Studi Kasus Keandalan Pabrik Farmasi
Profesional perawatan dan keandalan dapat membuat perbedaan. Di sebagian besar pabrik, itu berarti pekerjaan terfokus yang memungkinkan operasi mendapatkan lebih banyak produk jadi (apakah itu minuman ringan, sepeda motor, bola lampu, mobil, kue mangkuk, pemanas air, dll.) keluar dari pintu.
Di pabrik biosintetik human insulin (BHI) milik Eli Lilly di Indianapolis, membuat perbedaan memiliki arti penting tambahan.
Kelompok teknik keandalan pabrik Eli Lilly BHI termasuk (dari kiri) insinyur keandalan senior Vadim Redchanskiy, keandalan teknisi teknik Mary Ann Dust, pemimpin tim pemeliharaan dan keandalan Ken Swank, dan insinyur keandalan senior Mark Lafever.
Hampir 21 juta orang di Amerika – dan 200 juta orang di seluruh dunia – menderita diabetes. Di AS saja, hampir 1 juta kasus baru didiagnosis setiap tahun. Banyak penderita diabetes membutuhkan insulin untuk mengontrol gula darah (glukosa), dan tanaman BHI membantu memenuhi kebutuhan itu. Dibuka untuk produksi pada tahun 1992, situs ini menghasilkan persentase yang signifikan dari insulin obat dunia. Pekerjaan pemeliharaan dan keandalan yang meningkatkan produktivitas memungkinkan perusahaan mendapatkan obat penopang kehidupan berkualitas tinggi di tangan mereka yang membutuhkannya.
Eli Lilly telah memproduksi insulin obat selama lebih dari 80 tahun.
Baik Anda bekerja untuk perusahaan yang membuat keripik komputer atau keripik kentang, ketika Anda memberi nilai tambah kepada pemangku kepentingan atau ekonomi, itu tidak dapat diremehkan dengan cara apa pun, ”kata Ken Swank, pemimpin tim pemeliharaan dan keandalan pabrik. “Tidak masalah apa yang kamu lakukan. Ini penting. Namun, ada satu perbedaan yang jelas. Saya pernah bekerja di perusahaan pelapis industri. Pelapis kami digunakan untuk segala hal mulai dari bola golf hingga Pesawat Ulang-alik hingga instrumen bedah. Ketika saya melihat produk akhirnya, saya tahu saya adalah bagian dari itu. Tapi ketika Anda bekerja untuk sebuah perusahaan farmasi. . . itu sangat berarti pada tingkat pribadi.
Saya bertemu pasangan selama akhir pekan yang memiliki seorang putra yang masih kecil. Kami harus berbicara dan saya menemukan anak itu menderita diabetes. Saya bertanya apakah dia memiliki Tipe 1 atau Tipe 2. Ayah bertanya, bagaimana Anda tahu banyak tentang diabetes? Anak laki-laki itu memberi tahu saya bahwa dia adalah Tipe 1. Saya menatapnya dan berkata, 'Coba tebak, apa yang saya lakukan untuk mencari nafkah? Saya membuat insulin. Saya bekerja di Eli Lilly dan membuat Humulin.’ Dia berkata, ‘Terima kasih. Saya sangat suka obat saya. Itu membuatku merasa jauh lebih baik.’
“Departemen saya bertugas memastikan gedung ini membuat obat yang seharusnya dibuat setiap saat. Ada jutaan orang yang bergantung padanya dan meraihnya setiap hari.”
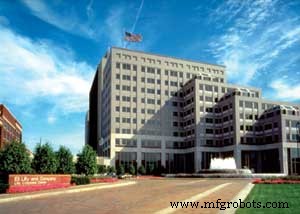
Kampus Indianapolis perusahaan berisi
lokasi manufaktur dan kantor perusahaan.
Meningkatnya Permintaan
Pabrik BHI berukuran besar dan secara teknis rumit. Ini menampung lebih dari 17.000 peralatan, 13.000 titik input/output dan 600 unit operasi. Metode pemrosesan untuk menghasilkan molekul BHI melibatkan beberapa langkah sentrifugasi, beberapa reaksi, banyak langkah pemurnian, dan berbagai langkah pertukaran pelarut. Akibatnya, sekitar sepertiga unit operasi diklasifikasikan sebagai operasi berisiko tinggi atau kritis terhadap keselamatan.
Beberapa tahun yang lalu, pemimpin pemeliharaan dan keandalan memutuskan perlunya melakukan perubahan substansial untuk memaksimalkan waktu, keterampilan, sumber daya, dan potensi dampak departemen pada pabrik. BHI berjalan lebih dari dua kali kapasitas desain aslinya, dan permintaan bisnis terus meningkat. Teknisi terlalu berkomitmen, upaya remediasi sering diprioritaskan untuk memenuhi kebutuhan saat itu, dan sistem penting tidak mendapatkan persentase perhatian yang adil.
Eli Lilly memproduksi 25 persen pasokan insulin dunia.
Kami tidak pernah khawatir tentang peralatan kami yang beroperasi dalam kondisi yang memenuhi syarat, ”kata Swank. “Tetapi seperti industri farmasi lainnya pada waktu itu, kami tidak memberikan penekanan ekstra pada peralatan kami, selain itu kami selalu menginginkan waktu kerja paling banyak yang bisa kami dapatkan untuk membuat obat sebanyak-banyaknya. Tetapi ketika Anda melihat untuk mengeluarkan sebanyak mungkin kilo dari pintu, kami sampai pada titik di mana Anda bertanya, 'Apakah kami terus menambah fasilitas atau melakukannya dengan cerdas dari perspektif bisnis dan fokus pada keandalan?'”
Itu adalah sesuatu yang direnungkan oleh sejumlah fasilitas Eli Lilly di akhir 1990-an. Misalnya, manajer teknik BHI Ron Reimer memimpin upaya untuk meningkatkan kerja proaktif dan waktu aktif serta mengurangi biaya pemeliharaan saat berada di lokasi Laboratorium Clinton (Ind.) perusahaan. Sebagai bagian dari proyek tersebut, yang kemudian disistematisasikan dan diberi nama Proactive Asset Management, ia mempekerjakan insinyur keandalan pertama perusahaan tersebut.
Keterlibatan langsung dari semua pemangku kepentingan utama dalam keandalan pabrik
(produksi, HSE, kontrol kualitas, keuangan, teknik, dan
manajemen) membantu memastikan keberhasilan inisiatif prioritas
keandalan. Upaya peningkatan BHI dimulai dengan penambahan insinyur keandalan pada tahun 1999, dan pengenalan proyek Reliability-Centered Maintenance (RCM) dan root cause failure analysis (RCFA). Upaya tersebut meningkat ketika badan pengatur seperti Food and Drug Administration dan Badan Perlindungan Lingkungan mulai meneliti pemeliharaan di industri farmasi. Pesan agensi sederhana:pemeliharaan sama dengan keandalan pabrik; keandalan pabrik sama dengan keandalan produk; dan keandalan keseluruhan sama dengan kepatuhan. Perusahaan yang “tidak dapat diandalkan” dapat menghadapi hukuman, termasuk penutupan operasi.
Pentingnya komunikasi
Menurut pemimpin tim pemeliharaan dan keandalan Ken Swank, komunikasi memainkan peran utama dalam keberhasilan inisiatif prioritas keandalan pabrik BHI.
“Komunikasi adalah salah satu bagian terpenting dari pekerjaan saya,” katanya. “Saya sering bertemu dengan para pemimpin produksi dan menjelaskan kepada mereka apa yang akan terjadi. Saya mendapatkan komitmen mereka dan membantu mereka memahami nilai yang ditambahkannya. Mereka juga harus mengumpulkan beberapa sumber daya. Analisis yang tepat bukan hanya departemen kami, tentu saja. Ini melibatkan teknik, pemeliharaan, keandalan, operasi, layanan teknis, otomatisasi di kali. Kami menghabiskan banyak waktu untuk memastikan bahwa mereka benar-benar memahami nilainya.
Saya harus melakukan banyak tarian dan nyanyian untuk membantu mereka memahami. Tapi dari semua akun, pembeliannya bagus.”
"Saat itulah, menurut saya, keandalan mulai menjadi fokus saat ini," kata Swank. "Dalam perjalanan kami untuk menjadi pabrik yang benar-benar andal, visinya adalah ketika produksi menggunakan sepotong peralatan, itu dalam kondisi yang memenuhi syarat, tersedia saat mereka membutuhkannya dan itu akan berjalan pada tingkat kinerja yang telah ditentukan. Kami jelas memainkan peran besar dalam hal itu. Strategi pemeliharaan yang kami susun berhubungan dengan menjaga peralatan itu di kondisi yang memenuhi syarat. Juga, kedalaman strategi pemeliharaan membahas pemanfaatan atau waktu kerja yang diperlukan. Ada operasi di fasilitas yang berjalan lebih dari yang lain, memiliki redundansi lebih sedikit daripada yang lain atau lebih penting daripada yang lain. Itu memerlukan perhatian lebih dan penyelidikan lebih rinci .”
Inisiatif penentuan prioritas yang dimulai pada awal 2004 telah menjadi inti dalam strategi ini untuk memberikan waktu kerja dan keandalan ke unit operasi yang paling membutuhkan perhatian.
Bagaimana Eli Lilly mendefinisikan peran keandalan
Menurut pemimpin pemeliharaan dan keandalan BHI Eli Lilly, fungsi pekerjaan dan tanggung jawab teknisi keandalan mereka meliputi:
- Meminimalkan kegagalan peralatan melalui RCFA, FMEA, analisis RCM, investigasi penyimpangan timbal, dll.
- Kembangkan metrik untuk mengoptimalkan upaya keandalan dan sumber daya.
- Rencana pemeliharaan sendiri (tinjau/hasilkan/setujui) untuk peralatan baru dan yang sudah ada.
- Hadirkan proyek yang berfokus pada keandalan yang berdampak luas pada aliran.
- Fokuskan praktik bisnis seputar pemeliharaan dan keandalan untuk meningkatkan ketersediaan peralatan.
- Mentor teknisi keandalan.
- Berintegrasi dengan tim ruang kontrol untuk mendukung bisnis mereka secara efektif.
- Cari dan terapkan teknologi baru untuk meningkatkan kinerja dan ketersediaan peralatan.
Fungsi pekerjaan dan tanggung jawab teknisi keandalan meliputi:
- Mendukung inisiatif situs.
- Lengkapi dan proses formulir entri data CMMS.
- Bantu insinyur keandalan dengan RCFA, penambangan data, FMEA, RCM, penyimpangan, kontrol perubahan, verifikasi lapangan, peningkatan data CMMS, dll.
- Proyek khusus – mendukung upaya keandalan, dll.
Jadikan Prioritas
Swank menceritakan perintah berbaris yang pada akhirnya akan mengarah pada pemulihan keandalan.
“Bos saya saat itu berkata, 'Cari tahu bagaimana kita akan membuat fasilitas BHI lebih andal. Kita perlu menangani ini,'” kata Swank. “Apa yang sebenarnya ingin dia katakan adalah, 'Anda dan tim Anda perlu memahami kebutuhan bisnis dari fasilitas tersebut, menentukan metode untuk menetapkan jalur ke depan untuk memulihkan kesenjangan keandalan yang diprioritaskan dengan benar, menjualnya ke bisnis, menjalankannya, dan membuat itu berkelanjutan.”
Kedengarannya cukup mudah, atau begitulah menurutnya.
“Kami mulai pada Februari (2004) dan berasumsi kami akan selesai pada Maret atau April,” katanya. “Kami segera menyadari bahwa ini lebih terlibat dan kompleks daripada yang kami perkirakan. Selain itu, kami ingin melakukannya dengan benar.”
Rencana permainannya adalah mengembangkan analisis yang menggunakan data yang ada untuk memprioritaskan perbaikan sistem sebagai upaya peningkatan berkelanjutan di luar upaya dukungan harian departemen. Persyaratan analisisnya adalah:
- sistem akan mengidentifikasi dan memeringkatnya berdasarkan dampak bisnis berdasarkan data;
- semua pemangku kepentingan akan terwakili;
- analisis dapat dilakukan dalam waktu kurang dari satu minggu kerja (40 jam).
Tantangan ini ditempatkan di pundak bagian rekayasa keandalan departemen. Kelompok tersebut termasuk insinyur keandalan senior Mark Lafever, Vadim Redchanskiy dan Rod Matasovsky (sekarang sudah pensiun), dan teknisi teknik keandalan David Doyle, Mary Ann Dust, dan Matt O'Dell. Mereka mulai menyusun strategi konten analisis.
“Mereka adalah orang-orang pintar. Saya adalah penerjemah dari manajemen ke orang-orang di lantai, ”kata Swank. “Mereka memahami sistem data, dan apa yang masuk akal dan apa yang tidak.”
Kelompok tersebut mengakui bahwa untuk mendapatkan dukungan bagi prakarsa ini, analisis harus didasarkan pada fakta dan kebutuhan untuk melibatkan secara langsung dan bermakna bagi semua pemangku kepentingan utama dalam keandalan pabrik – produksi; kesehatan, keselamatan dan lingkungan (HSE); kontrol kualitas (QC); keuangan; rekayasa; dan manajemen. Ini akan menjadi tindakan penyeimbang yang luar biasa.
“Siapa pun dapat keluar dan menarik banyak data,” kata Lafever. “Kami harus memutuskan dari mana kami akan menarik data, bagaimana kami akan mengambilnya, dan mencari tahu apakah data tersebut akan memberi tahu kami informasi yang kami butuhkan untuk membuat keputusan yang tepat.”
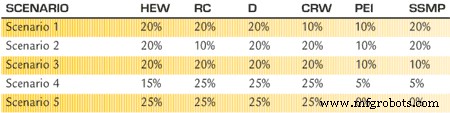
Tabel 1. Ringkasan bobot untuk lima skenario.
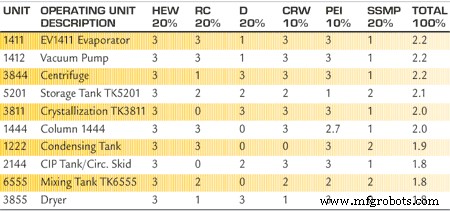
Tabel 2. Contoh dari analisis sensitivitas skenario pertama.
Setelah beberapa iterasi – dan “banyak menggosok kepala,” kata Lafever – tim menyelesaikan analisis yang mempertimbangkan pemangku kepentingan dengan menggunakan data yang ada dari 12 bulan terakhir. Data ini mencakup:
1) Jam Kerja Darurat, disamakan dengan waktu henti peralatan, untuk memenuhi produksi. Ini dikumpulkan dari sistem manajemen pemeliharaan terkomputerisasi pabrik, yang melacak semua jam yang dibebankan pada setiap unit operasi. Pekerjaan darurat didefinisikan sebagai "pekerjaan yang tidak bisa menunggu." Meskipun bukan pengukuran tradisional waktu henti sistem, hal ini berkorelasi langsung dengan jumlah gangguan produksi yang dirasakan saat sistem tidak berfungsi dengan baik.
2) Klasifikasi Risiko, per Lilly's Globally Integrated Process Safety Management (GIPSM), untuk memenuhi HSE. Sistem klasifikasi memiliki empat kemungkinan:operasi kritis keselamatan, faktor risiko teratas; risiko tinggi, yang melibatkan risiko lingkungan, kesehatan dan kebakaran yang cukup besar; integritas mekanik, yang ditentukan oleh Administrasi Keselamatan dan Kesehatan Kerja; dan tidak ada risiko atau “tidak satu pun di atas”.
3) Jumlah Penyimpangan pada Proses yang disebabkan oleh kegagalan peralatan untuk memenuhi QC. Penyimpangan yang ditargetkan ini merupakan hasil dari masalah keandalan peralatan, bukan kesalahan operator atau masalah non-peralatan lainnya. Jumlah penyimpangan diperhitungkan bersama dengan tingkat (1, 2 atau 3) yang menunjukkan dampak penyimpangan terhadap kualitas produk.
4) Biaya Pekerjaan Reaktif untuk memenuhi keuangan. Ini sekali lagi diambil dari CMMS, yang melacak semua biaya anggaran terhadap unit operasi. Biaya ini mencakup semua suku cadang dan tenaga kerja yang terkait dengan pekerjaan reaktif yang dilakukan pada sistem.
5) Proses Input Engineer untuk memenuhi engineering. Insinyur proses yang bertanggung jawab untuk setiap sistem disurvei tentang topik-topik seperti usia sistem, jam waktu henti potensial yang dihasilkan oleh kegagalan sistem, dan dampak peraturan.
6) Status Rencana Pemeliharaan Sistem, juga untuk memenuhi rekayasa. Ini dibuat untuk memasukkan empat level:Level 1, tidak ada perawatan rutin yang dilakukan, yang dianggap paling parah; Level 2, ada pemeliharaan preventif pada sistem; Level 3, Evaluasi Kualifikasi Berkala (PQEs), yang dirancang untuk memastikan sistem dalam status kualifikasi yang konstan dan layak digunakan, dijalankan; dan, Level 4, analisis berbasis RCM digunakan pada sistem untuk menghasilkan rencana pemeliharaan.
Data ini menciptakan evaluasi “peralatan penting” yang mengamati 420 unit operasi dan mengidentifikasi unit-unit yang berpotensi menghentikan produksi atau menyebabkan insiden yang dapat dilaporkan oleh OSHA atau EPA.
“Cara struktur kami diatur di CMMS kami, dan cara kami mengontrol basis data insiden kami, unit operasi adalah cara terbaik untuk melakukannya,” kata Lafever. “Terkadang, unit operasi adalah bagian dari peralatan. Sebagian besar waktu, itu adalah peralatan utama, ditambah lebih banyak lagi.”
Misalnya, Redchanskiy mengatakan bahwa unit operasi EV1411 (proses penguapan) mencakup “50 hingga 60 peralatan dan instrumentasi, seperti katup, penukar panas, dan pompa”.
Evaluasi tersebut memangkas daftar awal 70 persen, dari 420 unit operasi menjadi 135.
Fakta tidak berbohong
Saat menentukan pentingnya unit operasi tertentu, sulit untuk membantah faktanya.
“Sebelum kami melakukan analisis ini, semua yang dibicarakan produksi hanyalah sentrifugal pada ujung depan,” kata pemimpin tim pemeliharaan dan keandalan Eli Lilly, Ken Swank. “Setelah analisis dan menunjukkan kepada mereka apa yang kami dapatkan – saya menunjukkan bahwa centrifuge berada di peringkat ke-63 (dalam daftar 135 unit operasi) – mereka tidak banyak bertanya tentang hal itu.
“Ini juga membuat kami mencari di luar definisi peralatan produksi. Sebelum analisis, orang lupa memasukkan tangki limbah, penangan udara, dll. Mereka tidak memikirkan Tank 1099 di Ruang Kontrol 2, di mana semua saluran pembuangan lantai mengalir. Siram melewati saluran pembuangan dan masuk ke tangki. Jika tangki itu tidak beroperasi, kami harus menghentikan langkah pemurnian kami.”
Berat dan Ukuran
Untuk memastikan prioritas yang tepat dari 135 unit yang tersisa, grup memutuskan untuk menerapkan pembobotan pada setiap sumber data dan melakukan beberapa analisis sensitivitas.
“Kami tidak merasa bahwa keenam kriteria tersebut memiliki bobot yang sama,” kata Swank. “Kami merasa bahwa keselamatan dan kualitas memiliki dampak yang lebih tinggi daripada, katakanlah, jumlah uang yang kami keluarkan untuk pekerjaan darurat.”
Sistem penilaian (nol hingga 3, dengan nol sebagai dampak dan tingkat keparahan paling kecil dan 3 sebagai dampak dan tingkat keparahan paling besar) dikembangkan untuk setiap kumpulan data dan diterapkan ke setiap unit operasi. Rinciannya adalah sebagai berikut:
Jam Kerja Darurat (HEW) :kurang dari 15 jam (skor nol), 15 sampai kurang dari 25 jam (satu), 25 sampai kurang dari 40 jam (dua) dan 40 jam atau lebih (tiga).
Klasifikasi Risiko (RC) :tidak ada risiko K3L (nol), sistem integritas mekanis (satu), proses berisiko tinggi (dua) dan operasi kritis keselamatan (tiga).
Penyimpangan (D) :Dilakukan empat pengelompokan dengan memperhatikan tingkat dan jumlah penyimpangan. Ditentukan bahwa penyimpangan Tingkat 2 sama dengan tiga kali penyimpangan Tingkat 1 dan penyimpangan Tingkat 3 sama dengan dua kali penyimpangan Tingkat 2. Ini membuat penyimpangan Level 1 bernilai satu poin, penyimpangan Level 2 bernilai tiga poin dan penyimpangan Level 3 bernilai enam poin. Ini diterapkan pada setiap penyimpangan. Hasilnya adalah:dua atau kurang (nol), lebih besar dari dua sampai lima (satu), lebih besar dari lima sampai delapan (dua) dan lebih besar dari delapan (tiga).
Biaya pekerjaan reaktif (CRW) :kurang dari $5.000 (nol), $5.000 hingga kurang dari $7.499 (satu), $7.500 hingga $14.999 (dua) dan $15.000 atau lebih besar (tiga).
Input Insinyur Proses (PEI) :sistem dampak minimal (nol) dan meningkat hingga sistem dampak maksimum (tiga).
Rencana Pemeliharaan Sistem (SSMP) :Analisis RCM dilakukan pada sistem (nol), PQE dijalankan secara rutin (satu), dilakukan PM (dua) dan tidak dilakukan pemeliharaan rutin (tiga).
Skor diterapkan pada 135 unit operasi. Informasi tersebut kemudian dimuat ke dalam spreadsheet dan berbagai bobot diterapkan untuk menekankan pentingnya berbagai kumpulan data. Proyek analisis sensitivitas mencakup lima skenario pembobotan yang berbeda untuk memastikan satu titik data tidak mendorong penentuan prioritas sistem.
Skenario bervariasi dari distribusi bobot yang cukup merata (HEW, HSE, D dan SSMP, masing-masing 20 persen; CRW dan PEI, masing-masing 10 persen) hingga penghapusan dua kategori (HEW, HSE, D dan CRW, masing-masing 20 persen; PEI dan SSMP, nol persen). Dalam skenario terakhir, kumpulan data yang tersisa adalah "data sebenarnya" yang berubah sesuai dengan tingkat keandalan yang ditunjukkan oleh sistem. Skenarionya ditunjukkan pada Tabel 1.
Setiap skenario dalam analisis sensitivitas mengambil faktor risiko dan dikalikan dengan bobot skenario tertentu. Produk dari setiap kategori dijumlahkan untuk setiap unit operasi. Tabel 2 menunjukkan contoh dari skenario pertama.
Ketika kelima skenario selesai, skor akhir untuk unit operasi dibuat grafik dan diperiksa oleh tim keandalan. Sebelum menentukan peringkat akhir dan rencana remediasi, faktor tambahan dipertimbangkan. Apakah unit yang dimaksud baru saja diganti, atau apakah penggantian dalam rencana modal? Apakah rencana remediasi untuk unit ini dapat diterapkan ke unit lain? Gugus fungsi apa yang dibutuhkan untuk remediasi ini, dan apakah tersedia? Kegiatan remediasi apa yang telah dilakukan di masa lalu?
“Misalnya, salah satu sentrifugal muncul di dekat bagian atas daftar, tetapi kami tahu situs lain melakukan RCM pada sistem yang sangat mirip,” kata Swank. “Kami tidak perlu menduplikasi upaya.”
Daftar akhir kegiatan remediasi yang diusulkan bervariasi, tergantung pada unit operasi, dari analisis RCM mendalam hingga tidak meremediasi sistem sama sekali.
Pada saat itu, tim tahu bahwa mereka memiliki rencana yang komprehensif.
“Itu adalah penggilingan,” kata Lafever. “Kami datang dengan rencana tiga kali – rasanya seperti 30 – dan kami terus berkata, 'Ini tidak cukup baik.' 'Bagaimana perasaan kontrol kualitas tentang ini?' 'Bagaimana perasaan rekayasa proses tentang ini?' Kami sangat bingung. Kami harus memastikan bahwa kami menjawab semua aspek dan semua pertanyaan potensial.”
Swank menambahkan, “Tusukan pertama seperti, 'Wow, ini bahkan tidak dekat.' Menjadi jelas mengapa hal itu tidak dilakukan sebelumnya. Ini banyak pekerjaan. Ada juga hal-hal sehari-hari yang membuat Anda menjauh dari sesuatu seperti ini. Tetapi kami mengatakan kepada diri kami sendiri bahwa kami akan tetap melakukannya dan menyelesaikannya.”
Secara Tertulis
Pada 21 September 2004, Swank secara resmi mempresentasikan model prioritas kepada tim utama pabrik, yang mencakup kepala lokasi dan semua manajer fungsional. Tujuh bulan kerja yang melelahkan terbayar.
“Tidak ada barter atau diskusi bolak-balik,” katanya. "Mereka seperti, 'Ini bagus. Lanjutkan.’”
Tentu saja, anggukan kepala dan lambaian tangan hanya sebatas itu. Jadi, Swank meminta Lafever membuat laporan yang merangkum proses evaluasi dan merinci bagaimana analisis peralatan penting akan dilakukan dari tahun ke tahun. Laporan ini akan berfungsi sebagai template untuk evaluasi di masa mendatang.
“Saya menyuruh anggota tim utama untuk menandatanganinya,” kata Swank. "Mereka lakukan. Saya memilikinya secara tertulis. Tidak ada keraguan. Itu menunjukkan kepada Anda bahwa analisis yang kami lakukan benar-benar kuat.”
Pada tanggal 28 Februari 2005, analisis peralatan penting diformalkan dan disetujui oleh tim utama, dan kegiatan remediasi untuk unit operasi pabrik yang paling vital dimasukkan dalam rencana bisnis pabrik tahun 2005 dan 2006.
Template telah membuat evaluasi selanjutnya hampir mulus.
“Tahun lalu, sangat mudah untuk melakukan analisis,” kata Lafever.
Rencana 2006 selesai pada bulan Mei.
Hasil Pengobatan
Pemimpin departemen pemeliharaan dan keandalan di pabrik Eli Lilly ini mengatakan bahwa mereka saat ini tidak dapat mengukur dampak bottom-line, dolar dan sen dari inisiatif prioritas keandalan.
“Bagian yang disayangkan adalah kami tidak selalu melihat hasil kerja kami dari tahun ke tahun,” kata Lafever. “Mungkin ada penundaan satu tahun karena butuh waktu untuk mengerjakan sistem.”
Namun bukan berarti tidak ada manfaat dan hasil.
Redchanskiy dan Doyle mengatakan ada penghematan biaya yang tak terhindarkan hanya dengan mengevaluasi kembali bagaimana pemeliharaan dilakukan pada aset tertentu.
“Dalam analisis, kami menemukan bahwa kami menghabiskan banyak uang untuk beberapa sistem yang tidak memiliki pekerjaan reaktif,” kata Redchanskiy. “Kami menghabiskan banyak uang untuk pemeliharaan preventif. Kami melakukannya secara berlebihan di PM. Kami mengubah cara kami melakukan pemeliharaan pada sistem tersebut.”
“Pergeseran terbesar dari ini adalah bahwa untuk beberapa sistem, orang sekarang dapat mengatakan bahwa sebenarnya boleh saja mengalami kegagalan,” kata Doyle. “Jika itu adalah diagnosis dan rencana kami untuk sistem khusus itu, tidak apa-apa. Itu filosofi yang sangat berbeda bagi kami.”
Swank mengatakan hal positif dapat diambil dari tingkat produktivitas pabrik.
“Fakta bahwa kami telah memenuhi tingkat inventaris kami, dan fakta bahwa model bisnis kami bergerak menuju produktivitas yang lebih tinggi, menunjukkan bahwa kami telah mencapai tonggak utama pertama kami,” katanya.
Lafever percaya bahwa keterlibatan dengan proyek remediasi telah menghasilkan peningkatan pengetahuan teknis dan peningkatan waktu kerja.
“Ketika sebagian besar orang pemeliharaan dan operasi keluar dari analisis RCM, mereka dapat diklasifikasikan sebagai ahli dalam sistem itu,” katanya. “Setiap orang memiliki pemahaman yang lebih baik tentang fungsi individu kelompok dan bagaimana mereka bekerja sama untuk melakukan bagian mereka dalam memperbaiki peralatan atau mengidentifikasi ketika ada masalah dengan peralatan. Interaksi itu sendiri, menurut saya, mengurangi jumlah pekerjaan darurat yang berkembang.”
Indikator kesuksesan terbaik?
“Itu membuat manajemen atas kami senang,” kata Doyle.
“Dan itu membuatku bahagia,” kata Swank.
Semua perbaikan ini dapat menjelaskan mengapa BHI menerima Penghargaan Making Medicine 2005, yang diberikan kepada pabrik Eli Lilly yang “paling memenuhi kebutuhan bisnis dan mewujudkan seperti apa seharusnya manufaktur di perusahaan”.
Pabrik Lilly lainnya mencatat inisiatif prioritas dan sedang memeriksa kelayakan adopsi. Hal ini telah meningkatkan visibilitas di seluruh perusahaan untuk pemeliharaan dan keandalan.
“Bagian dari kebaikannya adalah pemahaman dan kesadaran perusahaan akan nilai yang ditambahkan oleh pemeliharaan,” kata Reimer. “Ini adalah sesuatu yang pasti ingin kami manfaatkan.”
Tim ini menunjukkan setiap hari bahwa profesional pemeliharaan dan keandalan dapat dan memang membuat perbedaan.