Otomatisasi dan Kontrol Ketebalan di Hot Strip Mill
Otomasi dan Kontrol Ketebalan di Hot Strip Mill
Efisiensi ekonomi dari proses penggulungan logam sangat berkorelasi dengan tingkat kualitas produk canai akhir. Pengerolan produk baja pipih adalah proses yang kompleks di mana kualitas produk dipengaruhi oleh berbagai faktor seperti material yang masuk, peralatan mekanik dan listrik, parameter operasi, pelumasan, dan strategi otomatisasi dan kontrol, dll. Parameter kualitas yang signifikan adalah material ketebalan, bentuk dan permukaan material, dan homogenitas distribusi tegangan. Untuk efisiensi biaya yang dioptimalkan dan untuk memaksimalkan penggunaan material, toleransi yang ketat untuk ketebalan sangat penting, untuk memungkinkan strip digulung sedekat mungkin ke ketebalan minimum yang diizinkan. Kualitas produk hanya dapat dioptimalkan secara efektif jika peralatan mekanik, elektrik, dan instrumentasi serta solusi strategi kontrol digabungkan dengan baik.
Proses hot strip mills (HSM) mengurangi dengan mengompresi pelat baja cor menerus yang memiliki penampang persegi panjang dan ketebalan dalam kisaran 250 mm hingga 350 mm ke dalam strip datar baja hingga ketebalan yang diinginkan tercapai. Beberapa HSM memiliki kemampuan untuk menghasilkan strip dengan ketebalan sekecil 1 mm. Langkah-langkah proses dalam HSM tipikal adalah (i) pemanasan ulang pelat dalam pusher atau tungku pemanas ulang jenis walking beam untuk mencapai suhu optimal, (ii) pabrik pengasaran (baik pabrik pembalik atau pabrik kontinu yang terdiri dari jumlah tegakan) untuk mencapai pengurangan ketebalan awal, (iii) penggilingan akhir yang terdiri dari 5 hingga 7 dudukan penggulung berturut-turut yang mengurangi ketebalan hingga nilai yang diinginkan, dan (iv) menggulung strip panjang dalam gulungan.
Di pabrik finishing HSM, tugas penting dilakukan oleh lengan hidrolik, yang disebut looper, ditempatkan di tengah antara dua tegakan berurutan dan yang tujuannya adalah untuk menjaga tegangan strip pada nilai konstan. Sistem mekanis ini tunduk pada dinamika yang sangat tidak stabil yang membuat masalah kontrol menjadi rumit
Pemrosesan slab menjadi strip canai panas di HSM dicapai melalui beberapa langkah proses yang kompleksitasnya melibatkan teknologi mekanis dan otomatisasi. Penggulungan panas dalam HSM tidak hanya membutuhkan solusi mekanis tetapi juga teknologi kontrol yang sesuai. Proses rolling di HSM dapat dikontrol melalui perangkat lunak standar dan arsitektur otomatisasi yang mencakup empat tingkat otomatisasi.
Sistem otomasi bukanlah satu-satunya penentu kinerja hot strip mill. Namun, untuk konfigurasi peralatan mekanik dan listrik apa pun, potensi kinerja pabrik hanya dapat dicapai dengan kontrol dan otomatisasi kinerja tinggi. Perhatian diperlukan untuk difokuskan pada throughput dan kualitas, di mana kontrol sangat penting dalam mencapai kinerja yang baik. Biasanya throughput dan kualitas berinteraksi dengan cara positif dan negatif dan interaksi ini harus dipertimbangkan dalam mendefinisikan sistem kontrol.
Keluaran – Throughput akhir yang dapat dicapai di pabrik dibatasi oleh kemampuan perangkat keras mekanik dan elektrik. Untuk mencapai throughput yang secara konsisten mendekati batas ini, diperlukan kontrol dan otomatisasi berkualitas tinggi. Pada throughput tinggi, tiga atau lebih benda kerja dapat berada di rolling mill pada berbagai tahap pemrosesan pada saat yang bersamaan. Untuk menghindari tabrakan bencana di pabrik, pelacakan yang akurat sangat penting. Sistem pelacakan menggunakan sinyal dari instrumentasi pabrik dan informasi proses (misalnya, saat sepotong digulung, sehingga panjangnya bertambah) untuk mempertahankan peta dinamis pabrik. Hal ini, tentu saja, harus kuat terhadap hilangnya instrumen pabrik individu.
Kontrol throughput melihat ke depan pada jadwal rolling dan menentukan bagian mana dari instalasi mill, furnace, roughing mill, finishing mill, atau coiler, yang dapat membatasi throughput. Proses pembatas kemudian dikendalikan untuk mencapai throughput maksimum dan bagian lain dari proses dikendalikan untuk mencocokkan throughput ini. Hal ini menghasilkan peningkatan efisiensi energi dan pengurangan keausan pada peralatan, sehingga mengurangi biaya.
Throughput dan kualitas juga berinteraksi. Ketika throughput meningkat, kontrol menjadi lebih sulit, dan untuk mempertahankan tingkat kualitas dan hasil yang diperlukan, diperlukan desain sistem kontrol yang cermat. Kontrol kualitas dan throughput juga berinteraksi secara positif. Misalnya, untuk mencapai jangkauan dan akurasi kontrol suhu yang lebih besar di pabrik akhir, semprotan pendingin antar-dudukan biasanya dipasang. Ini harus dikontrol untuk mempertahankan suhu strip di pabrik keluar, tetapi, selanjutnya, mereka dapat digunakan untuk meningkatkan kecepatan di mana benda kerja digulung di pabrik akhir, sambil mempertahankan suhu keluar target.
Kualitas – Tujuan utama dari sistem otomasi adalah untuk mengontrol peralatan pabrik sehingga gulungan gulungan memenuhi dimensi (pengukur, lebar, profil, dan kerataan) dan sifat material sesuai persyaratan spesifikasi. Ada dua aspek untuk mengontrol parameter kualitas yaitu (i) kontrol ujung kepala benda kerja saat memasang gilingan, dan (ii) kontrol peralatan pabrik untuk mempertahankan parameter kualitas yang diinginkan melalui penggulungan koil.
Ada dua mode kontrol yaitu (i) pengaturan pabrik, dan (ii) kontrol dinamis. Perbedaan mendasar dalam strategi kontrol dikenakan pada dua mode dengan ketersediaan pengukuran. Karena ulir strip di pabrik, tidak ada pengukuran parameter kualitas akhir, strip belum mencapai instrumen pengukuran, dan kontrol dicapai dengan umpan maju dan kontrol berbasis model. Setelah pabrik penuh, pengukuran langsung (beberapa) parameter kualitas akhir tersedia, dan kontrol umpan balik dinamis mulai beroperasi. Akurasi di kedua mode kontrol itu penting, dan parameter kualitas head-end yang baik menghasilkan hasil yang tinggi. Kontrol lebar di HSM juga penting. Gulungan sering dipasarkan berdasarkan panjangnya daripada beratnya, dan karenanya, setiap kelebihan lebar menunjukkan kehilangan hasil.
Bentuk strip ditentukan oleh dua parameter yang berinteraksi yaitu (i) profil, dan (ii) kerataan. Profil adalah variasi ketebalan di sepanjang lebar strip dan, untuk pemrosesan hilir diperlukan untuk dikontrol. Ada kebutuhan untuk ketebalan yang seragam baik di sepanjang panjang strip dan di sepanjang lebarnya. Kerataan adalah kemampuan strip untuk berbaring datar tanpa menerapkan kekuatan eksternal dan juga penting untuk pemrosesan hilir strip. Cacat kerataan disebabkan oleh kontrol yang buruk dari profil proporsional (profil dibagi dengan ketebalan) melalui penggilingan dan, oleh karena itu, ada interaksi antara profil dan kontrol kerataan.
Masalah kontrol kerataan juga berbeda dari profil karena kerataan penting, tidak hanya di pintu keluar pabrik, tetapi juga di celah antar-dudukan di antara dudukan pabrik finishing. Cacat kerataan yang buruk di antara dudukan dapat menyebabkan ketidakstabilan proses penggulungan di penggilingan akhir, yang mengakibatkan hilangnya kendali sepenuhnya dan hancurnya koil yang menghasilkan batu bulat. Hal ini menunjukkan hilangnya hasil dan juga mempengaruhi ketersediaan pabrik dengan menghentikan proses saat pabrik dibersihkan dari kerikil.
Selain parameter dimensi, ada parameter kualitas lain yang penting. Tujuan yang sangat penting adalah kontrol sifat mekanik dari strip jadi. Sifat mekanik ditentukan, sebagian besar, oleh struktur mikro, dan struktur mikro itu sendiri ditentukan, sampai batas tertentu, oleh regangan, dan sebagian besar oleh riwayat suhu gulungan gulungan. Dalam sistem kontrol dan otomasi saat ini, kontrol struktur mikro dicapai secara tidak langsung dengan mengontrol evolusi suhu saat strip didinginkan di meja antara pintu keluar pabrik dan coiler. Ahli metalurgi penggilingan menentukan lintasan pendinginan target, dan sistem kontrol menyesuaikan semprotan pendingin pada meja run out dan kecepatan penggilingan akhir agar sesuai dengan lintasan suhu yang diinginkan seakurat mungkin.
Struktur sistem kontrol – Tujuan pengendalian untuk HSM dinyatakan dalam parameter throughput dan kualitas produk. Namun, ruang lingkup kontrol praktis mencakup rentang aplikasi yang sangat luas mulai dari loop kontrol posisi kecepatan tinggi lokal individu dengan kecepatan operasional pada tingkat mili detik atau sub-mili detik hingga tugas penjadwalan benda kerja keseluruhan yang beroperasi setiap jam atau skala waktu yang lebih lama. Semua kontrol ini berkontribusi pada kinerja keseluruhan yang dibutuhkan dari sistem otomasi tetapi tujuannya sering dinyatakan dalam sub-tujuan yang lebih sesuai dengan skala waktu pengontrol tertentu. Misalnya, tujuan loop posisi dapat dinyatakan dalam tingkat perubahan dan overshoot dalam menanggapi perubahan posisi yang diminta, sedangkan penjadwalan keseluruhan produk melalui pabrik dapat dinyatakan dalam kecepatan memenuhi rencana produksi.
Teknologi otomasi yang diterapkan di pabrik hot strip biasanya dibagi dalam empat tingkat yang disebut sebagai tingkat 0, 1, 2, dan 3, masing-masing. Di semua tingkat otomatisasi ini yang perlu bekerja sama secara hierarkis untuk mencapai kinerja terbaik dan tingkat produktivitas tertinggi, sejumlah teknologi kontrol, model matematika dari fenomena fisik, dan algoritme pengoptimalan diimplementasikan. Struktur hierarki dari sistem otomasi kontrol yang biasanya diadopsi untuk hot strip mill ditunjukkan pada Gambar 1.
Perbedaan dalam skala waktu dan ruang lingkup kontrol individu ini tercermin dalam struktur multi-level dari sistem kontrol yang sekarang banyak digunakan pada rolling mills. Pada Gambar 1, diagram blok dari sistem multi-level seperti itu ditunjukkan. Pemisahan fungsi antara berbagai tingkat tidak tajam, dan apakah fungsi spesifik diimplementasikan di, katakanlah, tingkat 1 atau tingkat 2 dapat bervariasi dari instalasi ke instalasi dan sebagai respons terhadap pengembangan metode dan peralatan kontrol yang lebih baik.
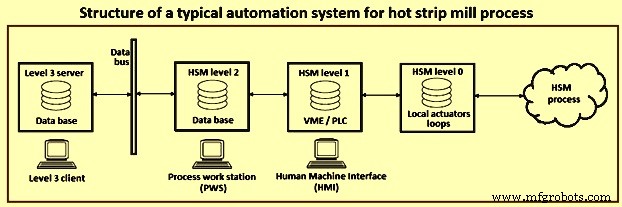
Gbr 1 Struktur sistem otomasi tipikal untuk proses hot strip mill
Tingkat 0 – Ini adalah tingkat kontrol terendah dan mencakup, misalnya, loop kontrol untuk kapsul hidraulik yang digunakan untuk memposisikan gulungan di pabrik penggulung dan untuk motor listrik utama yang menggerakkan pabrik.
Tingkat 1 – Hal ini terutama berkaitan dengan kontrol in-piece. Pada level ini, parameter kualitas seperti ketebalan strip dan suhu mulai muncul. Namun, tujuan untuk loop level-1 sering kali merupakan sub-tujuan yang dipasok oleh level 2. Misalnya, loop kontrol level 1 berfungsi untuk mengontrol ketebalan keluar dari stand perantara di pabrik finishing, dan pola ketebalan keluar ini melalui pabrik. diatur oleh level 2 untuk mencapai ketebalan keluar pabrik yang diperlukan dalam batasan mesin dan proses.
Otomatisasi level 1 berinteraksi langsung dengan perangkat level rendah (aktuator dan transduser). Loop kontrol waktu nyata dan urutan logika diimplementasikan di sini. Pengambilan sampel cepat (1 mili detik) dan daya komputasi tinggi dicapai, misalnya, melalui teknologi arsitektur VME (Versa Module European). PLC konvensional, sebaliknya, menjamin waktu sampel minimal 10 mili detik. Human–Machine Interface (HMI) menawarkan kepada operator tampilan proses secara real-time.
Tingkat 2 – Secara langsung menangani kontrol kualitas dan parameter throughput. Domain operasinya jauh lebih luas daripada level 1, dan, dalam sistem yang dikembangkan dengan baik, mencakup kontrol terintegrasi dari tungku pemanas ulang, pabrik pengasaran, pabrik finishing, dan meja run out. Ini sangat berkaitan dengan kontrol set-up pabrik dari benda kerja ke benda kerja, tetapi sering kali juga mencakup bagian dari kontrol dinamis dalam-piece. Biasanya kontrol dinamis pada level 2 berkaitan dengan kontrol terkoordinasi secara keseluruhan, katakanlah, penggilingan akhir. Loop kontrol lokal lebih sesuai untuk level 1. Sebagian besar kontrol di level 2 bersifat feed forward dan berbasis model. Performa kontrol yang baik membutuhkan model prediktif dari proses (misalnya model deformasi dan suhu) dan model dinamis dari mesin dan sensor pabrik. Sebagian besar model proses yang diperlukan untuk kontrol pabrik penggilingan yang canggih berada di sini.
Otomatisasi level 2 menyediakan fungsi dan utilitas kontrol tingkat yang lebih tinggi, seperti perhitungan penyiapan pabrik yang optimal, pembuatan laporan produksi, dan analisis statistik kualitas produk. Secara khusus model matematis dari proses teknologi digunakan untuk menghasilkan pengaturan pabrik yang tepat. Keandalan model fisik, pada kondisi kerja yang berbeda dan bahkan waktu bervariasi, dicapai dengan adaptasi diri yaitu, teknik identifikasi berdasarkan umpan balik tanaman yang meningkatkan keandalan prediksi model secara rekursif. Informasi teknologi dan arsip historis produksi disimpan ke dalam basis data (DB), sedangkan stasiun kerja proses (PWS) menawarkan antarmuka grafis ke utilitas level 2.
Tingkat 3 – Sistem otomasi level 3 diterapkan untuk menyediakan utilitas tambahan untuk pengawasan produksi tingkat atas (ini juga dikenal sebagai fungsi 'Sistem Eksekusi Manufaktur' (MES), manajemen halaman penyimpanan dan koordinasi di antara level 2 dari berbagai proses yang dimiliki ke tanaman yang sama. Sistem otomatisasi level 3 bertugas mengkoordinasikan penjadwalan produksi antara proses produksi HSM dan proses produksi unit hulu dan hilir.
Level 3 berfungsi terutama sebagai penjadwal hot strip mill. Dibutuhkan buku pesanan untuk pabrik dan mengaturnya ke dalam putaran, biasanya, 100 – 200 benda kerja yang sesuai dengan aturan penjadwalan yang dikembangkan untuk pabrik. Selain HSM itu sendiri, level 3 memperhitungkan proses hulu dan hilir serta area stok. Aturan penjadwalan yang digunakan pada dasarnya adalah model global rolling mill yang memungkinkan scheduler untuk mengatur putaran sehingga parameter kualitas yang dibutuhkan dapat dicapai dalam batasan yang diberlakukan oleh peralatan pabrik. Secara tradisional, faktor terpenting adalah evolusi profil gulungan di pabrik yang disebabkan oleh keausan dan ekspansi termal. Dari sini diperoleh jadwal `peti mati' yang berarti mulai dari yang sempit, dengan cepat membangun material yang lebih luas saat mahkota termal meningkat pada gulungan, dan secara bertahap memudar kembali menjadi menyempit saat gulungan aus.
Teknologi kontrol yang diterapkan di HSM
Penggunaan solusi kontrol dan pemodelan tingkat lanjut untuk HSM telah mengalami beberapa perkembangan di berbagai arah dalam 40-50 tahun terakhir. Ini termasuk (i) penggunaan teknik kontrol multivariabel yang telah diusulkan untuk pabrik finishing sejak tahun 1970-an dan sekarang dianggap sebagai alat konsolidasi untuk mengendalikan rolling stand generik bersama dengan looper hilir atau coiler hilir, (ii) pengembangan dari berbagai model untuk memprediksi karakteristik material sesuai dengan suhu material dan proses penggulungan dan penerapan kontrol untuk mengatur suhu koil, (iii) pengembangan teknik kontrol lanjutan yang diterapkan untuk mengkompensasi fenomena gesekan, (iv) pengembangan model dan pengontrol untuk meningkatkan kerataan dan profil material, dan (v) pengembangan teknik kontrol kemudi yang baru-baru ini diperkenalkan untuk meningkatkan tingkat produktivitas dengan mengurangi kemungkinan kejadian cobble. Gambar 2 menunjukkan tata letak tipikal hot strip mill dengan kontrol level-1.
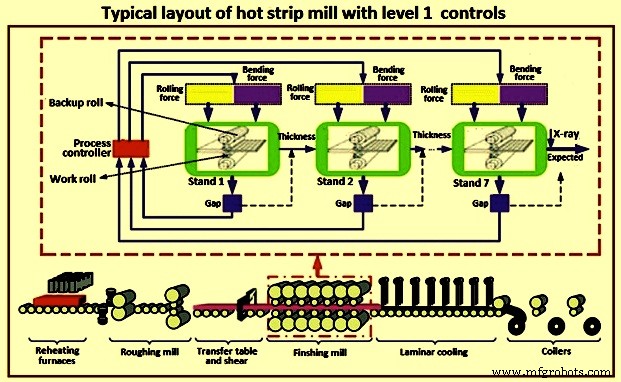
Gbr 2 Tata letak tipikal hot strip mill dengan kontrol level-1
Teknologi kontrol untuk pengaturan ketebalan
Gambar 3 menunjukkan contoh pengaturan ketebalan seperti yang diterapkan pada HSM secara normal dengan ketentuan sensor berikut. Instrumen dan sensor yang diperlukan untuk regulasi ketebalan diberikan di bawah ini.
Pengukur ketebalan dan profil – Pengukur ini didasarkan pada teknologi sinar-x dan ditujukan untuk mengukur ketebalan di garis tengah benda kerja. Pengukur jarang dipasang pada kereta yang bergerak dan dapat mengukur seluruh profil ketebalan di sepanjang lebar kumparan. Biasanya satu sistem pengukuran ketebalan / profil dipasang di ujung dudukan terakhir di pabrik.
Muat sel – Ini disediakan untuk memiliki pengukuran gaya guling yang mewakili sinyal pengukuran dasar untuk regulasi ketebalan HSM. Jika sel beban tidak tersedia maka pengukuran sinyal gaya hidraulik yang dihasilkan oleh transduser tekanan yang dipasang di silinder utama dapat digunakan sebagai ukuran alternatif.
Sel beban dalam beberapa kasus dipasang pada looper untuk mendapatkan pengukuran langsung dari tegangan strip antar stand. Juga dalam hal ini ukuran alternatif diwakili oleh sinyal gaya yang dihasilkan oleh transduser tekanan yang dipasang di silinder hidrolik yang bekerja pada looper.
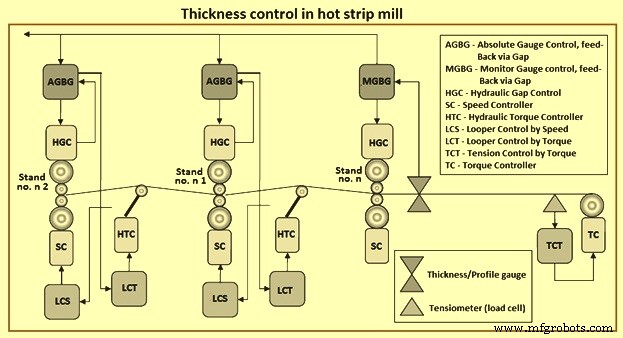
Gbr 3 Kontrol ketebalan di pabrik strip panas
Ada fitur tertentu yang membedakan antara pengontrol dasar dan pengontrol eksternal. Kontroler dasar adalah pengontrol yang bertugas mengimplementasikan referensi untuk aktuator fisik. Di sisi lain, pengontrol eksternal adalah pengontrol yang menghasilkan referensi untuk pengontrol dasar untuk mencapai target yang diinginkan. Kontrol ketebalan dicapai melalui pengontrol dasar berikut.
Kontrol celah hidrolik (HGC) – HGC dilakukan oleh pengontrol yang menerima referensi celah dan mengukur celah yang berasal dari enkoder posisi yang ditempatkan di silinder hidrolik dan menghasilkan perintah katup servo yang memang mengontrol aliran massa oli yang menghasilkan pergerakan silinder. Jelas, celah yang diukur dapat berbeda secara signifikan dari celah fisik dudukan karena peregangan elastis dudukan.
Pengontrol torsi (TC) – Kontroler torsi mengontrol torsi yang dihasilkan oleh dua gulungan. Kontroler ini menerima referensi torsi yang dihasilkan oleh kontroler 'tension control by torque (TCT)' yang bertujuan untuk menjaga agar tegangan strip coiling / uncoiling tetap konstan.
Pengontrol kecepatan (SC) – Pengontrol kecepatan bertugas mengatur kecepatan berdiri. Jelas, untuk mencapai stabilitas rolling, referensi kecepatan harus dikoordinasikan dengan operasi lain dari rolling mill.
Pengontrol torsi hidrolik (HTC) – Pengontrol torsi hidraulik bertugas mengontrol torsi yang dihasilkan oleh looper.
Kontrol pengukur otomatis
Sistem kontrol pengukur otomatis (AGC) disediakan di HSM untuk tujuan mencapai ketebalan strip panas yang diinginkan. Ini adalah sistem untuk pengaturan ketebalan. Untuk penerapannya di HSM, AGC sangat membutuhkan perolehan peregangan untuk setiap dudukan. Akuisisi peregangan tegakan sangat penting dalam kasus HSM sedangkan dalam kasus cold rolling mill itu jauh lebih penting.
Peregangan dudukan menunjukkan perilaku elastis struktur mekanik dudukan ketika gaya kompresi dihasilkan oleh silinder hidrolik utama (yaitu silinder HGC). Karakteristik ini harus diketahui terlebih dahulu untuk mengimplementasikan AGC di HSM dan untuk alasan ini urutan kontrol yang sesuai diterapkan dan dijalankan secara off-line, yaitu, sebelum bergulir, yang dikenal sebagai 'stretch acquisition sequence (SAS).
SAS diperoleh dengan menempatkan gulungan kerja dalam kontak dan secara linier memodifikasi referensi posisi untuk HGC dari nilai minimum ke nilai maksimum. Untuk setiap referensi posisi, gaya yang diukur oleh sel beban (atau dengan pengukuran gaya hidraulik HGC) dicatat untuk membangun karakteristik regangan yang serupa dengan yang digambarkan pada Gambar 4. Pencatatan pada umumnya dilakukan dua kali. Catatan pertama dibuat dengan meningkatkan referensi posisi HGC (pembacaan ke atas) dan catatan kedua dibuat dengan penurunan referensi posisi HGC (pembacaan turun).
Perbedaan antara pembacaan naik dan pembacaan bawah dihubungkan dengan histeresis yang tidak dapat diabaikan dalam perilaku elastis penyangga. Akhirnya, kurva polinomial paling cocok yang memenuhi persamaan berikut disimpan untuk melakukan tugas AGC. F dalam persamaan adalah gaya terukur.

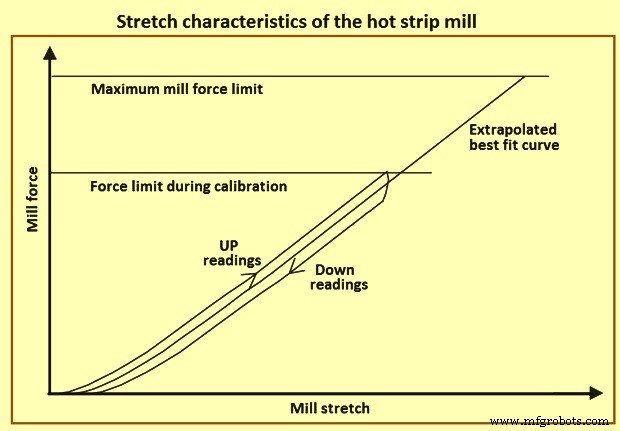
Gbr 4 Karakteristik regangan dari hot strip mill
Perlu ditunjukkan bahwa perolehan karakteristik regangan 'regangan' (F) dapat dimanfaatkan sepenuhnya selama pengerolan untuk memperoleh pengukuran tidak langsung dari ketebalan keluar benda kerja h karena persamaan h' =S + F ( peregangan) di mana h adalah ketebalan jalur keluar untuk dudukan yang dipertimbangkan, h' adalah perkiraannya yang diturunkan dari persamaan sebelumnya, S adalah celah terukur untuk dudukan yang dipertimbangkan yang berasal dari enkoder yang dipasang di silinder hidrolik, dan F adalah rol terukur kekuatan (dari sel beban atau dari tekanan HGC). Persamaan ini biasanya disebut sebagai 'persamaan pengukur meter' dan sering disederhanakan dengan memperkenalkan apa yang disebut 'Modulus Pabrik', Mm dari dudukan, yaitu konstanta elastis dudukan. Persamaan yang disederhanakan adalah h’ =S + F/Mm. Secara umum, implementasi nyata dari AGC konvensional didasarkan pada persamaan pertama, sedangkan sintesis pengontrol lanjutan berdasarkan model dapat memanfaatkan versi linier yang diwakili oleh persamaan kedua.
AGC di HSM memiliki tujuan untuk menjaga ketebalan strip yang konstan dengan bekerja pada referensi posisi untuk semua HGC dengan mengkompensasi beberapa fenomena, misalnya histeresis peregangan tegakan, variasi kekerasan material yang disebabkan oleh kemungkinan fluktuasi suhu bahan, dan sebagainya. Untuk melakukan ini, perlu diperhitungkan bahwa keberadaan looper antara satu stand dan stand berikutnya menyiratkan bahwa pengaturan yang dilakukan oleh satu stand tidak mempengaruhi regulasi yang dilakukan oleh stand yang berdekatan asalkan kontrol tegangan antar stand yang efektif. dijamin oleh looper. Fakta ini menunjukkan alasan utama mengapa arsitektur kontrol AGC untuk hot strip mill dan cold rolling mill berbeda secara signifikan.
AGC di HSM dicapai oleh beberapa pengontrol eksternal yang bekerja sama selama penggulungan. Secara khusus dua regulator bertugas mengendalikan looper. Ini dijelaskan di bawah ini.
Kontrol Looper dengan Torsi (LCT) – LCT mencapai pengaturan tegangan antar penyangga dengan bekerja pada referensi torsi yang digunakan oleh HTC. Biasanya, LCT diumpankan oleh kesalahan tegangan yang dihasilkan oleh sel beban yang dipasang pada looper atau, sebagai alternatif, dengan estimasi tegangan antar-tegangan yang diturunkan oleh gaya hidrolik looper.
Kontrol Looper berdasarkan Kecepatan (LCS) – LCS bertujuan untuk mengatur posisi sudut looper dengan bekerja pada referensi kecepatan tegakan hulu (yaitu, dengan bertindak pada referensi untuk SC yang bekerja pada tegakan hulu). Regulator ini juga disebut sebagai pengatur aliran massa.
Pengaturan ketebalan yang tepat dicapai dengan cara yang berbeda masing-masing untuk tegakan antara dan untuk tegakan akhir. Pada kenyataannya, untuk tegakan antara pengukuran ketebalan langsung tidak tersedia dan dengan demikian pengukuran ketebalan tidak langsung dicapai dari prinsip meteran pengukur seperti yang diberikan dalam dua persamaan di atas. Oleh karena itu, AGC yang ditunjukkan pada Gambar 4 terdiri dari dua regulator berikut.
Kontrol Pengukur Absolut, umpan balik melalui Celah (AGBG) – AGBG diterapkan ke semua tegakan perantara yang tidak dilengkapi dengan perangkat pengukuran ketebalan langsung dan didasarkan pada prinsip meteran pengukur dan menghasilkan trim untuk referensi celah HGC yang sesuai. Kontroler ini juga bertugas membuat beberapa kompensasi feed forward yang terhubung dengan variasi film oli untuk bantalan rol cadangan, ekspansi termal rol kerja karena kontak dengan strip dan variasi diameter rol karena keausan. .
Kontrol Monitor Gauge, feed-Back via Gap (MGBG) – MGBG bertujuan untuk menjaga ketebalan strip dari strip yang meninggalkan stand terakhir dari pabrik finishing sesuai dengan nilai target yang tepat dengan menggunakan umpan balik ketebalan yang berasal dari sinar-x yang terletak di pintu keluar pabrik. Sinyal deviasi digunakan untuk mengoreksi referensi celah untuk HGC dari semua tribun. Memang, algoritme khusus mendefinisikan cara mendistribusikan koreksi di antara semua dudukan akhir. Namun, masalah utama dalam penerapan MGBG adalah bahwa sangat perlu untuk memperhitungkan penundaan transportasi antara x-ray dan stand yang mengimplementasikan koreksi yang diperlukan.
Terakhir, seperti yang ditunjukkan pada Gambar 3, LCT dapat menerima trim dari regulator AGBG untuk mengurangi interaksi antara LCT dan AGBG.
Master Kecepatan
Kecepatan stand dan coiler perlu dikoordinasikan untuk memastikan stabilitas mill. Ini dilakukan oleh pengontrol umpan-maju yang dikenal sebagai 'Master Kecepatan'. Untuk mencegah masalah ketidakstabilan untuk proses hot rolling, satu stand dipilih sebagai 'pivot stand' dan variasi kecepatan dari pivot stand dikompensasikan dalam feed-forward melalui variasi kecepatan yang sesuai untuk stand lainnya. Untuk melakukan ini, sangat penting untuk mengetahui, setepat mungkin, 'geser maju' (FS) untuk semua tegakan, yaitu, koefisien berikut yang mewakili hubungan antara 'kecepatan sudut' motor penyangga (As) dan kecepatan jalur keluar (Vout). Hal ini diwakili oleh persamaan FS =Vout / RAs, di mana R adalah jari-jari work roll. Biasanya, koefisien FS diestimasi melalui model matematika yang sesuai yang dipasang di sistem otomatisasi level 2 bersama-sama dengan sensitivitasnya terhadap titik setel tegangan dan kecepatan strip.
Kontrol multivariabel diterapkan untuk penggilingan akhir
Selama beberapa tahun terakhir, teknologi kontrol canggih diterapkan dan sekarang dianggap mapan dalam kontrol ketebalan di pabrik finishing HSM. Tujuan utamanya adalah untuk menyediakan kerangka kerja multivariabel untuk mengintegrasikan pengontrol utama yang bertindak dalam proses HSM (lebih tepatnya, AGBG, LCT, dan LCS) hanya dalam satu pengontrol yang mengurangi kemungkinan interferensi antara berbagai tugas dan memungkinkan tidak hanya untuk meningkatkan kinerja tetapi juga untuk mengurangi kemungkinan jalan berbatu selama realisasi pengukur ultra-tipis.
Kontrol multivariabel akibatnya diterapkan di tegakan perantara untuk melakukan bersama-sama AGBG yang dicapai oleh tegakan (n-th) tertentu bersama-sama dengan LCT/LCS yang diterapkan ke looper hilir (Gbr 5). Satu lagi alasan untuk menggunakan kontrol lanjutan diwakili oleh perlunya memperkenalkan kekokohan apriori tentang kemungkinan ketidakpastian yang terkait dengan pengetahuan tentang bentangan tegakan:pada kenyataannya, adalah mungkin untuk membuktikan bahwa kehadiran ketidakpastian yang kuat dalam pengetahuan tentang modulus mill dapat menyebabkan ketidakstabilan AGBG. Di sisi lain, pengukuran peregangan dilakukan secara off-line dan tunduk pada variabilitas waktu bersama dengan keausan dudukan.
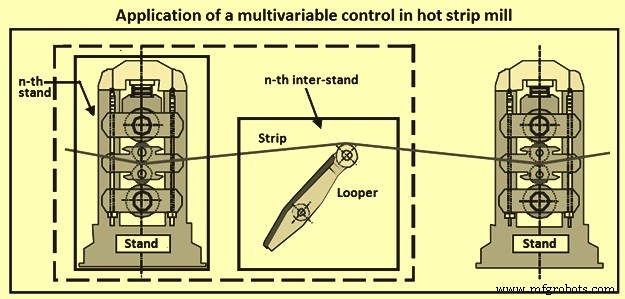
Gbr 5 Penerapan kontrol multivariabel di pabrik strip panas