Otomasi Pengelasan Nikel Menggunakan Robot
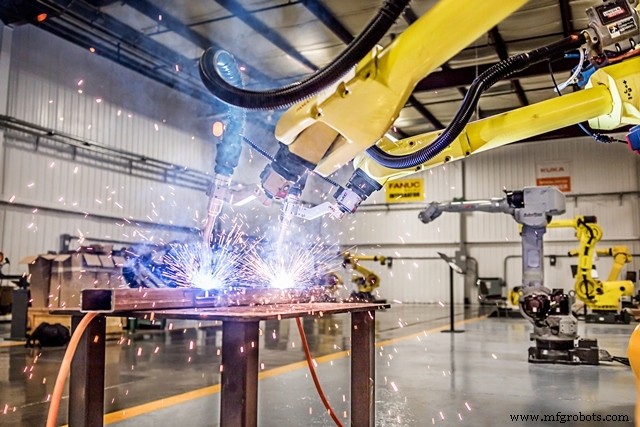
Paduan Nikel dan Kobalt:
Paduan dasar Nikel dan Kobalt adalah dua bahan las tahan panas yang sering dikelompokkan bersama karena digunakan untuk tujuan yang serupa. Dari tahan panas hingga tahan korosi, paduan dasar Nikel dan Kobalt, juga dikenal sebagai paduan super, adalah yang paling penting dari kelas tahan panas.
Paduan tahan panas adalah logam yang dikembangkan untuk tahan terhadap kondisi parah yang berlaku pada suhu tinggi di mana bahan lain yang lebih umum akan gagal.
Karakteristik apa yang diperlukan bahkan saat tidak mengelas bahan tahan panas?
- Ketahanan terhadap oksidasi dan penskalaan, sifat mekanik yang memadai, dan ketahanan pada suhu tinggi, baik untuk waktu singkat (kekuatan tarik panas) maupun waktu yang diperpanjang (ketahanan mulur).
- Stabilitas dengan waktu. Kondisi layanan yang parah yang memengaruhi material ini dapat menyebabkan perubahan struktur dan properti, dengan pembentukan retakan lebih lanjut.
- Daktilitas dan ketahanan terhadap serangan intergranular suhu tinggi (IGA) juga penting. Paduan tahan panas las tidak boleh menurunkan sifat ini.
Paduan Dasar Besi
Aplikasi penahan panas tidak dianggap sebagai baja karena perilakunya mirip dengan jenis material lainnya. Komposisinya kompleks dan mencakup persentase penting nikel dan kromium, dengan elemen lain yang ditambahkan untuk memberikan sifat khusus.
Paduan Dasar Nikel atau Kobalt
Bahan penahan panas lainnya termasuk paduan yang logam dasarnya adalah nikel atau kobalt, sedangkan komposisinya dimodifikasi dengan penambahan elemen lain yang berbeda untuk tujuan khusus.
Paduan logam dasar seperti di atas dengan berbagai unsur menghasilkan kelas bahan yang berbeda. Bahan yang menurunkan sifat-sifatnya secara eksklusif dari komposisinya dan tidak rentan terhadap perbaikan dengan perlakuan panas ditetapkan sebagai dikeraskan dengan larutan padat. Pengelasan bahan penahan panas dari jenis ini mudah dilakukan. Basis besi khas dari jenis ini disebut N-155 (atau Multimet). Basis Nikel yang umum adalah Inconel 600 dan Hastelloy X. Basis Kobalt yang umum adalah L-605 (atau HS-25) dan S-816.
Kelas lain, yang disebut dapat dikeraskan dengan proses larutan dan presipitasi (atau penuaan), merespons perlakuan panas karena reaksi halus yang mengubah struktur mikronya, terjadi saat pemanasan dan pendinginan. Basis Besi tipikal dari jenis ini adalah A-286 dan Incoloy 901. Basis Nikel tipikal adalah Waspaloy.
Kelas material yang berbeda, dengan sejumlah besar sifat yang sama dengan yang dibahas di atas, disebut paduan penahan korosi, yang dirancang untuk menahan serangan bahan kimia agresif, dengan atau tanpa pengaruh panas superposisi.
Ketika dianggap sebagai logam dasar, Nikel dan kobalt memiliki serangkaian sifat menarik yang membuatnya berguna untuk aplikasi suhu tinggi karena ketahanan panasnya, terutama untuk turbin gas, aksesori tungku, sistem pemrosesan bahan kimia panas, dan juga untuk aplikasi penahan korosi.
Pengelasan Paduan Penahan Panas
Sebagai aturan umum, pengelasan bahan penahan panas harus dilakukan dalam kondisi yang paling ulet, sering disebut sebagai kondisi anil atau dengan perlakuan larutan.
Nikel adalah elemen logam ulet yang digunakan untuk paduan baja dan baja tahan karat, dan dengan demikian itu memodifikasi sifat-sifat paduan yang terlibat. Sebagai logam dasar digunakan untuk ketahanannya yang luar biasa terhadap panas dan korosi. Secara khusus dapat mengembangkan ketahanan yang tinggi terhadap tekanan di bawah panas, baik dalam bentuk tuang atau tempa, saat paduan dan diperlakukan sesuai kebutuhan.
Bahan dasar nikel dipilih untuk ketahanan korosi dan sifat suhu tinggi, dengan perlakuan panas yang memadai. Meskipun tercakup dalam spesifikasi, mereka kebanyakan dikenal dengan nama komersial. Paduan yang dikeraskan dengan Solid Solution siap dilas dalam kondisi anil. Paduan presipitasi yang dapat dikeraskan dalam bentuk tempa dilas dalam kondisi yang diberi perlakuan larutan, diikuti dengan perlakuan panas sesuai kebutuhan. Dari nama paduan tempa yang dapat dilas, kami dapat mencantumkan beberapa di antaranya:Hastelloy B, C, C276, N, X, Inconel 600, 601, 625, Rene 41.
Kobalt juga merupakan logam ulet. Ini digunakan sebagai elemen paduan utama untuk berbagai pilihan bahan tujuan khusus. Sebagai logam dasar, yang dipadukan dengan elemen lain, sifat utamanya adalah kemampuan menahan oksidasi dan kerak pada suhu tinggi, meskipun hanya mengembangkan kekuatan terbatas pada suhu tinggi.
Bahan dasar kobalt memiliki komposisi yang agak berbeda tergantung pada apakah bahan tersebut dalam bentuk cor atau tempa. Beberapa paduan cor dikenal dengan nama berikut:HS 21, X 40 (Stellite 31), G 34, Mar M 509, dan FSX 414.
Paduan Tempa Umum Meliputi:S 816, L605 (HS 25), HS 188, Mar M 918, dan G 32 B. Semua ini memiliki sekitar 20% Kromium dan beberapa elemen pembentuk karbida seperti Niobium, Tantalum, Zirkonium, Vanadium. Kandungan karbon adalah 0,25-1,0% untuk paduan tuang dan 0,05-0,4% untuk paduan tempa.
Pengelasan
Semua proses pengelasan utama dapat diterapkan, tidak termasuk kemungkinan metode oxyacetylene yang tidak direkomendasikan karena penggunaan fluks menimbulkan komplikasi yang tidak ada pada teknik lain.
Pengelasan gesekan dapat digunakan untuk mengelas bahan tahan panas. Bagi mereka yang memperoleh sifat-sifatnya melalui pengerasan larutan dan presipitasi, seseorang harus menyadari pengaruh panas las pada sifat-sifat di sekitar sambungan. Jika hasil pengurangan kekuatan tidak dapat ditolak, tidak ada pertimbangan pembatas lainnya.
Pengelasan resistansi , spot dan jahitan banyak digunakan untuk pengelasan paduan tahan panas. Secara khusus, banyak item lembaran logam tahan panas, seperti liner pembakar, penahan api, dan banyak elemen lain dari mesin turbin gas modern dan bagian mesin kerja panas lainnya dilas dengan las titik dan jahitan sebagai prosedur produksi atau perbaikan, sama seperti yang dilakukan dengan yang lebih baru. baja tahan karat.
Perlu dicatat bahwa dalam banyak kasus, paduan tahan panas las busur dapat menghasilkan retak, terutama pada yang dikeraskan dengan larutan dan perlakuan panas presipitasi, selama pengelasan atau selama perlakuan panas:itulah sebabnya banyak perhatian harus diberikan untuk menghindari retak dengan mengembangkan prosedur yang sesuai. Semua proses las busur dapat digunakan, tetapi beberapa lebih cocok daripada yang lain tergantung pada ketebalan bahan.
Pengelasan Busur Tungsten Gas paduan tahan panas paling baik untuk bagian tipis. Merupakan praktik yang baik untuk memiliki perlengkapan yang menahan elemen yang dilengkapi dengan batang tembaga cadangan dengan lubang kecil yang berbatasan dengan alur di mana aliran tipis argon disediakan.
Komposisi logam pengisi untuk pengelasan paduan penahan panas harus kompatibel dengan logam dasar dan keuletan sedemikian rupa untuk memberikan kebebasan maksimum dari retak saat mempertimbangkan rasio pengenceran bahan pengisi terhadap logam dasar.
Sebelum mengelas paduan presipitasi tahan panas yang dapat dikeraskan, mereka harus dibebaskan dari semua tegangan pembentukan atau tekukan dengan proses perlakuan panas anil yang sesuai, mungkin dalam tungku vakum atau atmosfer terkontrol untuk mencegah oksidasi. Jika perlu, perawatan larutan ulang dan pengendapan (penuaan) harus segera mengikuti pengelasan. Pengelasan Busur Logam Terlindung terkadang digunakan untuk paduan tahan panas yang diperkuat dengan larutan padat, tetapi tidak digunakan untuk larutan dan yang mengeras dengan presipitasi.
Mengontrol Cacat
Cacat yang mungkin muncul pada paduan penahan panas jenis ini, porositas dikontrol dengan pembersihan yang tepat sebelum pengelasan dan menghilangkan kontaminasi permukaan. Membersihkan benda kerja dan logam pengisi sebelum mengelas paduan tahan panas sangat penting. Retakan jenis apa pun, pada las atau pada logam dasar tidak pernah diperbolehkan. Desain sambungan harus menghindari konsentrasi tegangan dan tegangan multiaksial. Input panas tinggi yang menghasilkan tegangan susut sisa yang besar juga dapat menjadi penyebab retakan.
Pengelasan energi tinggi dari paduan penahan panas menghadirkan berbagai tingkat kemampuan las tergantung pada ukuran pengekangan yang dialami bagian-bagian selama pengelasan. Bahkan paduan cor nikel, yang biasanya menunjukkan kemampuan las yang sangat rendah, dapat dilas dengan berkas elektron untuk aplikasi yang tidak menuntut.
Jika Anda tertarik untuk mengotomatiskan aplikasi pengelasan nikel atau kobalt, hubungi staf kami di 877-762-6881 atau isi formulir kontak dan teknisi kami dapat menentukan opsi terbaik untuk kebutuhan proses Anda.