Proses Tecnored untuk Pembuatan Besi
Proses Tecnored untuk Pembuatan Besi
Proses Tecnored dikembangkan oleh 'Tecnored Desenvolvimento Tecnológico S.A.' dari Brasil dan didasarkan pada tungku reduksi unggun bergerak bertekanan rendah yang mengurangi pelet ikatan dingin, bantalan karbon, fluks sendiri, dan reduksi sendiri. Reduksi dilakukan dalam tungku poros tinggi pendek dengan desain berbeda pada temperatur reduksi tipikal. Proses tersebut menghasilkan logam panas (besi cair).
Teknologi Tecnored telah dirancang dan dikembangkan untuk menjadi proses pembuatan besi 'tanpa kokas', sehingga menghindari investasi dan pengoperasian oven kokas yang berbahaya bagi lingkungan selain secara signifikan mengurangi emisi gas rumah kaca dalam produksi logam panas.
Proses tecnored menggunakan kombinasi ledakan panas dan dingin dan tidak memerlukan oksigen tambahan. Ini menghilangkan kebutuhan akan pabrik kokas, pabrik sinter, dan pabrik oksigen tonase. Oleh karena itu, proses ini memiliki biaya operasi dan investasi yang jauh lebih rendah dibandingkan dengan rute pembuatan besi tradisional.
Proses tecnored fleksibel sehubungan dengan jenis bantalan besi dan bahan baku bantalan karbon yang dapat diproses. Kemampuan proses untuk melebur pelet atau briket, atau bahkan campuran keduanya, menyediakan cara untuk menggunakan berbagai bahan pakan alternatif. Prosesnya menghasilkan produktivitas yang baik dan efisiensi energi yang tinggi.
Proses tecnored juga diklaim cocok untuk memproduksi paduan ferro seperti ferro mangan.
Sejarah perkembangan
Sejarah perkembangan proses Tecnored terdiri dari fase yang berbeda dengan tujuan yang berbeda, pengujian berbagai bahan baku dan menggunakan ukuran dan konsep reaktor yang berbeda.
Selama kurun waktu 1979 hingga 1985 telah dilakukan kegiatan pengembangan mengenai penggunaan pyrite cinder yang mengandung self-reducing pellet sebagai beban logam pada tungku cungkup. Konsep pengurangan diri ini diadaptasi untuk mengembangkan proses baru. Pada tahun 1985 konsep tungku Tecnored telah dirumuskan termasuk pengumpan samping untuk bahan bakar padat dan pembakaran pasca di poros atas sebagai dua fitur utama dari teknologi. Selama tahun 1985, perakitan prototipe pertama tungku Tecnored dimulai di kota Joinvile yang terletak di negara bagian Santa Catarina, Brasil, untuk mengalami proses reduksi pada skala pabrik percontohan.
Selama periode 1985 hingga 1990, pengembangan proses berlangsung di tungku melingkar kecil berdiameter 400 mm, yang bertujuan untuk menunjukkan kelayakan konsep tungku baru selain untuk menetapkan parameter operasional dan geometris pertama. Selama fase pengembangan ini, pengumpanan dan penyadapan terus menerus yang baik (hingga 24 jam pemanasan terus menerus) dicapai yang menguatkan kecukupan konsep tungku Tecnored. Meskipun hasil yang dicapai dalam fase ini ekspresif, lebih dari metode pengembangan empiris, pemahaman mendasar yang lebih baik tentang proses diperlukan untuk memutuskan langkah pengembangan selanjutnya. Oleh karena itu, untuk desain dan konstruksi tungku percontohan yang lebih besar, pemodelan matematis yang sangat komprehensif tentang perilaku pelet pereduksi diri di tungku Tecnored telah dibuat.
Selama periode 1990 hingga 1993, pengembangan proses dilakukan dalam tungku melingkar yang lebih besar dengan diameter 600 mm. Hal ini dilakukan dengan tujuan untuk mencapai kampanye yang lebih lama, stabilitas operasional yang lebih tinggi, penyesuaian geometris dan operasional berdasarkan pemodelan matematis dan hasil pasca pembakaran yang lebih tinggi. Hasil yang dicapai selama fase ini adalah periode yang lebih lama dari stabilitas operasional yang lancar, kontrol dan pemeliharaan laju pengisian muatan, kontrol prosedur penyadapan terak dan logam panas, perbaikan pada dinamika fluida proses, dan penilaian dekat dari termal dan gas. profil di dalam tungku. Namun, tungku 600 mm mendekati batasnya untuk membantu pengembangan eksperimental teknologi dan oleh karena itu, setelah 3 tahun eksperimen, diputuskan untuk melanjutkan proses pengembangan di tungku percontohan baru yang lebih besar dengan diameter 1000 mm. Juga, pemodelan matematis dari proses pada periode ini menunjukkan bahwa untuk mencapai produksi yang lebih tinggi di samping tungku yang lebih besar, untuk menjaga raceway yang sesuai dan rekayasa api pada tungku Tecnored, geometri tungku harus diubah dari lingkaran. ke penampang persegi panjang.
Selama kurun waktu 1994 hingga 1995, pengembangan proses dilakukan pada tungku sirkular berdiameter 1000 mm. Hal ini dilakukan dengan tujuan untuk mengkonfirmasi parameter geometris dan operasional dalam tungku besar, selain untuk memeriksa batasan pertumbuhan tungku melingkar seperti yang ditunjukkan oleh pemodelan. Hasil yang dicapai selama pengoperasian tungku percontohan melingkar yang lebih besar menegaskan stabilitas operasional yang tinggi, kontrol tungku yang baik, durasi kampanye yang panjang, logam panas yang baik dan kualitas terak, dll. Juga, tungku percontohan berdiameter 1000 mm mengkonfirmasi prediksi pemodelan matematis bahwa tungku ukuran tidak dapat bertambah saat berbentuk lingkaran, membuka jalan bagi penciptaan konsep modular, yaitu memiliki tungku persegi panjang akan memungkinkan untuk meningkatkan produksi dengan menambahkan modul tambahan sambil mempertahankan penampang tetap. Hal ini menyebabkan keputusan untuk membangun potongan modular ukuran penuh dari tungku Tecnored dengan penampang persegi panjang.
Selama tahun 1996, pengujian konsep tungku baru dilakukan dengan menggunakan tungku percontohan kecil dengan satu tuyere saja. Hasil operasional yang dicapai menguatkan kecukupan konsep baru untuk pembuatan besi berdasarkan penggunaan self-reducing aglomerates. Berdasarkan hasil, potongan modular tungku percontohan Tecnored ukuran penuh telah dibangun.
Selama periode 1997 hingga 2000, prosedur pengurangan risiko dan desain bantuan pengujian tungku industri menggunakan irisan ukuran penuh telah dilakukan. Berdasarkan desain persegi panjang baru ini, modularitas tungku dapat dimanfaatkan dengan keberhasilan konstruksi dan pengujian tungku seluler awal. Dalam fase ini, pengujian terus-menerus dalam kampanye selama seminggu dalam irisan modular skala penuh telah dilakukan di lebih dari 100 pengujian terpisah, menambahkan hingga 1000 jam operasi. Selama pengembangan lebih dari 100 uji coba ini, lebih dari 1000 ton logam panas berkualitas tinggi diproduksi. Kualitas logam panas mirip dengan logam panas dari tanur tinggi. Keberhasilan penyelesaian tahap pabrik percontohan pengembangan proses Tecnored telah membuka jalan bagi pembangunan fasilitas skala industri untuk pabrik unit besi perawan, serta pabrik untuk daur ulang limbah pertambangan dan pabrik baja.
Selama operasi pabrik percontohan tungku Tecnored terbukti menjadi metode baru dan sangat bermanfaat untuk mengembangkan proses metalurgi ini dan parameter desain tungku dasar yang diperlukan untuk fasilitas operasi pertama ditentukan selama pengujian pabrik percontohan. Pengujian membantu dalam pengembangan proyek pembangunan pabrik percontohan industri (IDP), dengan kapasitas 75.000 ton per tahun telah dilakukan.
IDP terletak di kotamadya Pindamonhangaba di negara bagian São Paulo, Brasil. Selama 2008-2009, pembangunan IDP telah selesai dan izin operasi telah diperoleh. Pada tahun 2011, modifikasi untuk perangkat periferal dan aksesori tungku Tecnored selesai, proyek pengembangan bahan baku dimulai, dan dimulainya tungku Tecnored. Selama tahun 2012, operasi tungku Tecnored dimulai serta studi kelayakan untuk pembangunan pabrik yang lebih besar dengan kapasitas 300.000 ton per tahun di Carajas, di negara bagian Para, Brasil dimulai.
Proses Tecnored
Proses Tecnored adalah pendekatan baru untuk teknologi pembuatan besi yang menggunakan aglomerat pereduksi diri terikat dingin (pelet atau briket), yang dihasilkan dari butiran halus bijih besi atau residu bantalan besi, ditambah butiran halus kokas hewan peliharaan, batubara, arang, atau residu bantalan karbon. Bahan-bahan ini, dicampur dengan bahan fluks dan pengikat, diaglomerasi dan dikeringkan pada pengering, menghasilkan briket/pelet yang memiliki kekuatan yang cukup untuk tuntutan fisik dan metalurgi dari proses Tecnored. Aglomerat yang dihasilkan dilebur dalam tungku poros dengan efisiensi tinggi dan desain unik yang dikenal sebagai tungku Tecnored. Tungku tecnored, karena ketinggian tumpukannya yang rendah menggunakan bahan bakar padat berbiaya rendah, seperti kokas minyak bumi hijau, batu bara, atau semi kokas.
Fitur utama dari proses ini adalah menggunakan bahan yang relatif murah seperti bijih besi halus atau sisa oksida dan batu bara/arang halus (atau kokas minyak bumi) sebagai reduktor/bahan bakar. Tungku Tecnored adalah inti dari prosesnya.
Lembar alir skematis dari proses ada di Gambar 1.
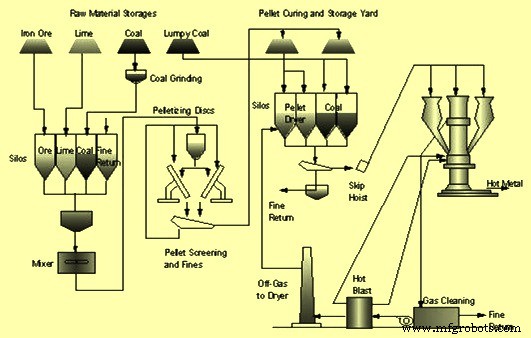
Gbr 1 Skema flow sheet proses Tecnored
Prosesnya terdiri dari pelletizing fine ore ore dengan ukuran kurang dari 140 mesh, fine coke dengan ukuran kurang dari 200 mesh, dan flux seperti kapur terhidrasi dengan ukuran kurang dari 140 mesh dengan menggunakan semen sebagai pengikat. Pelet dikeringkan dan dikeringkan pada 200 derajat C sebelum diumpankan ke bagian atas tungku Tecnored. Tekanan internal tungku dipertahankan dalam kisaran sekitar 0,25 kg/cm2 sampai 0,37 kg/cm2. Total waktu tinggal muatan dalam tungku adalah sekitar 30 menit sampai 40 menit. Bahan bakar padat dengan ukuran mulai dari 40 mm hingga 80 mm diumpankan ke dalam tungku di bawah area pelet panas menggunakan pengumpan samping. Udara panas ledakan di sekitar 1150 derajat C dihembuskan melalui tuyeres yang terletak di sisi tungku untuk menyediakan udara pembakaran untuk kokas. Sejumlah kecil gas tungku dibiarkan mengalir melalui pengumpan samping untuk digunakan untuk pengeringan dan pemanasan awal bahan bakar padat. Udara dingin ledakan dihembuskan pada titik yang lebih tinggi untuk mendorong pembakaran pasca CO di poros atas. Dalam hal penggunaan bahan bakar padat dengan belerang tinggi memerlukan sistem pembersihan yang rumit untuk gas tungku untuk memenuhi peraturan lingkungan. Logam panas yang dihasilkan disadap ke sendok di mobil sendok, yang dapat memiringkan sendok untuk menghilangkan kerak. Setrika cair didesulfurisasi dalam sendok, dan terak dimasukkan ke dalam panci terak.
Furnace memiliki tiga zona yaitu (i) zona poros atas, (ii) zona leleh, dan (ii) zona poros bawah.
Di zona poros atas tungku, bahan bakar padat diisi di poros atas. Reaksi Boudouard (CO2 + C =2 CO) pada bahan bakar dicegah yang menghemat energi. Pasca pembakaran di zona tungku ini membakar CO yang menyediakan energi untuk pemanasan awal dan pengurangan muatan. Juga di dalam pelet, reaksi berikut berlangsung dengan kecepatan yang sangat cepat.
FexOy + yCO =xFe + yCO2
yCO2 + yC =2yCO
Di zona leleh, reoksidasi dicegah karena atmosfer pereduksi dalam muatan. Peleburan muatan terjadi di bawah atmosfer pereduksi.
Di zona poros bawah tungku, bahan bakar padat kelas rendah diisi. Bahan bakar padat tingkat rendah juga dapat mencakup plastik bekas dan ban bekas karena ketinggian tumpukan tungku yang rendah. Di zona ini sisa reduksi oksida besi sisa dan reaksi slagging bahan gangue dan abu bahan bakar berlangsung dalam keadaan cair. Juga, terjadi pemanasan super dari tetesan logam dan terak. Tetesan logam dan terak yang sangat panas ini tenggelam karena gravitasi ke perapian dan menumpuk di sana.
Proses ini menggunakan dua input unit karbon yang berbeda yaitu (i) reduktor, dan (ii) bahan bakar padat, mengoptimalkan fleksibilitas proses. Zat pereduksi biasanya butiran halus batu bara tetapi butiran halus dari semua jenis bahan yang diperkaya karbon dapat digunakan. Itu ditambahkan dalam campuran dari mana aglomerat yang mereduksi sendiri (pelet atau briket) diproduksi. Jumlah butiran halus batubara yang dibutuhkan ditentukan oleh rasio C/F (karbon terhadap butiran halus), biasanya cukup untuk mencapai pengurangan penuh muatan, hanya dengan menyediakan panas yang dibutuhkan untuk proses tersebut. Dalam reduksi sendiri, CO eksternal tidak memainkan peran penting dalam proses reduksi.
Bahan bakar padat kental diisi melalui pengumpan samping (untuk menghindari reaksi Boudouard kehilangan larutan endotermik di poros atas) dan bertanggung jawab untuk membentuk lapisan arang dan menyediakan sebagian besar energi yang dibutuhkan oleh proses. Energi ini dibentuk oleh ledakan primer (C + O2 =CO2) dan oleh ledakan sekunder, di mana CO hulu, yang dihasilkan oleh gasifikasi bahan bakar padat di perapian, dibakar (CO + O2 =CO2). Gambar 2 menunjukkan penampang skema tungku Tecnored, di mana dua fitur penting ini disorot.
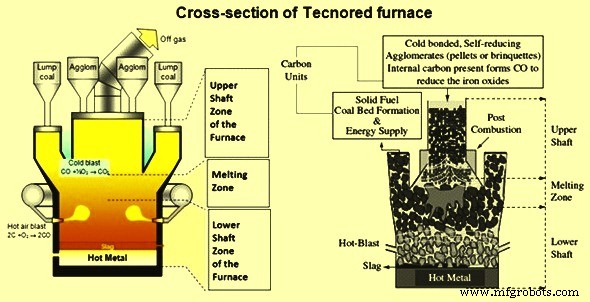
Gbr 2 Penampang melintang tungku Tecnored
Karena fungsi akhir dari dua unit karbon yang digunakan dalam proses Tecnored berbeda, ada spesifikasi yang berbeda dari kedua unit karbon ini, tidak hanya dalam hal komposisi kimia, tetapi juga dalam hal rentang ukuran. Porsi bahan bakar padat membutuhkan material yang kental, biasanya berukuran 40 mm hingga 80 mm yang mampu menangani kebutuhan fisik dan termal yang diperlukan dari bahan bakar padat dalam proses Tecnored.
Bahan bakar kental yang digunakan dalam tungku Tecnored diperlukan untuk menciptakan permeabilitas di tungku tungku untuk aliran fase cair dan gas yang merata. Oleh karena itu, bahan bakar padat yang dipilih untuk digunakan dalam proses, pada titik akhir pengumpan samping, setelah proses charification (Gbr 3), harus menyediakan arang yang kental, dengan kerangka yang cukup kuat untuk menopang beban muatan. , selain reaktivitas yang baik untuk mempromosikan RAFT (suhu api adiabatik raceway) dan geometri nyala yang sesuai. Itu juga harus mampu menciptakan rasio CO / CO2 yang diinginkan di bagian atas char bed.
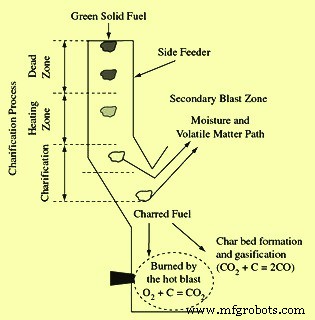
Gbr 3 Proses charifikasi bahan bakar padat di tungku Tecnored
Namun, agak penting untuk menyebutkan bahwa beban mekanis yang dikenakan pada unggun arang sangat kecil, karena produktivitas volumetrik tungku yang tinggi, menghasilkan tungku dengan tinggi poros yang lebih rendah. Fitur proses ini adalah salah satu alasan utama yang menjelaskan kemampuan tungku untuk berfungsi tanpa menggunakan kokas dan memungkinkan penggunaan bahan bakar padat bermutu rendah.
Konsumsi spesifik bahan bakar per ton logam panas adalah 250 kg batubara dan 310 kg bahan bakar padat untuk menghasilkan logam panas dengan 3% hingga 4,5% karbon dan 0,2% hingga 1,0% Si. Suhu logam panas biasanya berkisar antara 1380 derajat C hingga 1430 derajat C.