Kontrol Otomatisasi dan Pemodelan Tungku Busur Listrik
Kontrol Otomatisasi dan Pemodelan Tungku Busur Listrik
Electric Arc Furnace (EAF) merupakan proses utama dalam pembuatan baja berbasis scrap / DRI (direct reduction iron) dan rute proses pembuatan baja terpenting kedua dalam hal produksi baja global. Ini adalah proses utama untuk mendaur ulang skrap besi. Itu ditemukan pada tahun 1889 oleh Paul Heroult. Awalnya digunakan terutama untuk produksi baja khusus, tetapi memantapkan dirinya sebagai salah satu proses pembuatan baja utama di akhir abad ke-20.
Dibandingkan dengan rute pembuatan baja tanur sembur- tungku oksigen dasar, rute pembuatan baja EAF mengurangi konsumsi energi hingga 61% dan emisi karbon sekitar 77%. Efisiensi dan produktivitas proses telah meningkat secara dramatis melalui pengenalan perbaikan teknis seperti (i) peningkatan penggunaan oksigen, karbon, dan sumber energi kimia lainnya, (ii) terak berbusa, dan (iii) pasca-pembakaran karbon mono -oksida. Namun, potensi yang cukup besar untuk optimasi lebih lanjut tetap ada. Hal ini menjadi jelas dalam perbedaan antara permintaan energi teoritis sekitar 400 kWh per ton untuk peleburan dan pemanasan skrap dan konsumsi rata-rata aktual EAF saat ini yaitu sekitar 375 kWh per ton energi listrik dan jumlah energi listrik yang serupa. energi kimia, menghasilkan efisiensi total sekitar 50%.
Saat ini, EAF dioperasikan dengan peningkatan tegangan busur dan arus sekunder untuk meningkatkan produktivitas. Input daya hingga 300 MVA dicapai untuk EAF. Mengoperasikan daya busur tinggi seperti itu membutuhkan kontrol yang akurat dari proses pencairan. Busur, yang memancarkan kekuatan tinggi ke dinding tungku, menyebabkan kerusakan besar. Dengan mencegah perilaku yang tidak diinginkan tersebut, waktu henti dapat dipertahankan pada tingkat yang rendah dan produktivitas tungku yang tinggi dapat dipertahankan. Untuk mencapai tujuan ini, kontrol daya loop tertutup harus diatur. Kontrol daya seperti itu perlu bereaksi terhadap peristiwa yang terjadi dalam proses pencairan, khususnya pada dinding tungku yang tidak tertutup oleh skrap atau praktik terak berbusa yang sesuai. Poin penting adalah untuk mencapai informasi semacam ini tentang prosesnya.
Parameter yang diperlukan untuk analisis dan optimalisasi proses, bagaimanapun, dalam banyak kasus tidak dapat diukur secara langsung karena kondisi yang keras di dalam tungku. Misalnya, suhu dan komposisi lelehan dan terak hanya dapat ditentukan melalui pengukuran titik dan berpotensi dengan beberapa penundaan yang disebabkan oleh analisis sampel yang diperlukan. Sementara metode untuk pengukuran langsung dan terus menerus dari parameter ini sedang dikembangkan, mereka belum tersedia untuk sebagian besar tungku. Selain itu, uji coba instalasi yang diperlukan untuk mengevaluasi dampak dari strategi optimasi yang berbeda tidak mungkin dilakukan karena biaya yang mahal atau masalah keamanan. Oleh karena itu, model matematika adalah sumber informasi yang berharga mengenai parameter proses yang tidak diketahui. Simulasi juga dapat digunakan sebagai alternatif yang lebih murah, lebih cepat, dan lebih aman untuk uji coba pabrik. Untuk EAF, berbagai model telah dikembangkan dengan tujuan dan pendekatan pemodelan yang berbeda.
EAF dapat digambarkan sebagai reaktor kimia yang memanfaatkan listrik untuk mengubah skrap menjadi baja cair. Tren pengembangan tungku busur listrik adalah untuk mendapatkan produktivitas yang lebih tinggi dengan meningkatkan tegangan busur dan mencapai arus yang lebih tinggi untuk peleburan memo lebih cepat dan lebih efisien. Namun tegangan dan arus yang lebih tinggi dapat menyebabkan kerusakan luar biasa pada refraktori tungku jika busur tidak ditutupi dengan terak. Cara umum untuk mengontrol lelehan saat ini adalah dengan mengontrol tap trafo berdasarkan masukan energi. Ini berarti bahwa tidak ada informasi online yang digunakan untuk mengontrol proses dan operator secara manual menyesuaikan set point dengan informasi dari diagram operasional.
Kompleksitas yang berkembang dari proses EAF dalam kombinasi dengan peningkatan tuntutan produktivitas dan pengurangan dampak lingkungan memerlukan strategi pengendalian dengan mempertimbangkan dinamika sistem yang membutuhkan adaptasi titik operasi prasetel statis secara real-time. Juga, ketika produktivitas meningkat, operator dituntut untuk membuat keputusan lebih cepat. Dalam proses EAF yang 'canggih', otomatisasi diperlukan untuk membantu operator.
Otomatisasi konvensional EAF terutama menargetkan (i) otomatisasi rezim listrik, (ii) otomatisasi rezim termis, dan (iii) penempatan elektroda EAF. Sistem kontrol proses yang modern dan kuat memastikan operasi pabrik yang aman dan ramah pengguna bahkan dalam kondisi sulit. Ini memberikan keandalan dan ketersediaan tinggi untuk membuka jalan bagi proses yang lancar.
Solusi otomatisasi dalam pembuatan baja EAF ideal untuk EAF baru maupun yang sudah ada dalam berbagai ukuran. Mereka mengoptimalkan produksi berbagai tingkatan baja, termasuk baja karbon, baja tahan karat, dan baja khusus sambil mengakomodasi rasio pengisian variabel dari skrap, DRI, dan logam panas. Hal ini menghasilkan langkah-langkah koreksi perlakuan baja yang lebih sedikit, jumlah panas yang diturunkan secara minimum, dan kepatuhan yang tepat terhadap jadwal produksi yang ketat sebagai dasar untuk pengiriman tepat waktu ke unit pemrosesan hilir.
Kontrol proses otomatis didasarkan pada beberapa pengukuran waktu nyata misalnya suhu pada sistem pendingin, suara tungku, distorsi harmonik pada arus, getaran bejana tungku, dan analisis off gas. Penggunaan kontrol proses otomatis dapat menyebabkan pengurangan daya tepat waktu, optimalisasi karbon yang disuntikkan, stabilisasi busur, dan pengurangan waktu mati.
Mempertimbangkan kompleksitas yang besar dari prosedur khusus untuk pembuatan baja di EAF, operasi kompleks dari agregat teknologi ini menyiratkan secara sistematis meliputi langkah-langkah yaitu (i) mengukur dan mempertahankan keadaan teknologi tertentu (keadaan inersia) untuk agregat yang dapat dicapai melalui otomatisasi normal konvensional, dan (ii) otomatisasi kompleks EAF, yang bergantung pada pengendalian proses untuk memperoleh tujuan fungsi kriteria maksimum menurut model matematika.
Solusi otomatisasi EAF menggabungkan keunggulan sistem otomatisasi berbasis PLC (pengontrol logika yang dapat diprogram) (seperti kualitas dan stabilitas yang telah terbukti, biaya perangkat keras yang rendah, skalabilitas yang halus, kontrol proses yang andal, pengoperasian yang ramah pengguna, visualisasi yang jelas, dan alat teknik yang kuat ) dengan solusi teknologi spesifik yang disesuaikan dengan kebutuhan spesifik pabrik.
Otomatisasi dasar menggunakan sistem berbasis mikroprosesor berkecepatan tinggi untuk kontrol teknologi dan kontrol sekuensial. Sistem otomasi dibagi menjadi beberapa unit otomasi, yang dikoordinasikan untuk melaksanakan tugas-tugas yang diperlukan. Setiap unit otomatisasi terhubung ke periferal listrik terkait, biasanya menggunakan koneksi I/O (input-output) jarak jauh, untuk sensor dan penggerak. Tugas pengoperasian dan pemantauan yang dilakukan melalui HMI (human machine interface) adalah penyiapan informasi yang semakin banyak tentang proses sedemikian rupa sehingga operator menerima representasi pabrik yang jelas dan mudah dipahami. Sistem HMI mendukung operasi EAF yang sederhana dan sistematis.
Sistem kontrol proses EAF di Level 1 mencakup otomatisasi dasar dan fungsi kontrol teknologi untuk memungkinkan produksi baja EAF dengan cara yang efektif dan aman. Konfigurasi HMI yang ramah pengguna dan redundan dikombinasikan dengan penerapan perangkat kontrol canggih yang aman dari kegagalan memastikan ketersediaan tinggi dari sistem otomasi. Fitur khas dari kontrol proses EAF meliputi berikut ini.
Profil yang dapat disesuaikan – Konsep otomatisasi keseluruhan memungkinkan penentuan skema produksi individu untuk tap changer transformator, tap changer reaktor, kurva kontrol elektroda, burner, RCB (pembakar gabungan pemurnian) dan injektor yang meminimalkan tindakan operator.
Struktur Modular – Solusi standar yang sangat berkembang memudahkan penerapan logika dan komunikasi ke sistem eksternal seperti scrap yard, sistem dedusting, penanganan material, injeksi karbon / kapur, kontrol foaming slag, sistem penganalisis off-gas, dan pembangkit listrik.
Diagnostik sistem dan proses – Fungsi diagnostik seperti pemantauan kondisi, pelaporan panas/hari/bulan, dan perekaman tren mendukung pengoperasian EAF yang bebas masalah dan andal.
Simulasi perangkat lunak – Semua fungsi yang diimplementasikan disimulasikan sesuai dengan aturan operasional tertentu. Ini mencakup mis. stasiun hidrolik, gerakan, dan operasi proses. Simulasi siklus panas lengkap memverifikasi fungsionalitas perangkat lunak otomatisasi yang benar.
Lebih lanjut, solusi otomatisasi modern yang canggih juga menggunakan peralatan pengukuran tercanggih. Peralatan pengukuran tipikal, seperti suhu/tombak tangan Celox digunakan sebagai alat standar untuk pembuatan baja listrik. Untuk lebih meningkatkan kinerja EAF, beberapa sistem pengukuran yang dapat digunakan adalah (i) pengukuran suhu tanpa kontak, (ii) sistem analisis off-gas EAF kontinu, dan (iii) penggunaan sistem robot untuk suhu dan Celox pengukuran dan pengambilan sampel.
Sistem pengukuran suhu nirkontak yang baru, yang terintegrasi penuh ke dalam teknologi RCB, menyediakan metode yang sempurna untuk memprediksi waktu penyadapan yang tepat selama penyalaan. Suhu yang diukur dievaluasi dengan model kontrol untuk hasil yang dapat diulang dan proses yang konsisten. Sistem pengukuran suhu nirkontak mencakup tiga fungsi utama yaitu (i) mode pembakar di mana selama waktu penyalaan sistem pengukuran suhu nirkontak dapat digunakan sebagai pembakar untuk memanaskan skrap menggunakan berbagai pengaturan daya, (ii) mode tombak di mana sistem beralih untuk memberikan aliran oksigen supersonik segera setelah potongan dipanaskan ke titik di mana terjadi reaksi antara karbon, besi, dan oksigen, (iii) mode suhu di mana sistem beralih dari mode tombak ketika tingkat homogenisasi yang ditentukan fase cair tercapai, dan siklus pengukuran suhu dapat dimulai. Gambar 1 menunjukkan skema sistem suhu RCB.
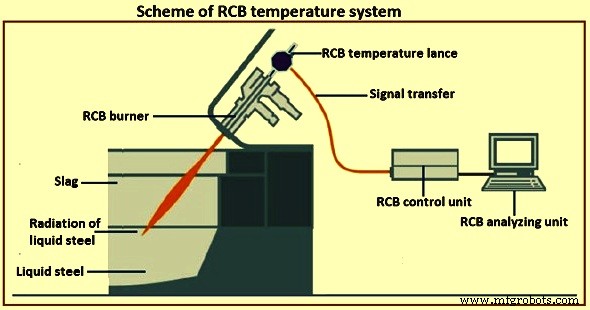
Gbr 1 Skema sistem suhu RCB
Berdasarkan metode di atas tidak perlu tombak untuk mengukur suhu. Hal ini menghasilkan tingkat keselamatan yang tinggi bagi operator dan mengurangi biaya konsumsi. Masukan konsumsi energi berkurang. Sistem ini memungkinkan prediksi sadapan yang tepat dengan beberapa manfaat termasuk, (i) peningkatan produktivitas melalui pengurangan power-off, (ii) hasil yang dapat diulang untuk proses yang konsisten, (iii) penurunan biaya operasi dan konsumsi, dan (iv) penurunan input konsumsi energi dengan ketukan yang akurat.
Sistem analisis off-gas EAF berkelanjutan adalah solusi untuk pengukuran off-gas EAF, yang melakukan analisis gas kontinu sepenuhnya otomatis. Perangkat pengambilan sampel gas ditempatkan di saluran off-gas EAF primer berpendingin air. Off-gas terus dianalisis selama power on time dan selama waktu power off dengan pembersihan dan pembersihan probe sampel yang sepenuhnya otomatis dilakukan. Oleh karena itu, sistem ini memungkinkan pengoperasian yang hampir bebas perawatan, bahkan di bawah kondisi lingkungan yang sangat panas, korosif, dan sangat berdebu pada posisi pengambilan sampel langsung setelah siku EAF.
Sistem otomasi biasanya memiliki struktur modular. Ini mencakup setiap level dari kontrol pabrik dasar (Level 1) hingga integrasi dengan fungsi pelacakan produksi dan manajemen pesanan manufaktur yang sedang berlangsung (Level 3 dan Level 4). Modul proses kontrol khusus mengoptimalkan operasi dan memberikan dukungan penting kepada pekerja lantai toko dan teknolog proses. Sistem otomatisasi lini bisnis pabrik dapat dikombinasikan dengan solusi teknologi mutakhir untuk optimalisasi penghematan energi dan produktivitas. Selain itu, solusi otomatisasi menggunakan sensor inovatif, yang bekerja sama dengan model kontrol canggih untuk kontrol waktu nyata yang dinamis.
Kontrol proses EAF memberikan solusi end-to-end yang sepenuhnya otomatis untuk kontrol elektroda di EAF tiga fase. Ini mengatur dan secara dinamis menyesuaikan busur listrik dan membuat penggunaan elektroda yang paling efisien. Solusinya mengandalkan kecerdasan buatan untuk mengoptimalkan proses peleburan. Ini juga mencakup modul kontrol pelelehan dengan program peleburan untuk memastikan reproduksi akurat dari proses peleburan untuk memastikan produktivitas tungku maksimum. Kontrol elektroda dan unit tambahannya dapat diintegrasikan ke dalam lingkungan dan arsitektur sistem apa pun. Ada tiga sistem kontrol dasar untuk kontrol proses di EAF. Ini adalah (i) sistem kontrol elektroda, (ii) sistem kontrol terak berbusa, dan (iii) sistem peleburan skrap berbasis kondisi.
Sistem kontrol elektroda – Ini adalah sistem kontrol utama untuk EAF. Pendekatan menuju kontrol daya otomatis biasanya bergantung pada evaluasi arus busur dan tegangan. Teknik pengukuran lainnya seringkali tidak dapat diterapkan karena kondisi ekstrim di lingkungan tungku.
Sistem kontrol elektroda adalah sistem kontrol elektroda loop tertutup. Tugas dasarnya adalah mengontrol posisi elektroda, lebih spesifik untuk mempertahankan titik operasi listrik. Kinerja tugas yang sangat mendasar ini pertama-tama mempengaruhi beberapa indikator kinerja utama (KPI) dari bengkel peleburan baja, seperti konsumsi energi listrik spesifik, konsumsi elektroda, dan produktivitas, dll. Kinerjanya juga penting untuk mengurangi tekanan mekanis dan sistem hidrolik serta untuk pembatasan gangguan jaringan listrik. Masuk akal bahwa kinerja terbaik dari tugas dasar ini dicapai dengan kontrol elektroda berbasis impedansi. Fungsi tambahan dasar untuk mengurangi arus lebih, hubung singkat, dan kerusakan elektroda adalah yang paling canggih dan meminimalkan waktu henti. Adaptasi terhadap karakteristik sistem aktuasi diperlukan untuk kinerja terbaik, yaitu karakteristik katup hidrolik.
Fungsi dasar kontrol elektroda yang disebutkan di atas pasti mempengaruhi kinerja EAF. Namun, kinerja tungku sangat tergantung pada pemilihan titik operasi listrik. Dengan mempertimbangkan desain tungku secara keseluruhan, diagram operasional disiapkan, juga disebut profil peleburan, atau program daya. Ini digunakan untuk menyediakan set-point listrik tungku, yaitu tap transformator, tap reaktor, dan set-point impedansi. Diagram ini biasanya bergantung pada masukan energi total. Fungsionalitas ini dicakup oleh sistem Level 2 atau solusi serupa. Pemilihan dan urutan set-point dalam diagram operasional ini berdampak langsung pada KPI EAF.
Saat ini, modul tambahan untuk kontrol elektroda digunakan untuk menyesuaikan titik setel yang disediakan oleh diagram operasional untuk memenuhi kondisi leleh aktual di dalam tungku, yaitu dengan mengevaluasi beban termal panel berpendingin air. Modul optimasi dapat digunakan untuk meningkatkan input daya ke tungku dengan menyesuaikan titik setel impedansi secara dinamis dengan kemajuan peleburan. Biasanya, operator tungku masih bertanggung jawab untuk mengambil tindakan kontrol lebih lanjut berdasarkan persepsi subjektifnya tentang emisi suara dan kesan visual tungku.
Sistem kontrol terak berbusa – Untuk operasi terak berbusa otomatis, ada beberapa pendekatan yang menggunakan pengukuran suara. Sistem kontrol terak berbusa adalah sistem sensor. Ini didasarkan pada kebisingan yang lahir dari struktur dan merupakan pendekatan untuk mengevaluasi jumlah terak berbusa di EAF. Sehubungan dengan tren dan reproduktifitas, metode ini telah terbukti berhasil mengikuti situasi terak berbusa nyata di tungku busur. Gambar 2 menunjukkan sistem kontrol terak berbusa di EAF.
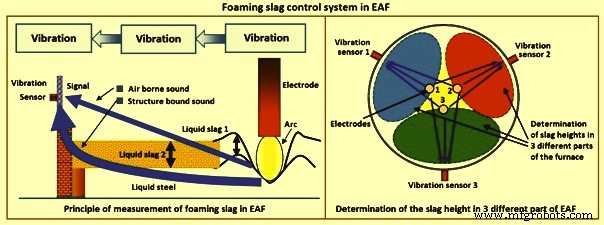
Gbr 2 Sistem kontrol terak berbusa di EAF
Sistem kontrol terak berbusa mengevaluasi propagasi suara dari busur listrik, tempat suara dibuat, ke cangkang tungku, di mana getaran yang dihasilkan dideteksi oleh sensor akselerasi, juga disebut sensor suara yang ditanggung struktur. Busur listrik berfungsi sebagai sumber akustik. Dengan menghitung redaman propagasi suara, ketinggian terak berbusa ditentukan.
Keuntungan besar dari metode ini adalah untuk menentukan tidak hanya tinggi terak rata-rata di sekitar elektroda, tetapi terutama ketinggian spesifik di area lengkap antara masing-masing elektroda dan cangkang tungku. Tampilan satu dimensi sebenarnya diperluas oleh sistem kontrol terak berbusa ke pengukuran dua dimensi dari distribusi ketinggian terak. Karena pemasangan tiga sensor yang berlawanan dengan elektroda yang sesuai, ketinggian terak dapat ditentukan secara independen di tiga zona tungku (Gbr 2). Oleh karena itu distribusi spasial ketinggian terak dapat dievaluasi dan ditampilkan dalam visualisasi. Pada skala waktu pembusaan terak dibagi menjadi periode yang berbeda. Periode ditentukan oleh input energi spesifik. Mereka dicirikan oleh pengaturan ketinggian terak referensi yang berbeda.
Tiga sensor suara yang ditanggung struktur, masing-masing ditugaskan ke satu segmen elektroda, digunakan untuk merekam sinyal. Mereka dipasang ke cangkang tungku dengan mengelas tiga pelat adaptor ke panel yang berlawanan dengan fase / elektroda masing-masing. Pelat adaptor diposisikan sekitar 800 mm di atas level bak baja. Sensor dihubungkan menggunakan kabel sinyal berpelindung suhu, yang harus dilindungi dari panas yang berlebihan dan kerusakan mekanis. Untuk memudahkan penggantian bejana tungku, kabel dihubungkan menggunakan soket Harting atau kotak konektor yang dipasang pada atau dekat dengan bejana tungku. Selain sinyal suara yang ditanggung struktur, sinyal arus direkam dengan menggunakan kumparan Rogowski. Sinyal sampel berkecepatan tinggi diteruskan ke akuisisi data dan modul komputasi.
Tingkat terak berbusa dihitung berdasarkan kombinasi kebisingan yang lahir dari struktur dan sinyal arus. Dengan metode deteksi, personel operasi berada dalam posisi yang lebih baik untuk memeriksa kualitas dan reproduktifitas kontrol proses dalam fase terak berbusa dengan tingkat akurasi yang tinggi. Proses dapat dioptimalkan dengan memperhatikan stabilitas, waktu proses, dan konsumsi daya atas dasar ini.
Peluang luar biasa dari pengukuran spasial yang benar dari ketinggian terak adalah untuk mengatur injeksi karbon dengan kontrol individual dari katup karbon untuk mencapai distribusi terak yang seragam. Untuk pengaturan injeksi karbon, telah dikembangkan sistem kendali berdasarkan algoritma Fuzzy. Hal ini memungkinkan penerapan aturan yang sesuai dengan mudah untuk injeksi karbon yang dapat disesuaikan dengan situasi spesifik dari konfigurasi tungku tertentu. Karena katup karbon biasanya tidak dirancang untuk kontrol analog kontinu, sinyal keluaran diubah menjadi modulasi lebar pulsa, yang menghasilkan pasokan karbon yang sesuai.
Karbon disuntikkan dalam mode modulasi berdenyut, di mana lebar dan frekuensi pulsa dikendalikan oleh sistem kontrol terak berbusa untuk menyuntikkan jumlah karbon yang tepat dari masing-masing dari tiga katup. Hal ini memungkinkan sistem kontrol terak berbusa untuk menerapkan jumlah karbon yang dibutuhkan secara tepat untuk setiap katup guna mencapai ketinggian terak yang paling seragam, memadai, dan stabil. Selama periode akhir, di mana terak berbusa sebagian dicurahkan, ketinggian terak diturunkan dan berfluktuasi
Sistem kontrol terak berbusa memastikan bahwa tingkat pembusaan terak secara merata tinggi selama proses berbusa. Akibatnya, efisiensi energi busur meningkat sementara pada saat yang sama jumlah karbon yang disuntikkan berkurang. Sistem ini juga menawarkan dasar yang andal untuk kontrol terak berbusa loop tertutup berdasarkan penentuan level terak secara tepat dan memasok sinyal untuk memicu tombak karbon / oksigen atau pembakar koheren yang dipasang di tungku.
Sistem peleburan bekas berdasarkan kondisi – Sistem peleburan skrap berbasis kondisi secara dinamis mengontrol masukan energi listrik selama periode peleburan skrap dan sebagian juga selama periode rendaman datar dengan segera bereaksi terhadap keadaan skrap dan lelehan. Ini menghasilkan pengoptimalan proses peleburan berbasis kondisi.
Sistem peleburan skrap berbasis kondisi menggunakan perangkat keras yang sama seperti yang dijelaskan sebelumnya untuk sistem kontrol terak berbusa. Mirip dengan sistem kontrol terak berbusa, sistem peleburan sisa berbasis kondisi mengukur propagasi suara dari busur listrik, tempat suara dibuat, ke cangkang tungku, di mana getaran yang dihasilkan dideteksi oleh sensor akselerasi. Dengan mengukur arus dari tiga busur dan getaran dinding yang berlawanan dengan elektroda, dua sinyal status berdasarkan kondisi yang berbeda dihitung secara dinamis (i) pelindung panel oleh skrap atau terak, (ii) status skrap di dasar busur, terutama penampilan potongan berat 'dingin'.
Kedua sinyal ini mendukung karakterisasi proses peleburan. Dikombinasikan dengan informasi tambahan tentang tungku, kontrol berbasis kondisi baru dari input energi listrik direalisasikan. Informasi tambahan termasuk beban termal panel tungku, masukan energi spesifik, data listrik, dan kondisi batas lebih lanjut dari proses. Sebuah pengontrol mengatur tegangan sekunder dengan mengganti keran transformator, menghitung titik setel impedansi individu baru untuk tiga fase, dan mengganti reaktansi seri. Pengontrol memaksimalkan input daya dengan mempertimbangkan pelindung dinding aktual dan beban termal.
Fitur utama dan keuntungan dari sistem peleburan skrap berbasis kondisi adalah kemampuannya untuk mendeteksi hilangnya pelindung dinding jauh lebih awal dibandingkan dengan kenaikan suhu yang dihasilkan dari panel, yang dihasilkan dari dampak radiasi yang meningkat. Jeda waktu sekitar 60 detik ini memungkinkan sistem peleburan skrap berbasis kondisi untuk bereaksi dengan mendistribusikan daya masing-masing radiasi dari tiga busur. Redistribusi langsung ini memoderasi atau menghindari dampak termal dari panel terkait.
Pengontrol sistem peleburan bekas berbasis kondisi bereaksi dalam dua cara berbeda pada hilangnya pelindung dinding dan beban termal panel. Pertama-tama, pada skala waktu yang lama ketika hilangnya pelindung dan peningkatan suhu yang diharapkan atau terukur berlangsung untuk waktu yang lebih lama atau sangat berbeda, transformator di-tap down. Oleh karena itu tegangan sekunder disesuaikan. Di sisi lain, keran transformator meningkat ketika kondisi leleh memungkinkan, mis. pada pelindung busur tinggi dan suhu panel rendah.
Sakelar tap transformator diaktifkan oleh loop histeresis untuk menghindari operasi pensaklaran yang tidak perlu. Kedua, pada skala waktu yang singkat, sinyal input yang sama dievaluasi untuk mengontrol titik setel impedansi dari tiga fase secara individual, yang menghasilkan operasi tungku listrik asimetris. Berdasarkan perisai yang dihitung dan prediksi atau pengukuran suhu panel, pengontrol fuzzy menghitung distribusi daya radiasi yang optimal. Menggunakan model radiasi baru yang dikembangkan dan model listrik analitik, titik setel impedansi yang sesuai dihitung dalam loop berulang untuk memenuhi distribusi radiasi optimal yang terbaik. Jadi redistribusi daya radiasi yang hampir segera dapat dicapai untuk mengurangi atau menghindari dampak termal secara instan.
Keuntungan utama dari sistem peleburan skrap berbasis kondisi adalah hasil dalam operasi yang lebih halus dan lebih stabil dengan operasi sakelar tap transformator yang lebih sedikit dan input energi yang meningkat setiap kali diizinkan oleh situasi pelelehan.
Sistem pakar EAF
Sistem pakar EAF telah dipahami sebagai pengawas kontrol proses terintegrasi. Secara otomatis mengenali penyimpangan dari perilaku yang diharapkan dan menyetel ulang program peleburan, bertindak pada perencanaan tenaga listrik, pada paket kimia, pada metalurgi terak dan baja. Kendala peralatan diintegrasikan ke dalam kontrol. Sistem pakar EAF bertindak sebagai pengawas proses yang mengintegrasikan otomatisasi dasar dan fungsi teknologi untuk memungkinkan produksi baja EAF dengan cara yang efektif dan aman, mendukung setiap operasi dari fase pengisian hingga prosedur penyadapan. Karena pemantauan proses berbasis sensor dan kamera yang ekstensif, generasi baru mimbar mesin dapat dipasang di posisi sembarang dan tidak memerlukan jendela khusus untuk mendapatkan umpan balik visual langsung dari proses, meningkatkan keselamatan operator dan kesadaran proses.
Sistem pakar EAF juga dapat mengintegrasikan sejumlah teknologi yang berdiri sendiri untuk lebih memaksimalkan waktu produktif, faktor pemanfaatan, dan keamanan, melalui unit mekatronik yang dikendalikan dari jarak jauh. Sistem pakar EAF adalah evolusi terbaru dari konsep EAF untuk secara otomatis mengontrol setiap tahap proses peleburan, mulai dari perencanaan tenaga listrik hingga optimalisasi pembakaran serta manajemen metalurgi terak dan baja untuk setiap operasi yang diperlukan dalam siklus EAF.
Sistem pakar EAF melakukan pra-perhitungan panas lengkap, menelusuri praktik peleburan yang ditentukan. Ini memberikan gambaran tentang proses peleburan dan kondisi baja pada penyadapan dan secara otomatis menyesuaikan profil daya dan penambahan material untuk mengoptimalkan proses. Ini memutuskan titik setel muatan untuk pemuatan ember bekas yang tepat. Perhitungan pengoptimalan biaya memilih jenis scrap dan menentukan jumlah yang dibutuhkan serta jumlah total DRI yang akan ditambahkan. Ini juga menentukan agen pembentuk terak sehubungan dengan massa terak minimum yang diberikan dan kebasaan tujuan. Selanjutnya, ini menghitung jumlah aditif paduan yang dioptimalkan biaya untuk tungku atau sendok sadap.
Sistem pakar EAF menentukan jumlah energi listrik yang diperlukan untuk melelehkan bahan yang disiapkan dan diisi dan untuk memanaskan bak baja hingga suhu penyadapan, dengan mempertimbangkan masukan energi dari oksigen yang ditiup. Sistem pakar EAF menyediakan pemantauan on-line konsumsi daya dan transmisi perkiraan konsumsi daya yang menargetkan pencegahan beban puncak dan tarif tarif tinggi. Untuk tungku dengan fasilitas pengumpanan DRI berkelanjutan, laju pengumpanan DRI dikontrol secara dinamis untuk menargetkan suhu baja yang konstan, dengan mempertimbangkan suhu DRI.
Sistem pakar EAF memiliki mesin penambangan data yang kuat yang biasanya dikembangkan dan dirancang khusus untuk aplikasi kontrol. Variabel data yang relevan dikumpulkan dan secara otomatis diklasifikasikan ke dalam hubungan terstruktur. Analisis proses statistik yang luas diterapkan pada sejumlah besar informasi, membedakan dari perilaku dan anomali yang konsisten yang diharapkan. Penyimpangan yang terus-menerus dari kondisi proses yang diharapkan mengarah pada optimalisasi berkelanjutan dari pembakaran karbon mono-oksida dan penggunaan bahan bakar yang efisien, dengan menyesuaikan profil leleh dengan kondisi operasional variabel. Kontrol terintegrasi dari proses peleburan secara keseluruhan, bersama dengan pelacakan waktu nyata dari variabel tungku yang menguraikan penyimpangan yang relevan dari kondisi proses yang diharapkan, memberikan peluang yang signifikan untuk meningkatkan efisiensi dan produktivitas energi.
Analisis off-gas on-line real-time, melalui sistem laser in-situ, mempromosikan pelacakan proses dan memungkinkan pengoptimalan lebih lanjut dengan kontrol loop tertutup yang layak yang bekerja pada bahan bakar dan oksigen pasca pembakaran. Analisis off-gas respon cepat memberikan informasi umpan balik yang cepat untuk pengaturan injeksi oksigen selama tahap pemurnian, mengontrol dekarburisasi baja dan membatasi oksidasi rendaman pada saat yang bersamaan.
Inti dari sistem pakar EAF adalah 'model leleh' yang secara otomatis mengidentifikasi penyimpangan dari variabel kontrol proses dan mengoreksinya untuk menghindari kehilangan atau pemborosan sumber energi yang tersedia. Ini mengoordinasikan data, dikumpulkan secara real-time oleh beberapa sensor terpasang, dan variabel proses yang dihitung berdasarkan profil leleh statis yang telah ditentukan sebelumnya. 'Model lelehan' mengoordinasikan kontrol loop tertutup yang terintegrasi dengan model untuk daya listrik dan model untuk paket bahan kimia. Ini mengelola interaksi profil peleburan listrik dan kimia untuk mencapai optimalisasi penggunaan energi, serta kontrol metalurgi terak dan baja, yang melibatkan, antara lain, cakupan busur dengan manajemen terak berbusa, optimalisasi pasca-pembakaran, pengurangan konsumsi energi listrik, dan optimasi konsumsi oksigen dan karbon. Gambar 3 menunjukkan kontrol loop tertutup dari sistem pakar model leleh.
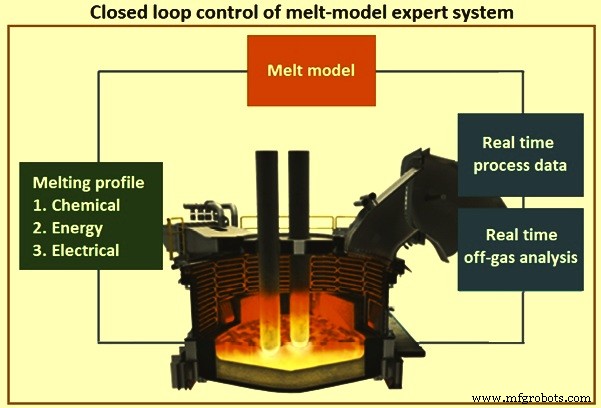
Gbr 3 Kontrol loop tertutup dari sistem pakar model leleh
Sistem pakar EAF beradaptasi dengan kondisi pengoperasian yang terus berubah sambil menjaga kinerja EAF tetap tinggi. Ini mengintegrasikan sistem kontrol elektroda, sistem kontrol terak berbusa, dan sistem peleburan skrap berbasis kondisi.
Manfaat utama dari sistem pakar adalah (i) pengurangan waktu tap-to-tap hingga 10%, (ii) pengurangan konsumsi energi hingga 5%, (iii) pengurangan biaya bahan paduan hingga 5%, dan (iv) mengurangi biaya energi dengan menghindari tingkat tarif puncak.
Pemodelan proses pembuatan baja EAF
Model proses adalah 'algoritma untuk memprediksi perilaku sistem terbuka atau tertutup'. Ini memungkinkan kontrol prediktif dan bantuan operator, optimalisasi proses off-line, pemahaman yang lebih baik tentang fenomena fisik yang mendasarinya, dan estimasi parameter on-line yang tidak dapat ditentukan secara langsung melalui pengukuran. Istilah model proses mengacu pada model deterministik berdasarkan hubungan fisik dan termodinamika, dan dengan demikian tidak termasuk pendekatan statistik murni.
Saat ini sebagian besar pembuatan baja EAF menggunakan sistem otomatisasi Level 1 dan Level 2. Dalam sistem otomasi ini, ada persyaratan model proses. Selama siklus produksi, sejumlah besaran penting tidak diketahui atau tidak dapat diukur karena alasan mendasar, seperti (i) suhu saat ini (rata-rata) bahan padat (scrap, DRI, dll.) tidak dapat diamati (ii) arus melt and slag temperature are difficult of measure, (iii) the current mass of the melt in the furnace cannot be measured.
The process model (for on-line and off-line use) is an important part of the EAF process and operation optimization cycle (Fig 4). The instrumentation of the furnace (weighting of scrap, and DRI etc.) continuously delivers measurement data during the operation which is fed into the model. To enhance the models’ abilities to predict important parameters like melt mass and temperature, new or more precise measurements can be implemented. The more precise data gives than better opportunities to test and furthermore enhance the model. Such more detailed or accurate models allow better control during the operation (on-line model) or the development of optimized process operation modes.
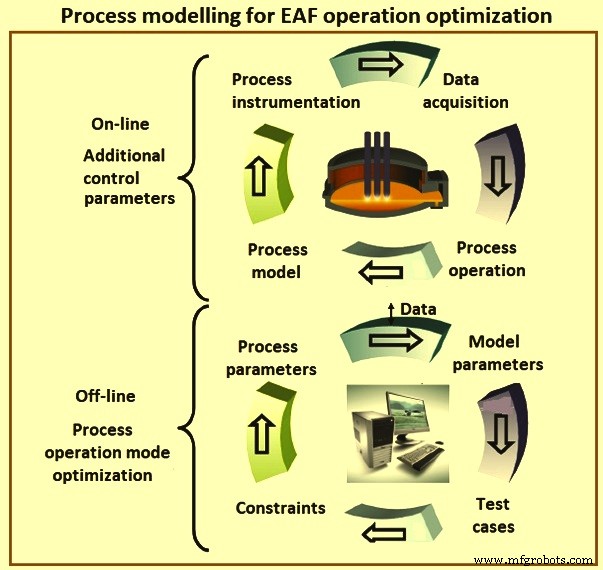
Fig 4 Process modelling for EAF operation optimization
The instrumentation of the EAF allows for a quantitative time dependent measurement of the energy and mass inputs. This data can be used for on-line or off-line modelling of the melt-down process. EAF process models have proven to be useful for improving process understanding and control as well as resource and energy efficiency by providing information which cannot be measured directly during the process due to the extreme conditions inside the furnace.
The use of on-line process models can hence enhance the knowledge on the current process state and thus support optimized process operation by providing additional input data for process control. Additionally, these models can use extrapolated input data to predict the future trends of the process variables. The same models can be used off-line with real or artificial process operation data to optimize the plant operation or to analyze the impact of process innovations. During the installation and optimization of such a process model the requirements of the model justify and support the implementation of advanced measurement systems, e.g. in order to get precise data on the energy and mass inputs into the furnace.
In the case of complex processes such as the EAF process, analytical models are normally more difficult to develop than the statistical models and may not reach the same degree of accuracy. They do, however, allow for extrapolation and are transferable since the physical and thermodynamic description is more universal.
The development of EAF models started in 1974 and in simpler forms and they became state-of-the-art within the following decades. The model developments have been undertaken into several directions, e.g. (i) determination of overall process characteristic and process control, (ii) CFD (computational fluid dynamics) modelling of the off-gas system or the heat transfer inside the furnace, and (iii) modelling of meltdown and slag chemistry and slag foaming.
Modelling and optimization of the EAF process constitutes a complex task due to the large number of variables such as the different charge materials, the share of different energy carriers, and the target composition and temperature. The different process phases, discontinuous changes during charging of material and many variations of the process with different furnace types, feed-stocks, desired steel qualities, and operation strategies have led to the development of various modelling approaches. A number of models have been developed using different approaches both for the complete process as well as local phenomena or single process phases.
Due to the wide range of different applications of modelling the EAF and the complexity of the process, numerous approaches have been applied to derive models for the process. There are purely statistical or data-driven models, including neural networks, used, for example, to evaluate the power consumption or the electrical system of an EAF. Another class of models for the evaluation of EAF energy consumption uses a statistical approach based on parameters which are determined using physical relationships such as the expected power delivery from the use of oxygen or natural gas.
Process models have been developed not only for the complete process but also to describe specific phenomena within the EAF, for example, the heat transfer at the electric arc, the reaction of injected carbon with the slag, or the influence and potential of energy recovery within the off-gas system. In some cases these have then been incorporated into more comprehensive EAF process models.
The process models are normally based on lumped zones with no spatial discretization except for the scrap charge which is discretized into multiple zones in some models. Heat and mass flows are exchanged between these zones and the surroundings and chemical reactions are normally considered within certain zones. Energy and mass balances are then used to track the temperature and composition of each zone. While most of these process models are dynamic, pseudo-dynamic approaches based on predefined process steps have also been proposed.
The models use different approaches, but have some important common properties namely (i) the physical conservation laws of mass, energy, and species are derived and solved, (ii) the general numerical method is to set-up and solve a set of non-linear ordinary differential equations (in most cases the small explicit integration scheme is used), (iii) the models need initial values and (in general time dependent) data for the time dependent inputs like electrical inputs, chemical inputs and mass loads (scrap, DRI etc.) etc.