Cara Menerapkan Rencana Pemeliharaan Produktif Total (TPM)
Implementasi Pemeliharaan Produktif Total yang berhasil dan berkelanjutan (juga dikenal sebagai TPM) harus menjadi perhatian utama bagi manajer pabrik atau pemimpin produksi yang teliti. TPM mengarah pada pengurangan waktu henti, lebih sedikit penghentian dan kerusakan, dan kemungkinan yang lebih kecil bahwa produk akan mengalami cacat kualitas selama proses manufaktur.
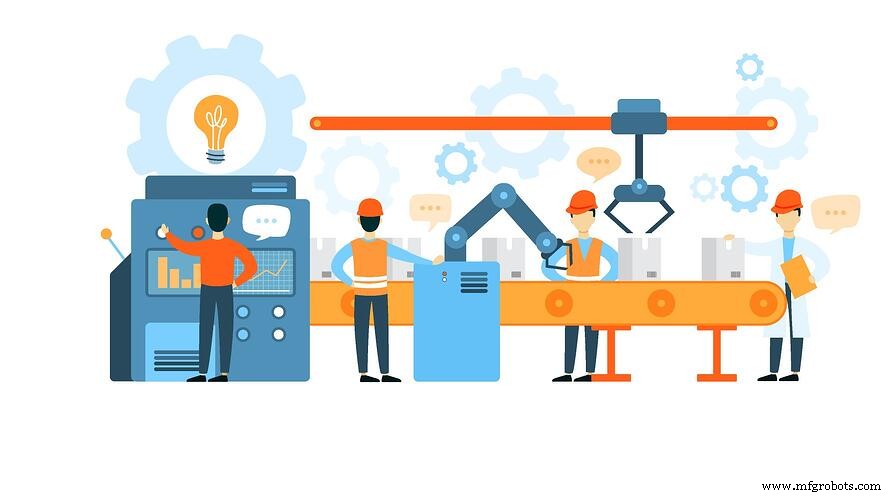
Mengapa TPM merupakan alat yang efektif? Singkatnya, karena operator yang diberdayakan yang berperan aktif dalam memeriksa dan memelihara peralatan mereka sendiri akan selalu berkontribusi pada peningkatan produksi dan keandalan peralatan.
Selama bertahun-tahun, penelitian telah mengkonfirmasi korelasi positif antara penerapan program TPM dan kinerja manufaktur secara keseluruhan. Beberapa temuan menunjukkan bahwa perusahaan dapat mengurangi produksi yang hilang sekitar 20% dengan melaksanakan rencana pemeliharaan produktif total. Namun, satu pertanyaan penting muncul:Bagaimana perusahaan dapat menerapkan TPM secara efektif ? Informasi berikut akan menjawab pertanyaan itu.
Tertarik menghemat uang untuk Biaya Pemeliharaan?
Anda dapat mengakses sumber daya dan makalah penelitian yang lebih berguna di sini.
Apa itu Pemeliharaan Produktif Total
Dengan cara meninjau, setiap program TPM melibatkan setidaknya 8 konsep inti yang memainkan peran besar dalam menentukan keberhasilan akhir dari inisiatif. 8 konsep tersebut adalah:
-
Pemeliharaan otomatis
Elemen dasar TPM ini berfokus pada pelatihan dan pemberdayaan personel perawatan seperti operator alat berat untuk melakukan manajemen perawatan rutin sendiri.
-
Peningkatan terfokus
Pilar TPM ini mengacu pada teknik pemeliharaan proaktif:memeriksa proses saat ini secara holistik, dan mengidentifikasi cara untuk memperbaikinya.
-
Pemeliharaan terencana
Program pemeliharaan terencana memanfaatkan data waktu henti historis dan analitik prediktif untuk menjadwalkan tugas pemeliharaan utama di sekitar kemungkinan tingkat kegagalan atau waktu menganggur yang diantisipasi.
-
Pemeliharaan kualitas
Proses pemeliharaan kualitas dirancang untuk memastikan bahwa tugas pemeliharaan aktual yang dilakukan secara efisien mencapai tujuan keseluruhan dari deteksi kesalahan, pencegahan cacat, dan jaminan kualitas.
-
Manajemen peralatan awal
Memanfaatkan umpan balik dari operator dengan pengalaman praktis, manajemen peralatan awal memastikan bahwa desain peralatan baru akan mengoptimalkan masa pakai, aksesibilitas, dan produktivitas alat berat.
-
Pelatihan
Setiap program TPM harus memasukkan unsur pelatihan dan pendidikan bagi operator dan manajer.
-
Keselamatan dan kesehatan
Semua proses TPM harus mempertimbangkan faktor keselamatan dan kesehatan untuk mendorong lingkungan kerja yang aman bagi operator dan karyawan lainnya.
-
Administrasi berorientasi TPM
Terlepas dari pertimbangan mekanis murni, program TPM yang dirancang dengan baik juga akan mempertimbangkan fungsi administratif seperti pemrosesan pesanan dan manajemen jadwal, serta mencari cara untuk meningkatkannya guna mendukung lantai produksi.
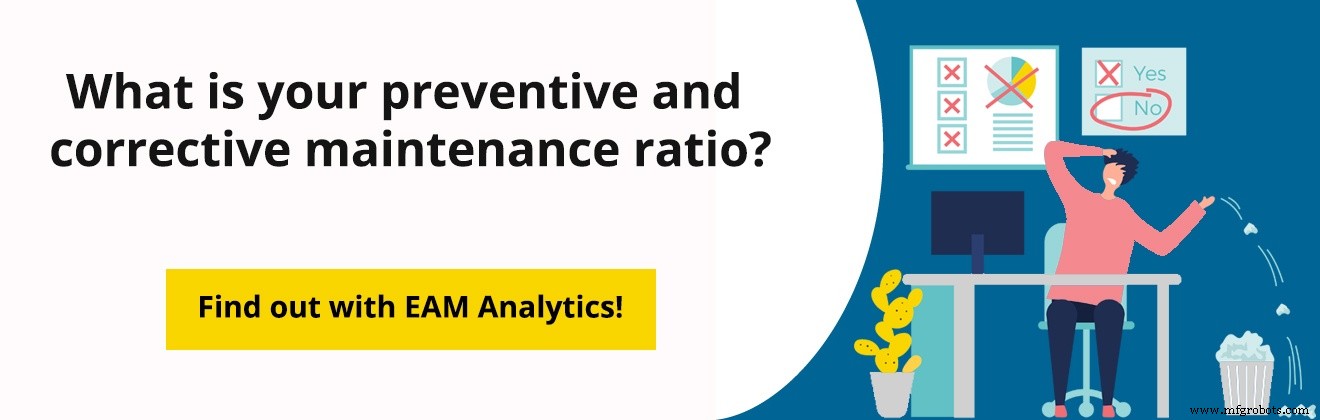
Cara Menerapkan TPM
Meskipun program TPM harus disesuaikan dengan kebutuhan dan keadaan perusahaan tertentu, ada 7 langkah-langkah dasar untuk menerapkan TPM, seperti yang tercantum di bawah ini:
1. Mengumumkan rencana implementasi TPM
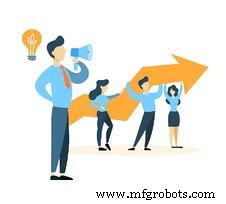
Program TPM yang sukses tidak akan pernah terwujud tanpa dukungan manajemen dari atas ke bawah. Dalam banyak kasus, manajemen harus mengatasi penolakan terhadap perubahan di pihak operator dan karyawan lain, dan skeptisisme terhadap manfaat TPM. Mengumumkan niat perusahaan Anda dengan jelas, dan kemudian secara teratur berbicara tentang manfaat penerapan TPM, dapat sangat membantu dalam mendobrak hambatan tersebut...
2. Identifikasi area untuk program percontohan TPM
Anda dapat berfokus pada peralatan yang paling mudah untuk diperbaiki, atau area produksi yang terbukti bermasalah, dan perlu diperbaiki untuk meningkatkan profitabilitas dengan cepat. Pada tahap awal proses TPM ini, identifikasi tujuan yang SMART:Specific, Measurable, Attainable, Realistic, dan Timed.
3. Fokus pada pemulihan peralatan yang ditargetkan ke kondisi kerja prima
Setelah area percontohan Anda diidentifikasi, catat standar dasar untuk produktivitas saat ini. Atur dan tentukan rencana Anda untuk
implementasi TPM . Gunakan metodologi 5S (Sort, Set, Shine, Standardize, Sustain). Fokus pertama pada pelaksanaan program pemeliharaan otonom, dan berikan pelatihan kepada operator peralatan sesuai kebutuhan. Sama seperti pemilik mobil yang dapat menghemat biaya perbaikan dalam jumlah yang signifikan dengan melakukan perawatan rutin dasar, demikian pula perusahaan dapat memperpanjang masa pakai alat berat dan mengidentifikasi masalah mekanis sejak dini dengan mengizinkan operator mereka untuk berpartisipasi secara teratur dalam prosedur perawatan dasar.
4. Mulai mengukur Efektivitas Peralatan Keseluruhan (OEE)
Bagaimanapun Anda memutuskan untuk melacak OEE, sangat penting bahwa waktu berhenti yang tidak direncanakan didokumentasikan, dan alasan diberikan untuk setiap kejadian. Berikan kategori untuk "penyebab tidak diketahui" atau "waktu berhenti yang tidak terisi" untuk kasus di mana operator tidak yakin dengan penyebab berhentinya. Seiring waktu, ini akan membantu Anda untuk
mengidentifikasi terlebih dahulu penyebab kerugian besar, yang pada gilirannya mengarah ke langkah #5:
5. Mengatasi Penyebab Kerugian Besar
Pada langkah ini, Anda harus menunjuk tim lintas fungsi yang terdiri dari sekitar 4 hingga 6 karyawan untuk menyelidiki satu penyebab utama waktu henti . Tim ini akan membuat rencana untuk menghilangkan penyebab kerugian, dan menjadwalkan waktu henti yang direncanakan untuk melaksanakan inisiatif ini. Misalnya, jika kerugian besar Anda berasal dari kemacetan pengisi yang sering terjadi, maka tim ini akan memeriksa proses operator saat ini dan opsi perbaikan, membuat rencana untuk menghentikan kemacetan, dan kemudian menjadwalkan waktu untuk menerapkan rencana tersebut. Setelah tindakan yang ditentukan selesai, mereka akan mengukur OEE ke depan, dan memulai kembali proses jika diperlukan.
6. Terapkan pemeliharaan proaktif
Pada langkah ini, fokus Anda adalah pada pencegahan kerusakan atau waktu berhenti. Identifikasi "titik nyeri" utama yang dapat menyebabkan kegagalan peralatan , dan buat jadwal pemeliharaan preventif secara berkala. Terakhir, lakukan proses umpan balik yang memungkinkan Anda untuk terus memantau efektivitas program Anda. Sistem umpan balik ini dapat mencakup log pemeliharaan, audit bulanan atau dua bulanan, dan kompilasi data dari termografi dan/atau analisis getaran.
7. Terapkan konsep TPM spesifik sesuai kebutuhan
Misalnya, manajemen peralatan awal harus berperan saat merancang dan/atau memasang mesin baru untuk lantai produksi. Mungkin desain peralatan baru harus dioptimalkan untuk memasukkan peningkatan aksesibilitas, prosedur pembersihan atau pelumasan yang lebih mudah, atau penambahan fitur keselamatan. Di sisi lain, jika ada masalah pengadaan atau keterlambatan dalam memproses perintah kerja, maka Anda harus mengatasi hambatan administratif ini sesegera mungkin.
Memanfaatkan TPM untuk Meningkatkan Manajemen Pemeliharaan
Pemeliharaan produktif total adalah elemen kunci untuk mengurangi kerugian produksi dari waktu henti. Program TPM yang efektif dapat memberdayakan karyawan untuk mengambil tindakan proaktif dalam pemeliharaan mesin vital; ini pada gilirannya akan memungkinkan peralatan produksi untuk menikmati umur fungsional yang lebih lama. Penerapan TPM juga akan membantu mengurangi cacat kualitas dan waktu pengoperasian yang kurang optimal.
Ada banyak alat yang tersedia di pasar, seperti platform Manajemen Aset Perusahaan dan program terkait, yang dapat membantu perusahaan dalam penerapan TPM. Dalam analisis akhir, sementara rencana pemeliharaan produktif total memerlukan beberapa upaya untuk desain dan pelaksanaan yang tepat, imbalan dari melakukannya sangat berharga untuk investasi!