Proses Corex untuk Produksi Besi
Proses Corex untuk Produksi Besi
Selama akhir abad kedua puluh, beberapa inisiatif baru telah diambil untuk pengembangan teknologi reduksi peleburan yang dapat menjadi jalur alternatif untuk produksi besi cair (logam panas) karena pembuatan besi tanur sembur (BF) konvensional bergantung pada batubara metalurgi, yang diperlukan untuk memproduksi kokas BF yang dibutuhkan untuk produksi logam panas di tanur tinggi. Batubara metalurgi tidak hanya mahal tetapi juga terkait dengan masalah lingkungan selama konversi menjadi kokas BF dalam baterai oven kokas. Proses peleburan reduksi adalah proses yang didasarkan pada teknologi reduksi peleburan dan karenanya dalam proses ini produksi logam panas dilakukan tanpa menggunakan kokas metalurgi. Proses Corex adalah salah satu inisiatif ini. Ini adalah proses peleburan-reduksi pertama dan satu-satunya yang didirikan secara komersial berdasarkan batubara non-coking yang tersedia sebagai rute alternatif tanur tinggi untuk produksi logam panas.
Proses Corex dikembangkan oleh pemasok teknologi Austria VOEST pada akhir 1970-an, dan kelayakannya dikonfirmasi selama 1980-an. Pabrik percontohan pertama dipasang di Kehl, Jerman, pada tahun 1981. Komersialisasi, bagaimanapun, dicapai bersama dengan pembuat baja Afrika Selatan ISCOR di mana modul C-1000 (C – 0,5 M) ditugaskan pada November 1989 di pekerjaan Pretoria-nya. Reaktor generasi pertama yang disebut melter-gasifier ini memiliki diameter tungku 5,5 m dan laju produksi logam panas berkisar antara 40 ton per jam hingga 60 ton per jam. Kapasitas pengenal pabrik adalah 300.000 metrik ton per tahun. Penerapan umum dari proses generasi pertama ini terbatas dan banyak masalah teknis yang harus dipecahkan. Namun demikian, ini membantu mengatasi tahap demonstrasi kritis untuk teknologi pengurangan peleburan ini.
Setelah keberhasilan teknologi reduksi peleburan dicapai melalui pengoperasian modul C-1000, modul C-2000 (C-0,8 M) diperkenalkan oleh pengembang proses. Modul ini memiliki diameter perapian 7,3 m dan tingkat produksi logam panas mulai dari 80 ton per jam hingga 100 ton per jam. Kapasitas pengenal pabrik berkisar antara 600.000 ton per tahun hingga 800.000 ton per tahun. Pabrik pertama yang ditugaskan dengan modul ini adalah pada tahun 1995 di Pohang works of POSCO. Komisioning dilakukan pada tahun 1995. Sejak itu satu modul C-2000 telah ditugaskan di Arcelor Mittal Afrika Selatan – Saldanha Works (Desember 1998), dua modul di pabrik JSW Bellary di India (Agustus 1999, dan April 2000), dan dua modul di pabrik ESSAR di Hazira, India.
Setelah sukses komersial modul C-2000, pengembang proses Corex mulai menawarkan juga modul berkapasitas lebih tinggi yaitu (i) modul C-1,0 M dengan diameter perapian 7,8 m dan tingkat produksi logam panas mulai dari 100 ton per jam hingga 125 ton per jam dan dengan kapasitas terukur mulai dari 800.000 ton per tahun hingga 1 juta ton per tahun, (ii) modul C-1,3 M dengan diameter perapian 9,4 m dan laju produksi logam panas mulai dari 125 ton per jam hingga 160 ton per jam dan dengan kapasitas terukur mulai dari 1,0 juta ton per tahun hingga 1,3 juta ton per tahun, (iii) modul C-3000 (C-1,5 M) dengan diameter perapian 9,6 m dan laju produksi logam panas berkisar dari 160 ton per jam hingga 180 ton per jam dan dengan kapasitas terukur mulai dari 1,3 juta ton per tahun hingga 1,5 juta ton per tahun, dan (iv) modul C- 2,0 M dengan diameter perapian 11,5 m dan logam panas tingkat produksi mulai dari 210 ton per jam hingga 240 ton per jam dan dengan kapasitas pengenal adalah mulai dari 1,7 juta ton per tahun hingga 2,0 juta ton per tahun. Dari modul berkapasitas lebih tinggi ini, dua modul nomor C-3000 (C-1,5 M) telah ditugaskan oleh Baosteel group China pada pekerjaan Luojing mereka di Shanghai, satu pada November 2007 dan yang kedua pada Maret 2011.
Saat ini teknologi Corex adalah proses yang diakui untuk menghasilkan logam panas cair dengan kualitas yang identik dengan logam panas yang diproduksi di tanur tinggi. Ini adalah proses pengurangan peleburan langsung yang terbukti secara industri dan komersial yang memungkinkan produksi logam panas yang hemat biaya dan ramah lingkungan langsung dari bijih besi dan batu bara non-coking. Proses ini merupakan satu-satunya alternatif untuk rute tanur sembur konvensional yang terdiri dari pabrik sinter, oven kokas, dan tanur sembur.
Proses Corex membedakan dirinya dari rute tanur sembur dengan (i) penggunaan langsung batubara non-kokas sebagai agen pereduksi dan sumber energi, (ii) Bijih besi dapat langsung dan layak dibebankan ke proses dalam bentuk bijih lump, dan pelet, dan (iii) penggunaan oksigen murni sebagai pengganti ledakan panas kaya nitrogen. Penggunaan langsung batu bara non-coking dimungkinkan karena batu bara hangus di dalam melter gasifier. Temperatur kubah yang tinggi melebihi 1.000 derajat C yang mengakibatkan perengkahan total hidrokarbon yang dilepaskan oleh batubara non-coking dan menghindari pembentukan tar. Beban bijih khas untuk Corex adalah 30% bijih lump dan 70% pelet. Hasil operasional menunjukkan bahwa operasi yang stabil bahkan dimungkinkan dengan fraksi bijih lump hingga 80%. Penggunaan oksigen dengan kemurnian tinggi dalam proses Corex menghasilkan gas atas bebas nitrogen. Karena nilai kalornya yang tinggi, gas ini dapat didaur ulang untuk pekerjaan reduksi atau digunakan untuk menghasilkan panas atau energi.
Daya tarik proses Corex adalah karena (i) kualitas logam panas yang cocok untuk pembuatan baja, (ii) biaya investasi dan operasional yang rendah karena penghapusan oven kokas dan oleh pabrik produk, (iii) tingkat emisi terkait proses yang rendah, (iv ) penggunaan berbagai macam bijih besi dan terutama batubara non-coking, dan (v) pembangkitan gas ekspor yang sangat berharga yang dapat digunakan untuk berbagai keperluan seperti pembangkit tenaga listrik, produksi DRI, atau substitusi gas alam.
Deskripsi proses
Fitur paling inovatif dari proses Corex adalah pemisahan operasi reduksi dan peleburan besi menjadi dua reaktor terpisah, yaitu poros reduksi dan melter-gasifier. Dalam operasi dua tahap proses DRI yang dihasilkan dari tungku poros dibebankan ke dalam melter-gasifier untuk peleburan. Dalam melter-gasifier, batubara non kokas digasifikasi dengan menyuntikkan oksigen dan bijih besi/pelet yang telah direduksi dilebur. Gas keluar digunakan untuk reduksi bijih besi/pelet di tungku poros hulu. Lembar aliran proses skema ditunjukkan pada Gambar 1 dan tampilan skema bagian tanaman Corex utama ditunjukkan pada Gambar 2.
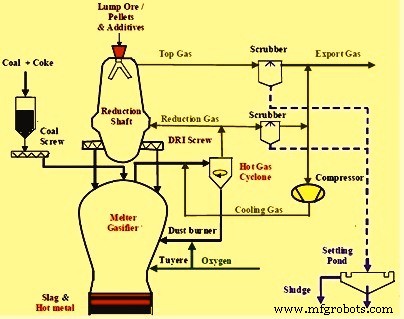
Gambar 1 Skema flow sheet proses Corex
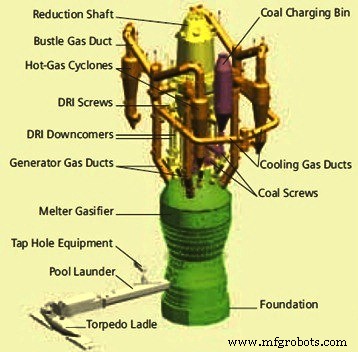
Gbr 2 Tampilan skema bagian tanaman Corex utama
Bijih besi (benih bijih, pelet, atau campurannya) dimasukkan ke dalam poros reduksi, di mana ia direduksi menjadi besi reduksi langsung (DRI) oleh gas reduksi dalam aliran berlawanan. Bahan turun di poros reduksi oleh gravitasi. Gas reduksi sekitar 800 derajat C sampai 850 derajat C dan dengan tekanan lebih dari 3 kg/sq cm bergerak berlawanan arah arus ke bagian atas poros dan keluar dari poros pada sekitar 250 derajat C sampai 300 derajat C. Setrika -bahan bantalan langsung dikurangi menjadi di atas 90% metalisasi di poros, dan disebut sebagai DRI (besi tereduksi langsung). Derajat metalisasi DRI dan kalsinasi aditif sangat bergantung pada empat parameter yaitu (i) jumlah dan kualitas gas reduksi, (ii) suhu gas reduksi, (iii) reduksi beban bantalan besi, dan (iv) ukuran partikel rata-rata dan distribusi padatan yang bermuatan. Selanjutnya, DRI panas (sekitar 800 derajat C) dan batu kapur dan dolomit yang terkalsinasi sebagian dibuang ke dalam melter-gasifier dari poros reduksi melalui konveyor sekrup pelepasan yang dikendalikan dengan kecepatan.
Peleburan-gasifier sebagian besar dapat dibagi menjadi tiga zona reaksi yaitu (i) zona papan bebas gas (bagian atas atau kubah), (ii) zona lapisan arang (bagian tengah di atas tuyer oksigen), dan (iii) zona perapian (bagian bawah). di bawah tuyer oksigen). Karena aliran gas terus menerus melalui unggun arang, terdapat juga unggun terfluidisasi di daerah transisi antara unggun arang dan zona papan bebas. Melter-gasifier beroperasi pada tekanan 3 kg/sq cm hingga 5 kg/sq cm dan terdiri dari area fluidized bed atas sekitar 1500 derajat C dan area pencairan dan pengumpulan cairan yang lebih rendah sekitar 1550 derajat C. Batubara non-coking , batu kapur, dan kuarsit dimasukkan melalui sistem lock hopper ke dalam freeboard di atas area fluidized bed di mana mereka dipanaskan dengan cepat hingga 1000 derajat C hingga 1200 derajat C. Sejumlah kokas juga ditambahkan ke poros untuk menghindari pengelompokan partikel. beban di dalam poros karena menempelnya bijih/pelet dan untuk menjaga permeabilitas lapisan yang memadai.
Zat yang mudah menguap didorong dan partikel karbon tetap yang hancur jatuh ke zona gasifikasi di mana oksigen disuntikkan melalui tuyeres jenis tanur tinggi untuk membakar karbon menjadi karbon monoksida (CO). Oksigen yang disuntikkan membuat arang batubara menjadi gas dan menghasilkan CO. Panas sensibel dari gas panas dipindahkan ke unggun arang, yang digunakan untuk melebur besi dan terak serta reaksi metalurgi lainnya. Pembakaran eksotermis menyediakan energi untuk menyelesaikan pengurangan DRI panas dan untuk melelehkan terak dan besi. Selain reduksi akhir dan peleburan, semua reaksi metalurgi lainnya juga berlangsung di dalam melter-gasifier. Logam panas dan terak disadap seperti dalam praktik tanur sembur konvensional.
Gas pereduksi untuk tungku poros dihasilkan dengan pembakaran parsial batubara dengan oksigen di dalam fluidized bed dari melter-gasifier. Gas pada rentang temperatur 1.050 derajat C sampai 1.100 derajat C dari melter-gasifier didinginkan sampai temperatur gas reduksi (800 derajat C sampai 850 derajat C) dengan penambahan gas pendingin. Gas dibersihkan dalam siklon panas untuk mendaur ulang denda entrained. Sebagian dari gas bersih kemudian dimasukkan ke dalam tungku poros sebagai gas pereduksi yang mengandung lebih dari 94% CO ditambah H2 (hidrogen). Gas yang tersisa dicampur dengan gas yang sudah dibersihkan dari tungku poros dan campuran tersebut digunakan sebagai gas bahan bakar ekspor. Gas bahan bakar ekspor juga dikenal sebagai gas Corex.
Nilai kalor gas Corex adalah sekitar 2000 kkal/N cum. Komponen utama gas Corex berdasarkan volume adalah sekitar karbon monoksida – 44%, karbon dioksida – 30%, hidrogen – 21%, kelembaban – 1%, nitrogen – 2%, metana – 1,5%, dan kandungan debu – kurang dari 5 mg /N sperma. Tekanan gas Corex yang dipasok ke berbagai konsumen biasanya sekitar 700 mm kolom air.
Perhitungan neraca panas dan massa untuk proses pembuatan besi memegang peranan penting selama pengoperasian proses Corex. .
Sistem daur ulang yang terdiri dari stasiun kompresor dan pembuangan CO2 memungkinkan penggunaan lebih banyak gas ekspor untuk pekerjaan metalurgi. Hal ini meningkatkan pemanfaatan gas ekspor ke tingkat yang lebih tinggi dan meningkatkan keekonomian proses secara keseluruhan selain membuatnya lebih ramah lingkungan. Karena peningkatan pemanfaatan gas yang didasarkan pada daur ulang gas ini, produksi gas di dalam melter gasifier dapat diturunkan secara signifikan, yang secara langsung tercermin dalam konsumsi bahan bakar dan oksigen yang lebih rendah. Dengan produksi terak ini juga berkurang sekitar lebih dari 20%.
Kimia proses
Dalam proses Corex, konsep tanur sembur digunakan tetapi tanur sembur sebenarnya dibagi menjadi dua bagian pada antarmuka zona kohesif (Gbr 3). Prosesnya memiliki tiga tahap. Tahap pertama dari proses berlangsung di poros reduksi, di mana beban bijih besi dikurangi oleh gas yang berasal dari melter-gasifier dan diubah menjadi DRI panas. DRI panas secara mekanis ditransfer ke melter-gasifier dimana tahap kedua dan ketiga dari proses berlangsung. Tahap kedua dari proses terdiri dari peleburan dan karburasi DRI panas oleh batubara dan oksigen yang ditambahkan dalam meter-gasifier. Dalam proses tahap ketiga yang berlangsung di bagian atas dari melter-gasifier, unggun terfluidisasi arang batubara dipertahankan. Di sini CO2 (karbon di oksida) dan uap air (H2O) diubah menjadi CO dan H2. Karena praktis tidak ada CO2 atau H2O dalam gas yang keluar dari melter-gasifier, tingkat pembakaran gas Corex pasca pembakaran adalah nol, menghasilkan gas yang kaya akan energi kimia.
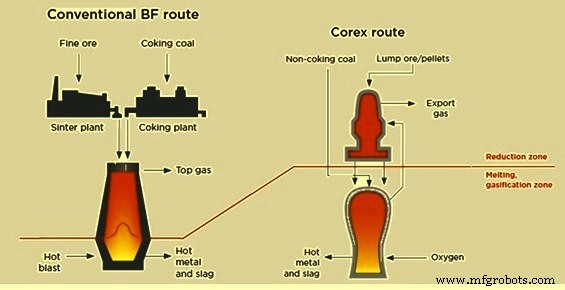
Gbr 3 Perbandingan konsep rute tanur sembur dan rute Corex
Reaksi yang terjadi di poros reduksi adalah sebagai berikut.
- Pengurangan beban besi oleh CO dan H2 dan metalisasinya dalam beberapa tahap. Fe2O3-> Fe3O4 -> FeO-> Fe.
- Kalsinasi batugamping dan dolomit. CaCO3 =CaO + CO2 dan CaCO3.MgCO3 =CaO.MgO + 2CO2.
- Reaksi pengendapan karbon dan pembentukan besi karbida (Fe3C). 2CO =CO2 + C dan 3Fe + 2CO =Fe3C+ CO2.
Dari reaksi-reaksi yang disebutkan di atas, reaksi reduksi oksida besi oleh hidrogen dan kalsinasi adalah reaksi endotermik, sedangkan reaksi reduksi oksida besi oleh gas CO dan deposisi karbon bersifat eksotermik. Gas reduksi hampir sepenuhnya terdesulfurisasi di poros karena adanya kapur dan dolomit yang terbakar sesuai dengan reaksi CaO + H2S =CaS + H2O dan MgO + H2S =MgS + H2O. Kandungan hidrogen sulfida yang rendah dari gas bagian atas penting sehubungan dengan penggunaan gas Corex lebih lanjut.
Reaksi yang terjadi dalam melter-gasifier adalah sebagai berikut.
- Pengeringan batubara yang berlangsung pada 100 derajat C.
- Devolatilisasi batubara yang terjadi pada kisaran suhu 200 derajat C hingga 950 derajat C dan pelepasan metana (CH4) dan hidrokarbon yang lebih tinggi (CnHm).
- Dekomposisi bahan yang mudah menguap terjadi karena suhu yang lebih tinggi yang berlaku di zona papan bebas melter-gasifier. Di daerah ini, hidrokarbon dipecah menjadi hidrogen dan karbon dasar (CnHm =n C + (m/2) H2). Diinginkan bahwa semua hidrokarbon yang lebih tinggi retak di zona papan bebas untuk menjamin pembangkitan gas reduksi kualitas yang baik. Hal ini dicapai dengan mempertahankan suhu kubah dalam kisaran 1050 derajat C hingga 1100 derajat C. Reaksi lain yang terjadi di zona papan bebas adalah (i) CO2 + C =2CO (reaksi Boudouard), (ii) H2O + C =CO + H2 (reaksi gas air), dan (iii) CO + H2O =CO2 + H2 (reaksi pergeseran).
- Kalsinasi batu kapur dan dolomit yang tidak dikalsinasi.
- Pengurangan oksida besi sisa dalam besi spons.
- Reduksi langsung FeO di DRI terjadi oleh karbon di unggun arang.
- Pembakaran arang batubara oleh oksigen terjadi di dekat tuyer karena suhu maksimum di dalam melter-gasifier ada di depan tuyer. Reaksi gasifikasi karbon yang terjadi di daerah tuyeres adalah (i) 2C + O2 =2CO, (ii) 2CO + O2 =2CO2, dan (iii) C + CO2 =2CO.
- Pencairan besi dan terak serta pemisahan logam panas dan terak cair.
Karakteristik produk dan konsumsi spesifik
Analisis tipikal logam panas dari proses Corex terdiri dari karbon – 4,5%, silikon – 0,5%, mangan – 0,08%, belerang – 0,03%, dan fosfor – 0,1%. Suhu logam panas sekitar 1470 derajat C hingga 1500 derajat C.
Analisis tipikal terak dari proses Corex terdiri dari CaO – 35%, MgO – 13%, SiO2 – 31%, Al2O3- 15%, FeO – 0,4%, TiO2 – 0,5%, dan S – 1,2%. Suhu terak cair adalah sekitar 1520 derajat C hingga 1580 derajat C.
Analisis tipikal gas atas proses Corex terdiri dari sekitar CO – 42%, H2 -19%, CO2 – 31% dan CH4 – 1,9%. Analisis tipikal gas reduksi adalah sekitar CO – 62%, H2 – 23%, CO2 – 9%, dan metana – 2%. Analisis tipikal gas ekspor adalah sekitar CO – 44 %, H2 – 21 %, CO2 – 30 %, kelembaban – 1 %, N2 – 2 %, CH4 – 1,5 %, dan kandungan debu – kurang dari 5 mg/N cum.
Angka konsumsi spesifik tipikal dalam per ton logam panas adalah sekitar 940 kg untuk batubara kering non-coking, 265 kg untuk aditif dan 520 cum untuk oksigen. Angka konsumsi spesifik tipikal yang sesuai dengan daur ulang gas ekspor dalam per ton logam panas adalah sekitar 770 kg untuk batubara non-coking kering, 185 kg untuk aditif dan 455 cum untuk oksigen. Angka generasi khas dalam per ton logam panas adalah sekitar 340 kg untuk terak cair dan sekitar 16.500 ribu cum gas ekspor dengan nilai kalori sekitar 1910 Kcal/N cum. Angka generasi khas yang sesuai dengan daur ulang gas ekspor dalam per ton logam panas adalah sekitar 265 kg untuk terak cair, dan sekitar 14.100 ribu cum gas ekspor dengan nilai kalori sekitar 1790 Kcal/N cum.
Dalam proses Corex sekitar 45% dari total input energi digunakan untuk pembuatan besi dan sisanya digunakan untuk ekspor bahan bakar gas. Logam panas yang dihasilkan memiliki kandungan karbon dan silikon yang mirip dengan logam panas tanur sembur. Namun, hampir semua belerang dalam batubara non-coking masuk ke terak dan logam panas. Dalam hal ini, sulfur organik dalam batubara tergas dan diserap oleh DRI dan dikembalikan ke melter-gasifier sebagai besi sulfida.
Aspek lingkungan dari proses
Proses Corex menangkap sebagian besar polutan dalam keadaan inert di terak dan hidrokarbon yang dilepaskan dihancurkan di kubah melter-gasifier. Lebih lanjut karena coking in-situ batubara di melter-gasifier, sebagian besar belerang ditangkap di terak, secara dramatis mengurangi emisi gas SO2 atau H2S. Juga, karena oksigen murni digunakan sebagai pengganti ledakan udara panas, proses Corex secara signifikan mengurangi emisi nitrogen dalam bentuk NOx dan memberikan keuntungan sehubungan dengan emisi debu. Tingkat emisi dengan proses Corex jauh lebih rendah dibandingkan dengan jalur produksi BF yang terdiri dari blast furnace, sinter plant dan coke oven.
Proses Corex memancarkan setidaknya 15% lebih sedikit CO2 dibandingkan dengan rute BF untuk produksi logam panas. Emisi udara juga lebih rendah dari unit BF konvensional. Emisi CO2 sekitar 1420 kg/tHM dibandingkan dengan sekitar 1900 kg/tHM untuk BF. Emisi SO2 sekitar 55 Kg/tHM dibandingkan dengan sekitar 1400 kg/tHM pada jalur produksi BF. Partikulat dan emisi NOx dalam proses Corex sekitar 10% dari rute produksi BF. Debit fenol sekitar 0,04 g/tHM, sedangkan pada jalur produksi BF adalah 100 g/tHM. Debit sulfida sekitar 0,01 g/tHM sedangkan untuk jalur produksi BF adalah 180 g/tHM. Debit amonia untuk proses Corex adalah 60 g/tHM sedangkan untuk jalur produksi BF adalah 900 g/tHM. Pembuangan sianida dalam air limbah sepenuhnya dihilangkan dalam rute Corex.
Keuntungan dan keterbatasan proses Corex
Keuntungan dari proses Corex termasuk (i) pengurangan biaya investasi spesifik dibandingkan dengan rute produksi tanur sembur konvensional, (ii) biaya produksi yang lebih rendah, (iii) kinerja lingkungan yang lebih baik karena emisi dan pelepasan yang lebih rendah, (iv) nilai kalor yang lebih tinggi gas ekspor membuatnya cocok untuk digunakan dalam berbagai aplikasi, (v) fleksibel sehubungan dengan penggunaan bahan baku karena berbagai macam bijih besi dan batubara dapat digunakan, (vi) fleksibilitas operasional yang baik sehubungan dengan kapasitas produksi , penghentian produksi dan perubahan bahan mentah.
Keterbatasan proses Corex antara lain (i) optimalisasi distribusi batubara dan DRI diperlukan dalam melter-gasifier untuk menghindari aliran periferal gas panas, (ii) tidak adanya hasil pasca pembakaran menjadi hilangnya energi kimia dalam gas ekspor yang dihasilkan menjadi konsumsi batubara yang tinggi, (iii) banyak peralatan seperti kompresor gas pendingin berorientasi pada pemeliharaan, (iv) transfer DRI panas dan daur ulang gas panas berbahaya terutama selama masa pemeliharaannya, (vi) melter-gasifier adalah mengalami puncak tekanan yang tinggi karena penggunaan batubara mentah dengan kondisi char bed yang buruk yang mengakibatkan macetnya sistem daur ulang debu serta sistem pembersihan gas, (vii) sensitivitas parameter kualitas input proses seperti granulometri, persentase denda dalam input, decrepitation, dan perilaku degradasi batubara, bijih besi dan pelet pada suhu tinggi.