Memahami Injeksi Batubara Serbuk di Blast Furnace
Memahami Injeksi Batubara Serbuk di Blast Furnace
Injeksi batubara bubuk (PCI) adalah teknologi mapan untuk produksi logam panas (HM) dalam tanur tinggi (BF). Ini dipraktikkan di sebagian besar BF dan semua BF baru biasanya dibuat dengan kemampuan PCI. Komposisi dan sifat batubara yang digunakan untuk injeksi dapat mempengaruhi operasi, stabilitas dan produktivitas BF, kualitas HM, dan komposisi gas BF. Batubara yang digunakan untuk PCI dijelaskan dalam artikel di bawah tautan ‘http://www.ispatguru.com/coal-for-pulverized-coal-injection-in-blast-furnace/’.
Aspek penting dari sistem PCI meliputi persiapan batubara, penyimpanan dan distribusinya untuk memastikan pasokan batubara yang seragam ke setiap tuyere tanpa fluktuasi dalam laju pengiriman batubara dan pembakarannya melalui desain tombak dan injeksi oksigen (O2).
Persiapan batubara
Penghancuran batubara dilakukan dalam satu atau beberapa pabrik penggilingan (pulverizer) tergantung pada kebutuhan. Penggilingan dan pendistribusian batubara ke tombak injeksi merupakan biaya operasi yang besar. Batubara yang direklamasi dari penyimpanan batubara disaring untuk menghilangkan material asing dan setiap gumpalan besar batubara dihancurkan. Batubara kemudian diumpankan ke pabrik di mana ia dihaluskan dan dikeringkan. Batubara dengan ukuran yang dibutuhkan diangkut keluar dari pabrik melalui aliran gas panas, dikumpulkan dalam bag filter dan dibawa ke tempat penyimpanan. Penggilingan dan pengangkutan dilakukan di bawah atmosfer inert untuk meminimalkan risiko penyalaan partikel batubara kering. Distribusi ukuran partikel yang dihasilkan dari batu bara yang dihancurkan mempengaruhi kemampuan penanganannya dalam peralatan transportasi pneumatik dan, pada laju injeksi yang tinggi, sifat mudah terbakarnya.
Pulverizer menggiling batubara menjadi salah satu dari dua fraksi ukuran yaitu (i) batubara bubuk dimana sekitar 70% sampai 80% dari batubara berada di bawah 75 mikron (mikro meter) dan sisanya di bawah 2 mm, dan (ii) batubara granular yang memiliki ukuran atas 2 mm hingga 3 mm dengan batas 2% batubara di atas 2 mm dan 20% hingga 30% di bawah 75 mikron. Sistem yang menginjeksi ukuran batubara ini disebut granular coal injection (GCI). Penggilingan yang lebih kasar memiliki keuntungan dari biaya penggilingan dan pengeringan yang lebih rendah dengan batu bara giling yang lebih mudah ditangani. Grinding yang lebih halus memiliki burnout yang lebih tinggi di raceway. PCI adalah teknologi yang lebih populer daripada GCI.
Kehalusan batubara dapat divariasikan dalam pulverizer dengan sejumlah ukuran yang mencakup memvariasikan laju umpan batubara, pengaturan pengklasifikasi, atau laju aliran udara. Meskipun pabrik dapat disetel agar sesuai dengan batubara tertentu untuk menghasilkan ukuran yang dibutuhkan, ini tidak praktis dalam kasus campuran batubara di mana sejumlah besar batubara digunakan. Dalam kasus seperti itu, beberapa konstituen batubara mungkin tidak mencapai kehalusan yang dibutuhkan.
Salah satu fungsi pulverizer adalah untuk menghilangkan sebanyak mungkin uap air dari batubara. Pengeringan diperlukan karena kelembaban menyebabkan masalah aliran bebas baik dalam sistem transportasi pneumatik dan di tempat penyimpanan. Juga, kelembaban perlu diminimalkan karena energi tambahan diperlukan untuk menghilangkannya di BF dan injeksi kelembaban meningkatkan laju reduktor. Selain itu, batubara dengan kadar air yang lebih tinggi mengkonsumsi lebih banyak daya dalam pulverizer selama penggilingan dan menurunkan throughput.
Penguapan kelembaban permukaan batubara mencegah masalah aglomerasi di dalam pulverizer karena batubara dengan kelembaban tinggi dan kandungan liat sebagian besar cenderung lengket. Oleh karena itu, biasanya perlu untuk mengurangi kadar air total batubara ke sekitar tingkat kelembaban keseimbangan untuk mengurangi masalah penanganan di dalam pabrik dan tempat penyimpanan. Kadar air batubara yang keluar dari pabrik adalah dua pertiga dari kadar air keseimbangan. Kelembaban keseimbangan batubara bervariasi dengan peringkat, komposisi maseral, dan kadar abu.
Penting untuk memastikan bahwa batu bara digiling hingga kehalusan yang diinginkan dengan keausan minimum pada bagian pulverizer dan dengan konsumsi daya paling sedikit untuk menurunkan biaya pengoperasian. Keausan mempengaruhi penghentian dan perawatan pulverizer. Sifat batubara yang mempengaruhi keausan meliputi kandungan abu dan komposisi, distribusi ukuran partikel, kelembaban, dan densitas curah. Kadar air yang lebih tinggi dari batubara mempercepat keausan karena efek gabungan dari keausan dan korosi. Mineral abrasif (keras) dalam abu batubara antara lain silika (SiO2) dan pirit (FeS2). Selain memakai elemen penggilingan, mineral abrasif juga dapat mengikis pipa dan saluran. Tes yang paling umum digunakan untuk mengevaluasi sifat abrasi batubara adalah 'Abrasion Index' (AI). Biasanya batubara dengan AI tinggi diperkirakan akan menyebabkan tingkat keausan yang lebih tinggi.
Pengurangan konsumsi daya pabrik menurunkan biaya operasi. Konsumsi daya dan kapasitas (throughput) pabrik tergantung pada desainnya, pengaturan pabrik, kehalusan yang diperlukan, dan sifat batubara. Semakin tinggi pengurangan ukuran batubara yang dibutuhkan, semakin besar konsumsi daya yang dibutuhkan. Tingkat kehalusan batubara yang lebih tinggi membutuhkan peningkatan kapasitas pabrik yang mungkin juga diperlukan saat menggiling batubara yang sulit.
Properti batubara utama yang memiliki pengaruh utama pada konsumsi daya dan kapasitas pabrik adalah kekerasan, yang ditentukan oleh 'Hardgrove grinding index' (HGI). Biasanya, semakin tinggi HGI, semakin mudah untuk menggiling batubara, dengan konsumsi daya yang lebih rendah dan throughput yang lebih tinggi. Jika kapasitas desain pulverizer membatasi laju PCI, maka dimungkinkan untuk meningkatkan laju injeksi dengan beralih ke batubara yang lebih lunak. Meningkatkan persentase bahan volatil rendah (VM), batubara lunak bernilai kalori tinggi (CV) di VM tinggi, campuran batubara keras membantu meningkatkan kapasitas pulverizer, serta menurunkan tekanan ledakan di BF dan meningkatkan konsumsi batubara.
Komposisi maseral juga mempengaruhi penggilingan. Secara umum, batubara vitrinit yang lebih tinggi cenderung memiliki kebutuhan energi penggilingan yang lebih rendah daripada batubara vitrinit yang lebih rendah karena vitrinit lebih mudah digiling daripada inertinit dan liptinit. Efek peringkat menurun di atas reflektansi sekitar 1,6 di mana energi kerusakan yang dibutuhkan untuk vitrinit dan inertinit hampir sama.
Batubara umumnya dicampur untuk mengoptimalkan kekuatan relatif. Namun, campuran tidak berperilaku sebagai rata-rata komponennya, tetapi dapat dipengaruhi secara tidak proporsional oleh satu batubara dengan karakteristik bermasalah. Penggilingan preferensial dari batubara yang lebih lunak terjadi ketika campuran dua batubara yang HGI-nya berbeda lebih dari 20 dihancurkan. Penghancuran campuran batubara 'keras' dan 'lunak' telah menunjukkan bahwa karakteristik yang buruk dari batubara penyusun cenderung mendominasi campuran, dengan kinerja pulverizer yang lebih mirip dengan batubara yang lebih keras. Penggilingan preferensial dari maseral yang lebih lembut juga dapat terjadi saat penggilingan campuran. Batubara yang mengandung lempung yang mengembang dapat menyerap uap air setelah meninggalkan pulverizer dan menjadi dingin. Bahkan ketika hadir sebagai komponen campuran, batubara tersebut dapat menyebabkan penyumbatan pada sistem injeksi.
Sistem injeksi batubara
Sistem injeksi secara pneumatik mengangkut dan mengukur bubuk batu bara dari tempat penyimpanan melalui bejana injeksi, di mana ia diberi tekanan hingga atau di atas tekanan BF, ke tombak injeksi tuyere. Tombak menyuntikkan batubara dalam jumlah yang sama melalui tuyeres, yang disusun secara simetris di sekitar keliling BF. Faktor penting dalam desain sistem distribusi adalah memastikan pasokan batubara yang seragam ke setiap tuyere tanpa fluktuasi dalam rute pengiriman batubara. Setiap gangguan dalam pasokan batubara dapat dengan cepat menyebabkan masalah serius. Semakin tinggi tingkat injeksi, semakin serius konsekuensi dari gangguan yang tidak direncanakan.
Setidaknya dua kapal injeksi diperlukan untuk menyediakan aliran batubara terus menerus ke BF. Pada dasarnya terdapat dua susunan yang berbeda dari vessel ini yaitu (i) susunan serial dimana vessel bagian atas secara berkala mengisi ulang vessel bagian bawah, yang selalu dijaga di bawah tekanan, dan menginjeksikan batubara, dan (ii) susunan parallel dimana kedua vessel menginjeksi secara bergantian. dengan operasi yang tumpang tindih untuk mempertahankan injeksi batubara selama periode pergantian.
Penting untuk mengontrol jumlah batubara yang disuntikkan. Oleh karena itu, bejana injektor ditimbang secara terus menerus dan laju aliran batubara dikontrol dengan hati-hati. Masalah penanganan batu bara bubuk di tempat penyimpanan yang memberi makan bejana injeksi dan jaringan pipa disebabkan oleh jumlah uap air dan partikel ultrafine, dan keberadaan lempung di dalam batu bara. Pemanas dan/atau insulasi eksternal mungkin diperlukan untuk mengurangi kemungkinan penyumbatan nampan karena kondensasi uap air yang dapat terjadi di bagian dalam dinding nampan. Di beberapa tempat, nitrogen (N2) dihembuskan melalui bantalan aerasi di bagian bawah tangki injeksi perantara untuk memastikan aliran bebas saat batu bara bubuk dipindahkan ke tangki injeksi bawah.
Batubara dari kapal injeksi umumnya diangkut oleh (i) pipa individu ke setiap tuyere di mana jumlah batubara dikontrol secara independen dan diisi di setiap pipa, (ii) pipa umum ke distributor yang berdekatan dengan BF dalam hal ini, distributor membagi batubara secara merata ke dalam masing-masing pipa yang menuju ke setiap tuyere. Keuntungan dengan sistem ini adalah jarak antara pabrik persiapan batubara dan BF bisa lebih lama dibandingkan dengan sistem pipa individu.
Perbedaan dalam rute pipa ke tuyer dan pemisahan batubara yang tidak merata pada titik pemisahan dapat mengakibatkan pengumpanan yang tidak merata ke tuyer. Ketidakseimbangan juga dapat menyebabkan keausan yang tidak merata pada pipa dan distributor.
Bergantung pada rasio batubara terhadap gas pembawa, batubara diangkut secara pneumatik dari bejana injeksi ke tuyer baik dalam fase encer, atau fase padat. Pemuatan gas pembawa dalam kasus sistem fase encer untuk batubara biasanya sekitar 10 kg batubara per kg gas pembawa, dan kecepatan gas pembawa sekitar 15 meter/detik (m/s) hingga 20 m/s. Gas pembawa biasanya merupakan campuran N2 dan udara dengan udara terkompresi ditambahkan ke pipa di bawah bejana injeksi. Dalam kasus sistem fase padat, pembebanan sekitar 40 kg sampai 80 kg batubara per kg gas pembawa, dan kecepatan gas pembawa sekitar 1 m/s sampai 5 m/s. Gas pembawa biasanya N2 atau campuran N2 dan udara.
Kecepatan gas pembawa selalu lebih tinggi dari kecepatan pengangkutan minimum untuk mencegah penyumbatan. Kecepatan minimum ini tergantung pada sejumlah parameter yang meliputi tekanan sistem dan diameter pipa. Variabel-variabel ini saling berinteraksi. Kecepatan rendah dalam sistem fase padat berarti rendahnya keausan pipa dan komponen, sedangkan kecepatan pengangkutan yang tinggi dari sistem fase encer dapat menyebabkan keausan, terutama pada belokan pipa. Laju keausan ditentukan oleh kekerasan, bentuk dan kecepatan partikel batubara. Sifat batubara juga mempengaruhi keausan. Melapisi bagian pipa yang rentan aus dengan, misalnya, bahan elastomer uretan memberikan ketahanan abrasi, serta memperlambat penumpukan butiran halus yang dapat menyebabkan penyumbatan. Sifat batubara yang berhubungan dengan penyumbatan saluran transfer adalah kadar air dan mineral lempung.
Kelembaban yang tinggi pada batubara dan campurannya dapat menimbulkan masalah. Jadi batas kelembaban yang ketat pada batubara tanah diterapkan. Kehadiran lempung, yang membengkak dengan adanya air, dapat menyebabkan masalah, terutama jika ada penurunan tekanan dalam sistem konveyor, dan/atau jika ada partikel ultrahalus. Ketika kandungan halus (kurang dari 5,8 mikron) dari batubara yang dihancurkan meningkat, penurunan tekanan dalam sistem konveyor meningkat. Jika penurunan tekanan melebihi nilai tertentu, yang terkait dengan desain pembangkit, maka penyumbatan dapat terjadi. Penyumbatan pipa terjadi karena penumpukan endapan di tikungan pipa yang biasanya terkait dengan sifat lunak batubara (distribusi ukuran partikel lebih halus). Saat menyuntikkan batubara, batubara ultrafine (kurang dari 10 mikron) memulai proses dengan menempel pada dinding siku, dan setelah permukaan kasar terbentuk maka partikel yang lebih besar mulai menempel. Selain itu, penggilingan preferensial dari batubara yang lebih lembut dalam campuran batubara dapat menghasilkan proporsi partikel ultrafine yang tinggi, yang menyebabkan penyumbatan.
Penyumbatan dapat dicegah dengan perbaikan tata letak pipa dan sistem distribusi dan, dalam beberapa kasus, dengan menyesuaikan sistem preparasi (seperti penghancur batubara) untuk menghasilkan ukuran partikel yang lebih kasar. Sistem injeksi biasanya memiliki prosedur untuk mendeteksi dan membersihkan penyumbatan karena merupakan fenomena umum. Jalur pengiriman termasuk port pembersihan di mana penyumbatan dibersihkan, biasanya dengan udara bertekanan tinggi. Pengujian yang sederhana dan praktis diperlukan untuk menilai kemampuan alir dan kemampuan penanganan batu bara bubuk dan campuran batu bara. Hal ini memungkinkan bahan yang sulit diidentifikasi sebelum digunakan.
Tombak injeksi menyuntikkan batubara ke dalam sumpitan yang mengarah ke tuyere. Partikel segera dipanaskan oleh ledakan panas, menyala, menjadi gas dan terbakar. Desain dan penempatan lance mempengaruhi efisiensi pembakaran batubara. Sebelumnya tombak digunakan untuk menjadi tombak baja lurus yang diposisikan pada atau dekat dengan antarmuka tuyere/pipa tiup. Desain yang menggabungkan injeksi O2 langsung ke aliran partikel batubara (oxy-coal lance) dan/atau cara menghasilkan lebih banyak turbulensi di ujung tombak telah dikembangkan untuk meningkatkan efisiensi pembakaran. Ini termasuk (i) tombak koaksial (di mana batubara disuntikkan melalui pipa bagian dalam dan O2 melalui anulus sekitarnya), (ii) tombak dispersif tinggi, (iii) tombak miring, (iv) slit lance, (v) eksentrik (non -konsentris) tombak ganda, dan (vi) tombak berputar.
Pemanasan awal batubara untuk meningkatkan efisiensi pembakaran juga dilakukan. Masalah yang terjadi ketika batubara pertama kali diperkenalkan, seperti penyumbatan tombak dan tuyere dan pencairan ujung tombak, sebagian besar telah diatasi. Penyumbatan sebagian besar disebabkan oleh batubara yang dipanaskan sampai suhu di mana mereka menjadi lengket dan menempel pada permukaan tombak injeksi dan tuyeres. Deposisi abu diminimalkan dengan memanfaatkan batubara dengan suhu fusi abu (AFT) yang tinggi. Untuk semua tujuan praktis, AFT harus 50 derajat C lebih tinggi dari suhu ledakan panas. Tombak juga bisa ditancapkan jika arang dengan fluiditas cake tinggi di dekat ujung tuyere. Hal ini dapat diatasi dengan menghindari batubara dengan indeks caking tinggi, atau dengan meningkatkan laju aliran.
Menempatkan tombak injeksi lebih dekat ke tuyere mengurangi tingkat pelampiasan abu di sumpitan. Pemanfaatan tombak koaksial berpendingin udara membantu mencegah penyumbatan dan erosi, dan dapat memperpanjang umur tip. Laju aliran udara pendingin harus diminimalkan untuk mengurangi efek pendinginannya pada pembakaran batubara. Namun, penyumbatan tombak masih bisa sering terjadi. Ada prosedur yang ditetapkan untuk mendeteksi dan membersihkan penyumbatan ini sebelum dapat menyebabkan masalah.
Penggunaan paduan yang berbeda untuk tombak injeksi dan membatasi suhu ledakan panas juga mempengaruhi pencairan ujung tombak. Daya tahan tombak merupakan pertimbangan operasional yang penting karena tombak akan terbakar seiring waktu.
Pembakaran batubara
Raceways adalah daerah vital dari BF meskipun volume totalnya biasanya tidak melebihi 1% dari volume bagian dalam BF. Mereka memasok proses dengan panas dan zat pereduksi. Injeksi batubara pasti mempengaruhi kondisi raceway yang, pada gilirannya, memiliki konsekuensi di luar raceway. Partikel yang tidak terbakar meninggalkan raceway dapat menyebabkan masalah operasional seperti penurunan permeabilitas, distribusi gas dan suhu yang tidak diinginkan, erosi kokas yang berlebihan, dan peningkatan sisa arang. Jumlah arang yang tidak terbakar meningkat dengan meningkatnya laju injeksi. Dengan demikian, perilaku pembakaran dan gasifikasi dari batubara yang diinjeksikan di raceway merupakan elemen penting untuk operasi BF yang stabil. Sangat jelas bahwa BF dapat mengkonsumsi lebih banyak batubara yang disuntikkan daripada yang dibakar di dalam raceway karena bahan yang tidak terbakar dikonsumsi di tempat lain di tungku.
Pembakaran batubara dalam BF telah dipelajari secara luas. Studi telah dilakukan dengan menggunakan peralatan skala bangku seperti analisis gravimetri termal (TGA), tungku tabung jatuh (DTFs) dan reaktor wire mesh (WMRs). Teknik-teknik ini tidak sepenuhnya mensimulasikan kondisi di dalam raceway. Waktu tinggal partikel batubara yang dihaluskan dalam DTF, sebagai contoh, adalah orde detik sedangkan sekitar milidetik dalam jalur BF. Oleh karena itu, teknik ini biasanya digunakan untuk memberikan evaluasi komparatif dari berbagai jenis batubara.
Pendekatan lain yang diikuti adalah penggunaan fasilitas yang dirancang khusus untuk mensimulasikan kondisi raceway. Ini termasuk injeksi ledakan panas ke tempat tidur kokas yang dikemas, sering disebut 'model panas'. Ini memiliki kemampuan untuk mensimulasikan kondisi pembakaran untuk waktu tinggal pendek milidetik, serta lokasi raceway yang berbeda. Namun, fasilitas skala pilot masih belum sepenuhnya mensimulasikan kondisi raceway di BF. Sebagai contoh, mereka mungkin tidak bekerja pada tekanan yang dekat dengan tekanan utama tuyere/sibuk. Tekanan yang lebih tinggi di raceway meningkatkan laju gasifikasi batubara.
Sejumlah model komputer tersedia untuk menilai perilaku batubara di raceway dan di tempat lain di BF. Validitas model-model ini telah dipertanyakan karena mekanisme yang mereka gambarkan sangat kompleks dan tidak sepenuhnya dipahami. Keakuratan mereka tergantung pada asumsi yang dibuat dan validitas hubungan yang dibangun ke dalam model. Karena perilaku batubara sangat dipengaruhi oleh desain BF dan kondisi operasi, serta sifat batubara, model komputer mungkin hanya dapat diterapkan untuk BF tertentu, kondisi operasi dan jenis batubara yang sama yang telah dikembangkan dan diuji. Ini adalah batasan dari semua teknik ini.
Pembakaran batubara antara pintu keluar injection lance dan dinding belakang raceway (jarak fisik sekitar 0,7 m hingga 2 m) terjadi pada suhu tinggi (1400 derajat C hingga 2200 derajat C), tekanan tinggi (sekitar 3 kg/ cm persegi hingga 6 kg/cm persegi dan waktu tinggal yang singkat (10 milidetik hingga 40 milidetik untuk partikel yang dihaluskan). Di bawah kondisi yang parah inilah pembakaran batubara tingkat tinggi diperlukan untuk dicapai.
Proses pembakaran batubara dapat dibagi menjadi langkah-langkah berikut dengan beberapa di antaranya tumpang tindih.
- Partikel bubuk yang disuntikkan (kurang dari 75 mikron) dipanaskan dengan cepat saat memasuki ledakan udara panas yang diperkaya O2. Tingkat pemanasan ditentukan oleh kondisi operasional tetapi sekitar 100 derajat C per detik. Temperatur ledakan panas biasanya 1000 derajat C hingga 1200 derajat C dan kecepatan gas sekitar 180 m/s hingga 250 m/s.
- Pirolisis partikel terjadi untuk menghasilkan volatil (gas) yang tidak dapat terkondensasi, volatil yang dapat terkondensasi (tar), dan arang berkarbon. Dibutuhkan sekitar 2 milidetik hingga 20 milidetik untuk menyelesaikan devolatilisasi.
- Pengapian dan pembakaran VM berlangsung untuk menghasilkan terutama CO2 (karbon di-oksida) dan H2O (uap air). Ini membutuhkan waktu beberapa mili detik.
- Pembakaran parsial arang sisa berlangsung oleh O2. Pembakaran arang menyumbang sebagian besar panas yang dilepaskan selama pembakaran. Berbeda dengan pembakaran VM, di mana VM berdifusi menuju atmosfer yang kaya O2 (menghasilkan area reaksi yang besar), O2 untuk oksidasi arang harus diangkut ke permukaan partikel yang relatif kecil. Akibatnya, oksidasi arang adalah proses yang lebih lambat. Selama VM dilepaskan, O2 tidak dapat menghubungi permukaan arang karena persyaratan stoikiometrik yang tinggi dari VM.
- Gasifikasi arang sisa oleh CO2 dan H2O untuk menghasilkan CO (karbon mono oksida) dan H2 (hidrogen). Ini adalah reaksi paling lambat dari semua proses ini, dan terutama terjadi di luar raceway.
Ini adalah karakteristik pembakaran batubara daripada pembakaran kokas yang mengatur komposisi gas dan distribusi suhu di raceway karena mereka lebih disukai dibakar. Gambar 1 mengilustrasikan beberapa langkah pembakaran batubara yang terjadi di dalam raceway, dan bagaimana komposisi gas bervariasi. Sebagian besar O2 dikonsumsi di dekat hidung tuyere, sementara atmosfer kaya CO2 diproduksi di tengah, dan atmosfer kaya CO di ujung raceway.
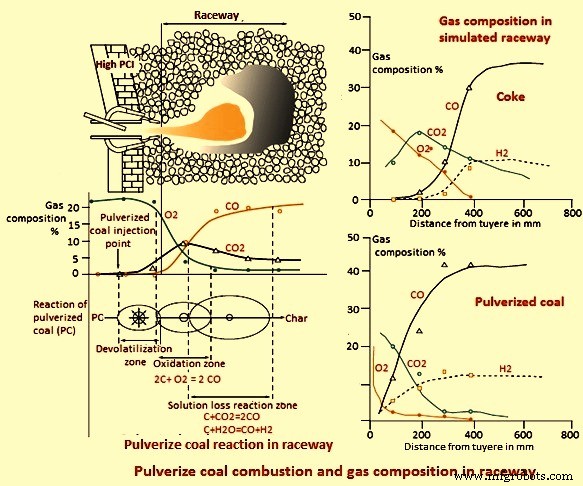
Gbr 1 Pembakaran batu bara bubuk dan komposisi gas di raceway
Tingkat pembakaran (efisiensi pembakaran), dan karenanya jumlah material yang tidak terbakar yang diangkut keluar dari raceway, tergantung pada beberapa parameter yang meliputi (i) sifat batubara, seperti kandungan VM, ukuran partikel dan densitas, dan (ii ) kondisi pengoperasian, misalnya, komposisi dan suhu gas ledakan, serta posisi dan desain tombak.
Grafik pada Gambar 2 yang menunjukkan efisiensi pembakaran dan laju injeksi batu bara bubuk didasarkan pada studi yang dilakukan saat menyelidiki laju maksimum batu bara bubuk dari keseimbangan karbon di BF menggunakan model keseimbangan material dan panas.
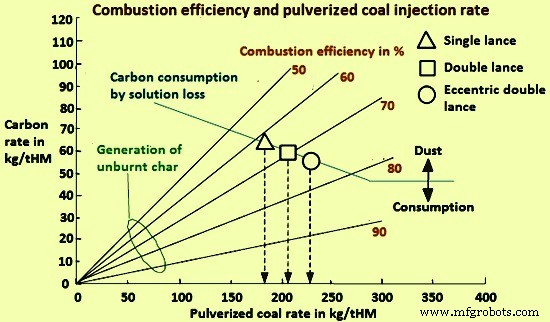
Gbr 2 Efisiensi pembakaran dan laju injeksi batubara bubuk
Berdasarkan berbagai investigasi yang dilakukan, langkah-langkah untuk mengintensifkan pembakaran batubara di raceway dirangkum di bawah ini.
- Memperkaya ledakan dengan O2. Namun, efek non-linier dari ledakan O2 pada tingkat pembakaran harus diperhitungkan. Peningkatan laju pembakaran menjadi lebih kecil dengan meningkatnya kandungan O2.
- Pencampuran awal batu bara bubuk dengan O2 sebelum dimasukkan ke dalam rongga tuyere.
- Penggunaan campuran batubara (biasanya batubara dengan kandungan VM tinggi dan rendah) dan campuran bahan bakar untuk mempertahankan tingkat pembakaran yang tinggi dan rasio penggantian kokas/batubara yang tinggi.
- Injeksi batubara dengan Fe oksida (bijih besi halus, dan limbah yang mengandung Fe dll.), karbonat, dan aditif kaya O2 lainnya.
- Penggunaan fenomena kimia dan fisika, mis. katalitik, polarisasi, dan efek lainnya.
- Optimasi penggilingan batubara, tergantung pada kondisi operasi dan sifat batubara.
Pengaruh peringkat batubara
Perilaku pembakaran dan gasifikasi batubara bubuk di raceway dipengaruhi oleh sifat-sifatnya. Pengaruh sifat-sifat umumnya pada suhu nyala (FT) dan efisiensi pembakaran (CE) dijelaskan di bawah ini.
PCI memiliki efek pendinginan pada FT. FT merupakan parameter penting karena mempengaruhi terak dan kimia logam, penguapan dan resirkulasi unsur alkali yang ada, dan aliran logam di perapian. Sulit untuk mengukur FT sehingga umumnya dihitung dari keseimbangan energi zona raceway. Nilai yang dihitung dikenal sebagai 'raceway adiabatic flame temperature' (RAFT), atau FT teoritis. Perhitungan RAFT dapat bervariasi dari satu BF ke BF lainnya tergantung pada asumsi yang dibuat, sehingga nilainya mungkin tidak dapat dibandingkan secara langsung. Ada RAFT optimal untuk setiap BF tergantung pada faktor-faktor seperti komposisi beban dan permeabilitas, kualitas kokas, dan laju hembusan. Penyuntikan batubara menurunkan RAFT (dibandingkan dengan operasi semua kokas) karena mendorong reaksi endotermik. Batubara VM rendah dan VM tinggi masing-masing menurunkan FT dalam kisaran 80 derajat C hingga 120 derajat C dan 150 derajat C hingga 220 derajat C per 100 kg/tHM. Secara umum, semakin tinggi rasio H2/C (karbon) dalam batubara, semakin besar efek pendinginannya. RAFT juga menurun dengan meningkatnya laju injeksi batubara. Peningkatan suhu ledakan dan/atau pengayaan O2, dan/atau penurunan kelembaban ledakan dapat mengimbangi efek pendinginan batubara.
Eksperimen pembakaran di bawah kondisi simulasi lingkungan BF telah menunjukkan bahwa CE biasanya meningkat dengan meningkatnya VM batubara. Batubara HV (high volatile) mudah digasifikasi, menghasilkan jumlah gas yang lebih besar, dengan CV yang lebih rendah, dan jumlah arang yang lebih kecil dibandingkan dengan batubara volatil rendah (LV) dan medium volatile (MV). Dengan demikian, pembakaran gas lebih penting untuk batubara peringkat rendah daripada pembakaran arang. Jika pembakaran gas tidak sempurna, jelaga dapat terbentuk, dan ini dapat menyebabkan penurunan permeabilitas BF saat meninggalkan raceway. Jelaga memiliki reaktivitas yang lebih rendah daripada arang yang tidak terbakar.
Tingkat devolatilisasi dipengaruhi oleh ukuran partikel batubara, dengan ukuran yang lebih halus menyebabkan devolatilisasi lebih lengkap. Saat kandungan VM batubara menurun, CE akhir diatur oleh reaksi arang karena pengapian dan pembakaran VM berlangsung cepat. Char dengan reaktivitas yang lebih tinggi memiliki CE yang lebih tinggi. Telah sering diperdebatkan bahwa pada suhu tinggi yang terjadi di raceway, reaktivitas kimia menjadi kurang penting karena laju pembakaran dibatasi oleh laju difusi O2 ke partikel, dan waktu burnout lebih bergantung pada ukuran partikel dan konsentrasi O2. Dikombinasikan dengan waktu tinggal yang singkat, pengaruh perbedaan reaktivitas arang antara batubara mungkin tidak terlalu signifikan di raceway. Ada pendapat lain yang menyatakan bahwa mengingat ukuran partikel kecil yang digunakan (lebih tinggi dari 80% kurang dari 75 mikron di PCI) dan kondisi yang sangat turbulen yang ada di raceway, laju keseluruhan pembakaran arang biasanya dipengaruhi oleh intrinsik. reaktivitas kimia arang. Reaktivitas arang tentu penting di luar raceway. Di bawah kondisi di tungku atas, gasifikasi char cenderung dikendalikan oleh laju reaksi kimia. Oleh karena itu, laju reaksi gasifikasi arang secara keseluruhan kemungkinan akan dipengaruhi oleh reaktivitas kimia arang terhadap CO2.
Secara umum, reaktivitas arang meningkat dengan VM batubara, yaitu, batubara HV biasanya menghasilkan arang yang lebih reaktif daripada batubara LV, dan karenanya burnout yang lebih baik. Ada pengecualian karena reaktivitas arang dipengaruhi oleh sejumlah faktor yang meliputi (i) morfologinya (luas permukaan dan porositas), (ii) struktur yang dihasilkan, (iii) komposisinya, dan (iv) kondisi operasinya. Laju pembakaran dan reaktivitas arang sebagian bergantung pada ukuran partikel dan struktur porinya. Struktur pori mengontrol suplai gas reaktif ke bagian dalam partikel batubara dan menyediakan permukaan internal yang bervariasi untuk reaksi.
Fragmentasi arang, yang dipengaruhi oleh strukturnya, meningkatkan luas permukaan luar. Proporsi partikel arang yang lebih tinggi dengan rongga berdinding tipis dan porositas makro dan luas permukaan pori makro yang lebih tinggi dihasilkan pada laju pemanasan yang tinggi. Secara umum, jenis arang ini cenderung terfragmentasi lebih banyak daripada yang memiliki dinding lebih tebal dan porositas lebih rendah, dan karenanya memiliki laju reaksi arang yang lebih tinggi. Fragmentasi dapat menjadi salah satu alasan mengapa beberapa operator menemukan bahwa VM memiliki pengaruh yang kecil terhadap daya bakar batubara. Arang yang terbentuk dari batubara peringkat tinggi (LV) pada suhu tinggi biasanya lebih teratur dan karenanya kurang reaktif. Perkembangan arang yang sangat anisotropik dengan peningkatan suhu juga menurunkan reaktivitas arang. Dengan demikian, batu bara ini mendapat manfaat dari suhu ledakan yang lebih rendah untuk meningkatkan daya bakar.
Perubahan komposisi maseral batubara dapat menjelaskan perbedaan dalam reaktivitas pembakaran, terutama di antara batubara dengan peringkat yang sama. Maseral inertinit biasanya dianggap 'inert' (tidak reaktif). Namun tidak sesederhana ini. Tidak semua maseral inertinit sebenarnya tidak reaktif, dan tidak semua vitrinit reaktif. Vitrinit, inertinit, dan bahkan liptinit, dapat berkontribusi pada C yang tidak terbakar dalam residu karbon. Juga telah diperhatikan bahwa meskipun arang batubara kaya inertinit pada dasarnya kurang reaktif dibandingkan arang batubara kaya vitrinit pada 500 derajat C, ini tidak lagi penting pada suhu tinggi (1300 derajat C). Kemungkinan perbedaan dalam daya bakar batubara sangat berkurang di bawah kondisi pembakaran yang sangat intens di raceway.
Kinerja pembakaran batubara dapat ditingkatkan karena efek katalitik dari mineral penyusunnya atau terhambat oleh konsentrasi mineral yang berlebihan. SiO2 dan Al2O3 (alumina) dapat memperlambat laju reaksi, sedangkan jenis kalsium (Ca), magnesium (Mg), besi (Fe) dan alkali dapat meningkatkannya, dengan efek katalitik yang lebih menonjol pada batubara peringkat rendah. Namun, peningkatan pembakaran partikel kaya mineral telah dikaitkan, bukan dengan efek katalitik, tetapi untuk difusi yang menguntungkan dari gas yang bereaksi melalui antarmuka mineral dan maseral-mineral. Kurangnya korelasi yang jelas antara reaktivitas arang dan fase anorganik individu dapat dikaitkan dengan perbedaan pengaruh suhu pada transformasi mineral batubara. Meskipun batubara dan arang dengan reaktivitas tinggi biasanya lebih disukai, reaktivitas yang terlalu tinggi dapat menyebabkan kondisi tungku tidak stabil.
Pencampuran dapat mencairkan sifat pembakaran yang tidak menguntungkan dari batubara. Tetapi kinerja pembakaran campuran lebih kompleks daripada batubara tunggal. Masing-masing komponen batubara mengalami devolatilisasi dan pembakaran pada temperatur dan waktu yang berbeda dan burnoutnya dapat sangat bervariasi. Selanjutnya, interaksi antara berbagai batubara dalam campuran dapat terjadi yang memperumit prediksi perilaku pembakaran campuran. Interaksi pertama terjadi di pulverizer dimana terdapat potensi perbedaan besar dalam distribusi ukuran komponen batubara, terutama jika terdapat perbedaan yang signifikan pada kekerasan masing-masing batubara. Disproporsionasi juga terjadi, mempengaruhi komposisi mineral dan petrografi dari partikel yang dihasilkan, dan perilaku pembakaran selanjutnya.
Interaksi antar komponen batubara dapat meningkatkan daya bakar campuran. Sebagai contoh, pembakaran batubara LV dapat ditingkatkan dengan mencampurkan dengan batubara HV. Batubara HV melepaskan lebih banyak VM yang membantu membentuk medan suhu gas yang lebih tinggi, yang kemudian memanaskan batubara LV. Ini mendorong devolatilisasi, pengapian, dan pembakarannya. Efek sinergis lebih terasa ketika fraksi batubara HV lebih tinggi, hingga persentase tertentu. Dalam kondisi BF yang disimulasikan, campuran yang mengandung sekitar 70% batubara HV yang memiliki 32,5% VM dan 30% batubara LV yang memiliki 20% VM telah memberikan burnout tertinggi.
Efek ukuran partikel
Kinerja pembakaran batubara dipengaruhi oleh ukuran partikelnya. For complete conversion, and hence effective utilization of the injected coal, the heating up, devolatilization, pyrolysis and combustion of the particles need to take place in the period between their entry into the hot blast and the raceway boundary. Normally, greater amount of VM is released with reducing coal particle size. This can facilitate gas phase combustion.
Finer particles have higher specific surface areas and thus higher heating rates. The granular coals releases lower amounts of VM than when they are pulverized. Calculated pyrolysis yields indicate that nearly all the VM from the pulverized coals are released whereas it is incomplete in case of the granular coals. The presence of residual VM in the granular coals affects the subsequent CO2 gasification reactivity of the chars. It has also been shown that the extent of devolatilization in the finer particles (45 microns to 75 microns) is more complete than the larger particles (75 microns to 150 microns). The effect is more pronounced for the LV coal (15 % VM) compared to the HV coal (37 % VM). This is since a higher VM release can result in more soot and tar production, produced from secondary reactions of the volatiles. The reactivity of the soot is lower than that of the unburned char. Thus, the lower is the soot formation; the better is the BF stability.
The CE (or burnout) of coal normally increases with decreasing particle size since a higher surface area is available for reaction. Larger particles require a longer time for burnout. The increase is more pronounced as VM content increases in coals. However, the particle size effect is also dependent on O2 stoichiometry, as well as coal rank (and char reactivity). It has been found that larger particles of coal generally have a higher CE (degree of burnout) at O2/C ratios of greater than 2 (fuel lean conditions) under simulated BF conditions. The smaller particles have higher CE under fuel rich conditions (O2/C ratio less than 2).
Operational factors
The effective use of coal needs operational changes to compensate for alterations in the raceway parameters and their effect elsewhere in the BF (such as the thermal state, slag regime and gas dynamics). Measures to intensify the combustion of coal in the tuyere/raceway region, and hence increase the injection rate include (i) increase the amount of O2 in the tuyeres, and (ii) adjustment in the blast temperature and moisture. There are some other measures taken to improve coal combustion, such as preheating the coal and the use of additives. Further, the choice of particle size, and hence the grinding parameters, can also influence the CE.
Oxygen can be added to the tuyere by (i) enrichment of the hot air blast, (ii) injection through the coal lances, and (iii) separate O2 lances. The addition of O2 results into higher availability of O2 for the participation in the combustion of coal in the raceway. Hence, the CE of the coal increases. However, the influence of O2 enrichment on CE is limited. It has been shown through calculation that the CE increases by around 6.7 % for a HV coal (34.5 % VM) and 3.3 % for a LV coal (14 % VM) when O2 enrichment of the hot air blast is raised from 0 % to 6 % by volume. With higher O2 enrichment, CE can actually decrease due to insufficient mixing. Increasing O2 enrichment increases the diffusion of O2, but diminishes the volume of combustion gas which transfers heat to the coal particles. Thus, there is the non-linear effect of blast O2 content on the degree of coal combustion.
Oxygen enrichment of the hot air blast produces both a reduction in bosh gas flow and a rise in FT. The former effect can help counteract the increase in the burden resistance (lower permeability) and the pressure drop associated with high injection rates. The latter effect can help compensate for the cooling effect of the decomposition of the coal VM. The CO and H2 contents also increase with O2 enrichment, resulting in the improved reduction of the iron ore in the central shaft. The CV of the top BF gas normally improves with O2 enrichment.
The lower limit of O2 enrichment is generally determined by the amount needed to maintain the required RAFT, with more O2 needed as the VM content of the coal increases. If the FT becomes too high, then burden descent can become erratic. Too low a FT hampers coal combustion and melting of the ore burden. The upper limit is dependent on maintaining a sufficient top gas temperature. As O2 is increased, the gas mass flow within the BF decreases, which decreases the heat flow to the upper region of the furnace for drying of the burden. The upper limit of the top gas temperature is also governed by the need to protect the top gas equipment. Other limitations to O2 enrichment include its cost and availability.
The position and design of the injection lance influence the CE and ash deposition in the tuyere. However, oxy-coal lance injection (co-annular injection) can produce an insulating effect around the coal particles, resulting in less coal combustion inside the tuyere. This effect carries over into the raceway, and less combustion is the end result. Lowering the O2 lance injection rate in this case improves the CE.
The key measure for combustion at high injection rate is a high blast temperature. O2 enrichment plays a more important role as a means of controlling gas flow in the BF rather than controlling the coal combustion. Normally, a higher hot blast temperature is a cost effective measure than O2 enrichment since it allows a lower consumption of O2. Increased blast temperature also reduces coke consumption, typically 10 kg/tHM for every increase of 40 deg C with PCI, and lead to a small rise in the raceway depth. A higher blast temperature is normally required as the VM of the coal increases. This is due to the lower char reactivity of the low VM coal.
Lowering of blast moisture can help to compensate for the cooling effects of PCI. If the RAFT becomes excessive, then blast moisture can be increased. Raising the hot blast moisture means more H2 in the bosh gas for iron ore reduction. The optimum RAFT in BF operating with higher H2 content can be lower than the BF operating with lower H2. Also, the blast velocity can be adjusted to not only improve coal combustion, but to maintain the needed length of the raceway zone which is critical for obtaining good conditions in the hearth.
Unburnt char
As the injection rate increases, the combustibility of coal tends to decrease resulting in unburnt material (such as char, fines, and fly ash) leaving the raceway. Some of these materials, along with coke debris, collect at the back of the raceway, in the bird’s nest, obstructing the rising gas flow and entrained solids in this area. The majority are swept upwards where they can accumulate under the cohesive zone, decreasing permeability and hence the productivity of the BF.
Changes in the permeability of the lower furnace zone can further affect the HM quality and slag viscosity. The unburnt material tends to collect at positions where large changes in the gas flow occur. Eventually it is entrained into the gas flow, passing through the cohesive zone coke slits, and up the shaft, where it can influence burden permeability, and is finally emitted with the top BF gas. Higher coal injection rates also increase the volume of combustion gases, and hence the gas flow, and change the heat load in the lower part of the BF. In addition, more slag is produced.
The deposition of unburnt fine material is a complex phenomenon consisting of several generation mechanisms, reactions, multiphase flow, buildup and re-entrainment. Different gas flow models have been developed to understand and predict the behaviour of fine material within the BF. With suitable burden charging patterns (such as central coke charging) and the use of stronger coke many of the problems relating to gas flow can be overcome.
Operating experience has shown that most of the unburnt material (char) is consumed within the furnace by the three mechanisms which are (i) gasification with CO2 and H2O, (ii) reaction with liquid iron (carburization), and (iii) reaction with slag. It is advantageous if the unburnt char participates in the ore reduction reactions, thus replaces more of the coke and lowers the amount of unburnt solids in the top BF gas. The three char consumption mechanisms are described below.
The gasification reaction of char with CO2 and H2O begins in the raceway, but because the residence time for fine particles is too short for appreciable reaction, gasification mainly occurs in the BF shaft. The reactions of char C with CO2 (the solution loss or Boudouard reaction) and H2O are slower than char combustion. The char obtained from coal competes with that from coke for CO2 and H2O. Char from coal is more reactive than the char from coke and hence is preferentially gasified. Therefore coke degradation by the solution loss reaction decreases with increasing PCI rates. In general, high VM coal char has a higher CO2 reactivity than low VM coal char. However the char reactivity in case of low VM coal can be improved by blending it with the high VM coal. The CO2 reactivity of coal blends is non-additive.
The reactivity of C in the unburnt char to CO2 and H2O is dependent not only on its surface area (particle size) but also on its structure and composition, as well as the operating conditions in the BF. It has been shown that the CO2 gasification reactivity of coal char increases with temperature upto 1500 deg C, especially between 1300 deg C and 1500 deg C. Complete char gasification usually requires a contact time of around 10 seconds at 1500 deg C. Since the residence time for particles at such high temperatures is too short in a BF, hence char gasification mainly occurs at decreasing temperatures in the furnace shaft.
The properties of char change as it moves up the BF, and thus its reactivity to CO2 and H2O. The reacting atmosphere is not uniform. As an example, the concentrations of CO, CO2, H2 and H2O vary at different locations within the BF. Injection of coal increases the bosh gas H2 concentration. Since the chemical reaction rate of H2 reduction is higher than that of CO, the extent of solution loss reaction diminishes as the bosh gas H2 rises. CO2 and H2O are present in the upper part of the BF due to the reduction of iron ore. Under the conditions here, char gasification by CO2 is expected to be controlled by the rate of the chemical reactions. In the lower part of the BF, char gasification is partly diffusion controlled. Hence, the overall reaction rate of char gasification is probably influenced by the chemical reactivity of char to CO2 in this region. Char reactivity towards CO2 is also influenced by its chemical structure, with less ordered structures being more reactive.
The presence of certain minerals in the char ash, such as Fe and alkalis, can catalyze the CO2 gasification reaction, whereas other minerals, such as SiO2 and Al2O3, can slow down the reaction. These catalytic effects become more prominent for low rank coals. Depending on its composition, ash can also retard the C conversion due to blockage of char particles as a result of increased proportion slag formation in the char particle. In the lower part of the BF, condensed alkalis from the recirculating gases (derived from coal, coke and iron ore) can have a catalytic effect. The loss of C by gasification increases the char ash content.
Carburization of the HM begins in the solid phase within the cohesive zone of the BF, and continues during descent of the metal droplets through the active coke, deadman and hearth zones. Unburnt char and fine material leaving the raceway can contact the dripping liquid metal in the bosh and hearth zones. C and other elements, such as Fe, Si (silicon) and S (sulphur), dissolve from the char into the liquid iron and hence influence the composition of the HM. The dissolution of C contributes to the carburization of liquid iron, and controls the level of char consumption by the HM. It becomes critical when the CE is low. If the HM is close to saturation when it reaches deadman and hearth, the unburnt material cannot be consumed, thus reduces the permeability in these regions. The C can come from unburnt coal as well as from coke. Since the dissolution rate of C from coal char is a slower process than that from coke, C from coke is preferentially consumed.
Carbon dissolution from unburnt char into liquid metal is influenced by the furnace operating conditions and the following factors.
- Char particle size – Unburnt char which maintains its pulverized form reacts very little with the liquid metal and the slag since it cannot penetrate into the liquid. If, however, the char particles are agglomerated into larger particles or captured by the larger pieces of coke, then they behave like bosh coke and carburize the liquid metal up to saturation. However, a tuyere probe sample taken at a BF in Australia indicated that ultrafine coal char particles can react with the dripping liquid metal, and that they are more readily dissolved than ultrafine coke particles. Experiments, though, have shown that the dissolution rate of C from coal char, though at larger particle sizes, is a slower process than that from coke.
- Char structure – Normally, the rate of dissolution improves as the C structure becomes more ordered.
- Char mineral matter – In general, SiO2, Al2O3 and MgO (magnesia) slow the C dissolution kinetics, whilst CaF2 (calcium fluoride) and Fe oxides increase the rate. The effect of CaO (calcium oxide) is less clear. The reaction of Ca (calcium) with S in the metal produces a layer of CaS (calcium sulphide) which can inhibit C transfer. The AFT is also one of the controlling mechanisms which limit the C dissolution. The formation of an ash layer on the carbonaceous material reduces the surface area available for dissolution, thus retarding C dissolution rates. Low AFT allows easy removal of the ash, in the form of liquid slag. This results in constant exposure of fresh C surface to the liquid iron, permitting the mass transfer of C to the liquid iron.
- Liquid iron composition – It changes over time. The C dissolution rate is typically decreased as the C content of the liquid iron increases. Higher S content also retards the C dissolution. Combustion of coal and coke releases sulphur oxides (SOx) which can react with the descending metal and slag.
Unburnt char, ash, fines and coke can interact with the dripping slag. The slag composition changes as it moves down the BF, with the Fe oxide concentration being continuously reduced. The reactions at the interface between the solid char and liquid slag play a major role in char consumption since they influence the kinetics of the reduction reactions and the contact area between the slag and char available for reaction.
Factors influencing unburnt char interactions with the slag include the slag composition, char C content, and char ash content and composition, as well as the furnace operating conditions. Char consumption by slags basically occurs through the following mechanisms.
- Reduction of the Fe oxides in slags by C in the char – The wetting characteristic has a significant effect on the dominant reduction mechanism taking place. The wetting characteristic of slags varies with slag composition, temperature, time, and carbonaceous material. Wetting varies as a function of time since the reduction of Fe oxide in the slag by char, and the dissolution of the char ash components into the slag, results in continuous variations in the slag and char compositions. An increase in temperature normally results in improved wettability at the slag/C interface. Reduction rate usually increases with increasing slag FeO (2 % to 10 %) content and with increasing reaction temperature (1300 deg C to 1600 deg C). In general, coal chars are poorly wetted by slag containing more than 10 % FeO at 1400 deg C and 1500 deg C. A faster reaction rate for coke suggests that coke fine is preferentially consumed before coal char.
- Reduction of SiO2 in slag by C of the char – It is a function of temperature. At temperatures less than 1500 deg C, only reduction of FeO takes place. At higher temperatures, both SiO2 and FeO in the slag are reduced, thus resulting in increased consumption of the char. SiO2 is reduced by C, through gaseous SiO, to Si or silicon carbide (SiC). Self-reduction of SiO2 in the char ash by C can also occur, resulting in further consumption of the char. The reduction kinetic of SiO2 is influenced by the wettability of char by the slag. Wetting behaviour is improved with an increase in slag SiO2 content, and with an increase in temperature (1500 deg C to 1700 deg C). Greater amounts of SiO2 and FeO in the char ash facilitate the slag/C interaction, leading to improved consumption of these oxides through reduction reactions.
- Interaction between components in the slag and char – This leads to the assimilation of char ash components such as S. In addition, the reduction of MgO in slag by char C can lead to further consumption. Self-reduction of the oxides in the char ash by C can also contribute to char consumption.
Slag viscosity has also a role to play. The presence of unburnt char in the slag can interfere with tapping by increasing slag viscosity, whereas absorption of char usually increases the fluidity of the bosh slag. Changes in slag mobility can affect the position and shape of the fluid and cohesive zones. A high viscosity slag around the tuyeres leads to serious gas flow problems. Slag viscosity is a complex function of slag composition, temperature and partial pressure of O2. Also unburnt char, coke, and unburnt ash from the coal can interact with the slag. All of these carbonaceous materials contribute oxides to the slag. In general, higher amounts of SiO2 or Al2O3 (acidic components) increase slag viscosity, whereas a higher basicity (higher CaO or MgO) lowers slag viscosity because of de-polymerization of the silicate network. Slag viscosity decreases with increasing FeO (0 % to 20 %) content at a fixed basicity. Basicity is normally determined by the CaO/SiO2 ratio. Since the slag does not completely absorb the char and ash in the bosh region, bosh slag usually has a higher basicity than tapped slag. The addition of fluxes can help in solving slag formation problems.