Industri 4.0:7 Contoh Nyata Manufaktur Digital dalam Tindakan
Industri 4.0, IIoT, dan digitalisasi saat ini merupakan beberapa topik yang paling banyak dibahas namun paling tidak dipahami dalam manufaktur saat ini.
Dengan masih banyaknya kebingungan seputar Industri 4.0, hari ini kita akan menjelajahi teknologi utama di balik Industri 4.0, serta aplikasi dunia nyata.
Industri 4.0 secara singkat
Industri 4.0 menandakan perubahan dalam lanskap manufaktur tradisional. Juga dikenal sebagai Revolusi Industri Keempat, Industri 4.0 mencakup tiga tren teknologi yang mendorong transformasi ini:konektivitas, kecerdasan, dan otomatisasi fleksibel .
Industri 4.0 menyatukan TI (Teknologi Informasi) dan OT (Teknologi Operasional), untuk menciptakan lingkungan fisik siber.
Konvergensi ini dimungkinkan berkat munculnya solusi digital dan teknologi canggih, yang sering dikaitkan dengan Industri 4.0. Ini termasuk:
- Internet of Things Industri
- Data Besar
- Komputasi awan
- Manufaktur aditif (AM)
- Robot tingkat lanjut
- Augmented reality dan virtual reality (AR/VR)
Teknologi ini membantu mendorong transformasi digital manufaktur melalui integrasi sistem dan proses yang sebelumnya berbeda melalui sistem komputer yang saling berhubungan di seluruh rantai nilai dan pasokan.
Merangkul Industri 4.0, manufaktur digital dan interkonektivitas yang menyertainya membuka segudang manfaat bagi perusahaan, termasuk kelincahan, fleksibilitas, dan kinerja operasional yang lebih baik.
1. Internet of Things Industri
Di jantung Industri 4.0 adalah Internet of Things (IoT).
Sederhananya, IoT mengacu pada jaringan perangkat fisik yang saling terhubung secara digital, memfasilitasi komunikasi dan pertukaran data melalui Internet. Perangkat pintar ini bisa berupa apa saja mulai dari smartphone dan peralatan rumah tangga hingga mobil dan bahkan bangunan.
Industrial IoT adalah subset dari Internet of Things, tempat berbagai sensor, tag Radio Frequency Identification (RFID), perangkat lunak, dan elektronik terintegrasi dengan mesin dan sistem industri untuk mengumpulkan data real-time tentang kondisi dan kinerjanya.
IIoT memiliki banyak kasus penggunaan, dengan manajemen aset dan pelacakan menjadi salah satu aplikasi utama teknologi saat ini.
Misalnya, IIoT dapat digunakan untuk mencegah overstocking atau kekurangan stok.
Salah satu cara untuk mencapainya adalah dengan menggunakan sensor yang dipasang di rak dan perangkat penimbangan untuk menyiarkan informasi inventaris ke sistem manajemen gudang Anda. Menempatkan sistem seperti itu memungkinkan manajer gudang untuk memantau tingkat inventaris, sehingga mendapatkan visibilitas waktu nyata dan kontrol atas inventaris.
Mari kita lihat bagaimana BJC HealthCare menggunakan solusi manajemen inventaris terintegrasi untuk mencapai penghematan biaya dalam rantai pasokannya.
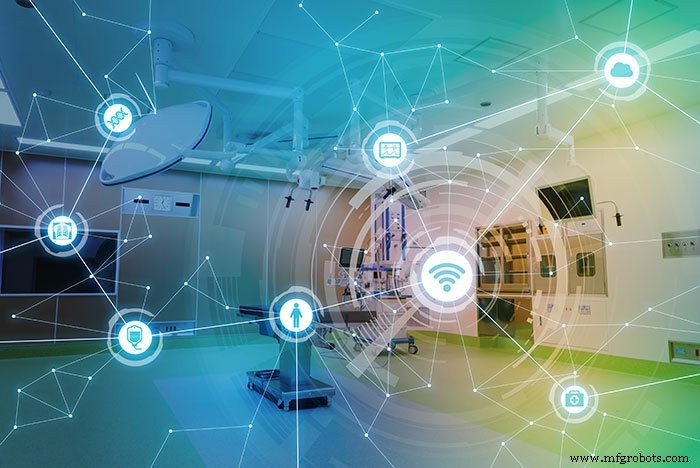
Sorotan:BJC HealthCare mengadopsi IoT untuk inventaris dan manajemen rantai pasokan
BJC HealthCare adalah penyedia layanan kesehatan yang mengoperasikan 15 rumah sakit di Missouri dan Illinois.
Perusahaan menyebarkan teknologi identifikasi frekuensi radio (RFID) untuk melacak dan mengelola ribuan pasokan medis. Teknologi RFID menggunakan gelombang radio untuk membaca dan menangkap informasi yang disimpan pada tag yang ditempelkan pada suatu objek, seperti persediaan perawatan kesehatan.
Sebelumnya, proses pelacakan inventaris melibatkan banyak tenaga kerja manual. Namun, memantau inventaris secara manual dapat menjadi tantangan, karena rumah sakit membeli berbagai produk dari pemasok dan menyimpan banyak barang di lokasi untuk prosedur tertentu.
Dalam beberapa kasus, tanggal kedaluwarsa produk perlu dipantau secara ketat, sementara hilangnya stok dapat menyebabkan banyak waktu yang dihabiskan untuk melakukan pemeriksaan inventaris.
Untuk alasan ini, BJC memutuskan untuk menerapkan teknologi penandaan RFID pada tahun 2015.
Sejak menerapkan teknologi tersebut, BJC telah mampu mengurangi jumlah stok yang disimpan di lokasi di setiap fasilitas sebesar 23 persen. Perusahaan memperkirakan bahwa mereka akan melihat penghematan berkelanjutan sekitar $5 juta per tahun, setelah penandaan RFID diterapkan sepenuhnya tahun ini.
Seperti yang ditunjukkan oleh contoh ini, IIoT dapat secara signifikan meningkatkan operasi, meningkatkan efisiensi, mengurangi biaya, dan memberikan visibilitas real-time yang berharga di seluruh rantai pasokan.
2. Data Besar dan Analisis
Big Data mengacu pada kumpulan data besar dan kompleks yang dihasilkan oleh perangkat IoT. Data ini berasal dari berbagai aplikasi cloud dan perusahaan, situs web, komputer, sensor, kamera, dan banyak lagi — semuanya hadir dalam format dan protokol yang berbeda.
Dalam industri manufaktur, ada banyak jenis data yang perlu dipertimbangkan, termasuk data yang berasal dari peralatan produksi yang dilengkapi dengan sensor dan database dari sistem ERP, CRM, dan MES.
Namun, bagaimana produsen dapat mengubah data yang dikumpulkan menjadi wawasan bisnis yang dapat ditindaklanjuti dan manfaat nyata?
Dengan analisis data.
Dalam hal data, penggunaan analitik data sangat penting untuk mengubah data menjadi informasi yang dapat memberikan wawasan yang dapat ditindaklanjuti.
Model pembelajaran mesin dan visualisasi data dapat membantu proses analisis data. Secara umum, teknik pembelajaran mesin menerapkan algoritme komputasi yang kuat untuk memproses kumpulan data yang sangat besar, sementara alat visualisasi data memungkinkan produsen untuk lebih mudah memahami kisah yang diceritakan oleh data.
Pada akhirnya, dengan mengambil kumpulan data yang sebelumnya terisolasi, mengumpulkan dan menganalisisnya, perusahaan kini dapat menemukan cara baru untuk mengoptimalkan proses yang memiliki efek terbesar pada hasil.
Sorotan:Pengambilan keputusan Big Data di pabrik Bosch Automotive di Cina
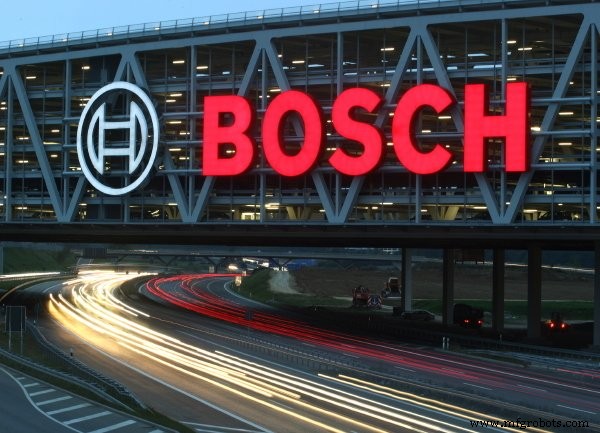
Menggabungkan IIoT dan Big Data adalah resep yang digunakan Bosch untuk mendorong transformasi digital pabrik Bosch Automotive Diesel System di Wuxi, Cina.
Perusahaan menghubungkan mesin-mesinnya untuk memantau keseluruhan proses produksi di inti pabriknya. Hal ini dicapai dengan menyematkan sensor ke dalam mesin pabrik yang kemudian digunakan untuk mengumpulkan data tentang kondisi mesin dan waktu siklus.
Setelah dikumpulkan, alat analitik data tingkat lanjut memproses data secara real time dan memperingatkan pekerja ketika ada hambatan dalam operasi produksi yang telah diidentifikasi.
Mengambil pendekatan ini membantu untuk memprediksi kegagalan peralatan, memungkinkan pabrik untuk menjadwalkan operasi pemeliharaan dengan baik sebelum terjadi kegagalan.
Hasilnya, pabrik dapat menjaga mesinnya tetap berjalan dan beroperasi untuk jangka waktu yang lebih lama.
Perusahaan menyatakan bahwa menggunakan analisis data dengan cara ini telah berkontribusi pada peningkatan output lebih dari 10% di area tertentu, sekaligus meningkatkan pengiriman dan kepuasan pelanggan.
Pada akhirnya, wawasan yang lebih luas tentang operasi pabrik mendukung pengambilan keputusan yang lebih baik dan lebih cepat di seluruh organisasi, memungkinkannya mengurangi waktu henti peralatan dan mengoptimalkan proses produksi.
3. Komputasi awan
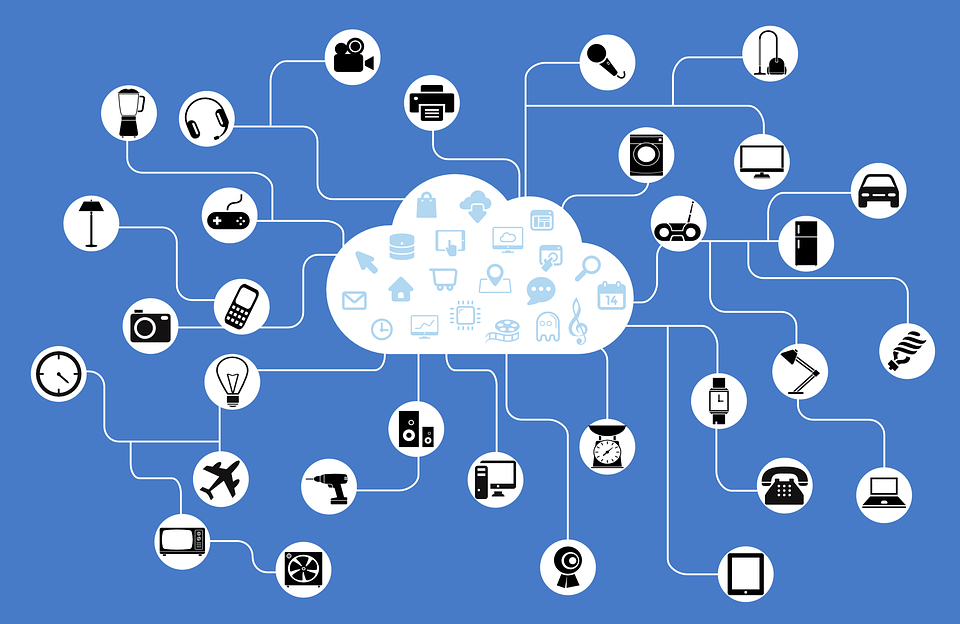
Selama beberapa dekade, produsen telah mengumpulkan dan menyimpan data dengan tujuan meningkatkan operasi.
Namun, dengan munculnya IoT dan Industri 4.0, kenyataannya adalah bahwa data dihasilkan dengan kecepatan yang mengejutkan dan volume tinggi, sehingga tidak mungkin untuk ditangani secara manual. Hal ini menciptakan kebutuhan akan infrastruktur yang dapat menyimpan dan mengelola data ini secara lebih efisien.
Di sinilah komputasi awan masuk.
Komputasi awan menawarkan platform bagi pengguna untuk menyimpan dan memproses sejumlah besar data di server jarak jauh. Ini memungkinkan organisasi untuk menggunakan sumber daya komputer tanpa harus mengembangkan infrastruktur komputasi di tempat.
Istilah komputasi awan mengacu pada informasi yang disimpan di "awan", diakses dari jarak jauh melalui Internet. Dengan sendirinya, komputasi awan bukanlah solusi tersendiri, tetapi memungkinkan penerapan solusi lain yang dulunya membutuhkan daya komputasi yang berat.
Kemampuan komputasi awan untuk menyediakan sumber daya komputasi dan ruang penyimpanan yang dapat diskalakan memungkinkan perusahaan untuk menangkap dan menerapkan intelijen bisnis melalui penggunaan analitik data besar, membantu mereka untuk mengkonsolidasikan dan merampingkan manufaktur dan operasi bisnis.
Pengeluaran global produsen untuk platform komputasi awan diperkirakan mencapai $9,2 miliar pada tahun 2021, menurut IDC. Faktor kunci di balik adopsi ini adalah manfaat untuk dapat memusatkan operasi, menghilangkan sehingga informasi dapat dibagikan ke seluruh organisasi.
Menurut salah satu survei IDC, Quality Control, Computer-Aided Engineering and Manufacturing Execution Systems (MES) adalah tiga sistem yang paling banyak diadopsi di cloud.
Jelas, komputasi awan mengubah hampir setiap aspek manufaktur, mulai dari manajemen alur kerja hingga operasi produksi – dan bahkan kualifikasi produk.
Sorotan:Volkswagen menciptakan Cloud Otomotif
Mobil terhubung adalah tren baru yang besar di industri otomotif, yang muncul sebagai peluang untuk menawarkan layanan nilai tambah digital bagi pelanggan. Salah satu produsen mobil pertama yang mengikuti tren ini adalah Volkswagen, yang bergabung dengan Microsoft untuk mengembangkan jaringan cloud, "Volkswagen Automotive Cloud".
Teknologi, yang direncanakan untuk tahun 2020, akan menawarkan berbagai fitur, termasuk konektivitas rumah pintar, asisten digital pribadi, layanan pemeliharaan prediktif, streaming media, dan pembaruan.
Volkswagen bertujuan untuk menambahkan lebih dari 5 juta penawaran merek Volkswagen per tahun ke Internet of Things (IoT) dengan bantuan layanan cloud ini.
Ketika industri otomotif membuat langkah yang mengesankan dalam mengembangkan kendaraan otonom dan listrik yang canggih, pembuat mobil perlu menemukan pendekatan yang efektif untuk mengelola dan mentransmisikan sejumlah besar data ke kendaraan mereka. Menggabungkan penyimpanan berbasis cloud dan platform komunikasi muncul sebagai cara yang efektif untuk mengatasi tantangan yang dihadapi oleh para pembuat mobil ini.
4. Robotika Tingkat Lanjut
Sementara robotika telah digunakan di bidang manufaktur selama beberapa dekade, Industri 4.0 telah memberikan kehidupan baru pada teknologi ini.
Dengan kemajuan teknologi baru-baru ini, generasi baru robotika canggih muncul, yang mampu melakukan tugas-tugas yang sulit dan rumit. Didukung oleh perangkat lunak dan sensor mutakhir, mereka dapat mengenali, menganalisis, dan bertindak berdasarkan informasi yang mereka terima dari lingkungan, dan bahkan berkolaborasi dan belajar dari manusia.
Salah satu bidang robotika yang mendapatkan daya tarik yang signifikan adalah robot kolaboratif (“cobots”), yang dirancang untuk bekerja dengan aman di sekitar orang, membebaskan pekerja dari tugas yang berulang dan berbahaya.
Sorotan:Fetch Robotics membantu DHL meningkatkan operasi gudang
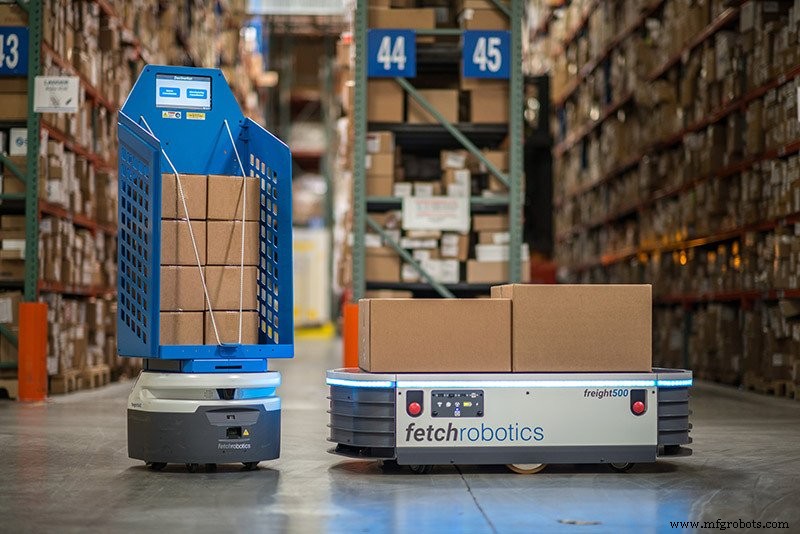
Fetch Robotics yang berbasis di California telah mengembangkan Autonomous Mobile Robots (AMRs) kolaboratif untuk menemukan, melacak, dan memindahkan inventaris di gudang dan fasilitas logistik.
Pusat distribusi DHL di Belanda menggunakan Ambil AMR untuk melakukan operasi pengambilan dan penempatan. Di DHL, AMR secara mandiri bergerak melintasi fasilitas bersama para pekerja, secara otomatis mempelajari dan berbagi rute perjalanan yang paling efisien. Menggunakan robot self-driving dengan cara ini dapat membantu mengurangi waktu siklus pemesanan hingga 50% dan memberikan peningkatan produktivitas hingga dua kali lipat, menurut perusahaan.
Saat robot menjadi lebih otonom, fleksibel, dan kooperatif, mereka akan mampu menangani tugas yang lebih kompleks, membebaskan pekerja dari tugas monoton, dan meningkatkan produktivitas di lantai pabrik.
5. Manufaktur Aditif
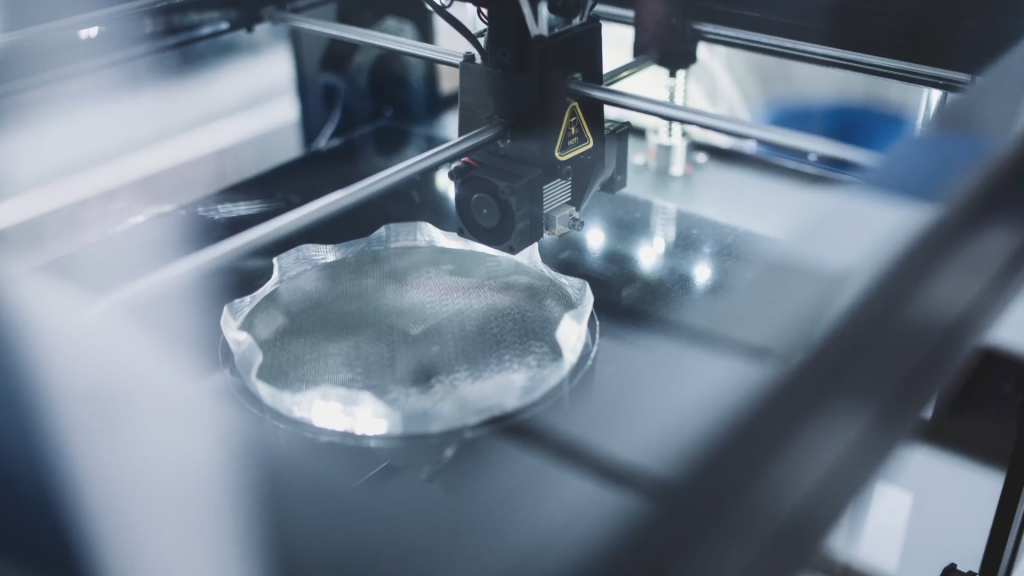
Di samping robotika dan sistem cerdas, manufaktur aditif, atau pencetakan 3D, adalah teknologi utama yang mendorong Industri 4.0. Manufaktur aditif bekerja dengan menggunakan model 3D digital untuk membuat komponen dengan printer 3D lapis demi lapis.
Dalam konteks Industri 4.0, pencetakan 3D muncul sebagai teknologi manufaktur digital yang berharga. Dulunya hanya merupakan teknologi prototyping yang cepat, hari ini AM menawarkan cakupan kemungkinan yang sangat besar untuk manufaktur mulai dari perkakas hingga kustomisasi massal di hampir semua industri.
Ini memungkinkan suku cadang untuk disimpan sebagai file desain dalam inventaris virtual, sehingga dapat diproduksi sesuai permintaan dan lebih dekat ke titik kebutuhan — model yang dikenal sebagai manufaktur terdistribusi.
Pendekatan desentralisasi untuk manufaktur dapat mengurangi jarak transportasi, dan karenanya biaya, serta menyederhanakan manajemen inventaris dengan menyimpan file digital, bukan bagian fisik.
Sorotan:Solusi manufaktur aditif digital Fast Radius untuk memungkinkan model bisnis baru
Ada banyak contoh manufaktur aditif yang dimanfaatkan dengan baik, tetapi contoh utamanya adalah, mungkin, Radius Cepat.
Pada tahun 2018, Forum Ekonomi Dunia menobatkan fasilitas Fast Radius' Chicago sebagai salah satu dari sembilan pabrik pintar teratas di dunia .
Produsen kontrak, yang berfokus pada AM tetapi juga menawarkan mesin CNC dan injection moulding, memiliki lokasi produksi di Chicago, Singapura dan di fasilitas UPS Worldport. Hal ini membuat Fast Radius memiliki posisi yang baik untuk mendorong visinya tentang perputaran cepat dan kustomisasi produk secara massal dengan bantuan teknologi manufaktur yang canggih.
Faktor kunci di balik kelincahan dan fleksibilitas Fast Radius adalah platform teknologi miliknya.
Platform dapat mengumpulkan data dan temuan dari setiap desain bagian yang disimpan dan diproduksi di gudang virtual Fast Radius. Data membantu tim untuk mengidentifikasi aplikasi yang cocok untuk pencetakan 3D dan mengevaluasi tantangan teknik dan ekonomi dalam memproduksi komponen dengan cara ini.
Selanjutnya, perusahaan menawarkan optimasi rantai pasokan melalui inventaris virtualnya. Misalnya, Fast Radius membuat gudang suku cadang virtual yang terdiri dari 3.000 item untuk produsen alat berat. Dengan biaya tinggi yang terlibat dalam penyimpanan suku cadang yang jarang dipesan, pendekatan ini merupakan solusi inovatif untuk manajemen rantai pasokan.
6. Kembar Digital
Konsep kembaran digital sangat menjanjikan untuk mengoptimalkan kinerja dan pemeliharaan sistem industri. Firma riset global, Gartner, memperkirakan bahwa pada tahun 2021, 50% perusahaan industri besar akan menggunakan kembaran digital untuk memantau dan mengontrol aset dan proses mereka.
Kembar digital adalah representasi digital dari produk, mesin, proses, atau sistem dunia nyata, yang memungkinkan perusahaan untuk lebih memahami, menganalisis, dan mengoptimalkan proses mereka melalui simulasi waktu nyata.
Sementara kembar digital dapat dikacaukan dengan simulasi yang digunakan dalam rekayasa, ada lebih banyak konsep ini.
Tidak seperti simulasi teknik, kembaran digital menjalankan simulasi online, berdasarkan data yang diterima dari sensor yang terhubung ke mesin atau perangkat lain.
Karena perangkat IIoT mengirimkan data hampir secara real time, kembaran digital dapat mengumpulkan data ini secara terus-menerus, mempertahankan kesetiaannya dengan data asli sepanjang masa pakai produk atau sistem.
Hal ini memungkinkan kembar digital untuk memprediksi masalah potensial sehingga tindakan pencegahan dapat diambil. Misalnya, operator dapat menggunakan kembaran digital untuk mengidentifikasi mengapa suatu bagian tidak berfungsi atau untuk memprediksi masa pakai suatu produk. Simulasi berkelanjutan ini membantu meningkatkan desain produk serta memastikan waktu pengoperasian peralatan.
Penggunaan kembar digital ini telah lama menjadi alat penting dalam aplikasi luar angkasa, mesin berat, dan otomotif yang menuntut. Sekarang, kemajuan teknologi komputasi, pembelajaran mesin, dan sensor memperluas konsep kembaran digital di industri lain.
Sorotan:Balapan untuk menang dengan kembar digital
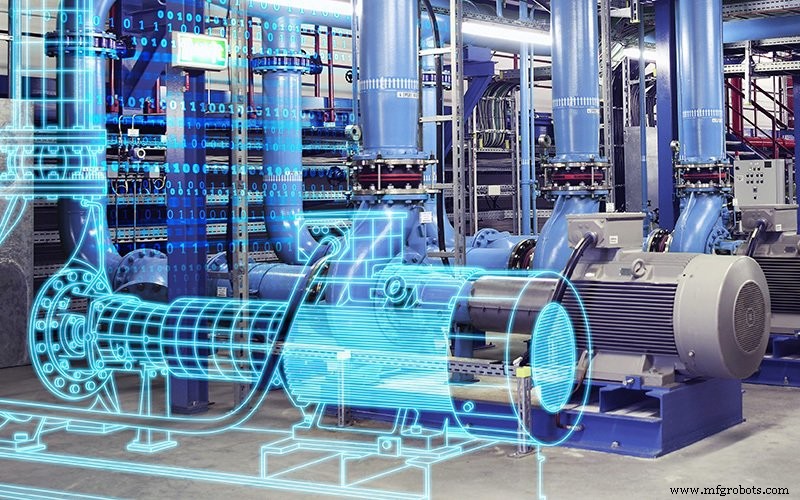
Tim balap motor menghadapi persyaratan yang sangat menantang dalam hal pengembangan produk, dan tim balap pro Amerika Tim Penske tidak terkecuali.
Dalam upaya untuk mempercepat proses pengembangan mobil balap, Team Penske bermitra dengan Siemens tahun lalu, mendapatkan akses ke desain digital canggih dan solusi simulasi – termasuk kembar digital.
Memiliki kembaran digital memberi insinyur Team Penske tempat uji virtual untuk berinovasi suku cadang baru, mengoptimalkan kinerja mobil sebelum mereka menyentuh mobil fisik.
Kembar digital mobil balap didasarkan pada sensor yang dipasang pada mobil sungguhan. Sensor ini mengumpulkan data seperti tekanan ban, kontrol mesin dan kecepatan angin, yang kemudian diubah menjadi model mobil virtual. Model inilah yang memungkinkan para insinyur menguji konfigurasi desain yang berbeda, membuat perubahan desain yang efektif berdasarkan data dengan sangat cepat.
Untuk Tim Penske, ini pada akhirnya sama dengan proses pengujian produk yang lebih murah, lebih hemat sumber daya dan, semoga, cara untuk mengembangkan kendaraan yang lebih cepat.
7. Realitas tertambah
Meskipun digunakan dalam aplikasi konsumen, industri manufaktur baru saja mulai mengeksplorasi manfaat teknologi Augmented Reality (AR). Namun, ada potensi besar yang belum dimanfaatkan untuk teknologi ini, mulai dari membantu proses perakitan hingga membantu memelihara peralatan manufaktur.
Augmented reality menjembatani kesenjangan antara dunia digital dan fisik dengan menempatkan gambar atau data virtual ke objek fisik. Untuk ini, teknologi menggunakan perangkat berkemampuan AR, seperti smartphone, tablet, dan kacamata pintar.
Mari kita ambil contoh medis sebagai contoh - seorang ahli bedah yang menggunakan kacamata AR selama operasi bedah. Kacamata dapat melapisi data dari MRI dan CT scan pasien, seperti saraf, pembuluh darah utama dan saluran, ke pasien, dan menyorotnya dalam warna. Ini membantu ahli bedah untuk menemukan jalur teraman ke daerah yang membutuhkan invasi, meminimalkan risiko komplikasi dan meningkatkan presisi ahli bedah.
Dalam konteks manufaktur, AR dapat memungkinkan pekerja untuk mempercepat proses perakitan dan meningkatkan pengambilan keputusan. Misalnya, kacamata AR dapat digunakan untuk memproyeksikan data, seperti tata letak, pedoman perakitan, lokasi kemungkinan kerusakan, atau nomor seri komponen, di bagian nyata, memfasilitasi prosedur kerja yang lebih cepat dan lebih mudah.
Sorotan:AR meningkatkan produktivitas di GE
General Electric menawarkan sekilas tentang bagaimana teknologi AR dapat memberdayakan manufaktur. Perusahaan saat ini sedang menguji coba penggunaan kacamata AR di fasilitas manufaktur mesin jetnya di Cincinnati. Sebelum menggunakan kacamata pintar ini, pembuat mesin jet sering kali harus menghentikan apa yang mereka lakukan untuk memeriksa manual mereka dan memastikan tugas dilakukan dengan benar.
Namun, dengan kacamata AR, mereka sekarang dapat menerima instruksi digital di bidang pandang mereka. Mekanik juga dapat mengakses video pelatihan atau menggunakan perintah suara untuk menghubungi pakar untuk mendapatkan bantuan segera.
Selama uji coba, GE melaporkan bahwa produktivitas pekerja yang menggunakan perangkat pintar yang dapat dikenakan meningkat hingga 11%, dibandingkan sebelumnya. Pada akhirnya, pendekatan ini dapat menawarkan potensi luar biasa untuk meminimalkan kesalahan, mengurangi biaya, dan meningkatkan kualitas produk.
Bahkan dengan contoh dari GE ini, kami masih belum memahami tentang penerapan AR dalam konteks manufaktur.
Lihat lebih dekat cara kerja kacamata AR GE:
Mengendarai Gelombang Manufaktur Digital
Dengan munculnya teknologi digital baru, sekarang adalah waktu yang menyenangkan bagi industri manufaktur. Gelombang teknologi baru membuka peluang bagi perusahaan untuk mengambil langkah menuju fleksibilitas, keberlanjutan, dan produktivitas yang lebih besar. Industri 4.0 juga memfasilitasi cara-cara baru bagi manusia dan mesin untuk bekerja bersama, memberdayakan bisnis untuk mencapai wawasan yang lebih luas, mengurangi risiko kesalahan, dan membuat keputusan yang lebih baik.
Pada akhirnya, Industri 4.0 akan mengakar di seluruh ekosistem manufaktur. Tetapi hanya dengan memahami dan memanfaatkan teknologi yang mendorong Industri 4.0, produsen akan tetap menjadi yang terdepan di era digital baru ini.