Proses peleburan merah untuk pembuatan besi
Proses peleburan untuk pembuatan besi
Redsmelt adalah proses pembuatan besi baru berdasarkan dua langkah reduksi. Ini adalah (i) pra-reduksi bahan bantalan besi dalam tungku perapian putar (RHF), dan (ii) peleburan besi pra-reduksi panas (DRI, besi reduksi langsung). Awalnya tungku busur terendam (SAF) telah digunakan untuk langkah kedua. SAF kini telah digantikan oleh konverter tiup batubara dan oksigen (reaktor oxy-coal) yang dikenal sebagai 'Teknologi Peleburan Baru' (NST). RHF mengurangi pelet hijau yang terbuat dari bijih besi, zat halus reduktor, dan pengikat untuk menghasilkan DRI logam panas yang dibebankan ke NST untuk peleburannya menjadi logam panas.
Proses Redsmelt telah dianggap terdiri dari teknologi yang hemat biaya dan ramah lingkungan. Sorotan penting dari proses ini adalah sebagai berikut.
- Prosesnya tidak memerlukan bahan pengisi daya yang disiapkan
- Prosesnya tidak membutuhkan energi listrik, karena peleburan DRI dilakukan dengan menggunakan energi kimia
- Smelter memiliki produktivitas tinggi sehingga biaya investasi terbatas
- Proses ini dapat menggunakan hampir semua residu yang dihasilkan selama berbagai proses di pabrik baja (termasuk lumpur dan kerak pabrik berminyak), sehingga memecahkan masalah yang meningkat dalam pengolahan limbah baja
- Off-gas yang berasal dari reaktor peleburan digunakan sebagai bahan bakar di RHF, dengan optimalisasi pemanfaatan energi secara keseluruhan. Ini menghasilkan pengurangan konsumsi energi yang efektif
Pabrik demonstrasi Redsmelt dengan proses reduksi peleburan dua langkah dibangun dan diuji di pekerjaan Piombino (Italia) untuk produksi logam panas. Pabrik percontohan ditugaskan pada tahun 2003. Dua langkah produksi di pabrik percontohan didasarkan pada pra-reduksi bahan bantalan besi dalam RHF dan peleburan DRI panas dalam konverter oxy-coal. Pabrik telah dirancang untuk memproses hingga 65.000 ton bahan pakan per tahun (secara kering) dengan output logam panas terukur 30.000 ton per tahun hingga 35.000 ton per tahun.
Teknologi proses Redsmelt telah dikembangkan untuk memenuhi permintaan yang terus meningkat akan alternatif pembuatan besi ramah lingkungan berbiaya rendah untuk rute tanur sembur tradisional di pabrik baja terintegrasi skala besar. Pabrik dengan proses ini dapat dirancang untuk kapasitas produksi 0,3 juta ton per tahun menjadi 1,0 juta ton logam panas per tahun. Proses ini terutama dirancang untuk dua aplikasi dasar yaitu (i) untuk mengubah produk sampingan yang mengandung besi dari pabrik menjadi logam panas yang berharga, dan (ii) untuk menghasilkan logam panas pada ukuran skala rendah-menengah (biasanya sekitar 500.000 ton per tahun), agar sesuai dengan konsep pabrik mini di mana logam panas digunakan sebagai pengganti skrap.
Konsep proses Redsmelt ditunjukkan pada Gambar 1.
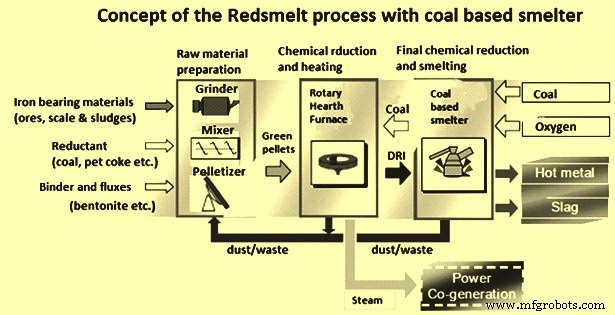
Gbr 1 Konsep proses Redsmelt
Proses
Prosesnya terdiri dari beberapa langkah seperti yang diberikan di bawah ini.
Persiapan bahan – Bahan bantalan besi yang digiling halus dan reduktor berbasis karbon, seperti batu bara atau kokas minyak bumi digunakan untuk pembuatan pelet hijau. Proses peletisasi membutuhkan bahan dengan granulometri sedekat mungkin dengan optimum yaitu 80% di bawah 100 mikro meter dan 100% di bawah 250 mikro meter. Campuran basah disiapkan dalam mixer di mana bahan-bahan ini diberi dosis secara hati-hati dengan penambahan air dan sedikit bahan pengikat (bentonit). Campuran yang disiapkan dipeletkan pada pelet disk dengan penambahan lebih banyak air. Pelet hijau yang dihasilkan kemudian disaring untuk menghilangkan fraksi berukuran kecil yang didaur ulang, sementara produk berukuran besar dimuat ke pengering sabuk logam.
Pengering pelet hijau – Dua tujuan pengering pelet hijau adalah (i) untuk menghindari masalah lengket pada sistem pengumpanan RHF, dan (ii) untuk mencegah pembusukan pelet hijau di RHF. Panas yang dibutuhkan untuk pengeringan pelet hijau disediakan oleh off-gas dari RHF. Hal ini juga menghasilkan peningkatan efisiensi energi secara keseluruhan dari proses tersebut.
Tungku perapian putar – Perapian melingkar yang berputar ditempatkan di ruang tungku yang ditutupi oleh atap tipe gantung. Dinding samping, atap, dan perapian RHF dilapisi tahan api untuk memungkinkan suhu operasi hingga 1450 derajat C. Pelet hijau kering dimasukkan ke dalam RHF melalui pengumpan bergetar dan didistribusikan ke seluruh perapian sebagai lapisan seragam sekitar 20 mm (satu hingga tiga pelet) di sekitar seluruh lebar perapian.
Bahan bakar gas dan udara pembakaran dimasukkan melalui beberapa pembakar samping yang dikelompokkan dalam tiga zona kontrol. Di setiap zona pembakaran, laju aliran bahan bakar dan udara dikontrol secara individual oleh sistem kontrol, untuk mendapatkan suhu dan komposisi gas (CO dan O2) yang diinginkan. Di zona 1 dan 2, udara sekunder dimasukkan melalui saluran masuk udara terpisah untuk pembakaran CO yang dilepaskan melalui proses reduksi. Pelet, setelah diisi, dipanaskan dengan cepat hingga mencapai suhu reduksi. Total waktu tinggal berkisar dari 10 menit hingga 18 menit di perapian RHF untuk mencapai tingkat metalisasi akhir 70 % hingga 90 %. Bergantung pada sifat bahan mentah yang berbeda, produksi spesifik DRI bervariasi dalam kisaran 60 kg/m² jam hingga 100 kg/m² jam.
Panas yang diperlukan untuk proses tersebut disediakan oleh empat sumber energi yang berbeda yaitu (i) pembakaran bahan bakar tambahan (gas kaya CO dari bejana reaktor NST), (ii) pembakaran CO yang dihasilkan dari reduksi oksida besi, (iii) pembakaran volatil yang dilepaskan oleh reduktor (batubara), dan (iv) pembakaran sebagian kecil dari reduktor itu sendiri (carbon burnout). Pemanfaatan sumber energi ini jelas bersaing dengan fenomena yang tidak diinginkan dari oksidasi ulang besi. Desain RHF secara khusus ditujukan untuk mengoptimalkan sistem gas-dinamis yang kompleks ini. Ini termasuk pembakar khusus dan saluran masuk udara, untuk injeksi udara pembakaran sekunder, yang mampu menyesuaikan tingkat turbulensi yang tepat di setiap zona dan di setiap tingkat ruang tungku. Faktor penting lainnya yang diperlukan untuk desain RHF yang baik adalah kebutuhan akan kontrol suhu yang sangat akurat di seluruh area perapian untuk mendapatkan sifat mekanik dan kimia yang konsisten dari pelet yang dihasilkan. Sistem burner biasanya dirancang untuk memenuhi semua target ini dan untuk menjamin pembentukan NOx minimum.
Pelet DRI yang dihasilkan dibuang melalui sekrup berpendingin air ke dalam saluran dan kemudian dipindahkan oleh konveyor sabuk logam kontinu (dirancang untuk transportasi DRI panas) ke tungku peleburan. Konveyor logam terbuat dari bahan tahan panas dan tertutup dalam poros kedap gas. Gas lepas yang meninggalkan RHF dan pengering dibuang ke atmosfer setelah pasca pembakaran, pengenceran udara, injeksi air, dan penghilangan debu melalui bag filter.
Sebagian energi gas buang RHF digunakan untuk mengeringkan pelet hijau. Energi gas buang juga digunakan untuk memanaskan awal udara pembakaran dan menyediakan panas untuk pengeringan bahan mentah. Di pembangkit skala besar, energi gas buang juga dapat digunakan untuk menghasilkan uap dengan boiler panas limbah.
Tungku peleburan – Dalam konsep proses Redsmelt asli, tungku busur terendam telah disertakan untuk peleburan dan reduksi akhir DRI. Namun dalam demonstrasi Redsmelt di Piombino, tungku peleburan NST telah digunakan untuk peleburan dan reduksi akhir DRI.
Tungku peleburan NST terdiri dari bejana reaktor vertikal yang tidak dapat dimiringkan. Bagian bawahnya (perapian) dilengkapi dengan lubang keran siphon yang serupa dengan yang digunakan dalam tanur sembur mini atau kubah (pemisahan terak dan logam panas dengan skimmer). DRI panas diisi oleh gravitasi dari atas oleh saluran berpendingin air, ditempatkan di tengah kapal. Tirai udara di sekitar ujung tombak meminimalkan sisa DRI langsung dengan aliran gas buang. Fluks dalam ukuran gumpalan dibebankan melalui port pengumpanan terpisah. Pendinginan bejana reaktor di area antarmuka terak dan terak logam dilakukan oleh elemen pendingin tembaga khusus. Atap bejana reaktor dan saluran off-gas terbuat dari dinding air dengan pengelasan pipa-ke-pipa.
Reaktor peleburan dilengkapi dengan dua tingkat tombak samping (tiga tombak per tingkat) untuk menyuntikkan oksigen dan batubara. Posisi dan orientasi tombak ini ditujukan untuk menghasilkan kondisi dinamis kimia dan fluida yang tepat untuk proses tersebut. Khususnya sistem ini dirancang untuk meningkatkan perpindahan panas antara zona pengoksidasi atas, di mana terjadi pasca-pembakaran gas CO, dan zona pereduksi, di mana reduksi langsung oksida besi dan reaksi endotermik lainnya berlangsung. Tombak atas menyuntikkan oksigen ke dalam tingkat emulsi untuk mempromosikan pasca-pembakaran di zona transisi sementara tombak bawah menyuntikkan oksigen dan batubara ke dalam bak logam panas. Dengan pengaturan ini, injeksi gas meningkatkan turbulensi terak yang cukup untuk membawa energi panas yang diperlukan dari zona eksotermik (pasca pembakaran) ke zona endotermik (peleburan) di mana reduksi langsung FeO terjadi. Batubara yang relatif kasar digunakan untuk mengurangi kehilangan karbon dan meningkatkan karburisasi logam panas. Logam panas yang dihasilkan dicor menjadi pig iron baik dalam cetakan pasir atau mesin pig casting tergantung pada kapasitas pabrik.
Bagian atas smelter memiliki atap berpendingin air untuk menghindari keausan tahan api karena suhu tinggi yang dihasilkan dari pasca pembakaran. Setelah itu, saluran berpendingin air mengumpulkan dan mendinginkan gas peleburan ke suhu yang tepat untuk memasuki sistem pendinginan. Off-gas didinginkan dan dibersihkan tanpa pembakaran dan dikirim ke penampung gas kecil untuk menstabilkan tekanannya dan kemudian digunakan di RHF sebagai bahan bakar burner.
Sistem pendingin tanpa gas – Saluran pengkondisian off-gas terdiri dari saluran pasca-pembakaran berlapis tahan api, pemadam gas dengan semprotan air, stasiun pengenceran udara, dan bag filter. Karena kombinasi RHF dan off-gas NST ke dalam sistem hisap umum, desain sistem yang tepat penting terutama saluran off-gas RHF.
Off-gas meninggalkan RHF pada suhu sekitar 1100 derajat C dan tidak sepenuhnya teroksidasi. Hal ini kemudian disampaikan ke saluran berlapis tahan api. Nozel yang cocok untuk injeksi udara segar ditempatkan setelah pintu masuk off-gas di saluran berlapis tahan api untuk membakar senyawa seperti CO, dan untuk membatasi suhu di bawah nilai di mana abu terbang mulai meleleh. Kondisi yang sesuai untuk mencapai pembakaran sempurna off-gas adalah (i) tingkat oksigen bebas lebih tinggi dari 3%, (ii) tingkat turbulensi tinggi, dan (iii) waktu tinggal di atas 1 detik. Nozel injeksi udara didistribusikan secara homogen di sepanjang saluran untuk meminimalkan pembentukan NOx.
Dibandingkan dengan off-gas yang meninggalkan RHF, off-gas yang berasal dari smelter memiliki suhu yang lebih tinggi (sekitar 1700 derajat C) dan tingkat pasca-pembakaran yang lebih rendah dengan kandungan senyawa yang tidak terbakar (CO+H2 lebih besar dari 30%) . Off-gas peleburan dialirkan ke saluran berpendingin air, di mana udara pasca-pembakaran disuntikkan. Parameter pembakaran (waktu tinggal, oksigen, turbulensi, dan suhu) sama dengan yang digunakan untuk perawatan off-gas RHF.
Gas RHF dan smelter pada suhu tidak lebih tinggi dari 950 derajat C kemudian dialirkan ke quencher yang sama, untuk mengurangi suhu asap menjadi sekitar 320 derajat C. Nozel tipe 'spill-back' memungkinkan nebulisasi penuh tetesan air dan pengurangan suhu gas yang cepat.
Tumpukan darurat yang dilengkapi dengan katup pemeras (membuka sendiri saat darurat) ditempatkan di bagian atas quencher. RHF primer, smelter primer dan udara dedusting sekunder akhirnya dikirim ke pabrik dedusting.
Lembar aliran proses Redsmelt dengan tungku busur terendam diberikan pada Gambar 2.
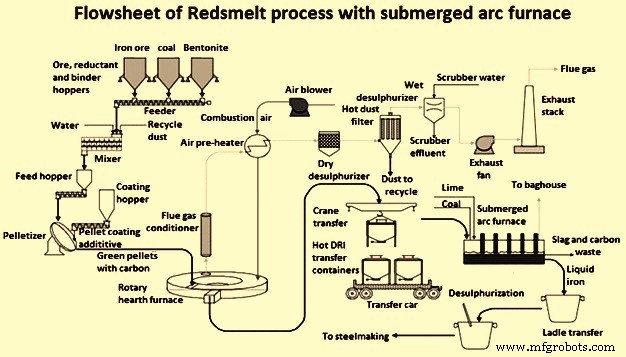
Gambar 2 Alur proses Redsmelt dengan tungku busur terendam sebagai unit peleburan