TPM dengan RCM Membentuk Kombinasi yang Kuat
Dua filosofi yang saling melengkapi membentuk kombinasi yang kuat untuk mengubah budaya organisasi dan membangun proses untuk perbaikan berkelanjutan. Pendekatan Total Productive Maintenance (TPM), berdasarkan orang dan proses, mengubah budaya dan cara kita memandang aset kita.
Pendekatan Pemeliharaan Berpusat Keandalan (Reliability-Centered Maintenance/RCM) dapat menjadi hal yang menakutkan, meskipun pendekatan ini membangun fondasi yang kuat untuk strategi pemeliharaan. Secara individual, keduanya merupakan pendekatan monumental untuk keunggulan pemeliharaan, tetapi bila digabungkan telah terbukti mengurangi waktu henti dan meningkatkan produktivitas.
SKF telah membuat keputusan untuk mengubah cara memandang asetnya. Aset kami – seperti milik Anda – sangat berharga. Mungkinkah sesederhana membuat keputusan untuk berubah?
Filosofi Pelengkap
Dengan mendukung proses TPM, khususnya pilar Planned Maintenance &Autonomous Maintenance, metodologi RCM akan semakin memperkuat fondasi manajemen pemeliharaan dan memfasilitasi peningkatan berkelanjutan.
Anda dapat secara meyakinkan mendapatkan program pemeliharaan berdasarkan tujuan bisnis organisasi secara keseluruhan. Apa yang pertama-tama harus kita pahami adalah bahwa sebelum siapa pun pergi ke mana pun (yaitu produksi dan pemeliharaan "kelas dunia") atau melakukan apa pun (yaitu "bekerja lebih cerdas daripada lebih keras") – keputusan harus dibuat di semua tingkat organisasi untuk berubah.
SKF mempelajari ini secara langsung dari salah satu pabrik Divisi Otomotif kami di Amerika Selatan. Di pasar yang sangat kompetitif, pabrik ini sulit mendapatkan keunggulan kompetitif dengan perilaku tradisional terkait produksi dan pemeliharaan.
Ketika dihadapkan dengan penutupan yang menjulang di tahun-tahun mendatang, mereka memutuskan untuk membuat perubahan. Agar tetap terbuka dan menyelamatkan banyak pekerjaan dalam prosesnya, pabrik ini memilih TPM sebagai katalis perubahan.
Beberapa waktu kemudian, SKF telah mengadopsi filosofi ini sebagai salah satu cara mereka membangun landasan untuk Keunggulan Manufaktur Kelas Dunia.
Sejak mengadopsi TPM, SKF mulai menyadari bahan yang hilang, pemikiran keandalan. Adaptasi tersebut awalnya dianggap sebagai RCM, tetapi kemudian ternyata lebih mahir menggunakan proses SKF SRCM.
Mengapa? RCM sangat berguna dan layak untuk pemeliharaan instalasi yang identik (seperti pesawat terbang), tetapi mengingat konteks operasional dan pemeliharaan aset kami, hal itu tidak terjadi.
Masalah lainnya adalah bahwa tingkat jatuh tempo pemeliharaan tertentu diperlukan untuk memastikan data aset yang akurat dan lengkap. Sulit untuk mengukur dan memastikan bahwa setiap orang akan berada pada level yang setara. Berdasarkan ketidakteraturan aset dan jatuh tempo pemeliharaan yang tidak pasti, SKF memilih SKF SRCM.
SKF SRCM adalah proses peninjauan strategi pemeliharaan yang memberikan hasil yang hampir sama dengan RCM klasik, tetapi menggunakan proses yang efisien untuk menentukan kebutuhan dan memfokuskan upaya yang tepat pada peralatan, fungsi, dan sistem yang penting dan tidak penting.
Baik TPM maupun SKF SRCM telah terintegrasi, dan Pilar Pemeliharaan Terrencana dari TPM telah didesain ulang. Dampaknya tidak hanya memengaruhi pilar Pemeliharaan yang Direncanakan, tetapi memiliki efek berjenjang pada semua pilar yang telah dipilih SKF untuk diterapkan.
Pilar yang dipilih, tanpa urutan tertentu, adalah Peningkatan Terfokus, Pelatihan dan Pendidikan, Pemeliharaan Terrencana, dan Pemeliharaan Otonom dengan landasan 5-S.
Pemeliharaan Produktif Total
TPM, filosofi Jepang yang digunakan di banyak aspek industri, berupaya meningkatkan produktivitas dengan menghilangkan segala upaya yang sia-sia. TPM menarik bagi banyak industri yang berbeda tetapi telah terbukti baik dalam produksi lini dan batch.
Idenya dimulai pada tahun 1951 ketika pemeliharaan preventif diperkenalkan ke Jepang dari Amerika Serikat. Nippondenso, bagian dari Toyota, adalah perusahaan pertama di Jepang yang memperkenalkan pemeliharaan preventif di seluruh pabrik pada tahun 1960.(5)
Setelah beberapa realisasi dibuat, beban kerja terlalu banyak untuk pemeliharaan saja. Hubungan pemeliharaan bersama antara operator dan pemeliharaan diimplementasikan yang disebut pemeliharaan terencana dan otonom.
Hal ini telah berkembang menjadi delapan pilar yang biasa kita kenal sekarang sebagai Kobetsu Kaizen, Pemeliharaan Otonom, Pemeliharaan Terrencana, Pelatihan dan Pendidikan, Manajemen Peralatan Dini, Kebersihan &Lingkungan Keselamatan, Pemeliharaan Kualitas, dan TPM di Kantor.
Banyak organisasi berbeda mengubah TPM dan menjadikannya unik untuk filosofi perusahaan mereka; namun, konsep dan perkembangan batin sebagian besar tetap sama.
Pemeliharaan Berpusat pada Keandalan
RCM dapat dijelaskan secara singkat sebagai proses terstruktur, yang awalnya dikembangkan di industri penerbangan, untuk menentukan strategi pemeliharaan peralatan yang diperlukan untuk aset fisik apa pun guna memastikan bahwa aset tersebut terus memenuhi fungsi yang dimaksudkan dalam konteks operasinya saat ini.
Aset didekomposisi, dianalisis dan dijelaskan secara ekstensif, mode kegagalan dan analisis efek (FMEA) dibuat untuk komponen yang paling penting, dan organisasi serta proses pemeliharaan didefinisikan (kembali) secara hati-hati.(1)
Untuk membuat pernyataan tegas, RCM berasal dari proses untuk membantu menjaga pesawat agar tidak jatuh dari langit dan membuat pembangkit listrik tenaga nuklir menjadi bencana seperti Chernobyl berikutnya.
RCM dikembangkan di industri penerbangan komersial AS pada akhir 1960-an. RCM kemudian diadopsi oleh Departemen Pertahanan AS pada 1970-an. RCM diidentifikasi oleh USA Electric Power Research Institute (EPRI) pada tahun 1984 sebagai kandidat untuk aplikasi pembangkit listrik tenaga nuklir. Selanjutnya, tiga aplikasi percontohan disponsori oleh EPRI dari tahun 1985 hingga 1987; semuanya adalah studi sistem tunggal yang dimulai.
Untuk lebih memperjelas apa itu RCM dan bukan, standar dari Society of Automotive Engineers dikembangkan yang dikenal sebagai SAE JA10112 dan dapat ditemukan di www.SAE.org. Standar ini memberikan kriteria evaluasi untuk menghilangkan pertanyaan apakah proses RCM yang disebut benar sampai ke akarnya atau tidak untuk memastikan bahwa aset terus memenuhi fungsi yang dimaksudkan dalam konteks operasinya saat ini.
Ketujuh kriteria yang disederhanakan adalah sebagai berikut:
- Apa fungsi dan konteks operasinya?
- Bagaimana bisa gagal mencapai fungsi ini?
- Apa yang membuat kegagalan fungsi menjadi kenyataan?
- Apa akibat dari kegagalan yang sebenarnya?
- Apa hasil dari hasil dan signifikansi yang ditentukan?
- Apa yang harus dilakukan untuk menghilangkan kegagalan?
- Apa yang harus dilakukan jika kegagalan tidak dapat dihilangkan?
Langkah Pertama Pertama
SKF memutuskan untuk membuat perubahan dan memilih kendaraan. Kami kemudian mengubah kendaraan itu untuk memenuhi kebutuhan kami dan mengatasi budaya. TPM sederhana dan SKF SRCM adalah metode yang disponsori. Kedua metode ini bila digabungkan hanya akan menjadi titik awal untuk Keunggulan Manufaktur Kelas Dunia.
Banyak area lain seperti Six Sigma, efisiensi energi, dll., perlu ditaburkan dan semuanya harus seimbang satu sama lain. Alasan kepemilikan membatasi beberapa konten tentang bagaimana, tetapi jika hanya berfokus pada pilar Pemeliharaan Terrencana dari TPM, poin utama dapat disorot dan disampaikan.
Perubahan ini tidak hanya dibutuhkan di lantai manufaktur, tetapi juga oleh tim manajemen. SKF perlu membuka matanya untuk melihat dengan cara yang berbeda. Tolok ukur adalah metrik kunci pertama.
Mengukur kinerja kami terhadap industri manufaktur lain di seluruh dunia sangat penting. SKF memang memiliki kantong “praktik terbaik” secara internal, tetapi akan lebih kuat untuk membandingkan organisasi eksternal. Ini akan membantu mendorong kebutuhan akan perubahan.
Lima Cara Utama Meningkatkan SKF
Perusahaan-perusahaan yang berkunjung seperti Bosch, Tetra Pak, Fiat dan Unilever (antara lain) memberikan landasan untuk membuat analisis kesenjangan untuk secara akurat mengukur situasi kita saat ini jika dibandingkan dengan visi SKF. Analisis kesenjangan serta Analisis Kebutuhan Klien (CNA) SKF adalah alat yang digunakan. SKF diperlukan untuk mengukur kematangan produksi dan pemeliharaan.
Alat ini cukup mudah untuk menyampaikan informasi antara fasilitas manufaktur individu di seluruh dunia ke lokasi terpusat. Analisis kesenjangan dan CNA merupakan upaya berkelanjutan yang biasanya dilakukan pada frekuensi tahunan untuk memeriksa kemajuan dan mengatasi area yang lemah.
Struktur organisasi sangat dibutuhkan. Mengapa? Dalam organisasi global, tidak praktis memiliki kelompok kecil atau besar yang ditempatkan di pusat untuk membuat perubahan global.
Butuh beberapa waktu untuk mengkonfigurasi struktur organisasi yang paling tepat. Biasanya tidak ada cara yang benar atau salah, tetapi pasti ada produk sampingan dari struktur organisasi yang buruk.
Pendekatan bottom-up adalah cara yang lebih disukai. SKF menemukan bahwa ia harus terus berubah untuk mengatasi masalah baru dan mendorong perbaikan berkelanjutan. Diagram di bawah menggambarkan pendekatan dari bawah ke atas dan di mana dukungan diselaraskan untuk perbaikan berkelanjutan.
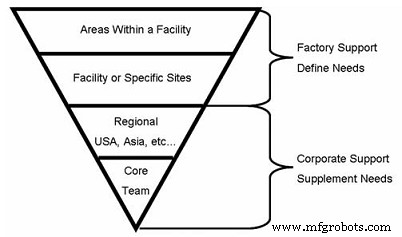
Gambar 1. Pendekatan top-down untuk struktur organisasi.
Konsultasi adalah bidang utama yang terus membuat perbedaan. Ketika SKF tidak memiliki sumber daya atau ketersediaan internal, SKF harus dilengkapi. Kami telah meminta konsultan TPM, serta pakar konten lainnya, untuk memberikan bantuan kepada SKF agar dapat bertransformasi secara global.
Karena sifat konsultan, hasil mereka sesuai dengan kebutuhan organisasi. Konsultan berkualitas baik adalah suatu keharusan bagi SKF untuk lebih memahami situasinya saat ini dan untuk mendapatkan keunggulan kompetitif atas arah tujuan oposisi.
Manajemen Proses Bisnis (BPM) adalah sesuatu yang muncul baru-baru ini dalam konteks sistem BPM. Sistem BPM memungkinkan manajemen dan insinyur untuk menganalisis dan mengukur efektivitas proses bisnis.
Dengan menggunakan sistem BPM yang belum sempurna, Divisi Industri dan Divisi Layanan SKF menggabungkan kekuatan dan melapisi Optimalisasi Efisiensi Aset (AEO) menggunakan proses SKF SRCM dan pilar Pemeliharaan Terrencana dari TPM. Enam karakteristik mendasar diidentifikasi dalam konteks pemeliharaan terencana:
- Evaluasi tahap saat ini (KPI dan keselarasan tujuan bisnis)
- Perbaiki aset dan tingkatkan titik lemah
- Mengatur Sistem Manajemen Pemeliharaan Komputer (CMMS)
- Kembangkan strategi pemeliharaan
- Menerapkan strategi pemeliharaan
- Mengevaluasi dan mempertahankan strategi pemeliharaan
Area kunci terakhir yang dapat dimanfaatkan SKF adalah bagaimana dan kapan menggunakan teknologi dan teknik apa. SKF Asset Management Services bekerja sama untuk meresepkan obat yang tepat untuk diagnosis yang akurat. Ini tentu saja dalam konteks manajemen pemeliharaan. Sudah terbukti dengan baik untuk mendapatkan kemenangan cepat – kemenangan singkat dan cepat.
Bagian dari proses pengambilan keputusan, seperti yang dibahas di atas, adalah untuk memutuskan apakah perbaikan berkelanjutan dari waktu ke waktu tepat atau apakah lebih cerdik untuk mendapatkan beberapa kemenangan cepat untuk mendapatkan momentum. SKF memilih peningkatan berkelanjutan dari waktu ke waktu.
Kesimpulannya, cukup sederhana untuk memutuskan untuk melakukan apa pun. Menindaklanjuti dan terus meningkatkan adalah hal yang paling gagal dilakukan. Menetapkan sistem dan proses serta menempatkannya pada tempatnya sangat penting untuk perbaikan berkelanjutan.
Mungkinkah sesederhana membuat keputusan untuk berubah? Jawabannya, menurut saya, adalah tidak; itu adalah apa isinya dan apa yang kita lakukan. Bukan apa yang kita bicarakan, melainkan tindakan. Inilah yang dibutuhkan untuk mencapai visi secara keseluruhan.
SKF terus mengalami hasil seperti pengurangan waktu henti, peningkatan hasil, peningkatan efisiensi, dan kepuasan karyawan karena keputusan ini. Apalagi pilihan ada di tangan Anda. Apa yang akan Anda putuskan?
Referensi
- Glosarium Aptitude Exchange www.aptitudexchange.com
- Diterbitkan Agustus 1999. Kriteria Evaluasi untuk Proses Reliability-Centered Maintenance (RCM), SAE JA 1011. www.sae.org
- Nowlan FS, Heap HF,. 1978. Pemeliharaan Berpusat Keandalan, Layanan Informasi Teknis Nasional, Departemen Perdagangan AS, Springfield, Va.
- Roberts J. 1997. "Total Productive Maintenance (TPM)," Departemen Teknologi Industri dan Rekayasa Texas A&M University-Commerce; Antarmuka Teknologi. http://et.nmsu.edu/~etti/fall97/manufacturing/tpm2.html
- Venkatesh J. direvisi 28 Oktober 2007. Pengantar Total Productive Maintenance (TPM) http://www.plantmaintenance.com/articles/tpm_intro.shtml