OEE Kelas Dunia Menggerakkan Pabrik BMW
Ketua dewan global adalah pendukung besar pemeliharaan pabrik yang efektif.
Pekerja produksi pabrik, teknik, dan logistik berkata dengan wajah datar, "Saya tidak ingat kami mengalami downtime pada tahun 2006" dan "peralatan itu bukan batu sandungan bagi kami."
Target untuk efektivitas peralatan secara keseluruhan melebihi 90 persen (kelas dunia dianggap 85 persen). Pemimpin pabrik mengatakan bahwa nilai tersebut dapat dicapai atau telah dilampaui.
Uptime mendekati 100 persen di beberapa area penting misi.
Perhatian pemeliharaan sama-sama terfokus pada masa lalu, masa kini, dan masa depan (hingga tujuh tahun ke depan).
Pekerjaan reaktif di beberapa area terdiri dari kurang dari 5 persen dari keseluruhan beban tugas.
Mustahil? Mimpi pipa? Tujuan yang jauh? Tidak. Itulah kondisi keandalan saat ini di pabrik BMW Manufacturing Company di Spartanburg, S.C.
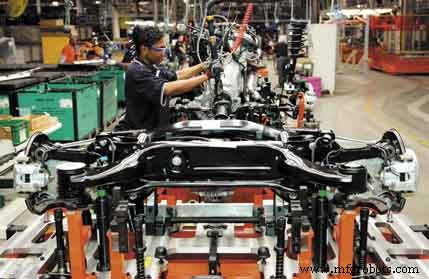
Pabrik BMW Manufacturing di Spartanburg, S.C., memiliki luas 4,73 juta kaki persegi dan mempekerjakan 4.500 pekerja.
KINERJA TINGGI
"Untuk fasilitas berusia 14 tahun, kondisinya benar-benar super," kata Duncan Seaman, manajer departemen untuk Fasilitas/Energi di lokasi ini, yang terletak tepat di Interstate 85, beberapa mil dari Bandara Internasional Greenville-Spartanburg.
BMW Manufacturing adalah komponen dari BMW Group yang berbasis di Munich, Jerman dan satu-satunya pabrik produksi mobil perusahaan yang berlokasi di Amerika Utara. Dibangun pada tahun 1993 dan dibuka untuk produksi penuh pada tahun 1994, saat ini merupakan satu-satunya sumber di dunia untuk kendaraan aktivitas olahraga X5, roadster Z4, coupe Z4, roadster M, dan coupe M. Lebih dari 2.000 kendaraan kelas atas, berteknologi canggih, dan berat kustomisasi ini dibuat di sini setiap minggu.
BMW mengutamakan performa - di jalan dan di dalam pabrik.
"Kami mengambil pendekatan yang lebih ketat untuk berbagai hal, termasuk keandalan," kata Seaman.
Phil Volino, asisten manajer yang fokus pada pemeliharaan di Toko Perakitan, mengungkapkan pemikiran itu.
"Dalam apa pun yang kami lakukan dan apa pun yang kami lacak, kami menargetkan 100 persen," katanya.
Herman Adams, spesialis perencanaan perawatan di Body Shop, menambahkan, "Orang yang membeli BMW membayar untuk teknik dan kualitas, bukan kerusakan di lantai pabrik."
Untuk mencapai keunggulan pemeliharaan dan keandalan, ini semua tentang menjadi pengemudi.
Pada tingkat makro: "Kami mencari cara yang dapat memastikan peralatan dapat melakukan apa yang kami inginkan," kata Seaman.
Dan, pada tingkat mikro: "Kami merencanakan semua pemeliharaan dan menjadwalkannya. Itu tidak menjadwalkan kami," kata Adams.
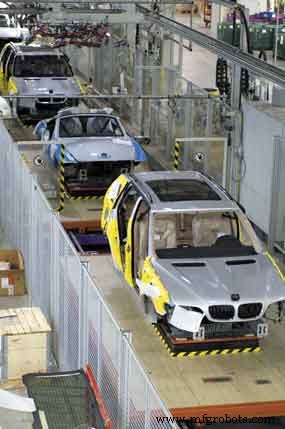
Situs ini memproduksi sport activity vehicle (SAV) X5 BMW, roadster Z4, roadster M, coupe Z4, dan coupe M.
EIN PROSIT, Y'ALL
Keandalan pabrik memiliki cita rasa yang unik di BMW Manufacturing. Ini seperti steak ayam goreng dengan sisi spaetzle.
"Pengaruh Jerman terbukti dalam penekanan kuat kami pada perencanaan. Rekan-rekan Jerman kami unggul dalam hal itu," kata manajer komunikasi Bunny Richardson. "Jika Anda menghabiskan satu hari di sini, Anda akan kagum dengan berapa kali kata 'perencanaan' digunakan atau berapa banyak orang yang memiliki perencanaan dalam jabatan atau deskripsi pekerjaan mereka. Perencanaan jelas merupakan salah satu kunci untuk memastikan keandalan. "
Nada Jerman juga berasal dari, antara lain, Dr. Norbert Reithofer, ketua dewan di BMW Group.
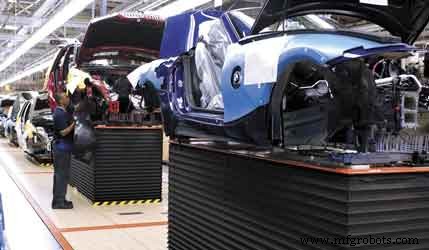
Pada akhir 2005 dan awal 2006, pabrik mengubah tata letak perakitannya dari sistem dua jalur menjadi sistem satu jalur. Semua model SAV, roadster, dan coupe kini diproduksi di lini yang sama.
Reithofer, yang diangkat menjadi ketua pada 1 September 2006, adalah presiden pabrik Spartanburg dari 1997 hingga 2000. Pada 1980-an, ia adalah perencana pemeliharaan dan direktur perencanaan pemeliharaan di pabrik BMW di Munich.
"Dr. Reithofer, mungkin karena asal-usulnya, sangat tertarik dengan perawatan ketika dia ada di sini, dan dia percaya pentingnya hal itu hari ini," kata Volino. "Itu menunjukkan bahwa kami benar-benar didukung oleh top ekstrim untuk apa yang kami coba lakukan.
"Kami telah diberkati. Kami selalu memiliki orang-orang di level dewan direksi di Jerman yang sangat selaras dengan lantai. Saya pikir BMW memahami bahwa apa yang terjadi di luar sana adalah penting."
Adams menambahkan:"Semua orang di tingkat manajemen yang lebih tinggi memahami bahwa pusat laba bukanlah kantor di suatu tempat. Ini adalah lini dan bagaimana kinerjanya."
Pengaruh Carolina Selatan/Amerika sama-sama lazim.
"Ini adalah BMW Manufacturing. Sama sekali tidak 'di seberang kolam'," kata Briggs Hamilton, manajer bagian untuk layanan lingkungan.
Karena itu, manajer dan teknisi (dikenal di sekitar lokasi sebagai rekanan layanan peralatan, atau ESA) diberi wewenang untuk membentuk struktur dan fungsi pemeliharaan agar sesuai dengan kebutuhan pabrik.
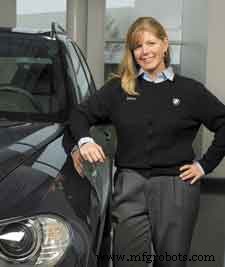
Sherry McCraw memimpin konversi pabrik yang berhasil menjadi jalur perakitan satu lini yang fleksibel.
Penataannya sangat unik. Pabrik seluas 4,7 juta kaki persegi ini dibagi menjadi empat unit:Body Shop, Assembly, Paint Shop, dan Facilities/Energy. Setiap unit melakukan perawatan yang sedikit berbeda.
Misalnya, Body Shop mengambil pendekatan terpadu. Tidak ada "departemen pemeliharaan", itu sendiri. Meskipun ada rekanan yang sangat fokus pada pemeliharaan, mereka bekerja sama sebagai tim dengan rekanan produksi dan kualitas, dan melapor ke supervisor toko.
106 Body Shop ESA bekerja shift dasar 10 jam plus menerima dua jam lembur wajib. Jika antrean berjalan dalam performa terbaik setelah Jam 10, mereka akan keluar lebih awal. ESA bukanlah spesialis. Mereka adalah teknisi multi-kerajinan yang melakukan tugas preventif, prediktif dan korektif. Karena sebagian besar jalur terdiri dari peralatan otomatisasi (ada 477 robot), pemindahan dasar melibatkan pemeliharaan prediktif dosis tinggi (termografi inframerah dan pemantauan arus motor), pekerjaan korektif terjadwal, dan perencanaan proyek. Pemeliharaan preventif (PM) pada robot terjadi setelah shift atau pada titik terjadwal lainnya saat peralatan tidak berjalan (itulah sebabnya perencanaan sangat penting).
Majelis, sementara itu, beroperasi dengan cara yang lebih tradisional. 65 ESA multi-kerajinan melapor kepada manajer teknik perakitan/pemasangan B.J. Watkins, yang berfungsi sebagai manajer pemeliharaan. Shift mirip dengan Body Shop, tetapi aktivitas PM merupakan bagian terbesar dari pekerjaan dalam shift.
"Karena kami memiliki sangat sedikit robot (sembilan), 75 persen dari PM kami dapat dilakukan saat jalur sedang berjalan," kata Volino.
Pekerjaan korektif sebagian besar dijadwalkan untuk waktu fleksibel dan giliran kerja.
Outsourcing memainkan peran staf kunci dalam pemeliharaan keempat unit pabrik. Ini memberikan fleksibilitas dan memungkinkan kelompok untuk fokus pada kompetensi inti mereka.
"Kami semua telah membuat keputusan untuk mengontrakkan persentase tertentu dari pemeliharaan kami," kata Adams. “Jika ada fluktuasi volume, kami selalu menjaga kelompok inti personel pemeliharaan kami. Outsourcing memberi kami fleksibilitas untuk memperluas dan berkontraksi. Jika kami harus menyeimbangkan sedikit, kami hanya menghilangkan beberapa kontrak. Kami tidak menghilangkan kontrak kami sendiri. orang."
Fasilitas/Energi, dengan 22 staf, termasuk 18 ESA, bergantung pada kontraktor. Mereka melakukan 30 persen dari beban kerja unit itu.
"Kami berlari sangat ramping," kata Seaman. "Kami telah melihat kompetensi inti kami dan apa yang perlu kami lakukan. Kami benar-benar perlu bergerak menuju manajemen peralatan - membuat peralatan berjalan seefisien mungkin. Ada peluang keterampilan komoditas yang dapat dengan mudah dibeli dari mitra eksternal kami - perubahan udara filter, misalnya. Itu bukan keterampilan teknis yang harus kita curahkan waktu staf kita."
Meskipun ada independensi per unit, ada juga kehadiran kolektif. Tidak ada posisi manajer pemeliharaan pabrik secara keseluruhan. Sebagai gantinya, perwakilan manajerial dari masing-masing unit membentuk Komite Pengarah Pemeliharaan Pabrik yang beranggotakan delapan orang, sebuah entitas pengawas yang memandu upaya M&R situs.
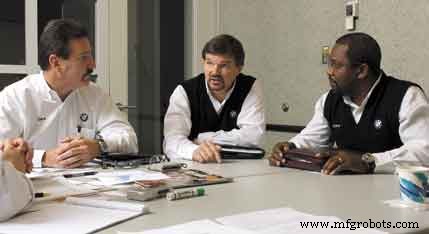
Dara Leadford (kiri), Briggs Hamilton dan Cleve Beaufort mendiskusikan kemajuan proyek-proyek teknik yang berkaitan dengan fasilitas dan energi.
MULTI-MEDIA MELIHAT MANUFAKTUR BMW
Situs Web Manufaktur BMW (www.bmwusfactory.com) berisi hampir tiga lusin video dan tayangan slide tentang berbagai subjek yang berkaitan dengan sejarah, tata letak, dan kinerja fasilitas perusahaan di Carolina Selatan.
Beberapa video catatan antara lain:
Selang waktu dari dekonstruksi, pembongkaran, dan rekonstruksi pabrik BMW selama proyek konversi satu jalurnya. Untuk mengakses video, klik tautan "Pusat Media" di bagian tengah atas halaman beranda, lalu klik tautan "Tonggak Pencapaian" di sebelah kiri halaman berikutnya. Dari sana, pilih ikon video untuk "Konversi Satu Baris dalam Perakitan".
Sebuah film dokumenter dari proyek inovatif Landfill Gas-to-Energy pabrik. Klik tautan "Komunitas" di bagian atas halaman beranda, lalu klik tautan "Lingkungan" di sebelah kiri halaman berikutnya. Pada saat itu, pilih "Gas-to-Energy" dan kemudian klik tautan video.
PERMAINAN ANGKA
BMW Manufacturing percaya pendekatan non-tradisional ini telah memainkan peran utama dalam pendakiannya ke kinerja pabrik kelas dunia dan melampauinya.
"Pemeliharaan dan keandalan tidak berada di satu departemen atau dengan satu individu," kata Adams. "Semua orang memiliki pemeliharaan, keandalan, waktu aktif, dan efektivitas peralatan secara keseluruhan. Ini adalah permainan tim."
Terbukti bahwa tim ini memenangkan pertandingan ini. Lihat efektivitas peralatan secara keseluruhan, waktu aktif, dan angka lainnya di papan skor.
"OEE dan waktu aktif adalah metrik terbesar dari tingkat pabrik atau departemen. Semua orang melihatnya," kata Adams. "OEE dan waktu aktif secara langsung berhubungan dengan jumlah mobil yang dapat kami buat untuk pelanggan kami."
Pabrik menghitung OEE sebagai Ketersediaan Peralatan kali Efisiensi Peralatan kali Tingkat Kualitas (EA x EE x QR).
Volino mengatakan EA mengacu pada uptime teknis. Ini adalah runtime yang direncanakan dikurangi downtime peralatan dibagi dengan runtime yang direncanakan.
EE mengacu pada kinerja proses dalam unit. Ini adalah unit yang diproduksi dikali waktu siklus dibagi dengan runtime yang direncanakan.
Catatan Volino:"Adalah standar untuk menggunakan kecepatan maksimum sebagai dasar dalam perhitungan ini. Dalam kasus kami, kami tidak dapat menggunakannya karena kami mendasarkan kecepatan kami pada tujuan satuan dan kemudian mengatur pabrik untuk itu. Kami memasang peralatan kami dengan rentang kecepatan dan sesuaikan dengan kondisi pasar."
QR adalah tingkat kualitas dalam hal peralatan. Jika suatu peralatan menyebabkan mobil harus dikerjakan ulang, maka ini dihitung terhadap OEE. Ini adalah total unit dikurangi unit cacat dibagi dengan total unit.
"Kami memiliki dua lapisan OEE," kata Volino. "OEE tingkat departemen mengukur seluruh lini terhadap target. OEE tingkat peralatan mengukur setiap bagian terhadap target."
Dengan latar belakang itu, Volino menyatakan bahwa Majelis memiliki tujuan OEE departemen sekitar 93 persen, termasuk sub-tujuan EA dan EE masing-masing sebesar 98,5 dan 98 persen. "Semua orang menargetkan dekat dengan angka itu," katanya. "Untuk komponen produktivitas dan kualitas OEE, kami menginginkan 100 persen."
Fasilitas/Energi memiliki target OEE sebesar 90 persen, tetapi rata-rata 93 persen untuk tahun 2006.
Memetakan waktu aktif, toko-toko melampaui 90 persen sebagai departemen dan untuk peralatan penting. Nilai keseluruhan Majelis secara teratur melebihi 95 persen dan telah setinggi 99,4 persen. Di gudang, manajer bagian logistik fisik Bill Ramsey mengutip skor uptime 99,99 dan 99,8 persen untuk peralatan penting seperti derek, mobil transfer, dan sistem. "Saya tidak ingat kami mengalami downtime pada tahun 2006," katanya.
Tanda bintang lainnya termasuk:
-
persentase kecil dari pekerjaan yang reaktif dan tidak direncanakan. "Kami bahkan tidak reaktif 5 persen," kata Volino.
-
88 persen kepatuhan rencana. "Semua pekerjaan kami direncanakan dan dijadwalkan," kata Cleve Beaufort, manajer bagian teknik pabrik di Fasilitas/Energi. "Upaya besar dilakukan untuk itu. Jadi, kami melacak seberapa baik kami benar-benar mematuhi rencana tersebut. Sasaran itu ditetapkan pada 90 persen."
Semua ini membuat Sherry McCraw, manajer perencanaan dan rekayasa perakitan, berkomentar, "Kami tidak memiliki banyak masalah peralatan. Peralatan bukanlah batu sandungan bagi kami."
Hanya fakta
Tanaman: Manufaktur BMW di Spartanburg, S.C. Pabrik yang mulai memproduksi kendaraan pada September 1994, terletak di Carolina Selatan bagian utara, sekitar 20 mil dari perbatasan Carolina Utara. Perusahaan ini merupakan bagian dari BMW Group, yang berkantor pusat di Munich, Jerman.
Ukuran tanaman: 4,73 juta kaki persegi.
Ukuran situs: 1.150 hektar.
Pekerjaan pabrik: 4.500 karyawan non-serikat, termasuk lebih dari 200 dalam fungsi pemeliharaan penuh waktu.
Produk: Kendaraan aktivitas sport (SAV) X5, roadster Z4, roadster M, coupe Z4 dan coupe M. Produk ini dibuat secara eksklusif di pabrik ini dan dikirim ke seluruh dunia.
Kapasitas: Pabrik tersebut memproduksi sekitar 2.000 unit per minggu. Produksi tahun 2006 sebanyak 104.632 unit. Itu termasuk 65.876 kendaraan X5, 29.331 kendaraan Z4 dan 9.425 total coupe.
Untuk diketahui: Pabrik memproduksi kendaraan ke-1 juta pada 28 Februari 2006. . . . Mobil pertama yang diluncurkan dari jalur perakitan adalah model 318i pada 8 September 1994.
Insinyur pabrik membantu menjaga lokasi Pabrik BMW di Spartanburg, S.C., di jalur kepemimpinan dengan menghadirkan solusi inovatif untuk kebutuhannya.
Salah satu contoh luar biasa telah menghemat jutaan dolar dalam biaya energi. Pabrik tersebut, sebagian besar, menggunakan gas sampah yang dibakar dari tempat pembuangan sampah setempat.
Awal mula ide ini berasal dari percakapan para insinyur dari unit Fasilitas/Energi dengan Program Penjangkauan Metana TPA Badan Perlindungan Lingkungan AS pada tahun 1999.
"Semakin kami menelitinya, semakin baik tampilannya," kata manajer layanan lingkungan Briggs Hamilton. "Itu mengambil sumber daya yang terbuang di tempat pembuangan sampah - mereka memiliki dua api setinggi 30 kaki yang menyala 24 jam sehari, tujuh hari seminggu. Energi itu benar-benar naik dalam asap. Kami memikirkan cara untuk mendapatkannya di sini jadi kita bisa menggunakannya."
Hasil akhirnya adalah Proyek Landfill Gas-to-Energy. Ini memiliki tiga manfaat inti:
1) Ini mengurangi jumlah gas rumah kaca berbahaya yang dilepaskan ke udara.
2) Memungkinkan BMW menggunakan sumber energi yang terbuang dengan mengubah gas metana yang dihasilkan dari Tempat Pembuangan Akhir Palmetto terdekat menjadi listrik dan panas untuk pabrik.
3) Menghemat banyak uang.
Metana adalah produk sampingan dari pembusukan sampah dan dapat memiliki efek berbahaya pada kualitas udara. Dengan mengubah metana ini menjadi energi, pabrik tersebut mengurangi emisi karbon dioksida yang setara dengan menghilangkan 61.000 mobil dari jalan raya AS setiap tahun. "Kekuatan hijau" yang dimanfaatkan oleh proyek ini juga sama dengan jumlah yang dibutuhkan untuk memanaskan 15.000 rumah per tahun.
Untuk memanfaatkan gas, pipa sepanjang 9,5 mil dibangun dari TPA Palmetto Waste Management ke BMW Manufacturing oleh Ameresco Energy Services. Proyek BMW unik karena sebagian besar proyek gas TPA lainnya menciptakan energi di TPA dan mengirimkannya melalui kabel. BMW menyalurkan gas untuk menggerakkan generator turbin di pabrik.
Ameresco menanggung biaya $12 juta untuk merancang dan membangun jalur pipa, dan menangani perkuatan dan kebutuhan infrastruktur. Sebagai imbalannya, pembuat mobil menandatangani kontrak 20 tahun untuk membeli gas dengan tarif tetap.
Sejak awal, proyek ini telah diperluas untuk memanfaatkan gas TPA untuk bahan bakar 23 pembakar oven di toko cat dan memasok panas tidak langsung ke area tersebut. BMW sekarang adalah perusahaan mobil pertama di dunia yang menggunakan energi hijau untuk bahan bakar fasilitas pengecatannya.
Penggunaan metana dari proyek gas TPA sangat mengurangi ketergantungan toko cat pada gas alam dan memanfaatkan metana yang sebelumnya belum dimanfaatkan dengan lebih baik. Saat ini, 63 persen dari total energi pembangkit tersebut berasal dari gas TPA.
Untuk mempelajari lebih lanjut tentang gas TPA dan aplikasinya, kunjungi www.epa.gov/lmop.
BAGAIMANA MEREKA MELAKUKANNYA?
Jumlahnya luar biasa - hasil akhir dari berbagai alat, aktivitas, dan inisiatif. Ini termasuk:
Fokus akar penyebab: Pabrik dan organisasi pemeliharaannya fanatik dalam mengidentifikasi sumber masalah dan mencegah kemungkinan terulangnya kembali.
Di Body Shop, jika kerusakan saluran membutuhkan waktu 15 menit atau lebih untuk diselesaikan (dalam Majelis, standarnya adalah 10 menit), pemimpin pemeliharaan dan ESA melakukan analisis akar penyebab "lima-mengapa" lengkap untuk menentukan apakah ditemukan dan memperbaiki akar masalah yang sebenarnya.
"Kami menggunakan setiap akronim yang dapat Anda pikirkan sejauh alat pemecahan masalah," kata Adams. "Kami terus mengejarnya sampai masalahnya hilang. Namun, RCA bukanlah sesuatu yang merupakan tindakan cepat. Dibutuhkan tenaga untuk melakukannya, apakah itu orang per jam Anda di lantai atau kelompok perencanaan. Jadi, Anda harus menemukan kebahagiaan itu. media 'kapan agak konyol bagi saya untuk melakukan aktivitas lima-mengapa ini?' Sebenarnya tidak perlu melakukan RCA penuh pada beberapa hal. Di beberapa daerah, kami memiliki peralatan yang sangat baru. Ketika ada masalah, itu akan memakan waktu lebih lama karena mereka masih mempelajari seluk beluknya."
Temuan dan solusi diterapkan pada semua peralatan serupa di pabrik. Grup juga memastikan untuk membagikan informasi ini dengan manajer departemen senior.
"Mereka bisa melihat apa yang dilakukan pemeliharaan dan mengapa itu penting," kata Adams. "Mereka melihat apa yang terus kami lakukan untuk memastikan bahwa proses mereka akan tetap berjalan dan berjalan. Kami ingin memberikan sorotan konstan pada kinerja dan pemeliharaan peralatan."
Pabrik, secara keseluruhan, juga menyelidiki dan menghilangkan akar penyebab masalah melalui proyek Lean Six Sigma. Saat ini, empat sabuk hitam utama, 18 sabuk hitam, dan lebih dari 20 sabuk hijau memainkan peran kunci dalam tim penyerang yang beranggotakan lima hingga tujuh orang.
"Lean Six Sigma didorong oleh data. Itulah perbedaan antara Lean Six Sigma dan langkah-langkah pemecahan masalah lainnya," kata sabuk hitam Lean Six Sigma Dara Leadford. "Melihat data dan menganalisisnya akan mengarahkan Anda ke solusi yang tepat untuk masalah tertentu."
Standarisasi dan kemitraan: BMW adalah pendukung besar standarisasi peralatan, baik di tingkat pabrik maupun global.
Misalnya, situs baru-baru ini memulai proyek untuk mengubah pengontrol logika yang dapat diprogram menjadi produk Siemens. Pabrik dan perusahaan sekarang berada dalam satu platform PLC. Untuk organisasi yang tersebar luas seperti BMW, standardisasi memungkinkan kemitraan korporat dan lintas pabrik.
"Sebagian besar peralatan sama untuk semua pabrik kami," kata Volino. "Saya dapat menelepon Afrika Selatan atau Munich dan mendapatkan jawaban atas pertanyaan yang saya miliki. Itu membuat kami lebih kuat, serta meningkatkan OEE dan waktu aktif."
Standar peralatan dan pemeliharaan (dan praktik terbaik pemeliharaan) ditempatkan secara global di Pusat Kompetensi perusahaan di Munich.
"Semua yang dipelajari pergi ke pusat sehingga dapat diakses dan digunakan oleh situs lain," kata Adams. "Wawasan dan pelajaran yang dipetik membantu kami melakukan sesuatu dengan benar pertama kali dan membangun keandalan ke dalam peralatan dan proses."
Kemitraan/pembagian ide yang cukup besar juga terjadi antara pabrik dan banyak modalnya serta pemasok MRO (pemeliharaan, perbaikan, dan operasi).
Desain untuk pemeliharaan: Pada akhir 2005 dan awal 2006, pabrik mengubah tata letak perakitannya dari sistem dua jalur menjadi sistem satu jalur. Semua model SAV, roadster, dan coupe kini diproduksi di lini yang sama. Setelah bagian konversi yang dibongkar, pabrik dapat mengambil pendekatan "bersih" untuk banyak hal, termasuk pemeliharaan. Peralatan baru disiapkan dan dipasang dengan cara yang meningkatkan aksesibilitas dan pemeliharaan.
"Kami dulu memiliki lemari kontrol di lantai dasar," kata McCraw. "Mereka selalu terhalang oleh barang-barang produksi atau mesin minuman, dan itu akan memakan waktu untuk memindahkan semuanya. Jadi, kami memindahkan lemari ke atas. Sekarang, orang-orang pemeliharaan memiliki akses yang mudah. Mereka juga dapat bekerja secara pribadi tanpa harus orang di belakang mereka mengemudikan forklift."
Pemantauan kondisi: Konversi satu baris juga memberikan kesempatan untuk memasang sensor pada banyak komponen peralatan yang sangat penting.
"Kami dulu memiliki sistem yang memantau seluruh pabrik dan membaginya menjadi beberapa zona, tetapi sekarang kami dapat melihat lokasi masalah yang tepat hingga ke masing-masing operator," kata McCraw. "Jika kami melihat penurunan atau potensi masalah, kami mengambil tindakan dan mengatasi masalah tersebut sebelum insiden terjadi."
Sensor dan antarmuka PLC dengan perangkat lunak manajemen pemeliharaan terkomputerisasi pabrik dan sistem SAP dan menyampaikan informasi status terkini. Berdasarkan data tersebut, dan perbandingan tingkat dan standar deviasi, SAP dapat menentukan perlunya tindakan pencegahan. Bergantung pada berbagai faktor, ini dapat menghasilkan perintah kerja atau pemberitahuan di CMMS, atau mengirim halaman, panggilan telepon, dan/atau email.
Peralatan pemantauan kondisi diimplementasikan atas dasar efisiensi biaya. Misalnya, Assembly telah mengeksplorasi perangkat keras pendeteksi getaran yang akan mengotomatiskan analisis getaran pada dinamometernya.
"Dari sudut pandang biaya saat ini, itu tidak layak," kata Volino. "Ini seperti 50 kali lipat biaya teknisi getaran."
Total Pemeliharaan Produktif: TPM telah membantu meningkatkan waktu kerja dan OEE dengan menciptakan pendekatan tim untuk melakukan pemeliharaan dan meningkatkan keandalan.
Kegiatan TPM bervariasi menurut unit dan area produksi. Di Body Shop, peralatan di beberapa area dimatikan selama 15 menit setiap shift sehingga pekerja produksi dapat melakukan aktivitas pembersihan dan penyesuaian. Di area Body Shop lainnya, penutupan terjadi lebih sering (15 menit setiap dua jam) atau lebih jarang (blok satu jam seminggu sekali). Di Majelis, beberapa pekerja produksi ditugaskan tugas TPM penuh waktu. Sel kaca dan sel pengisi cairan masing-masing memiliki dua orang per shift yang dikhususkan untuk tugas-tugas ini.
Pekerja produksi memang memiliki batasan TPM. Misalnya, pelumasan secara ketat merupakan tugas pemeliharaan. "Kami mencoba memastikan bahwa tangan yang masuk ke peralatan tidak berdampak negatif," kata Adams.
Itu sedikit berbeda dari Fasilitas/Energi, di mana kegiatan TPM dasar dan lanjutan dibagikan kepada kontraktor unit.
Dalam bentuk apa pun, TPM telah berupaya meningkatkan keandalan melalui peningkatan komunikasi, kepemilikan, dan daya tanggap.
Perubahan konstan: Pabrik berfungsi pada interval tujuh tahun. Setiap tujuh tahun, lini mobil baru diperkenalkan. Dengan setiap lini mobil baru datang peralatan baru untuk memproduksi kendaraan. Ini memberikan beberapa manfaat OEE.
"Peralatan tertua yang dikerjakan salah satu orang di departemen saya berusia 7 tahun," kata Adams. "Ini adalah teknologi mutakhir. Itu bagus, tapi di sisi lain, kami terus belajar dan berlatih untuk peralatan itu."
Perubahan dan churn itu memungkinkan pemeliharaan untuk secara konsisten mengevaluasi kembali proses dan aktivitas PM-nya. Jika sebuah mesin mengalami peristiwa PM delapan kali per tahun dan tidak menunjukkan masalah, frekuensi PM tahunan mungkin, mungkin, dipotong setengahnya.
"Kami tidak ingin melakukan terlalu banyak," kata Beaufort. "Kami tidak ingin melakukan terlalu sedikit. Kami ingin memastikan bahwa kami melakukan hal yang benar."
Frekuensi PM dengan cepat berubah dari berbasis waktu menjadi berbasis kondisi atau siklus.
"Itu memberdayakan Anda untuk menggunakan tenaga kerja Anda dengan lebih baik karena Anda tidak perlu dibebani dengan beban PM yang berat ketika Anda mungkin tidak perlu melakukan pekerjaan itu," kata Adams. "Anda menjalankan pemeliharaan preventif berdasarkan seberapa keras peralatan Anda bekerja."
Perencanaan jangka panjang: Semua pabrik BMW mengembangkan dokumen berbasis Excel yang memeriksa kebutuhan pemeliharaan sistem kritis selama jangka waktu tujuh tahun.
"Kami mengidentifikasi aktivitas besar dan kecil yang perlu dilakukan untuk memastikan keberlanjutan jangka panjang aset kami," kata Seaman. "Itu sangat penting untuk menyoroti masalah pemeliharaan yang membutuhkan sumber daya."
Misalnya, pabrik harus secara teratur merombak turbin gasnya karena cara penggunaannya yang sulit.
"Ini membantu kami melihat masa pakai peralatan dan kapan harus dikembalikan ke kondisi seperti baru," kata Seaman.
IT'S REV UP ATAU Mundur
Merek mobil BMW memegang status tingkat utama karena kinerja, gaya, dan keandalannya. Pabrik Spartanburg layak mendapatkan penghargaan serupa karena kemajuannya di tiga area yang sama.
"Ini adalah tanaman yang berbeda hari ini daripada lima tahun yang lalu," kata Adams. "Lima tahun lalu, kami hampir tidak menggunakan sistem CMMS kami. Kami melakukannya hari ini dengan SAP. Apakah kami melacak PM lima tahun lalu? Tidak. Kami melakukannya demi melakukan PM. Tidak ada seorang pun memantau efektivitas PM. Rata-rata waktu antara perbaikan dan respons terhadap panggilan tidak sebaik itu. Tidak ada tingkat pemeliharaan prediktif yang terjadi. Kami telah membuat langkah besar."
Tapi, semua orang setuju, pekerjaan belum selesai.
"Jika Anda tidak berubah, Anda melakukan sesuatu yang salah atau Anda tertinggal jauh," kata Ramsey. "Semuanya, termasuk ketidakmampuan untuk berubah, memengaruhi kepuasan pelanggan dan permintaan pelanggan. Jika pelanggan tidak senang, kami juga tidak senang."
McCraw merangkumnya dengan baik.
"Bar telah dinaikkan," katanya. "Pelanggan kami meningkatkannya. Sekarang, kami harus keluar dan tampil di level yang lebih tinggi itu."
Itu benar. "Mesin penggerak terbaik" berasal dari mesin dengan keandalan terbaik.
PABRIK MEMBUKAR GAS TPA DAN HEMAT HIJAU
Insinyur pabrik membantu menjaga lokasi Pabrik BMW di Spartanburg, S.C., di jalur kepemimpinan dengan menghadirkan solusi inovatif untuk kebutuhannya.
Salah satu contoh luar biasa telah menghemat jutaan dolar dalam biaya energi. Pabrik tersebut, sebagian besar, menggunakan gas sampah yang dibakar dari tempat pembuangan sampah setempat.
Asal usul ide tersebut berasal dari percakapan yang dilakukan oleh para insinyur dari unit Fasilitas/Energi dengan Program Penjangkauan Metana TPA Badan Perlindungan Lingkungan AS pada tahun 1999.
“Semakin kami menelitinya, semakin baik tampilannya,” kata manajer layanan lingkungan Briggs Hamilton. “Itu mengambil sumber daya yang terbuang di tempat pembuangan sampah – mereka memiliki dua api setinggi 30 kaki yang menyala 24 jam sehari, tujuh hari seminggu. Energi itu benar-benar naik dalam asap. Kami memikirkan cara untuk mendapatkannya di sini sehingga kami dapat menggunakannya.”
Hasil akhirnya adalah Proyek Landfill Gas-to-Energy. Ini memiliki tiga manfaat inti:
1) Mengurangi jumlah gas rumah kaca berbahaya yang dilepaskan ke udara.
2) Memungkinkan BMW untuk menggunakan sumber energi yang terbuang dengan mengubah gas metana yang dihasilkan dari TPA Palmetto terdekat menjadi listrik dan panas untuk pabrik.
3) Menghemat banyak uang.
Metana adalah produk sampingan dari pembusukan sampah dan dapat memiliki efek berbahaya pada kualitas udara. Dengan mengubah metana ini menjadi energi, pabrik tersebut mengurangi emisi karbon dioksida yang setara dengan menghilangkan 61.000 mobil dari jalan raya AS setiap tahun. “Kekuatan hijau” yang dimanfaatkan oleh proyek ini juga sama dengan jumlah yang dibutuhkan untuk memanaskan 15.000 rumah per tahun.
Untuk memanfaatkan gas, pipa sepanjang 9,5 mil dibangun dari TPA Palmetto Waste Management ke BMW Manufacturing oleh Ameresco Energy Services. Proyek BMW unik karena sebagian besar proyek gas TPA lainnya menciptakan energi di TPA dan mengirimkannya melalui kabel. BMW menyalurkan gas untuk menggerakkan generator turbin di pabrik.
Ameresco menanggung biaya $12 juta untuk merancang dan membangun jalur pipa, dan menangani perkuatan dan kebutuhan infrastruktur. Sebagai imbalannya, pembuat mobil menandatangani kontrak 20 tahun untuk membeli gas dengan tarif tetap.
Sejak awal, proyek ini telah diperluas untuk memanfaatkan gas TPA untuk bahan bakar 23 pembakar oven di toko cat dan memasok panas tidak langsung ke area tersebut. BMW sekarang adalah perusahaan mobil pertama di dunia yang menggunakan energi hijau untuk bahan bakar fasilitas pengecatannya.
Penggunaan metana dari proyek gas TPA sangat mengurangi ketergantungan toko cat pada gas alam dan memanfaatkan metana yang sebelumnya belum dimanfaatkan dengan lebih baik. Saat ini, 63 persen dari total energi pembangkit tersebut berasal dari gas TPA.
Untuk mempelajari lebih lanjut tentang gas TPA dan aplikasinya, kunjungi www.epa.gov/lmop.