Pembakaran Bahan Bakar dan Perpindahan Panas di Tungku
Pembakaran Bahan Bakar dan Perpindahan Panas di Tungku
Panas dibutuhkan dalam tungku untuk memanaskan muatan tungku (bahan yang akan dipanaskan di tungku) dan kadang-kadang untuk reaksi kimia. Tiga sumber energi panas adalah (i) pembakaran bahan bakar, (ii) energi listrik, dan (iii) energi kimia yang tersedia melalui reaksi eksoterm. Selain tungku elektro-termal, kebutuhan panas ini (tidak termasuk energi kimia) dipenuhi melalui pembakaran bahan bakar. Bahan bakar dapat berupa bahan bakar gas (misalnya gas produk sampingan seperti gas oven kokas, gas tanur sembur, dan gas konverter, gas alam, dan gas minyak cair dll.), bahan bakar cair (misalnya bahan bakar minyak, dan tar, dll.) , atau bahan bakar padat (misalnya batu bara, dan kokas, dll.).
Semua bahan bakar mengandung energi potensial. Pada pembakaran, energi potensial ini dilepaskan dalam produk pembakaran (POC). Pembakaran biasanya dianggap sebagai pelepasan panas dan energi yang terkontrol dari reaksi kimia antara bahan bakar dan oksidator. Hampir semua pembakaran dalam proses industri menggunakan bahan bakar hidrokarbon. Reaksi pembakaran umum untuk bahan bakar hidrokarbon tipikal diberikan oleh persamaan bahan bakar + oksidator =karbon di-oksida (CO2) + uap air (H2O) + spesies lain. 'Spesies lain' tergantung pada jenis oksidator yang digunakan dan rasio bahan bakar terhadap oksidator. Oksidator yang paling umum digunakan adalah udara, yang terdiri dari hampir 79% nitrogen (N2) berdasarkan volume dan umumnya dibawa melalui proses pembakaran. Jika pembakarannya kaya bahan bakar, artinya tidak ada cukup oksigen (O2) untuk membakar bahan bakar sepenuhnya, maka ada hidrokarbon yang tidak terbakar dalam produk buangan dan sedikit, jika ada, kelebihan O2. Jika pembakaran bahan bakar kurus, berarti ada lebih banyak O2 daripada yang dibutuhkan untuk membakar bahan bakar sepenuhnya, dan kemudian ada kelebihan O2 dalam produk buangan.
Bahan bakar memiliki pengaruh yang signifikan terhadap perpindahan panas dalam sistem pembakaran tungku. Salah satu sifat yang paling penting adalah nilai kalor bahan bakar. Ini digunakan untuk menentukan berapa banyak bahan bakar yang akan dibakar untuk memproses laju produksi yang diinginkan dari bahan yang sedang dipanaskan. Nilai kalor ditentukan sebagai nilai kalor yang lebih tinggi (HHV) atau nilai kalor yang lebih rendah (LHV).
LHV tidak termasuk panas penguapan, yang merupakan energi yang dibutuhkan untuk mengubah air cair menjadi uap. Ini berarti bahwa LHV mengasumsikan semua POC adalah gas, yang biasanya terjadi pada hampir semua aplikasi pembakaran industri. Jika produk pembakaran akan meninggalkan proses pada suhu yang cukup rendah sehingga semua air diubah dari gas menjadi cair, maka panas kondensasi akan dilepaskan ke dalam proses sebagai sumber energi tambahan. HHV bahan bakar termasuk energi tambahan ini.
Komposisi bahan bakar penting dalam menentukan komposisi POC dan jumlah oksidator yang dibutuhkan untuk membakar bahan bakar. Kepadatan bahan bakar diperlukan untuk menentukan laju aliran melalui sistem pengiriman bahan bakar tungku dan ukuran pipa terkait.
Komposisi gas buang sangat penting dalam menentukan perpindahan panas di dalam tungku. Hidrokarbon yang tidak terbakar di knalpot menunjukkan bahwa bahan bakar belum sepenuhnya terbakar dan karenanya semua panas yang tersedia belum dilepaskan. Kadar O2 berlebih yang tinggi dalam gas buang biasanya menunjukkan bahwa terlalu banyak oksidator yang disuplai. Oksidator berlebih membawa energi yang masuk akal keluar melalui gas buang. Ini sekali lagi berarti bahwa sebagian panas bahan bakar yang tersedia belum sepenuhnya digunakan untuk memanaskan muatan tungku. Jika oksidatornya adalah udara, maka sebagian besar energi yang tersedia dalam bahan bakar dilakukan dalam cerobong asap bersama produk buangan.
POC mentransfer energi panas ke muatan tungku untuk menaikkan suhunya ke nilai yang diperlukan dan kemudian meninggalkan tungku. Panas sensibel dalam POC pada suhu proses kritis tidak tersedia untuk tungku. Semakin tinggi suhu kritis proses, semakin tinggi panas sensibel dalam POC. Panas sensibel dalam POC ini sangat penting dari sudut pandang penggunaan bahan bakar.
Ada dua jenis oksidator yang umum digunakan dalam proses pembakaran industri. Sebagian besar proses menggunakan udara sebagai oksidator. Namun, banyak dari proses suhu yang lebih tinggi menggunakan oksidator yang mengandung konsentrasi O2 yang lebih tinggi daripada yang tersedia di udara (sekitar 21% berdasarkan volume). Jenis pembakaran ini disebut sebagai pembakaran yang ditingkatkan O2. Dalam banyak kasus, laju produksi dalam proses pemanasan dapat ditingkatkan secara signifikan hanya dengan pengayaan O2 dalam jumlah yang relatif kecil.
Dalam beberapa kasus, pembakar udara/bahan bakar dapat berhasil beroperasi dengan oksidator yang mengandung hingga sekitar 30% O2 dengan sedikit atau tanpa modifikasi. Pada konsentrasi O2 yang lebih tinggi, nyala api bisa menjadi tidak stabil atau suhu nyala api bisa menjadi terlalu tinggi untuk pembakar yang dirancang untuk beroperasi di bawah kondisi udara/bahan bakar. Dalam aplikasi suhu yang lebih tinggi, di mana manfaat kemurnian O2 yang lebih tinggi membenarkan biaya tambahan, pengoksidasi dengan kemurnian lebih tinggi dapat digunakan (lebih besar dari 90% O2). Proses pemanasan sangat diintensifkan oleh kemurnian tinggi O2. Kemurnian oksidator memiliki pengaruh yang signifikan terhadap perpindahan panas dalam sistem pembakaran.
Aspek penting dalam sistem pembakaran adalah rasio bahan bakar dengan oksidator. Ada banyak cara yang dengannya hal ini dapat ditentukan. Ini dibahas di sini secara singkat. Reaksi pembakaran global menggunakan CH4 (metana) sebagai bahan bakar dapat ditulis sebagai CH4 + (xO2 + yN2) =CO, CO2, H2, H2O, N2, NOx, O2, trace component. Stoikiometri reaksi menunjukkan rasio O2 terhadap bahan bakar untuk sistem pembakaran tertentu. Salah satu metode untuk mengukur stoikiometri adalah dengan hanya mempertimbangkan O2 dalam oksidator, karena inert dalam oksidator tidak diperlukan untuk reaksi. Oleh karena itu, dengan mempertimbangkan CH4 sebagai bahan bakar, reaksi stoikiometri sederhana global dengan udara dapat ditulis sebagai CH4 + (2O2 + 7.52N2) =CO2 + 2H2O + 7.52N2. Dalam reaksi ini, udara direpresentasikan sebagai 2O2 + 7.52N2. Di sini rasio stoikiometrinya adalah 2 karena 2 molekul O2 diperlukan untuk membakar satu molekul CH4.
Metode penentuan rasio stoikiometri ini umumnya digunakan untuk sistem pembakaran yang menggabungkan pengayaan O2. Ini karena jumlah O2 yang dipasok ke sistem pembakaran sangat penting.
Nyala api yang sebenarnya umumnya membutuhkan beberapa O2 berlebih untuk pembakaran bahan bakar yang sempurna. Hal ini disebabkan pencampuran yang tidak sempurna antara bahan bakar dan oksidator. Untuk pembakaran CH4 yang kaya bahan bakar, rasio stoikiometrinya kurang dari 2. Dalam kasus pembakaran tanpa bahan bakar CH4, rasio stoikiometrinya lebih besar dari 2. Oleh karena itu, komposisi oksidator penting. Cara umum untuk menentukan komposisi oksidator adalah dengan menghitung fraksi mol O2 dalam oksidator.
Banyak proses pembakaran industri berjalan dengan sekitar 3% lebih banyak O2 daripada yang dibutuhkan secara teoritis untuk pembakaran sempurna. Ini sering kali merupakan jumlah kelebihan O2 yang dibutuhkan untuk meminimalkan emisi hidrokarbon yang tidak terbakar dan memastikan pembakaran bahan bakar yang sempurna. Hal ini dapat terjadi karena keterbatasan pencampuran antara bahan bakar dan oksidator, terutama pada sistem non-premix.
Terlalu banyak kelebihan O2 berarti energi yang terbuang dalam pemanasan udara pembakaran berlebih, bukan biaya tungku. Oleh karena itu, sangat disarankan untuk hanya menggunakan kelebihan O2 yang cukup untuk mendapatkan emisi CO (karbon mono-oksida) yang rendah. Contoh reaksi global yang disederhanakan untuk CH4 dengan 3% kelebihan O2 adalah reaksi CH4 + (2.06O2 + 7.75N2) =CO2 + 2H2O + 0,06O2 + 7.75N2.
Sebagian besar nyala api industri bersifat turbulen yang umumnya ditentukan oleh bilangan Reynolds turbulen (Re). Skala panjang karakteristik turbulen biasanya disebut panjang Kolmogorov. Panjang Kolmogorov mewakili dimensi di mana disipasi terjadi. Skala panjang Taylor dapat didefinisikan sebagai rasio laju regangan terhadap gaya viskos. Berbagai panjang dapat digunakan untuk mengkarakterisasi nyala api. Nyala api dapat berupa (i) nyala berkerut, (ii) nyala berkerut parah, (iii) nyala api di pusaran, dan (iv) reaksi terdistribusi. Bilangan Damköhler (Da) non-dimensi menunjukkan jenis waktu reaksi yang signifikan untuk jenis reaksi pembakaran tertentu. Angka ini adalah rasio waktu reaksi terhadap laju aliran.
Sifat pembakaran
Sifat pembakaran normal yang umumnya digunakan dalam aplikasi industri adalah (i) komposisi produk pembakaran, (ii) suhu nyala, (iii) panas yang tersedia, dan (iv) volume gas buang setelah pembakaran. Ini penting dalam menghitung perpindahan panas dari nyala api. dan gas buang ke tungku dan ke muatan tungku.
Produk pembakaran
Ada sejumlah variabel yang dapat memiliki dampak signifikan pada produk pembakaran. Beberapa variabel penting termasuk komposisi oksidator, rasio pencampuran, suhu pemanasan awal udara dan bahan bakar, dan komposisi bahan bakar. Ini dibahas secara singkat di bawah ini.
Komposisi pengoksidasi – Mengambil contoh pembakaran CH4, pembakaran stoikiometri CH4 dengan udara dapat diwakili oleh persamaan global CH4 + 2O2 + 7.52N2 =CO2, 2H2O, 7.52N2, dan komponen jejak. Dapat dilihat bahwa lebih dari 70 persen volume gas buang adalah N2. Demikian pula, proses pembakaran O2/CH4 stoikiometrik dapat diwakili oleh persamaan CH4 + 2O2 =CO2, 2H2O, dan spesies jejak. Volume gas buang sangat berkurang dengan eliminasi N2. Secara umum, proses pembakaran CH4 dengan peningkatan O2 secara stoikiometri dapat direpresentasikan dengan persamaan CH4 + 2O2 + xN2 =CO2 + 2H2O + xN2 + komponen jejak.
Komposisi sebenarnya dari produk buangan dari reaksi pembakaran tergantung pada beberapa faktor, termasuk komposisi oksidator, suhu gas, dan rasio ekivalensi. Rasio ekivalen didefinisikan sebagai rasio rasio bahan bakar/udara aktual dengan rasio bahan bakar/udara stoikiometrik. Pembakaran stoikiometrik terjadi ketika semua O2 dikonsumsi dalam reaksi, dan tidak ada molekul O2 dalam produk.
Proses adiabatik berarti bahwa tidak ada panas yang hilang selama reaksi, atau reaksi terjadi dalam ruang yang terisolasi sempurna. Ini tidak terjadi dalam proses pembakaran yang sebenarnya di mana panas hilang dari nyala api oleh radiasi. Produk utama yang diprediksi untuk pembakaran kesetimbangan adiabatik CH4 adalah fungsi dari komposisi oksidator.
Proses kesetimbangan berarti bahwa ada jumlah waktu yang tak terbatas untuk reaksi kimia berlangsung, atau produk reaksi tidak dibatasi oleh kinetika kimia. Namun, dalam kondisi sebenarnya, reaksi pembakaran selesai dalam sepersekian detik. Selanjutnya, saat N2 dihilangkan dari oksidator, konsentrasi N2 dalam produk buangan juga menurun. Demikian juga terjadi peningkatan konsentrasi CO, CO2 dan H2O. Untuk proses adiabatik ini, terdapat sejumlah besar CO pada tingkat O2 yang lebih tinggi dalam oksidator.
Produk radikal H, O, dan OH semuanya meningkat dengan O2 dalam oksidator. NO (nitrat oksida) awalnya meningkat dan kemudian menurun setelah sekitar 60% O2 dalam oksidator karena semakin banyak N2 yang dikeluarkan dari sistem. Ketika pengoksidasi adalah O2 murni, NO tidak terbentuk karena tidak ada N2 yang tersedia. Bahan bakar yang tidak terbakar dalam bentuk H2 dan oksidator yang tidak bereaksi dalam bentuk O2 juga meningkat dengan meningkatnya konsentrasi O2 dalam oksidator. Peningkatan konsentrasi radikal ini, bahan bakar yang tidak terbakar dalam bentuk CO dan H2, dan O2 yang tidak bereaksi semuanya disebabkan oleh disosiasi kimia yang terjadi pada suhu tinggi.
Suhu nyala api sebenarnya lebih rendah dari suhu nyala api kesetimbangan adiabatik karena pembakaran yang tidak sempurna dan radiasi dari nyala api. Suhu nyala api yang sebenarnya ditentukan oleh seberapa baik nyala api memancarkan panasnya dan seberapa baik sistem pembakaran, termasuk muatan tungku dan dinding refraktori, menyerap radiasi tersebut.
Nyala api yang sangat bercahaya umumnya memiliki suhu nyala yang lebih rendah daripada nyala api yang sangat tidak bercahaya. Suhu nyala yang sebenarnya juga lebih rendah ketika muatan tungku dan dinding lebih menyerap radiasi. Ini terjadi ketika muatan tungku dan dinding berada pada suhu yang lebih rendah dan memiliki serapan pancaran yang lebih tinggi.
Sebagai produk pembakaran gas meninggalkan api, mereka biasanya kehilangan lebih banyak panas oleh konveksi dan radiasi saat mereka berjalan melalui ruang bakar. Tujuan dari proses pembakaran adalah untuk mentransfer energi kimia yang terkandung dalam bahan bakar ke muatan tungku, atau dalam beberapa kasus ke ruang bakar. Semakin efisien termal proses pembakaran, semakin banyak panas yang dipindahkan dari produk pembakaran ke muatan tungku dan ke ruang bakar. Oleh karena itu, suhu gas di cerobong asap diinginkan jauh lebih rendah daripada di nyala api dalam proses pemanasan yang efisien secara termal. Komposisi produk pembakaran kemudian berubah dengan suhu gas.
Rasio campuran – Konsentrasi O2 dan N2 dalam gas buang menurun drastis dengan rasio ekivalensi. Konsentrasi H2O dan CO2 memuncak pada kondisi stoikiometri. Ini penting karena kedua gas ini menghasilkan radiasi gas yang tidak bercahaya. Bahan bakar yang tidak terbakar dalam bentuk H2 dan CO keduanya meningkat dengan rasio ekivalen. Hal ini tercermin dalam panas yang tersedia karena tidak semua bahan bakar habis terbakar.
Suhu pemanasan awal udara dan bahan bakar – Dalam banyak proses pembakaran industri, panas diperoleh kembali untuk meningkatkan efisiensi termal keseluruhan proses guna mengurangi biaya pengoperasian. Panas yang diperoleh kembali biasanya digunakan untuk memanaskan awal udara pembakaran yang masuk dan kadang-kadang digunakan untuk memanaskan bahan bakar yang masuk. Pemanasan awal baik udara atau bahan bakar mempengaruhi komposisi produk pembakaran. CO2, H2O, dan N2 dengan semua penurunan gas buang dengan pemanasan awal udara, karena disosiasi kimia. Karena pertimbangan keselamatan dan kemungkinan menyedot pipa pasokan bahan bakar, suhu pemanasan awal bahan bakar yang lebih tinggi tidak praktis atau direkomendasikan di sebagian besar kondisi. Secara umum terlihat bahwa hanya ada sedikit penurunan konsentrasi komponen utama dan sedikit peningkatan konsentrasi komponen minor gas buang. Hal ini disebabkan oleh kenyataan bahwa massa bahan bakar relatif kecil dibandingkan dengan massa udara pembakaran yang disuplai ke sistem pembakaran. Ini berarti bahwa pemanasan awal udara pembakaran memiliki dampak yang jauh lebih signifikan daripada pemanasan awal bahan bakar untuk suhu pemanasan awal tertentu.
Komposisi bahan bakar – Produk pembakaran tergantung pada komposisi bahan bakar. Komposisi produk pembakaran yang diprediksi untuk bahan bakar yang berbeda di bawah berbagai kondisi operasi dapat dihitung. Bahan bakar gas yang paling umum digunakan adalah H2 (hidrogen), CH4, C3H8 (propana), dan campuran H2 dan CH4. Ini dimaksudkan untuk mewakili bahan bakar yang biasanya digunakan dalam aplikasi industri. Dalam hal luminositas, H2 menghasilkan nyala api yang tidak bercahaya, CH4 menghasilkan nyala api dengan luminositas rendah, dan C3H8 menghasilkan nyala api dengan luminositas yang lebih tinggi.
Suhu api – Temperatur nyala api merupakan variabel kritis dalam menentukan perpindahan panas dari nyala api ke muatan tungku. Temperatur nyala adiabatik dipengaruhi oleh oksidator dan komposisi bahan bakar, rasio pencampuran, dan temperatur pemanasan awal udara dan bahan bakar. Namun, suhu nyala api sebenarnya tidak setinggi suhu nyala api adiabatik, tetapi trennya sebanding dan mewakili kondisi sebenarnya.
Pengoksidasi dan komposisi bahan bakar – Suhu nyala meningkat secara signifikan ketika udara diganti dengan O2 karena N2 bertindak sebagai pengencer yang mengurangi suhu nyala. Temperatur nyala biasanya bervariasi untuk udara dan O2 murni. Ada peningkatan yang cepat dalam suhu nyala api dari udara hingga sekitar 60% O2 dalam oksidator. Temperatur nyala meningkat pada tingkat yang lebih lambat untuk konsentrasi O2 yang lebih tinggi. Juga, komposisi bahan bakar memiliki dampak yang kuat pada suhu nyala. Dalam campuran bahan bakar H2 dan CH4, suhu meningkat seiring dengan meningkatnya kandungan H2 dalam campuran. Penting untuk dicatat bahwa peningkatannya tidak linier, dengan peningkatan yang lebih cepat pada tingkat H2 yang lebih tinggi. Karena biaya H2 yang relatif tinggi dibandingkan dengan CH4 dan C3H8, H2 tidak digunakan dalam banyak aplikasi industri. Namun, bahan bakar H2 tinggi sering digunakan dalam banyak aplikasi hidrokarbon. Bahan bakar ini adalah produk sampingan dari proses pembuatan bahan kimia dan karenanya jauh lebih murah daripada membeli H2 dari pemasok gas industri dan lebih hemat biaya daripada menggunakan bahan bakar lain yang dibeli.
Rasio pencampuran – Suhu nyala puncak terjadi pada kondisi stoikiometri. Semakin rendah konsentrasi O2 dalam oksidator, semakin berkurang suhu nyala api dengan beroperasi pada kondisi non-stoikiometrik (baik bahan bakar kaya atau bahan bakar kurus). Hal ini disebabkan konsentrasi N2 yang lebih tinggi, yang menyerap panas dan menurunkan suhu keseluruhan. Pada kondisi stoikiometri, hanya ada cukup oksidator untuk membakar semua bahan bakar. Setiap oksidator tambahan menyerap energi yang masuk akal dari nyala api dan mengurangi suhu nyala. Pada sebagian besar nyala api nyata, suhu nyala puncak sering terjadi pada kondisi sedikit bahan bakar. Ini karena pencampuran yang tidak sempurna di mana sedikit lebih banyak O2 diperlukan untuk membakar semua bahan bakar sepenuhnya. Hampir semua aplikasi pembakaran industri dijalankan pada kondisi hemat bahan bakar untuk memastikan bahwa emisi CO rendah. Oleh karena itu, tergantung pada desain burner yang sebenarnya, suhu nyala api dapat mendekati puncaknya, yang seringkali diinginkan untuk memaksimalkan perpindahan panas. Satu masalah yang sering dihadapi ketika memaksimalkan suhu nyala adalah bahwa emisi NOx (oksida dari N2) juga dimaksimalkan karena NOx meningkat kira-kira secara eksponensial dengan suhu gas. Hal ini menyebabkan banyak konsep desain untuk mengurangi suhu nyala api puncak dalam nyala api untuk meminimalkan emisi NOx. Ini juga mempengaruhi perpindahan panas dari nyala api.
Suhu pengoksidasi dan pemanasan awal bahan bakar – Suhu nyala adiabatik bervariasi dan merupakan fungsi dari suhu pemanasan awal oksidator untuk nyala api udara/CH4 dan O2/CH4. Kenaikan suhu nyala relatif kecil untuk nyala O2/CH4 karena kenaikan panas sensibel O2 hanya sebagian kecil dari energi kimia yang terkandung dalam bahan bakar. Untuk api udara/CH4, pemanasan awal udara memiliki dampak yang lebih dramatis karena peningkatan panas sensibel sangat signifikan karena massa udara yang besar dalam reaksi pembakaran. Suhu nyala adiabatik meningkat dengan cepat untuk nyala api udara/bahan bakar di banyak bahan bakar.
Panas yang tersedia – Panas yang tersedia dalam sistem pembakaran tungku penting dalam penentuan efisiensi termal keseluruhan dan karenanya merupakan faktor saat menghitung perpindahan panas dalam proses. Kurang efektif untuk mencoba memaksimalkan perpindahan panas dalam sistem yang secara inheren memiliki panas yang tersedia rendah. Panas yang tersedia didefinisikan sebagai nilai kalor kotor bahan bakar, dikurangi energi yang dilakukan dari proses pembakaran oleh gas buang panas.
Panas kotor yang tersedia (GAH) dalam tungku diberikan oleh persamaan GAH =nilai kalor bahan bakar + panas sensibel reaktan – panas yang dibawa oleh POC meninggalkan tungku. GAH mewakili panas yang tersedia pada suhu proses kritis. Itu tidak mewakili panas yang tersedia untuk melakukan fungsi tertentu karena berbagai jenis kerugian. Ini dapat digunakan sebagai kriteria untuk membandingkan sistem pembakaran bahan bakar yang berbeda.
Selanjutnya, dalam tungku, ada kehilangan panas yang diatur oleh suhu kritis proses, ketebalan lapisan refraktori dan konduktivitas termal refraktori. Oleh karena itu panas bersih yang tersedia (NAH) dalam tungku diberikan oleh persamaan NAH =GAH kehilangan panas. NAH dapat digunakan sebagai kriteria untuk membandingkan efisiensi peleburan/peleburan/pemanasan berbagai tungku.
Panas yang hilang dari proses melalui bukaan di tungku, melalui dinding tungku, atau dengan infiltrasi udara tidak dipertimbangkan dalam perhitungan panas yang tersedia secara teoritis karena ini tergantung pada proses. Panas yang tersedia secara teoritis harus sebanding dengan jumlah energi yang sebenarnya diserap oleh muatan tungku dalam proses aktual, yang secara langsung berhubungan dengan efisiensi termal sistem. Oleh karena itu, panas yang tersedia secara teoritis umumnya digunakan untuk menunjukkan tren efisiensi termal sebagai fungsi dari suhu gas buang, komposisi oksidator dan bahan bakar, rasio pencampuran, dan suhu pemanasan awal udara dan bahan bakar.
Panas yang tersedia bervariasi sebagai fungsi dari suhu gas buang dan menurun dengan cepat dengan suhu gas buang dan relatif tidak tergantung pada komposisi bahan bakar. Oleh karena itu, untuk memaksimalkan efisiensi termal dari proses, diinginkan untuk meminimalkan suhu gas buang. Hal ini biasanya dilakukan dengan memaksimalkan perpindahan panas dari gas buang ke muatan tungku (dan dinding tungku) dan dengan memulihkan sebagian panas dalam gas buang dengan memanaskan oksidator dan/atau bahan bakar.
Saat suhu gas buang meningkat, lebih banyak energi yang dikeluarkan dari sistem pembakaran dan lebih sedikit yang tersisa di sistem. Panas yang tersedia berkurang menjadi nol pada suhu nyala api kesetimbangan adiabatik di mana tidak ada panas yang hilang dari gas. Panas yang tersedia dari sistem pembakaran CH4/O2 bahkan pada suhu gas buang sekitar 2000 derajat C, panas yang tersedia masih 57%. Juga, biasanya tidak terlalu ekonomis untuk menggunakan sistem CH4/udara untuk proses pemanasan dan peleburan suhu tinggi. Pada suhu pembuangan sekitar 1300 derajat C, panas yang tersedia untuk sistem CH4/udara hanya sedikit di atas 30%. Pemulihan panas dalam bentuk udara yang dipanaskan sebelumnya umumnya digunakan untuk proses pemanasan suhu yang lebih tinggi untuk meningkatkan efisiensi termal tungku.
Ketika suhu gas buang meningkat, panas yang tersedia berkurang karena lebih banyak energi dilakukan dengan gas buang. Ada peningkatan cepat awal dalam panas yang tersedia karena konsentrasi O2 dalam oksidator meningkat dari 21% yang ditemukan di udara. Ini adalah salah satu alasan mengapa pengayaan O2 telah menjadi teknik yang populer karena peningkatan efisiensi secara bertahap sangat signifikan. Efisiensi termal sistem CH4/udara adalah dua kali lipat saat udara dipanaskan hingga sekitar 1100 derajat C.
Untuk sistem CH4/O2, peningkatan efisiensi jauh lebih kecil dengan pemanasan awal O2. Ini karena efisiensi awal tanpa pemanasan awal sudah 70% dan karena massa O2 hampir tidak signifikan dalam reaksi pembakaran dibandingkan dengan massa udara dalam sistem bahan bakar/udara. Ada juga ketakutan keamanan saat mengalirkan O2 panas melalui pipa, peralatan pemulihan panas, dan burner. Penghematan bahan bakar untuk teknologi tertentu dapat dihitung menggunakan kurva panas yang tersedia.
Volume gas buang – Laju aliran gas melalui ruang bakar tungku sebanding dengan perpindahan panas konvektif ke muatan tungku. Ada beberapa faktor yang mempengaruhi laju aliran ini. Salah satunya adalah suhu gas karena gas dengan suhu lebih tinggi memiliki laju aliran aktual yang lebih tinggi ( meter kubik per jam) karena ekspansi termal gas. Ini berarti bahwa pemanasan awal bahan bakar atau oksidator, yang keduanya biasanya meningkatkan suhu nyala, menghasilkan laju aliran aktual yang lebih tinggi. Namun, laju aliran gas adalah sama ketika dikoreksi ke kondisi suhu dan tekanan standar (STP).
Faktor lain yang memiliki pengaruh yang sangat kuat terhadap laju aliran gas melalui sistem pembakaran adalah komposisi oksidator. Peningkatan pembakaran O2 pada dasarnya melibatkan penghilangan N2 dari oksidator. Perubahan besar dibandingkan dengan pembakaran udara/bahan bakar adalah pengurangan volume gas buang. Ini berarti bahwa untuk setiap unit volume bahan bakar, 3 volume gas yang dinormalisasi dihasilkan untuk pembakaran O2/bahan bakar dibandingkan dengan 10,5 volume untuk pembakaran udara/bahan bakar. Pengurangan ini dapat memiliki efek positif dan negatif, tetapi efek pada perpindahan panas konveksi adalah pengurangan kecepatan gas rata-rata melalui ruang tungku dan menghasilkan pengurangan perpindahan panas konveksi ke muatan tungku.
Properti transportasi gas buang
Sifat transportasi komponen gas dalam ruang tungku penting untuk menentukan perpindahan panas dan dinamika fluida. Sifat sangat tergantung pada suhu dan komponen gas. Sifat gas penting untuk perpindahan panas di ruang tungku industri bervariasi sebagai fungsi komposisi bahan bakar dan oksidator, rasio pencampuran, dan suhu pemanasan awal udara. Variasi properti sebagai fungsi suhu pemanasan awal bahan bakar memiliki efek minimal. Komposisi dan suhu gas diperlukan untuk menghitung radiasi gas tidak bercahaya. Sifat transpor gas diperlukan untuk menghitung koefisien perpindahan panas konveksi, yang sering diberikan dalam bentuk bilangan Nusselt (Nu). Nu dihitung dari bilangan Prandtl (Pr) dan bilangan Reynolds (Re). Koefisien perpindahan panas konveksi 'h' kemudian dihitung dari bilangan Nusselt menggunakan Nu =hd/k di mana d adalah dimensi karakteristik untuk sistem aliran dan k adalah konduktivitas termal fluida. Sifat-sifat gas diperlukan untuk menghitung bilangan Nu, Pr, dan Re diberikan di bawah ini.
Kepadatan – Densitas gas dapat digunakan untuk menghitung bilangan Re, yang umumnya diperlukan untuk menghitung koefisien perpindahan panas konvektif. Kepadatan juga digunakan untuk menghitung kecepatan gas rata-rata melalui ruang tungku, yang juga biasanya diperlukan untuk menghitung koefisien konveksi. Massa jenis gas berbanding terbalik dengan suhu gas sehingga semakin tinggi suhu maka massa jenis semakin berkurang. Pengurangan densitas gas secara kasar sebanding dengan kebalikan dari suhu gas absolut. Juga, densitas gas menurun dengan cepat seiring dengan meningkatnya kandungan O2 dalam oksidator. Ini karena suhu nyala api yang meningkat. Densitas gas yang lebih rendah berarti angka Re yang lebih rendah dan karenanya mengurangi perpindahan panas konveksi, jika semua variabel lainnya tetap sama. Namun, laju aliran massa gas juga menurun. Oleh karena itu, kecepatan gas rata-rata tidak terpengaruh secara signifikan sebagai akibat dari efek gabungan dari kepadatan yang lebih rendah dan laju aliran massa yang lebih rendah sehingga dampak pada konveksi karena kecepatan gas minimal.
Kepadatan gas mencapai minimum pada rasio kesetaraan menengah. Ini sekali lagi dapat dikaitkan dengan suhu api kesetimbangan adiabatik. Selanjutnya, densitas gas menurun hampir secara linier dengan meningkatnya suhu pemanasan awal udara, yang berkorelasi terbalik dengan kurva untuk suhu nyala. Juga, kerapatan gas tidak berkurang secara linier sebagai fungsi dari komposisi campuran gas, seperti yang umumnya diharapkan secara naluriah. Sekali lagi, kerapatan berbanding terbalik dengan suhu nyala adiabatik.
Panas spesifik – Panas spesifik gas, kadang-kadang disebut sebagai kapasitas panas gas, adalah sifat transpor lain yang berdampak pada perpindahan panas konvektif dalam sistem tungku. Ini digunakan untuk menghitung nomor Pr, yang sering digunakan untuk menghitung koefisien perpindahan panas konveksi. Ada peningkatan nonlinier dalam panas spesifik gas sehubungan dengan suhu produk buangan. Panas spesifik meningkat lebih cepat pada suhu yang lebih tinggi. Selanjutnya, panas spesifik gas buang meningkat hampir secara linier dengan meningkatnya persen O2 dalam oksidator. Semua hal lainnya tetap sama, hal ini meningkatkan perpindahan panas konvektif dari gas produk pembakaran ke muatan tungku.
Namun, ada hubungan yang jauh lebih rumit antara panas spesifik dan rasio ekivalen, termasuk ketergantungan bahan bakar yang kuat juga. Semua bahan bakar menunjukkan peningkatan awal dalam panas spesifik ketika rasio ekivalensi meningkat, mencapai maksimum lokal pada kondisi stoikiometrik. Di luar kondisi stoikiometri, panas spesifik kemudian menurun, mendatar, dan meningkat lagi. Dalam kasus CH4, panas spesifik meningkat sangat cepat pada nilai ekivalen yang tinggi. Meskipun hubungan antara panas spesifik dan rasio ekivalen cukup rumit, kenyataannya adalah bahwa sebagian besar proses pembakaran industri dioperasikan pada kondisi sedikit bahan bakar di mana ada hubungan yang kuat tetapi lebih linier antara rasio ekivalen dan panas spesifik. Dalam hal campuran bahan bakar H2/CH4, panas spesifik meningkat dengan cepat pada kandungan H2 yang tinggi dalam campuran bahan bakar. Suhu nyala api menunjukkan hubungan yang sangat mirip dengan kandungan H2 dalam campuran.
Konduktivitas termal – Seperti panas jenis, konduktivitas termal gas mempengaruhi bilangan Pr, yang selanjutnya mempengaruhi koefisien perpindahan panas konveksi. Dalam hal ini, ada hubungan terbalik antara konduktivitas termal dan bilangan Pr. Ketika konduktivitas termal meningkat (menurun), bilangan Pr menurun (meningkat) seiring dengan koefisien konveksi, dengan asumsi semua variabel lain tetap konstan. Konduktivitas termal gas secara kasar tergantung pada akar kuadrat dari suhu absolut. Peningkatan non-linier serupa dalam konduktivitas termal terjadi dengan suhu gas seperti untuk panas spesifik.
Selanjutnya, konduktivitas termal meningkat dengan cepat karena kandungan O2 dalam oksidator meningkat. Hubungannya hampir linier meskipun ada peningkatan yang lebih cepat pada kandungan O2 yang lebih rendah dibandingkan dengan peningkatan kandungan O2 yang lebih tinggi dalam oksidator. Namun, ada hubungan yang rumit antara properti transportasi dan rasio ekivalensi. Ada maksimum lokal pada kondisi stoikiometri. Untuk H2, maksimum lokal juga merupakan maksimum keseluruhan untuk berbagai rasio ekivalensi. Untuk CH4, ada peningkatan cepat dalam konduktivitas termal pada kondisi yang sangat kaya bahan bakar (rasio ekivalensi tinggi), dengan konduktivitas melebihi nilai maksimum lokal pada kondisi stoikiometri. Meski tidak sedramatis itu, ada fenomena serupa untuk C3H8. Meskipun sebagian besar proses industri dijalankan pada kondisi sedikit bahan bakar, masih ada perubahan cepat dalam konduktivitas termal di sisi kondisi stoikiometrik yang sedikit bahan bakar.
Ada hubungan yang lebih sederhana antara konduktivitas dan suhu pemanasan awal udara pembakaran. Konduktivitas meningkat sedikit lebih cepat daripada linier saat suhu pemanasan awal meningkat. Selain itu, konduktivitas termal meningkat jauh lebih cepat seiring dengan meningkatnya kandungan H2 dalam campuran bahan bakar H2/CH4.
Viskositas – The absolute or dynamic viscosity is a measure of momentum diffusion. Gas viscosity is having a similar relationship to the thermal conductivity. The viscosity is important in calculating both the Pr and Re numbers, but in opposite ways. As the gas viscosity increases (decreases), the Pr number increases (decreases) and the Re number decreases (increases) assuming that all the other variables are constant. The kinematic viscosity is related to the dynamic viscosity.
There is a nearly linear increase in gas viscosity with the exhaust product temperature. The gas viscosity increases as the O2 content in the oxidizer increases, similar to the adiabatic flame temperature. The gas viscosity peaks at an equivalence ratio of 1.0 (stoichiometric conditions) and declines as the mixture becomes either more fuel rich or more fuel lean. The gas viscosity also increases with the air preheat temperature, comparable to the flame temperature. The viscosity increases as the H2 content increases in an H2/CH4 fuel blend. The increase in the viscosity is more rapid at higher H2 contents.
Pr number – The Pr number is frequently used to calculate the convection heat transfer coefficient. The components of Pr include the specific heat, viscosity, and thermal conductivity. The combination of these variables which forms the Pr number changes as functions of the fuel and oxidizer compositions, the mixing ratio, and the air preheat temperature. However, there is little change in Pr number as a function of the fuel preheat-temperature. The Pr number decreases as a function of temperature, but in a non-uniform way. Initially, it decreases moderately quickly, then decreases more slowly, and finally decreases rapidly at higher temperatures.
There is also a highly nonlinear relationship between the Pr number and the oxidizer composition. For CH4 and C3H8, the Pr number decreases rapidly at first and then levels off at higher O2 contents. For H2, the Pr number actually has a minimum at around 50 % O2 content. Also, a highly nonlinear relationship exists between the Pr number and the equivalence ratio. Most of the fuels show local maximum and minimum. The Pr number also declines almost linearly with the air preheat temperature. The Pr number declines as the H2 content in an H2/CH4 fuel blend decreases, and decreases rapidly at high H2 contents.
Lewis number – The Lewis number (Le) is the ratio of the thermal diffusivity to the molecular (mass) diffusivity. The Le number is important for the heat transfer in combustion systems. In general, for Le values greater than 1, there are some enhancements in convective heat transfer due to chemical recombination reactions. The Le number is 1 for temperatures below 1200 deg C, depending on the fuel, and then rises fairly rapidly at higher temperatures. The Le number is greater than one for all oxidizer compositions under adiabatic equilibrium conditions, which equates to the highest flame temperature possible for those conditions. The values of Le number peaks at intermediate oxidizer compositions and declines at higher O2 contents. There is a dramatic peak in the Le number at stoichiometric conditions, with the Le number going below 1.0 at higher equivalence ratios. The Le number increases almost linearly with the air preheat temperature for adiabatic equilibrium conditions. It increases more rapidly as the H2 content in a fuel blend of H2/CH4 increases.
Heat transfer in a furnace
Factors affecting the heat transfer in a furnace to the furnace charge are described below.
Flow of heat within the furnace charge – In case of an electrically heated furnace charge where the charge is used as a resistance in a circuit or by induction heating, the flux lines concentrate just inside the surface. In a fuel-fired heating process, heat enters the charge through its surface (by radiation or by convection) and diffuses throughout the charge by conduction. This heat flow requires a difference in temperature within the charge. Steady heat flows through a flat furnace charge. For other than flat charge, heat flux lines are seldom parallel and rarely steady. In transient heat flow, determination of the temperature at a given time and point within the charge necessitates use of the finite element method. Increasing the furnace temperature (a high ‘thermal head’) or ‘high-speed heating’ often results in non-uniform heating, which necessitates a longer soak time, sometimes defeating the purpose of high-speed heating.
Thermal conductivity and diffusion – There is normally wide variation in thermal conductivities of various metals, which has a direct bearing on the ability of heat to flow through or diffuse throughout them, and hence has a very strong effect on temperature distribution or uniformity in solids. The factor which affects temperature distribution is the thermal diffusivity. It is thermal conductivity divided by the volume specific heat of the solid material and is represented by the equation thermal diffusivity =thermal conductivity/ (specific heat x density). In this equation, the numerator is a measure of the rate of heat flow into a unit volume of the material while the denominator is a measure of the amount of heat absorbed by that unit volume. With a higher ratio of numerator to denominator, heat gets conducted into, distributed through, and absorbed.
Thermal conductivities and diffusivities of solids vary greatly with temperature. Specific heats and densities vary little, except for steels at their phase transition point. The thermal conductivities of solid pure metals drop with increasing temperature, but the conductivities of solid alloys generally rise with temperature.
Lag time – The effect of thermal conductivity on heat flow and internal temperature distribution is shown in Fig 1 for three same-size slabs of ferrous alloys heated from two sides. The surface temperatures in all the three cases generally rise very quickly, but the interior temperatures of rise differentially because of their poorer diffusivities. The slabs take different time to come to the equilibrium condition with the furnace temperature.
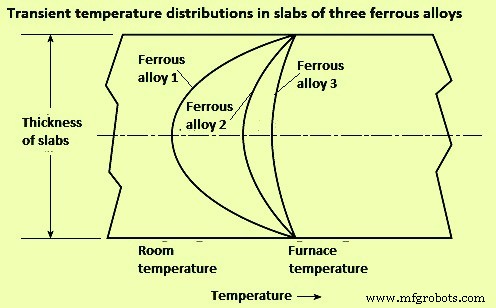
Fig 1 Effect of thermal conductivity on heat flow and internal temperature distribution
Solid materials which are heated in industrial furnaces are not necessarily continuous. Many times, the charge consists of coiled strip material or separate pieces piled to various depths or close side by side. In such cases, heat only can flow from one piece to the adjacent piece through small contact points on their surfaces, or through gas filled spaces, the thermal conductivity of which is very small. A stack of flat plates is an example of very low conductance. Even very small gaps constitute a big thermal resistance than solid metal. A stack cannot be treated as a solid, since thin air spaces are insulators. The differing air gaps in a stack result in bad non-uniformities in temperatures.
Rapid heat flow in each piece of a piled charge is obtained only by circulation of hot gases through the piled material by convection and gas radiation. These gas masses are to be constantly replaced with new hot gas since they have low mass, low specific heat, and thin gas beam thickness, so they cool quickly without delivering much heat to the loads. For uniform heating and precise reproducibility, piling of pieces of materials are to be avoided.
Heat transfer to the surface of the furnace charge – In furnace practice, heat is transferred by three modes namely (i) conduction, (ii) convection, and (iii) radiation. There are some essentials of heat transfer which are helpful to designers and operators of industrial furnaces. Most industrial furnaces, ovens, kilns, incinerators, boilers, and heaters use combustion of fuels as their heat source. Combustion, as used in industrial furnaces, comes from rapid and large chemical reaction kinetics and this result into conversion of chemical energy to sensible heat (thermal) energy. Increasing fuel and oxidizer (usually air) mixing surface area or increasing temperature of the reactants can cause faster combustion reactions, usually resulting in higher heat source temperatures. Fuel oxidation reactions are exothermic, so they can develop into a runaway condition (e.g. thermal energy being released faster than it can be carried away by heat transfer). This positive feedback can cause an explosion.
A flame is a thin region of rapid exothermic chemical reaction. An example is a Bunsen burner flame. In a Bunsen burner, a thoroughly premixed laminar stream of fuel gas and air is ignited by an external heat source, and a cone-shaped reaction zone (flame front) forms. Turbulence increases the thickness and surface area of the reaction zone, resulting in higher burning velocity. Laminar burning velocity for natural gas is around 18 metres per minute (mpm) while the turbulent burning velocity can be two to ten times faster. In a laminar flame, thermal expansion from chemical heat release can combine with increased reactivity caused by higher temperatures, resulting in acceleration to a turbulent flame. Except for long luminous flames, most industrial flames are turbulent.
Conduction heat transfer – Conduction heat transfer is molecule-to-molecule transfer of vibrating energy, usually within solids. Heat transfer solely by conduction to the charged load is rare in industrial furnaces. It occurs when cold metal is laid on a hot hearth. It also occurs, for a short time, when a piece of metal is submerged in a salt bath or a bath of liquid metal.
If two pieces of solid material are in thorough contact (not separated by a layer of scale, air, or other fluid), the contacting surfaces instantly assume an identical temperature somewhere between the temperatures of the contacting bodies. The temperature gradients within the contacting materials are inversely proportional to their conductivities (Fig 2).
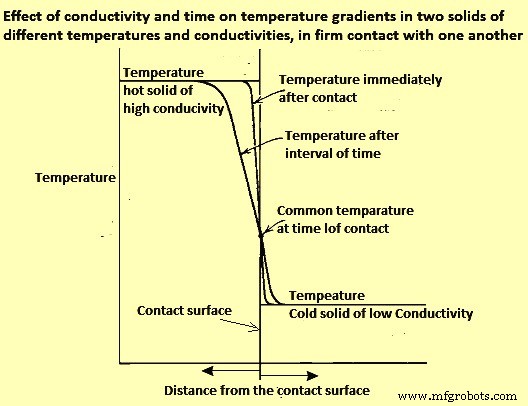
Fig 2 Effect of conductivity and time on temperature gradients in two solids of different temperatures and conductivities, in firm contact with one another
The heat flux (rate of heat flow per unit area) depends not only on the temperatures of the two solids but also on the diffusivities and configurations of the contacting solids. In practice, comparatively little heat is transferred to (or abstracted from) a charge by conduction, except in the flow of heat from a billet to water-cooled skids.
When a piece of cold metal is suddenly immersed in liquid salt, lead, zinc, or any other liquid metal, the liquid freezes on the surface of the cold metal, and heat is transferred by conduction only. After a very short time, the solid jacket, or frozen layer, remelts. From that time on, heat is transferred by conduction and convection.
Convection heat transfer
Convection heat transfer is a combination of conduction and fluid motion, physically carrying heated (or cooled) molecules to another surface. If a stream of gaseous fluid flows parallel to the surface of the solid, the vibrating molecules of the stream transfer some thermal energy to or from the solid surface.
A ‘boundary layer’ of stagnant, viscous, poorly conducting fluid tends to cling to the solid surface and acts as an insulating blanket, reducing heat flow. Heat is transferred through the stagnant layers by conduction. If the main stream fluid velocity is increased, it scrubs the insulating boundary layer thinner, increasing the convection heat transfer rate. The conductance of the boundary layer (film coefficient) is a function of mass velocity (momentum, Re number).
In furnaces which operate below 600 deg C, heat transfer by convection is of major importance since radiation is weak there. Modern high-velocity (high-momentum) burners give high convection heat transfer coefficients. High velocities often provide more uniform temperature distribution around a single piece charge, or among multiple piece charges, since more mass flow carries additional sensible heat at more moderate temperatures. At low furnace temperatures, high rates of total heat transfer can be obtained only by high gas velocities since heat transfer by radiation at around 550 deg C is less than one-tenth of what it is at around 1200 deg C. High-velocity (high momentum) burners are widely used to fill in where radiation cannot reach because of shadow problems.
Radiation heat transfer
Radiation between solids – Heat is radiated by solids even at low temperatures. The net radiant heat actually transferred to a receiver is the difference between radiant heat received from a source and the radiant heat re-emitted from the receiver to the source. The net radiant heat flux between a hot body (heat source) and a cooler body (heat receiver) can be calculated by Stefan-Boltzmann equations.
Emissivity and absorptivity of materials are important properties for radiation between solids. Emissivity is the radiant heat emitted (radiated) by a surface, expressed as a decimal of the highest possible (black body) heat emission in a unit time and from a unit area. Emittance is the apparent emissivity of the same material for a unit area of apparent surface which is actually much greater, due to roughness, grooving, and so on. Absorptivity is the radiant heat absorbed by a surface per unit time and unit area, expressed as a decimal of the most possible (black body) heat absorption.
Engineers use emissivity value of 0. 85 in conventional refractory lined furnaces. However, the temperature, surface condition, and alloy can make considerable difference. As an example, if stainless-steel strip is heated in less than three minutes in a catenary furnace, the emissivity may not change even though the temperature increases from ambient to 1100 deg C. By measuring both strip surface temperature and furnace temperature, it has been possible to revise heating curve calculations, assuming that oxidation has not changed the emissivity or absorptivity during the heating cycle.
Radiation from clear flames and gases – There are two origins of radiation from the products of combustion to solids. The two origins of radiation are (i) from clear flame and from gases, and (ii) from the micron-sized soot particles in luminous flame. Radiation from clear gas does not follow the Stefan-Boltzmann fourth-power law. The only clear gases which emit or absorb radiation appreciably are those having three or more atoms per molecule (triatomic gases) such as CO2, H2O, and SO2 (sulphur di-oxide). An exception is diatomic CO, which gives off less radiation. The other diatomic gases, such as O2, N2 (and their mixture, air), and H2 have only negligible radiating power.
Gaseous radiation does not follow the fourth-power law since gases do not radiate in all wavelengths, as do solids (gray bodies). Each gas radiates only in a few narrow bands. Radiation from clear gases depends on their temperature, on the partial pressure or percent volume of each triatomic gas present, and on the thickness of their gas layer.
The temperature of a radiating gas gets lower in the direction of gas travel. To maintain active gas radiation, the gas is to be continually replaced by new hot gas, which also improves convection. Higher gas feed velocities reduce the temperature drop along the gas path. This factor is very critical in maintaining good temperature uniformity in high temperature industrial furnaces.
The furnaces are often designed on the basis of refractory radiation heating the charge, with usually reasonable results, but some situations cannot be explained by refractory radiation alone. Direct radiation from furnace gases generally delivers 62 % (+/- 2 %) of the heat to the charge, and refractories transfer the remaining 38 % (+/- 2 %). Gas temperatures needed to transfer the heat to refractory and charge are generally much higher than generally assumed.
Radiation from luminous flames – If a fuel-rich portion of an air/fuel mixture is exposed to heat, as from a hotter part of the flame, the unburned fuel molecules polymerize or suffer thermal cracking, resulting in formation of some heavy, solid molecules. These soot particles glow when hot, providing luminosity, which boosts the flame’s total radiating ability.
If fuel and air are not thoroughly mixed promptly after they leave the burner nozzle, they can be heated to a temperature at which the hydrocarbons crack (polymerize). Further heating brings the resulting particles to a glowing temperature. As O2 mixes with them, they burn. As the flame proceeds, formation of new soot particles can equal the rate of combustion of previously formed particles. Farther along the flame length, soot production diminishes, and all remaining soot is incinerated. This series of delayed-mixing combustion processes are to be completed before the combustion gases pass into the flue. If the flame is still luminous at the flue entry, smoke can appear at the stack exit. Smoke is soot that has been cooled (chilled, quenched) below its minimum ignition temperature before being mixed with adequate air.
The added radiating capability of luminous flames causes them to naturally cool themselves faster than clear flames. This is performing their purpose—delivering heat. The cooling phenomenon can negate some of the gain from the higher luminosity (effective emissivity).
Luminous flames often have been chosen because the added length of the delayed mixing luminous flames can produce a more even temperature distribution throughout large combustion chambers. As industrial furnaces are supplied with very high combustion air preheat or more oxy-fuel firing, luminous flames can enable increases in heat release rates.
Fuels with high C/H2 ratios (most oils and solid fuels) are more likely to burn with luminous flames. Fuels with low C/H2 ratios (mostly gaseous fuels) can be made to burn with luminous flames namely (i) by delayed mixing, injecting equally low-velocity air and gas streams side-by-side, and (ii) by using high pressure to ‘shoot’ a high-velocity core of fuel through slower moving air so that the bulk of the air cannot ‘catch up’ with the fuel until after the fuel has been heated (and polymerized) by the thin ‘sleeve’ of flame annular interface between the two streams.
Flames from solid fuels can contain ash particles, which can glow, adding to the flame’s luminosity. With liquid and gaseous fuels, flame luminosity usually comes from glowing C and soot particles. The effective flame emissivity, as measured is usually between that of the POC gases and a maximum value of 0.95, depending on the total surface area of solid particles. Normally, heat transfer from a luminous flame is greater than that from a clear flame having the same temperature. The difference in the rate of heat transfer is quite noticeable in furnaces for reheating steel and metals. The difference becomes more pronounced at high temperature, where the radiating power of each triatomic gas molecule increases, but the gain is partially canceled by the decreasing density of radiating molecules per unit volume.
In another phenomenon, the bands of gaseous radiation hold their wavelengths regardless of temperature. At higher temperatures, however, the area of high intensity of solid radiation (glowing soot and C particles) moves toward shorter wavelengths (away from the gas bands). In higher temperature realms, radiation from clear gases does not increase as rapidly as radiation from luminous flames.
Flame radiation is a function of many variables such as C/H2 ratio of the fuel, air/fuel ratio, air and fuel temperatures, mixing and atomization of the fuel, and thickness of the flame. Some of these can change with distance from the burner. Fuels with higher C/H2 ratio, such as oils, tend to make more soot, so they usually create luminous flames, although blue flames are possible with light oils. Many gases have a low C/H2 ratio, and tend to burn clear or blue. It is difficult to burn tar without luminosity. It is equally difficult to produce a visible flame with blast furnace (BF) gas or with H2.
When comparing luminous and nonluminous flames, it is important to remember (i) soot radiation (luminous) usually ends where visible flame ends because soot is most often incinerated at the outer surface or skin of the flame, where it meets secondary or tertiary air, and (ii) gas radiation (nonluminous) occurs from both inside and outside the visible flame envelope, greatly increasing the uniformity and extent of its coverage, although gas radiation within the flame is somewhat shadowed by any surrounding soot particles or triatomic gases, and gas radiation outside the flame can be from cooler gases.
The effect of excess fuel on flame radiation is considerably greater than the effect of less excess air. The merits and demerits of clear flames versus long luminous flames have been debated for years. Modified burners and control schemes are helping to utilize the best of both. A problem common to several burner types is change of the flame characteristic as the burner input is turned down. Problems with some clear flame burners are (i) movement of the hump in the temperature profile closer to the burner wall as the firing rate is reduced, and (ii) at lower input rates, temperature falls off more steeply at greater distances from the burner wall (e.g., the temperature profile of a burner firing at 50 % of its rated capacity or below is at its peak temperature (maximum heat release at or near the burner wall, falling off further from the burner wall). At lower firing rates, the temperature drop off gets worse. At higher firing rates, the burner wall temperature decreases as the peak temperature moves away from it. In some steel reheating furnaces at maximum firing rate, the temperature difference between the burner wall and the peak can be 150 deg C.
The problem of a temperature peak at the far wall during high fire is aggravated by spur of furnace gases into the base of the flame, delaying mixing of fuel with O2. If the burner firing rate is increased, the spur of the products of complete combustion increases exponentially. Resulting problems are many. When side-firing a furnace at low firing rate, the peak temperature is at the burner wall, but at maximum firing rate, the peak temperature can be at the furnace centre or the opposite wall. Thus, the location of a single temperature control sensor is never correct. If the temperature sensor is in the burner wall, low firing rates have peak temperature hugging the furnace wall and driving the burner to low fire rate resulting into the rest of the furnace width receiving inadequate input. At high firing rates, a sensor in the burner wall is cool while the temperature away from the burner wall is very high, perhaps forming liquid scale on the surfaces of the charge pieces at the centre and/or far wall. To remedy this issue, inexperienced operators can lower the set point, reducing the furnace heating capacity.
Another example of the effect of the problem occurs with the bottom zone of a steel reheating furnace when fired longitudinally counter flow to the load movement, and with the control sensor installed 3 metre (m) to 6 m from the (end-fired) burner wall. At low-firing rates, with the zone temperature set at 1300 deg C, the burner wall can rise to higher than 1370 deg C. At that temperature, scale melts and drips to the floor of the bottom zone where it can later solidify as one big piece. At high firing rates, the peak temperature can move beyond the bottom zone T-sensor, possibly melting scale some distance toward the charge end of the furnace. Again, to avoid the problem, operators can lower temperature control settings, reducing the furnace capacity.
Control of the aforementioned problems requires an additional temperature sensor in each zone and a means for changing the mixing rate characteristic of the burner in response to the temperature measurements. Burners with adjustable spin (swirl) can be set to prevent much of the problem, especially if combined with a low-fire, forward-flow gas or air jet through the center of the burner. Such a jet is typically sized for 5 % of maximum gas or air flow.
Long, luminous flames, either laminar type or turbulent type, tend to have much less temperature hump and do not change length as rapidly when input is reduced. They can be great ‘levelers’, providing better temperature uniformity.
This information on in-flame soot radiation and triatomic gas radiation has been known for some time, but recent developments may be changing the picture. Use of oxy-fuel (100 % O2), both of which elevate flame turndown. The major gain from oxy-fuel firing is from more intense radiation heat transfer because of the higher concentration of triatomic gases, due to the elimination of N2 from the POC. This also decreases the mass of gas carrying heat out the flue (reducing stack loss). In another development, some lean premix gas flames (designed for low NOx emissions) make a ubiquitous flame field (seemingly transparent) through much of the chamber.