Pabrik Harley-Davidson Unggul dengan Pemeliharaan Proaktif dan Prediktif
"Ambil motormu. Pergilah ke jalan raya. Cari petualangan dan apa pun yang menghadang kita ..." - lirik dari lagu klasik Steppenwolf tahun 1968 "Born to Be Wild"
Citra Harley-Davidson adalah kebalikan dari yang dapat diprediksi. Tidak ada jadwal. Tidak ada rencana. Tidak ada batasan. Tidak peduli. Yang tidak diketahui terletak di tikungan. Cukup ikat helm, nyalakan mesin, dan kendarai.
Ini adalah citra mengendarai sepeda motor - gaya hidup - yang dianut oleh pelanggan dan diagungkan dalam musik, film, iklan, dan acara TV. Harley-Davidson adalah jalan keluar dari dunia lama yang sama, jam 8-ke-5, lapor-ke-bos Anda.
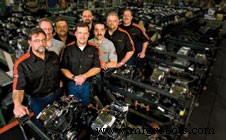
Namun, citra manufaktur Harley-Davidson adalah tentang prediktabilitas. Tidak ada kejutan. Tidak ada kemacetan. Tidak ada kerusakan. Tidak ada waktu henti. Apa yang ada di depan diketahui. Nyalakan saja peralatan produksi dan buat.
Ini adalah citra keandalan - gaya hidup - yang dibangun dengan pemeliharaan dan dianut oleh karyawan dalam produksi, operasi, keuangan, serta manajemen pabrik dan perusahaan. Prediktabilitas yang didukung oleh keandalan adalah jalan menuju peningkatan output, produktivitas, efisiensi, dan profitabilitas di perusahaan industri Amerika yang sesungguhnya ini.
Mungkin tidak ada pabrik Harley-Davidson yang mewujudkan semangat dan visi ini seperti pabrik operasi powertrain yang terletak di pinggiran Milwaukee, Menomonee Falls.
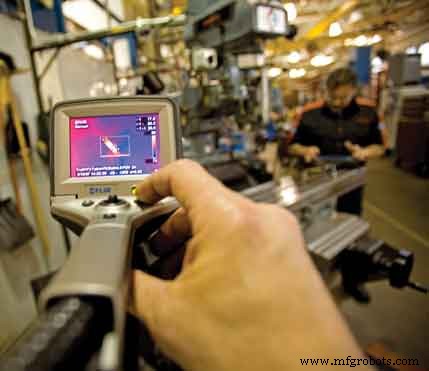
Pabrik Harley-Davidson di Menomonee Falls, Wis., sering menggunakan beberapa alat perawatan prediktif untuk mengatasi masalah permesinan.
"Di banyak tempat, pemeliharaan reaktif dan pemadaman kebakaran dirayakan," kata Larry Angel, manajer pemeliharaan pabrik. "Dari sudut pandang Harley, jika Anda benar-benar ingin mencapai home run, itu adalah proses latar belakang Anda - pekerjaan peningkatan - yang membuat perbedaan. Ini tidak semenarik itu. Ini tidak terlihat oleh orang lain untuk dilihat. Tapi, inilah yang menyelamatkan Anda. waktu, tenaga, dan uang. Ini dapat diprediksi. Kami percaya akan hal itu, dan kami menghargai orang-orang kami karena melakukan hal yang benar yang membantu kami mencapai tujuan itu."
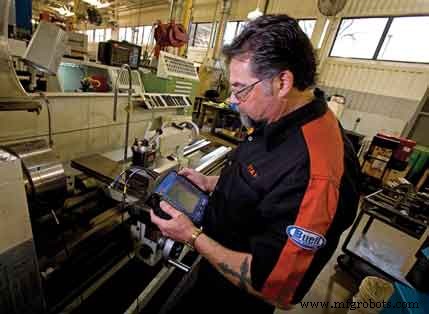
Tukang perbaikan mesin Gordy Pollari adalah ahli analisis getaran di pabrik.
Organisasi pemeliharaan pabrik adalah pendukung kuat dari:
Dengan menggunakan "alat-alat" ini secara efektif, kata insinyur keandalan pemeliharaan utama Dana Fluet, "kami bergerak ke arah menjadi 100 persen proaktif dan tidak melakukan pemadaman kebakaran... Begitulah cara kami menjalankan bisnis di Harley-Davidson."
Hanya Fakta
Tanaman: Harley-Davidson Motor Company di Menomonee Falls, Wis. Pabrik pengoperasian powertrain Pilgrim Road dibangun pada tahun 1997.
Ukuran situs: 480.000 kaki persegi.
Pekerjaan pabrik: Sekitar 1.000 karyawan, termasuk 148 pekerja pemeliharaan per jam dan 10 pekerja pemeliharaan gaji. Produksi berjalan 24 jam per hari, lima hari per minggu. Pekerja per jam diwakili oleh serikat pekerja United Steel dan International Association of Machinists Lodge 78.
Produk: Mesin dan komponen transmisi untuk sepeda motor H-D.
Produksi: Pengiriman siklus perusahaan secara keseluruhan pada tahun 2006 adalah 349.196 (vs. 329.017 pada tahun 2005); Pengiriman siklus merek Buell adalah 12.460 pada tahun 2006 (vs. 11.166 pada tahun 2005).
Untuk diketahui: Perusahaan ini memiliki $6.186 milyar dalam penjualan dan $1.043 milyar laba pada tahun 2006. . . . . Itu berada di peringkat No. 369 dalam daftar Fortune 500 2007, naik 11 peringkat dari tahun lalu. . . . Selain Menomonee Falls, H-D memiliki fasilitas di lima kota Wisconsin tambahan (Milwaukee, Wauwatosa [2], Tomahawk, Franklin dan East Troy), dan di York, Pa.; Kota Kansas, Mo.; dan Lincoln, Ala.
KEKUATAN PDM
Pabrik yang memproduksi mesin dan komponen untuk tiga variasi powertrain yang dipasang pada sepeda motor merek Harley-Davidson, bukanlah pendatang baru dalam strategi perawatan progresif.
"Kami selalu memiliki departemen pemeliharaan yang sangat agresif," kata Dean Bodoh, ahli listrik dengan pengalaman 19 tahun di lokasi.
Namun kecepatan, kemajuan, dan kecakapan telah meningkat pesat sejak perekrutan Angel pada tahun 2001 dan Fluet pada tahun 2003.
Angel dan Fluet mengubah mentalitas outsourcing kegiatan pemeliharaan prediktif (PdM), alih-alih menempatkan tanggung jawab dan peluang pada keahlian departemen.
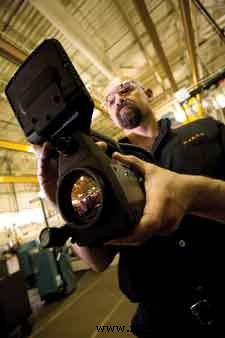
Dekan Bodoh Ahli Listrik terlatih dan bersertifikat dalam termografi inframerah.
"Banyak perusahaan mengalihdayakan hal-hal ini ketika mereka menguji atau mencoba-coba PdM," kata Angel. "Kami menemukan bahwa dengan memanfaatkan orang-orang kami sendiri, kami bisa lebih efektif dalam memantau dan tetap berada di atas masalah peralatan. Selain itu, kami akan memiliki kedekatan dengan beralih dari waktu penyelesaian satu minggu atau dua minggu untuk hasil dan laporan dari kontraktor luar."
Fluet berasal dari industri tenaga nuklir dengan pengetahuan tingkat lanjut tentang teknologi PdM. "Dana membuka pintu bagi kami dalam hal bagaimana menerapkan sepenuhnya teknologi ini dan memanfaatkan temuannya," kata Angel.
Tujuannya adalah untuk menyediakan layanan teknis yang tidak mengganggu dan gangguan sesedikit mungkin pada proses produksi.
Pekerjaan para pemimpin pemeliharaan ini mencapai puncaknya dalam pembentukan tim super PdM pada awal tahun 2006.
"Kami memiliki orang yang tepat di posisi yang tepat," kata Fluet. "Ini adalah pekerjaan penuh waktu mereka. Kami tidak mengejar setengah jalan. Orang-orang ini memberikan keterampilan dan konsistensi untuk upaya ini. Intinya adalah penghematan waktu, keahlian internal, penghematan biaya keseluruhan, dan peningkatan waktu kerja alat berat."
Tim prediksi meliputi:
-
Bodoh, yang bertanggung jawab atas termografi inframerah.
-
Randy Czeszynski, seorang pembuat gilingan yang berfokus pada pelumasan mesin dan analisis oli.
-
Gordy Pollari, seorang tukang reparasi mesin yang fokus pada analisis getaran.
Mereka bergabung dengan tukang pipa Eric Radke dan tukang reparasi mesin Steve Cummins, yang menggabungkan aplikasi PdM dalam peran mereka sebagai pemimpin aktivitas Perbaikan Berkelanjutan terkait pemeliharaan.
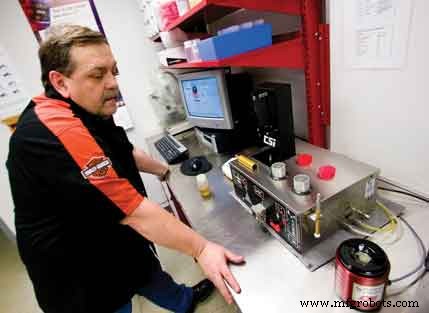
Randy Czeszynski, seorang ahli pabrik dan analis pelumasan bersertifikat, mengelola program analisis oli.
"Orang-orang ini bersemangat tentang apa yang mereka lakukan," kata Fluet. "Kami tidak keluar dan memilih orang-orang ini untuk slot ini. Mereka secara sukarela. Mereka sangat tertarik untuk meningkatkan apa yang dapat dilakukan pemeliharaan untuk pabrik ini."
Setiap pemimpin teknologi PdM menjalani pelatihan ekstensif untuk menjadi mahir dalam alat fokusnya. Bodoh mengikuti kelas termografi melalui Sistem FLIR dan memperoleh sertifikasi Level I. Czeszynski mengambil kelas melalui Noria Corporation dan Computational Systems Inc., dan sekarang menjadi analis pelumasan bersertifikat. Pollari telah mengambil kursus melalui CSI dan Technical Associates, dan sedang mengejar sertifikat analisis getaran Level I.
Tim prediksi bekerja pada shift pertama dan tinggal di area kantor pusat.
"Ini memaksimalkan komunikasi," kata Fluet. "Dengan berbicara satu sama lain tentang apa yang mereka lihat dan temukan dengan setiap teknologi, setiap orang dapat belajar. Sinergi tim berkembang. Kolaborasi orang-orang terampil ini dan alat mereka membantu mengonfirmasi dan memverifikasi temuan."
MENGHEMAT MINYAK DAN UANG
Pada tahun pertama tim prediksi, program pelumasan mesin/analisis oli memberikan beberapa keuntungan terbesar dengan menulis ulang aturan. Departemen tersebut mengubah filosofi pemeliharaan preventif (PM) terkait dengan pelumasan.
"Proses lama pemeliharaan preventif dan penulisan PM pada dasarnya mengikuti manual lama," kata Czeszynski, seorang karyawan Harley-Davidson selama 17 tahun. "Dalam enam bulan, Anda membuang minyak ini. Dalam setahun, Anda membuang ini. Dalam dua tahun, Anda membuang ini. Dengan memasukkan program analisis minyak, kami telah berpindah dari sistem berbasis waktu ke sistem berbasis kondisi. PM-PM itu telah ditulis ulang; cara-cara lama telah hilang. Kami melakukan semuanya sesuai kebutuhan. Itu adalah buah yang tidak mudah, dan itu menghemat banyak uang kami."
Sedemikian rupa sehingga pengurangan konsumsi minyak saja dalam enam bulan pertama program dibayar untuk laboratorium analisis minyak departemen yang rumit (ini satu-satunya lab dari jenisnya di dalam Harley-Davidson).
"Kami belum melacak penghematan biaya terkait ketersediaan, pembuangan limbah, tenaga kerja," kata Fluet. "Kami juga mencoba mendokumentasikan penghematan ini."
Program ini juga telah menulis ulang definisi "apa itu minyak bersih?"
"Mungkin serangan paling agresif sejak kami melakukan lab adalah memulai program untuk minyak yang masuk," kata Fluet. "Awalnya, kami tidak menyadari betapa terkontaminasinya beberapa minyak yang masuk — tidak sampai kami memiliki kemampuan untuk menguji sendiri minyak yang masuk."
Ada "bersih", lalu ada bersih.
Fluet awalnya berfokus pada minyak yang disimpan dalam tangki curah. Sistem penyaringan yang rumit telah menurunkan tingkat kontaminasi dalam oli baru menjadi 3 mikron yang sangat kecil.
"Saat kami mengirimkan minyak ke wadah transportasi dan stasiun minyak kami, kami sekarang tahu bahwa itu berada pada tingkat kebersihan yang diharapkan di stasiun pelumasan," kata Fluet.
Czeszynski menindaklanjutinya dengan mengajari operator cara melumasi mesin mereka dengan benar sebagai bagian dari program Pemeliharaan Produktif Total pabrik. Sebagai alat instruksi, Fluet membuat lembar instruksi warna-warni yang menggunakan foto dan grafik untuk mengidentifikasi titik pelumasan yang benar dan jenis pelumas yang tepat untuk setiap mesin.
Program oli/pelumas saat ini bekerja untuk memperluas analisis serpihan keausan, sehingga, seperti yang dikatakan Czeszynski, "kami dapat memprediksi tiga atau empat bulan sebelumnya bahwa alat berat menunjukkan tanda-tanda awal degradasi atau kegagalan."
MENGAMBAR JALAN UNIK MENUJU KEANDALAN TANAMAN
Meskipun Harley-Davidson percaya pada kekuatan prediktif, pemeliharaan proaktif, Harley-Davidson sengaja memutuskan bahwa pabriknya tidak mengambil pendekatan yang tidak tepat untuk pemeliharaan dan keandalan.
Banyak fasilitas produksinya telah berinvestasi dalam teknologi prediktif dan mengeksplorasi manfaat tim PdM dan sistem pemeliharaan cerdas nirkabel, tetapi sebagian besar, setiap pabrik merencanakan jalannya sendiri di area ini.
"Kami memiliki otonomi untuk membangun program keandalan yang sesuai dengan kebutuhan situs ini," Larry Angel, manajer pemeliharaan di pabrik produksi mesin dan komponen perusahaan di Menomonee Falls, Wis. "Situs Harley-Davidson lainnya dapat melakukan hal yang sama untuk menyesuaikan dengan kebutuhan mereka. kebutuhan. Situs yang berbeda memiliki lingkungan atau proses atau kebutuhan yang berbeda. Itu salah satu hal yang membuat Harley-Davidson begitu unik dan istimewa."
TERLIHAT LEBIH JAUH
Penghematan dan penghematan besar juga terjadi setelah program termografi diterapkan dan prosesnya diperiksa ulang.
Kontraktor luar sebelumnya melakukan pemindaian inframerah semi-tahunan dari sistem switchgear yang menyediakan daya untuk mesin produksi. Di sela-sela pemindaian, sebagai bagian dari jadwal PM, teknisi listrik pabrik membuka kabinet listrik dan memverifikasi pengaturan torsi pada kontaktor. Proses terakhir membutuhkan shutdown mesin yang terikat pada kabinet tersebut.
Semua itu telah berubah. Saat ini, Bodoh tidak hanya melakukan pemindaian switchgear secara rutin, tetapi juga pada masing-masing mesin.
"Menggunakan inframerah di jalur perakitan adalah nilai tambah yang besar," katanya. "Jika saluran terputus, pabrik ini tidak menghasilkan uang."
Dia juga secara teratur memindai lemari dan komponen listrik lainnya untuk titik panas, membuat pemeriksaan torsi cukup usang. Aktivitas inframerah ini tidak perlu dimatikan.
"Saya bisa keluar dan menghemat waktu dan uang perusahaan dengan menggunakan kamera dan menemukan sesuatu sebelum rusak," katanya.
Salah satu contoh terkait dengan tugas PM tertentu untuk generator.
PM listrik sebelumnya meminta generator dimatikan. Setelah membuang sakelar pemutus, roda terbang revolusi penuh unit akan membutuhkan waktu hampir satu jam untuk meluncur hingga berhenti total. Kemudian, pemeriksaan bisa dilakukan. Hari ini, Bodoh membuka panel listrik pada generator yang sedang berjalan dan melakukan pemindaian penuh. Dalam 15 menit, PM selesai. Tidak ada waktu henti mesin.
Dalam contoh lain, Bodoh menggunakan teknologi untuk mengungkap masalah yang rumit dan mudah diabaikan dengan kontaktor di dalam panel. Masalah intermiten menyebabkan mesin sesekali mogok.
"Pemindaian Dean menunjukkan suhu sekitar di dalam panel adalah 146 derajat," kata Angel. “Masih berfungsi, tapi tidak lama. Dengan informasi dari kamera itu, kami melihat lebih dalam dan mengidentifikasi masalahnya. Bagian depan kontaktor terlihat sempurna, tetapi bagian sampingnya matang. Kontaktor memanas, dan mungkin ada las yang buruk di suatu tempat. Saat memanas, ia kehilangan kontak. Saat mendingin, ia bersentuhan kembali. Sulit untuk menemukannya hanya dengan pemeriksaan visual. Kelihatannya normal. Tapi, Anda mendapatkan pemandangan lain dengan kamera."
Penghematan waktu sangat besar.
"Butuh waktu pemecahan masalah turun dari jam - atau lebih jika Anda memiliki tukang listrik nongkrong untuk satu atau dua shift, menunggu untuk gagal lagi - ke menit," kata Angel. "Kami mendapatkan gambarannya dan menemukan masalahnya. Kami pergi ke boks alat dan mendapatkan suku cadang yang diperlukan, mematikannya selama 15 menit untuk melakukan penggantian, dan kami selesai. Itu diselesaikan. Teknologi membawa kami ke akar masalahnya. "
GETARAN YANG BAIK
Prediktabilitas dan deteksi juga merupakan produk sampingan dari program analisis getaran.
Pabrik memiliki pengalaman paling praktis dengan teknologi PdM ini. Kontraktor luar menyiapkan parameter analisis asli untuk program pada akhir 1990-an. Departemen pemeliharaan kemudian menjadikan implementasi alat sebagai pekerjaan paruh waktu sebagai tukang reparasi mesin.
"Itu cukup," kata Fluet, "tapi masih ada ruang untuk perbaikan."
Masuk Pollar. Sejak naik ke peran penuh waktu sebagai pemimpin getaran, ia telah menggunakan penganalisis dua saluran dan keyboard komputernya untuk meningkatkan keandalan dan kemampuan yang sedang tren. Pollari, veteran Harley sembilan tahun, mengatakan pekerjaan itu penting tetapi jauh dari seksi.
"Sebagian besar waktu saya dihabiskan untuk melakukan pekerjaan database," katanya. "Kontraktor menyiapkan program awal. Ketika perusahaan seperti itu masuk, biasanya meluncurkan program getaran menggunakan parameter analisis standar untuk melihat mesin apa pun yang memiliki pompa di dalamnya atau memiliki kisaran tenaga kuda tertentu pada motor. Saya telah mengambil set data tersebut dan menyesuaikan parameter analisis sehingga spesifik untuk mesin kami.
"Saya akan melihat mesin dan mencari tahu berapa banyak batang rotor di motor itu. Saya akan mendokumentasikan slot stator, jenis bantalan tertentu. Dalam pompa, saya akan memeriksa berapa banyak baling-baling pada impeller, ditambah bantalan. jenis, suhu proses. Karakteristik tersebut perlu dimasukkan ke dalam database sehingga saya dapat memperoleh data getaran secara akurat dan melakukan diagnosa menyeluruh. Dengan begitu, ketika saya melakukan rute, saya memperoleh data yang bagus dan trendi, dan saya dapat mengidentifikasi potensi masalah komponen sebelum kegagalan."
Teknologi ini terbukti bermanfaat, antara lain, dalam menemukan kondisi di atas garis dasar pada spindel motor. Pekerjaan proaktif berikutnya meredakan risiko kegagalan bencana. Dan, perubahan tidak memengaruhi produksi.
Pekerjaan Pollari memungkinkan pemeliharaan mengomunikasikan temuan secara efektif kepada siapa pun di dalam dan di luar organisasi.
"Berlawanan dengan 'Saya pikir kami memiliki masalah getaran,' itu 'Kami memiliki masalah getaran. Ini adalah bantalan dalam. Mari kita kirim motor keluar atau lakukan sendiri dan ganti bantalan,'" kata Fluet. "Kami tahu persis apa yang perlu kami perbaiki atau ganti."
SOLUSI CERDAS
Pabrik Harley-Davidson ini mencapai prediktabilitas tinggi berkat analisis oli, termografi, dan analisis getaran. Namun, ia hampir meluncurkan teknologi tambahan yang akan mendorong kemampuannya ke wilayah yang belum dipetakan.
Sejak 1999, perusahaan dan khususnya pabrik Menomonee Falls telah mendukung penelitian yang dilakukan oleh Dr. Jay Lee di bidang sistem pemeliharaan cerdas (IMS). Profesor Lee awalnya mendirikan Pusat Sistem Pemeliharaan Cerdas di Universitas Wisconsin-Milwaukee. Hari ini, program tersebut berada di University of Cincinnati. Karya terobosannya adalah mengembangkan teknologi penginderaan berbasis kondisi yang dapat memprediksi dan memperkirakan kinerja peralatan ke titik di mana status "kerusakan hampir nol" dapat dicapai.
Musim panas ini, pabrik akan menjadi pionir dalam menerapkan perawatan cerdas yang sesungguhnya.
Proyek implementasi ini telah dibuat selama dua tahun. Pada tahun 2005, departemen pemeliharaan membeli peralatan penginderaan nirkabel dari Techkor Instrumentation. Seorang siswa dari program Lee menghabiskan seluruh musim panas lalu di pabrik mengembangkan program komputer yang menggunakan mekanisme pemicu untuk memulai penangkapan data pemantauan dari mesin. Intinya, ini melompati kemampuan penginderaan berbasis waktu dan memberikan pengumpulan data pada tanda pertama dari suatu peristiwa atau anomali.
Sejak saat itu, Techkor telah mengembangkan protokol komunikasi antara teknologi penginderaan dan program komputer. Solusi sebenarnya dijadwalkan untuk dikirimkan pada akhir Mei atau awal Juni.
"Kami masih dalam tahap perkembangan dan masa pertumbuhan ini," kata Fluet. "Kami akan mulai melihat manfaat harian aktual dari teknologi ini musim panas ini."
Delapan mesin akan berfungsi sebagai area uji awal untuk proyek IMS yang terhubung. Rencananya adalah memperluasnya ke mesin-mesin penting di antara total 1.400 aset pabrik di musim gugur.
Manfaatnya akan sangat besar.
"Saat ini, Gordy memiliki program getaran keliling," kata Fluet. "Dia harus secara fisik mengeluarkan mesin dari produksi, mengatur spindel pada kecepatan tetap dengan alat di atasnya, dan mengambil data getarannya. Ini informasi yang bagus, tetapi kontraproduktif dengan produksi karena kami mengeluarkan mesin dari produksi untuk dapatkan data non-intrusif itu. Sistem nirkabel ini akan memicu anomali apa pun dan memungkinkan kami mengumpulkan data itu. Di masa mendatang, Gordy akan dapat masuk, duduk di desktopnya, dan secara aktif menonton peralatan secara langsung."
Tapi getaran bukan satu-satunya aplikasi.
"Kami juga akan memantau arus. Kami dapat memantau masa pakai alat," katanya. "Alat baru akan menarik sejumlah X arus dari motor spindel. Saat pahat itu menjadi tumpul, permintaan saat ini untuk pahat tertentu akan mulai naik. Kami dapat menetapkan garis dasar dan tren masa pakai pahat. Kami memiliki mesin di luar sana yang menggunakan 60 hingga 70 alat untuk proses tertentu. Jadi di masa mendatang, kami akan dapat membuat dasar setiap alat dan secara mandiri melacak masa pakai alat untuk setiap alat tertentu.
"Premis dari program komputer ini akan berdampak pada bagaimana kita menggunakan teknologi prediktif di masa depan."
Fluet dan Angel membayangkan IMS mengantarkan era perintah kerja dan peringatan yang dibuat secara otomatis berdasarkan temuan data.
"Saya ingin memiliki mekanisme pemicu yang akan mengingatkan operator, dengan mengatakan, 'Kami memiliki tren yang merugikan di spindel Anda. Hubungi perawatan,'" kata Fluet. "Insinyur listrik kami sedang bekerja untuk memasang papan andon yang akan menandai saat mesin tertentu membutuhkan perhatian."
Angel berkata, "Akibatnya sangat besar. Produksi akan langsung merasakan dampaknya. Pemeliharaan akan secara langsung membantu produksi menjadi lebih hemat biaya."
TENAGA MANUSIA
Teknologi sangat penting dan menjadi faktor utama dalam rencana masa depan departemen pemeliharaan. Tetapi kartu truf dari pabrik Harley-Davidson ini, seperti yang didokumentasikan dalam banyak inisiatif yang tercantum dalam artikel ini, adalah manusia. Ini adalah pekerjaan mereka, sebagai individu dan sebagai anggota kelompok atau tim, yang memungkinkan keandalan dan prediktabilitas kelas dunia.
Fluet telah memainkan peran utama dalam merevisi manual spesifikasi mesin yang digunakan oleh pemasok saat ini dan calon pemasok. Buku setebal 200 halaman ini memberikan panduan ketat kepada produsen peralatan asli tentang cara merancang mesin yang diikat Harley berdasarkan persyaratan pemeliharaan dan keandalan perusahaan. Ini mencakup kriteria untuk, antara lain, fitur desain, pengujian run-off, dan standarisasi.
Terkait dengan spesifikasi tertulis tersebut, pabrik juga mengumpulkan tim integrasi aset yang membuat strategi perawatan lengkap untuk mesin baru sebelum dipasang di lantai pabrik. Tim tersebut mencakup perwakilan perdagangan yang terampil, anggota tim PdM, insinyur, dan operator mesin. Strategi perawatan aset berasal dari analisis Pemeliharaan Berpusat Keandalan yang lengkap. Ini mencakup daftar periksa dan jadwal perawatan preventif yang lengkap, daftar periksa dan jadwal perawatan prediktif, dan daftar suku cadang yang lengkap.
Perwakilan pemeliharaan juga bekerja dengan insinyur dan operator dalam tim peningkatan peralatan. Mereka memeriksa masalah mekanis kronis dan, dalam format kaizen/RCM, bersama-sama mengembangkan solusi perawatan, penggunaan, dan/atau desain yang meningkatkan kinerja.
Temuan dari tim dan proyek tersebut, atau dari aktivitas PM/PdM/RCM/IMS, dibagikan dengan pabrik Harley-Davidson lainnya melalui lingkaran praktik terbaik atau ruang elektronik.
Lingkaran praktik terbaik adalah pertemuan tatap muka triwulanan untuk para pemimpin dari disiplin tertentu (manajemen pemeliharaan, teknik keandalan, dll.). E-room adalah outlet berbasis Web tempat orang-orang dari departemen, kelompok kerja, atau fungsi tertentu mengumpulkan dan berbagi catatan rapat, dokumen, prosedur, dan strategi.
Rapat keandalan mingguan mempertemukan para pemimpin pemeliharaan dengan para perencana, pemimpin produksi, dan manajer umum pabrik. Mendemonstrasikan bahwa "Anda tidak dapat memprediksi hari esok kecuali Anda tahu apa yang terjadi kemarin", mereka melakukan pemeriksaan mayat pada masalah peralatan terbaru. Mereka juga mendiskusikan rencana pertempuran untuk yang baru muncul.
Kekuatan orang yang digerakkan oleh komunikasi juga terlihat dalam hal-hal kecil. Penasihat kelompok kerja pemeliharaan Jim Breister mengunjungi area produksi tempat kegiatan pemeliharaan baru-baru ini dilakukan. Dia mengobrol dengan operator untuk memastikan kepuasan mereka dan mungkin untuk mengidentifikasi kebutuhan tambahan yang dapat ditangani oleh departemen.
"Saya tahu semua operator dengan nama depan mereka," kata Breister. "Komunikasi yang baik menghasilkan keputusan yang baik."
'APAKAH KITA SUDAH SAMPAI?'
Harley-Davidson sedang menuju kejayaan perawatan. Rekan profesionalnya melihat organisasi pemeliharaan perusahaan sebagai yang terdepan.
"Harley-Davidson telah melakukan pekerjaan yang fantastis," kata Bruce Bremer, manajer teknik fasilitas untuk Toyota Motor Manufacturing Amerika Utara.
Rekan Toyota David Absher, manajer kontrol fasilitas di pabriknya di Georgetown, Ky., juga terkesan. "Saya telah meninjau beberapa pekerjaan yang telah dilakukan Harley-Davidson dalam pemeliharaan," katanya. "Saya kagum."
Bisa ditebak, pabrikan sepeda motor mengalihkan banyak pujian.
"Apakah kita 10 persen atau 20 persen perjalanan ke sana? Saya tidak tahu," kata Angel. "Saya melihat kita di bagian bawah kurva, naik. Masih banyak yang bisa kita lakukan."
Itu bukan hanya sikap manajemen.
"Ini menjadi lebih baik dan lebih baik setiap tahun," kata Bodoh. "Saya pikir kita berada di ambang membawa ini ke tingkat yang sama sekali berbeda. Langit benar-benar batas dari apa yang bisa kita capai."
Itulah yang membuat motor mereka tetap berjalan.
"Saya berharap dalam waktu dekat, semua PM kami akan bersifat prediktif," kata Czeszynski. "Tidak akan ada kejutan. Saya pikir perusahaan akan mendapat manfaat yang luar biasa karena kami terus bergerak maju dengan program ini. Ada banyak janji."
Dilahirkan untuk dapat diprediksi.
Anda tidak akan menemukannya ditato di bisep atau airbrush ke helm sepeda. Namun, ini adalah citra keandalan dan gaya hidup yang harus diupayakan oleh produsen mana pun.
IKUTI PEMIMPIN:PELAJARAN DARI PENGAWASAN PEMELIHARAAN
Apa yang telah dipelajari oleh para pemimpin pemeliharaan di pabrik Harley-Davidson ini dari pengalaman peningkatan keandalan mereka?
Larry Angel, manajer pemeliharaan: "Proses ini membutuhkan waktu. Komunikasi dan komunikasi berulang serta penjelasan adalah kuncinya. Setiap orang perlu memahami apa yang Anda lakukan dan mengapa Anda melakukannya. Jika Anda melakukannya, orang-orang akan mulai bergabung. Pada awalnya, beberapa orang dalam pemeliharaan meremehkan banyak hal ini karena mereka tidak memahaminya. Namun, ketika orang-orang dan rekan-rekan mereka mulai menunjukkan bahwa hal-hal ini berhasil, mereka menjualnya."
Jim Breister, penasihat kelompok kerja pemeliharaan: "Membangun kepercayaan sangat besar, terutama dengan operasi. Kita bisa masuk dengan data yang kuat dari orang-orang ini yang menunjukkan apa yang perlu kita lakukan. Ketika Anda bisa mendatangi seseorang dan berkata, 'itu adalah landasannya,' itu mengejutkan mereka. juga penting untuk memiliki kisah sukses dan untuk mempromosikannya. Dana pandai mempublikasikannya kepada orang lain. Dia adalah alat penting dalam kotak peralatan saya."
Dana Fluet, teknisi keandalan pemeliharaan utama: "Ini semua tentang kredibilitas. Hasil dari teknologi prediktif dan upaya pemeliharaan preventif membuktikan bahwa seluruh organisasi pemeliharaan melakukan pekerjaan yang luar biasa dalam meningkatkan ketersediaan alat berat. Jika kami memiliki temuan, saya akan menghadiri pertemuan keandalan mingguan dengan seorang komponen yang gagal dan menunjukkan kepada pemimpin dari pemeliharaan luar bagaimana kami mengekstrak data. Ini menunjukkan kepada mereka bahwa kami akan melakukan perbaikan yang benar. Kami tidak hanya menyapu. Kami mengidentifikasi dan memperbaiki komponen yang tepat. Ini menunjukkan bahwa 'pemeliharaan' adalah tenaga kerja terampil yang dapat kami andalkan.'"