Di dalam Toyota MR-50
"Pengurangan Pemeliharaan 50 Persen" adalah tujuan yang tinggi, tetapi siapa yang akan bertaruh melawan pembuat mobil ini?
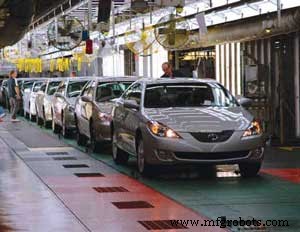
Pabrik Georgetown, Ky., membuat Camry empat pintu
sedan, sedan Avalon, dan Solara coupe dan convertible.
Bagaimana nomor perusahaan Anda? Sebagai perbandingan, berikut adalah beberapa dari Toyota:
3 - peringkatnya dalam daftar perusahaan paling dihormati di dunia, berdasarkan hasil jajak pendapat PricewaterhouseCoopers dan Financial Times baru-baru ini.
5 - peringkatnya dalam daftar perusahaan yang paling dikagumi di dunia (No. 1 di antara produsen mobil), seperti yang dipilih oleh 10.000 eksekutif dalam survei majalah Fortune.
6 - peringkatnya dalam studi Harris Interactive tentang merek-merek terbaik dunia.
10 - peringkatnya dalam survei reputasi perusahaan Harris (sekali lagi, peringkat pertama di antara pembuat mobil).
10 - persentase pertumbuhan perusahaan pada tahun 2005.
13 - persentase pangsa pasar mobil global pada tahun 2005.
13.3 - persentase pangsa pasar Amerika Serikat tahun lalu.
9,06 juta - produksi yang direncanakan untuk tahun 2006, yang akan melampaui General Motors sebagai yang teratas di industri.
Namun jika menurut Anda angka-angka tersebut mengesankan atau patut diperhatikan, pertimbangkan yang ini:50, seperti dalam 50 persen.
7 Sampah Mematikan
Setelah bertahun-tahun bekerja untuk menghilangkan pemborosan, Toyota mengidentifikasi tujuh jenis pemborosan berikut sebagai yang paling menonjol:
1) Produksi berlebih
2) Menunggu
3) Kelebihan alat angkut
4) Pemrosesan berlebihan
5) Persediaan berlebih
6) Gerakan yang tidak perlu
7) Cacat dan koreksi
Maintenance Reduction 50 Percent, atau MR-50, adalah yang terbaru dari rangkaian inisiatif Toyota yang bertujuan untuk menghilangkan pemborosan dan inefisiensi di pabrik mobilnya.
Di sebagian besar perusahaan, empat kata itu – Pengurangan Pemeliharaan 50 Persen – akan memicu kepanikan. Namun, untuk memahami MR-50, dan apa itu dan bukan, Anda harus tahu semua detailnya, dan Anda harus tahu Toyota.
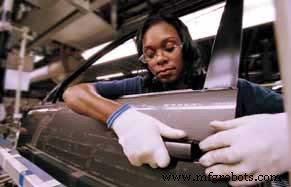
Toyota Motor Manufacturing, Kentucky (TMMK)
mempekerjakan sekitar 7.000 pekerja .
Harapan Besar
Harapan yang tinggi adalah bagian penting dari budaya perusahaan Toyota.
Teruyuki Minoura, presiden dan CEO Toyota Motor Manufacturing North America (TMMNA) dari tahun 1998 hingga 2002, pernah menyatakan, "Adalah karakteristik dasar manusia bahwa mereka mengembangkan kebijaksanaan dari berada di bawah tekanan."
Baru-baru ini, Atsushi Niimi (presiden/CEO TMMNA dari tahun 2002 hingga 2005) menuntut pengembalian yang tinggi ketika ia meluncurkan Global Body Line, sebuah inisiatif yang bertujuan untuk meningkatkan fleksibilitas lini produksi. Selama pidato utama di pameran dagang National Manufacturing Week 2004, Niimi dengan bangga melaporkan penghematan 50 persen dalam biaya untuk memasang garis bodi baru dan 50 persen penghematan ruang.
Dengan latar belakang itu, tidak mengherankan bahwa pemimpin pemeliharaan dan keandalan di pabrik Toyota di Georgetown, Ky. – lokasi perusahaan terbesar di Amerika Utara dalam hal ukuran, pekerjaan, dan output – tidak terpengaruh ketika perusahaan meminta agar pabrik mengejar pengurangan perawatan 50 persen selama beberapa tahun ke depan.
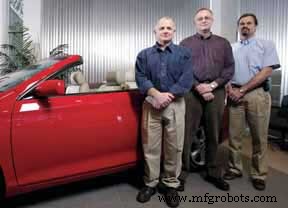
Pemimpin perawatan Toyota Ed Welch (kiri), David
Absher dan Bruce Bremer.
“MR-50 hanyalah sebuah akronim,” kata Ed Welch, manajer pemeliharaan di pabrik, yang dikenal sebagai Toyota Motor Manufacturing, Kentucky (TMMK). “Ini adalah tantangan dan masalah penekanan.” Penekanannya adalah murni Toyota.
Pertama, Pengurangan Pemeliharaan 50 Persen, bukan Pengurangan Biaya 50 Persen atau Pengurangan Karyawan 50 Persen.
“Tujuannya adalah untuk mengurangi aktivitas perawatan dan perawatan yang Anda lakukan pada mesin hingga 50 persen. Sasaran itu mencakup setiap mesin dan setiap aktivitas,” kata manajer kontrol fasilitas TMMK, David Absher.
Ini bukan tentang memotong anggaran atau personel secara sewenang-wenang. Ini adalah rencana permainan yang menyeimbangkan keinginan dan kebutuhan perusahaan saat ini dengan implikasi dan visi jangka panjang.
Hanya Fakta
Situs :Toyota Motor Manufacturing, Kentucky, Inc. (TMMK), di Georgetown, Ky. Kantor pusat Toyota Motor Manufacturing Amerika Utara terletak di dekat Erlanger, Ky.
Pekerjaan TMMK :sekitar 7.000, termasuk 710 dalam pemeliharaan.
Ukuran situs:7,5 juta kaki persegi yang tersebar di 1.300 hektar.
Produk :Camry sedan empat pintu, sedan Avalon, dan Solara coupe dan convertible; juga, mesin empat silinder dan V6, gandar, komponen kemudi, blok mesin, kepala silinder, poros engkol, poros bubungan, rakitan batang dan poros, dan dies.
Produksi :Pada tahun 2005, situs ini memproduksi 492.889 kendaraan (termasuk 351.883 Camry) dan 498.908 mesin.
Untuk diketahui :Produksi dimulai pada Juli 1988; situs tersebut membuat kendaraannya yang ke-6 juta pada bulan Juni 2005.
Bruce Bremer, manajer teknik fasilitas yang ditempatkan di kantor pusat manufaktur Toyota Amerika Utara di Erlanger, Ky., menyelaraskannya dengan prinsip-prinsip dasar Sistem Produksi Toyota.
“MR mencari apa pun di organisasi yang sia-sia atau membuat Anda sia-sia,” katanya. Welch menjadi spesifik dan lugas.
“Di mana mudanya (istilah Jepang untuk sampah)? Apakah itu lembur? Kurangi itu. Apakah biaya bahan tidak langsung Anda? Cari tahu mengapa biaya Anda lebih tinggi dari tolok ukur dan temukan cara untuk menguranginya,” katanya. “Suku cadang, waktu henti, perencanaan, dan penjadwalan – identifikasi pemborosan, lalu kejar.”
Tetapi apakah pengurangan 50 persen dalam pemeliharaan itu realistis, apalagi mungkin? Pertimbangkan aktivitas Anda sendiri dan tentukan apakah setengahnya tidak diperlukan.
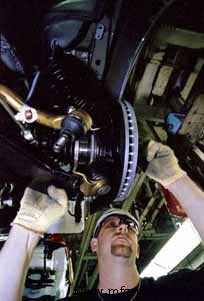
Toyota memiliki sejarah panjang inisiatif
yang ditujukan untuk mengidentifikasi limbah dan
inefisiensi. Jika suatu proses atau aktivitas
(dalam pemeliharaan, produksi, dll.) tidak
tidak menambah nilai, maka ditargetkan untuk dihilangkan.
"Ini mungkin mimpi yang mustahil, tetapi Anda tidak akan tahu kecuali Anda mencobanya," kata Absher. “Pola pikir kami adalah menjadi agresif. Kami tidak melakukan apa pun dengan sikap bahwa ini adalah yang terbaik yang bisa atau bisa kami lakukan. Jika Anda tidak memiliki tujuan yang agresif, bagaimana Anda menentukan kesuksesan? Apakah Anda mendapatkan hasil maksimal dari inisiatif? Siapa tahu? Kami menetapkan target yang sangat tinggi dan kemudian mencoba seperti orang gila untuk sampai ke sana. Jika kami tidak mencapai target, kami mencoba mencari tahu mengapa kami gagal. Apa yang menghentikan kami? Apakah ada yang bisa kita lakukan untuk mengambil langkah lain?”
Meskipun jelas apa yang dimaksud dengan M di MR-50, para pemimpin ini menjelaskan bahwa ini bukan "inisiatif pemeliharaan".
“Semua orang terlibat dengannya,” kata Absher. “Orang-orang kami membenci pemborosan – pemborosan gerak, semua dari tujuh muda mematikan (lihat bilah sisi di halaman 10). Sepertinya kami memiliki 7.000 insinyur industri yang bekerja di sini. Mereka melihat pemborosan, dan mereka tahu cara memperbaikinya.”
Menghindari S
Sebelum artikel ini berlanjut, Anda perlu memahami bahwa konsep-konsep ini dan yang berikutnya bukan untuk orang yang berkemauan lemah. Lebih penting lagi, Anda harus memahami bahwa konsep ini berlaku untuk Anda dan pabrik Anda, bukan hanya Toyota.
“Saya terkejut dengan persepsi orang-orang tentang kami,” kata Welch, menjelaskan bahwa orang luar menganggap perusahaan dan orang-orangnya sebagai Supermen manufaktur. “Kami adalah manusia yang sama yang ada di jalan. Saya tidak berpikir kami berbeda dari kebanyakan fasilitas manufaktur Amerika. Kami memiliki birokrasi yang sama, rasa frustrasi yang sama seperti kebanyakan perusahaan.”
Absher juga menghindari label elit untuk 710 orang kru pemeliharaan pabriknya.
“Saya tidak tahu apakah saya dalam posisi untuk memberikan saran karena, sejujurnya, ada banyak perusahaan di luar sana yang benar-benar bagus dalam perawatan. Mereka jauh lebih baik daripada kita,” katanya.
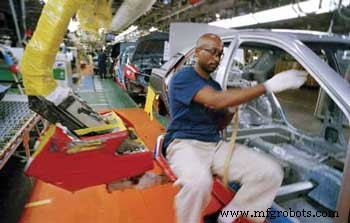
Pengurangan Pemeliharaan 50 Persen bukanlah inisiatif “pemeliharaan” .
Ini melibatkan semua karyawan pabrik.
Absher dan Bremer mengutip Eli Lilly, National Starch, Alcoa dan Harley-Davidson sebagai panutan pemeliharaan untuk berbagai alasan. Misalnya, mereka memuji Alcoa karena kemampuan perencanaan jangka panjangnya.
Yang membuat Toyota berbeda dari perusahaan lain adalah budaya dan cara departemen pemeliharaan menerapkan berbagai alat dari Sistem Produksi Toyota.
Budaya Kaizen
Sebagian besar pabrik perusahaan, bahkan mungkin milik Anda, berkembang dan berfungsi berdasarkan prinsip sejarah. “Manajer asli kami di area ini menerapkan proses itu.” “Kami memenangkan penghargaan tanaman terbaik di negara bagian kami pada tahun 1991.” “Kami selalu melakukannya seperti itu.”
Toyota tidak menyarankan pemikiran spion seperti itu.
Taiichi Ohno, mantan wakil presiden eksekutif perusahaan dan orang yang dianggap mengembangkan Sistem Produksi Toyota, pernah berkata:“Ada yang salah jika pekerja tidak melihat-lihat setiap hari, menemukan hal-hal yang membosankan atau membosankan, dan kemudian menulis ulang prosedurnya. Bahkan manual bulan lalu harusnya sudah ketinggalan zaman.”
Karyawan didorong, bahkan diharapkan, untuk mengubah keadaan dan mencari cara yang lebih baik. Sistem perbaikan terus-menerus semua tangan ini disebut kaizen. Ini berlaku untuk apa pun mulai dari kemacetan hingga nyeri leher hingga melonjaknya biaya energi dan segala sesuatu di antaranya. Kegiatan Kaizen berusaha mengidentifikasi dan menghilangkan pemborosan, sambil juga berusaha memastikan kualitas dan keamanan.
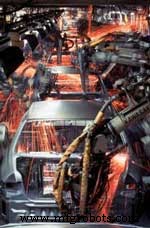
Toyota adalah pemimpin teknologi tinggi
yang mutakhir. Itu akan
berlanjut dengan adopsi
teknologi prediktif
seperti sistem pemeliharaan
cerdas (IMS).
“Kami tidak menerima situasi ini,” kata Absher. “Kami memiliki pikiran kaizen dan kami bekerja untuk perbaikan berkelanjutan. Semua orang melakukannya. Pekerjaan saya sama dengan pekerjaan plus kaizen. Ini bukan hanya pekerjaan. Ini memikirkan tentang meningkatkan apa yang sedang terjadi.”
Tidak ada sapi suci. Karyawan didorong untuk "tidak takut" dan "menantang norma." Keterampilan pemecahan masalah diasah untuk menangani tugas-tugas ini.
Berhenti Singkat
Pola pikir kaizen paling terlihat dalam acara kaizen formal. Proyek-proyek ini menyatukan tim lintas fungsi individu selama seminggu hingga tiga minggu untuk menemukan solusi bagi masalah berprioritas tinggi.
Ini adalah alat yang digunakan di banyak pabrik Amerika, bahkan mungkin milik Anda. Di TMMK di Georgetown, personel pemeliharaan memainkan peran kunci dalam kaizen yang dipimpin oleh produksi.
“Itu adalah situasi yang sempurna, cara yang bagus untuk bekerja sama, dan saya mendorong itu,” kata Welch. “Anggota pemeliharaan memiliki jari mereka pada denyut nadi masalah manufaktur pabrik. Keterampilan mereka dimanfaatkan dengan baik.”
Misalnya, pekerja produksi berusaha mengatasi masalah ergonomis di lini Solara. Selama proses perakitan untuk coupe dua pintu ini, operator yang bekerja di bawah mobil di dalam lubang harus secara manual membuka dan menutup setiap pintu berat 150 kali sehari. Prosesnya secara fisik melelahkan.
Anggota tim pemeliharaan merancang, membuat, memprogram, dan menerapkan perangkat yang sangat mendasar yang menggunakan silinder pneumatik untuk menutup pintu saat operator menekan tombol lengkap.
Akar MR-50
Menurut manajer kontrol fasilitas TMMK David Absher, MR-50 dimulai sebagai proyek lingkaran kualitas di Jepang. Kelompok lingkaran kualitas khusus anggota tim Toyota ini meninjau prosedur perawatan pada satu peralatan, kompresor. Proyek ini akhirnya mengurangi perawatan pada kompresor itu hingga 50 persen. Judul presentasi grup berikutnya adalah “MR 50 Persen.”
Para pemimpin perusahaan Toyota terkesan dengan proyek tersebut dan merasa proses pemikiran ini dapat diterapkan pada semua peralatan pabrik.
Pesan MR-50 akhirnya dikirimkan ke semua pabrik Toyota.
Untuk kru pemeliharaan di sebagian besar pabrik A.S., di sinilah proses kaizen berhenti. Sangat sedikit yang menggabungkan alat kaizen dan Sistem Produksi Toyota lainnya (Anda dapat menyebutnya lean manufacturing) secara internal untuk mengatasi pemborosan dan inefisiensi mereka sendiri. Mereka juga gagal menggunakannya untuk memecahkan masalah atau membuat strategi untuk keandalan alat berat yang optimal.
Bahwa P (produksi) di TPS (atau "manufaktur" dalam lean manufacturing) seringkali sulit untuk diabaikan. Bahkan organisasi perawatan Toyota mengalami kesulitan.
“Seperti banyak organisasi, kami berjuang keras dalam mencoba membawa pesan TPS dari produksi ke dalam pemeliharaan,” kata Welch. “Kami terjebak, dan terkadang kami masih terjebak, mencoba mengubah 'alat berbasis produksi' menjadi alat pemeliharaan."
Namun pemanfaatan komponen TPS dan strategi pengoptimalan lainnya adalah apa yang menurut para pemimpin ini akan membuat perbedaan dalam MR-50 dan dorongan untuk mengurangi aktivitas pemeliharaan hingga 50 persen.
Berikut ini adalah penjelasan tentang alat tradisional dan non-tradisional yang dimiliki oleh organisasi pemeliharaan di TMMK dan pabrik Toyota lainnya.
Kotak Alat MR
Kaizen yang berfokus pada pemeliharaan: Produksi memiliki masalah yang dapat diselesaikan dengan pemikiran tim kreatif, tetapi pemeliharaan juga demikian. Kuncinya adalah menggunakan waktu dan energi yang tersedia untuk acara kaizen yang membahas masalah yang berarti.
“Kami menggunakan data untuk semua analisis kami,” kata Bremer. “Kami memiliki indikator kinerja utama yang melihat waktu henti, penggunaan energi, keandalan, biaya, dan banyak lagi. Informasi itu akan memberi tahu Anda di mana Anda perlu memfokuskan waktu Anda.”
Misalnya, Welch dan Absher baru-baru ini mengumpulkan grup untuk acara yang terkait dengan pengurangan dan duplikasi suku cadang, keausan poros driver servo pada robot, perencanaan dan penjadwalan, respons kesalahan listrik, dan mengidentifikasi solusi CMMS global yang lebih kuat.
“Suku cadang secara tradisional sangat sulit untuk dipecahkan,” kata Welch. “Jika kita bisa menyamakan desain peralatan, kita bisa sampai pada titik di mana desain yang dibuat oleh satu orang menggunakan silinder yang sama dengan desain yang saya buat.”
Absher memuji hasil pengurangan perawatan dari peristiwa respons kesalahan di kontrol fasilitas.
“Kami menemukan bahwa, rata-rata, kami mengalami gangguan pada saluran bus di pabrik setiap sembilan bulan yang biasanya membutuhkan waktu 2,7 jam untuk memperbaikinya dan mempengaruhi produksi di area di mana gangguan itu terjadi,” katanya. “Kami melakukan sejumlah besar pemecahan masalah, dan ketika kami yakin bahwa kami telah melakukan segala yang kami bisa untuk mencegah kesalahan, kami memutuskan bahwa kami akan melakukan segala yang kami bisa untuk meminimalkan dampaknya.
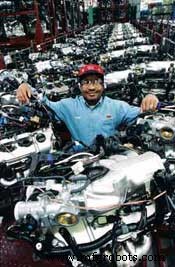
Pada tahun 2005, pabrik Georgetown
memproduksi 498.908 mesin.
“Kami mengembangkan prosedur untuk respons kesalahan saluran bus listrik dan mempraktikkannya dengan setiap tim sampai kami mendapatkan prosedur dan tim ke titik di mana mereka dapat memperbaiki kondisi kesalahan dan membuat bus kembali on line dalam 0,9 jam. Ini adalah pengurangan 66 persen.
“Kami kemudian mengembangkan kereta penghancur sistem kelistrikan. Kereta memiliki segala sesuatu di dalamnya yang kami tentukan, melalui pemeriksaan kami dan melalui proses kering, diperlukan untuk memperbaiki dan memulihkan kondisinya. Ia juga memiliki semua yang diperlukan untuk mengganti sekering di bus dan untuk memecahkan masalah dan mengoperasikan pemutus sistem distribusi.”
Sementara acara kaizen memiliki panjang yang terbatas, konsorsium memungkinkan pemeriksaan terus-menerus atas isu-isu spesifik serta pengembangan standar. Kualitas air, peralatan listrik, pengelasan dan energi adalah beberapa dari konsorsium yang aktif.
Teknologi: Toyota sedang menjajaki aplikasi dan kelayakan sistem perawatan cerdas. IMS memprediksi dan memperkirakan kinerja peralatan sehingga status "kerusakan hampir nol" dapat dicapai.
Data berasal dari dua sumber:sensor (dipasang pada mesin untuk mengumpulkan informasi) dan seluruh sistem perusahaan (termasuk data berkualitas, riwayat masa lalu, dan tren). Dengan menghubungkan data dari sumber-sumber ini (saat ini dan historis), memungkinkan untuk memprediksi kinerja di masa mendatang.
Toyota telah menjadi kontributor keuangan untuk program Center for Intelligent Maintenance Systems di University of Cincinnati dan University of Michigan. Akibatnya, TMMK berfungsi sebagai situs uji coba untuk teknologi inovatif ini. Aktivitas saat ini berpusat pada efisiensi kompresor udara, kesehatan robot, dan pemantauan bantalan.
“Itu adalah pernikahan yang bagus antara akademisi dan manufaktur,” kata Welch. “Beberapa masalah yang sedang kami tangani sekarang bukanlah masalah 10 besar kami karena akademisi tidak bergerak pada tingkat itu. Mereka meneliti lebih dalam.”
Dia mengatakan aliansi ini masih dalam tahap awal, dan kepraktisan serta efektivitas biaya akan menentukan perluasan dan penggabungan keseluruhan teknologi IMS generasi berikutnya.
“Pemeliharaan prediktif akan luar biasa, dan itu adalah sesuatu di masa depan,” katanya. “Tetapi bahkan jika kami menemukan alat prediksi, bisakah itu hemat biaya? Dua ribu robot, masing-masing tujuh sambungan:Itu adalah 14.000 sensor yang perlu kita pasang jika kita ingin melihat sambungan robot itu. Jadi, seberapa jauh Anda melangkah?”
Lima alasan: Teknik pemecahan masalah sederhana ini membantu pengguna mendapatkan akar masalah dengan cepat. Strateginya melibatkan melihat masalah apa pun dan terus bertanya "Mengapa?" dan “Apa yang menyebabkan masalah ini?” Jawaban untuk "mengapa" yang pertama sering kali akan memunculkan "mengapa" yang lain. Jawaban untuk "mengapa" kedua akan mendorong yang lain, dan seterusnya.
“Anda akan menemukan akar masalahnya, dan jika Anda bisa menghilangkannya, itu tidak akan pernah terjadi lagi,” kata Ohno seperti dikutip.
Kutipan Minoura yang sama relevannya berbunyi, “Jika Anda memasukkan semua akumulasi pengetahuan tentang akar penyebab yang Anda dapatkan dari selalu bertanya 'Mengapa? Mengapa? Mengapa?’ ke dalam peralatan Anda, Anda akan memiliki sesuatu yang tidak dapat didekati oleh orang lain.”
Lima-mengapa, analisis akar penyebab dan Pemeliharaan Berpusat Keandalan semuanya digunakan oleh TMMK untuk menentukan tingkat dan metode pemeliharaan yang tepat untuk aset pabrik tertentu. Mereka juga memungkinkan organisasi untuk mengarahkan sumber daya yang terbatas ke tempat mereka akan memiliki efek terbesar. Misalnya, fasilitas memutuskan untuk membiarkan kipas knalpot atap gagal daripada mengganti pelumas bantalan dan mengganti sabuk. Sumber daya dialihkan ke pemeliharaan chiller, upaya dengan implikasi biaya total yang lebih besar.
Heijunka: Toyota mendefinisikan ini sebagai perataan keseluruhan, dalam jadwal produksi, volume dan variasi barang yang diproduksi dalam periode waktu tertentu. Namun, heijunka mudah diterapkan pada pemeliharaan.
Fokus pada leveling. Beban kerja pemeliharaan terkenal dengan puncak dan lembahnya. Melalui perencanaan dan penjadwalan yang tepat, beban kerja dapat diratakan, mengurangi waktu lembur serta ketidakaktifan. Penciptaan pekerjaan standar dan pemecahan proyek besar menjadi yang lebih kecil adalah cara yang baik untuk mengurangi hambatan waktu dan untuk meratakan puncak.
“Daripada merencanakan PM besar sekali setiap enam bulan, bagilah menjadi peningkatan yang sangat kecil yang dapat Anda standarkan dan lakukan setiap hari atau setiap minggu,” kata Absher. “Ketika Anda melakukan itu, Anda benar-benar dapat mencapai heijunka.”
Bremer menerapkan leveling ke standar keterampilan perawatan.
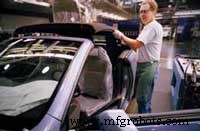
Di dalam budaya kaizen, pekerja
mengidentifikasi titik masalah, mencari tahu
akar masalahnya dan kemudian kembangkan solusi.
“Standar adalah dasarnya. Mereka menjelaskan bagaimana sesuatu harus dilakukan,” katanya. “Standar membantu seorang pekerja pemeliharaan baru dengan cepat membawa tingkat keahliannya ke tingkat kompetensi teknisi yang lebih berpengalaman. Tujuannya adalah untuk mencapai tingkat kompetensi yang tinggi secara konsisten untuk semua teknisi di organisasi Anda.”
Pembandingan: Seperti yang mungkin telah Anda perhatikan, kerendahan hati dan perbaikan terus-menerus adalah komponen budaya Toyota. Untuk itu, personel pemeliharaan di TMMK dan pabrik Toyota lainnya terus mencari praktik terbaik.
“Kami tidak berada di dekat yang sangat baik, tetapi kami sedang dalam perjalanan itu. Kami belajar sedikit dengan membandingkan fasilitas lain,” kata Welch. “Saat ini kami sedang melakukan benchmark terhadap pemasok (Tingkat 1 dan 2) kami yang upaya keandalannya, sejujurnya, lebih kuat dari kami.”
Mereka membandingkan pabrik mobil dan pabrik non-mobil. Mereka menghadiri acara-acara industri untuk mendengarkan studi kasus, bertemu rekan-rekan dan melakukan tur pabrik. Mereka mengunjungi situs Toyota lainnya di Amerika Serikat dan Jepang. Beberapa pemikiran "lima-mengapa" yang baik muncul dari memeriksa saudara-saudara mereka di Toyota.
“Mengapa tanaman itu berbeda dari milikku?”
“Mengapa angka keandalan mereka lebih tinggi dari saya?”
“Mengapa catatan keselamatan mereka lebih baik daripada milik saya?”
Ujian dilakukan untuk menutup kesenjangan.
Genchi genbutsu: Hal-hal baik datang dari berjalan di sekitar tanaman orang lain, tetapi kebaikan yang sama bisa datang dari berdiri diam di tanaman Anda sendiri.
Praktek genchi genbutsu memegang tempat yang penuh warna dalam pengetahuan Toyota. Cerita yang tak terhitung jumlahnya (nyata dan dibumbui) menceritakan tentang karyawan baru yang dikirim ke lantai toko untuk "pergi dan melihat." Orang tersebut berdiri atau duduk di satu tempat untuk seluruh shift delapan jam dan mencatat sesuatu yang penting. Lebih sering daripada tidak, orang tersebut menunjukkan limbah dan masalah yang berkaitan dengan keselamatan, aliran, kualitas, dll. Tetapi dia juga dapat mengidentifikasi masalah pemeliharaan. Mungkin mesin mengeluarkan suara yang tidak biasa dan terputus-putus. Mungkin prosedur pelumasan tidak diikuti dengan benar. Mungkin seorang teknisi perlu melakukan banyak perjalanan ke tempat tidur alat untuk menyelesaikan perintah kerja tertentu. Mungkin operator melakukan penyesuaian yang tidak tepat pada mesin.
Sila Toyoda
Pada Oktober 1935, lima tahun setelah kematian pendiri Toyota Group, Sakichi Toyoda, anggota keluarga mengumpulkan ajarannya dan menerbitkannya sebagai Ajaran Toyoda. Sila bertindak sebagai inti dari manajemen Toyota dan memandu tindakan perusahaan. Mereka termasuk:
- Berkontribusilah pada pembangunan dan kesejahteraan negara dengan bekerja sama tanpa memandang posisi, dalam menjalankan tugas dengan setia.
- Jadilah pelopor zaman melalui kreativitas tanpa akhir, rasa ingin tahu, dan upaya peningkatan.
- Bersikaplah praktis dan hindari kesembronoan.
- Bersikap baik dan murah hati; berusaha keras untuk menciptakan suasana yang hangat dan seperti di rumah.
- Hormat dan tunjukkan rasa syukur untuk hal-hal besar dan kecil dalam pikiran dan perbuatan.
Standathon delapan jam tidak diperlukan dalam praktik ini. Intinya adalah:Untuk mengetahui masalahnya, Anda perlu melihat masalahnya.
Pemeliharaan Produktif Total: Manfaat TPM didokumentasikan dengan baik. Semakin banyak aktivitas pemeliharaan yang dapat dialihkan ke operator, semakin banyak waktu yang dimiliki teknisi untuk pekerjaan yang produktif dan proaktif.
Di TMMK, operator terlibat dengan tugas mulai dari pelumasan, filtrasi, kalibrasi, dan perbaikan kecil. Di bengkel las, mereka melakukan perubahan tip pada robot las. Secara keseluruhan, penugasan bervariasi berdasarkan kompleksitas dan keamanan operasi.
“Selama bertahun-tahun, saya telah melihat lebih sedikit tugas yang disebut sebagai ‘pekerjaan terampil,'” kata Absher. “Pekerjaan terampil telah memiliki arti yang sama sekali berbeda karena kemajuan teknologi yang pesat.”
Kontrol visual: Alat ini terkait erat dengan TPM. Pada dasarnya, ini adalah metode penyampaian informasi secara visual.
Rekaman pengukur adalah contoh sederhana. Pita kode warna diterapkan pada pengukur di bagian berbentuk pai untuk menentukan tingkat yang tepat (zona hijau), tinggi (kuning) dan tinggi (merah). Operator yang baru direkrut mungkin tidak tahu apa-apa tentang mesinnya, tetapi dia dapat menarik kesimpulan dari visual itu. “Ada di merah. Lebih baik aku memberitahu seseorang.” Identifikasi potensi masalah yang lebih cepat menghasilkan lebih sedikit kerusakan dan pemadaman yang lebih singkat.
"Orang itu menelepon Anda dan mengatakan 'ini dan ini di luar standar.' Dalam 90 detik yang diperlukan untuk sampai ke sana, Anda seharusnya sudah memecahkan masalah di kepala Anda," kata Absher. “Itu menghemat waktu.”
Lingkaran kualitas: Sekelompok kecil anggota tim bertemu secara teratur untuk mengidentifikasi dan memecahkan masalah. Orang-orang ini meningkatkan kualitas, efisiensi, dan aspek lain dari performa kerja.
“Para ahli – personel produksi, pemeliharaan, dan fasilitas – menentukan cara melakukan perbaikan pada proses dan menghilangkan pemborosan dari sistem,” kata Bremer.
Angka Menjumlahkan
Item yang disebutkan hanyalah sembilan alat yang dimiliki departemen perawatan Toyota untuk mengurangi perawatan dan meningkatkan keandalan pabrik secara keseluruhan. Ada banyak penerapan pemeliharaan di alat TPS lainnya, termasuk 5-S, hoshin, jidoka, jishuken, kanban, nemawashi, poka-yoke, dan yokaten.
Intinya adalah bahwa TMMK tidak mencoba untuk mengurangi perawatan 50 persen melalui acara kaizen dua minggu atau alat tunggal lainnya. Itu bukan cara Toyota. Dengan menggunakan sejumlah besar alat yang secara tradisional dianggap bermanfaat bagi produksi dan menerjemahkan serta menerapkannya ke dalam dunia pemeliharaan, peluang untuk mewujudkan tujuan – bahkan tujuan “mimpi yang mustahil” – meningkat.
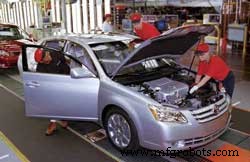
Dengan memanfaatkan alat Sistem Produksi Toyota
seperti heijunka, five-whys , kontrol visual dan
genchi genbutsu, organisasi pemeliharaan TMMK
menjadi mesin yang disempurnakan.
Peristiwa Kaizen mungkin mengurangi pemeliharaan 12 persen. TPM mungkin memasok 8 persen. Sistem perawatan cerdas mungkin mengembalikan 5 persen. 5-S . . . mungkin 4 persen. Dan seterusnya dan seterusnya. Segera, MR-50 tampaknya tidak mustahil.
Anda tidak harus menjadi Superman, atau bahkan Toyota dalam hal ini, untuk membuat terobosan, perubahan yang berarti.
Pepatah Toyota mengatakan bahwa "tidak akan ada monozukuri (membuat sesuatu) yang berhasil tanpa hito-zukuri (membuat orang)." Mengembangkan semua yang terlibat dengan pemeliharaan dan keandalan menjadi pemecah masalah yang berpikiran kaizen, dan kemudian memberi orang-orang itu waktu, alat, dan dukungan yang diperlukan untuk mengejar praktik terbaik, dapat secara radikal mengubah jumlah departemen, pabrik, dan perusahaan Anda. Reputasi yang ditingkatkan, produksi, pangsa pasar, dll., berada dalam jangkauan Anda.
Jika Anda merasa tidak dapat menerapkan ini, mulailah bertanya “Mengapa?”