Pembuatan baja di Tungku Induksi
Pembuatan Baja di Tungku Induksi
Tungku induksi tanpa biji telah digunakan dalam industri besi selama lebih dari 50 tahun dan sekarang menjadi salah satu cara paling populer untuk melelehkan dan menahan bahan besi. Peleburan induksi memiliki pertumbuhan dramatis selama tahun 1960 berdasarkan teknologi frekuensi garis, dan kemudian dengan pengenalan skala besar catu daya frekuensi menengah selama tahun 1980-an. Pembuatan baja ringan di tungku induksi pertama kali dicoba pada awal 1980-an dan mendapatkan popularitas ketika produksi besi spons menggunakan proses rotary kiln berbasis batubara menjadi populer.
Tungku induksi adalah jenis tungku peleburan listrik yang menggunakan arus listrik untuk melelehkan logam. Prinsip peleburan induksi adalah bahwa sumber listrik tegangan tinggi dari kumparan primer menginduksi tegangan rendah, arus tinggi dalam logam (kumparan sekunder). Pemanasan induksi hanyalah metode transfer energi panas. Dua hukum yang mengatur pemanasan induksi adalah (i) induksi elektromagnetik, dan (ii) efek joule.
Tungku induksi tanpa biji terdiri dari wadah tahan api yang relatif tipis yang dikelilingi oleh koil tembaga berpendingin air yang dieksitasi dari suplai AC tunggal. Ketika kumparan diberi energi, medan magnet aksial yang berfluktuasi menyebabkan arus mengalir dalam potongan-potongan bahan muatan yang menghantarkan listrik di dalam wadah. Daya yang diinduksi dalam muatan tergantung pada sifat fisik material, fluks yang menghubungkannya, dan bentuk geometrisnya. Tergantung pada resistivitas bahan yang dilebur, tungku induksi tanpa biji mengubah energi listrik menjadi panas muatan pada efisiensi antara 50% dan 85%, meskipun efisiensi tungku selanjutnya dikurangi dengan kehilangan panas dari radiasi dari permukaan leleh dan konduksi melalui lapisan tungku.
Tungku induksi frekuensi menengah yang biasa digunakan untuk pembuatan baja menggunakan panas yang dihasilkan oleh arus eddy yang dihasilkan oleh medan bolak-balik frekuensi tinggi. Induktor biasanya terbuat dari tembaga untuk membatasi rugi-rugi listrik. Induktor didinginkan dengan air. Tungku terdiri dari wadah yang terbuat dari bahan tahan api yang sesuai yang dikelilingi oleh kumparan tembaga berpendingin air. Dalam jenis tungku ini, muatan dilebur oleh panas yang dihasilkan dari busur listrik. Kumparan membawa arus frekuensi tinggi. Medan magnet bolak-balik yang dihasilkan oleh arus frekuensi tinggi menginduksi arus eddy yang kuat dalam muatan yang menghasilkan pemanasan yang sangat cepat.
Energi listrik yang dibutuhkan untuk memanaskan satu ton besi sampai 1500 derajat C adalah 396 kWh. Dalam tungku beberapa kerugian terjadi yang meningkatkan konsumsi energi spesifik. Rugi-rugi tersebut terdiri dari (i) rugi-rugi termal, (ii) rugi-rugi koil tungku, (iii) rugi-rugi bank kapasitor, (iv) rugi-rugi konverter, dan (v) rugi-rugi pada sisi utama transformator. Semakin tinggi kerugian yang lebih rendah adalah efisiensi tungku. Kerugian termal memberikan kontribusi maksimum terhadap hilangnya energi. Kehilangan termal utama adalah (i) kehilangan radiasi dari bagian atas tungku, (ii) kehilangan konduksi dari lapisan refraktori, (iii) kehilangan panas dalam air pendingin koil, dan (iv) panas yang dibawa oleh terak yang dihilangkan.
Selama pembuatan panas, tungku terus-menerus kehilangan panas baik ke air pendingin dan oleh radiasi dari cangkang dan permukaan logam yang terbuka. Energi listrik harus dikeluarkan untuk menggantikan kehilangan panas ini. Oleh karena itu, semakin lama waktu pemanasan, semakin besar inefisiensi tungku.
Bahan mentah
Tungku induksi tanpa biji biasanya dianggap sebagai unit 'cair mati', di mana secara efektif hanya terjadi sedikit perubahan selama proses berlangsung. Oleh karena itu, bahan baku memainkan peran penting selama pembuatan baja.
Bahan baku untuk membuat panas di tungku harus dipilih dan dikendalikan untuk memastikan bahwa baja cair yang dibuat memiliki sifat mekanik dan komposisi kimia yang diinginkan setelah pengecoran di mesin pengecoran kontinu dan bebas dari cacat. Selain itu kualitas bahan baku baja yang dihasilkan juga mempengaruhi (i) volume terak yang dihasilkan, (ii) umur lapisan refraktori, dan (iii) keselamatan baik pabrik maupun pekerja. Selanjutnya, bahan mentah beserta praktik pengisiannya memiliki pengaruh yang cukup besar terhadap konsumsi spesifik energi listrik dan produktivitas tungku.
Parameter penting yang harus dikontrol dalam bahan baku adalah (i) ukuran, (ii) berat jenis, (iii) komposisi kimia, (iv) kebersihan, jumlah kontaminasi, dan bebas dari karat, kerak, pasir, kotoran, minyak/lemak , dan (v) pelapis non-logam. Muatan bahan baku dengan berat jenis lebih besar dari 1 ton/cum memberikan konsumsi energi yang lebih rendah daripada bahan muatan dengan berat jenis lebih rendah sekitar 0,5 ton/cum.
Di antara berbagai bahan baku yang digunakan untuk membuat panas, logam mengambil bagian terbesar baik dari segi teknologi dan ekonomi. Bahan baku utama pembuatan baja di tungku induksi adalah (i) scrap baja, (ii) scrap besi atau/dan pig iron, (iii) besi spons, (iv) karburator, dan (v) aditif. Dari ketiganya, tiga yang pertama adalah logam.
Scrap yang kotor atau terkontaminasi cenderung mengendapkan lapisan terak pada refraktori tungku. Ini terjadi pada, atau tepat di bawah, tingkat cairan dalam wadah dan membatasi jumlah daya yang ditarik oleh tungku. Pengurangan efektif dalam diameter internal tungku juga dapat membuat pengisian lebih sulit dan berlarut-larut. Ini sekali lagi mempengaruhi efisiensi energi tungku.
Potongan berkarat tidak hanya membutuhkan lebih banyak waktu untuk meleleh tetapi juga mengandung lebih sedikit logam per pengisian. Memo harus diperiksa untuk memastikan bahwa baja pra-lapisan seperti pelat kaleng dan berlapis seng tidak termasuk, karena bahan-bahan ini menghasilkan asap dan terak metalurgi dalam jumlah berlebihan. Untuk setiap 1% terak yang terbentuk pada 1500 derajat C, kehilangan energi adalah 10 kWh per ton.
Tidak seperti skrap baja, skrap besi, dan besi kasar, besi spons dicirikan oleh (i) porositas tinggi, (ii) densitas rendah, (iii) konduktivitas termal rendah, (iv) luas permukaan spesifik tinggi, (v) kandungan oksigen tinggi , dan (vi) kandungan karbon antara. Besi spons memiliki karakteristik kimia dan fisik yang seragam. Ini memiliki persentase elemen logam tramp yang rendah (sekitar 0,02%) dan kandungan belerang yang rendah.
Aditif yang digunakan untuk pembuatan baja dalam tungku induksi biasanya adalah paduan besi. Paduan ferro harus diperiksa apakah memenuhi spesifikasi untuk ukuran, gradasi dan komposisi. Secara khusus, mereka harus diperiksa untuk denda karena ini merupakan sumber kerugian yang tinggi dan karenanya variasi dalam kimia yang diharapkan dari baja yang dibuat dalam panas.
Peran karburator selama pembuatan baja di tungku induksi adalah untuk menghilangkan oksigen dari besi spons yang ada dalam bentuk FeO dan menyediakan pengambilan karbon dalam baja cair ke tingkat yang diinginkan. Kokas minyak bumi dan batubara antrasit adalah dua karburator populer yang digunakan selama pembuatan baja di tungku induksi. Namun masukan karbon dalam bak melalui besi kasar atau besi tuang lebih diinginkan untuk mendapatkan pemulihan karbon yang lebih baik. Penggunaan ukuran partikel yang sangat halus dari karburator harus dihindari karena kehilangan yang berlebihan. Karburator lain yang dapat digunakan adalah kokas metalurgi, karbida besi dan karbida silikon metalurgi (63% silikon dan 31% karbon). Silikon karbida biasanya diisi dengan skrap dan memiliki keunggulan (i) penyerapan lebih cepat, (ii) bertindak sebagai de-oksidator, dan (iii) meningkatkan umur lapisan.
Perhitungan yang akurat dari campuran muatan yang diperlukan berdasarkan analisis material, dan penentuan berat yang tepat serta pengukuran bahan pengisi dan aditif (karburator dan aditif) adalah prasyarat dasar untuk meminimalkan waktu leleh dan kebutuhan daya selain memastikan komposisi baja cair yang tepat. Penggunaan bahan pengisi bersih dan kering diperlukan untuk hasil yang lebih baik.
Pengoperasian tungku induksi yang efisien terutama bergantung pada penerapan praktik pengoperasian. Langkah-langkah yang terlibat dalam pengoperasian tungku induksi ditunjukkan pada Gambar 1.
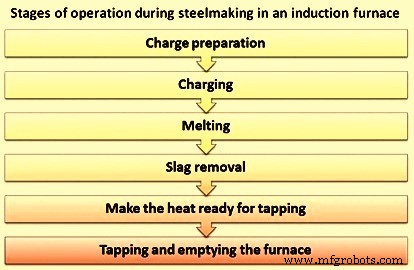
Gbr 1 Tahapan operasi selama pembuatan baja di tungku induksi
Persiapan dan pengisian daya
Konsumsi energi meningkat secara signifikan dengan praktik pengisian daya yang salah. Praktik terburuk adalah mengisi sejumlah kecil dan menunggu pencairan terjadi sebelum menambahkan bahan lebih lanjut. Praktik terbaik adalah menambahkan muatan ke tingkat atas koil daya dan mengisi ulang saat muatan berkurang.
Bahan baku harus ditimbang dan diatur di lantai operasi dekat tungku sebelum memulai pemanasan. Bahan baku yang akan diisi disimpan dalam wadah yang sesuai dan harus siap untuk diisi dengan metode yang dipilih. Karburator dan aditif harus ditimbang secara akurat dan ditangani dengan benar untuk menghindari pemborosan selama penanganan.
Ukuran maksimum satu potongan logam/memo harus kurang dari 0,4 kali diameter wadah tungku. Ini menghindari masalah menjembatani. Selanjutnya setiap muatan logam/sampah harus sekitar 10% dari volume wadah tungku. Juga, harus dipastikan bahwa praktis tidak ada ujung yang tajam karena dapat merusak refraktori.
Tungku tanpa biji frekuensi menengah dioperasikan tanpa bah (tumit). Metode pengisian tungku ini bergantung pada beberapa faktor yang meliputi (i) ukuran tungku, (ii) keluaran tungku, dan (iii) bahan pengisi yang digunakan.
Baik metode mekanis atau manual dapat digunakan tetapi tiga faktor yang diberikan di atas biasanya menentukan metode tersebut. Untuk bahan magnetik seperti skrap baja, besi tuang, besi kasar dan pengembalian pabrik, derek atas yang dilengkapi dengan elektromagnet digunakan untuk pengisian langsung tungku. Besi spons dapat diisi baik dengan derek di atas kepala yang dilengkapi dengan elektromagnet atau/dan dengan metode manual.
Metode pengisian manual hanya cocok untuk tungku yang lebih kecil. Jika throughput tinggi atau kondisi pengoperasian sulit, bahan pengisi daya ditambahkan ke tungku dengan ember bagian bawah atau pengisi daya getar, yang sering kali dilengkapi perangkat penimbangan untuk memastikan susunan pengisian daya yang benar.
Tungku tidak pernah diisi melebihi tingkat koil, yaitu pengisian tungku ke kapasitasnya. Lebih lanjut harus dipahami bahwa ketika lapisan tungku aus, jumlah bahan pengisi akan meningkat sesuai dengan itu. Urutan pengisian yang benar harus diikuti. Pengisian skrap ringan di bagian bawah diikuti dengan skrap yang lebih berat di bagian atas melindungi lapisan bawah dari kerusakan selama pengisian. Pengisian bahan basah atau lembab dalam lelehan dapat menyebabkan ledakan dan harus dihindari.
Pencairan dan penghilangan terak
Bahan diisikan ke dalam tungku kosong sampai ke tepi atas koil tungku. Ketika catu daya listrik dihidupkan, tegangan diinduksi dalam bahan yang diisi, yang menyebabkan arus eddy yang kuat. Karena arus listrik yang tinggi dan hambatan material, material dipanaskan hingga titik leleh.
Bahan peleburan mengendap bersama, dan tungku dapat diisi ulang dengan lebih banyak bahan. Dalam tungku frekuensi menengah, bahan tidak diisi ke dalam penangas cairan, tetapi ke bahan yang masih padat.
Dalam kasus besi spons dalam muatan, oksigen yang ada dalam besi spons dalam bentuk FeO, yang bereaksi kuat dengan karbon dalam penangas cair dan meningkatkan perpindahan panas, kontak logam terak, dan homogenitas penangas.
Untuk kelancaran operasi peleburan, penghilangan terak secara berkala diperlukan karena terak akan mengeras di atas penangas cairan dan menghambat pelelehan lebih lanjut dari besi spons. Besi spons dapat ditambahkan langsung ke dalam logam cair ketika aksi pengadukan mempercepat perpindahan panas ke dalamnya dan mendorong pencairan. Perawatan diperlukan untuk memastikan bahwa ada cukup kolam cairan sebelum menambahkan besi spons.
Terlepas dari mode pengisian, besi spons selalu diisi setelah pembentukan awal kolam cair (yaitu tumit panas) dengan melelehkan skrap baja. Pelelehan besi spons sangat dipengaruhi oleh faktor-faktor seperti kandungan karbon dari penangas cair dan tingkat metalisasi besi spons. Kandungan karbon dari penangas cair bereaksi dengan kandungan oksida besi yang tidak tereduksi dari besi spons memberikan evolusi gas CO dan CO2 dari penangas cair yaitu terjadi pendidihan karbon, yang menghasilkan penghilangan gas hidrogen dan nitrogen berikutnya, yang pada akhirnya menghasilkan baja bersih. Pendidihan karbon terjadi pada antarmuka logam terak melalui reaksi 3 FeO + 2C =3 Fe + CO + CO2.
Kandungan karbon dalam penangas cairan harus dijaga pada tingkat yang tepat untuk mempertahankan titik didih karbon yang sesuai selama periode peleburan. Jumlah karbon yang dibutuhkan (C, dalam kg) untuk mengurangi kandungan FeO dari besi spons diberikan oleh persamaan C =1,67 [100 – % M–{(% Slag /100) x % Fe}]. Di sini, M adalah derajat metalisasi dan Fe adalah jumlah besi dalam terak.
Karbon dalam bentuk antrasit atau kokas minyak bumi biasanya ditambahkan selama periode pengisian logam untuk meningkatkan pencampuran dan mengurangi jumlah penambahan trim yang harus dilakukan pada rendaman cair penuh. Tungku frekuensi menengah menunjukkan aksi pengadukan yang kurang kuat saat frekuensi operasi meningkat. Hal ini pada gilirannya membuat penambahan karbon ke rendaman cair menjadi lebih sulit.
Terak umumnya dikembangkan di tungku tanpa biji frekuensi menengah tidak cair dan cukup berat dan lengket dan sering kering dan dalam bentuk sampah. Penghapusan terak oleh karena itu umumnya difasilitasi dengan penggunaan sendok penghilang terak yang dilengkapi dengan batang baja panjang. Sendok ini dibuat khusus untuk tujuan tersebut.
Jika koagulan terak digunakan untuk membantu menghilangkan terak, penggunaannya harus dikontrol secara ketat untuk mencegah serangan kimia pada bahan pelapis tungku. Volume terak dapat dikurangi dengan memilih bahan pengisi yang bersih dan tepat dan dengan besi spons yang memiliki persentase besi total yang lebih tinggi.
Kehilangan logam untuk bahan pengisi logam tergantung pada ukuran fisik komponen dan kualitasnya, tetapi biasanya kurang dari 5%, dengan proporsi yang wajar dari kehilangan ini disebabkan oleh tumpahan dan percikan selama operasi penghilangan slagging dan penuangan. Pemulihan karbon tergantung pada ukuran dan kualitas karburator, metode penambahan, dan waktu penambahan. Ini dapat diharapkan berada dalam kisaran 85% hingga 95%.
Menyiapkan panas, mengetuk dan mengosongkan tungku
Ketika tingkat pengisian cairan telah mencapai sekitar tepi atas koil, sampel diambil dan bahan untuk analisis akhir ditambahkan ke tungku. Bahan ini sekarang dilelehkan, dan lelehannya dinaikkan ke suhu 80 derajat C hingga 100 derajat C di bawah suhu penyadapan.
Ketika sendok sadap siap, tungku disaring dan dibawa ke suhu sadapan. Dalam kasus tungku frekuensi menengah, 2 hingga 5 menit diperlukan untuk aktivitas ini. Suhu cairan diukur dengan termokopel dip. Sebelum penyadapan, sejumlah kecil paduan besi diisikan ke dalam tungku untuk menghindari tindakan mendidih selama penyadapan.
Dalam sendok yang penuh, jumlah paduan besi dan karburator yang diperlukan (jika diperlukan) dimasukkan ke dasar sendok dan logam disadap.
Kontrol dan otomatisasi proses
Konsep modern toko pembuatan baja melibatkan kontrol semua fungsi yang terjadi sehingga pengetahuan rinci tentang kualitas baja cair dan biaya dapat dikumpulkan. Sebelumnya, hanya toko pembuat baja yang lebih besar yang memiliki bentuk kontrol tungku. Namun, biaya komputer yang rendah dan perangkat kontrol logika yang dapat diprogram (PLC) sekarang memungkinkan sistem kontrol dengan berbagai tingkat kerumitan dipasang secara ekonomis di instalasi yang lebih kecil. Sistem ini melakukan beberapa fungsi yang dapat diklasifikasikan di bawah judul (i) otomatisasi proses, (ii) pemantauan proses, (iii) tampilan dan perekaman informasi, dan (iv) antarmuka dengan tungku lain dan sistem kontrol.
Otomasi proses – Sistem otomasi paling canggih dapat mengontrol siklus pembuatan baja mulai dari pemilihan bahan pengisi hingga penyadapan baja cair dan juga antarmuka dengan sistem manajemen lainnya. Sistem yang lebih sederhana hanya mengontrol operasi pembuatan baja. Agar berfungsi, sistem ini memerlukan informasi tentang bobot pengisian, waktu, dan input daya. Bobot muatan diperoleh dari sel beban atau masukan dari operator sementara waktu diketahui dari jam internal perangkat yang disetel ulang pada awal setiap pemanasan. Daya berasal dari pengukuran tegangan dan arus untuk koil tungku. Masukan energi kemudian dihitung dan dibandingkan dengan nilai yang ditetapkan yang ditentukan dari pengalaman pabrikan dengan tungku serupa dan dapat diubah oleh operator agar sesuai dengan kasus individual. Ketika nilai yang ditetapkan tercapai, tungku secara otomatis dimatikan dan muatannya meleleh di sekitar suhu target. Pengukuran parameter-parameter ini cukup akurat, namun variasi dalam muatan dan bagaimana letaknya di tungku menghasilkan energi induksi yang bervariasi sehingga suhu yang diperoleh bervariasi antara panas. Tahap selanjutnya adalah memanaskan logam hingga suhu penyadapan yang disetel yang hanya dapat dicapai jika suhu awal diketahui. Hal ini disediakan dengan memastikan bahwa pengukuran kemiringan logam cair yang akurat dilakukan, dengan hasilnya langsung diumpankan ke sistem kontrol atau dimasukkan oleh operator.
Antara pelelehan dan pemanasan berlebih, logam biasanya dipisahkan, diambil sampelnya dan komposisinya diubah untuk memenuhi spesifikasi. Jika diperlukan, sistem kontrol menahan suhu pada nilai yang ditetapkan dan menghitung tingkat daya optimal untuk melakukannya. Dengan cara ini, kontrol yang akurat pada energi yang disuplai dapat dipertahankan, menghindari biaya energi yang tinggi dan suhu yang berlebihan.
Sistem kontrol dapat digunakan untuk operasi otomatis lainnya seperti (i) tungku start dingin, dan (ii) sintering lapisan baru. Dalam kasus ini, data suhu disediakan oleh termokopel dan sistem mengontrol suhu dengan memvariasikan input daya.
Pemantauan proses – Saat mengontrol operasi pembuatan baja, sistem juga dapat memantau alat bantu seperti air, hidrolik, catu daya, dan sistem ekstraksi asap. Saat terjadi masalah, tampilan alarm memperingatkan operator. Catatan jangka panjang dapat disimpan dari arus kumparan dan trennya pada tegangan tertentu karena peningkatan apa pun dapat menunjukkan keausan lapisan. Oleh karena itu, sistem dapat memberikan indikasi kepada operator kapan refraktori perlu diganti.
Tampilan dan perekaman informasi – Sistem kontrol menyediakan informasi dan sistem yang lebih kompleks melakukannya di semua tingkatan mulai dari operator hingga manajemen. Unit tampilan visual (VDU) memberikan informasi tentang konsumsi energi, daya, suhu, dan berat logam di tungku selama peleburan, penahanan, dan pemanasan berlebih. Data sering ditampilkan dalam bentuk grafik untuk membantu dalam membaca informasi. Ada layar menu yang berbeda untuk fungsi yang berbeda seperti (i) untuk menunjukkan alarm, (ii) untuk menyesuaikan lapisan, atau (iii) untuk mengetuk. Monitor budak dapat menduplikasi tampilan jauh dari platform tungku. Sistem yang lebih sederhana dapat memiliki layar kristal cair (LCD) yang dapat memberikan data umum yang sama tetapi tidak secara grafis.
Operator dapat berkomunikasi dengan sistem untuk memasukkan informasi atau mengubah pengaturan, dengan papan tombol, pena ringan, atau layar sentuh tergantung pada preferensi pabrikan dan kecanggihan sistem. Catatan juga dapat diberikan untuk panas, shift, atau sebulan.
Berinteraksi dengan tungku lain dan sistem kontrol – Sistem juga dirancang untuk mengontrol operasi pembuatan baja dengan lebih dari satu tungku. Sistem kemudian mengontrol semua tungku dan mengoptimalkan peleburan untuk memberikan keluaran logam yang diperlukan dari seluruh instalasi pembuatan baja. Ini memperhitungkan batasan daya yang dikenakan pada beberapa periode hari oleh kontrak dengan pemasok listrik dan mengoptimalkan pembuatan baja untuk memberikan tingkat leleh terbaik.
Sistem juga telah dikembangkan untuk melaporkan dan menerima informasi dari jaringan kontrol yang beroperasi pada tingkat yang lebih tinggi. Ini dapat bertindak berdasarkan informasi dari jaringan seperti perubahan suhu penuangan logam, perubahan komposisi paduan, ketersediaan bahan baku dan berat muatan dan mengoperasikan tungku sesuai dengan itu.
Sistem kontrol yang dijelaskan di atas adalah metode yang menyediakan kontrol otomatis untuk peleburan, penahanan dan penyadapan. Mereka dapat memulai tungku dari dingin, mengontrol siklus sintering lapisan dan melakukan pemeriksaan diagnostik berkelanjutan pada catu daya, komponen tungku, sistem tambahan dan lapisan tungku. Setiap kesalahan atau kegagalan dapat diidentifikasi dan menarik perhatian operator. Catatan yang komprehensif dapat disimpan dari semua data yang dipantau untuk pengendalian manajemen. Sistem dapat mengontrol lebih dari satu tungku dan menjadi bagian dari jaringan yang lebih besar yang mengontrol semua fungsi toko peleburan. Sistem yang paling canggih tidak hemat biaya untuk toko pembuatan baja kecil. Beberapa sistem dapat dipasang kembali ke peralatan yang ada.