Kebersihan Baja dan Teknologi Baja Bersih
Kebersihan Baja dan Teknologi Baja Bersih
Kebersihan baja merupakan faktor penting yang menentukan kualitas baja. Ini dapat memiliki pengaruh yang luar biasa pada sifat baja, seperti kekuatan tarik, sifat mampu bentuk, ketangguhan, kemampuan las, ketahanan retak, ketahanan korosi, dan ketahanan lelah, dll. Permintaan akan sifat mekanik baja yang lebih baik dari konsumen baja telah mendesak baja produsen untuk meningkatkan kebersihan baja.
Di lingkungan sekarang, peningkatan kebersihan baja telah menjadi kebutuhan bagi industri baja. Ini telah memandu pengembangan proses pembuatan baja sekunder. Kekuatan pendorong di balik perkembangan ini adalah untuk memungkinkan baja baru yang dapat mentolerir aplikasi yang sangat menuntut seperti komponen transmisi untuk industri otomotif, serta suku cadang dan tabung konstruksi untuk lingkungan yang agresif dan korosif.
Baja bersih mengacu pada baja yang bebas dari inklusi. Inklusi adalah partikel non logam yang tertanam dalam matriks baja. Selain menurunkan inklusi oksida non-logam dan mengendalikan morfologi, komposisi dan distribusi ukurannya, baja bersih memerlukan penurunan elemen pengotor residu lainnya seperti fosfor (P), belerang (S), oksigen total (O2), nitrogen ( N2), hidrogen (H2), juga kadang-kadang karbon (C), dan elemen-elemen jejak seperti arsenik (As), timah (Sn), antimon (Sb), selenium (Se), tembaga (Cu), timbal (Pb), dan bismut (Bi). Unsur-unsur pengotor ini bervariasi dengan nilai baja yang berbeda. Beberapa elemen berbahaya untuk grade baja tertentu, tetapi bisa jadi kurang berbahaya atau bahkan berguna untuk grade baja lainnya. Dengan kata lain, elemen kontrol berbeda untuk persyaratan kinerja berbeda yang dibutuhkan dari baja.
Untuk mencapai kebersihan yang memuaskan dalam baja, perlu untuk mengontrol dan meningkatkan berbagai praktik operasi di seluruh proses pembuatan baja. Ini termasuk (i) penambahan agen deoksidasi dan paduan besi, (ii) perawatan metalurgi sekunder, dan (iii) sistem selubung dan praktik pengecoran.
Sejarah pengembangan baja bersih
Istilah 'baja bersih' diciptakan pada pertengahan abad ke-20. Saat itu produksi baja mulai meningkat secara global. Pada saat itu, dipahami bahwa kualitas baja juga harus dianggap sebagai masalah khusus dan penting. Kemajuan dalam pembuatan baja sejak saat itu telah menghasilkan pengembangan banyak mutu baja dengan tingkat pengotor yang sangat rendah. Dalam beberapa tahun terakhir, baja 'bersih dan ultra-bersih' baru telah dikembangkan dan dikomersialkan untuk memenuhi persyaratan kualitas saat ini dan masa depan yang dibutuhkan oleh industri konsumen baja. Kebersihan baja juga telah meningkatkan sifat mekanik (seperti kekuatan lelah dan ketangguhan impak) dan ketahanan korosi baja secara signifikan.
Konsep kebersihan lahir awalnya dari pengamatan di bawah mikroskop optik inklusi non-logam (NMIs) oleh disiplin metalografi yang baru lahir selama pertengahan abad ke-20. Kebersihan dinilai berdasarkan gambar standar bidang mikroskopis, di mana geometri (bentuk dan ukuran) dan distribusi NMI dibedakan berdasarkan berbagai jenis gambar. Pengamat terlatih telah menetapkan bahwa beberapa bentuk dapat diterima di beberapa kelas baja dan inklusi yang lebih kecil umumnya lebih dapat diterima daripada yang lebih besar. Meskipun komposisi inklusi tidak tersedia pada saat itu, pengamat telah menetapkan korespondensi antara kadar dan komposisi inklusi oleh keluarga (sulfida, silikat, aluminat, alumina, dan inklusi komposit) berdasarkan kandungan S dan riwayat deoksidasi baja.
Metode-metode yang dikembangkan pada abad ke-20 ini segera dibakukan. Mereka mendahului penggunaan umum dari proses pembuatan baja sekunder dan pengecoran baja secara terus menerus. Pengembangan lebih lanjut dari konsep kebersihan dilakukan dengan mengeksplorasi berbagai masalah secara paralel, terkait dengan kimia fisik pembuatan baja, pengembangan reaktor proses baru, dan solusi inovatif baru untuk mengontrol komposisi, bentuk, ukuran, dan distribusi inklusi yang seiring waktu menjadi rutinitas praktik pembuatan baja. Visi modern tentang kebersihan telah muncul dari upaya membangun konsep yang dilakukan selama 30 tahun hingga 40 tahun. Selanjutnya, subjek kebersihan baja telah mencapai tingkat kematangan tertentu sekarang, terutama untuk proses pembuatan baja sekunder baru dan untuk baja yang dihasilkan oleh proses pengecoran kontinu.
Inklusi non-logam
NMI dibentuk oleh fase kaca-keramik yang tertanam dalam matriks baja. Kehadiran NMI di baja adalah alasan utama yang mempengaruhi kebersihan baja. NMI dalam baja berasal dari banyak sumber yang meliputi berikut ini.
Produk deoksidasi – Contoh inklusi tersebut adalah inklusi alumina (Al2O3) yang menyebabkan mayoritas inklusi asli dalam baja C aluminium (Al) kill (LCAK) rendah. Inklusi ini dihasilkan oleh reaksi antara O2 terlarut dan agen deoksidasi yang ditambahkan, seperti Al. Inklusi Al2O3 bersifat dendritik ketika terbentuk dalam lingkungan O2 yang tinggi, atau dapat dihasilkan dari tumbukan partikel yang lebih kecil.
Produk reoksidasi – Contoh inklusi tersebut adalah inklusi Al2O3 yang dihasilkan ketika (i) Al yang tersisa dalam baja cair dioksidasi oleh FeO dalam terak, atau (ii) oleh paparan baja cair ke atmosfer.
Jebakan terak – Jebakan terak terjadi ketika fluks metalurgi terperangkap selama transfer antar bejana pembuat baja. Jebakan terak membentuk inklusi cair yang umumnya berbentuk bola.
Inklusi eksogen – Inklusi ini berasal dari sumber lain, seperti kotoran lepas, bata tahan api yang pecah, dan partikel lapisan tahan api. Mereka umumnya besar dan berbentuk tidak teratur. Mereka dapat bertindak sebagai situs untuk nukleasi heterogen Al2O3.
Inklusi reaksi kimia – Inklusi ini adalah produk modifikasi inklusi ketika perawatan Ca (kalsium) tidak dilakukan dengan benar.
Distribusi ukuran inklusi sangat penting karena inklusi besar adalah yang paling berbahaya bagi sifat mekanik baja. Satu kg baja LCAK biasanya berisi 10.000.000 hingga 1000.000.000 inklusi, termasuk hanya 400 inklusi ukuran 80 mikron hingga 130 mikron, sepuluh inklusi ukuran 130 mikron hingga 200 mikron, dan kurang dari satu inklusi ukuran 200 mikron hingga 270 mikron. Jelas, mendeteksi inklusi besar yang langka sangat sulit. Meskipun inklusi besar jauh kalah jumlah dengan yang kecil, fraksi volume totalnya bisa besar. Kadang-kadang cacat bencana disebabkan oleh hanya satu inklusi besar dalam panas baja utuh. Dengan demikian, baja bersih tidak hanya mencakup pengendalian kandungan inklusi rata-rata dalam baja, tetapi juga menghindari inklusi yang lebih besar dari ukuran kritis yang berbahaya bagi produk.
NMI merupakan awan fase yang tersebar dalam matriks baja dan ditentukan oleh serangkaian parameter multi-dimensi, termasuk komposisi, bentuk, ukuran, dan distribusi. Deskripsi lengkap ini biasanya tidak tersedia dan salah satu masalah utama yang terkait dengan penilaian kebersihan adalah mengamati sampel yang representatif untuk memperkirakan parameter ini dengan akurasi dan keterwakilan yang wajar. Satu kesulitan terkait dengan inklusi besar (berukuran 100 mikron atau lebih), yang sangat langka dan karenanya sulit dilihat, kecuali jika sampel berukuran sangat besar dianalisis.
Masalah lain adalah karena fakta bahwa populasi NMI bergantung pada waktu (dalam garis waktu proses di bengkel peleburan baja) dan pada suhu. Jadi sampel sendok, yang dikumpulkan dan dianalisis dengan hati-hati dan cermat, dapat memberikan perkiraan yang cukup baik tentang kebersihan di sana dan kemudian, tetapi hampir tidak ada hubungannya, apa pun, dengan kebersihan baja padat. Oleh karena itu, ada kebutuhan untuk menilai kapan sampel representatif dari baja cair akan diambil untuk menilai komposisi baja dan kebersihan NMI.
Jenis inklusi non-logam
Berdasarkan ukurannya, inklusi dapat berupa inklusi mikro (ukuran 1 mikron hingga 100 mikron) atau inklusi makro (ukuran lebih dari 100 mikron). Inklusi makro berbahaya. Mikro-inklusi bermanfaat karena membatasi pertumbuhan butir, meningkatkan kekuatan luluh dan kekerasan. Mikro-inklusi bertindak sebagai inti untuk pengendapan karbida dan nitrida. Makro-inklusi harus dihapus. Inklusi mikro dapat digunakan untuk meningkatkan penguatan dengan menyebarkannya secara seragam dalam matriks.
Menurut klasifikasi tradisional, ada dua jenis utama NMI yang fungsinya berasal dari asalnya. Mereka adalah (i) inklusi endogen, dan (ii) inklusi eksogen (Gambar 1).
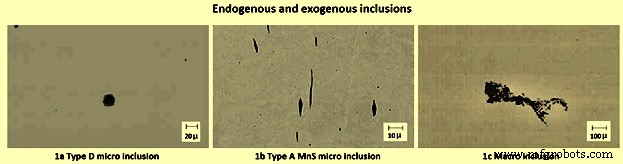
Gbr 1 Inklusi endogen dan eksogen
Endogen adalah inklusi mikro yang terbentuk dari efek fisika-kimia yang terjadi selama proses peleburan dan pemadatan. Inklusi endogen dibentuk oleh pengendapan dalam fase cair karena penurunan kelarutan spesies kimia yang terkandung dalam baja. Itu juga dapat dibentuk dari O2 dan S yang tersisa setelah proses deoksidasi dan desulfurisasi atau melalui reoksidasi (Gambar 1a dan 1b). Kelas NMI ini tidak dapat sepenuhnya dihilangkan dari baja tetapi penurunan fraksi volume dan ukuran rata-rata harus dilakukan di bawah kendali yang ketat untuk menghindari aktivasi fenomena yang merusak.
Sebaliknya, inklusi eksogen adalah inklusi makro yang diakibatkan oleh terperangkapnya material non-logam yang berasal dari terak, pecahan refraktori atau dari serbuk naik dan penutup yang digunakan untuk melindungi baja dan menghindari lengket selama pengecoran (Gambar 1c). ). NMI yang termasuk dalam kelas ini dapat ditampilkan dengan ukuran besar dan asalnya tidak dapat langsung dikenali, meskipun keberadaannya dapat sangat membahayakan kesehatan mikro-struktur baja dan keandalan mekanis terkait.
NMI memiliki pengaruh kuat pada kualitas dan kinerja baja. Inklusi ini terutama senyawa kimia logam seperti besi (Fe), mangan (Mn), Al, silikon (Si), dan Ca dll dengan non logam seperti O2, S, N2, C, dan H2.
Berbagai jenis NMI adalah (i) oksida seperti FeO, Al2O3, SiO2, MnO, Al2O3.SiO2, FeO.Al2O3, MgO.Al2O3, dan MnO.SiO2 dll. (ii) sulfida seperti FeS, CaS, MnS, MgS, Ce2S3, (iii) nitrida seperti TiN (titanium nitrida), AlN, VN (vanadium nitrida), dan BN (boron nitrida) dll., (iv) oksisulfida seperti MnS.MnO, dan Al2O3.CaS dll., (v) karbonitrida seperti karbonitrida dari titanium (Ti), vanadium (V), dan niobium (Nb) dll., dan (vi) fosfida seperti Fe3P, Fe2P, Mn5P2. Alat dasar untuk deskripsi komposisi kimia NMI oksida adalah diagram fase terner (CaO-SiO2-Al2O3), karena ini adalah sistem utama yang mengatur pembentukan senyawa non-logam ini. Kelas NMI ini dibentuk oleh elemen deoksidasi yang ditambahkan ke lelehan baja untuk menghilangkan kandungan O2. Inklusi nitrida melakukan efek merugikan yang diperparah oleh bentuk tepi yang aneh yang meningkatkan amplifikasi tegangan yang dikembangkan pada antarmuka antara NMI dan matriks logam.
Berdasarkan kandungan mineraloginya, inklusi O2 diklasifikasikan sebagai (i) oksida bebas seperti FeO, MnO, Cr2O3 (kromium oksida), SiO2, dan Al2O3 dll, (ii) spinel seperti ferit, kromit, dan aluminat, dan ( iii) silikat seperti SiO2 dengan campuran Fe, Mn, Cr (kromium), Al (aluminium), dan W (tungsten) oksida serta silikat kristal.
Klasifikasi lain dari NMI adalah dengan stabilitas. NMI agak stabil atau tidak stabil. Inklusi yang tidak stabil adalah sulfida Fe dan Mn serta beberapa oksida bebas.
Sesuai dengan morfologi inklusi, inklusi dapat memiliki (i) bentuk globular, (ii) bentuk trombosit, atau (iii) bentuk polihedral. Bentuk globular dari inklusi diinginkan. Inklusi tertentu seperti MnS, oksi-sulfida, aluminat besi, dan silikat berbentuk bulat. Bentuk trombosit dari inklusi tidak diinginkan. Baja terdeoksidasi Al mengandung MnS dalam bentuk film tipis yang terletak di sepanjang batas butir. Inklusi dengan bentuk polihedral tidak terlalu berbahaya.
Unsur-unsur kimia yang awalnya terlibat dalam kebersihan sebagian besar adalah non-logam dari tabel periodik Mendeleev, karena mereka menunjukkan kelarutan yang lebih tinggi dalam baja cair daripada dalam padatan. Ini terutama C, N2, O2, P, S, Se, dan H2. Pada daftar ini, tetangga metaloid dalam tabel seperti B (boron), As, Sb, dan Te (telurium) dapat ditambahkan. Beberapa dari unsur tersebut berasal dari bahan baku primer (P, S, As, Sb) atau dari logam panas dari tanur tinggi, sedangkan sebagian besar lainnya baik karena kontaminasi oleh atmosfer (O2, N2, dan H2) dan praktik pengoperasian yang digunakan dalam pembuatan baja, atau ditambahkan secara sukarela (C, Se, Te, dan B).
Sulfida sering merupakan konsekuensi dari perlakuan Ca yang diterapkan untuk memodifikasi inklusi oksida, tetapi inklusi CaS yang sangat tahan api dan terdispersi secara halus dapat merusak pengecoran (penyumbatan nozzle) dan untuk efek merusak. Sebaliknya, NMI MnS (sering dimodifikasi dengan kombinasi dengan CaS) berguna untuk kemampuan kerja pahat potong selama pemesinan baja.
Tiga mekanisme utama telah diakui pada asal NMI. Mekanisme ini terkait dengan efek merusak yang dimainkan oleh fase non-logam terhadap matriks logam. Mekanisme ini menganggap NMI sebagai (i) elemen bentukan yang memperkuat medan tegangan di sekitar NMI, (ii) tangki gas bertekanan yang secara progresif bermigrasi ke dalam NMI menghasilkan medan tegangan di sekitar NMI, dan (iii) fase non-logam yang menghasilkan tegangan sisa karena koefisien ekspansi termal yang berbeda yang terkait dengan fase logam dan keramik kaca.
Metode mengevaluasi kebersihan baja
Mengetahui secara akurat kandungan inklusi realistis dalam baja sangat penting untuk meningkatkan kualitas baja dan juga dalam memprediksi kinerja komponen yang terbuat dari baja. Untuk mempelajari dan mengontrol kebersihan baja, sangat penting untuk memiliki metode yang akurat untuk evaluasinya. Jumlah, distribusi ukuran, bentuk dan komposisi inklusi harus diukur pada semua tahap dalam produksi baja. Teknik pengukuran berkisar dari metode langsung, yang akurat tetapi mahal, hingga metode tidak langsung, yang cepat dan murah, tetapi hanya dapat diandalkan sebagai indikator relatif.
Metode langsung
Ada beberapa metode langsung untuk mengevaluasi kebersihan baja dan dirangkum di bawah ini.
Pengamatan mikroskop metalografi (MMO) – Ini adalah metode tradisional di mana irisan dua dimensi melalui sampel baja, diperiksa dengan mikroskop optik dan diukur dengan mata. Di dalamnya, hasilnya dievaluasi menggunakan grafik seperti skala referensi JK. Teknik ini hanya cocok untuk inklusi yang memenuhi syarat antara 2 mikron hingga 15 mikron dan terbatas pada ukuran sampel yang sangat kecil. Metode ini tidak memberikan data tentang komposisi kimia inklusi. Masalah muncul ketika menafsirkan irisan melalui inklusi berbentuk kompleks. Meskipun ada beberapa metode untuk menghubungkan hasil dua dimensi dengan realitas tiga dimensi, ini umumnya sangat bermasalah.
Analisis gambar – Ini adalah peningkatan pada MMO yang meningkatkan evaluasi mata dengan menggunakan evaluasi komputer berkecepatan tinggi dari gambar mikroskop video-scan untuk membedakan daerah gelap dan terang berdasarkan skala abu-abu. Metode ini dapat dengan mudah mengevaluasi area yang lebih luas dan jumlah inklusi yang lebih besar daripada MMO, tetapi dapat terjadi kesalahan seperti salah mengira goresan, lubang, dan noda untuk NMI.
Cetakan belerang – Ini adalah metode makrografik yang populer dan murah yang membedakan inklusi makro dan retakan dengan mengetsa area yang kaya belerang. Ini tunduk pada masalah yang sama seperti metode dua dimensi lainnya.
Pengujian patahan biru – Ini adalah teknik yang digunakan secara historis untuk mengungkapkan inklusi makro yang lebih besar dari 0,5 mm. Ini dilakukan pada area penampang batang yang telah dikeraskan, dipatahkan, dan kemudian ditempa menjadi biru untuk meningkatkan visibilitas cacat.
Metode lendir (elektrolisis) – Ini adalah metode yang akurat tetapi memakan waktu. Sampel baja yang relatif besar (200 g hingga 2 kg) dilarutkan seluruhnya dalam asam klorida (HCl) dan NMI yang tetap tidak larut dikumpulkan untuk penghitungan dan analisis lebih lanjut. Sebagai alternatif, untuk melindungi inklusi FeO, sebagian besar pelarutan dilakukan dengan menerapkan arus listrik melalui sampel baja yang direndam dalam larutan FeCl2 atau FeSO4. Metode ini digunakan untuk mengungkap individu, inklusi utuh.
Berkas elektron (EB) mencair – Sebuah sampel baja dilebur oleh berkas elektron di bawah vakum. Inklusi mengapung ke permukaan atas dan membentuk rakit di atas sampel cair. Indeks EB biasa adalah area spesifik dari rakit inklusi. Metode yang disempurnakan EB-EV (nilai ekstrem) telah dikembangkan untuk memperkirakan distribusi ukuran inklusi. Hal ini dilakukan dengan mengukur ukuran inklusi maksimum di beberapa bidang rakit dan mengekstrapolasi hasilnya di seluruh rakit, dengan asumsi distribusi ukuran inklusi eksponensial.
Cawan lebur dingin (CC) mencair – Inklusi pertama-tama terkonsentrasi pada permukaan sampel yang dilelehkan seperti pada peleburan EB. Setelah pendinginan, permukaan sampel kemudian dilarutkan, dan inklusi disaring dari zat terlarut. Metode ini meningkatkan ekstraksi slime.
Pemindaian mikroskop elektron (SEM) – Metode ini dengan jelas mengungkapkan morfologi tiga dimensi dan komposisi setiap inklusi yang diperiksa. Komposisi diukur dengan electron probe micro analyzer (EPMA). SEM mampu menilai area yang luas dan menyediakan data yang kaya tentang kimia inklusi, morfologi, dan ukuran.
Spektrometri emisi optik (OES) dengan analisis diskriminasi pulsa (PDA) – Metode OES secara konvensional digunakan untuk analisis elemen terlarut dalam baja. Teknik ini telah lebih ditingkatkan untuk menganalisis kandungan O2 total, distribusi ukuran inklusi mikro dan komposisi dalam waktu 10 menit setelah pengambilan sampel. Untuk membedakan inklusi padat (OES-PDA), pencatatan cahaya dilakukan pada frekuensi percikan emisi. Karakteristik listrik didefinisikan untuk mengoptimalkan rasio cahaya antara sinyal latar belakang elemen terlarut dan sinyal gangguan karena heterogenitas seperti inklusi. Jumlah percikan puncak Al intensitas tinggi adalah indeks PDA.
Deteksi inklusi Mannesmann oleh papan selancar analisis (MIDAS) – Sampel baja pertama-tama digulung untuk menghilangkan porositas dan kemudian dipindai secara ultrasonik untuk mendeteksi inklusi padat dan inklusi padat majemuk / pori-pori gas. Metode ini baru-baru ini ditemukan kembali sebagai metode 'liquid sampling hot rolling (LSHP).
Penganalisis ukuran partikel difraksi laser (LDPSA) – Teknik laser ini dapat mengevaluasi distribusi ukuran inklusi yang telah diekstraksi dari sampel baja menggunakan metode lain seperti slime.
Pemindaian ultrasonik konvensional (KUS) – Metode ini dapat memperoleh distribusi ukuran inklusi yang lebih besar dari 20 mikron dalam sampel baja yang dipadatkan.
Pemindaian sampel kerucut – Dalam metode ini, volume baja cor kontinu berbentuk kerucut dipindai dengan detektor spiral, seperti sistem ultrasonik padat, yang secara otomatis mendeteksi inklusi permukaan di setiap lokasi di area sampel, termasuk dari permukaan hingga garis tengah.
Dekomposisi termal pecahan (FTD) – Inklusi oksida yang berbeda secara selektif dikurangi pada suhu yang berbeda, seperti oksida berbasis Al2O3 pada 1400 derajat C hingga 1600 derajat C, atau inklusi refraktori pada 1900 derajat C. Kandungan O2 total adalah jumlah kandungan O2 yang diukur pada setiap pemanasan langkah.
Spektrometri massa mikroprobe laser (LAMMS) – Partikel individu disinari oleh sinar laser berdenyut, dan intensitas laser terendah di atas nilai ambang ionisasi dipilih untuk pola spektrum karakteristiknya karena keadaan kimianya. Puncak dalam spektrum LAMMS dikaitkan dengan elemen, berdasarkan perbandingan dengan hasil sampel referensi.
Spektroskopi fotoelektron sinar-X (XPS) – Metode ini menggunakan sinar-x untuk memetakan keadaan kimia inklusi yang lebih besar dari 10 mikron.
Spektroskopi elektron Auger (AES) – Metode ini menggunakan berkas elektron untuk memetakan keadaan kimia metode hamburan foto. Sinyal hamburan foto dari inklusi (yang telah diekstraksi dari sampel baja menggunakan metode lain seperti slime) dianalisis untuk mengevaluasi distribusi ukuran.
Analisis kebersihan logam cair (LIMCA) – Ini adalah sensor on-line yang mendeteksi inklusi langsung dalam cairan. Partikel yang mengalir ke sensor ini melalui lubang kecilnya terdeteksi karena mengubah konduktivitas listrik melintasi celah.
Analisis tanggapan Coulter – Metode ini, yang mirip dengan LIMCA, dapat digunakan untuk mengukur distribusi ukuran inklusi yang diekstraksi oleh slime dan tersuspensi dalam air (inklusi lebih besar dari sub-mikron).
Teknik ultrasonik untuk sistem cair – Metode ini menangkap pantulan dari pulsa ultrasound untuk mendeteksi inklusi online dalam baja cair.
Metode pengujian ultrasonik terendam – Ini digunakan untuk menguji inklusi yang lebih besar dan menghasilkan hasil yang mengesankan. Untuk pengujian inklusi dengan ukuran di atas 120 mikron, sampel tunggal baja 500.000 cum, bidang giling paralel, dan direndam dalam tangki air dipindai dengan probe 10 MHz. Ini setara dengan 16.000 tes patah tulang biru. Tes ini tidak menghasilkan informasi tentang komposisi kimia inklusi, tetapi merupakan alat penting untuk proses tersebut. Untuk menguji inklusi yang lebih kecil, dimungkinkan untuk meningkatkan frekuensi probe ultrasonik menjadi 15 MHz, 25 MHz, 50MHz, atau bahkan lebih tinggi. Namun, saat frekuensi dan resolusi meningkat, ukuran volume sampel menurun.
Metode tidak langsung
Karena biaya, persyaratan waktu, dan kesulitan pengambilan sampel, kebersihan baja biasanya diukur di industri baja menggunakan total O2, pengambilan N2, dan metode tidak langsung lainnya.
Total pengukuran O2 -Total O2 dalam baja adalah jumlah dari O2 bebas (O2) dan O2 yang digabungkan sebagai NMI. O2 bebas atau O2 'aktif' dapat diukur dengan relatif mudah menggunakan sensor O2. Hal ini dikendalikan oleh termodinamika kesetimbangan dengan elemen deoksidasi, seperti Al. Karena O2 bebas tidak terlalu bervariasi, total O2 adalah ukuran tidak langsung yang masuk akal dari jumlah total inklusi oksida dalam baja. Karena populasi kecil inklusi besar dalam baja dan ukuran sampel kecil untuk pengukuran O2 total (biasanya 20 g), kemungkinan tidak ada inklusi besar dalam sampel. Bahkan jika sampel memiliki inklusi yang besar, kemungkinan akan diabaikan karena pembacaan yang sangat tinggi. Dengan demikian, kandungan O2 total benar-benar mewakili tingkat inklusi oksida kecil tetapi tidak yang lebih besar. Kandungan O2 total yang rendah, bagaimanapun, menurunkan kemungkinan inklusi oksida besar. Jadi total O2 masih merupakan indeks kebersihan baja yang sangat penting dan umum. Total O2 dalam baja LCAK terus menurun seiring berjalannya waktu, seiring dengan penerapan teknologi baru. Misalnya, pabrik baja dengan degassing vakum mencapai total O2 yang lebih rendah (10 ppm hingga 30 ppm) daripada pabrik baja dengan hanya pengadukan gas sendok (35 ppm hingga 45 ppm)). Total O2 umumnya turun setelah setiap langkah pemrosesan seperti pada sendok 40 ppm, pada tundish 25 ppm, pada cetakan 20 ppm, dan pada baja tuang 15 ppm.
Penjemputan N2 – Perbedaan kandungan N2 antara bejana pembuat baja (terutama sendok dan tundish) merupakan indikator dari udara yang masuk selama operasi pemindahan. Setelah deoksidasi, kandungan O2 terlarut yang rendah dari baja memungkinkan penyerapan udara yang cepat. Pengambilan N2 dengan demikian berfungsi sebagai ukuran tidak langsung kasar dari total O2, kebersihan baja, dan masalah kualitas dari inklusi reoksidasi. Dengan penerapan teknologi baru dan peningkatan operasi, pick-up N2 telah mati selama bertahun-tahun. Biasanya, pengambilan N2 dapat dikontrol pada 1 ppm hingga 3 ppm dari sendok ke cetakan. Dengan operasi transfer yang optimal untuk mengurangi masuknya udara, pengambilan N2 dapat diturunkan selama pengecoran kondisi tunak menjadi kurang dari 1 ppm. Tingkat N2 dalam baja LCAK umumnya dikendalikan pada tingkat 30 ppm sampai 40 ppm di sebagian besar pabrik baja. Ini dikendalikan terutama oleh konverter pembuatan baja atau operasi tungku listrik, tetapi dipengaruhi oleh operasi pemurnian dan selubung.
Pengukuran kehilangan Al terlarut – Untuk baja LCAK, kehilangan Al juga menunjukkan bahwa telah terjadi reoksidasi. Namun, ini adalah ukuran yang kurang akurat dibandingkan pengambilan N2 karena Al juga dapat dioksidasi ulang oleh terak.
Pengukuran komposisi terak- Analisis evolusi komposisi terak sebelum dan sesudah operasi dapat diinterpretasikan untuk memperkirakan penyerapan inklusi pada terak. Selain itu, entrainment terak dari bejana tertentu dapat ditentukan dengan mencocokkan elemen jejak dalam komposisi terak dan inklusi.
Penyumbatan nozzle masuk terendam (SEN) – Masa pakai SEN yang pendek karena penyumbatan umumnya merupakan indikator tingkat kebersihan baja yang rendah. Inklusi kecil Al2O3 dalam baja LCAK diketahui menyebabkan penyumbatan nozzle. Oleh karena itu, frekuensi penyumbatan SEN adalah metode kasar lainnya untuk mengevaluasi kebersihan baja.
Dengan demikian, terlihat bahwa tidak ada teknik tunggal yang ideal untuk mengevaluasi kebersihan baja. Beberapa teknik lebih baik untuk pemantauan kualitas sementara yang lain lebih baik dari sudut penyelidikan masalah. Oleh karena itu, perlu untuk menggabungkan beberapa metode bersama-sama untuk memberikan evaluasi kebersihan baja yang lebih akurat di pabrik baja. Kuantifikasi inklusi yang andal memungkinkan pengembangan generasi baru baja bersih.
Teknologi dan praktik operasional untuk baja bersih
Pembuatan baja sekunder telah menjadi alat yang diterima untuk mengelola kebersihan baja karena memungkinkan tidak hanya untuk membuat penambahan pada baja cair di bawah kondisi yang terkendali, tetapi juga berkontribusi pada pengadukan terak-logam yang hati-hati, pengurangan terak, pemangkasan suhu, penggabungan inklusi, eliminasi oleh flotasi dan jebakan dalam slag dan kontrol komposisi, penghilangan gas vakum, dan kadang-kadang deoksidasi C dll. Fungsi yang diperlukan untuk baja rekayasa telah tersedia untuk produsen baja dan sebagian dari mereka digunakan untuk semua kelas baja dan ini telah membuat perbedaan antara kualitas komersial dan baja khusus menjadi sedikit kabur.
Salah satu fitur penting dari pembuatan baja sekunder dan pengecoran kontinu adalah bahwa fungsi metalurgi tersebar di ruang di sepanjang jalur peralatan, digunakan sepanjang skala waktu, dan karenanya dapat distandarisasi, terkadang otomatis dan dikontrol dengan lebih baik. Di sisi lain, sumber kontaminasi telah berlipat ganda tetapi juga dapat dikendalikan dengan lebih baik. Ladle to tundish (ladle nozzle, sliding gate, dan ladle stream gas protection, dll.), tundish (bubuk, bendung, dam dan baffle, dan elemen bubbling dll.), tundish to mold (nozzle, sliding gate atau stopper rod, terendam nozzle dan gelembung gas dll.), cetakan (bubuk cetakan, kontrol level cetakan, dan geometri nozzle terendam dll.), pengecoran kontinu itu sendiri (cetakan lurus, melengkung, cetakan lurus dan melengkung, pengadukan elektromagnetik, rem elektromagnetik, dan cetakan berbentuk transversal kastor pelat tipis, dll.), semua telah menjadi bagian dari rantai proses dan berubah menjadi reaktor metalurgi sejati. Ungkapan 'metalurgi tundish' telah menjadi umum dan mesin pengecoran kontinyu, terutama cetakannya, juga bertindak sebagai reaktor metalurgi, di mana nasib NMI terus ditentukan.
Sejumlah besar teknologi dan praktik operasional di seluruh proses pembuatan baja sekunder untuk meningkatkan kebersihan baja, termasuk waktu dan lokasi penambahan agen deoksidasi dan paduan besi, tingkat dan urutan proses pembuatan baja sekunder, operasi pengadukan dan pemindahan. , sistem selubung, geometri dan praktik tundish, kapasitas penyerapan berbagai fluks metalurgi, dan praktik pengecoran.
Pembentukan dan kontrol komposisi kimia NMI melibatkan langkah-langkah yang berbeda dari proses produksi dan sistem industri di mana mereka dilakukan. Proses produksi harus dilaksanakan dengan hati-hati di setiap langkah untuk menghindari masalah yang berkaitan dengan (i) kesulitan selama operasi pengecoran yang terkait dengan penyumbatan nosel antara tundish dan cetakan (proses pengecoran kontinu) dan antara sendok dan kolom pengecoran (proses pengecoran ingot), dan (ii) efek merugikan pada sifat mekanik baja.
Pada akhir pembuatan baja di BOF (tungku oksigen dasar) atau EAF (tungku busur listrik), O2 berada dalam kesetimbangan dengan C, yang berarti tingkat yang sangat tinggi untuk kadar baja C rendah (1250 ppm O2 untuk 0,02 % C). Jika baja hanya untuk dipadatkan seperti itu, eutektik Fe, S, dan O2 mengendap di inter-dendritik, sementara deoksidasi C yang kuat terjadi pada tahap awal pemadatan, sehingga menghasilkan baja rimming, penuh dengan lubang sembur di dekat permukaan. Baja yang dihasilkan selain menjadi keropos juga rapuh selama operasi pengerolan panas atau penempaan panas dan penggunaan selanjutnya pada suhu kamar.
Untuk menghindari pengendapan eutektik besi O2 dan S, agen deoksidasi (C, terutama di bawah tekanan tereduksi, Mn, Si, Al, Ca, dan Ti dll.) dan agen desulfurisasi (Mn, dan Ca) dimasukkan ke dalam proses untuk mempromosikan keseimbangan baru dimana fase ketiga mengendap dan rimming dihindari sama sekali. Fase ketiga merupakan NMIs endogen (oksida, nitrida, karbida, sulfida, dan fosforida dll) yang awalnya dibuat dalam baja cair, biasanya di sendok. These equilibriums can be implemented by adding deoxidizing agents into liquid steel by bulk additions or wire injection or by ensuring that the liquid metal is in equilibrium with an active metallurgical slag of the proper composition.
The population NMIs changes all the time, since the existing inclusions coalesce, float out and get finally adsorbed in a slag or a simple covering powder or flux, by aggregation against refractory in the ladle, the tundish or inside nozzles that some of them (solid non-metallic inclusions, like Al2O3 or spinels) tend to clog. Steel and slag change as well, and inclusions entertain complex connection with them, at equilibrium, if time allows, or out of it. Gas evolution at the solidification front can still take place if N2 and H2 are not properly controlled. More inclusions appear, since temperature drops, which generally means more precipitation, or solidification starts, or O2 penetrates the system (reoxidation),from the slag, the refractories, from the atmosphere at refractory junctions (sliding gates, submerged nozzle mounting, and across the refractories etc.), or because the slag or the refractories generate new inclusions or release inclusions previously captured. The latter is known as the exogenous NMIs. Of course, the trend is generally towards improved cleanliness with all these mechanisms are being deeply looked into for finding counter-measures.
An important point regarding reoxidation is that the phenomenon does not take place at thermo-dynamic equilibrium, but rather generates oxides of whichever element happens to meet the incoming O2, most often generating Fe oxides. Out of the equilibrium in deoxidized liquid steel, these oxides later reverse back to equilibrium NMIs, if time permits.
The distinction between endogenous and exogenous NMIs is however somewhat ad-hoc, as deoxidation or reoxidation are actually an integral parts of the total process of the steelmaking and both result from the technology put in place to produce steel. As an example, deoxidation does not take place inside liquid steel, but at the interface of the deoxidizing agent injected.
NMIs are large enough to interact with the metal matrix as mechanical discontinuities, basically like holes. There are other third phases in steel of much smaller dimensions called precipitates, which interact with the matrix as the scale of dislocations or even at atomic scale. Precipitates, normally carbides or nitrides, constitute the key features of the micro-alloying of steels or of more substantial alloying like in tool steels or in stainless steels.
Steel refining and continuous casting operations have important effects on improving steel cleanliness. A systematic study of inclusion removal carried out in a steel plant has indicated that the ladle treatment drops inclusions by around 65 % to 75 %, the tundish removes inclusions by around 20 % to 25 %, although reoxidation can sometimes occur, and the mould removes inclusions around 5 % to 10 % of the total inclusions.
Ladle operations
The tap O2 content is measured during tapping the liquid steel in the ladle or before the addition of the deoxidizing agents. The value is typically high. It varies in a wide range (250 ppm to 1200 ppm) depending on the primary steelmaking practice. Al additions when used to deoxidize the steel, create larger amounts of Al2O3. This suggests that a limitation on tap O2 content is to be imposed for clean steel grades. However, there is no correlation between furnace practice and steel cleanliness, since around 85 % of the Al2O3 clusters formed after large additions of Al, float out to the ladle slag, and that the remaining clusters are smaller than 30 microns. Naturally, the decision to ignore tap O2 depends on the time available to float inclusions and on the availability of ladle refining, which can remove most of the generated inclusions. However the tap O2 content strongly affects the decarburization rate for producing ultra low C steel.
FeO and MnO in slag – An important source of reoxidation is the carryover slag from the converter to the ladle, which contains a high content of FeO and MnO. These oxides react with the dissolved Al to generate Al2O3 in liquid steel, owing to the strong favourable thermodynamics of the reactions 3FeO (l) + 2Al =Al2O3 + 3Fe (l), and 3MnO + 2Al =Al2O3 + 3Mn (l). The higher is the FeO and MnO content in the ladle slag, the greater is the potential for reoxidation and the corresponding generation of the Al2O3 inclusions. Many slivers in the final product have been traced to reoxidation that originated from FeO in the ladle slag.
Many counter-measures can be adapted to lower FeO and MnO contamination. These counter-measures are (i) minimizing of slag carryover from converter to ladle during tapping, (ii) increasing aim turndown C, (iii)avoiding the reblows, thus minimizing the dissolved O2 content in the steel and reduce the amount of FeO in the furnace slag, (iv) use of a sub-lance in the BOF substantially reduces the frequency of reblows, (v) use of an efficient mechanical slag stopper, such as a slag ball (which floats in steel and sinks in slag), and (vi) using other sensors which are alternatively available. A thick ladle slag layer after tapping suggests high slag carryover problems. In some plants, the ladle slag for critical grades is mechanically skimmed at the ladle furnace to a thickness in the range of 25 mm to 40 mm.
Ladle slag reduction treatment – It has been found that minimizing slag carryover, together with adding a basic ladle slag and basic lining to lower the ladle slag to less than 1 % to 2 % of FeO + MnO, can reduce total O2 content to 10 ppm for LCAK steel. Another way to lower the FeO + MnO content of the ladle slag is to add a slag conditioner (i.e. slag reduction or deoxidation treatment), which is a mixture of Al and burnt lime or limestone. There is a drop in FeO + MnO content after ladle slag reduction treatment. On an average, this treatment lowers the FeO + MnO level to below 5 %. This results in sharp improvement of coil cleanliness.
Effect of vacuum treatment and ladle stirring – Vacuum treatment of liquid steel started with the production of engineering steels for the automotive, power, and the aircraft sectors with the purpose of increasing the reliability and life of the mechanical parts of vehicles or nuclear reactors. The major need is to control the H2 level in liquid steel (to less than 1 ppm in a C steel) in order to avoid its departure at solidification and its entrapment in the solid, which leads to serious integrity defects during the use of the steel part. The use of vacuum, which removes H2 straight forwardly, came into existence in the steelmaking shops, using various technologies like tank degassing, stream degassing, and DH and RH (Rheinstahl Heraeus) ladle degassing processes. The vacuum degassing besides reducing the non-metallic inclusions, also allows other benefits such as (i) C deoxidation, which has the major advantage of producing gaseous deoxidation products, (ii) intensive stirring with its several advantages, (iii) allows for the time management in the logistics of ladle flow, hence on the quality of temperature control of liquid steel, and (iv) reheating of the liquid steel by Al and O2 injections.
Ladle stirring and the ladle degassing processes greatly promote inclusion growth and removal. The effect of vacuum treatments on the cast steel inclusion levels shows the improvement of steel cleanliness over argon (Ar) stirring in the ladle. The pronounced benefit of Ca-based powder injection is due to its greater stirring power in addition to its primary effect of deoxidization and liquefying inclusions. The vacuum degassing and Ca treatment together can drop the total O2 to 15 ppm level.
However, excessive stirring is detrimental, since the upward circulation of steel onto the slag layer can expose an ‘eye’ region of the steel surface to reoxidation as well as due to the refractory erosion. Sufficient stirring time (more than 10 min) after the addition of ferro-alloys is also important, to allow the Al2O3 inclusions to circulate upto the slag and be removed. In some plants, the practice of first stirring vigorously to encourage the collision of small inclusions into large ones, followed by a ‘final stir’ which slowly re-circulates the steel to facilitate the removal of inclusions into the slag while minimizing the generation of more large inclusions via collisions.
Tundish operation
Important phenomena which are taking place in the tundish are shown the Fig 2. The factors which are affecting the steel cleanliness are (i) casting transitions, (ii) tundish refractory lining, (iii) tundish flux, (iv) gas stirring, and (v) tundish flow control.
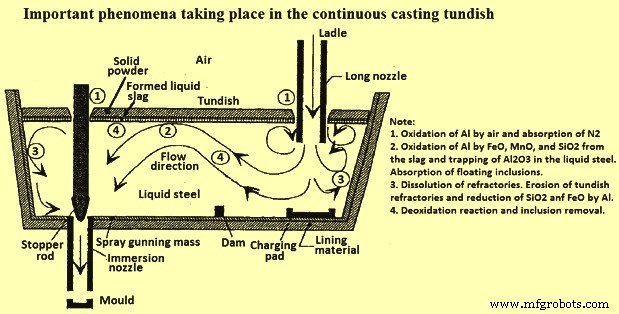
Fig 2 Important phenomena taking place in the continuous casting tundish
Casting transitions – Casting transitions occur at the start of casting, during ladle exchanges and SEN (submerged entry nozzle) changes, and at the end of the casting sequence. Inclusions are often generated during transitions and can continue for a long time, hence contaminate a large quantity of steel. During these unsteady casting periods, slag entrainment and air absorption are more likely, which induce reoxidation problems
During the first casting heat, the entrainment of air and slag in the tundish pour box due to the turbulence during ladle open is accompanied by an initial maximum in total O2 content in the tundish (including both slag and Al2O3 inclusions). Open pouring at the start of the casting causes total O2 in tundish to increase to twice normal levels for more than an entire heat. Several minutes of filling are needed before tundish flux can be added. Eventually, during steady casting, the total O2 decreases to lower levels, consisting mainly of Al2O3.
One improvement during ladle transitions is to stop the flow of liquid into the mould until the tundish is filled and to bubbling gas through the stopper to promote inclusion flotation. Another improvement effect is to open new ladles with submerged shrouding. With this measure, the total O2 is decreased with more consistent quality throughout the sequence. Near the end of a ladle, ladle slag can enter the tundish, due in part to the vortex formed in the liquid steel near the ladle exit. This phenomenon needs some steel to be kept in the ladle upon closing (example 5 ton ‘heel’). In addition, the tundish depth drops after ladle close, which disrupts normal tundish flow and can produce slag vortexing, slag entrainment, and increased total O2 in the mould.
Lapisan tahan api tundish – Dissolved Al in the liquid steel reacts with an O2 source in the lining refractory. The extent of this reaction can be quantified by monitoring the Si content of the liquid steel. The O2 for the reaction can come from CO (carbon monoxide) when C in the refractory reacts with binders and impurities or from SiO2 refractory decomposition. SiO2 based tundish linings are worse than MgO based sprayed linings.
Tundish flux – The tundish flux is to carry out many functions. Firstly, it is to insulate the liquid steel both thermally (to prevent excessive heat loss) and chemically (to prevent air entrainment and reoxidation). Further, the tundish flux with lower SiO2 content can decrease N2 pick-up from the ladle to the mould substantially. Secondly, in ideal circumstances, the flux is also to absorb inclusions to provide additional steel refining. A normal tundish flux is burnt rice husk, which is inexpensive, a good insulator, and provides good coverage without crusting. However, rice husk is high in SiO2 (around 80 %), which can be reduced to form a source of inclusions. Also, rice husk is very dusty and with their high C content, (C around 10 %), can contaminate ultra low C steel.
Basic flux (CaO-Al2O3-SiO2 based) is theoretically better than burnt rice husk at refining LCAK steels, and has been correlated with lower O2 in the tundish. Use of basic tundish flux (CaO-40 %, Al2O3-24 %, MgO-18 %, SiO2-5 %, Fe2O3-0.5 %, and C-8 %), together with baffles, significantly lowers the total O2 fluctuation, as compared to the flux (CaO-3 %, Al2O3-10 % to 15 %, MgO-3 %, SiO2- 65 % to 75 %, and Fe2O3-2 % to 3 %). The basic flux, however, show similar results for other parameters as compared to rice husk, may be because the basic flux also contains a high content of SiO2. The basic flux is thus ineffective since it easily forms a crust at the surface, owing to its faster melting rate and high crystallization temperature. Also, basic flux normally has lower viscosity, and hence it is more easily entrained. To avoid these issues, some steel plants use a two-layer flux, with a low-melting point basic flux at the bottom to absorb the inclusions, and a top layer of rice husk to provide insulation, which lowers the total O2.
Tundish stirring – Injecting inert gas into the tundish from its bottom improves mixing of the liquid steel, and promotes the collision and removal of inclusions. This technology lowers the total O2 in the tundish. The danger with this technology is that any inclusions-laden bubbles which escape the tundish and become entrapped in product result into severe defects in the product.
Tundish flow control -The tundish flow pattern is to be designed to increase the liquid steel residence time, prevent the ‘short circuiting’ and promote inclusions removal. Tundish flow is controlled by its geometry, level, inlet (shroud) design, and flow control devices such as impact pads, weirs, dams, baffles, and filters. The tundish impact pad is an inexpensive flow control device which suppresses turbulence and prevents erosion of the tundish bottom where the liquid steel stream from the ladle impinges the tundish. The incoming stream momentum is diffused and allows the naturally buoyancy of the warm incoming steel to avoid short circuiting, particularly at startup. Together with weir and dam, the impact pad improves steel cleanliness, especially during ladle exchanges.
Transfer operations
One of the most important sources of O2 pick-up is atmospheric reoxidation of steel during the transferring from ladle to tundish or from tundish to mould. This generates inclusions which cause production problems such as nozzle clogging, in addition to defects in the final product. Optimization of shrouding system is very important to prevent this phenomenon. Using a shroud lowers the N2 pick-up relative to open pouring. Replacing the tundish pour box with a ladle shroud and dams also lowers the N2 pick-up (ladle to tundish) and also lowers the slag entrainment during transitions.
Ladle opening – Ladle self open is a heat in which the ladle nozzle does not have to be lanced open, but opens on its own. When the nozzle is to be lanced open, then the shroud is to be removed. The cast is unshrouded from ladle to tundish during the first 600 mm to 1200 mm of the cast, and hence the reoxidation by air occurs. Hence, the total O2 level for the self-open ladle is lower than the lanced-opened ladle. Careful packing ladle opening sand is helpful to realize ladle self open.
Argon protection – Argon protection is used to prevent the liquid steel from air reoxidation. When adding the tundish flux too early, the flux can be entrapped into liquid steel and cast into the steel, thus normally there is no protective cover for the first few minutes of a cast. Also at the period of ladle opening, air is very easy to reach liquid steel. The effects of these two factors can last upto 15 minutes into the cast for a tundish of 60 ton capacity. For countering this problem, purging the tundish with inert gases (to displace the air) prior to opening the ladle into the tundish is adopted in some steel plants. Another measure to improve shrouding system for lowering of total O2 is to incorporate an appropriate gas injection.
Sealing issues –For decreasing the N2 pick-up during continuous casting, the factors normally considered are sealing of shroud from ladle to tundish, and SEN from tundish to the mould.
Nozzle clogging – In addition to interfering with production, the clogging of tundish nozzle and SEN is detrimental to steel cleanliness for three reasons. Firstly, dislodged clogs either become trapped in the steel, or they change the flux composition, leading to defects in either case. Secondly, clogs change the nozzle flow pattern and jet characteristics leaving the nozzle, which disrupt flow in the mould, leading to slag entrapment and surface defects. Thirdly, clogging interferes with mould level control, as the flow control device tries to compensate for the clog. Several practices can used to minimize clogging. In addition to taking general measures to minimize inclusions, clogging via refractory erosion can be countered by controlling nozzle refractory composition, (example avoiding of Na, K, and Si impurities), or coating the nozzle walls with pure Al2O3, BN, or other resistant materials.
Mould and continuous casting machine (CCM) operation
The casting of liquid steel in a continuous casting machine (CCM) involves many phenomena, shown in Fig 3, which have far reaching consequences on the strand quality. Inclusions carried into the mould through the nozzle include deoxidation products, nozzle clogs, and entrained of tundish/ladle slag (reoxidation by SiO2, FeO, and MnO in the slag), and reoxidation products from air absorption from nozzle leaks. Mould slag can be entrained by excessive top surface velocities or level fluctuations. New inclusions can precipitate as the superheat drops, such as TiO2 inclusions in Ti-treated steels. On the other hand, inclusions can be removed into the slag/steel interface by buoyancy flotation, fluid flow transport, and attachment to the bubble surfaces.
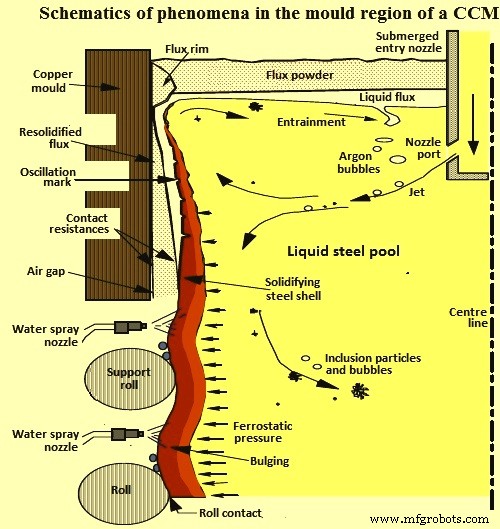
Fig 3 Schematics of the phenomena in the mould region of a CCM
The mould is the last refining equipment where inclusions are either safely removed into the top slag layer or get entrapped into the solidifying shell to form permanent defects in the cast product. Important insight into inclusion entrapment has been obtained in the past through collecting statistical data and conducting trials on the operating CCMs. It has been noticed that increasing steel flow rate increases the level of pencil blisters (from Ar bubble entrapment) considerably, while it reduces the level of slivers (from slag entrapment). While measuring the inclusion and bubble distribution in the cast steel, it has been observed that individual 1 mm bubbles are often coated with inclusion clusters, and can be carried from far upstream, even if no gas is injected into the tundish nozzle. It has been also observed that the inclusion entrapment varies from side to side, which suggests a link with variations in the transient flow structure of the lower recirculation zone.
Defects are frequently found associated with transients in the process, such as changes in casting speed, tundish changes, or clogged nozzles. Pencil pipe defects occur intermittently and are rare, relative to the quantity of injected gas. The conclusions made in one of the study are that 80 % the particle are eventually removed to meniscus (20 % entrapped in cast product), and a given particle circulate for upto 300 seconds before being removed or entrapped.
In a CCM with curved-mould, inclusions are preferentially trapped 1 m to 3 m below the meniscus. Thus, inclusions concentrate at one-eighth to one-quarter of the thickness from the top of the inside radius surface, in addition to the surfaces. It has also been reported that the electromagnetic stirring can improve the steel cleanliness by lowering the total O2 content in the cast product. CCM with curved mould machines are known to entrap many more particles than the CCM with straight (vertical) mould, since the inclusion spiral upwards the inside radius, where they collect at a specific distance through the thickness , corresponding to 2 m to 3 m below the meniscus.
It has been reported that the cast speed has its effect on the slivers. High speeds and high variation in casting speed result in a higher rate of slivers. Adequate stable casting speeds can be obtained with the use of a stopper. With a stopper, the speed is no longer determined by the level of steel in the tundish, but by the level of steel in the mould. It is better to control mould level control in the range +/- 3 mm. A beneficial tool for the optimizing of the fluid flow and hence improving the quality of the cast product is the electromagnetic brake (EMBR), which bends the jet and shortens its impingement depth, inclusions thus move more upwards, tend to top powder or be captured by the solidified shell at the surface of the cast product. After the use of EMBR, the inclusions distribution shows that there is a shift to the surface of the cast product.