Proses Midrex untuk Reduksi Langsung Bijih Besi
Proses Midrex untuk Reduksi Langsung Bijih Besi
Midrex adalah proses pembuatan besi, dikembangkan untuk produksi besi tereduksi langsung (DRI). Ini adalah proses tungku poros berbasis gas adalah proses reduksi keadaan padat yang mereduksi pelet bijih besi atau bijih bongkahan menjadi DRI tanpa peleburannya menggunakan gas pereduksi yang umumnya terbentuk dari gas alam. Prinsip proses reduksi menggunakan gas pereduksi ditunjukkan pada Gambar 1.
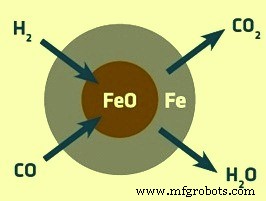
Gbr 1 Prinsip proses reduksi menggunakan gas pereduksi
Sejarah proses Midrex kembali ke 1966 ketika Donald Beggs dari Surface Combustion Corporation menyusun ide untuk proses reduksi langsung Midrex. Proses aslinya dikembangkan oleh Midland-Ross Co., yang kemudian menjadi Midrex Technologies, Inc. Sekarang merupakan anak perusahaan yang dimiliki sepenuhnya oleh Kobe Steel. Pabrik percontohan dibangun di Toledo, Ohio pada tahun 1967. Pabrik komersial pertama, dengan kapasitas produksi 150.000 ton per tahun, dibangun di Portland, Oregon, pada tahun 1969. Kejeniusan proses Midrex adalah kesederhanaannya. Konsep Donald Beggs yang menggabungkan reformasi gas alam stoikiometri dengan reduksi langsung bijih besi tungku poros merupakan inovasi terobosan yang telah teruji oleh waktu.
Sejak 1969, produksi DRI melalui proses Midrex telah menembus 500 juta ton. Produksi dari banyak pabrik Midrex melebihi kapasitas desainnya. Setiap tahun sejak 1987, produksi DRI melalui proses Midrex lebih dari 60% dari total produksi DRI global.
Prosesnya belum matang pada tahun 1978, ketika Kobe Steel memulai pembangunan pabrik dengan kapasitas produksi 400.000 ton/tahun di Negara Qatar. Kobe Steel secara signifikan memodifikasi desain, mengeksploitasi teknologi perusahaan yang dikembangkan melalui operasi tanur tinggi, dan menstabilkan proses baru saat itu. Di sisi lain, Midrex Technologies juga melakukan berbagai penyempurnaan terhadap pabrik yang mereka bangun di berbagai negara. Semua ini terintegrasi pada awal 1980-an, membuat prosesnya hampir selesai.
Kapasitas produksi maksimum unit Midrex pada tahun 1984 adalah 600.000 ton per tahun. Tungku poros Midrex dengan diameter poros 5,0 m, 5,5 m, dan 6,5 m memiliki kapasitas produksi tahunan masing-masing 800.000 ton, 1 juta ton dan 1,6 juta ton DRI merupakan tahap pengembangan yang berbeda. Kemudian dengan perbaikan yang dilakukan, kapasitas meningkat ke level 1,8 juta ton per tahun pada tahun 2007, yang sebanding dengan blast furnace ukuran yang cukup baik. Modul Super Megamod berkapasitas 2,2 juta ton DRI per tahun memiliki shaft furnace dengan diameter internal 7,5 m dan mampu memproduksi lebih dari 275 ton per jam. Saat ini modul Super Megamod bahkan dapat memiliki kapasitas 2,7 juta ton per tahun.
Selain itu, proses telah ditingkatkan secara signifikan sejak commissioning pabrik pertama pada tahun 1969. Keuntungan produktivitas dari proses Midrex adalah karena (i) tungku poros kapasitas yang lebih besar karena peningkatan skala peralatan proses, (ii) terus-menerus penyempurnaan proses yang mencakup peningkatan perolehan panas, (iii) peningkatan katalis, (iv) pembriketan panas, dan (v) penggabungan teknologi baru seperti double bustle, in-situ reforming, pelapisan oksida, refraktori dinding tipis, injeksi oksigen, dll. .
Deskripsi proses
Beban besi untuk tungku poros dapat berupa pelet bijih besi atau bijih berukuran lump atau kombinasi keduanya. Namun, beban bijih biasanya terdiri dari campuran pelet dan bijih lump. Bahan beban bijih diangkut dan dimuat ke tempat sampah yang ditunjuk yang diperuntukkan bagi pelet atau bijih lump. Kapasitas tempat sampah tergantung pada kapasitas pabrik. Tempat sampah yang diperuntukkan untuk lump ore dilengkapi dengan 'tangga' khusus untuk mencegah pembentukan halus karena ketinggian jatuh. Rasio pencampuran normal pelet untuk bijih benjolan adalah 80:20. Pengumpan konstan di bawah nampan mengontrol rasio pencampuran. Campuran beban bijih diumpankan ke tungku poros melalui saringan bijih yang dimaksudkan untuk menghilangkan material yang terlalu besar (+45 mm) dan yang berukuran terlalu kecil (-6 mm).
Proses Midrex mudah dioperasikan dan melibatkan tiga unit operasi utama yaitu (i) reduksi bijih besi, (ii) pemanasan awal gas, dan (iii) reformasi gas alam. Inti dari proses Midrex adalah tungku porosnya. Ini adalah silinder, bejana berlapis tahan api dan merupakan komponen kunci dari proses reduksi langsung. Ini fleksibel serta reaktor serbaguna. Bisa menggunakan gas alam, syngas dari batubara, gas coke oven, atau gas buang dari proses Corex sebagai gas pereduksi. Ini beroperasi pada sedikit di atas tekanan atmosfer dan pada suhu operasi sekitar 950 derajat C. Ketersediaan tungku poros memastikan pabrik Midrex dioperasikan selama lebih dari 8000 jam per tahun.
Tungku poros dirancang berdasarkan prinsip aliran balik gas dan padatan untuk memaksimalkan efisiensi reduksi. Tungku memastikan aliran padatan yang seragam dengan mendistribusikan beban tungku secara efektif dan menghindari jembatan material dan penyaluran gas. Kontrol dilakukan sehubungan dengan aliran gas antara berbagai zona tungku. Tungku poros juga mencegah gas pereduksi bersentuhan dengan udara. Ini melarang aliran gas dari fluidisasi beban tungku. Profil suhu yang seragam dipertahankan di seluruh penampang tungku. Penghentian aliran beban tungku dihindari. Desain tungku menghilangkan kebutuhan akan kerucut pelepasan berpendingin air.
Saat ini tungku poros Midrex standar memiliki fitur seperti (i) dinding refraktori tipis di zona reduksi tungku untuk mengurangi penurunan tekanan beban dan untuk meningkatkan volume tungku, (ii) port hiruk pikuk ganda untuk injeksi gas pereduksi karena ini memungkinkan gas untuk menembus lebih baik ke pusat beban di zona reduksi dan dengan demikian meningkatkan metalisasi di tengah tungku poros, dan (ii) sisipan bantuan aliran dengan bentuk yang dimodifikasi untuk menyamakan kecepatan penurunan beban antara tengah dan sisi dinding zona reduksi tungku poros.
Proses tersebut memiliki kemampuan untuk menghasilkan DRI dingin (CDRI), DRI panas (HDRI) dan/atau besi briket panas (HBI). Lembar alur proses adalah en givat Gambar 2.
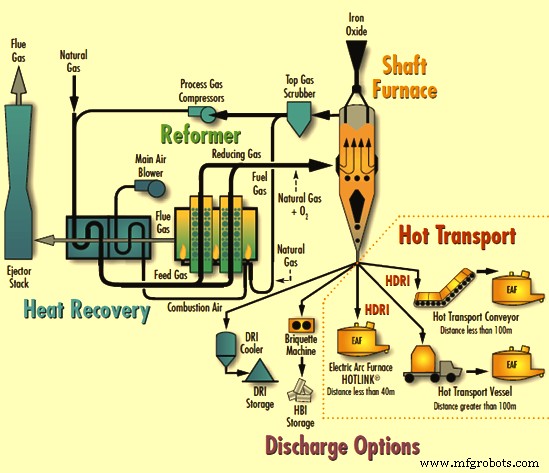
Gambar 2 Lembar alur proses Midrex
Tungku poros adalah reaktor unggun yang dikemas dengan aliran arus berlawanan dari reaktan. Reaktor jenis ini umumnya merupakan reaktor yang sangat efisien untuk pengolahan bahan padat. Ada tiga alasan utama untuk efisiensi ini yaitu (i) karena reaktor terisi penuh dengan beban bijih, produktivitas volumetrik biasanya sangat tinggi, (ii) unggun yang bergerak memastikan bahwa setiap bagian dari beban bijih mengalami profil suhu yang sama. , komposisi gas, dan waktu tinggal seperti setiap bagian lainnya, dan (iii) aliran arus berlawanan memberikan beban bijih kekuatan pendorong yang sangat besar untuk reaksi dan waktu reaksi yang cepat.
Pengoperasian tungku poros sederhana dan mudah. Bahan beban besi dimasukkan di bagian atas tungku melalui hopper proporsional dan turun ke bawah oleh aliran gravitasi. Dalam tungku itu dihubungi oleh gas pereduksi suhu tinggi yang mengalir ke atas, dipanaskan dan diubah menjadi DRI. Gas pereduksi, yang terutama hidrogen (H2) dan karbon mono oksida (CO), bereaksi dengan oksida besi (Fe2O3) untuk mereduksi yaitu untuk menghilangkan kandungan oksigen (O2) dan mengkarburasi material sebelum dibuang. Untuk produksi CDRI, besi tereduksi didinginkan dan dikarburasi oleh gas pendingin aliran balik di bagian bawah tungku poros. DRI juga dapat dibuang panas baik sebagai HDRI atau diumpankan ke mesin briket untuk menghasilkan HBI. Oleh karena itu, produk tungku dapat dibuang sebagai CDRI, HDRI, HBI atau kombinasi apa pun secara bersamaan.
Reaksi yang terjadi di tungku poros diberikan di bawah ini.
Pengurangan oleh CO
Fe2O3 + 3CO =2Fe + 3CO2 (Reaksi keseluruhan)
3Fe2O3 + CO =2Fe3O4 + CO2 (Reaksi Eksoterm)
Fe3O4 + CO =3FeO + CO2 (Reaksi endotermik)
FeO + CO =Fe + CO2 (Reaksi eksotermik)
Pengurangan H2
Fe2O3 + 3H2 =2 Fe + 3H2O (Reaksi keseluruhan)
3Fe2O3 + H2 =2Fe3O4 + H2O (Reaksi Eksoterm)
Fe3O4 + H2 =3FeO + H2O (Reaksi endotermik)
FeO + H2 =Fe + H2O (Reaksi endoterm)
Reaksi karburasi
3Fe + CH4 =Fe3C + 2H2 (Reaksi endoterm)
3Fe + 2CO =Fe3C + CO2 (Reaksi eksotermik)
3Fe + CO + H2 =Fe3C + H2O (Reaksi Eksoterm)
Gas buang (gas atas) yang dipancarkan dari bagian atas tungku poros dibersihkan dan didinginkan oleh scrubber basah (scrubber gas atas) dan disirkulasikan kembali untuk digunakan kembali. Gas atas yang mengandung CO2 dan H2O diberi tekanan oleh kompresor, dicampur dengan gas alam, dipanaskan dan dimasukkan ke dalam tungku reformer.
Gas pereduksi yang terutama terdiri dari H2 dan CO dapat dihasilkan dari berbagai sumber energi. Gas alam terutama mengandung metana yang dapat bervariasi dari 83% hingga 96%. Konstituen lain dari gas alam adalah hidrokarbon yang lebih tinggi. Gas alam dapat direformasi dalam reformer yang merupakan tungku berlapis tahan api yang berisi tabung baja paduan. Gas umpan ke reformer adalah gas alam segar yang dicampur dengan off gas untuk tungku poros yang sedang didaur ulang. Campuran gas campuran ini dipanaskan dan dilewatkan melalui tabung yang diisi katalis. Gas yang direformasi dihasilkan karena reaksi katalitik yang terjadi di dalam tabung yang diisi katalis. Gas yang baru direformasi yang mengandung sekitar 90% hingga 92% H2 + CO (dalam basis kering) kemudian diumpankan panas langsung ke tungku reduksi poros sebagai gas pereduksi.
Proses Midrex menggunakan katalis padat untuk reaksi fase gas. Alumina atau magnesia adalah bahan pembawa yang memberikan katalis bentuk dan kekuatannya. Bahan aktif katalis, yang meningkatkan kecepatan reaksi, biasanya adalah nikel. Cobalt juga telah digunakan dalam beberapa kasus. Sulfur dan halogen adalah racun katalis reformasi yang paling umum.
Reaksi yang berlangsung dalam reformer diberikan pada Tab 1.
Tab 1 Reaksi reformis |
No Sl. | Jenis reaksi | Reaksi |
1 | Pembaruan uap | CnH(2n+2) + n H2O =(2n+1)H2 + nCO |
2 | reformasi CO2 | CnH(2n+2) + n CO2 =(n+1)H2 + 2nCO |
3 | Reaksi perpindahan gas air | CO + H2O =CO2 + H2 |
4 | Reaksi pengendapan karbon Boudouard | 2CO =CO2 + C |
5 | Meminta reaksi pengendapan karbon | CO + H2 =H2O + C |
6 | Retak hidrokarbon berat | CnH(2n+2) =(n+1)H2 + nC |
Desain reformer dan katalis harus sedemikian rupa sehingga mendorong reaksi reformasi tanpa membiarkan reaksi deposisi karbon berlangsung. Umumnya steam reformer digunakan untuk mereformasi gas alam. Untuk steam reformer, gas alam harus didesulfurisasi. Proses midrex menggunakan stoikiometri reformer. Dalam pembaharu ini rasio stoikiometri merupakan parameter yang penting. Rasio stoikiometrik hanyalah rasio molar atau volume oksidan, CO2 dan H2O terhadap hidrokarbon yang akan menghasilkan konsumsi hidrokarbon tanpa oksidan yang tersisa jika reaksi berlanjut hingga selesai. Versi lain dari rasio stoikiometri adalah rasio oksidan terhadap karbon dalam hidrokarbon dalam gas umpan reformer. Dalam steam reformer itu adalah rasio uap terhadap karbon. Dalam pembaharu Midrex, rasio stoikiometri adalah rasio aktual oksidan terhadap hidrokarbon dibagi dengan rasio stoikiometri oksidan terhadap hidrokarbon. Dengan demikian merupakan ukuran kelebihan oksidan dalam gas umpan reformer. Dengan demikian lebih tepat disebut rasio oksidan terhadap karbon.
Karakteristik reformer Midrex meliputi (i) tidak diperlukan sistem steam untuk reforming, (ii) tidak diperlukan sistem penghilangan CO2 untuk operasi, (iii) gas pereduksi panas dapat langsung digunakan di tungku poros tanpa pendinginan dan pemanasan ulang, ( iv) tidak memerlukan O2 untuk reformasi, (v) dengan menggunakan CO2 untuk reformasi, lebih sedikit gas alam yang dibutuhkan , dan (vi) memungkinkan proses Midrex menjadi sistem loop tertutup sederhana yang meminimalkan konsumsi energi dan jumlah bagian yang bergerak di dalam pabrik.
Tungku reformer Midrex dilengkapi dengan beberapa ratus tabung reformer yang diisi dengan katalis nikel. Melewati tabung-tabung ini, campuran gas atas dan gas alam direformasi untuk menghasilkan gas reduktor yang terdiri dari CO dan H2. Reaksi yang terjadi pada tabung reformer Midrex adalah sebagai berikut.
CH4 + CO2 =2CO + 2H2
CH4 + H2O =CO + 3H2
2CH4 + O2 =2CO + 4H2
CO + H2O =CO2 + H2
CH4 =C(S) + 2H2
Reformer Midrex berbeda dari steam reformer dalam banyak hal. Ini (i) mereformasi karbon dioksida dan uap air, (ii) beroperasi pada rasio oksidan/karbon (Midrex stoikiometri) sekitar 1,4, (iii) beroperasi dengan sulfur yang ada dalam gas umpan reformer, (iv) beroperasi pada tekanan rendah , dan (v) membutuhkan desain katalis yang unik.
Efisiensi termal reformer Midrex sangat ditingkatkan oleh sistem pemulihan panas. Panas sensibel diperoleh kembali dari gas buang reformer untuk memanaskan campuran gas umpan dan udara pembakaran burner. Selain itu, tergantung pada keekonomiannya, bahan bakar gas juga dapat dipanaskan terlebih dahulu.
Selanjutnya untuk pembangkitan gas pereduksi, batubara jenis apa pun atau kandungan abu dapat digasifikasi. Gas oven kokas dapat direformasi menggunakan 'Sistem Reaktor Termal' Midrex. Syngas ekspor dari unit Corex juga menghasilkan gas pereduksi berkualitas tinggi yang dapat digunakan dalam tungku poros Midrex yang terkait erat untuk menghasilkan DRI.
Ada empat opsi pelepasan (Gbr 1) yang tersedia untuk proses Midrex. Ini adalah DRI dingin, HBI, DRI panas melalui hot link (HOTLINK), dan DRI panas melalui konveyor atau kapal pengangkut panas.
Proses hot link terutama menggunakan transportasi gravitasi dan menggunakan teknologi yang sama seperti yang digunakan untuk umpan gravitasi HDRI untuk produksi HBI. HDRI dari kiln poros DRI dibuang ke tempat penampung gelombang di luar dan di atas bengkel peleburan baja. Modul Midrex dengan tautan panas dilengkapi untuk menangani segala kondisi yang tidak menyenangkan melalui nampan lonjakan. Sistem ini memasok HDRI ke tanur busur listrik (EAF) sesuai permintaan EAF. Proses HOTLINK digunakan bila jarak antara kiln poros DRI dan EAF kurang dari 40 meter.
Sistem konveyor transportasi panas digunakan di mana toko peleburan baja tidak berdekatan dengan tungku poros DRI (lebih dari 40 m tetapi kurang dari 100 m), konveyor mekanis berinsulasi digunakan untuk pengangkutan HDRI ke toko peleburan baja. Dalam hal ini, DRI dikeluarkan dari tungku poros DRI ke konveyor tertutup dan terisolasi, yang dirancang untuk meminimalkan kehilangan suhu dan mencegah deoksidasi. Konveyor memiliki wadah khusus yang bentuknya mirip dengan ember. Kap tertutup konveyor berisi sistem inerting. Konveyor menyediakan pengoperasian yang andal dengan biaya yang wajar.
Pengangkutan dengan kapal pengangkut panas digunakan ketika jarak antara kiln poros DRI dan EAF lebih dari 100 meter atau satu tungku poros DRI untuk memasok dua toko peleburan baja atau lebih. Pengangkutan HDRI dilakukan dengan menggunakan kapal berinsulasi, biasanya berkapasitas 60 ton hingga 90 ton. Dari tanur vertikal DRI, bejana diisi melalui pipa dengan segel kedap udara. Setelah satu bejana diisi, pipa ditutup dan bejana lain mulai diisi, bejana yang diisi diangkut ke bengkel peleburan baja baik di atas rel maupun di truk.
Peningkatan proses
Sejumlah besar peningkatan proses telah dilakukan sejak commissioning pabrik pertama pada tahun 1969. Praktik awal yang diikuti di awal adalah menggunakan umpan pelet 100% dan suhu gas pereduksi rendah (sekitar 780 derajat C) karena kecenderungan sintering dari bahan beban pelet. Pada pertengahan 1970-an, bijih lump pertama kali digunakan dan praktik ini diadopsi secara luas pada 1980-an. Penggunaan bijih lump telah memberikan manfaat tambahan untuk mencegah sintering beban tungku poros. Hal ini mengakibatkan peningkatan suhu gas pereduksi dari 780 derajat C menjadi 850 derajat C. Hal ini menghasilkan peningkatan sekitar 13% dalam produktivitas sistem.
Pengembangan lebih lanjut dalam praktik operasi terjadi pada pertengahan 1990-an yang terdiri dari pengenalan pelapisan bahan umpan oksida besi di pabrik dengan CaO atau CaO/MgO. Hal ini mengakibatkan peningkatan lebih lanjut dari suhu gas pereduksi (sedikit lebih dari 900 derajat C). Dengan ini, produktivitas proses meningkat 11% lagi. Semua perkembangan hingga pertengahan 1990-an telah mengakibatkan peningkatan suhu beban sekitar 40 derajat C.
Perkembangan hingga pertengahan tahun 1990-an mengarah pada peningkatan suhu gas pereduksi tanpa menyentuh kualitas suhu gas pereduksi. Upaya pengembangan lebih lanjut mengarah pada peningkatan penurunan suhu gas dengan mengorbankan penurunan kualitas gas. Perkembangan akhir 1990-an ini menyebabkan peningkatan suhu gas pereduksi dengan mengorbankan kualitas gas pereduksi. Hal ini dicapai melalui oksigen (O2) pembakaran gas. Suhu gas pereduksi yang lebih tinggi bersama dengan hilangnya kualitas gas pereduksi memberikan keuntungan produksi yang jelas. Pengenalan injeksi O2 menghasilkan pembakaran sebagian dari gas pereduksi CO+H2 oleh O2 dan membantu pencapaian efek ini dengan sukses. Desain injeksi O2 akhir-akhir ini terdiri dari pengenalan O2 kemurnian tinggi ke dalam aliran gas pereduksi panas yang mengalir melalui pengaturan beberapa nosel. Praktik injeksi O2 telah menghasilkan peningkatan suhu gas pereduksi hingga lebih dari 1000 derajat C dan peningkatan lebih lanjut dalam suhu beban hingga 70 derajat C. Meskipun sebagian H2+CO dikonsumsi oleh pembakaran dengan O2, menaikkan suhu pengurangan gas meningkatkan produktivitas tungku poros sebesar 10% hingga 20%. Konsumsi oksigen yang umum untuk peningkatan ini berada dalam kisaran 12 N cum/ton hingga 15 N cum/ton. Peningkatan produktivitas secara keseluruhan atas produktivitas unit Midrex pertama tahun 1969 karena penggunaan bijih lump, lapisan oksida besi dan injeksi O2 adalah sekitar 37 %.
Injeksi O2, yang dijelaskan di atas, telah berkembang menjadi teknologi yang ditingkatkan, yang disebut OXY+, yang dimungkinkan oleh pengenalan teknik pembakaran parsial. OXY+ menggunakan ruang bakar selain reformer. Ruang bakar membakar sebagian bahan bakar gas dengan O2 untuk menghasilkan H2+CO, yang ditambahkan ke gas pereduksi yang dihasilkan oleh reformer. Sistem OXY+ menghasilkan gas pereduksi dengan mereaksikan O2 dan bahan bakar gas pada rasio stoikiometri sekitar 0,5. Burner untuk OXY+ dipasang di saluran gas pereduksi setelah reformer. Inti dari sistem ini adalah reaktor OXY+ dimana bahan bakar gas dan O2 dicampur dan dibakar dalam dua tahap. Dengan staging yang tepat, sistem Oxy+ memberikan (i) pembakaran yang stabil, (ii) menghilangkan pembentukan jelaga, (iii) konversi bahan bakar gas menjadi H2+CO, dan (iv) perlindungan material konstruksi dari suhu ekstrem. Penting untuk keberhasilan sistem Oxy+ adalah mekanisme kontrolnya. Ini secara akurat mengukur O2 dan bahan bakar gas ke setiap tahap reaktor. Kontrol yang ketat dari pencampuran pembakaran O2 dan bahan bakar gas membantu menjaga kualitas dan suhu gas yang konsisten. Ini berfungsi untuk meminimalkan kenaikan suhu gas yang masuk ke tungku poros dan memberikan peluang tambahan untuk meningkatkan produksi. Penerapan OXY+ menghasilkan potensi peningkatan sebesar 21% dalam produktivitas tungku poros.
Produktivitas optimal dicapai dengan memaksimalkan penurunan suhu beban dan kualitas gas pereduksi yang masuk ke tungku poros. Kedua faktor ini adalah kunci untuk mengoptimalkan produksi tungku poros dan peralatan pembangkit gas terkait. Dengan memanfaatkan kombinasi dari dua praktik operasi, injeksi oksigen dan sistem OXY+, serta dengan mempertahankan gas alam dalam aliran gas pereduksi, suhu beban tungku poros dan suhu gas pereduksi dapat dikontrol secara independen. Hal ini memungkinkan operator pabrik untuk memaksimalkan kinerja tungku poros dengan memaksimalkan pemanfaatan gas pereduksi di dalam tungku. Praktik ini menawarkan potensi peningkatan produksi sekitar 5%.
Desain hiruk pikuk ganda Midrex untuk mendistribusikan gas pereduksi ke tungku poros terdiri dari dua cincin port di sekitar keliling tungku poros. Kesibukan ganda memungkinkan distribusi gas pereduksi yang lebih baik jika dibandingkan dengan hiruk pikuk tunggal. Kesibukan ganda juga memungkinkan aliran gas pereduksi yang lebih tinggi ke tungku tanpa fluidisasi lokal DRI. Keunggulan ini membantu dalam meningkatkan produktivitas tungku poros.
Injeksi gas alam ke dalam zona transisi tungku telah diperkenalkan untuk mencapai tingkat karbon produk yang lebih tinggi dan juga tingkat produksi yang lebih tinggi. Zona transisi adalah bagian dari tungku yang berada di bawah zona reduksi dan di atas zona pendinginan. Saat DRI turun dari zona reduksi ke zona transisi, suhunya sangat panas. Pada titik ini, kelebihan panas harus dihilangkan sebelum DRI dikeluarkan dari tungku. Dengan menyuntikkan, gas alam di zona transisi, sebagian panas yang tersedia dimanfaatkan dalam perengkahan hidrokarbon. Perengkahan hidrokarbon ini menyimpan karbon dalam produk DRI dan melepaskan H2, yang mengalir ke atas dan menjadi reduktor memberikan pengurangan tambahan.
Pemanasan awal gas alam yang masuk ke zona transisi sedang dijajaki. Manfaat pemanasan awal gas alam adalah karbon produk yang lebih tinggi dan tingkat produksi yang lebih tinggi karena jumlah yang lebih besar dari gas alam transisi dapat ditambahkan. Saat ini, aliran gas alam zona transisi dibatasi oleh efek pendinginannya. Pemanasan awal gas alam dapat memastikan injeksi jumlah gas yang lebih tinggi tanpa pendinginan zona reduksi.
Parameter operasi dan konsumsi spesifik
Beban tipikal 1,0 juta ton per tahun Unit Midrex di Comsigua, Venezuela terdiri dari 80% pelet bijih besi dan 20% gumpalan bijih besi. Analisis tipikal bahan pakan untuk pabrik ini diberikan di Tab 2 dan analisis tipikal produk diberikan di Tab 3.
Tab 2 Analisis umum bahan pakan |
No.Sl. | Komponen | Satuan | Pelet bijih besi | Benjolan bijih besi |
1 | Total Fe | % | 65-68 | 65,2 |
2 | SiO2 (maks) | % | 3 | 3 |
3 | Al2O3 (maks) | % | 3 | 3 |
4 | Al2O3 + SiO2 (maks) | % | 5 | 5 |
5 | CaO + MgO | % | 0,35 | 0,01 |
7 | Belerang | % | 0,005 | 0,012 |
8 | Fosfor | % | 0,05 | 0,1 |
9 | LOI | % | | 3 |
10 | Ukuran nominal | mm | 6-18 | 10-35 |
11 | Dikurangi 6 mm | % | 3 | 5 |
12 | Kekuatan gelas | | | |
| + maksimal 6,73 mm | % | 95 | 90 |
| – 0,595 mm min | % | 4 | 7 |
13 | Kekuatan kompresi min | kg | 250 | |
Tab 3 Analisis umum DRI |
No.Sl. | Elemen | Satuan | HBI | CDRI | HDRI |
1 | Fe Metalik | % | 83 – 90 | 83 – 90 | 83 – 90 |
2 | Total Fe | % | 89 -94 | 89 – 94 | 89 – 94 |
3 | Metalisasi | % | 92 – 96 | 92-96 | 92-96 |
4 | P | % | 0,005 – 0,09 | 0,005 – 0,09 | 0,005 – 0,09 |
5 | S | % | 0,001-0,03 | 0,001-0,03 | 0,001-0,03 |
6 | C | % | 1,5 – 4,0 | 1,5 – 4,0 | 1,5 – 4,0 |
7 | Al2O3 + SiO2 | % | 2.8 – 6.0 | 2.8 – 6.0 | 2.8 – 6.0 |
8 | Kepadatan massal | t/Cum | 2,4 – 2,8 | 1,6 -1,9 | 1,6 – 1,9 |
9 | Kepadatan yang terlihat | g/cc | 5.0 – 5.5 | 3,4 – 3,6 | 3,4 -3,6 |
10 | Suhu produk | Deg C | 100 | 50 | 600 – 700 |
11 | Ukuran biasa | mm | 30 x 50 x 110 | 4-20 | 4-20 |
Parameter operasi khas dari proses Midrex diberikan di Tab 4
Tab 4 Parameter operasi umum |
No.Sl. | Komponen | Satuan | Nilai |
1 | Rasio campuran bijih pelet | Rasio | 80:20 |
2 | Produktivitas spesifik | ton/jam | 150 |
3 | Proses aliran gas | N cum/jam | 165.000 |
4 | Proses gas CO2 | % | 20.0-21.0 |
5 | Suhu kotak reformer | Deg C | 1.130 |
6 | Suhu gas yang berubah | Deg C | 930 |
7 | Gas reformasi CH4 | % | 1.1 |
8 | Reformasi gas CO2 | % | 2.8 |
9 | Suhu gas hiruk pikuk | Deg C | 830-850 |
10 | Gas hiruk pikuk CH4 | % | 3.5-4.0 |
11 | Tekanan zona pengurangan | kg/cm persegi | 0,85-0,95 |
12 | Konsumsi gas alam | G cal/ton DRI | 2.4 |
13 | Konsumsi daya | kWh/ton DRI | 95 |
14 | Konsumsi oksigen | N cum/ton DRI | 15 |
15 | Konsumsi air | N cum/ton DRI | 1,2 – 1,5 |
Komposisi tipikal dan suhu gas pada input dan output reformer ada di Tab 5.
Tab 5 Parameter gas di inlet dan outlet reformer |
No.Sl. | Komponen | Satuan | Masuk | Outlet |
1 | H2 | % | 35 | 55 |
2 | CO | % | 19 | 35 |
3 | CO2 | % | 15 | 2 |
4 | H2O | % | 13 | 6 |
5 | CH4 | % | 17 | 1 |
6 | N2 | % | 1 | 1 |
7 | Suhu | Deg C | 580 | 980 |
Parameter kontrol lingkungan yang umum ada di Tab 6.
Tab 6 Parameter kontrol lingkungan |
Emisi udara | Satuan | Partikulat | SO2 | NOx | CO2 |
Pengisi daya hopper | kg/ton DRI | <0,001 | Jejak | <0,004 | |
Tumpukan pembaru | kg/ton DRI | <0,04 | 0,025 | <0.50 | <500 |
Sistem pengumpulan debu (umum untuk satu unit) | kg/ton DRI | 0,015 | Jejak | <0,006 | |
Pembuangan air | | Padatan tersuspensi | Aliran | | |
Tanaman meledak | kg,cum/ton DRI | 0,01 | 0,2 | | |
Tingkat kebisingan | | | | | |
Di dalam area peniup | desibel | 95-105 | | | |
Area lain | desibel | 80-90 | | | |