Proses Tungku Busur Listrik Consteel
Proses Tungku Busur Listrik Baja
Proses baja adalah proses yang dipatenkan. Ini adalah teknologi konservasi energi inovatif untuk pra-pemanasan skrap dalam tungku busur listrik (EAF) yang dikembangkan oleh 'Intersteel Technology Inc., Charlotte, North Carolina (sejak 1994 bagian dari Techint, Tenova S.p.A.). Aplikasi industri pertama dari teknologi Consteel terjadi pada tahun 1989, di Gerdau-Ameristeel Charlotte (AS). Sejak itu telah ada penerimaan industri yang stabil dari teknologi ini. Saat ini proses Consteel EAF adalah teknologi pembuatan baja yang terbukti dan andal. Ini memastikan penggunaan energi dan bahan baku yang efisien, pengoperasian dan perawatan yang mudah, serta ramah lingkungan.
Dalam EAF dengan proses Consteel, solusi pabrik yang diadopsi adalah pengumpanan EAF secara terus-menerus oleh skrap, dipanaskan sebelumnya dan disalurkan melalui konveyor yang bergerak di terowongan pra-pemanasan, di mana gas buang dari EAF, mengalirkan arus berlawanan muatan logam dibakar oleh udara yang disuntikkan. Pengumpanan terus menerus dan pemanasan awal skrap menawarkan beberapa keuntungan potensial dibandingkan dengan pengumpanan batch EAF konvensional.
Proses Consteel meningkatkan produktivitas dan meningkatkan efisiensi energi dengan dampak lingkungan yang minimal. Sorotan utama dalam penerapan teknologi ini adalah langkah-langkah konservasi seperti (i) pemulihan panas dari gas buang tungku menjadi sisa pra-panas sebelum pengisian di tungku, (ii) pengurangan energi listrik spesifik, (iii) pengurangan O2 (oksigen), dan penggunaan C (karbon) tanpa konsumsi bahan bakar burner , (iv) peningkatan laju produksi karena penurunan waktu tap-to-tap, (v) penurunan signifikan gangguan listrik pada jaringan, (vi) konsumsi elektroda lebih rendah dan kerusakan elektroda, (vii) peningkatan hasil skrap, (viii) lebih sedikit debu yang dievakuasi ke rumah kantong, dan (ix) pengurangan biaya untuk logistik, tenaga kerja, pemeliharaan, dan pengelolaan produk limbah.
Kebutuhan daya yang rendah dan operasi bak datar yang stabil, di bawah terak berbusa dalam kasus proses Consteel, menjadikan proses Consteel teknologi EAF yang ideal ketika jaringan listrik relatif lemah dan hanya mampu mentolerir gangguan yang sangat rendah. Proses Consteel juga meminimalkan kebisingan, debu, dan emisi polusi, baik di dalam toko lelehan (tidak diperlukan rumah anjing) dan ke sistem gas buang, yang, tidak seperti EAF konvensional, tidak perlu terlalu besar untuk menangani emisi ledakan.
Pemanasan awal skrap konvensional telah digunakan sejak lama terutama di negara-negara dengan biaya listrik yang tinggi. Pemanasan awal skrap konvensional melibatkan penggunaan gas panas untuk memanaskan skrap di ember sebelum mengisi skrap ke EAF. Sumber gas panas dapat berupa gas buang dari EAF atau gas yang dihasilkan dari pembakaran bahan bakar gas. Pemanasan awal skrap konvensional dapat dilakukan dengan mengirimkan gas tungku panas ke ember pengisian skrap dengan menyalurkan gas buang dari lubang keempat di EAF ke tudung khusus di atas ember pengisian. Biasanya gas meninggalkan EAF pada suhu sekitar 1200 derajat C, masuk ke ember pada suhu sekitar 815 derajat C, dan keluar pada suhu sekitar 200 derajat C. Jumlah pemanasan awal tergantung pada perpindahan panas ke scrap yang merupakan fungsi dari ukuran dan waktu scrap pada suhu. Biasanya skrap dipanaskan terlebih dahulu hingga kisaran 350 derajat C hingga 450 derajat C. Jumlah pemanasan awal ini biasanya mengurangi konsumsi energi sebesar 40 kWh/ton hingga 60 kWh/ton, konsumsi elektroda sekitar 0,35 kg/ton, konsumsi refraktori sekitar 1,2 kg/ton dan waktu tap-to-tap sekitar 5 menit hingga 6 menit. Beberapa kelemahan dengan pemanasan awal scrap konvensional termasuk (i) tidak nyaman untuk dioperasikan seperti scrap menempel pada ember dan umur ember pendek, (ii) pengendalian pemanasan awal yang buruk karena variasi suhu gas buang dan laju aliran melalui berbagai fase di EAF operasi, dan (iii) untuk waktu tap-to-tap kurang dari 70 menit logistik pemanasan awal skrap konvensional menghasilkan penghematan energi minimal yang tidak dapat membenarkan biaya modal sistem pemanasan awal.
Proses Consteel secara terus menerus melakukan pra-pemanasan dan memasukkan muatan logam (scrap, pig iron, dll.) ke EAF sekaligus mengontrol emisi gas. Proses Consteel mencapai pengumpanan skrap secara terus-menerus melalui konveyor inersia, yang memindahkan skrap dari bagian terbuka, yang digunakan untuk pengisian (biasanya dengan derek), ke tungku, melewati bagian tertutup (terowongan) di mana skrap ditempatkan dipanaskan oleh gas buang proses yang berjalan dalam arah yang berlawanan, menuju sistem ekstraksi gas buang. Energi untuk pra-pemanasan disediakan oleh gas panas yang memasuki terowongan dari EAF, setelah dibakar oleh udara yang ditambahkan ke dalam terowongan. Scrap yang telah dipanaskan secara terus-menerus dimasukkan ke dalam EAF, di mana ia dilebur dengan perendaman dalam baja cair. EAF beroperasi dalam kondisi rendaman datar yang konstan, keunggulan utama dibandingkan proses batch konvensional di mana skrap dicairkan oleh aksi langsung busur listrik. Gas EAF dikirim ke pabrik pembersih gas buang dalam kondisi yang sesuai untuk pembakaran sempurna karbon monoksida (CO) dan polutan lainnya tanpa konsumsi bahan bakar. Konsep proses Consteel ditunjukkan pada Gambar 1.
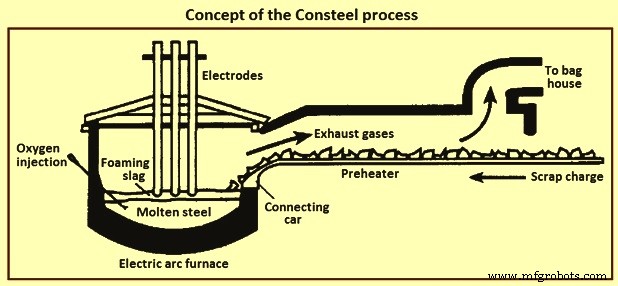
Gbr 1 Konsep proses Consteel
Deskripsi proses dan karakteristik tanaman
Proses Consteel adalah proses yang memungkinkan pengumpanan terus menerus dan pemanasan awal muatan logam ke EAF. Dalam proses ini, scrap dibebankan langsung dari scrap yard ke konveyor muatan. Scrap tersebut kemudian secara otomatis dan terus menerus dikirim ke EAF sambil dipanaskan di konveyor preheater yang disebut tunnel.
Energi untuk pra-pemanasan disediakan oleh gas panas yang berasal dari EAF, pasca-pembakaran oleh udara yang disuntikkan di terowongan melalui injektor yang sengaja ditempatkan di atap terowongan. Bersama dengan udara yang disuntikkan, udara yang tidak terkontrol memasuki EAF dan terowongan. Di terowongan, udara yang tidak terkendali terutama masuk di zona di mana EAF dan terowongan terhubung yang disebut area mobil penghubung. Udara yang tidak terkontrol berkontribusi pada pasca-pembakaran gas buang dari EAF.
Gas terowongan keluar kemudian disalurkan ke sistem pembersihan gas buang. Sistem kipas angin dan tirai mekanis ditempatkan di ujung terowongan untuk menghindari masuknya udara yang disebut segel dinamis.
Karena proses Consteel berdasarkan gas pasca pembakaran yang berasal dari EAF, sangat terkait dengan proses pembuatan baja yang dilakukan di EAF, oleh karena itu untuk mengoptimalkan proses, seluruh sistem yang terdiri dari EAF dan terowongan harus dipertimbangkan.
Manajemen laju aliran di masing-masing injektor diperbolehkan. Injeksi udara dapat dikontrol secara otomatis atau diatur secara manual. Kontrol otomatis didasarkan pada pengukuran konsentrasi O2 dalam gas di outlet terowongan. Nilai target parameter ini dicapai dan dipertahankan melalui sistem kontrol pabrik, dengan pengelolaan laju aliran udara yang tepat di enam injektor. Gambar 2 menunjukkan diagram skema dari proses Consteel.
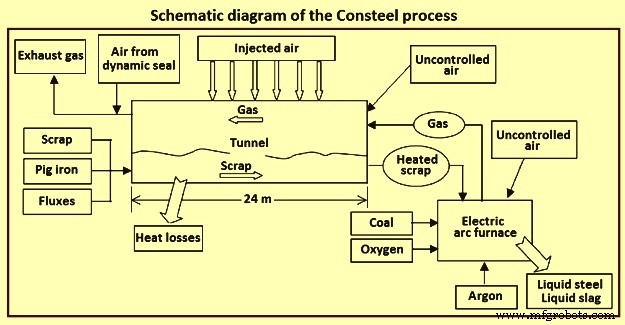
Gambar 2 Diagram skematis proses Consteel
Fitur khusus dari proses Consteel
Proses Consteel menggabungkan pengisian skrap secara terus menerus ke dalam EAF melalui sistem konveyor yang menghubungkan halaman skrap dengan EAF. Tidak ada pengisian ember konvensional yang terjadi. Memo dimuat ke konveyor oleh derek halaman memo dan konveyor ini memindahkan memo dalam gerakan berosilasi yang terdiri dari gerakan maju lambat dan gerakan mundur cepat yang menyebabkan memo bergerak bersama dengan konveyor selama langkah maju tetapi meluncur di permukaan konveyor selama langkah mundur yang lebih cepat sehingga menghasilkan perjalanan ke depan bersih dari skrap menuju tungku.
Beberapa jarak sebelum mencapai tungku skrap memasuki bagian pemanasan awal yang terdiri dari terowongan di mana gas panas yang keluar dari aliran EAF berlawanan arah dengan gerakan skrap. Di bagian pemanasan awal, CO dalam gas buang dibakar oleh injeksi udara yang dikontrol secara otomatis, memungkinkan lebih banyak energi untuk dipulihkan ke memo. Selama operasi pengumpanan terus menerus, penangas baja di EAF dijaga tetap cair dan skrap yang masuk ke tungku dilebur dengan pencelupan dalam penangas. Busur listrik dengan demikian selalu bekerja pada bak cair (kondisi bak datar), bukan pada skrap padat. Dalam situasi ini busur stabil dan tidak terpengaruh oleh adanya sisa padat seperti halnya dengan pengisian batch.
Proses EAF dengan Consteel dapat menggunakan semua jenis skrap baja dan semua bahan mentah logam yang dapat diisi dalam EAF tradisional. Dalam hal dimensi maksimum skrap, batas normal yang ditentukan oleh spesifikasi skrap baja (1,5 m x 0,5 m x 0,5 m) sesuai dengan pengisian terus menerus melalui proses Consteel.
Aturan utama yang harus diikuti adalah bahwa potongan potongan maksimum tidak boleh melebihi jarak antara ujung konveyor proses Consteel dan elektroda, untuk menghindari kemungkinan jembatan listrik antara bagian-bagian ini. Ini dapat membatasi panjang potongan maksimum yang dapat diterima pada tungku kecil sementara tungku besar dapat lebih toleran. Dalam praktiknya, skrap baja yang biasanya tersedia di pasar sudah kompatibel dengan EAF Consteel terkecil.
Dalam proses Consteel, muatan scrap terus menerus, sehingga kepadatan scrap tidak mempengaruhi operasi sebanyak yang terjadi pada tungku pengisian atas konvensional, di mana scrap yang terlalu ringan dapat membutuhkan lebih banyak biaya bucket, mengurangi efisiensi dan produktivitas, dan di mana terlalu banyak skrap berat menghasilkan penundaan dalam pencairan muatan, jika tidak sering terjadi kerusakan elektroda karena runtuhan skrap besar-besaran selama peleburan awal.
Proses Consteel dilakukan dengan menyeimbangkan input daya ke tungku dengan laju aliran massa bahan muatan (mirip dengan logika kontrol yang diterapkan di tungku yang diberi makan DRI) dan laju aliran massa yang diperlukan dicapai secara otomatis oleh logika kontrol proses, menyesuaikan laju pengumpanan konveyor yang lebih cepat untuk skrap ringan dan lebih lambat untuk skrap berat. Laju aliran massa dikendalikan oleh sistem penimbangan tungku dan/atau oleh sistem pelacakan muatan di instalasi yang lebih baru.
Potongan yang dikeluarkan oleh konveyor meleleh dengan cara direndam dalam kumpulan besar logam cair (tumit panas) yang menyediakan kondisi yang paling menguntungkan untuk peleburan potongan potongan berat, seperti bundel, yang cukup merepotkan untuk EAF konvensional. Satu-satunya persyaratan adalah mendistribusikan potongan berat secara merata di sepanjang muatan.
Secara umum, jauh lebih mudah untuk melelehkan potongan potongan berat dalam EAF dengan proses Consteel daripada di EAF konvensional dengan ukuran yang sama, dan kinerja tungku diuntungkan jika ukuran hot heel benar dan prosesnya dikombinasikan dengan pengadukan bawah. dengan N2 (nitrogen) atau Ar (argon). Biasanya tumit panas berukuran 42% sampai 50% dari berat tap. Massa logam cair ini dipertahankan di berbagai panas dan bertindak sebagai 'roda gila termal' yang menstabilkan untuk proses tersebut. Pada panas pertama kampanye tungku, tumit panas dibuat dengan melelehkan muatan ember. Ketika tungku perlu dikeringkan, muatannya dikurangi dan tumit panas digunakan untuk menyadap panas penuh. Gambar 3 memberikan tampilan skema dari garis proses Consteel.
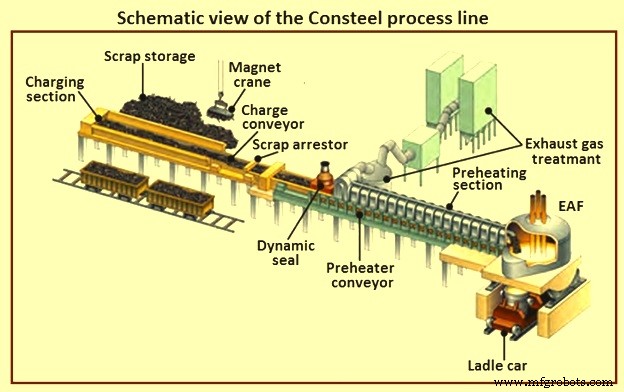
Gbr 3 Tampilan skema garis proses Consteel
Ada dua karakteristik utama yang membuat sistem Consteel berbeda dari kebanyakan teknologi EAF lainnya. Karakteristik ini adalah kombinasi dari pemanasan awal dan, yang lebih penting, pengisian terus menerus. Pemanasan awal penting untuk menghemat energi, tetapi pengisian terus menerus terbukti memiliki manfaat yang lebih besar, yaitu (i) biaya produksi rendah, (ii) produktivitas tinggi, (iii) fleksibilitas, (iv) pengurangan dampak lingkungan, dan (v) lebih besar keamanan
Pengisian skrap terus menerus mendistribusikan muatan di seluruh periode penyalaan. Tidak ada biaya ember yang digunakan dan konveyor mengumpankan skrap dari halaman langsung ke EAF. Atap EAF selalu tertutup sehingga penghisapan gas terus-menerus terjadi melalui sirkuit primer, bukan melalui kanopi di sirkuit sekunder. Di tungku, skrap meleleh dengan pencelupan dan busur listrik bekerja pada bak datar yang ditutupi oleh terak berbusa. Sistem kontrol EAF secara otomatis menyesuaikan kecepatan pengangkutan untuk mempertahankan rendaman baja pada suhu target dan mengontrol injeksi O2 dan C untuk mempertahankan terak berbusa yang tepat.
Pemanasan awal muatan efektif dalam mengurangi konsumsi energi. Penghematan energi yang dapat diperoleh adalah fungsi dari suhu pemanasan awal dan efisiensi leleh. Dengan asumsi suhu pemanasan awal rata-rata dalam kisaran 400 derajat C hingga 600 derajat C, penghematan energi mulai dari 80 kWh/ton hingga 120 kWh/ton baja cair yang disadap diperoleh. Nilai-nilai ini dikonfirmasi oleh pengalaman instalasi Consteel yang ada.
Siklus panas tipikal untuk EAF yang dilengkapi dengan sistem Consteel ditunjukkan pada Gambar 4. Karakteristik ini memberikan banyak keuntungan kepada Consteel dalam hal penghematan operasional dan pengurangan dampak lingkungan. Karakteristik operasional Consteel menghadirkan kebisingan yang lebih rendah ke lingkungan kerja, sedikit debu, dan tidak adanya pengisian bucket dengan kebisingan yang diakibatkannya, pengangkutan, dan hilangnya panas serta gas buang saat atap tungku dibuka untuk pengisian daya.
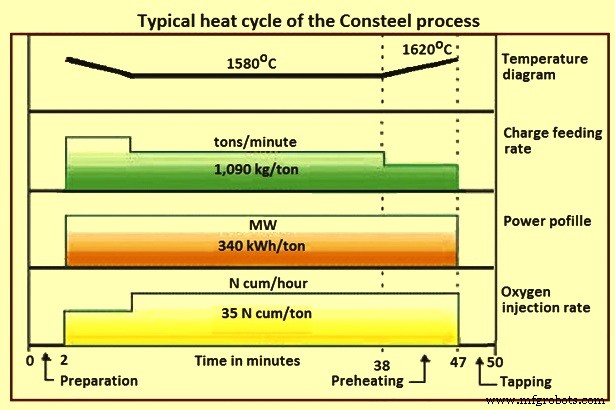
Gbr 4 Siklus panas khas dari proses Consteel
Secara metalurgi, baja cair di dalam tungku berada dalam keseimbangan yang lebih baik dan kecil kemungkinannya untuk menghasilkan reaksi kekerasan. Dinding samping, atap, dan tombak berpendingin air tungku tidak mengalami masalah kebocoran yang disebabkan oleh busur api atau benturan, sehingga meminimalkan risiko air di tungku. Semua ini berkontribusi untuk menciptakan lingkungan kerja yang lebih aman dan nyaman dibandingkan dengan standar industri baja pada umumnya.
Karakteristik utama dari proses Consteel terbaru adalah pengenalan solusi baru untuk meningkatkan jumlah dan efisiensi energi kimia yang digunakan dalam proses. Ini telah dikembangkan melalui uji laboratorium dan penggunaan analisis CFD secara ekstensif. Solusi baru ini menampilkan konveyor yang lebih luas untuk meningkatkan permukaan pertukaran, profil terowongan yang berbeda untuk meningkatkan pertukaran panas konvektif, dan bagian terowongan baru yang dilengkapi dengan burner, untuk meningkatkan masukan energi kimia. Melalui solusi baru, penggunaan energi kimia dikontrol, bagian demi bagian, dengan pengukuran terus menerus dari aliran gas buang, suhu, dan komposisi, dengan pengoptimalan otomatis parameter operasional yang relevan. Hasilnya adalah biaya pra-pemanasan yang lebih efektif dan biaya pengoperasian yang lebih rendah.
Perbandingan dengan pembuatan baja EAF konvensional
Perbedaan terbesar dengan pembuatan baja EAF konvensional adalah hasil yang lebih baik, meskipun ada beberapa aspek yang terkait dengan logistik dan pemeliharaan.
Operasi yang paling penting adalah pengelolaan aliran skrap dari halaman skrap ke tungku. Ini dilakukan dengan persiapan ember di EAF konvensional dan dengan sistem pengisian berkelanjutan dalam proses Consteel. Penanganan bahan baku di EAF konvensional biasanya dilakukan oleh crane perjalanan overhead dalam jumlah yang cukup untuk memiliki margin keamanan yang memadai terhadap kerusakan. Jumlah derek tergantung pada jumlah ember yang harus disiapkan dalam waktu tertentu, dengan mempertimbangkan ukuran panas tungku, kepadatan sisa dan ukuran ember. Proses Consteel mengadopsi organisasi yang berbeda dari halaman memo, biasanya menyimpan bahan baku di sisi konveyor pengisian. Ukuran dan jumlah derek pengisian tergantung pada laju pengumpanan sisa maksimum yang diperlukan oleh tungku (Gbr 3). Proses Consteel menyederhanakan logistik karena meminimalkan pergerakan sisa.
Praktek pemeliharaan tergantung pada peralatan scrap yard, peralatan tungku bay dan tungku EAF, bersama dengan pembuangan terak dan debu. Proses Consteel hanya memiliki crane perjalanan overhead untuk pengisian konveyor, yang juga dapat melakukan operasi penimbangan untuk setiap pengangkatan. Dalam hal perawatan EAF, hal ini sangat dipengaruhi oleh proses peleburan yang digunakan. Tekanan termal dan kimia yang mempengaruhi komponen tungku yang dapat dikonsumsi terutama bergantung pada parameter proses peleburan (Gbr 5).
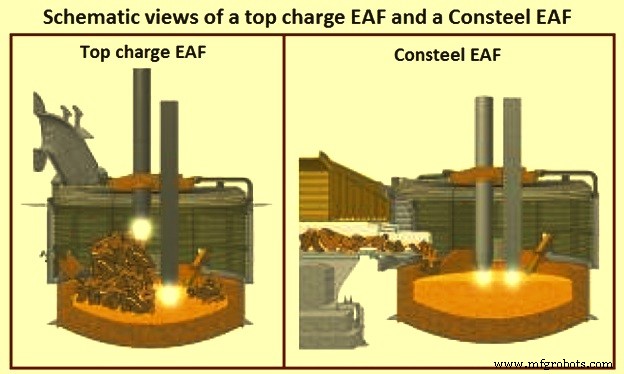
Gbr 5 Tampilan skema EAF muatan teratas dan EAF Consteel
Konsumsi elektroda memiliki biaya perawatan tertinggi, namun, proses Consteel memiliki konsumsi sekitar 15% lebih rendah karena diatur oleh tingkat oksidasi yang lebih rendah karena rasio pasca-pembakaran yang lebih rendah di dalam tungku. Erosi elektroda juga tergantung pada produktivitas toko lelehan. Pada kondisi kerja yang sama, proses Consteel memiliki produktivitas yang lebih tinggi, sehingga konsumsi elektroda dapat dianggap sama dengan EAF konvensional dengan produktivitas yang lebih rendah. Selain itu, operasi rendaman datar menjaga stabilitas busur listrik yang baik dan secara praktis menghilangkan terjadinya kerusakan elektroda.
Proses Consteel juga memiliki keausan lapisan refraktori yang lebih rendah karena kondisi pengoperasian yang lebih mulus daripada EAF konvensional dan menghasilkan lebih sedikit oksida besi dalam terak. Dengan proses Consteel, asalkan terak berbusa dengan benar, busur listrik dapat sepenuhnya ditutup dan dikubur di bawah lapisan pelindung yang mengurangi radiasi busur ke refraktori tungku selama hampir seluruh periode penyalaan. Ini juga menghilangkan pelepasan listrik pada atap dan cangkang tungku karena perawatan panel berkurang secara drastis.
Berkenaan dengan pemeliharaan konveyor skrap Consteel, ini sangat sederhana dan telah dikurangi menjadi tingkat pemeriksaan berkala terhadap struktur mekanik, motor listrik dan peralatan hidrolik, dan pemeliharaan terencana dari bagian-bagian yang paling penting. Lapisan tahan api dari bagian pemanasan awal tidak memiliki tekanan khusus dan biasanya dapat di-brick ulang setiap tahun.
Ujung mobil penghubung adalah komponen yang paling tertekan dari sistem konveyor karena menerima tegangan termal dari bak peleburan dan beban mekanis yang dihasilkan oleh pengangkutan skrap. Ini menjadi bagian dari program pemeliharaan terencana dan, sesuai pengalaman unit operasi, memiliki masa pakai rata-rata empat bulan. Batang suspensi mudah diganti, biasanya selama perputaran tungku. Analisis kegagalan menunjukkan rata-rata 100 batang suspensi patah setahun untuk konveyor yang terisi penuh.
Dalam hal pembuangan debu dan terak, proses Consteel mencapai produksi terak dan debu yang lebih rendah daripada EAF konvensional, karena sangat bergantung pada karakteristik utama proses yang merupakan pengisian terus menerus dan pemanasan awal muatan logam. Penghapusan muatan ember mengurangi pembentukan debu di tudung kanopi, dan bagian pra-pemanasan konveyor bekerja seperti ruang pengendapan di mana debu dapat mengendap pada skrap, mendorong daur ulang debu ke dalam tungku. Emisi debu keseluruhan dari 5 kg/ton hingga 9 kg/ton baja cair kurang dari EAF konvensional.
Fleksibilitas dengan bahan pengisi daya
Untuk praktik pembuatan baja EAF saat ini, kemungkinan untuk dengan mudah menyesuaikan muatan logam tungku untuk mengikuti variasi skenario biaya bahan baku dan permintaan pasar, jelas, sangat penting. EAF secara intrinsik fleksibel dalam hal bahan muatan. EAF yang beroperasi dengan proses Consteel memberikan fleksibilitas maksimum dalam pemilihan bahan pengisi logam, yang dapat berupa skrap, pig iron, DRI, dan logam panas, dalam semua kemungkinan kombinasi dan rasio. Pengisian terus menerus berarti ember tidak digunakan, konveyor terus menerus memasukkan muatan logam langsung ke EAF.
Proses pengisian terus menerus biasanya digunakan oleh EAF yang memproses DRI atau HBI dalam jumlah besar, karena pemrosesan batch (pengisian atas dengan ember) dari bahan ini terbukti tidak dapat dijalankan. Konsep ini telah diperluas ke pemrosesan skrap dengan diperkenalkannya proses Consteel. Kekurangan skrap dan listrik di beberapa negara telah menyebabkan penggabungan muatan skrap dengan logam panas. Pengalaman menunjukkan bahwa proses Consteel juga merupakan pilihan terbaik untuk memanfaatkan logam panas dalam pembuatan baja EAF. Hal ini pada dasarnya karena proses Consteel memungkinkan penyebaran dekarburisasi lelehan di seluruh waktu penyalaan, seringkali tanpa perubahan besar pada sistem gas buang utama dan tanpa menimbulkan penundaan dekarburisasi yang membatasi produktivitas EAF pengisian-atas tradisional saat muatan logam panas naik di atas sekitar 30% dari total.
Pengalaman dengan hot-metal di EAF dengan proses Consteel telah membentang dari 20% menjadi sekitar 86%, mencapai titik di mana tungku dapat dioperasikan seperti konverter oksigen dasar, tanpa tenaga listrik, dengan waktu blowing power-on/O2 sekitar 32 menit, namun masih dapat beroperasi dengan 100% biaya sisa saat dibutuhkan.
Jika biaya skrap baja turun dan tekanan meningkat untuk mengurangi emisi CO2 (karbon di-oksida), logam panas dapat dikurangi dan penggunaan skrap dapat ditingkatkan karena fleksibilitas yang disediakan oleh EAF dengan Proses baja. Contoh fleksibilitas Consteel adalah Consteel EAF 140 t di Vallourec-Sumitomo Brazil (Brasil), yang dipesan pada tahun 2012, yang telah dirancang untuk bekerja dengan campuran muatan yang terbuat dari skrap, hingga 40% pig iron dan hingga 40% hot metal. .
Ada EAF dengan proses Consteel, dipasang di Korea Selatan, di mana pengisian terus menerus dari scrap telah digabungkan dengan pengumpanan DRI dan HBI secara terus menerus. Oleh karena itu, proses Consteel dapat dengan mulus menggabungkan pengisian skrap secara terus menerus dengan segala bentuk muatan besi murni yaitu logam panas, besi kasar, DRI atau HBI seperti yang ditunjukkan pada Gambar 6.
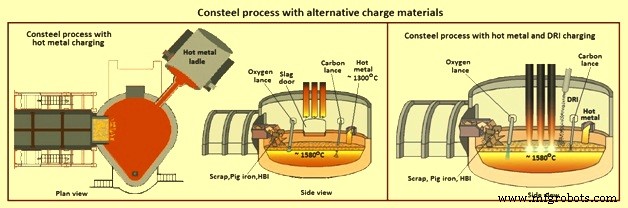
Gbr 6 Proses baja dengan bahan pengisi alternatif
Sebagai aturan umum, DRI dan HBI diumpankan ke tungku dengan cara tradisional yaitu langsung melalui atap tungku. Logam panas dituangkan ke dalam tungku melalui pintu atau pelari dinding samping, besi kasar, sebagai gantinya, dapat dicampur dengan skrap ke dalam konveyor pengisian. Seperti pig iron, juga scrap besi, dalam potongan beberapa ton masing-masing, dapat diisi melalui proses Consteel bersama dengan scrap.
Manfaat proses Consteel
Manfaat yang telah terbukti dari proses Consteel Meliputi (i) pengembalian cepat, (ii) fleksibilitas tinggi, (iii) ramah lingkungan, (iv) keselamatan personel operasional, (vi) gangguan minimum pada jaringan listrik, (vii) pengurangan biaya logistik, pemeliharaan dan tenaga kerja, (viii) peningkatan penggunaan energi kimia, (ix) konsumsi elektroda yang lebih rendah, (x) peningkatan hasil skrap dibandingkan dengan tungku yang diisi batch, (xi) kontrol berkelanjutan dan optimalisasi parameter operasional, dan ( xii) meningkatkan kontrol biaya melalui pelacakan kualitas dan kuantitas memo otomatis.
Selain itu, ada manfaat lingkungan. Produksi debu dalam EAF yang diisi ember tradisional menghasilkan sekitar 20 kg/ton baja cair. Produksi debu di EAF setara dengan proses Consteel sekitar 30% hingga 40% lebih rendah. Ini karena daur ulang alami dari deposit debu pada skrap di dalam terowongan pemanas dan tingkat dekarburisasi yang lebih rendah yang diizinkan oleh teknologi proses ini. Produksi debu yang lebih rendah berarti biaya pembuangan yang lebih rendah, yang semakin mahal karena peraturan lingkungan yang lebih ketat.
Proses ini mengurangi emisi PCCD/F dan NOx. Scrap dapat mengandung minyak, cat, plastik dan zat lain yang dapat berubah menjadi polutan selama proses pembuatan baja. Beberapa zat ini dapat menjadi prekursor polychlorinated di-benzo-p-dioxins (PCDD), polychlorinated di-benzo-p-furans (PCDF) dan polychlorinated biphenyls (PCD), suatu kelas zat yang emisinya telah sangat dibatasi oleh zat baru. peraturan lingkungan. Emisi polutan ini merupakan fenomena kompleks yang dipengaruhi oleh beberapa faktor bersamaan seperti jumlah prekursor dalam muatan sisa, jenis proses yang dilakukan di tungku dan, pada akhirnya, dan pada sistem ekstraksi gas buang, yang berperan peran kunci, karena emisi diukur di tumpukan.
Telah didemonstrasikan bahwa diberikan muatan sisa dengan kandungan yang sama dari prekursor PCDD/F (misalnya plastik polivinil klorida), proses Consteel melepaskan jumlah PCDD/F yang jauh lebih rendah dalam gas buang dibandingkan dengan proses diskontinu yang setara, dengan biaya batch.
Ada perhatian yang berkembang juga untuk emisi NOx dan telah ditemukan bahwa busur listrik adalah penyebab utama emisi ini dalam proses EAF. Jumlah NOx yang dipancarkan per ton baja cair yang dihasilkan melalui EAF bermuatan ember konvensional adalah sekitar 250 g/ton baja cair, sedangkan untuk muatan kontinu nilai ini hanya 120 g/ton baja cair. Hal ini disebabkan oleh pengoperasian busur listrik di bawah pembentukan terak, yang mengurangi interaksi busur listrik ini dengan O2 dan N2 atmosfer.
Menggunakan EAF untuk melelehkan skrap yang diisi oleh ember sangat bising dibandingkan dengan melelehkan muatan DRI yang terus menerus. Ini karena busur terbakar di bak datar dan di bawah terak berbusa. Proses Consteel memperluas jenis operasi ini ke pemrosesan skrap, yang secara signifikan mengurangi emisi akustik pabrik. Selama operasi proses Consteel, tingkat intensitas suara di dekat tungku dilaporkan sekitar 85 dBA sedangkan dengan EAF yang diisi ember, tingkat intensitas suara umumnya di atas 90 dBA.
Beberapa parameter operasi yang dicapai di pabrik yang beroperasi adalah (i) pengurangan 30% sampai 40% emisi debu yang harus dibuang, (ii) ketersediaan 98%, (iii) produktivitas tinggi pada 2,7 ton baja cair /jam/MW, ( iv) pengurangan konsumsi daya pada 300 kWh/ton baja cair, (v) peningkatan hasil skrap sebesar 1% hingga 2%, (vi) peningkatan produktivitas sebesar 33%, (vii) pengurangan konsumsi elektroda sebesar 40%, (vii) pengurangan emisi debu sekitar 30%, (viii) penghematan listrik diperkirakan 60 kWh/t untuk retrofit, dan (ix) penghematan biaya operasional tahunan sebesar USD 1,90 / ton baja mentah (termasuk peningkatan produktivitas, pengurangan konsumsi elektroda, dan peningkatan hasil ). Selain itu juga terjadi penurunan gangguan listrik pada jaringan, dan penggunaan bahan bakar bekas yang lebih rendah serta konsumsi bahan bakar yang tidak menggunakan burner.