Karbonisasi Batubara untuk Produksi Coke
Karbonisasi Batubara untuk Produksi Coke
Karbonisasi batubara adalah proses dimana batubara dipanaskan dan produk volatil (cair dan gas) dikeluarkan, meninggalkan residu padat yang disebut kokas. Karbonisasi batubara melibatkan pemanasan batubara ke suhu tinggi baik tanpa adanya oksigen (O2) atau dalam jumlah kontrol O2. Produk sampingan berupa gas yang disebut sebagai gas oven kokas (COG) bersama dengan senyawa amonia (NH3), air, dan belerang juga dihilangkan secara termal dari batubara. Kokas yang tersisa setelah penyulingan ini sebagian besar terdiri dari karbon (C), dalam berbagai bentuk kristalografi, tetapi juga mengandung sisa-sisa mineral yang dimodifikasi secara termal dari berbagai mineral yang telah ada dalam batubara asli. Sisa-sisa mineral ini, biasanya disebut sebagai abu kokas, tidak terbakar dan tertinggal sebagai residu setelah kokas dibakar.
Sampai saat ini, karbonisasi batubara dianggap sebagai 'destilasi destruktif', tetapi dengan semakin pentingnya produk karbonisasi, frasa ini tidak lagi digunakan. Sekarang, karbonisasi batubara dianggap sebagai proses fisiko-kimia yang bergantung pada laju kokas, parameter operasi, sifat campuran batubara dan pengangkutan energi panas. Laju pemanasan batubara mempengaruhi kekuatan dan sifat pecahnya kokas. Untuk mencapai kualitas yang homogen, pemanasan kue batubara dalam oven kokas karena itu harus seragam di atas total panjang dan tinggi oven. Selain itu, tingkat migrasi lapisan plastik mempengaruhi tingkat tegangan termal pada massa yang dipadatkan kembali dan oleh karena itu, tingkat retakan.
Proses karbonisasi batubara dimulai pada awal abad ke-18 dengan mengkarbonisasi batubara kokas berkualitas baik di tumpukan di tanah, yang kemudian mengarah pada pengembangan oven sarang lebah dengan berbagai bentuk dan ukuran untuk memenuhi meningkatnya permintaan kokas keras yang dibutuhkan untuk peleburan besi.
Karbonisasi batubara dapat dilakukan pada tiga rentang suhu berikut.
- Karbonisasi suhu rendah biasanya dilakukan dalam kisaran suhu 500 derajat C hingga 700 derajat C. Dalam jenis karbonisasi ini, hasil produk cair lebih tinggi dan hasil produk gas lebih rendah. Coke yang dihasilkan memiliki volatile matter (VM) yang lebih tinggi dan bebas pembakaran.
- Karbonisasi suhu sedang dilakukan pada kisaran suhu sekitar 800 derajat C. Karbonisasi ini menghasilkan soft coke tanpa asap. Produk sampingan yang dihasilkan memiliki karakteristik yang mirip dengan karbonisasi suhu tinggi. Karbonisasi suhu sedang jarang dilakukan akhir-akhir ini.
- Karbonisasi suhu tinggi dilakukan pada suhu di atas 900 derajat C. Karbonisasi ini memberikan hasil produk gas yang lebih tinggi dan hasil produk cair yang lebih rendah. Karbonisasi ini menghasilkan kokas keras dari batu bara kokas.
Karbonisasi suhu rendah
Karbonisasi suhu rendah pada awalnya dikembangkan untuk menyediakan gas kota untuk penerangan jalan dan perumahan dan untuk produksi bahan bakar tanpa asap untuk pemanas rumah tangga dan industri. Tar produk sampingan secara ekonomi penting dan seringkali merupakan bahan baku penting untuk industri kimia atau disuling menjadi bensin, minyak pemanas, dan pelumas. Batubara yang disukai untuk karbonisasi suhu rendah biasanya adalah batubara lignit, batubara subbituminus, atau batubara bitumen yang sangat mudah menguap, yang ketika pirolisis dalam kisaran suhu 500 derajat C hingga 700 derajat C, menghasilkan arang berpori dengan reaktivitas yang biasanya tidak jauh lebih rendah. dibandingkan dengan batubara induknya. Arang reaktif ini (i) mudah dinyalakan dan digunakan sebagai bahan bakar tanpa asap atau sebagai bahan baku untuk proses gasifikasi, (ii) dicampur dengan batu bara untuk membuat umpan oven kokas, atau (iii) digunakan sebagai bahan bakar pembangkit listrik.
Tar yang dihasilkan selama karbonisasi suhu rendah jauh berbeda dibandingkan dengan karbonisasi suhu tinggi. Karbonisasi suhu tinggi cenderung menghasilkan terutama senyawa aromatik, sedangkan yang dihasilkan selama karbonisasi suhu rendah didominasi senyawa alifatik, oleh karena itu aplikasi penggunaan akhir yang berbeda dari produk samping tar. Hasil dan komposisi gas juga berbeda selama karbonisasi suhu rendah, dengan hasil gas sekitar 25% dari yang dihasilkan selama karbonisasi suhu tinggi, tetapi gas mengandung lebih banyak metana (CH4) dan lebih sedikit hidrogen (H2), sehingga memberikan nilai kalor yang lebih tinggi .
Aplikasi utama dari karbonisasi suhu rendah adalah membuat bahan bakar tanpa asap untuk digunakan di rumah dan boiler industri kecil di daerah yang memiliki kepadatan penduduk tinggi dan mengandalkan batubara sebagai bahan bakar, terutama batubara yang memiliki kandungan VM tinggi.
Karbonisasi suhu tinggi
Tujuan utama dari karbonisasi suhu tinggi adalah produksi kokas metalurgi untuk digunakan dalam tanur tinggi (BF) dan pengecoran. Beberapa kokas digunakan untuk produksi kalsium karbida (CaC2) dan karbon elektroda. Lebih dari 90% kokas yang dihasilkan digunakan di BF untuk melebur bijih besi untuk produksi logam panas.
Ada tiga jenis proses untuk karbonisasi batubara suhu tinggi. Ini adalah (i) oven sarang lebah, (ii) oven kokas pemulihan produk sampingan, dan (iii) oven kokas non-pemulihan/pemulihan panas.
Oven sarang lebah adalah struktur bata kubah sederhana di mana batubara dapat diisi melalui lubang di bagian atas dan kemudian diratakan melalui pintu samping untuk membentuk di atas lapisan dengan ketebalan sekitar 600 mm sampai 900 mm. Panas disuplai dengan membakar VM yang dilepaskan dari batubara, dan karbonisasi berlangsung dari atas ke bawah melalui muatan. Sekitar 5 ton hingga 6 ton batu bara dapat diisi, dan diperlukan waktu 48 jam hingga 72 jam untuk karbonisasi. Beberapa oven sarang lebah masih beroperasi karena perbaikan sistem dan penambahan boiler limbah panas untuk memulihkan panas dari produk pembakaran.
Oven kokas pemulihan produk sampingan pertama yang menghasilkan kokas BF atau kokas pengecoran yang memuaskan sebagai produk utama, dan tar, amonia, dan kemudian benzena sebagai produk sampingan, dibangun sekitar tahun 1856. Modifikasi desain terus berlanjut tetapi desain dasar oven ini, pada dasarnya oven coke modern, selesai pada tahun 1940-an. Oven coke (pemulihan produk sampingan) tipe slot horizontal, di mana suhu yang lebih tinggi dapat dicapai dan kontrol yang lebih baik atas kualitas kokas dapat dilakukan, telah menggantikan desain lain dan digunakan untuk kokas batubara bituminous.
Oven kokas produk sampingan modern terdiri dari ruang dengan panjang 15 meter (m) hingga 20 m, tinggi 6 m hingga sekitar 9 m, lebar 500 mm hingga 600 mm, dan memiliki ketebalan dinding sekitar 100 mm. Sejumlah ruang ini (dari 20 hingga 100) berselang-seling dengan sel serupa yang menampung bentuk cerobong pemanas sebagai baterai. Batubara, dihancurkan hingga 80% dikurangi 3 mm dengan ukuran atas 15 mm, dimuat di sepanjang bagian atas oven menggunakan mobil pengisi daya pada rel dan diratakan dengan batang yang dapat ditarik.
Pengoperasian setiap oven adalah siklus, tetapi baterai berisi oven dalam jumlah yang cukup besar untuk menghasilkan aliran gas oven kokas mentah yang pada dasarnya terus menerus. Oven individu diisi dan dikosongkan pada interval waktu yang kira-kira sama selama siklus kokas. Coking berlangsung selama 15 jam sampai 18 jam untuk menghasilkan BF coke. Selama periode ini, VM batubara tersuling sebagai COG. Waktu kokas ditentukan oleh campuran batubara, kadar air, kecepatan pembakaran, dan sifat kokas yang diinginkan. Ketika permintaan coke rendah, waktu coking dapat ditingkatkan menjadi 24 jam. Temperatur kokas umumnya berkisar dari 900 derajat C hingga 1100 derajat C dan dijaga pada kisaran yang lebih tinggi untuk menghasilkan kokas BF. Udara dicegah agar tidak bocor ke dalam oven dengan mempertahankan tekanan balik positif di saluran pengumpul. Oven dipertahankan di bawah tekanan positif dengan mempertahankan tekanan utama hidraulik tinggi sekitar 10 mm kolom air dalam baterai. Gas dan hidrokarbon yang berkembang selama distilasi termal dikeluarkan melalui sistem pengambilan dan dikirim ke pabrik produk sampingan untuk pemulihan.
Coking selesai ketika suhu pusat dalam oven sekitar 950 derajat C -1000 derajat C. Pada titik ini oven diisolasi dari listrik hidrolik dan setelah ventilasi yang tepat dari gas sisa, pintu dibuka untuk mendorong coke. Pada akhir periode kokas, massa kokas memiliki penyusutan volume tinggi yang mengarah pada pelepasan massa dari dinding untuk memastikan dorongan yang mudah. Coking terjadi dalam oven yang benar-benar tertutup rapat, dan ketika karbonisasi selesai, pintu oven dibuka dan sebuah alat pendobrak di satu sisi mendorong coke merah-panas ke dalam mobil pendingin.
Gas produk sampingan dan uap tar yang keluar dari oven kokas mengalami proses pemisahan untuk menghilangkan tar dari gas. Gas kemudian diolah untuk memulihkan NH3, sebagai amonium sulfat, sedangkan tar difraksinasi dengan distilasi menjadi tiga potongan minyak, yang ditetapkan sebagai minyak ringan, sedang (atau asam tar), atau berat. Gas tersebut, terutama campuran H2 dan CH4, memiliki nilai kalor yang baik dan digunakan sebagai bahan bakar.
Dalam kasus oven kokas non-pemulihan/pemulihan panas, energi panas gas buang diperoleh kembali dalam bentuk uap. Dalam proses pembuatan kokas dalam oven non-pemulihan, volatil yang terbentuk selama karbonisasi batubara tidak diperoleh kembali sebagai produk sampingan tetapi dibakar di dalam oven itu sendiri dengan adanya udara dalam jumlah yang terkendali dan panas volatil dari gas yang berkembang adalah digunakan untuk kokas massa batubara menjadi kokas dan dengan demikian tidak diperlukan pemanasan eksternal. Tingkat panas yang lebih tinggi penting digunakan untuk memecah hidrokarbon yang berpotensi mencemari menjadi senyawa penyusun yang mudah terbakar dan membakarnya sehingga menghindari polusi yang berpotensi berbahaya. Panas akibat pembakaran hanya sebagian dimanfaatkan selama proses dan keseimbangan panas dalam gas buang limbah dipulihkan untuk pembangkit energi.
Oven non-pemulihan umumnya berdesain horizontal dan beroperasi di bawah tekanan negatif tidak seperti oven produk sampingan yang beroperasi di bawah tekanan positif. Udara pembakaran primer, yang dimasukkan melalui port di pintu oven, membakar sebagian langsung volatil (Termasuk tar dan benzol) di ruang oven di atas batubara. Ini menghasilkan panas yang dibutuhkan untuk proses tersebut. Campuran minyak mentah dan gas sisa dialirkan melalui saluran vertikal di dinding samping ke sistem cerobong pemanas di bawah sol oven. Udara sekunder dimasukkan ke dalam satu-satunya cerobong asap, yang berjalan dengan cara serpentin di bawah lapisan batubara dan menyelesaikan pembakaran gas. Desain cerobong asap dan kontrol aliran udara memungkinkan laju kokas di bagian atas dan bawah unggun batubara menjadi seimbang. Karena suhu yang dihasilkan, semua hidro-karbon dan produk sampingan dibakar di dalam oven. Waktu pemanggangan bervariasi dari 48 jam hingga 72 jam tergantung pada desain oven kokas non-pemulihan. Gas panas mengalir di terowongan limbah ke generator uap pemulihan panas (HRSG), di mana uap bertekanan tinggi dihasilkan yang biasanya digunakan untuk pembangkit listrik.
Proses karbonisasi
Ketika batu bara dimasukkan ke dalam oven kokas panas, bagian batu bara itu, yang bersentuhan langsung dengan dinding, dipanaskan dengan sangat cepat. Ketika sekeringnya tercapai, lapisan tipis batubara yang dipanaskan melunak dan melebur. Reaksi destilasi destruktif berlangsung cepat di lapisan plastik, dengan evolusi produk volatil yang melimpah. Gas dan uap yang dapat terkondensasi terperangkap dalam massa plastik dan, ketika mengembang, cenderung membengkak. Ketika reaksi berlangsung dan suhu zona leburan meningkat, plastisitas muatan mulai menurun. Dengan pemanasan dan evolusi gas yang berkelanjutan, lapisan yang menyatu secara bertahap memadat kembali ke struktur kokas seluler yang khas. Karakteristik suhu dan tahapan selama karbonisasi batubara ditunjukkan pada Gambar 1, dan perkembangan lapisan plastik dan pergerakannya selama proses karbonisasi batubara ditunjukkan pada Gambar 2.
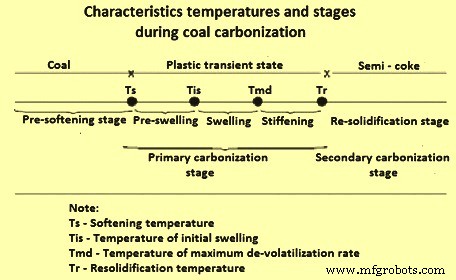
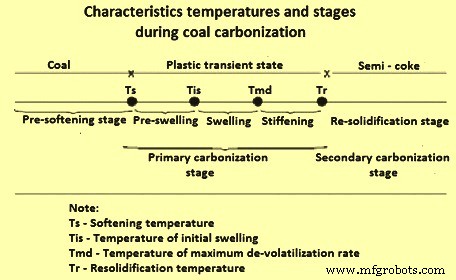
Gbr 1 Karakteristik suhu dan tahapan selama karbonisasi batubara
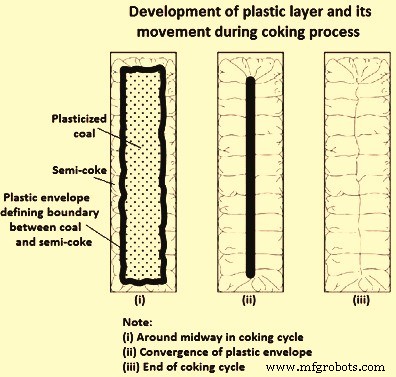
Gbr 2 Perkembangan lapisan plastik dan pergerakannya selama proses karbonisasi
Kokas yang tersisa setelah pemadatan zona plastik masih mengandung sejumlah besar VM, karena suhunya dinaikkan lebih tinggi lagi, reaksi destilasi destruktif berlanjut dengan evolusi gas dan sedikit tar. Reaksi akhir yang berlangsung dalam kokas tampaknya sebagian besar memisahkan H2 dari hidrokarbon berbobot molekul tinggi yang sangat kompleks yang menyusunnya. Dengan meningkatnya suhu kokas cenderung menarik diri dari dinding oven, dan retak susut berkembang, yang membentang dari dinding oven ke dalam menuju pusat massa kokas. Kedua zona plastik bergerak perlahan dari dinding oven yang berlawanan menuju satu sama lain dan akhirnya bertemu di tengah oven. Persimpangan zona muncul sebagai retakan vertikal yang memanjang melalui oven di pusat muatan. Saat oven didorong, kokas membelah secara vertikal di celah ini.
Saat zona plastis bergerak ke dalam, laju perjalanannya cenderung menurun karena meningkatnya jarak melalui mana panas akan dilakukan. Peningkatan panas sensibel yang dibawa oleh gas yang melewati kokas, dan setiap panas yang diserap dalam reaksi perengkahan yang terjadi dalam gas, juga cenderung memperlambat laju perjalanan zona. Suhu dan perilaku muatan yang berada di zona oven yang berbeda berbeda pada waktu pemasakan yang berbeda.
Transformasi batubara menjadi kokas terjadi saat batubara dipanaskan. Ketika keadaan sekering tercapai, lapisan batubara yang dipanaskan melunak dan menyatu. Dari sekitar 375 derajat C hingga 475 derajat C, batubara terurai membentuk lapisan plastik. Reaksi destilasi destruktif berlangsung cepat di lapisan plastik dengan evolusi produk yang mudah menguap. Pada sekitar 475 derajat C hingga 600 derajat C, ada evolusi yang nyata dari senyawa tar, dan hidrokarbon aromatik. Gas dan uap yang dapat dikondensasikan terperangkap dalam massa plastis dan, ketika mengembang, cenderung membengkak. Saat reaksi berlangsung dan suhu zona fusi meningkat, plastisitas batubara menurun. Dengan pemanasan dan evolusi gas yang berkelanjutan, lapisan yang menyatu secara bertahap memadat kembali menjadi semi-kokas yang memiliki struktur kokas seluler yang khas. Kokas pada tahap ini masih mengandung sejumlah besar VM. Ketika suhu meningkat lebih jauh di atas 600 derajat C, reaksi distilasi destruktif berlanjut dengan evolusi gas dan sedikit tar. Stabilisasi kokas terjadi saat suhu meningkat dari 600 derajat C menjadi 1100 derajat C. Hal ini ditandai dengan kontraksi massa kokas, perkembangan struktural kokas, dan evolusi H2 akhir. Pada tahap ini terjadi reaksi akhir. Reaksi-reaksi ini memisahkan H2 dari hidrokarbon berbobot molekul tinggi yang sangat kompleks. Dengan meningkatnya suhu, massa kokas menyusut dengan berkembangnya retak susut.
Mekanisme karbonisasi
Selama proses karbonisasi, batubara bubuk diubah menjadi kokas padat berpori, pecah-pecah, berwarna hitam keperakan. Secara mikroskopis, kokas terdiri dari matriks padat, inklusi organik dan anorganik dalam matriks, pori-pori dan celah mikro. Proses pengembangan struktur berpori dan tekstur mikro kokas berlangsung pada dasarnya dalam kisaran plastik. Struktur yang terbentuk dalam kokas oleh gelembung gas menempati hampir setengah dari volumenya dan mempengaruhi dua sifat kokas, kekuatan mekanik dan densitas curah.
Bahan padat yang membentuk dinding pori terdiri dari entitas optik-anisotropik yang biasanya diamati menggunakan mikroskop cahaya terpolarisasi (PLM). Tekstur mikro kokas mempengaruhi sifat kokas yang penting untuk penggunaannya di BF.
Selama proses karbonisasi, batubara metalurgi (coking) melunak menjadi plastis, terurai, mengembang, menggumpal dan akhirnya memadat kembali. Kisaran suhu plastik umumnya berkisar antara 350 derajat C sampai 500 derajat C. Jadi dalam proses karbonisasi, dua lapisan plastik vertikal terbentuk sejajar dengan dinding pemanas yang berjalan menuju pusat di mana mereka menyatu (Gbr 2). Selama karbonisasi beberapa batubara menghasilkan tekanan gas internal dan memberikan tekanan dinding terukur, terkadang sangat tinggi, pada dinding oven.
Selama proses karbonisasi, dua proses terjadi selama rentang suhu plastik. Struktur pori kokas berkembang dan batubara C menjadi terorganisir ke dalam bidang lapisan tipe grafit yang urutannya menghasilkan anisotropi optik kokas. Variasi dalam ukuran unit anisotropik menimbulkan komponen tekstur dalam kokas. Proporsi dari berbagai komponen yang ada menjadi komposisi tekstur kokas.
Ada beberapa penelitian mengenai mekanisme karbonisasi selama proses karbonisasi suhu tinggi, dan beberapa hipotesis mekanisme karbonisasi batubara telah diberikan. Dua di antaranya adalah mekanisme karbonisasi plastik dan mekanisme karbonisasi mesofasa.
Dalam mekanisme karbonisasi plastis batubara, dianggap ada tiga reaksi konversi berkelanjutan dari batubara menjadi kokas melalui fase plastis. Ketika batubara kokas dipanaskan di atas 350 derajat C tanpa adanya udara, bahan organik batubara mulai dekomposisi termal. Campuran gas, cair dan batubara lunak, yang merupakan dekomposisi termal dari batubara, disebut massa plastik. Batubara kokas melunak, meleleh, melebur, membengkak, dan bergabung bersama dalam tahap plastik. Ketika suhu dinaikkan menjadi 450 derajat C menjadi 550 derajat C, sebagian dari massa plastik berkembang dalam gas dan uap yang dapat dikondensasikan dan bagian lainnya membeku kembali menjadi semi-kokas. Dengan peningkatan lebih lanjut dalam suhu di atas 550 derajat C, bahan organik semi-kokas terurai dan mengembun lebih lanjut, CH4 dan H2 berkembang, lamela C dari semi-kokas meningkat terus menerus, akhirnya terbentuk kokas. Dua tahap utama yang diubah dari batubara menjadi kokas adalah fase karbonisasi menghasilkan massa plastik dan fase menyusut semi-kokas.
Dalam mekanisme karbonisasi oleh mesofasa, pembentukan anisotropik C dari lelehan isotropik batubara, pitch atau senyawa organik model yang dipilih pertama-tama dikaitkan dengan pengembangan fase khas kristal cair. Ketika batubara dikarbonisasi, massa plastik isotropik optik pertama kali terbentuk, dan kemudian membentuk kristal cair nematik pipih secara bertahap. Fase polimerik ini disebut mesofasa. Yaitu fase peralihan antara batubara fluida isotropik dan semi-kokas padat anisotropik yang pada akhirnya terbentuk dari mesofasa, dan memiliki sifat-sifat perantara antara padatan dan cairan. Jika fluiditas fase antara cukup tinggi, mesofasa segera bergabung menjadi satu unit yang lebih besar. Selama rentang peningkatan suhu, mesofasa terbentuk terus menerus, tumbuh dalam ukuran dan akhirnya saling menyentuh. Dengan demikian mesofasa dapat memadat dan mengubah dari batubara menjadi tekstur anisotropik optik dari kokas.
Sebuah perkembangan yang signifikan dalam memahami proses karbonisasi telah dibuat dengan penemuan mesofasa dalam tahap plastik karbonisasi yang mengarah ke karbon graphitizable, seperti yang diamati dengan mikroskop optik. Perkembangan partikel mesofasa sferis dari massa isotropik dan pertumbuhan progresif serta koalesensinya pada akhirnya membentuk struktur anisotropik telah ditetapkan dengan baik untuk prekursor seperti pitch. Pada dasarnya, selama proses karbonisasi, polimerisasi de-hidrogenatif molekul aromatik terjadi, dengan konsekuensi peningkatan berat molekul rata-rata. Struktur kokas akhir terkait dengan sifat mesofasa pada saat pemadatan dan ini, pada gilirannya, secara dominan bergantung pada sifat kimia bahan induk. Peningkatan kualitas kokas ditentukan oleh kualitas bahan baku induk yang menentukan tekstur optik dari kokas yang dihasilkan.
Berbeda dengan bahan seperti pitch, karbonisasi batubara menghasilkan mesofasa dalam bentuk banyak bola terdistorsi yang tidak menunjukkan koalesensi yang dapat diamati karena viskositasnya yang tinggi. Perbedaan perilaku ini dapat dikaitkan dengan efek penghambatan unsur-unsur seperti N2 (nitrogen), O2, dan S (sulfur) dan pengaruh materi inert partikulat dalam batubara.
Mekanisme dan faktor utama yang mempengaruhi pembentukan pori-pori di semi-coke telah menjadi subyek berbagai penelitian. Studi-studi ini telah menunjukkan bahwa struktur pori kokas sangat ditentukan dalam kisaran suhu plastis dari proses karbonisasi. Selama penelitian, telah diamati bahwa pori-pori awalnya muncul pada partikel besar pada suhu dekat titik pelunakan, sedangkan partikel ukuran sedang menjadi berpori pada suhu yang lebih tinggi. Tidak ada pembentukan pori yang terdeteksi pada suhu berapa pun di dalam partikel berukuran kurang dari 125 mikro meter (mikron). Peningkatan suhu menyebabkan peningkatan baik dalam jumlah dan ukuran pori-pori. Lebih banyak partikel telah diamati memiliki pori-pori dan partikel besar menjadi multi-pori. Dengan meningkatnya suhu, partikel menjadi lebih bulat dan membengkak ke dalam rongga antar-partikel.
Dalam kasus batubara dengan fluiditas nol, tahap yang disebutkan di atas menandai akhir dari perubahan yang diamati. Namun, untuk batubara dengan fluiditas yang lebih tinggi, peningkatan suhu, yang pada akhirnya mencapai suhu kontraksi maksimum, menghasilkan pengembangan partikel yang lebih besar dan konsentrasi partikel kecil dalam ruang kosong yang semakin berkurang. Pembengkakan batubara yang lebih cair berlanjut sampai semua partikel kecil tergabung dalam dinding sel yang meluas dari partikel yang lebih besar sehingga menyebabkan hilangnya identitas terpisah mereka. Di atas suhu fusi lengkap ini, ukuran pori rata-rata meningkat mencapai nilai puncak sebelum akhirnya jatuh ke ukuran yang praktis tidak berubah pada suhu yang lebih tinggi. Peningkatan jumlah pori-pori dengan suhu terganggu oleh minimum transisi pada suhu yang sesuai dengan ukuran pori maksimum. Ukuran pori-pori besar ini dikurangi sebelum suhu pemadatan ulang, sehingga meninggalkan struktur yang lebih koheren. Pertumbuhan pori-pori kecil hampir bulat dan fusi matriks di dekat suhu ini umumnya menghasilkan pembentukan pori-pori yang saling berhubungan.
Di atas suhu re-solidifikasi, perubahan yang tidak signifikan diamati selain dari sedikit pengurangan ukuran pori rata-rata. Pemadatan struktur yang sepenuhnya menyatu yang terjadi di dekat suhu pemadatan ulang telah membangkitkan minat yang besar. Penjelasan untuk ini adalah bahwa ekspansi besar dari zona yang sedikit lebih dingin dapat menekan lapisan pemadatan terhadap semi-kokas yang lebih kaku. Interkoneksi pori-pori yang mungkin terjadi pada tahap ini dapat memfasilitasi proses ini. Penjelasan ini selanjutnya didukung oleh pengamatan perkembangan anisotropi dalam bentuk pori, dengan dimensi terbesar terletak di sepanjang isoterm suhu.
Studi lebih lanjut tentang pengaruh kerapatan muatan dan ukuran partikel pada perkembangan struktur pori menunjukkan bahwa ukuran pori rata-rata dan dinding pori mencapai nilai maksimum dalam zona plastis. Temuan baru dijelaskan oleh saran dari dua proses lebih lanjut yaitu (i) pecahnya beberapa dinding pori tipis selama tahap ekspansi pasca fusi, dan (ii) nukleasi pori sekunder yang terjadi pada suhu yang lebih tinggi selama proses pemadatan. Telah ditunjukkan bahwa peningkatan densitas muatan mengurangi porositas, terutama ukuran pori rata-rata dari kokas yang dihasilkan, sedangkan ukuran dinding pori rata-rata menunjukkan variasi yang dapat diabaikan. Pengaruh kerapatan muatan dikaitkan dengan pembatasan ekspansi sepanjang arah horizontal yang tegak lurus terhadap dinding oven. Tidak ada bukti yang ditemukan untuk setiap variasi sistematis dalam struktur pori kokas yang dihasilkan dari variasi distribusi ukuran partikel batubara dalam kisaran yang dipertimbangkan.
Penyelidikan telah dilakukan untuk mempelajari secara mikroskopis transformasi batubara menjadi kokas. Dalam penelitian ini telah dilakukan penelitian mengenai morfologi lapisan plastis sebagai fungsi dari rank batubara. Telah diamati bahwa untuk batubara dengan kandungan VM dalam kisaran 25% sampai 30%, langkah pertama dalam transformasi adalah pembentukan medium kontinu dari partikel batubara deformasi kental yang ditandai dengan tidak adanya gelembung. Tahap kedua adalah devolatilisasi yang terlihat dengan adanya zona yang sangat porous. Kesimpulan dari penelitian ini adalah bahwa pembentukan pori-pori dimulai secara tiba-tiba ketika batas-batas partikel individu tidak dapat diidentifikasi. Selain zona lebur yang tidak memiliki pori-pori, ada satu lagi yang kaya akan pori-pori dengan dinding yang sangat tipis yang digambarkan sebagai zona buih.
Dalam studi serupa, perbedaan antara batubara peringkat tinggi dan menengah telah diperhatikan. Telah diamati bahwa, dalam kasus batubara VM menengah, selama re-solidifikasi, pemadatan gelembung mendominasi pembentukannya sementara yang sebaliknya terjadi selama zona fluiditas maksimum sebelumnya. Terjadi perpindahan massa di lapisan plastik dari daerah fluiditas maksimum ke semi-kokas yang dinyatakan dalam porositas tinggi yang diukur di tengah lapisan plastik. Dalam kasus batubara peringkat tinggi, tidak ada maksimum yang serupa yang diamati dan ini menunjukkan bahwa untuk batubara ini mekanisme yang berbeda untuk menghilangkan gelembung mungkin ada.
Tekanan karbonisasi
Tekanan karbonisasi yang dikembangkan selama karbonisasi dinyatakan sebagai gaya yang diberikan pada dinding dan diukur dengan alat yang sesuai dan disebut tekanan dinding. Ini adalah fenomena yang menjadi penting dengan penggunaan dinding berdinding ganda, vertikal, oven kokas tipe slot. Dalam oven sarang lebah bundar, batubara dapat dengan bebas mengembang ke atas dan dengan demikian pembengkakan muatan diakomodasi oleh ekspansi bebas ini. Sebaliknya dalam oven tipe slot, ekspansi batubara secara horizontal ke dinding yang dipanaskan dibatasi.
Telah ditetapkan bahwa beberapa batubara dapat merusak dinding oven kokas karena tekanan berlebihan yang terjadi selama karbonisasi atau kontraksi kokas yang tidak mencukupi pada akhir proses karbonisasi. Masalah ini akhir-akhir ini menjadi penting karena pemanasan awal batubara dan penerimaan luas baterai tinggi yang meningkatkan densitas muatan batubara, sehingga mempengaruhi tekanan kokas, kontraksi dan umur oven kokas. Pengaruh tekanan yang timbul selama karburisasi batubara dalam bentuk kejadian yang tidak diinginkan dari dinding yang terdistorsi lebih terlihat pada oven yang lebih tinggi.
Banyak faktor telah ditemukan untuk mempengaruhi besarnya tekanan karbonisasi. Faktor-faktor ini dapat dipisahkan menjadi tiga kategori besar secara spesifik (i) karakteristik yang melekat pada batubara, (ii) persiapan batubara dan sifat fisik, dan (iii) kondisi operasi oven.
Apakah suatu tekanan berlebihan atau tidak, tidak hanya bergantung pada tekanan yang diberikan tetapi juga pada tekanan yang dapat ditahan oleh dinding oven. Oleh karena itu, berbagai upaya telah dilakukan untuk menilai kekuatan dinding oven kokas. Persyaratan kekuatan dinding sebagian besar diatur oleh tekanan kokas tidak seimbang puncak yang diberikan pada dinding selama proses karbonisasi. Tekanan yang tidak seimbang ini menyebabkan pembengkokan dinding dalam arah horizontal yang perlu distabilkan oleh beban gravitasi vertikal, termasuk berat atap dan dinding, karena sambungan pada dinding tidak memiliki kekuatan tarik yang konsisten.
Batas yang sangat rendah membatasi fleksibilitas dalam memilih sumber batubara, campuran batubara dan kondisi karbonisasi. Dalam sebuah penelitian, yang membandingkan hasil beberapa ratus batu bara yang dikarbonisasi dalam oven dinding bergerak dan, dengan mempertimbangkan perilaku batu bara ini dalam oven komersial, menetapkan batas keamanan berikut untuk batu bara yang dikarbonisasi dalam oven kokas.
- Batubara dengan tekanan lebih besar dari 0,14 kilogram per sentimeter persegi (kg/cm persegi) berbahaya.
- Batubara yang memiliki tekanan lebih besar dari 0,1 kg/cm persegi dapat berbahaya jika dikarbonisasi secara teratur dalam oven yang lebih tinggi dari 3 meter.
- Batubara yang memberikan tekanan kurang dari 0,1 kg/cm persegi aman digunakan.
Studi telah menunjukkan bahwa defleksi elastis dinding oven komersial hingga 1,25 mm dapat terjadi tanpa munculnya retakan. Di luar titik itu, defleksi lebih lanjut tidak segera terjadi dan keretakan terjadi.
Pada 1960-an dan 1970-an, konstruksi oven kokas tinggi (tinggi 6 m ke atas) menjadi lazim. Oven ini dioperasikan dengan asumsi bahwa tekanan kokas di bawah 0,14 kg/cm2 aman. Hasilnya adalah bahwa dalam beberapa kasus oven ini mengalami kerusakan refraktori awal yang serius. Telah dilaporkan bahwa baterai setinggi 6 m telah mengalami kerusakan progresif dan harus dimatikan setelah kurang dari lima tahun beroperasi. Penyelidikan untuk menentukan penyebab kegagalan prematur termasuk analisis struktural dari dinding setinggi 6 m. Sebuah studi matematis telah dilakukan pada dinding oven setinggi 6 m yang diberi tekanan dari satu sisi. Dari analisis ini, tekanan lateral yang tidak seimbang yang dapat menyebabkan keruntuhan telah dihitung hanya di atas 0,12 kg/cm2. Dengan mempertimbangkan faktor beban hidup yang direkomendasikan sebesar 1,7 serta kemudahan servis relatif terhadap retak, telah direkomendasikan bahwa tekanan lateral tidak seimbang yang diizinkan tidak melebihi 0,07 kg/cm persegi.