Cara Menerapkan Strategi Pemeliharaan yang Benar pada Aset Anda
Banyak perusahaan baru-baru ini menerapkan inisiatif keandalan yang diarahkan untuk mengoptimalkan fungsi pemeliharaan di pabrik mereka. Beberapa berhasil; namun, sebagian besar akan mengakui bahwa mereka tidak menyadari manfaat yang diharapkan.
Ada banyak pendekatan untuk berhasil menerapkan program keandalan dan strategi pemeliharaan. Mari kita bahas model yang telah terbukti untuk meningkatkan program Pemeliharaan Berbasis Keandalan perusahaan melalui optimalisasi tugas pemeliharaan yang berfokus pada penghapusan kegagalan.
Mari kita mulai dengan mengasumsikan bahwa kita sedang berhadapan dengan pabrik besar dengan banyak program yang telah diterapkan saat mereka mencoba bergerak menuju Pemeliharaan Berbasis Keandalan. Sistem manajemen pemeliharaan terkomputerisasi (CMMS) digunakan untuk mengelola operasi, program pemeliharaan preventif (PM) berbasis inspeksi yang besar telah dibangun, dan program pemeliharaan prediktif (PdM) yang relatif besar diterapkan untuk memantau kondisi aset.
Banyak potongan teka-teki keandalan yang ada, tetapi peningkatan biaya dan hasil keandalan belum terwujud karena integrasi sistem yang terpisah belum dipertimbangkan, sehingga setiap sistem tidak dioptimalkan.
Seringkali, program seperti yang tercantum di atas dipandang oleh organisasi sebagai program "berdiri sendiri". Namun jika ada upaya bersama untuk menyempurnakan dan mengintegrasikan semua program yang sudah ada, kita biasanya akan melihat peningkatan efektivitas peralatan secara keseluruhan (OEE) dengan pengurangan yang signifikan dalam pengeluaran pemeliharaan.
Di Mana Memulai Saat Mengembangkan Strategi Pemeliharaan
Keberhasilan biasanya diukur dengan peningkatan laba perusahaan. Untuk mencapai keberhasilan finansial dari setiap proyek, pemicu biaya utama yang ditangani oleh proyek harus dipahami. Misalnya, pabrik dapat mengukur jenis pekerjaan (pencegahan, prediksi, kegagalan dan modifikasi), tenaga kerja dan bahan.
Mari kita asumsikan kita sedang melihat sebuah pabrik di mana sekitar 15 persen pekerjaannya bersifat prediktif, 35% bersifat preventif, 25% adalah kegagalan tak terduga dan sekitar 15% dari PM menunggak setiap bulan. Selain itu, organisasi mungkin memiliki tumpang tindih antara kegiatan pemeliharaan preventif dan prediktif. Tumpang tindih membutuhkan biaya dan itu terjadi karena alasan tertentu. Penting untuk memahami alasannya sebelum mengembangkan strategi pemeliharaan.
Pabrik dapat menghabiskan waktu bertahun-tahun untuk membangun program pemeliharaan preventif, dan mereka didorong untuk membuat PM karena mereka dihargai karena berkurangnya kegagalan saat proses PM diimplementasikan. Seiring waktu, sistem PM ini akan berkembang untuk menyertakan inspeksi untuk semua jenis kegagalan.
Mungkin ada pengalaman negatif terkait dengan kegagalan, yang membutuhkan penambahan PM. Frekuensi akan diatur dan PM diterapkan ke setiap peralatan yang serupa dengan peralatan yang gagal. Konsekuensi atau sifat kegagalan biasanya diabaikan karena tidak ada hubungannya dengan pertemuan dengan atasan untuk menjelaskan kegagalan.
Mesin gagal, bos tidak senang, dan PM membuat bos tidak senang. Seiring waktu, jumlah PM meningkat ke titik di mana banyak yang tidak diselesaikan; bahkan dengan program PM yang ekstensif, masih ada kegagalan yang tidak dapat dihilangkan.
Sebuah pabrik akan memulai program PdM dengan memantau beberapa peralatan yang sangat kritis dengan analisis getaran (di mana biasanya ada beberapa keberhasilan). Tentu saja, kesuksesan adalah hadiah positif, dan untuk meningkatkan kesuksesan itu, program akan berkembang.
Jika organisasi memiliki banyak dukungan secara korporat untuk implementasi PdM, mereka biasanya akan menerapkan teknologi tersebut ke 50% dari aset mereka yang diketahui dan menggunakan semua teknologi yang tersedia. Untuk menentukan berapa banyak aset yang akan dipantau, pabrik harus menentukan berapa banyak teknologi yang dapat didukungnya dan kemudian membeli peralatan yang dibutuhkan untuk melakukan pekerjaan tersebut.
Dalam kedua kasus, implementasi PM maupun PdM, mode kegagalan, efek, atau konsekuensi kegagalan tidak dievaluasi untuk menentukan efektivitas biaya atau bahkan kelayakan tugas pemeliharaan untuk benar-benar memprediksi atau menghilangkan kegagalan.
Sebagai contoh, pabrik mungkin menggunakan teknologi prediktif untuk memantau bantalan, tetapi sering kali mengirim mekanik untuk merobohkan aset dan memeriksa bantalan yang sama. Konyol ini mungkin tampak mendasar. Namun, itu umum di industri. Karena itu, pertama-tama kita harus mendiskusikan metodologi strategi pemeliharaan sebelum menjelaskan langkah-langkah implementasi.
Prinsip-prinsip yang digunakan untuk memperbaiki inefisiensi tersebut adalah:
-
Semua tugas pemeliharaan harus mengatasi mode kegagalan tertentu
-
Gunakan tugas yang paling murah dan paling efektif untuk memelihara aset
-
Interval tugas pemeliharaan akan sedemikian rupa sehingga mengatasi kegagalan pada titik optimal dalam siklus kegagalan aset tersebut
-
Total biaya kegagalan harus melebihi biaya tugas untuk memelihara aset
-
PM pada akhirnya harus menjadi perbaikan berdasarkan waktu, bukan inspeksi
-
Kegagalan yang disebabkan oleh pengoperasian aset di luar kemampuan tidak dapat dipertahankan. Aset harus didesain ulang
Untuk mengilustrasikan pendekatan ini, mari kita lihat sekilas Kurva PF yang ditunjukkan pada Gambar 1. Penulis John Moubray menggunakan kurva PF dalam bukunya “Reliability-Centered Maintenance II” untuk menunjukkan ketepatan waktu dan efektivitas tugas PdM.
Titik telah ditempatkan di sepanjang kurva untuk mewakili periode waktu (PF) dari titik deteksi cacat P ke titik kegagalan fungsional F. Logika memberi tahu kita bahwa semakin lama periode peringatan, semakin mudah untuk mendukung upaya perencanaan dan penjadwalan yang diperlukan untuk organisasi Pemeliharaan Berbasis Keandalan yang efisien.
Apa yang dapat kita lihat dengan mempelajari kurva ini adalah bahwa tugas PdM memiliki kemampuan untuk mengidentifikasi kondisi penyebab kegagalan pada interval P-F yang lebih lama daripada tugas PM. Selain itu, tugas PdM mungkin lebih cocok untuk mengidentifikasi mode kegagalan.
Analisis lebih lanjut dari tenaga kerja yang dibutuhkan untuk melakukan pekerjaan menunjukkan kepada kita bahwa dari sudut pandang keuangan, tugas PdM, rata-rata, adalah seperempat dari biaya tugas PM yang digunakan untuk mendeteksi mode kegagalan yang sama. Selain itu, PM terbukti memperkenalkan kegagalan yang sebaliknya tidak akan terjadi. Kegagalan dini ini sering disebut sebagai kematian bayi.
Dampak finansial tambahan, dan seringkali terbesar, adalah waktu henti produksi. Tugas PdM biasanya dilakukan saat peralatan sedang berjalan dan pekerjaan korektif yang diidentifikasi oleh teknologi PdM dijadwalkan bersamaan dengan tugas korektif bernilai tinggi lainnya. Inspeksi PM biasanya mengharuskan peralatan dimatikan.
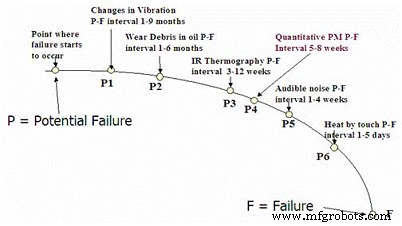
Gambar 1:Kurva PF, dari buku John Moubray “Reliability Centered Maintenance II ”
Seperti yang Anda lihat, keputusan yang paling ekonomis, dan yang paling masuk akal secara teknis, adalah mempertahankan aset dengan menggunakan sumber daya berikut, sesuai urutannya:
- Pemantauan proses
- Teknologi PdM
- Tugas terarah (PM) berdasarkan waktu/meter
Menyelaraskan Tugas Pemeliharaan dengan Kegagalan
Kegagalan dapat dikelompokkan ke dalam tiga kategori berikut. Memahami kategori ini sangat penting saat menetapkan tugas pemeliharaan.
- Terinduksi
- Intermiten
- Lelah
Kegagalan yang disebabkan adalah hasil dari kekuatan luar yang menyebabkan mode kegagalan. Misalnya, pabrik dapat menjalankan proses produksi sedemikian rupa sehingga aset dipaksa sebelum waktunya ke dalam situasi potensi kegagalan, atau kondisi kaki yang lemah pada rangkaian peralatan yang menyebabkan ketidaksejajaran kopling pada akhirnya menyebabkan kegagalan bantalan dalam kapal.
Sementara pemantauan proses dan PdM dapat membantu mendeteksi potensi kegagalan ini (sehingga menghilangkan penghentian yang tidak terjadwal), penting untuk memahami bahwa kegagalan yang disebabkan harus dikenali dan analisis dilakukan untuk menentukan akar penyebabnya. Baru setelah itu kami bertindak secara proaktif dan melakukan transisi menjadi organisasi Pemeliharaan Berbasis Keandalan.
Kegagalan intermiten bisa terjadi kapan saja. Beberapa mungkin benar-benar menggunakan istilah "acak"; namun, implikasinya adalah mean time between failure (MTBF) tidak dapat ditentukan. Ini berbeda dari kegagalan yang diinduksi karena biasanya terjadi cukup jauh di atas Kurva P-F sehingga perbaikan dapat direncanakan dan dijadwalkan secara efektif. Pabrik dapat mendeteksi mode kegagalan ini dengan baik melalui proses dan pemantauan PdM jika memungkinkan.
Banyak pabrik juga menemukan bahwa PMs tidak efektif dalam menentukan permulaan kegagalan baik dalam kegagalan yang diinduksi atau terputus-putus dan, oleh karena itu, pemborosan modal. Terlalu sering, pabrik kemudian dapat memilih untuk meningkatkan frekuensi PM, atau lebih buruk lagi, menulis dan menjadwalkan prosedur baru untuk mencoba mengurangi kegagalan ini. Inilah yang pada akhirnya mengarah pada program pemeliharaan yang tidak efektif, mahal, dan tidak terkendali.
Kegagalan aus memiliki MTBF yang diketahui dan terjadi ketika masa manfaat suatu komponen telah habis. Jenis mode kegagalan ini sering dapat dideteksi melalui proses dan pemantauan PdM. Namun, perbaikan berbasis waktu biasanya terbukti menjadi strategi pemeliharaan yang paling efektif.
Pengertian PM
PM, menurut definisi, adalah aktivitas perbaikan/penggantian yang akan mengembalikan fungsionalitas atau masa manfaat aset kembali ke keadaan semula. Jenis PM lainnya adalah tugas pencarian kegagalan atau evaluasi kondisi. Sebuah pabrik akan menyebarkan tugas menemukan kegagalan ketika konsekuensi dari kegagalan atau risiko yang terkait dengan kegagalan dapat ditoleransi; tugas-tugas ini juga membantu dalam menemukan kegagalan tersembunyi. Salah satu metode untuk menemukan kegagalan adalah dengan menguji-jalankan peralatan pabrik siaga pada beberapa frekuensi untuk memastikan peralatan tersebut tidak gagal saat tidak digunakan.
Tugas evaluasi kondisi dilakukan untuk menentukan tingkat kegagalan komponen. Ketika organisasi memilih untuk melakukan tugas evaluasi kondisi, dengan pemahaman bahwa evaluasi kondisi digunakan untuk mencoba menentukan MTBF. Diterapkan dengan benar, itu harus bersifat kuantitatif. Dengan kata lain, pengukuran presisi diambil dan dibandingkan dengan kriteria yang ditetapkan yang menentukan kapan penggantian diperlukan. Ada dua alasan prinsip pabrik akan menetapkan ukuran kuantitatif.
-
Perbedaan keterampilan kerajinan diminimalkan.
-
Tren tingkat keausan. Jika memungkinkan, tingkat peringatan atau waspada (kondisi kuning) dan tingkat kritis atau tindakan (kondisi merah) harus ditentukan.
Menerapkan Strategi Pemeliharaan
Pemahaman menyeluruh tentang potensi kegagalan setiap peralatan dapat dikembangkan melalui mode kegagalan dan analisis efek (FMEA) untuk setiap jenis peralatan di pabrik. Template FMEA dapat dikembangkan pada tingkat kelas/subkelas/kualifikasi (yaitu Pump/Centrifugal/Coupled atau Pump/Centrifugal/Belt Driven). Penghematan waktu yang signifikan dapat diwujudkan dengan mengembangkan template. Dengan setiap jenis peralatan, pabrik harus mampu menjawab tujuh pertanyaan dasar RCM.
- Apa fungsinya?
- Apa saja kegagalan fungsionalnya?
- Apa saja mode kegagalannya?
- Apa efek dari kegagalan tersebut?
- Apa akibatnya?
- Bagaimana cara mengatasi kegagalan?
- Bagaimana jika tugas yang sesuai tidak dapat ditemukan?
Saat menjawab Pertanyaan 6, pertimbangkan jalur logis untuk memanfaatkan tiga sumber daya – pemantauan proses, pemantauan PdM, dan PM, dalam urutan itu – seperti yang dijelaskan sebelumnya.
Setelah FMEA selesai, mereka dapat diterapkan pada tingkat aset. Tinjauan yang lebih terperinci ini terkait dengan kriteria peringkat kekritisan untuk menentukan apakah konsekuensi kegagalan cukup besar untuk melakukan tugas. Ini benar-benar aturan keputusan ekonomi, "Apakah biaya kegagalan lebih besar daripada biaya mitigasi?" Hal ini sangat penting untuk diperhatikan karena tujuan dari program ini adalah untuk mengurangi biaya pemeliharaan sambil mempertahankan utilisasi aset yang tinggi.
Sekarang pabrik dapat mendefinisikan dan mengomunikasikan parameter proses dan membangun kembali serta mengimplementasikan rute PdM. Misalnya, pabrik dapat menggunakan:pemantauan getaran lambat dan kecepatan tinggi, termografi listrik dan mekanik, analisis sirkuit motor, analisis oli, dan pengujian ketebalan NDT. Tugas PM yang ada yang mencakup mode kegagalan yang sama yang sekarang didefinisikan dengan tugas PdM kemudian dapat dihapus dari sistem.
Contoh Strategi Pemeliharaan
Jika pabrik menentukan bahwa PM adalah cara paling efektif untuk mengurangi kegagalan, komponen yang aus diganti. Misalnya, jika konveyor sekrup dimatikan untuk PM yang menangani bantalan gantungan, bantalan akan diganti daripada diperiksa untuk menentukan apakah penggantian diperlukan.
Pendekatan ini sering diambil karena biaya untuk mematikan saluran dan tenaga yang dibutuhkan untuk membongkar peralatan untuk pemeriksaan lebih besar daripada biaya beberapa bantalan gantungan. Setelah perbaikan selesai, bantalan yang dilepas dapat diperiksa "di bangku" untuk membantu menentukan MTBF lebih lanjut dan dengan demikian "mengubah" frekuensi tugas jika diperlukan. Ini menghilangkan hampir semua tugas jenis evaluasi kondisi.
Frekuensi PM ditentukan oleh riwayat perintah kerja dan pengetahuan kerajinan. Jika ada pertanyaan tentang MTBF, pabrik mana pun akan memilih durasi yang lebih lama untuk mengatur frekuensi PM. Mengapa mereka harus memilih durasi yang lebih lama untuk tingkat kegagalan?
Orang mungkin berpikir ini akan menyebabkan beberapa kegagalan, tetapi pikirkan seperti ini:Jika setiap PM dimasukkan secara konservatif dan dilakukan pada interval yang pendek dan aman, akan membutuhkan waktu lama untuk mengetahui apakah kita mengukur sistem PM dengan benar. Jika setiap PM diatur pada interval yang sejauh yang kami ketahui adalah interval sebenarnya, akan ada beberapa kesalahan yang dibuat, tetapi ini akan terlihat dengan relatif cepat.
Ini mungkin lompatan besar untuk beberapa tanaman. Namun, untuk membuat langkah besar dalam sebagian besar upaya keandalan, ini akan terbukti menjadi metode yang benar. Jika beberapa frekuensi terlewatkan, mereka akan dapat menerima kegagalan sementara dan meningkat seiring waktu. Keberhasilan akan bergantung pada apakah frekuensi tampaknya telah disetel dengan tepat dan jika kegagalan tak terduga tidak meningkat.
Hasil
Pendekatan ini biasanya menghasilkan hal berikut:
-
Selama tahap awal, biaya pemeliharaan akan turun, dan akan terus berlanjut.
-
Jumlah staf pemeliharaan akan berkurang secara signifikan dibandingkan dengan tingkat pra-proyek dan akan terus berkurang. Hal ini biasanya diwujudkan melalui penghapusan kontraktor).
-
Pengembalian investasi proyek yang signifikan (yaitu kinerja tiga bulan pertama membayar kembali lebih dari setengah dari total biaya proyek).
-
Penghentian besar-besaran akan dimungkinkan untuk memungkinkan pemasangan peralatan modal baru sementara OEE untuk fasilitas tersebut tidak menurun.
-
Peralatan tidak dapat digunakan jauh lebih jarang karena PM.
-
Jumlah teknolog prediktif meningkat seperti halnya persentase aset yang dipantau kondisi. Karena kedalaman cakupan pemantauan kondisi, pemantauan berkelanjutan memastikan keandalan pembangkit tidak terganggu karena proyek.
Banyak pabrik dan manajer mengidentifikasi alat dan sistem yang mengklaim dapat memperbaiki penyakit keandalan fasilitas. Diimplementasikan secara independen, alat dan sistem hanyalah modul tambahan yang meningkatkan biaya tanpa meningkatkan keandalan pabrik. Keandalan yang sebenarnya dicapai ketika metode yang paling hemat biaya diterapkan pada aset di pabrik, sehingga memaksimalkan upaya pemeliharaan dengan total biaya minimum untuk bisnis.
"Ekonomi kekuatan" adalah istilah militer yang digunakan untuk menggambarkan teknik hanya menggunakan kekuatan yang diperlukan untuk mengalahkan musuh. Di dunia keandalan, musuhnya adalah waktu henti, tenaga kerja, pengerjaan ulang, dan biaya material. Untuk bersaing secara global, kita harus menggunakan prinsip “ekonomi kekuatan” untuk memastikan pabrik kita berjalan dengan andal pada output maksimum dengan biaya total minimum. Strategi pemeliharaan dan keandalan terpadu untuk pabrik dan peralatan adalah bagian penting untuk mencapai tujuan ini.
Timothy White mempresentasikan artikel ini di konferensi Noria Corporation di Nashville, Tennessee. Untuk informasi lebih lanjut tentang konferensi dan acara pendidikan Noria, kunjungi conference.reliableplant.com.