Program Keandalan dan Ramping Pembangkit Listrik Tenaga Baterai Energizer
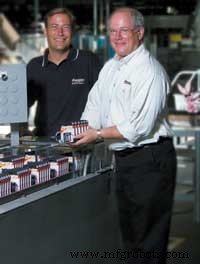
Direktur perusahaan lean global
Steve Hockridge (kiri) dan koordinator lean
Dana Billings telah melihat manfaat dari
menyatukan lean dan keandalan.
Ada tiga jenis perusahaan manufaktur yang menerapkan lean:
-
Mereka yang melakukannya atas nama hanya untuk memuaskan atau menarik investor. Lean terbatas pada status kata kunci dalam laporan tahunan dan iklan.
-
Mereka yang melakukannya di permukaan. Mereka membangun beberapa sel berbentuk U, mengecat dinding dan membuang beberapa barang yang berantakan, lalu berseru, “Itu dia; kami kurus.” Lean adalah proyek “perbaikan rumah” untuk pabrik.
-
Mereka yang melakukannya dengan benar.
Hanya sedikit yang termasuk dalam kategori ketiga itu. Sebuah laporan baru-baru ini dari QAD Inc. menemukan 80 persen perusahaan yang disurvei mengatakan bahwa mereka saat ini memiliki "inisiatif lean", tetapi hanya 1 persen yang telah mendokumentasikan praktik lean. Tidak cukup banyak pemimpin pabrik dan perusahaan yang membawa lean manufacturing melampaui level permukaan.
Tidak cukup untuk melihat lebih dalam dan melihatnya sebagai alat yang berharga untuk peningkatan keandalan mesin dan peningkatan kemampuan dan kinerja total aset. Aset mekanis yang kuat dan efisien adalah prasyarat yang meletakkan dasar bagi elemen dasar lean seperti aliran dan fleksibilitas.
Mengakui kehandalan sebagai bagian penting dari transformasi lean memungkinkan perusahaan untuk mencapai tujuan yang mencapai tujuan dengan lebih baik – mengurangi inventaris, biaya, waktu pengerjaan dan pekerjaan yang sedang berjalan, serta peningkatan kualitas, waktu kerja, dan produktivitas.
Energizer, perusahaan manufaktur baterai terbesar di dunia, dapat menghitung sendiri bahwa 1 persen perusahaan melakukan lean dengan cara yang benar. Dalam waktu singkat, ia telah mencapai hasil yang luar biasa melalui aktivitas terfokus yang mendorong orang, proses, dan kinerja produksi.
Setiap hari, Energizer berupaya meningkatkan dengan menyatukan lean dan keandalan. Sama seperti cinta dan pernikahan, orang-orangnya tahu bahwa Anda tidak dapat memiliki satu tanpa yang lain.
“Kami memiliki beberapa tujuan terkait lean yang sangat tinggi untuk perusahaan, tetapi kami tidak dapat dan tidak akan mencapainya kecuali kami memiliki peralatan yang andal,” kata Steve Hockridge, direktur perusahaan lean global Energizer. “Anda tidak dapat meningkatkan produktivitas tenaga kerja atau mencapai pengurangan waktu tunggu atau mengurangi inventaris tanpanya.
Anda tidak dapat meningkatkan kecepatan aliran produk ke pelanggan jika Anda harus memperhitungkan masalah keandalan peralatan yang memaksa Anda untuk membawa inventaris buffer. Satu-satunya cara untuk melakukan semua itu adalah dengan meningkatkan keandalan peralatan Anda hingga selalu siap kapan pun Anda membutuhkannya.”
Joe Tisone, wakil presiden operasi global perusahaan, sependapat.
“Dalam bisnis kami, kecepatan dan fleksibilitas adalah elemen kunci kesuksesan,” katanya. “Anda tidak bisa cepat atau fleksibel dengan proses yang tidak dapat diandalkan. Jika mesin tidak bekerja, kita tidak akan memiliki aliran. Oleh karena itu, kami memandang lean dari perspektif bisnis total.”
Kisah ini akan membagikan beberapa teknik lean yang telah membuat pabrik Energizer di Maryville, Mo., efisien dan proaktif dari perspektif perawatan mesin dan keandalan mekanis. Ini juga akan berfungsi untuk menjadikan organisasi ini dan orang-orangnya sebagai panutan dari fleksibilitas, kelincahan, kemampuan, kreativitas, dan solusi berbasis tim.
AKAR MARYVILLE
Tidak seperti beberapa produsen, Energizer tidak membuat lompatan untuk bersandar sebagai akibat dari platform yang terbakar. Perusahaan, yang sejarahnya dimulai pada tahun 1886, memiliki pijakan keuangan yang kokoh pada awal abad ke-21. Setelah lepas dari Ralston Purina, pendapatan, profitabilitas, dan pangsa pasarnya tumbuh. Tapi bukan berarti puas atau berpuas diri.
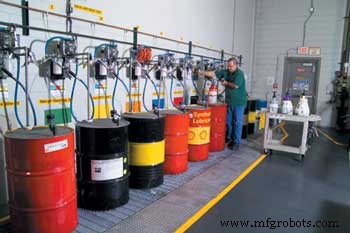
Analis perawatan prediktif Clyde Henry mengubah gudang minyak
drum pabrik menjadi pusat manajemen pelumas berkode warna yang bersih.
“Jika Anda tidak berubah, Anda akan tertinggal,” kata Tisone.
Pelanggan utama seperti Wal-Mart dan Target terus berharap dan menuntut lebih banyak. Pesaing lama Energizer di AS, dan pesaing baru dari Asia, memberikan tekanan pasar.
Di tingkat pabrik, fasilitas Energizer yang dibangun pada awal 1970-an, seperti Maryville, mulai menunjukkan usia. Akibatnya, waktu henti mesin dan pekerjaan pemeliharaan reaktif meningkat.
“Kami telah melakukan beberapa hal yang sangat positif selama 25 tahun terakhir untuk mengurangi biaya produk kami, tetapi kami melakukannya dengan cara tradisional, dengan batch besar dan skala efisiensi,” kata Hockridge. “Itu mungkin tepat saat itu, tetapi dunia berubah dan Anda harus menyesuaikan.”
Perjalanan Energizer menuju lean – dan penyatuan konsep lean dengan keandalan mesin – dimulai di Maryville . . . dan di suatu tempat di atas Samudra Pasifik.
Dana Billings, asisten manajer pabrik untuk lokasi Maryville, menjadi terpesona oleh prinsip-prinsip perbaikan yang diterapkan oleh perusahaan seperti Toyota. Belakangan tahun itu, ia mulai bereksperimen dengan aktivitas organisasi tempat kerja 5-S dan berhasil.
“Dana terus mendorong, mendorong, mendorong,” kata Hockridge. “Dia akan memotong artikel dan memberikan informasi ini kepada Joe Tisone. Dia akan mengirim mereka dengan catatan yang mengatakan, 'Ini adalah hal yang harus kita bahas.'”
Tisone membaca artikel tentang perjalanan pesawat untuk mengunjungi pabrik Energizer di Singapura.
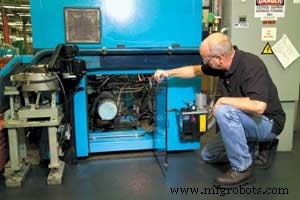
Setiap mesin paku kini dilengkapi pintu tembus pandang,
pencahayaan interior dan sistem pelumasan eksternal.
“Jika Anda terbang ke Singapura, Anda punya banyak waktu untuk membaca,” kata Billings.
Informasi itu menyentuh hati Tisone. Dia melanjutkan membaca buku tentang subjek, menghadiri seminar dan mengunjungi tanaman "ramping". Dia melakukan perjalanan ke 22 situs Energizer di seluruh dunia dan memperkenalkan lean kepada karyawan pabrik.
Saat inisiatif mendapatkan momentum dan struktur, Hockridge dipilih untuk mengawasi implementasinya secara global dan koordinator ditunjuk untuk mendorong lean di tingkat pabrik individu. Billings menjadi koordinator lean untuk situs Maryville.
Para pemimpin ini membantu mengubah lean dari konsep “menarik dan menarik” (jenis yang, melalui 5-S, membuat pengenalan, peningkatan tingkat permukaan di Maryville) ke pendekatan holistik yang mampu menghasilkan manfaat yang luas dan mendalam.
TIGA SURAT KECIL
Peran keandalan dalam program lean yang muncul dari Energizer bukanlah sesuatu yang baru. Saat lean mulai terbentuk di tingkat perusahaan, Maryville memperkenalkan ACW. Akronim tiga huruf ini, kependekan dari bengkel perawatan otonom, mengubah cara pabrik dan lebih dari 500 karyawannya memandang produksi, pemeliharaan, dan tarian.
ACW dimulai satu bulan sebelum kickoff lean resmi perusahaan. ACW pertama berlangsung di salah satu area pencetakan pabrik.
“Bisnisnya bagus, dan kami mendorong mesin dengan keras,” kata Hockridge. “Kami ingin mengadakan acara di area ini untuk benar-benar membawa mesin ini kembali.”
Format ACW adalah perpaduan dari kaizen, Reliability-Centered Maintenance, pendidikan teknis, analisis akar penyebab kegagalan dan Total Productive Maintenance.
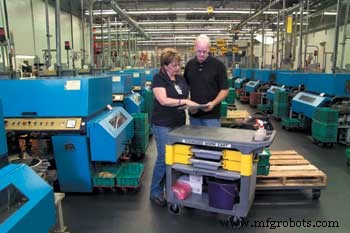
Operator Vicki Cady dan mekanik Steve Piveral melakukan
pemeliharaan preventif mereka tugas di area produksi kuku.
Selama acara selama seminggu, beberapa mekanik pemeliharaan bekerja sama dengan operator dari area produksi untuk bersama-sama menyusun rencana permainan guna mencapai tingkat keandalan yang tinggi untuk peralatan di area tersebut.
Mekanik membuka peralatan dan berbicara dengan operator tentang isinya dan bagaimana komponen ini bekerja, secara individu dan sebagai bagian dari sistem. Mereka menjelaskan (dan, dalam beberapa kasus, menunjukkan) tanda-tanda dan alasan keausan dan kegagalan komponen. Mereka juga menginstruksikan praktik yang tepat yang memperpanjang umur komponen dan memastikan kesehatan peralatan. Selama proses tersebut, operator menyampaikan wawasan dan pengalaman mereka tentang peralatan ini kepada para mekanik.
Bersama-sama, mereka kemudian mengidentifikasi cacat pada mesin, memecahkan masalah akar penyebab, dan membuat perbaikan mekanis dan proses yang sangat mengurangi kemungkinan kegagalan. Mereka memeriksa persyaratan pemeliharaan preventif saat ini, yang direkomendasikan, dan dirasionalisasi, serta menentukan strategi PM terbaik secara keseluruhan.
Setelah itu, sebuah rencana dibangun untuk mewujudkan peningkatan kesehatan peralatan. Daftar periksa PM dan instruksi kerja standar dibuat. Sejak saat itu, keandalan sehari-hari menjadi usaha bersama antara mekanik dan operator.
“Dulu ada batasan yang sangat ketat antara apa yang dilakukan pemeliharaan dan apa yang dilakukan produksi,” kata manajer pemeliharaan global Joe Plagens. “Kami ingin menciptakan lebih banyak kemitraan – hubungan dan keterkaitan – antara kedua organisasi ini. Apa yang membantu kami lakukan lean adalah memiliki pengaturan di mana operator mengambil lebih banyak peran kepemilikan peralatan mereka. Mereka mengambil tanggung jawab untuk memastikan pemeliharaannya.”
Ini bukan tentang menempelkan operator dengan daftar "yang harus dilakukan". Ini tentang tanggung jawab bersama dan pergeseran strategi perawatan aset dari reaktif menjadi terencana dan proaktif. Ini berbasis waktu dan "teratur" untuk memaksimalkan kerja sama dan penyelesaian tugas serta meminimalkan waktu henti.
Area produksi paku pabrik (paku kuningan adalah komponen baterai) memberikan contoh yang sempurna.
Setiap minggu, mekanik Steve Piveral dan operator Vicki Cady bersama-sama menjadwalkan kegiatan PM untuk 15 mesin di area tersebut. Pada waktu yang telah ditentukan, mereka bertemu untuk membahas instruksi kerja standar untuk tugas operator dan tugas mekanik. Instruksi diurutkan, selangkah demi selangkah, untuk efisiensi.
“Langkah-langkah tarian diatur. Siapa yang akan melakukan apa dan kapan?” kata Billings. “Dalam kegiatan koreografi yang disebut PM itu menjadi sebuah kemitraan. 'Kamu perlu melakukan ini agar aku bisa melakukannya.' Ini menjadi cara baru dalam menampilkan tarian pemeliharaan.”
Pada hari ini, kegiatan Piveral (umumnya lebih bersifat teknis) dijadwalkan untuk menyelesaikan 10 menit dan Cady (membersihkan, meminyaki dan mengoles) dijadwalkan selama 90 menit. Ketika Piveral menyelesaikan tugasnya, dia membuka file perintah kerja yang direncanakan untuk mesin itu. Dia menemukan pekerjaan atau pekerjaan yang cocok di sisa waktu. Piveral dan Cady menyelesaikan pekerjaan, dan menjalankan mesin kembali.
“Saya merasa lebih terlibat dan menjadi bagian dari banyak hal,” kata Cady. “Saya tahu bagaimana melakukan tugas perawatan yang lebih ringan. Saya rasa apa yang saya lakukan membantu alat berat tetap dalam kondisi yang lebih baik dan berkinerja lebih baik.”
Piveral juga melihat sisi positifnya.
“Dulu saya melakukan 30 jam PM setiap minggu di daerah ini. Sekarang saya punya 10 menit di setiap mesin (15 mesin) dalam tiga minggu. Itu 150 menit dalam tiga minggu dibandingkan dengan 90 jam dalam tiga minggu, ”katanya. “Nilai tersembunyi dari semua itu adalah sekarang saya dapat melakukan pekerjaan terencana yang sebelumnya tidak dapat saya lakukan.”
Konsep ini tersebar luas di pabrik dan berperan penting dalam mendorong pekerjaan yang terencana dan proaktif. Empat tahun lalu, 20 persen dari pesanan kerja adalah untuk pemeliharaan terencana; hari ini, angka itu 60 persen dan terus bertambah.
“Pemeliharaan tidak terencana menghabiskan biaya empat kali lipat lebih besar daripada pemeliharaan terencana, jadi saya rasa itu membuat pekerjaan saya empat kali lebih penting daripada sebelumnya,” kata analis prediktif Rick Staley.
TETAP SEDERHANA
Karyawan Maryville percaya bahwa mereka melihat pabrik, dan mesinnya, secara berbeda sebagai hasil dari aktivitas lean dan keandalan.
“Kami memiliki pemikiran teknik yang cemerlang di sini, dan para insinyur dapat berpikir dalam istilah yang sangat kompleks dan rumit,” kata Billings. “Sebagian besar dari apa yang kami miliki adalah peralatan khusus. Jadi, dengan latar belakang kami, kami ingin merancang atau membeli mesin yang melakukan 15 hal sebelum mengeluarkan sebagian.
Lean, di sisi lain, mengajarkan Anda untuk melihat hal-hal dalam istilah yang sangat sederhana. Anda ingin menyederhanakan setiap aspek pemeliharaan, produksi, kualitas, dll. Ini merupakan transisi bagi kami, tetapi saya pikir kami melihat titik terangnya.”
Kompleksitas sangat meningkatkan kemungkinan pemborosan (gerakan berlebihan, inventaris, pengangkutan, dll.). Ini juga meningkatkan risiko tidak dapat diandalkan (berdasarkan banyaknya kemampuan dan komponennya) dan waktu henti yang diperpanjang.
Insinyur, mekanik, dan operator kini memeriksa kembali mesin, sel, dan seluruh proses produksi individu dan mencari solusi sederhana yang mengurangi limbah.
“Ini semua tentang memisahkan langkah-langkah bernilai tambah dari yang tidak bernilai tambah,” kata Hockridge. “Mari kita pertahankan langkah bernilai tambah. Tetapi mengapa kita memiliki peralatan berlebihan yang memuat produk ke dalam proses dengan cara ini, atau mengapa kita memiliki semua alat angkut ekstra ini untuk proses ini? Ini sia-sia. Pabrik menggunakan pemikiran itu di satu area dan memindahkan 30 peralatan.
Produk akhirnya sama. Tetapi prosesnya lebih sederhana dan lebih andal, serta kualitasnya lebih baik. Saat Anda mengeluarkan peralatan sebanyak itu, Anda meningkatkan peluang kinerja yang andal. Juga, berapa banyak PM yang hilang secara bersamaan? Kami fokus pada hal-hal yang penting.”
Ini bukan contoh yang terisolasi. Billings and Plagens mencatat beberapa proyek yang masing-masing menghilangkan lebih dari 30 peralatan.
Hockridge mengatakan ini menunjukkan pentingnya menyatukan lean dan keandalan.
“Jangan membabi buta mulai melakukan reliabilitas atau TPM dulu, karena tahu? Anda mungkin menemukan bahwa peralatan tidak diperlukan, ”katanya. “Anda perlu mengintegrasikan strategi — ramping dan andal.”
Dengan meningkatkan keandalan proses yang penting dan bernilai tambah, dan membuang limbah, hasil impiannya adalah mampu menghubungkan proses secara fisik bersama-sama (berlawanan dengan proses berbeda yang mengarah pada kelebihan inventaris, pergerakan, pekerjaan dalam proses, dan transportasi) .
“Anda dapat menautkan proses yang tidak dapat diandalkan bersama-sama, tetapi saya tidak akan merekomendasikannya,” kata Billings. “Jika Anda menautkan empat proses bersama-sama yang masing-masing 80 persen efisien, 80 kali 80 kali 80 kali 80 tidak sama dengan 80.”
Proses keseluruhan malah 41 persen efisien, dan keadaan darurat menunggu untuk terjadi. Meningkatkan keandalan keempat proses individu tersebut hingga, katakanlah, 95 persen meningkatkan efisiensi total sistem hingga 81,5 persen yang lebih dapat diterima.
“Setiap kali Anda melakukan perawatan yang tidak direncanakan, Anda memengaruhi seluruh pabrik, bukan hanya area di mana Anda berada. Tetapi saat kita menuju aliran, itu membuatnya semakin penting, ”kata Staley. “Saat Anda mulai menautkan proses bersama, kerusakan memiliki dampak yang lebih besar.”
KIT, KAIZEN DAN KECIL-K
Pabrik Maryville juga mencari limbah dalam bentuk non-mekanis. Untuk menghilangkan menunggu, bergerak dan transportasi dan meningkatkan waktu kunci pas, pabrik beralih ke konsep lean kitting dalam dua tahun terakhir.
Alih-alih seorang mekanik melakukan perjalanan bolak-balik ke tempat tidur alat untuk mendapatkan suku cadang, alat, dan bahan yang dibutuhkan untuk menyelesaikan perintah kerja (jarak berjalan itu bertambah di pabrik setengah juta kaki persegi), pekerja itu menerima semua yang dia butuhkan untuk melakukan tugas dalam satu paket yang nyaman.
“Dalam membuat bagan spageti (mengikuti gerakan melalui suatu proses), terobosan datang ketika Anda menembus kertas karena Anda menelusurinya berkali-kali,” kata Billings.
Petugas boks alat MRO seperti Deb Hayes dan Donna Wilson menerima perintah kerja yang direncanakan dari perencana pemeliharaan. Petugas melewati buaian dan mengumpulkan semua yang dibutuhkan dan kemudian memasukkan semuanya ke dalam tas jinjing, bak mandi atau (jika pekerjaannya besar) di atas gerobak.
Ketika pekerjaan sudah siap, perencana diberitahu. Pekerjaan kemudian dijadwalkan. Mekanik yang menerima perintah kerja pergi ke tempat tidur bayi sekali untuk menerima kit dan kemudian menuju ke lokasi kerja.
Plagens mengatakan konsep seperti kitting telah berperan dalam menggandakan waktu kunci pas selama tiga tahun terakhir.
Pengurangan sampah datang dalam berbagai bentuk. Seperti banyak perusahaan lean lainnya, Energizer adalah pendukung berat acara kaizen (perbaikan berkelanjutan). Pembuat baterai telah menyelesaikan lebih dari 800 kaizen selama seminggu yang telah berkontribusi pada penghematan biaya lebih dari $10 juta.
Ini juga mempromosikan small-k, kependekan dari kaizen kecil. Ini adalah kegiatan pembuangan limbah langsung yang sederhana yang dilakukan oleh satu atau dua pekerja. Sebuah pabrik Energizer di Indonesia saat ini menjalankan 500 kegiatan kecil yang terdokumentasi setiap bulan.
KREATIF YANG TERLIHAT
Alat ramping seperti small-k berfungsi untuk membuka kreativitas pekerja lantai pabrik.
“Kreativitas adalah landasan dan salah satu yang ditutupi oleh pendekatan tradisional kami terhadap berbagai hal,” kata Billings. “Ketika orang menyadari bahwa tidak apa-apa untuk berpikir secara berbeda, itu benar-benar membuka pintu air.”
Plagens menambahkan, “Kreativitas untuk memperbaiki masalah yang berulang ada di tangan mereka. Kami ingin secara umum meningkatkan keandalan pada mesin atau sekelompok mesin. Apa yang kelompok itu lakukan untuk membawa kita ke sana terserah mereka.”
Ide-ide ini memecahkan masalah, meningkatkan keandalan, dan mempermudah pekerjaan orang.
Sebuah contoh bersinar terselip di salah satu sudut bangunan. Area ini sebelumnya merupakan gudang untuk drum minyak yang diisi. Drum-drum ini ditumpuk, menunggu untuk disadap dan isinya digunakan untuk melumasi mesin.
Beberapa praktik formal dilakukan pada saat itu untuk menyimpan drum atau untuk menyadap dan mengangkut minyak ke lantai. Tidak ada teknik penyaringan yang digunakan. Hasilnya adalah kelebihan persediaan, pelumas tidak murni, dan peningkatan risiko kontaminasi.
Analis pemeliharaan prediktif Clyde Henry mengembangkan solusi yang ramping dan andal. Dia berbicara dengan vendor dan melihat banyak katalog. Drum-drum berisi minyak yang sudah usang telah dibuang, dan kelebihan-kelebihan drum minyak yang dapat digunakan dikembalikan ke pemasok.
Henry membuat sketsa dan membuat sketsa ulang model sampai dia menemukan tata letak yang benar yang akan dengan bersih, aman, dan efisien menampung pelumas yang benar dan peralatan terkait. Repositori menjadi pusat manajemen pelumas. “Kami ingin produk oli yang baik dan bersih masuk ke peralatan kami,” kata Henry.
“Kami ingin memulai dari dalam ke luar, memastikan semuanya bersih dan tersaring, tanpa kelembapan atau kotoran, sehingga kami dapat mengatakan bahwa peralatan tersebut menggunakan oli 100 persen murni dan bersih.
“Kami sekarang menyaring minyak menjadi 3 mikron. Kami menyaring air sebelum masuk ke peralatan. Kami menempatkan minyak dalam wadah yang tepat untuk mekanik PM kami. Kami memiliki sistem kode warna yang sangat mudah.
Kami telah memberi kode warna pada pelumas kami ke wadah dan ke komponen mesin itu sendiri. Jika diberi kode kuning, itu masuk ke gearbox kami, yang juga ditandai dengan warna kuning. Sudah banyak pekerjaan, tetapi kami telah menempuh perjalanan panjang dalam waktu satu tahun dan benar-benar membersihkan area ini.”
Pengodean warna hanyalah salah satu teknik visibilitas yang digunakan di seluruh pabrik untuk meningkatkan komunikasi dan menghilangkan miskomunikasi. Titik pemeriksaan diberi nomor. Komponen mesin individu diberi label. Pengukur ditempel untuk menunjukkan tingkat yang tepat dan tidak tepat. Operator menempatkan tag pada masing-masing komponen mesin untuk menunjukkan masalah (tag merah) dan peluang untuk perbaikan (tag hijau).
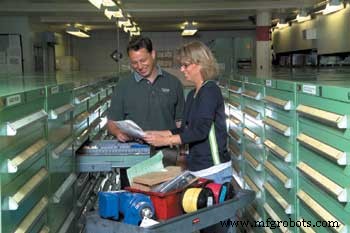
Manajer pemeliharaan global Joe Plagens dan tempat tidur alat
petugas Deb Hayes memeriksa proyek kiting.
Alat visibilitas mengirim pesan ke mekanik dan operator, tetapi mereka juga dapat bekerja hanya untuk meningkatkan visibilitas.
Area produksi kuku memberikan contoh yang sempurna. Masing-masing dari 15 mesin berbentuk kotak, tingginya sekitar 4 kaki dan ditempatkan di lantai beton. Awalnya, masing-masing dari empat sisi mesin adalah lembaran logam padat.
Anda tidak dapat melihat menembus logam, jadi masalah yang muncul seperti kebocoran oli tidak diketahui sampai genangan air keluar dari bawah mesin. Jika Anda perlu memeriksa atau menambahkan oli ke sistem pelumasan, mesin harus dimatikan, dikunci, dan pelindung logam dilepas. Bagian dalamnya gelap, jadi senter selalu dibutuhkan.
Solusinya kreatif dan berlimpah. Mekanik memasang pintu Plexiglas di dua sisi mesin. Ini memungkinkan mekanik dan operator akses cepat ke interior. Pencahayaan permanen dipasang di dalam untuk memberikan visibilitas.
Lembaran penyerap berukuran khusus ditempatkan di dalam untuk tidak hanya menangkap tetesan minyak tetapi juga untuk menyampaikan informasi itu secara visual kepada operator atau mekanik. Dan, sistem pelumasan dipindahkan ke bagian luar mesin, sehingga tidak diperlukan shutdown atau penguncian. Pelumas dapat ditambahkan dengan cepat.
“Kita bisa bereksperimen,” kata Piveral. “Terkadang ide itu tidak berhasil, tetapi itu bukan masalah besar. Kami hanya mengembalikannya seperti semula. Itu semua bagian dari itu. Terkadang Anda benar, terkadang salah, dan jika Anda salah, apa yang kita pelajari darinya. Ketika berhasil, itu luar biasa. Anda tahu bahwa Anda memiliki andil dalam memastikan keandalan dan kinerja alat berat.”
1 PERSENTER BENAR
Beberapa perusahaan manufaktur mencoba-coba lean atau membodohi diri mereka sendiri (dan orang lain) untuk percaya bahwa mereka berada di jalur yang benar. Namun ada perusahaan lain yang benar-benar melakukannya dengan cara yang benar dan membuat perubahan berarti yang memungkinkan pabrik dan karyawan mereka menghadapi tantangan hari ini dan masa depan dengan lebih baik.
Apakah Anda termasuk dalam kategori 80 persen atau kategori 1 persen? Jelas di mana Energizer berdiri.
“Kami telah mengurangi jumlah mekanik yang memadamkan api atau bekerja secara reaktif di lantai dan meningkatkan jumlah yang berfokus pada pekerjaan terencana, prediktif, preventif, dan proaktif,” kata Staley. “Kami menggunakan sumber daya kami dengan cara dan cara yang berbeda.”
Tisone menambahkan, “Melihat ke belakang tiga tahun, di mana kami berada di semua pabrik kami dan di mana kami berada hari ini, itu berbeda 180 derajat dalam hal kepemilikan dan peningkatan yang telah kami buat di semua proses. Kami telah membuat langkah besar, tetapi jalan kami masih panjang. Lean adalah sebuah perjalanan; itu bukan tujuan. Tidak pernah ada akhir.”
Seperti kelinci bertenaga baterai Energizer, ia terus berjalan dan berjalan.