Revolusi Keandalan Pusaran Air
Whirlpool Corporation berjalan di lingkaran yang sudah dikenal. Secara mekanis, bagian dalam mesin pencuci piring dan mesin cuci perusahaan ini berputar di sekitar air dan deterjen untuk membersihkan kotoran pada masakan dan pakaian Anda.
Secara finansial, ini adalah perusahaan senilai $ 13 miliar per tahun yang selama beberapa dekade telah memegang tempat bergengsi di daftar Fortune 500 (No. 79 dalam peringkat 2005).
Secara sosial, ini adalah salah satu merek paling dikenal di dunia. Dan secara sosial, ia memegang status di atas kroni peralatan konsumennya yang terkenal – General Electric, Maytag, dan Frigidaire.
Keakraban adalah salah satu aset terbesar Whirlpool, tetapi juga merupakan tantangan besar.
“Pasar sedang berubah dan dipimpin oleh perusahaan yang hampir tidak kita ketahui,” kata Larry Dunfee, manajer Manufaktur yang Berpusat pada Konsumen di situs Whirlpool di Findlay, Ohio, pabrik mesin pencuci piring terbesar di dunia.
Itu bukan putaran. Jika Anda belum pernah mendengar tentang perusahaan seperti Shian Jing, Wenling Changtian, dan Naiko Asia – produsen peralatan dapur dari China dan Taiwan – Anda akan segera mendengarnya.
“Kami terbiasa bersaing dengan produsen Amerika Utara dalam hal mesin pencuci piring. Kami mengenal mereka dan mereka mengenal kami,” kata Dunfee. “Kita semua berada di pasar Amerika Utara dengan biaya tenaga kerja tinggi. Kita semua dapat melakukan perbaikan, tetapi tidak ada yang memiliki kaki kuat di atas orang lain. Tapi sekarang, kami mulai melihat perusahaan lain datang dari negara dengan upah rendah. Mereka mulai memasarkan produk mereka di Amerika Utara dengan harga yang kompetitif. Kami melihat kemungkinan mereka menggunakan leverage yang mereka miliki dari sudut pandang biaya tenaga kerja. Itu akan menempatkan kita pada posisi yang sulit untuk bersaing kecuali kita melakukan sesuatu dengan cara yang berbeda.”
Tanggapan Whirlpool adalah revolusi. Sementara masih bercokol sebagai pemain No. 1 di sektor ini, perusahaan telah mengaduk-aduk air dan mencari cara untuk:
Revolusi telah menghasilkan peningkatan waktu kerja, produktivitas, dan kualitas. Hal ini berdampak positif pada pendapatan, profitabilitas, dan harga saham.
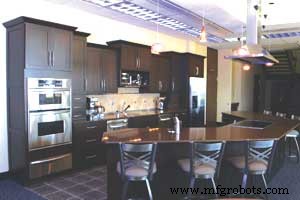
Potongan-potongan Cocok Bersama
2.000 karyawan di fasilitas Whirlpool seluas 1 juta kaki persegi di Findlay, Ohio, tidak asing dengan konsep keandalan dan pemberdayaan alat berat.
Manajemen pemeliharaan, bersama dengan para pemimpin produksi dan operasi, memperkenalkan Total Productive Manufacturing (TPM) dan Reliability-Centered Maintenance (RCM) ke pabrik pada pertengahan dan akhir 1990-an. Dan sejak awal, karyawan pabrik memainkan peran kunci dalam mengimplementasikan proyek peningkatan.
Perbedaannya, dibandingkan 2005 dengan 1995, adalah kekompakan. Alat peningkatan pusaran air sekarang cocok bersama alih-alih, dalam beberapa kasus, berjalan paralel satu sama lain. Dan, pekerja pemeliharaan dan produksi secara lebih seragam menyetujui visi bahwa “kita semua bertanggung jawab atas peralatan”.
TPM + RCM =Hasil
TPM (juga dikenal sebagai Total Productive Maintenance) adalah pendekatan berbasis tim untuk menjaga kondisi peralatan. Komponen utamanya adalah kepemilikan peralatan oleh operator, identifikasi berkelanjutan dan implementasi perbaikan, dan pengembangan pemeliharaan terencana.
Whirlpool menempatkan sekitar 10 operator area dan personel pemeliharaan di berbagai shift dalam tim TPM. Pada tahun-tahun pembentukan TPM di Whirlpool, sebuah tim dipimpin oleh seorang insinyur proses atau supervisor area. Setelah menerima instruksi tentang prinsip-prinsip TPM dan efektivitas peralatan secara keseluruhan (OEE adalah metrik yang melacak sumber kerugian operasi, termasuk ketersediaan, kinerja, dan kualitas peralatan), setiap tim mulai mengidentifikasi peluang di area fungsionalnya. Tim kemudian mencari dan menerapkan solusi untuk menghilangkan sumber kerugian yang teridentifikasi.
Hari ini, pekerja per jam berbagi peran kepemimpinan di masing-masing dari 32 tim pabrik. Dalam keberangkatan lain dari masa lalu, RCM telah menjadi bagian penting dari kurikulum TPM. Semua tim sekarang mendapatkan paparan awal untuk analisis RCM.
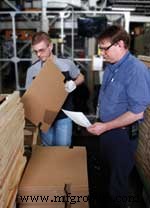
Insinyur listrik Tom Jones (kanan)
bekerja sama dengan pekerja produksi .
RCM menghubungkan proses pemikiran terstruktur dengan pengetahuan tim lintas fungsi. Selama periode tiga hingga lima hari, tujuannya adalah untuk mengembangkan strategi pemeliharaan lengkap untuk suatu proses atau peralatan.
Selama acara RCM baru-baru ini, misalnya, insinyur keandalan senior Richard Word menjabat sebagai fasilitator kelompok lintas fungsi yang beranggotakan 12 orang yang mencakup dua operator, dua ahli listrik, satu supervisor operasi, satu insinyur operasi, satu teknisi cetakan plastik, satu kualitas analis proses, satu millwright, satu teknisi pemeliharaan, satu supervisor pemeliharaan, dan satu perwakilan pemasok.
Kelompok ini dengan susah payah menganalisis komponen pers plastik vertikal (penukar panas hidrolik, katup kontrol aliran, tirai cahaya, dll.), menunjukkan dengan tepat semua mode dan efek kegagalan, dan menerapkan strategi pemeliharaan untuk setiap komponen untuk membuat pers keseluruhan lebih kuat.
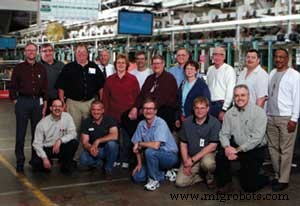
Insinyur keandalan senior Richard Word (duduk di tengah)
diapit oleh anggota tim RCM baru-baru ini.
Secara keseluruhan, mereka mengikuti proses analisis 14 langkah:
- Tinjau riwayat operasional peralatan.
- Detailkan parameter probabilitas kegagalan.
- Detail parameter untuk konsekuensi kegagalan.
- Sebutkan fungsi-fungsi utama.
- Buat daftar sub-fungsi.
- Buat daftar mode kegagalan.
- Buat daftar efek kegagalan.
- Cantumkan waktu henti.
- Sebutkan konsekuensinya.
- Menavigasi pohon keputusan.
- Tentukan tugas pemeliharaan yang tepat.
- Tentukan kebutuhan stok suku cadang.
- Tinjau kelengkapan analisis untuk waktu yang dijadwalkan.
- Lakukan pemeriksaan realitas.
“RCM adalah awal yang baik untuk tim TPM,” kata manajer pemeliharaan dan perkakas John Siefker. “Mereka benar-benar meninjau proses dan peralatannya. Ini adalah latihan belajar tentang cara kerjanya. Ketika Anda memiliki operator bersama teknisi pemeliharaan dan insinyur, mereka mulai berbicara bersama tentang berbagai komponen dan apa yang mereka lakukan. Setiap orang memberikan perspektif dunia nyata mereka. Tiba-tiba, bola lampu menyala. Ini memberikan pemahaman yang lebih baik kepada semua orang tentang proses total dan apa hasil akhirnya.”
Hingga saat ini, lebih dari 20 persen pekerja di pabrik Findlay telah berpartisipasi dalam acara RCM.
Sampai beberapa tahun yang lalu, analisis RCM berfungsi sebagian besar independen dari proyek perbaikan lainnya. Sebagian besar, mereka sekarang ada untuk memberikan perspektif dan tugas kerja bagi tim TPM.
Sebagian besar implementasi RCM melibatkan peninjauan dan pemindahan tugas pemeliharaan terperinci ke dalam sistem pemeliharaan preventif (PM). Tugas PM, yang dulunya sangat umum, sekarang sarat informasi. Setiap tugas mencakup status peralatan (berjalan, kapan saja atau turun), kata kerja tindakan (periksa, ukur, periksa), komponen spesifik (motor utama), kondisi spesifik (dapat diukur bila memungkinkan) dan referensi ke standar pemantauan kondisi ( jika tersedia atau diperlukan).
Tanggung jawab untuk menangani tugas-tugas PM ini umumnya dibagi 50/50 antara operator dan teknisi pemeliharaan.
“TPM dan RCM bukan lagi entitas yang terpisah,” kata Word. “Mereka selalu melengkapi satu sama lain, tetapi kita telah sampai pada titik di mana mereka bersatu dan bertemu.”
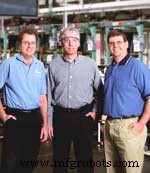
Pemimpin pabrik, termasuk manajer teknik fasilitas
Randy Statzer (kiri) , Berpusat pada Konsumen
Manajer manufaktur Larry Dunfee dan fasilitator
TPM Jim Dray, membantu mengawasi kemajuan
inisiatif keandalan.
'Kita Semua Bertanggung Jawab'
Pergeseran banyak fungsi pemeliharaan ke operator telah memungkinkan operator untuk mengambil lebih banyak "kepemilikan" dari peralatan.
“Operator awalnya mengira pekerjaan mereka adalah membuat komponen atau merakit mesin pencuci piring,” kata fasilitator TPM Jim Dray. “Itu berubah. Kami menekankan bahwa Anda bertanggung jawab atas kesehatan dan produktivitas peralatan. Ini pekerjaan Anda. Itu tugas semua orang di pabrik ini.”
Kepemilikan berarti operator melakukan tugas-tugas PM seperti membersihkan dan melumasi mesin, mengganti sabuk dan selang, dan memantau strip panas dan pita pengukur. Ini juga berarti bahwa mereka menangani banyak tugas pemeliharaan prediktif.
“Kami telah membagikan beberapa senjata inframerah genggam. Kami juga memiliki peralatan ultrasound yang dapat digunakan oleh operator penyiapan peralatan kami,” kata Dray.
Semua ini memungkinkan teknisi pemeliharaan untuk lebih fokus pada aktivitas yang benar-benar mencegah kegagalan mekanis.
“Pencegahan ada di urutan teratas daftar kami sekarang,” kata insinyur listrik Tom Jones. “Lebih baik mencegah kegagalan daripada memprediksinya.”
Sebagai contoh, perwakilan dari pemeliharaan dan rekayasa bekerja dengan pemasok peralatan dan memberi mereka ide, umpan balik, dan riwayat kinerja peralatan serupa yang saat ini digunakan. Hasil akhirnya adalah peralatan yang lebih kokoh dan lebih andal bahkan sebelum dipasang di lantai pabrik di Whirlpool.
Hubungan berbagi itu berlanjut setelah instalasi. Misalnya, perwakilan dari Battenfeld, produsen mesin cetak injeksi, bertugas di proyek RCM baru-baru ini.
“Kami masih mencari cara untuk menjangkau dan melibatkan basis pasokan kami,” kata Dunfee. “Ini adalah area peluang.”
Dengan berfokus pada pencegahan sebagai lawan untuk mendeteksi, Word mengatakan bahwa pabrik tersebut telah mampu melampaui angka 90 persen dalam waktu kerja. Selain itu, aktivitas pemeliharaan yang tidak direncanakan hanya menyumbang 13,4 persen dari perintah kerja yang terdokumentasi selama periode 30 hari terakhir.
Melangkah ke Piring
Pencegahan kegagalan dan kepemilikan peralatan terpadu juga terlihat dalam dorongan pabrik untuk mengembangkan keterampilan pemecahan masalah para pekerjanya. Ini adalah bukti lebih lanjut dari sifat terintegrasi dari alat peningkatan Whirlpool.
Anggota tim TPM, orang yang sama yang menjalani analisis RCM, menerima pelatihan tentang konsep "lean manufacturing" tambahan seperti Continuous Improvement. Proses CI menyerang area peluang dengan metodologi pemecahan masalah tujuh langkah formal.
Langkah-langkahnya antara lain:
-
Nyatakan masalah awal (umum, non-spesifik).
-
Perjelas masalahnya. (Apa cacat spesifiknya? Apa itu standar vs. aktual? Apa target untuk masalah spesifiknya?)
-
Tentukan proses saat ini yang berkontribusi pada masalah. (Tindakan atau tindakan spesifik apa yang menyebabkan kondisi tidak standar?)
-
Identifikasi akar penyebab masalah. (Penyebab sebenarnya sering tersembunyi di balik gejala yang lebih jelas.)
-
Sarankan tindakan pencegahan untuk memastikan masalah tidak terjadi lagi. (Ini adalah ide untuk menyerang akar masalahnya.)
-
Buat rencana untuk mengimplementasikan tindakan pencegahan. (Dapatkan rencana pertempuran formal untuk menyerang akar masalah.)
-
Melaksanakan penanggulangan dan melakukan tindak lanjut. (Apakah tindakan pencegahan efektif? Jika ya, terus pantau dan pastikan solusi tetap berjalan. Jika tidak, mundur dan kembangkan tindakan pencegahan baru.)
"Ini adalah pendekatan disiplin untuk pemecahan masalah yang bertentangan dengan menembak dari pinggul," kata Jones, menjelaskan bahwa metode tradisional mungkin atau mungkin tidak mengatasi akar penyebab atau mungkin fokus pada masalah "sepele banyak" sebagai lawan dari "bermakna sedikit.”
Dalam pertemuan Komite Pengarah TPM baru-baru ini, tim mempresentasikan studi kasus tentang bagaimana mereka memecahkan masalah yang terkait dengan segel konsol yang tidak pas, kinerja yang tidak konsisten pada senjata perakitan obeng, dan gangguan visibilitas lampu indikator siklus.
Latihan pemecahan masalah ini diperlukan bagi tim TPM untuk mendapatkan dan mempertahankan status sertifikasi Whirlpool (lihat bilah sisi untuk panduan sertifikasi).
Di atas CI, pabrik juga menggabungkan pemikiran ramping dalam praktik yang disebut jalan “gemba”. (Gemba adalah istilah Jepang yang secara kasar diterjemahkan menjadi "tempat di mana nilai ditambahkan.") Di sini, pemimpin pemeliharaan dan produksi, pekerja per jam dan bahkan wakil presiden divisi John Haywood berjalan-jalan di area tertentu dari fasilitas dan mengidentifikasi area limbah, aktivitas yang tidak bernilai, dan masalah ergonomis atau keselamatan.
Penghapusan limbah adalah dorongan besar. Seperti salah satu tanda di pabrik menyatakan:“Jika tidak menambah nilai, itu sia-sia! Apa yang kamu lakukan untuk mengurangi sampah? Apakah Anda, sebagai pelanggan, bersedia membayar untuk kelebihan produksi, inventaris, pergantian lama, mencari alat/suku cadang, waktu henti yang tidak direncanakan, pengerjaan ulang/memo, jarak jauh yang tidak perlu, atau menyimpan ide untuk diri sendiri?”
Salah satu metrik yang digunakan oleh pabrik untuk mencatat tingkat limbah adalah hasil proses yang kritis. CPY menyumbang banyak sumber kerugian. Ini dimulai dengan dasar tingkat produksi teoritis maksimum dan kemudian semua sumber kerugian dihitung dan dikurangkan untuk memberikan persentase kapasitas maksimum teoritis. Pada tingkat tinggi, sumber kerugian meliputi ketersediaan, kinerja, dan kualitas. Saat angka CPY meningkat, produktivitas juga meningkat.
Sebelum pematangan dan kohesi alat peningkatan Whirlpool, aset di pabrik Findlay menghasilkan 60 hingga 70 persen dari kemampuan mereka. Tolok ukur menunjukkan bahwa 85 hingga 90 persen adalah mungkin. Dalam beberapa tahun terakhir, rata-rata CPY pabrik naik menjadi 79 persen pada tahun 2003, 84 persen pada tahun 2004 dan 85 persen untuk tiga bulan pertama tahun 2005.
“Jika kami membuat keputusan yang tepat dan melakukan perawatan yang tepat, semuanya akan menyatu dan kami memiliki beberapa jaminan,” kata Jones. “Semua ini mengurangi tekanan pada saya dan orang lain.”
Evolusi Revolusi
Pabrik Findlay, Ohio, ini adalah contoh cemerlang tentang apa yang dapat terjadi ketika orang-orang yang bersemangat dan alat-alat canggih bersatu untuk mendorong peningkatan.
Whirlpool telah melihat manfaatnya. Ia tahu bahwa model ini memungkinkannya untuk mengatasi tantangan dan penantang saat ini dan masa depan dengan lebih baik. Oleh karena itu, ia bekerja untuk menyebarkan berita. Word mengunjungi situs saudara di Amerika Utara tahun ini untuk mengajarkan strategi implementasi RCM. Dray melakukan hal yang sama untuk TPM di tahun-tahun sebelumnya.
Namun, kembali ke Findlay, tidak ada yang berpuas diri.
“Ketika tujuan akhir Anda adalah peningkatan berkelanjutan, Anda tidak akan pernah sampai di sana,” kata Dray. “Ini adalah proses yang tidak pernah berakhir. Itu sulit bagi sebagian orang. Mereka berkata, 'Beri saya gol. Saya akan mencapainya. Saya selesai. Apa selanjutnya?’ Dengan ini, tidak ada akhir.”
Itu hanya berputar-putar ... seperti lingkaran.
Pedoman Sertifikasi TPM
-
Terapkan sistem untuk mengukur kemajuan tim TPM.
-
Bersihkan dan periksa.
-
Buat daftar suku cadang yang lengkap dan sediakan secara luas.
-
Identifikasi dan dokumentasikan semua titik pelumasan.
-
Hilangkan sumber masalah dan area yang tidak dapat diakses.
-
Buat jadwal pembersihan, pelumasan, dan inspeksi.
-
Terapkan inspeksi perdagangan terampil.
-
Tentukan operator, keahlian, dan tugas bersama.
-
Operator kereta api dan pekerja terampil.
-
Komunikasikan kemajuan implementasi ke seluruh tim.
-
Carilah peningkatan berkelanjutan.
-
Tinjauan sertifikasi.
-
Sertifikasi.