkan kehilangan panas selama transportasi dan selama berbagai langkah proses. Dalam hal ini, perkembangan signifikan telah dilakukan untuk memanaskan sendok dengan benar sebelum pemanasan pertama, dan memutar sendok pada pemanasan berikutnya dengan cara meminimalkan kehilangan panas.
STL dirancang agar tahan panas dan kuat. Juga perlu untuk memanaskan sendok. Insulasi panas yang tepat diperlukan agar baja cair yang terkandung dalam STL tetap pada suhu yang tepat.
Umur lapisan refraktori STL harus dapat diprediksi dan direproduksi untuk alasan keamanan dan untuk menghindari penundaan proses. STL sering dikeluarkan dari sirkulasi untuk melakukan pemeliharaan lapisan. Hal ini dapat mempengaruhi pasokan sendok yang memadai untuk produksi baja. Juga biaya refraktori untuk STL signifikan dan biaya pembuangan lapisan bekas juga cukup besar.
Pemilihan lapisan refraktori yang paling cocok tergantung pada sejumlah faktor yang meliputi siklus sirkulasi STL, proses pembuatan baja sekunder, kualitas baja, ketersediaan sendok, pengembangan refraktori baru, logistik toko dan biaya refraktori per ton baja mentah yang diproduksi. .
Siklus sirkulasi sendok
Waktu penyelesaian sendok adalah waktu yang dibutuhkan untuk menyelesaikan satu siklus sirkulasi dan penting untuk kelancaran bengkel peleburan baja. Biasanya dibutuhkan beberapa jam dari satu penyadapan baja ke penyadapan baja berikutnya dalam sendok. Waktu penyelesaian sendok menentukan jumlah sendok yang harus dimasukkan ke dalam sirkulasi. Siklus sirkulasi sendok melibatkan langkah-langkah berikut.
• Pemeriksaan dan pemeliharaan STL ? STL diperlukan untuk menahan baja cair pada suhu sekitar 1600 derajat C hingga 1650 derajat C untuk jangka waktu yang lama. Temperatur tinggi ini bersama dengan berbagai proses yang harus dilakukan di STL berarti bahwa ada keausan pada lapisan. Oleh karena itu, STL membutuhkan pemeriksaan dan pemeliharaan yang berkelanjutan agar tetap dalam kondisi yang baik. Pemrosesan STL di antara pemanasan diperlukan untuk menghilangkan terak sendok dan menyediakan pembersihan sumur sendok, pemeriksaan dan perbaikan pintu geser, dan pengamplasan sumur sendok.
• Pemanasan awal sendok – Setelah pemeriksaan dan pemeliharaan, STL dipanaskan terlebih dahulu untuk memasukkan sendok ke dalam suhu ke nilai yang diinginkan. Jika suhu bagian dalam sendok telah mencapai tingkat yang diinginkan setelah pemeriksaan dan pemeliharaan, maka langkah ini dapat dilewati.
• Penyadapan baja cair – Baja cair dari proses pembuatan baja utama disadap ke dalam STL. Saat menyadap baja cair, diperlukan tindakan pencegahan agar papan bebas yang cukup tersedia di STL untuk melakukan proses pemurnian sekunder.
• Pengangkutan sendok ?STL dengan baja cair diangkut biasanya dengan mobil transfer ke proses pemurnian sekunder. Selama langkah ini, penantian sendok dengan baja cair harus dihindari untuk mengontrol kehilangan suhu.
• Proses pemurnian sekunder – Baja cair di STL mengalami berbagai perlakuan dalam proses pemurnian sekunder sesuai persyaratan kualitas baja. Pada tahap ini dilakukan penyesuaian komposisi kimia dan temperatur baja cair. Pembilasan baja cair juga dilakukan untuk mengurangi stratifikasi dan membuat baja lebih homogen.
• Pengecoran kontinyu – Setelah proses pembuatan baja sekunder, kompon penutup sendok diletakkan pada permukaan cairan di STL untuk mengurangi kehilangan panas pada bagian atas karena radiasi dan STL dibawa ke ladle turret mesin continuous casting (CC) untuk pengecoran baja cair. Penutup sendok juga digunakan untuk mengurangi kehilangan panas. Setelah operasi CC selesai, baja cair dan terak yang tersisa dibuang ke dumping ladle dan STL dikirim ke area inspeksi dan perawatan ladle.
Siklus sendok ditunjukkan pada Gambar 1.
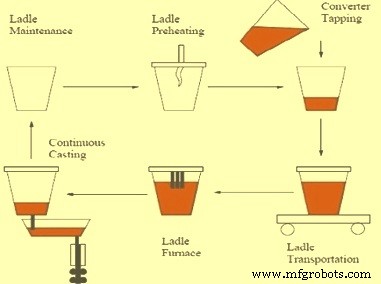
Gbr 1 Siklus sendok
Pemanasan awal STL dan perangkat penutup telah meningkat secara signifikan dalam beberapa tahun terakhir, dan banyak jenis pemanas awal (sendok horizontal atau vertikal) tersedia. Ada beberapa keuntungan dari pemanasan awal dan siklus ladle yang tepat yang mencakup umur refraktori yang lebih lama dengan meminimalkan kejutan termal. Kemampuan sebenarnya untuk menggilir STL dengan cepat dan membuat penggunaan preheater yang paling efisien dapat sangat bervariasi antar operasi, tergantung pada tata letak bengkel dan kemampuan pemindahan sendok.
Pembuatan baja adalah proses yang kompleks dan sulit dan jenis serta pemilihan refraktori bukanlah tugas yang mudah. Pemilihan refraktori itu sendiri seringkali merupakan kompromi, karena biasanya tidak mungkin untuk memiliki semua sifat yang diinginkan (fisik, kimia, dan termal) semua dalam satu bahan. Satu fitur biasanya diperoleh dengan merugikan yang lain. Lapisan tahan api STL juga dapat mempengaruhi kualitas baja yang dihasilkan jika oksigen diambil dari lapisan selama setiap tahap pemrosesan. Lapisan yang mengandung SiO2 dalam bentuk yang tidak digabungkan dapat menyebabkan masalah pada sendok modern.
Dalam beberapa tahun terakhir, analisis elemen hingga menggunakan sifat refraktori non linier dan rezim suhu transien sedang digunakan untuk mempelajari perilaku refraktori di STL. Meskipun sangat kompleks, studi pada dasarnya berusaha untuk mempertahankan tingkat kompresi yang tepat pada refraktori sendok selama semua fase penggunaannya di sendok. Gaya tekan yang berlebihan dapat mengakibatkan retak tahan api dan/atau tekuk di area seperti bagian datar sendok. Tegangan tekan yang lebih rendah dari yang diinginkan dapat menyebabkan sambungan atau celah terbentuk, yang memungkinkan baja cair atau penetrasi terak.
Sifat refraktori dapat disesuaikan untuk memberikan perilaku yang tepat dalam STL. Hal ini diperlukan untuk menggunakan refraktori khusus untuk meningkatkan atau menurunkan ekspansi refraktori ke tingkat yang lebih diinginkan. Analisis elemen hingga sendok memberikan panduan berharga untuk meningkatkan perilaku layanan refraktori di STL.
Refraktori di STL dikategorikan dalam jenis dan ketebalan untuk memberikan layanan maksimal dengan biaya minimum. Lapisan relatif tipis untuk memenuhi kapasitas sendok dan persyaratan berat. Biasanya ketebalan lapisan kerja adalah 150 mm hingga 225 mm di dalam laras dan 225 mm hingga 300 mm di bagian bawah. Ketebalan lapisan pengaman dapat bervariasi dari 50 mm hingga 150 mm.
Bahan tahan api yang biasa digunakan untuk pelapis adalah bata dolomit, bata krom magnesia, bata karbon magnesia, bata alumina tinggi, bata karbon aluminium, dan castable alumina tinggi. Jenis konstruksi refraktori sangat bervariasi tergantung pada kondisi operasi dan kemampuan untuk memutar STL dengan cepat. Refraktori alumina tinggi cocok untuk sebagian besar area STL selain jalur terak.
Lapisan pengaman berfungsi untuk menahan baja atau terak untuk periode waktu yang terbatas, tetapi pada dasarnya menyediakan insulasi cangkang. Beberapa lapisan pengaman komponen dapat digunakan untuk lebih menurunkan suhu cangkang. Di beberapa pabrik, lapisan pengaman setebal 100 mm yang terbuat dari komposit dengan batu bata insulasi kekuatan tinggi digunakan untuk menurunkan suhu cangkang baja.
Temperatur cangkang baja yang lebih tinggi di jalur terak terutama disebabkan oleh konduktivitas termal yang lebih tinggi dari bata pelapis kerja jalur terak. Secara umum, hanya sedikit STL yang menggunakan bahan insulasi sejati sebagai bagian dari lapisan pengaman karena umur lapisan pengaman yang berkurang dan/atau meningkatnya bahaya penetrasi baja dan kemungkinan pecah.
Konstruksi tahan api khusus yang digunakan untuk STL selalu berubah di sebagian besar toko peleburan baja. Ada beberapa faktor dan sifat refraktori yang penting untuk pemilihan refraktori di setiap area STL. Beberapa di antaranya dijelaskan di bawah ini.
Keausan di zona tumbukan terjadi saat aliran baja momentum tinggi menghantam dasar sendok (dan dalam beberapa kasus dinding samping bawah) selama periode awal penyadapan. Tingkat keparahan keausan ini cukup spesifik untuk toko dan membutuhkan ketebalan atau kualitas refraktori tambahan untuk digunakan. Secara umum, refraktori untuk tumbukan sungai dipilih untuk memiliki ketahanan erosi maksimum berdasarkan kekuatan panas.
Di bagian bawah dan area laras bawah STL, keausan terjadi akibat erosi selama pembilasan atau pemanasan ulang dan dari kerusakan fisik selama deskulling di antara pemanasan. Dalam beberapa kasus, terak yang tersisa di area ini pada waktu antara penghentian baja pada mesin CC dan pembuangan terak dapat menyebabkan masalah erosi terak. Secara umum, erosi terak di daerah ini tidak cukup untuk membuat zona, kecuali untuk menambah ketebalan refraktori. Kerusakan akibat pengangkatan tengkorak terkadang cukup parah sehingga memerlukan perbaikan bagian bawah.
Area barel biasanya merupakan area keausan paling ringan di STL dan dapat dikategorikan untuk kualitas dan/atau ketebalan.
Area keausan yang paling parah dari banyak STL adalah garis ladle slag dimana refraktori mengalami korosi yang parah. Terak yang ditemukan sangat bervariasi, dan termasuk terak besi oksida (FeO) tinggi yang terbawa dari tungku pembuatan baja, terak buatan yang dimasukkan setelah skimming terak parsial, terak ditambahkan atau dibentuk selama tujuan metalurgi tertentu seperti pembilasan atau injeksi, dan terak yang dibentuk atau diedarkan selama degassing. Karena berbagai jenis terak biasanya bersifat basa, refraktori dasar diperlukan dalam jalur terak STL.
Efek korosif pada refraktori sangat parah ketika pemanasan ulang busur digunakan untuk mengontrol dan menambah suhu baja dengan memanaskan terak sendok. Suhu terak dapat diharapkan 40 derajat C sampai 150 derajat C di atas suhu baja. Pada suhu ini laju erosi terak dapat meningkat dua hingga lima kali lipat. Erosi terak dapat dikurangi dengan mengontrol kebasaan terak, kandungan Al2O3, dan penambahan MgO pada terak. Oleh karena itu, kontrol yang signifikan atas jumlah erosi selama pemanasan ulang busur dapat diperoleh dengan menggunakan terak terkontrol yang diperoleh dengan menggunakan komposisi dengan tambahan MgO dan penggunaan pembilasan terak yang konsisten untuk mengontrol panas berlebih terak. Untuk garis terak dolomit, digunakan batu bata magnesit chrome atau MgO-C.
Kerusakan siklus termal juga merupakan salah satu alasan keausan di semua area STL. Tingkat kerusakan tersebut sangat diminimalkan dengan penggunaan pemanasan awal yang tepat dan penggunaan penutup sendok yang lebih ekstensif. Penggunaan jumlah STL seminimal mungkin setiap saat dan untuk memutar sendok ini secepat mungkin juga meminimalkan tingkat kerusakan siklus termal.
Melenturkan sendok saat mengangkat dan selama bagian lain dari siklus sendok diketahui mempengaruhi masa pakai sendok.
Upaya untuk memerangi efek ini dengan desain yang lebih baik di sendok dan pelapis terus berlanjut.
STL dilapisi dengan konstruksi bata jenis arch-wedge atau keyed. Jenis konstruksi bata lainnya menggunakan bentuk semi-universal yang memungkinkan penggunaan spiral bata ke atas pada sisi miring sendok. Dalam konstruksi jenis ini, penguncian bata dilakukan dengan permukaan perkawinan yang melengkung.
Dalam semua kasus, konstruksi yang rapat dengan sambungan mortar yang sangat tipis (atau tanpa sambungan) diperlukan untuk menjaga agar lapisan tetap di bawah tekanan dan mencegah penetrasi sambungan. Beberapa pabrik telah dikonversi menjadi STL yang dilapisi dengan castable di bagian laras dan bawah, tetapi upaya untuk membuat garis terak dasar tidak terlalu berhasil.
Lining dengan castables memberikan konstruksi tanpa sambungan yang sangat baik dan banyak yang menawarkan keuntungan biaya di mana sebagian dari pelapis bekas dapat digunakan kembali. Sendok castable memang membutuhkan peralatan khusus, termasuk ruang, dan harus dipasang dan dikeringkan dengan sangat hati-hati.
STL juga digunakan di mana kombinasi bata dan castable digunakan untuk mendapatkan kombinasi teknis dan ekonomis terbaik dari pendekatan castable dan bata untuk lapisan ladle.
Kerucut atau sumbat tahan api digunakan di dasar sendok untuk memasukkan gas pembilas, terutama argon, untuk pembilasan sendok. Colokan yang memiliki penampang melintang menggunakan mekanisme arah yang berbeda untuk menyediakan aliran argon yang terkontrol digunakan.
Performa dan masa pakai busi yang andal sangat penting dalam menghasilkan kualitas produk baja yang konsisten. Untuk memastikan aliran yang tepat, sering kali perlu membersihkan permukaan sumbat setelah diberi panas dengan pembakaran oksigen atau pembersihan mekanis.
Refraktori untuk colokan adalah bahan Al2O3 tinggi atau MgO yang dibakar, dirancang khusus untuk aplikasi ini, dan dipasang dari luar sendok oleh perangkat mekanis atau manual. Sistem biasanya memungkinkan pertukaran steker cepat dalam sendok panas. Steker dicabut dari servis setelah waktu penggunaan yang telah ditentukan sebelumnya atau ketika indikator keausan visual yang terpasang pada steker digunakan secara berlebihan. Karena keausan pada blok tempat duduk tahan api di sekitar steker, perbaikan panas di area sekitar steker mungkin diperlukan.
Kontrol aliran baja dari STL ke cetakan CC dilakukan dengan sistem gerbang geser. Aliran baja cair oleh gerbang geser menggunakan pelat tahan api yang ditahan di bawah tekanan oleh pegas atau perangkat lain yang digerakkan untuk mengontrol aliran. Desain dan konstruksi sistem gerbang geser yang berbeda sangat bervariasi sesuai dengan persyaratan penuangan baja dari mesin CC. Misalnya, lokasi pegas dan metode pendinginan bervariasi antara berbagai sistem gerbang dan pergerakan pelat dapat dilakukan dengan mekanisme hidrolik atau lainnya.
Semua sistem pintu geser menyediakan cara yang cepat untuk menghilangkan tekanan dari pelat di antara panas untuk memungkinkan pemeriksaan refraktori dan untuk memungkinkan penggantian pelat atau nozzle bawah dengan cepat.
Konstruksi tahan api dari sistem gerbang tipikal mencakup refraktori di blok tempat duduk dan nosel atas di bagian bawah sendok, pelat tetap dan geser, serta sambungan nosel bawah untuk tabung atau selubung ke dalam tundish mesin CC.
Pelat geser dan pelat tetap adalah salah satu refraktori paling unik dan tahan lama yang digunakan dalam aplikasi pabrik baja. Pelat-pelat ini harus tahan terhadap goncangan termal yang parah dan erosi baja untuk jangka waktu yang lama. Komposisi pelat ini dapat bervariasi dari alumina sederhana hingga zirkonia dalam sistem oksida, hingga sistem oksida-karbon kompleks. Pelat yang tepat yang digunakan sangat bergantung pada komposisi baja yang akan dicor dan frekuensi penggantian pelat. Penggantian pelat tersebut dapat disertai setelah pemeriksaan pelat yang dilakukan setelah setiap pemanasan. Pelat dapat diganti hanya setelah satu kali pemanasan atau mungkin memiliki masa pakai hingga 20 kali pemanasan, tergantung pada mutu baja dan/atau kualitas tahan api yang digunakan.
Setelah setiap pemanasan, seluruh sistem gerbang harus dibersihkan dari sisa logam dan terak dengan oksigen lancing dan pengisi refraktori granular yang dipasang sebelum pemanasan berikutnya. Pengisi ini (sendok pasir) mencegah baja cair memasuki sistem gerbang sebelum gerbang dibuka pada waktu yang tepat di mesin CC. Pasir sendok dapat berupa silika, zirkon, atau kombinasi tahan api lainnya, yang memungkinkan aliran bebas baja cair dari pintu geser saat dibuka tanpa memerlukan pemeriksaan mekanis atau lancing.