Lapisan Tahan Api dari Tungku Busur Listrik
Lapisan Tahan Api Tungku Busur Listrik
Refraktori adalah bahan yang tahan terhadap suhu tinggi tanpa perubahan signifikan dalam sifat kimia atau fisik. Bahan tahan api sangat penting untuk operasi tungku busur listrik (EAF) karena memungkinkan penahanan baja cair di perapian tungku tanpa merusak struktur tungku. EAF membutuhkan berbagai produk tahan api di mana yang paling penting adalah produk tahan api yang bersentuhan langsung dengan baja cair.
Refraktori untuk lapisan EAF bergantung pada desain EAF. Kondisi operasi juga memiliki pengaruh besar pada kinerja refraktori. Kondisi operasi di EAF memerlukan refraktori yang secara kimia dasar dan memiliki ketahanan yang sangat baik terhadap suhu tinggi dan siklus termal. Desain EAF saat ini menampilkan lubang keran bawah eksentrik (EBT) dan tungku ini membutuhkan refraktori khusus untuk lapisannya. Penampang khas EAF yang menunjukkan zona tungku yang berbeda ada di Gambar 1.
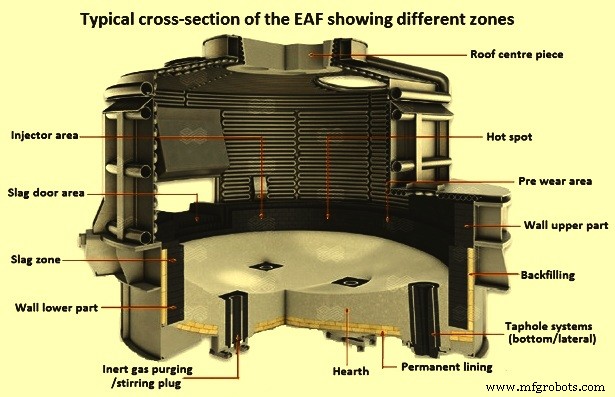
Gbr 1 Penampang khas EAF yang menunjukkan zona berbeda
Ada fitur desain yang berbeda dari EAF tetapi mereka terutama dikelompokkan menjadi tiga bidang yaitu (i) desain sadap seperti sadap samping atau sadap bawah, (ii) sumber daya seperti AC (arus bolak-balik) atau DC (arus searah), dan (iii) penggunaan oksigen tambahan (O2) untuk meningkatkan laju leleh.
EAF penyadapan samping memiliki cerat yang memanjang dari dinding samping tungku untuk penyadapan baja cair di sendok. Ceratnya dilapisi tahan api, dan lubang keran melalui dinding samping tungku menghubungkan tungku di dalam dengan cerat. EAF sadapan samping miring sekitar 45 derajat, dan karenanya memerlukan lapisan dinding samping refraktori yang lebih tinggi di sisi sadapan tungku untuk menampung baja cair. EAF sadapan bawah memiliki taphole melalui bagian perapian bawah tungku dan membutuhkan produk refraktori taphole khusus. Penyadapan bawah juga memungkinkan pengurangan ketinggian dinding samping tahan api karena sudut kemiringan sadapan yang lebih rendah sekitar 15 derajat hingga 20 derajat. Kedua jenis desain sadap ini biasanya ditunjukkan pada Gambar 2.
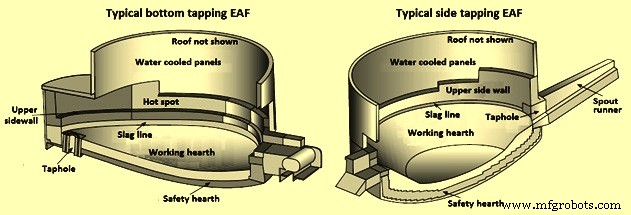
Gbr 2 Dua jenis desain sadap
Sumber listrik AC membutuhkan tiga kolom elektroda di dalam tungku untuk tiga fase listrik. Elektroda ini telah meningkatkan arc flare selama operasi yang dapat menimpa dinding samping refraktori yang mengakibatkan hot spot. Titik panas harus diperhatikan dengan desain refraktori. AC EAF juga membutuhkan tiga lubang melalui atap tahan api dan bagian tengah atap tahan api di antara elektroda seringkali merupakan area yang membatasi kinerja tungku. EAF DC memiliki elektroda tunggal melalui atap dengan busur listrik yang melewati langsung ke bak baja cair yang menghubungi elektroda anoda bawah untuk menyelesaikan rangkaian listrik. DC EAF memiliki arc flare yang lebih rendah ke dinding samping refraktori dan karenanya tidak ada hot spot. Desain atap lebih sederhana dengan kondisi pengoperasian yang tidak terlalu sulit. Namun, perapian tungku harus berisi elektroda bawah, yang memperumit desain refraktori dari dasar tungku.
Penggunaan tombak dan burner O2 tambahan untuk meningkatkan desain dan kinerja refraktori berdampak pada laju leleh. O2 yang diarahkan dari tombak atau pembakar dapat dibelokkan oleh bahan bekas atau muatan dan dapat menimpa lapisan tahan api. Ini menghasilkan panas berlebih yang terlokalisasi dan keausan yang dipercepat dari refraktori. Kondisi oksidasi lokal juga dapat terjadi karena O2 dan ini dapat mengakibatkan erosi yang cepat pada lapisan refraktori.
Mekanisme keausan tahan api di EAF
Ada beberapa jenis mekanisme keausan refraktori seperti yang dijelaskan di bawah yang dikenakan refraktori EAF selama pembuatan baja. Penting untuk memahami dengan benar mekanisme keausan yang beroperasi di setiap zona untuk merancang dan mengelola sistem refraktori EAF dengan benar.
Korosi – Ini adalah mekanisme keausan yang paling penting dalam kasus refraktori EAF. Korosi terjadi karena reaksi kimia oksida logam (FeO, SiO2, atau MnO) dalam terak dengan bahan tahan api. Magnesia (MgO) dari lapisan refraktori larut dalam terak cair, dengan tingkat kejenuhan berkisar antara 6% hingga 14%, tergantung pada kandungan FeO dan suhu penangas. Reaksi korosi kimia mengakibatkan keausan lapisan dan produk reaksi menjadi bagian dari terak. Reaksi korosi dapat diminimalkan dengan menetralkan FeO dengan fluks dan mengontrol kandungan O2 terak. Korosi juga dapat diminimalkan dengan menjenuhkan terak dengan MgO melalui cara eksternal (misalnya penambahan dolomit terkalsinasi atau magnesit terkalsinasi). Cara lain untuk mengendalikan korosi adalah dengan menggunakan batu bata tahan api yang mengandung karbon (C). C dalam refraktori mendeoksidasi terak korosif pada antarmuka refraktori / terak sehingga meminimalkan korosi lapisan.
Oksidasi – Dalam keausan refraktori oleh oksidasi, C dari lapisan refraktori dioksidasi dengan mereaksikan baik dengan O2 atau FeO dalam terak. Saat C dari lapisan refraktori bereaksi, kandungan C dari refraktori berkurang dan refraktori kehilangan kekuatannya dan hanyut. Mekanisme oksidasi C juga terjadi pada permukaan dingin bata jika terdapat lubang pada cangkang baja. O2 dari udara bereaksi dengan bata C, dan bagian belakang lapisan bata berubah menjadi bubuk.
Erosi – Ini adalah mekanisme refraktori lain yang terjadi di EAF. Erosi adalah keausan fisik refraktori karena baja cair dan terak cair bergerak di atas permukaan lapisan refraktori dan secara fisik mengikis atau mengikis lapisan. Erosi adalah mekanisme umum untuk keausan refraktori di taphole, slag line, bukaan elektroda atap, dan saluran pembuangan.
Mencair – Ini adalah salah satu mekanisme keausan untuk refraktori di EAF. Busur listrik tanpa pelindung menghasilkan suhu yang jauh di atas titik leleh banyak refraktori. Mencair adalah perubahan fase sederhana dari refraktori dari padat ke cair, dan fase cair ketika terbentuk kemudian hanyut. Pencairan dapat menjadi masalah serius pada lapisan jika tidak terdeteksi tepat waktu dan tidak segera diperbaiki.
Hidrasi – Karena air banyak digunakan di EAF saat ini, ada insiden kebocoran air. Refraktori mudah rusak oleh air atau uap karena hidrasi kandungan MgO atau kapur dari produk refraktori. Hidrasi menghasilkan perluasan butir individu yang terdiri dari lapisan tahan api. Butir-butir ini tumbuh dan pecah, merusak lapisannya.
Spalling – Keausan refraktori karena spalling terjadi ketika refraktori mengalami pemanasan cepat atau pendinginan cepat. Pemanasan cepat atau pendinginan cepat menyebabkan tegangan pada lapisan dan ketika tegangan ini melebihi kekuatan yang melekat pada bahan tahan api, maka itu menyebabkan keretakan. Ketika retakan ini berpotongan, potongan refraktori jatuh dari lapisan. Mekanisme kerusakan refraktori ini sering diamati pada refraktori atap karena terkena pemanasan dan pendinginan siklik.
Zona EAF
Berdasarkan kondisi operasi yang ada di EAF, tungku dapat dibagi menjadi zona tertentu. Masing-masing zona ini memiliki persyaratan refraktori yang berbeda-beda sifatnya. Zona ini telah ditunjukkan pada Gambar 1 dan Gambar 2. Zona utama EAF adalah (i) perapian yang berisi baja cair serta bahan pengisi awal, (ii) garis terak yang merupakan area transisi antara perapian dan dinding samping, (iii) dinding samping atas yang terletak di atas garis terak, dan di bawah panel berpendingin air, (iv) taphole yang merupakan bukaan yang disediakan untuk sadapan baja cair, dan (v) atap yang memiliki bagian refraktori (kadang-kadang disebut sebagai delta), untuk menyediakan bukaan bagi elektroda untuk memasuki tungku dan untuk gas buang tungku agar ada tungku.
EAF saat ini adalah tungku EBT dan umumnya menggunakan refraktori magnesit (MgO) atau magnesit-karbon (Mag-C) di zona kontak baja cair. Refraktori khusus dengan ketahanan kejut termal yang baik umumnya digunakan di atap/delta, taphole, dan cerat atau runner tungku. Deskripsi berikut memberikan rekomendasi refraktori umum untuk setiap zona EAF..
Perapian – Zona perapian EAF menahan baja cair pada suhu tinggi dan tahan terhadap benturan material bermuatan berat. Selain itu, perapian harus menahan korosi oleh terak cair saat tungku disadap. EAF tipikal menggunakan tungku tahan api dua komponen yang terbuat dari batu bata sekitar 230 mm sebagai lapisan pengaman pada cangkang baja bawah (kadang disebut sub-bawah) dan 300 mm hingga 600 mm magnesit monolitik sebagai lapisan kerja. Beberapa EAF memiliki semua perapian batu bata, di mana lapisan awal seluruhnya terbuat dari batu bata, dan bahan monolitik hanya digunakan untuk memperbaiki lubang di perapian batu bata setelah beberapa periode operasi. Batu bata MgO yang diresapi tar umumnya digunakan untuk lapisan pengaman. Bata yang digunakan untuk safety lining memiliki kandungan MgO berkisar antara 90% sampai 97%. Batu bata ini memiliki kekuatan dan sifat tahan terak untuk menahan rendaman cairan jika baja cair atau terak cair menembus lapisan kerja. Lapisan pengaman berfungsi sebagai lapisan permanen dan tidak perlu sering diganti.
Lapisan kerja monolitik juga memiliki kandungan MgO yang tinggi (60% hingga 95%) dan terdiri dari bahan granular kering. Ukuran butir bahan perapian diformulasikan agar dapat dipadatkan dengan mudah dengan menggunakan vibrator selama pemasangan lapisan. Bahan perapian monolitik umumnya memiliki oksida pengotor, seperti FeO, untuk memfasilitasi sintering. Temperatur yang tinggi dari panas awal menyebabkan sintering (ikatan, densifikasi, dan penguatan) pada lapisan monolitik. Sintering menyebabkan lapisan menjadi cukup kuat dan tahan penetrasi. Lapisan perapian dirancang sedemikian rupa sehingga sekitar sepertiga bagian atas dari ketebalan bahan lapisan monolitik disinter sepenuhnya, sedangkan sepertiga tengah lapisan hanya disinter sebagian, dan sepertiga bagian bawah dari bahan lapisan monolitik terhadap keamanan lapisan tidak disinter sama sekali. Efek pelapisan ini memfasilitasi penambalan refraktori perapian ketika refraktori perapian rusak karena penetrasi atau korosi. Area yang rusak dapat dibersihkan dengan menghilangkan magnesit yang ditembus dan disinter dan diperbaiki dengan bahan monolitik baru, yang akan disinter selama panas berikutnya yang dibuat di tungku.
Desain dasar EAF saat ini sering kali mencakup elemen pengaduk gas yang membutuhkan bahan tahan api berpori atau tuyer melalui refraktori padat untuk mengirimkan gas pengaduk ke baja cair. Pengadukan gas ini dapat menyebabkan erosi refraktori perapian yang mengakibatkan kebutuhan pemeliharaan rutin refraktori perapian.
Garis terak – Garis terak EAF adalah area transisi antara perapian dan dinding samping. Daerah ini terkena suhu tinggi karena paparan busur listrik, oksidasi, dan pelampiasan api dari injeksi O2 tambahan, dan yang paling penting adalah serangan terak dari terak suhu tinggi yang mengandung FeO, SiO2, dan MnO. Pemilihan refraktori di jalur terak harus dikoordinasikan dengan hati-hati dengan kimia terak yang diharapkan. Dalam kasus EAF yang memproduksi baja C, terdapat pembentukan terak kaya kapur, FeO -SiO2 dengan rasio kapur:silika plus 2:1. Ini menuntut refraktori dasar. Di daerah garis terak EAFs umumnya digunakan batu bata Mag-C atau batu bata magnesit yang diresapi tar. Dalam EAF untuk produksi baja tahan karat, bata krom magnesit butir leburan yang lebih netral dapat digunakan.
Desain refraktori garis terak di EAFs adalah kombinasi dari bata dan refraktori monolitik. Desain yang sangat umum untuk garis terak adalah bata Mag-C dengan ketebalan 300 mm hingga 450 mm dan dengan kandungan C 10% hingga 20%. Fase C batu bata terdiri dari grafit dan ikatan resin karbon. Bahan C ini memiliki ketahanan yang sangat baik terhadap serangan terak serta ketahanan yang sangat baik terhadap suhu tinggi. Namun, C rentan terhadap oksidasi dan untuk melindungi refraktori garis terak dari serbuk logam oksidasi seperti aluminium, silikon, atau magnesium ditambahkan. Serbuk logam ini bergabung dengan C untuk membentuk karbida yang memiliki ketahanan oksidasi yang lebih tinggi. Karbida juga memperkuat batu bata tahan api. Kekuatan diperlukan untuk menahan aksi erosi dari terak cair dan pencucian baja yang terjadi di zona garis terak tungku. Batu bata Mag-C di garis terak juga dilindungi oleh refraktori monolitik. Pemasangan awal refraktori monolitik biasanya mencakup semua atau sebagian dari batu bata garis terak. Namun, karena kondisi operasi yang sulit di zona ini, refraktori terkorosi. Perlindungan tambahan dari garis terak dilakukan dengan menembak dengan campuran guniting berbasis MgO untuk membangun lapisan pelindung pada garis terak. Aktivitas pembentukan refraktori garis terak harus sering dilakukan tergantung pada tingkat keparahan kondisi operasi.
Dinding sisi atas – Dinding sisi atas EAF dilapisi dengan batu bata Mag-C yang mirip dengan batu bata garis terak. Dinding sisi atas mengalami arc flare (suhu yang sangat tinggi) dan pelampiasan oleh skrap berat selama proses pengisian tungku. Selama penyadapan tungku, ketika tungku miring, baja cair dan terak cair berada dalam kontak dengan dinding samping atas pada sisi sadapan tungku. Selain itu, bata dinding sisi atas harus tahan terhadap korosi oleh terak dan percikan api dari tombak O2 dan pembakar oxy-fuel. Batu bata Mag-C dengan kandungan C 5% sampai 20% cocok untuk pelapis dinding sisi atas. Berbagai kualitas dan kemurnian magnesit, grafit dan serbuk logam digunakan. Pada AC EAF, yang memiliki hot spot di dinding sisi atas, diperlukan batu bata dengan kualitas lebih tinggi. Batu bata berkualitas lebih tinggi ini harus didasarkan pada butiran magnesia leburan dibandingkan dengan butiran magnesia sinter yang digunakan untuk batu bata kualitas standar. Batu bata magnesia yang menyatu telah meningkatkan ketahanan suhu tinggi tetapi harganya jauh lebih tinggi.
Refraktori taphole – Refraktori taphole diperlukan untuk EAF tap samping dan EAF tap tap bawah. Kondisi operasi di kedua jenis tungku ini serupa terdiri dari mengalir pada kecepatan tinggi baja cair dan pada tingkat lebih rendah terak cair melalui lubang tap berdiameter 125 mm sampai 200 mm. Aliran kecepatan tinggi mengikis refraktori taphole. Di tungku sadap samping, refraktori lubang tap memiliki banyak desain alternatif. Alternatif yang memiliki desain paling sederhana terdiri dari meninggalkan bukaan di dinding samping saat memasang lapisan awal dan ketika bata selesai, baik selongsong taphole tahan api atau pipa baja ditempatkan di bukaan taphole. Kemudian campuran guniting berbasis MgO digunakan untuk mengisi rongga antara selongsong atau pipa dan tembok yang berdekatan. Alternatif kedua terdiri dari penggunaan rakitan taphole besar dengan taphole yang telah dibentuk sebelumnya. Rakitan ini dipasang di EAF sebelum peletakan tembok samping tembok. Setelah rakitan taphole diposisikan dengan benar, batu bata yang berdekatan selesai dibuat, menciptakan kesesuaian yang erat antara rakitan taphole dan dinding samping tembok bata.
Refraktori taphole harus berkualitas tinggi. Jika taphole dibuat dengan campuran guniting yang disemprotkan di sekitar mandrel pipa baja, campuran guniting harus berkualitas tinggi. Campuran guniting harus memiliki kekuatan dan ketahanan erosi maksimum untuk meminimalkan aksi erosif dari baja cair yang mengalir. Dalam kasus rakitan taphole di mana selongsong tahan api digunakan, selongsong itu juga harus dari bata MgO berkualitas tinggi dengan C dan serbuk logam. Penambahan logam pada rakitan batu bata taphole Mag-C memberikan kekuatan tambahan dan ketahanan oksidasi pada batu bata dalam aplikasi penting ini.
Tungku sadap samping memiliki cerat yang memanjang dari lubang sadap untuk memungkinkan baja cair mengalir ke sendok. Cerat adalah bentuk pelari monolitik pracetak yang ditempatkan di cangkang baja pelari selama proses pelapisan. Bentuk runner pracetak terbuat dari castable berbasis MgO jika praktik pengoperasian tungku mengakibatkan terak masuk ke taphole dan runner tungku. Resistensi terak dari MgO diperlukan untuk menangkal serangan terak. Di sisi lain, jika praktik pengoperasian EAF membatasi masuknya terak ke dalam taphole dan runner, maka castable alumina tinggi dan kekuatan tinggi digunakan untuk runner pracetak. Pelari alumina tinggi umumnya memiliki masa pakai yang lebih tinggi karena peningkatan ketahanan kejut termal dan kekuatan yang lebih tinggi dibandingkan dengan pelari pracetak magnesit.
EAF sadapan bawah memerlukan selongsong taphole yang dirancang khusus dan blok ujung untuk desain taphole. Selongsong taphole berada di dalam perapian di rakitan tempat duduk taphole. Rakitan dapat dibuat dari bentuk bata atau bentuk pracetak yang menghasilkan lubang berdiameter sekitar 450 mm melalui refraktori perapian tungku. Selongsong taphole dipusatkan di dalam rakitan tempat duduk taphole dan campuran castable atau serudukan dasar dikemas dalam bukaan melingkar antara selongsong dan blok tempat duduk. Taphole sleeve adalah blok Mag-C yang terbuat dari magnesia dengan kemurnian tinggi atau butiran magnesia leburan dengan kandungan C 10% hingga 15%. Serbuk logam digunakan sebagai bahan penguat untuk memaksimalkan ketahanan terhadap erosi dan oksidasi. Bagian bawah taphole melampaui cangkang tungku memanfaatkan bentuk yang disebut end block. Blok ujung adalah bata Mag-C serupa yang ditahan di tempatnya dengan pengecoran blok ujung yang dipasang pada EAF. Blok ujung terkena lingkungan luar dan diharuskan memiliki ketahanan oksidasi yang sangat baik serta ketahanan erosi yang tinggi untuk menahan aksi erosi aliran taphole. Blok ujung cukup sering menjadi faktor pembatas untuk kinerja taphole. Saat erosi refraktori terjadi, aliran sadapan mulai berkobar, meningkatkan reoksidasi baja cair. Maka penting untuk melakukan perbaikan panas untuk mengganti blok ujung dan selongsong taphole.
Atap dan Delta – Refraktori atap EAF untuk tungku AC dan DC biasanya berbentuk pracetak alumina tinggi (70 % Al2O3 hingga 90 % Al2O3) yang memiliki kekuatan tinggi. Karena, atap terangkat dan berayun menjauh dari badan tungku selama proses pengisian, refraktori di atap mengalami kejutan termal yang ekstensif. Ekspansi termal yang lebih rendah dari castable alumina tinggi dibandingkan dengan castables dasar menawarkan keuntungan dalam menahan kejutan termal. Selanjutnya, castable alumina tinggi memiliki kekuatan yang lebih tinggi daripada castables dasar. Oleh karena itu, atap alumina tinggi lebih mampu menahan tekanan yang timbul saat atap diangkat dan dipindahkan selama operasi tungku. Refraktori atap EAF biasanya bertahan lebih lama.
Atap juga memungkinkan gas buang tungku untuk meninggalkan tungku melalui saluran. Sementara pintu keluar langsung dari tungku biasanya didinginkan dengan air, ada zona berlapis tahan api dalam sistem saluran. Refraktori di saluran pembuangan harus mampu menahan sisa-sisa terak dan abrasi terak dari gas buang bermuatan partikulat yang bergerak dengan kecepatan tinggi. Bahan refraktori pada ductwork adalah bata alumina (50 % Al2O3 sampai 70 % Al2O3) atau campuran fire clay/alumina guniting (40 % Al2O3 sampai 60 % Al2O3). Kedua bahan ini memiliki kombinasi yang diperlukan antara ketahanan kejut termal dan ketahanan terak untuk menahan kondisi pengoperasian.
Refraktori untuk EAF DC
Tungku listrik DC memiliki persyaratan refraktori khusus karena fakta bahwa elektroda balik biasanya dipasang di bagian bawah tungku (beberapa tungku DC menggunakan pengaturan alternatif dengan dua elektroda grafit). Dalam kasus dasar konduksi arus, lapisan tahan api di tengah dasar tungku bertindak sebagai anoda. Pelat tembaga biasanya dihubungkan di bawah refraktori konduktif dan batang bus tembaga kembali terhubung ke pelat. Dalam hal ini persyaratan khusus untuk refraktori adalah hambatan listrik yang rendah (sebaiknya kurang dari 0,5 mili-ohm per meter), konduktivitas termal yang rendah, dan ketahanan aus yang tinggi.
Dalam kasus EAF DC, desain refraktori perapian adalah untuk menggabungkan elektroda bawah. Kondisi pengoperasian untuk refraktori elektroda bawah sangat keras. Temperatur tinggi yang terlokalisasi dan turbulensi yang intens sering terjadi pada permukaan elektroda bawah. Kondisi ini membutuhkan refraktori dengan stabilitas dan kekuatan suhu tinggi. Untuk EAF DC yang menggunakan elektroda bagian bawah pin atau sirip, refraktori monolitik magnesit getar kering yang mengandung 5% hingga 10% C dapat digunakan. Namun, lebih disukai jika refraktori monolitik lebih tahan suhu dan dengan kandungan MgO yang lebih tinggi. Bahan monolitik dapat dipasang baik panas atau dingin. Di bawah lapisan kerja, bata Mag-C tiga lapis dipasang. Kandungan C sisa dari batu bata berkisar antara 10% sampai 14%.
Konfigurasi elektroda balik billet menggunakan satu hingga empat billet baja besar (berdiameter sekitar 250 mm) tergantung pada ukuran tungku. Billet tertanam di refraktori bawah. Billet dikelilingi dengan bata tahan api dasar. Untuk sisa perapian, campuran serudukan magnesit khusus digunakan. Campuran serudukan magnet digunakan untuk mempertahankan area bata di sekitar elektroda.
Jenis pin elektroda balik menggunakan beberapa pin logam berdiameter 250 mm hingga 500 mm untuk menyediakan jalur balik aliran listrik. Pin ini benar-benar menembus refraktori ke bagian bawah tungku di mana mereka melekat pada pelat logam. Campuran serudukan magnesit kering digunakan untuk seluruh lapisan perapian. Campuran ini menabrak antara pin logam. Atau bata Mag-C dapat digunakan di area sekitar anoda. Ini membantu meningkatkan masa pakai dasar tungku tetapi lebih mahal.
Elektroda pengembalian sirip baja menggunakan sirip baja yang disusun dalam sebuah cincin di dasar tungku untuk membentuk beberapa sektor. Setiap sektor terdiri dari pelat tanah horizontal dan beberapa sirip baja yang dilas yang menonjol ke atas melalui refraktori. Campuran serudukan magnesit kering digunakan di antara sirip. Perapian juga dilapisi dengan bahan ini.
Ada desain lain yang menggunakan refraktori konduktif, baik bata atau monolitik, yang merupakan kombinasi C dan magnesit, untuk mengalirkan arus listrik dari bak ke sambungan listrik tembaga di bagian bawah tungku. Refraktori konduktif terdiri dari campuran rumit magnesit, grafit, dan serbuk logam dengan kemurnian tinggi untuk mencapai kombinasi yang diperlukan antara refraktori suhu tinggi dan konduktivitas listrik untuk menahan baja cair serta untuk menghantarkan arus listrik.
Poin penting yang perlu dipertimbangkan selama pemasangan refraktori di EAF DC adalah pola zonasi, kontur perapian, lokasi garis terak, kapasitas baja tungku, lokasi taphole, ukuran dan sudut taphole, orientasi atap/delta, kelonggaran ekspansi, lokasi port burner, konstruksi pintu terak, elemen pengaduk bawah, dan elektroda bawah tungku DC.
Prosedur untuk memasang lapisan baru di EAF
Prosedur tipikal untuk pemasangan lapisan baru EAF yang lengkap dijelaskan di bawah ini.
Tungku dibawa ke posisi rata dan cangkang dibersihkan dari semua kotoran sebelum memulai pelapisan tungku. Ini membantu untuk menemukan pusat tungku yang tepat dan membuat tanda di bagian tengah bawah cangkang. Konstruksi yang disukai adalah batu bata magnesit persegi panjang yang diletakkan di atas permukaan datar dengan menggunakan bahan dasar granular sebagai pengisi untuk memberikan permukaan yang rata terhadap cangkang baja bulat. Setelah menemukan blok tempat duduk taphole EBT, elemen pengaduk bagian bawah dan memungkinkan elektroda bawah tungku dalam kasus DC EAF, lapisan pertama bata sub-perapian diletakkan kering, rapat dan rata, dan mortar magnesit kering disapu ke dalam sambungan bata. Bahan pengisi tambahan ditempatkan di sekeliling jalur pertama ini dan diratakan. Kursus kedua diletakkan pada sudut 45 derajat ke kursus pertama dan sekali lagi mortar magnesit kering disapu ke dalam sambungan. Proses ini diulang untuk tiga atau empat kursus datar. (Ada alternatif, kurang disukai, desain lapisan pengaman yang meletakkan dua sampai empat program datar yang mengikuti kontur melengkung dari shell baja. Ini dapat digunakan di EAF di mana shell memiliki radius bola kecil dan memberikan ketebalan yang lebih seragam di bahan perapian monolitik).
Pada ketinggian yang tepat, batu bata berbentuk kunci digunakan untuk memulai jalur stadion pertama. Lebih disukai untuk memulai dengan cincin terbesar 25 mm dari cangkang dan bekerja ke arah tengah. Untuk menutup cincin, batu bata kunci dipotong pada gergaji batu bata dengan dimensi yang tepat yang diperlukan untuk menutup cincin. Jika bentuk potongannya kurang dari setengah bata, dua bentuk potongan harus digunakan. Kekosongan di ujung jalur hingga cangkang diisi dengan bahan magnesit granular. Cincin stadion berikutnya dipasang dengan cara yang sama. Kontur perapian stadion yang ditunjukkan pada gambar tahan api tungku harus diikuti dengan hati-hati untuk meninggalkan ruang yang cukup untuk menambahkan bahan perapian monolitik dengan ketebalan yang sesuai.
Untuk tungku EBT, bahkan lebih penting untuk mengikuti gambar dasar tahan api dengan tepat. Ada sebagian cincin bata dengan jari-jari yang bervariasi memanjang ke bagian hidung tungku yang harus dijaga agar tetap rata. Salah satu cara untuk memfasilitasi ini adalah dengan mengebor lubang di bagian atas datar bata bawah tepat di tengah tungku dan kemudian menggunakan sapu dengan paku di atasnya memanjang dari tengah bata ini sebagai mandrel untuk menggambar lingkaran dan busur untuk cincin stadion dan cincin parsial memanjang ke hidung.
Jika bahan perapian monolitik tidak digunakan, jalur terakhir atau dua jalur terakhir di perapian semua bata diletakkan dalam konstruksi rowlock (di tepi) atau tentara (di ujung). Konstruksi Rowlock atau tentara memberikan kontak bata-ke-bata yang jauh lebih besar dan meminimalkan naiknya perapian dalam pelayanan. Sekali lagi, semua lapangan di perapian dan stadion dikeringkan dan disapu dengan mortar magnesit untuk mengisi sambungan.
Setelah cincin stadion selesai, batu bata garis terak dipasang tentu saja menggunakan konsep keying up yang sama yang digunakan untuk cincin stadion. Garis terak juga harus dipasang lebih dari 25 mm dari cangkang baja untuk memungkinkan ekspansi termal tanpa mengelupas atau mengangkat batu bata. Cincin bata atau cincin parsial harus dilanjutkan ke dinding samping dan titik panas sampai panel berpendingin air atau bagian atas tungku tercapai.
Kusen pintu adalah area desain penting untuk lapisan tahan api. Beberapa desain hanya menggunakan bentuk kunci biasa dalam kursus yang saling terkait sebagai kusen pintu mereka, dan desain ini cukup berhasil. Desain lain menggunakan bentuk kusen pintu khusus yang memiliki luas permukaan lebih besar untuk interlocking yang lebih baik antara jalur dan sudut yang lebih tajam yang membuka bukaan pintu dan menghilangkan atau mengurangi kerusakan refraktori saat terak. Masih desain kusen pintu lainnya melibatkan rakitan bentuk bata atau pracetak yang dilas atau dibaut ke cangkang baja. Ini umumnya dipasang terlebih dahulu dan garis terak dan bata dinding samping diletakkan langsung pada rakitan ini, dengan cincin dinding samping dikunci di tengah antara pintu dan lubang keran.
EAF miring konvensional umumnya menggunakan bentuk modul taphole yang disetel dengan derek pada elevasi yang tepat sebelum memasang bata pada garis terak dan dinding samping. Salah satu alternatifnya adalah meninggalkan lubang di cincin dinding samping dan kemudian ram atau gunite di sekitar pipa baja yang membentuk taphole. Pipa ini kemudian dicairkan pada pemanasan pertama. Bentuk taphole tahan api juga dapat digunakan dengan cara yang sama dengan material monolitik yang menahannya pada ketinggian dan sudut yang tepat.
Atap atau bagian delta di atas berpendingin air biasanya dipasang di area reline refraktori, dan atap yang sudah jadi menunggu tungku dibangun kembali. Dengan atap berpendingin air dan delta pracetak, refraktori yang dapat dicetak sering ditempatkan di sekeliling bentuk pracetak untuk menguncinya pada tempatnya terhadap atap berpendingin air. Untuk atap bata tahan api, diperlukan bentuk atap (umumnya beton) yang menciptakan bentuk kubah yang sesuai dengan kontur bagian dalam atap. Mandrel diatur untuk elektroda. Bentuk atap tungku listrik tiga runcing diletakkan dalam cincin konsentris terhadap cincin atap untuk dua pertiga bagian luar atap. Seringkali sebagian cincin bata diletakkan dalam pola irisan di antara elektroda. Batu bata cincin elektroda mengelilingi setiap mandrel dan ditahan di tempatnya dengan pita baja. Sebuah refraktori castable dilemparkan atau dibenturkan ke tempatnya di rongga antara cincin luar dan batu bata cincin elektroda.
Sebagian besar desain EAF menggunakan bahan perapian monolitik. Bahan ini memiliki kandungan magnesit yang tinggi dan merupakan produk self sintering yang bersifat granular. Setelah memasang blok tempat duduk taphole EBT, elemen pengaduk bawah, dan bentuk elektroda bawah dalam kasus DC EAF, peletakan perapian monolitik dimulai. Bahan perapian siap digunakan dalam tas curah besar. Sebuah derek menahan kantong curah pada posisinya di atas perapian bawah bata (lapisan pengaman) sementara kantong dibelah dan bahannya disekop ke tempatnya. Setelah dua atau tiga kantong curah berada di tungku, beberapa pekerja menggunakan sekop atau garpu pitch berulang kali menusuk bahan granular untuk menghilangkan udara dan memadatkan perapian tahan api. Saat material semakin padat, para pekerja selanjutnya memadatkannya dengan vibrator mekanis atau hanya dengan berjalan di atas perapian untuk mencapai kontur yang tepat. Kantong tambahan bahan perapian ditambahkan dan dihilangkan udaranya dan dipadatkan sampai kontur akhir tercapai (biasanya diukur dengan rantai atau formulir). Perapian baru dipasang selama pemanasan awal.
Jadwal pemanasan
On a new EAF lining with a completely new monolithic hearth, steel plates or light scrap are generally lowered by magnet into the bottom of the furnace to provide protection for the unsintered hearth material. After this cushioning scrap is in place the first bucket is charged and the arc is struck, utilizing a long arc to avoid boring down into the new monolithic bottom. The bottom is usually sintered after the first heat, although it is important to inspect the bottom and banks for any holes or erosion due to unsintered material leaving a void in the lining. Since the new EAF lining has very little moisture in it, no special precautions are required during the initial heat up, other than using a long arc to avoid eroding the bottom prior to sintering.
Lining maintenance practices
EAF linings are maintained by guniting, fettling, and patching with brick.
Guniting maintenance – Guniting maintenance consists of mixing water with a magnesite based gunning mix and spraying this mixture onto the refractory lining. Guniting is used to maintain hot spots, slag line erosion, taphole, the door breast area, or any other portion of the lining which experiences selective refractory wear. Gunning material is usually a temporary measure and there is need to re-guniting in the same place within the next several heats. Guniting maintenance, while temporary, does offer balanced life by evening out the highly selective wear pattern in the EAF lining. That is, refractory wear in AC furnaces is usually greater in the sidewall closest to the mast electrode and guniting this area maximizes overall lining performance. Most refractory guniting maintenance is done with a pressurized gun. The gun delivers dry material pneumatically to a water mixing nozzle, and the air pressure sprays the wet gunning mix onto the surface of the lining. The nozzle operator skill is a factor in the quality of the gunited patch. Guniting can be automated by using a mechanical centre-throw guniting device which shoots the guniting material in a circular pattern while suspended from a crane. This mechanical guniting is faster and easier, but often wastes material by placing it where it is not be needed.
Basic guniting mixes range from 40 % MgO to 95 % MgO in quality. High temperature operations and high power EAFs generally use higher MgO content guniting mixes, while moderate temperature operations uses lower MgO content guniting mixes.
Fettling maintenance – Fettling maintenance is the technique used to patch holes in the monolithic bottom. A rapid sintering version of the granular hearth material, or the original product, is used for fettling. The dry material is shoveled or dropped by crane wherever there is a hole in the monolithic bottom, or a mechanical chute suspended by crane delivers material onto the sloped banks of the hearth. Occasionally the magnet is used to level this patch material, which then sinters in place during the next heat.
Brick patching – After several weeks of operation, guniting maintenance becomes less efficient in maintaining the refractory lining. In such cases, the furnace is cooled to dig out anywhere from 30 % to 80 % of the sidewall and hot spots. The rubble is then removed from the furnace and new bricks in all areas of the hot spots and sidewall are installed in these areas. Often the same refractory quality and thickness are reinstalled as was used in the initial lining. Alternatively, lesser quality or thinner linings are installed during this patch since slightly less lining life is needed than the anticipated from the patch made as per the new complete lining. The brick patch is completed by guniting MgO guniting mix into all the voids and cracks in the patched brickwork.
Normally during a brick patch, the taphole is completely replaced or repaired with ramming mix or guniting material, if not replaced with brick work. In many EAF operating practices, a regular brick patching schedule is followed. This schedule can include one or two intermediate patches for every complete sidewall job. These maintenance and patching decisions are normally dictated by the severity of the operating conditions.
Miscellaneous refractory maintenance – Each EAF has unique features or conditions requiring specific refractory maintenance. Roof delta sections are to be replaced at failure or on a regular schedule. Tapholes are to be replaced or repaired when the tap time gets too short or slag carry over starts. Conventional EAF tapholes are normally replaced with a high MgO guniting mix shot around a steel pipe, while EBT tapholes are knocked out and a new assembly or one-piece tube inserted by crane from above. Bottom stirring elements and bottom electrodes each require specialized maintenance procedures which vary with design.