Faktor-faktor yang mempengaruhi Sinter dan Proses Sintering
Faktor yang mempengaruhi Sinter dan Proses Sintering
Proses sintering digunakan untuk menggumpalkan campuran fine ore bijih besi, return fine, flux, dan coke dengan ukuran partikel kurang dari 10 mm, sehingga sinter yang dihasilkan dengan ukuran screened 5 mm sampai 30 mm dapat menahan kondisi tekanan dan temperatur di dalam blast furnace (BF). Proses sintering butiran halus bijih besi terutama dikembangkan untuk mengubah butiran halus yang dihasilkan di pertambangan dan mengubah butiran halus ini menjadi produk yang cocok untuk pengisian ke BF.
BF membutuhkan sinter berkualitas tinggi dengan kekuatan tinggi, kandungan butiran halus serendah mungkin, ukuran rata-rata yang baik, RDI (indeks degradasi reduksi) rendah, RI tinggi (indeks reducibility), kadar butiran halus, ukuran sinter terkalibrasi rata-rata yang baik, dan sedikit variasi dalam komposisi kimia untuk beroperasi dalam rezim kondisi mapan. Kontrol kualitas sinter, melalui sintering yang memadai, penting untuk mengoperasikan BF dengan bahan bakar rendah dan laju operasi yang stabil.
Proses sintering didasarkan pada perlakuan lapisan campuran mentah (butiran halus bijih besi, butiran halus kembalian, dan fluks dll.) dengan adanya butiran halus kokas dengan aksi pembakar yang ditempatkan di permukaan lapisan. Dengan cara ini, pemanasan terjadi dari bagian atas ke bagian bawah. Lapisan campuran mentah terletak di atas sistem untai dan sistem pembuangan memungkinkan seluruh ketebalan untuk mencapai suhu yang sesuai untuk pelelehan sebagian campuran, dan aglomerasi berikutnya. Dalam sistem Dwight-Lloyd, jeruji sintering adalah rantai kontinu dengan panjang dan lebar yang besar, dibentuk oleh gabungan serangkaian gerbong palet yang membuat untaian sintering.
Di pabrik baja terintegrasi, proses sintering memainkan peran penting dalam menyediakan bahan baku ke BF. Dari sudut pandang sumber daya alam, proses sintering adalah teknologi utama yang memungkinkan daur ulang bahan limbah pabrik (produk sampingan atau debu) yang dihasilkan di dalam fasilitas pabrik baja lainnya. Prosesnya kompleks yang melibatkan berbagai fenomena fisik dan kimia. Bahan baku yang digunakan dapat sangat bervariasi, mulai dari bijih besi hingga daur ulang debu dan agen fluxing. Sumber daya alam bijih besi sangat bervariasi tergantung pada komposisi mineral dan teknologi penambangan yang diterapkan untuk menghasilkan bahan umpan sinter.
Proses sintering bijih besi halus adalah proses metalurgi yang dilakukan pada mesin sintering. Lebar dan panjang untai tergantung pada kapasitas mesin dan bervariasi untuk setiap pabrik baja. Ini pada dasarnya adalah proses aglomerasi yang dicapai melalui pembakaran. Energi proses, dari urutan 360 juta kalori hingga 480 juta kalori per ton sinter, dipasok terutama oleh pembakaran kokas. Flowsheet proses sintering ditunjukkan pada Gambar 1.
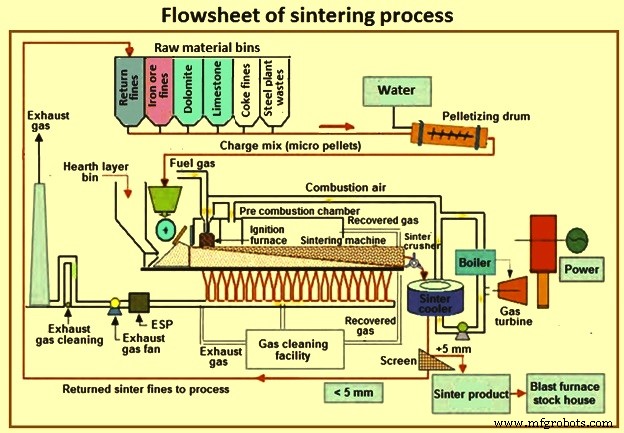
Gbr 1 Flowsheet proses sintering
Denda bijih besi adalah bijih alami dengan ukuran 0 mm sampai 10 mm. Campuran mentah (juga disebut campuran sinter) dibuat dengan jumlah yang ditimbang dari bijih besi halus, batu kapur, dolomit, pasir atau butiran kuarsit (fluks), bahan bakar padat (angin coke atau antrasit) dan limbah metalurgi (debu yang terkumpul, lumpur dan penggilingan). skala dll). Campuran sinter ini ditambahkan dengan air (6% sampai 8%) dan butiran halus sinter kembali kemudian digranulasi atau dipelet dalam drum yang berputar sebelum di-charge sebagai bed pada moving strand dari mesin sintering. Campuran butiran terus diisi bersama-sama dengan sinter yang dikembalikan dari ukuran kecil dari proses pengayakan untuk membentuk lapisan tebal sekitar 300 milimeter hingga 500 milimeter.
Sintering adalah proses yang berkelanjutan. Untai sinter dibentuk oleh serangkaian palet, yang masing-masing memiliki dinding samping dan jeruji permeabel. Campuran butiran dimuat ke parutan untai sinter yang permeabel. Pelet yang dimuat dengan campuran sinter berbutir, lewat di bawah kap pengapian, dikenai hisap aliran ke bawah, dimiringkan, dan kemudian kembali ke posisi pemuatan.
Saat untai bergerak maju, partikel bahan bakar pada lapisan permukaan atas pertama kali dinyalakan dalam tungku oleh pembakar gas bahan bakar (gas BF atau oven kokas campuran dan gas BF). Gas panas, yang dihasilkan oleh pembakaran dengan udara, kemudian disedot melalui unggun yang dikemas dari kotak angin yang dilengkapi dengan blower yang ditempatkan di bawah jeruji. Untaian terus bergerak maju dan bagian depan yang menyala atau pembakaran berlangsung secara bertahap ke bawah melalui tempat tidur sampai ujungnya tercapai. Pembakaran halus kokas atau bahan berkarbon lainnya dimulai di bagian atas lapisan, dan saat bergerak, pita bagian depan pembakaran yang relatif sempit (bagian depan api) bergerak ke bawah melalui lapisan, memanaskan setiap lapisan secara berurutan. Di tempat tidur butiran dipanaskan hingga 1.250 derajat C hingga 1.350 derajat C untuk mencapai pelunakan dan kemudian meleleh sebagian.
Beberapa reaksi kimia dan transformasi fase terjadi di dalam unggun, bagian dari bahan meleleh ketika suhu lokal mencapai suhu leleh (titik bakar) dan saat bergerak, fenomena re-solidifikasi dan transformasi fase terjadi dengan perubahan yang cukup besar pada komposisi fase. dan sifat fisik termo. Dalam rangkaian reaksi ini dihasilkan bahan semi cair yang, dalam pendinginan berikutnya, mengkristal menjadi beberapa fase mineral dengan komposisi kimia dan morfologi yang berbeda yang terutama terdiri dari hematit, magnetit, ferit, dan gangue yang sebagian besar terdiri dari kalsium silikat. Gambar 2 menunjukkan siklus termal material di dudukan sinter.
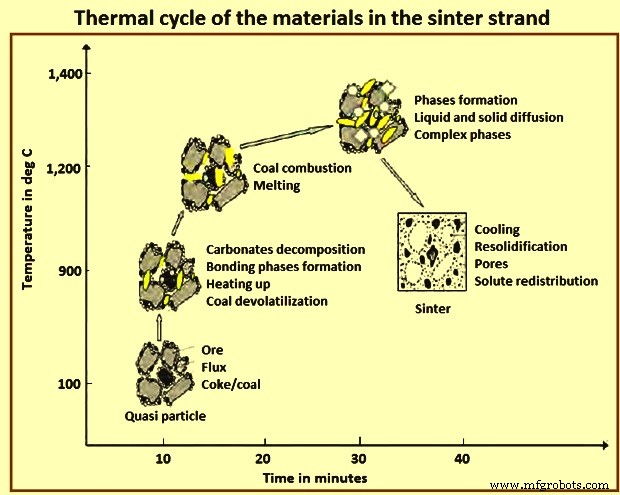
Gbr 2 Siklus termal material di dudukan sinter
Kecepatan untai dan aliran udara yang dihisap dikontrol untuk memastikan bahwa 'terbakar' (titik di mana lapisan bahan bakar yang terbakar mencapai dasar untaian) terjadi sesaat sebelum sinter dibuang. Suhu proses sintering terutama dikendalikan oleh pembakaran partikel bahan bakar.
Selama proses sintering, terdapat zona-zona yang berbeda pada strand mesin sinter. Zona-zona dari sisi pengisian ini adalah zona basah, zona pemanasan dan pengeringan, zona pembakaran dan zona produk. Di zona pembakaran, fase cair terbentuk antara bijih besi, fluks dan elemen lainnya dan partikel bijih besi yang tidak bereaksi diikat bersama oleh cairan. Produk akhir 'sinter' adalah material padat berpori yang memiliki kekuatan tertentu.
Peleburan parsial dan difusi dalam bahan menyebabkan partikel menggumpal membentuk kue sinter berpori terus menerus. Setelah kue sintering dikeluarkan dari palet, sinter disaring dengan panas, dan fraksi halus (halus kembali, kurang dari 5 mm) didaur ulang untuk dicampur dengan bahan baku sementara fraksi kasar didinginkan dan dikirim ke hopper BF . Kotak angin di bawah untaian terhubung ke kipas angin melalui sistem penggosok gas. Secara umum, gas panas yang dihasilkan selama sintering juga dapat disirkulasi ulang untuk efisiensi termal yang lebih baik.
Untaian dapat bervariasi dari mesin kecil hingga besar dengan area dan ketinggian tempat tidur yang kompatibel dengan peralatan tambahan yang digunakan untuk menyedot gas keluar. Area untai dan daya isap bersama dengan permeabilitas unggun menentukan kecepatan maksimum dan karenanya, produktivitas proses. Namun, tergantung pada parameter operasional dan bahan baku yang dipilih, kualitas sinter yang dihasilkan dapat sangat bervariasi dan dapat sangat mempengaruhi operasi proses BF selanjutnya.
Ada beberapa faktor yang mempengaruhi proses sintering, produktivitas mesin sinter, dan kualitas sinter. Utama di antara mereka dijelaskan di bawah ini.
Komposisi kimia – Komposisi kimia dan struktural sangat penting dalam sinter, dan baik untuk stabil sehingga terak primer dan akhir memiliki karakteristik yang memadai dalam hal suhu pelunakan dan leleh, suhu cair dan viskositas untuk operasi BF yang stabil . Penting untuk memiliki kandungan besi tinggi, kandungan gangue rendah, dan kebasaan orde 1,6 hingga 2,1. Reduksibilitas sinter, dan kualitas sinter secara umum, meningkat dengan tingkat hematit yang lebih tinggi daripada magnetit, dan strukturnya meningkat dengan tingkat hematit dan ferit primer atau residu yang lebih tinggi daripada hematit sekunder atau endapan.
Struktur sinter – Karena keragaman komponen mineralogi yang menyusun campuran mentah, serta heterogenitas campuran, struktur sinter menjadi kompleks karena dibentuk terutama oleh butiran oksida besi dan kalsium ferit yang diikat oleh matriks gangue. Ferit, yang jumlahnya meningkat dengan indeks kebasaan, mudah dikurangi. Dengan meningkatkan ketangguhan mekanik sinter ke tingkat tertentu, mereka dianggap sebagai komponen yang sangat berguna. Ferit adalah jenis SFCA dan dibentuk oleh reaksi padat-cair antara hematit dan lelehan Fe2O3·CaO, dengan asimilasi berikutnya dari SiO2 dan Al2O3 dalam lelehan. Gangue terdiri dari kalsium, besi dan magnesium silikat yang sulit untuk direduksi, dan menjadi bagian dari terak di BF.
Struktur dan komposisi sinter meliputi keberadaan hematit primer (tidak berasimilasi atau residu), hematit sekunder (endapan), magnetit primer (tidak berasimilasi atau residu), magnetit sekunder (endapan) dan ferit sebagai fase utama, serta jumlah gangue yang lebih kecil. Ada porositas yang cukup untuk mendukung reduksibilitas sinter, termasuk pori-pori mikro dalam banyak kasus. Struktur optimum untuk reducibility dibentuk oleh inti hematit primer yang dikelilingi oleh kisi ferit acicular.
Pengaruh kualitas butiran bijih besi – Dalam proses sintering, bahan baku utama yang digunakan adalah bijih besi halus, Kualitas bijih besi halus mempengaruhi proses sintering untuk sebagian besar. Peningkatan ukuran rata-rata butiran bijih besi meningkatkan produktivitas mesin sintering, menghemat konsumsi bahan bakar spesifik tetapi mengurangi kekuatan sinter. Bijih besi alumina rendah yang padat memberikan kekuatan sinter yang lebih baik dan konsumsi bahan bakar spesifik yang lebih rendah. Tingkat mikro-halus yang sangat tinggi dalam bijih menurunkan efisiensi granulasi dan karenanya, menurunkan permeabilitas unggun dan mempengaruhi produktivitas sintering secara merugikan. Porositas bijih besi berpengaruh terhadap porositas sinter serta sifat fisik dan metalurginya. Bijih besi dengan loss on ignition yang tinggi mempengaruhi proses sintering secara negatif dengan mengurangi produktivitas, meningkatkan konsumsi bahan bakar spesifik dan mengurangi kekuatan sinter.
Persiapan campuran sinter – Kinerja sintering tergantung pada efisiensi pencampuran komponen campuran sinter dan granulasi campuran sinter dalam drum pencampuran. Aktivitas ini bila dilakukan dalam dua tahap dalam dua drum pencampur daripada dilakukan dalam satu tempat dalam satu drum memberikan kinerja yang lebih baik sehubungan dengan permeabilitas sinter bed dan karenanya menghasilkan peningkatan produktivitas sintering.
Mekanisme sintering – Mekanisme sintering terdiri dari dua fenomena yang berbeda yaitu fenomena fisik perpindahan panas dari lapisan atas karena lapisan bawah karena aksi udara yang dihisap melewati bed dan fenomena kimia pembakaran bahan bakar yang menghasilkan panas dan reaksi kimia depan. Kedua fenomena ini independen dan perlu memiliki kecepatan rambat yang sama untuk memastikan suhu nyala maksimum. Keseimbangan antara dua fenomena ini penting untuk kinerja proses sintering yang tinggi, konsumsi bahan bakar spesifik yang rendah, dan kualitas sinter yang tinggi.
Permeabilitas lapisan sinter – Tempat tidur sinter membutuhkan permeabilitas yang baik agar udara dapat dihisap melalui campuran sinter. Permeabilitas yang baik dari campuran sinter memastikan produktivitas untaian yang tinggi dan efisiensi yang tepat dari bahan bakar padat yang dibakar.
Kelembaban campuran sinter – Ini memainkan peran penting dalam proses granulasi dan karenanya mempengaruhi produktivitas sinter. Kelembaban membentuk jembatan cair antara partikel untuk memulai proses granulasi. Gaya kapiler bertanggung jawab untuk mengurangi jarak antar partikel dan meningkatkan ketahanan butiran. Kadar air harus optimum (biasanya bervariasi antara 6% sampai 8%) karena kelebihan air memiliki efek berbahaya pada butiran dan pada permeabilitas dan stabilitas sinter bed. Pengaruh kelembaban pada proses granulasi ditunjukkan pada Gambar 3.
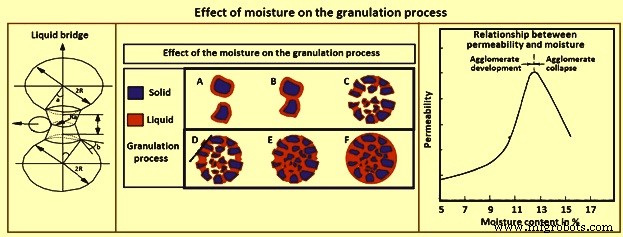
Gbr 3 Pengaruh kelembapan pada proses granulasi
Sistem pemuatan campuran sinter – Sistem pemuatan campuran terpisah untuk memuat campuran sinter pada untaian mesin sinter membantu permeabilitas campuran dan karenanya meningkatkan produktivitas alat berat. Gambar 4 menunjukkan sistem pengisian tanpa dan dengan sistem pemuatan campuran terpisah.
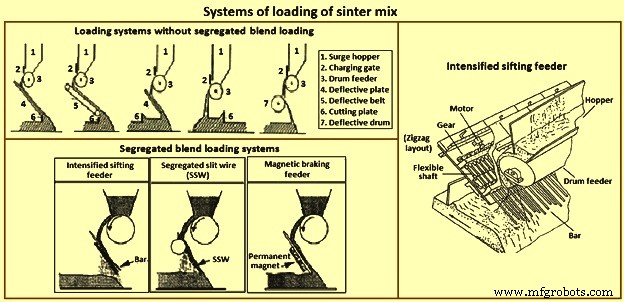
Gbr 4 Sistem pemuatan campuran sinter
Sistem pengapian – Waktu dan suhu penyalaan sangat penting untuk kemajuan yang tepat dari bagian depan nyala api dan kualitas sinter yang tepat. Kelebihan pengapian menyebabkan penurunan permeabilitas unggun dan sifat metalurgi sinter. Hal ini meningkatkan generasi denda pengembalian dan karenanya produktivitas. Penggunaan pembakar multi celah meningkatkan efisiensi pengapian dan mengurangi energi pengapian sekitar 30%.
Jenis bahan bakar padat – Bahan bakar padat dengan reaktivitas sangat rendah atau reaktivitas sangat tinggi menyebabkan perbedaan antara pembakaran bagian depan dan perpindahan panas. Distribusi ukuran bahan bakar padat yang sesuai diperlukan untuk mengoptimalkan proses sintering.
Kontrol proses otomatis – Meningkatkan produktivitas mesin sinter. Teknologi ini menghasilkan penghematan konsumsi energi sebesar 2% hingga 5%.
Pemasangan sintering yang dioptimalkan emisi – Ini mengurangi konsumsi bahan bakar padat dalam kisaran 6 kg per ton sinter hingga 12 kg per ton sinter.
FeO dalam sinter – Kandungan FeO merupakan parameter kontrol penting di pabrik sinter. Ketika komposisi kimia dari campuran bijih tetap, FeO dapat memberikan indikasi kondisi sintering, khususnya laju kokas. Peningkatan 2% dalam kandungan FeO dalam sinter telah ditemukan untuk menurunkan (meningkatkan) RDI sebesar 8 poin. Namun, kandungan FeO yang lebih tinggi secara negatif mempengaruhi reducibility. Penting untuk menemukan tingkat FeO yang optimal dalam sinter untuk meningkatkan RDI tanpa mengubah sifat sinter lainnya.
SiO2 dalam sinter – Persentase silika yang lebih tinggi dalam campuran sinter melawan efek alumina tinggi dalam bijih. Silika bergabung dengan FeO dan CaO untuk membentuk senyawa dengan titik leleh rendah yang mendukung pembentukan lelehan primer yang terdiri dari FeO·SiO2 (1.180 derajat C), 2FeO·SiO2 (1.205 derajat C), dan FeO·SiO2·CaO (1.223 derajat derajat C). Peningkatan kandungan silika dan kebasaan butiran halus yang menempel menyebabkan suhu pembentukan lelehan primer turun, yang menguntungkan untuk reaksi asimilasi berikutnya pada antarmuka cair-padat antara butiran halus dan partikel inti. Biasanya, rasio alumina / silika yang diinginkan dalam campuran sinter adalah 0,5 atau lebih rendah.
Al2O3 dalam sinter – Alumina memainkan peran penting dalam pembentukan kembali dan proses penggabungan selama sintering dengan mengubah sifat fisio-kimia dari lelehan primer. Ini mengarah pada struktur pori sinter yang unik. Terlihat bahwa luas pori meningkat secara drastis dan bentuk pori menjadi lebih tidak beraturan seiring bertambahnya alumina dari 1,6% menjadi 2,4%.
Efek alumina yang paling berbahaya adalah memperburuk RDI sinter, yang meningkat seiring dengan meningkatnya kandungan alumina. Pengalaman industri dengan BF menunjukkan bahwa dalam kisaran kandungan CaO 10% hingga 10,5%, peningkatan 0,1% dalam kandungan alumina meningkatkan RDI sebesar 2 poin. Kekuatan dan kualitas sinter menurun seiring dengan meningkatnya kandungan alumina. Alumina mempromosikan pembentukan SFCA (silico ferit kalsium dan aluminium), yang bermanfaat untuk kekuatan sinter, tetapi kekuatan komponen bijih lebih rendah, karena kandungan alumina yang tinggi dalam kisi mereka telah dilaporkan menjadi penyebab utama dari kekuatan yang lebih rendah diamati. Alumina meningkatkan viskositas lelehan primer yang terbentuk selama proses sintering, yang mengarah ke struktur sinter yang lebih lemah dengan pori-pori tidak beraturan yang lebih saling terhubung.
Reduksibilitas sinter ditentukan oleh komposisi kimia dan mineralogi dan oleh struktur pori. Karena kompleksnya efek alumina pada masing-masing faktor ini, pertimbangan tentang bagaimana alumina mempengaruhi reduksibilitas telah menghasilkan hasil yang kontradiktif. Dalam sebuah penelitian yang dilakukan dalam pot sinter yang diisi dengan 65 kg campuran bijih dengan kandungan alumina yang berbeda, peningkatan kandungan alumina dari 2% menjadi 5,5% meningkatkan RI sinter dari 58% menjadi 64%.
Efek fluks – Dalam campuran sinter, batu kapur atau kapur dan dolomit atau dolomit yang dikalsinasi ditambahkan sebagai fluks dasar sedangkan butiran halus pasir atau kuarsit digunakan sebagai fluks asam. Oksida fluks dalam sinter diperlukan untuk memodifikasi kimia terak BF sedemikian rupa sehingga memiliki karakteristik yang diinginkan. Fluks dasar yang ditambahkan ke dalam campuran sinter dalam bentuk kapur dan dolomit yang dikalsinasi juga bertindak sebagai pengikat dalam campuran sinter dan meningkatkan aglomerasi partikel halus. Mereka meningkatkan produktivitas mesin sinter dan mengurangi konsumsi bahan bakar padat tertentu. Distribusi ukuran fluks penting untuk produktivitas sintering.
CaO dalam sinter – CaO bergabung dengan oksida besi untuk membentuk senyawa dengan titik leleh rendah yang mendukung pembentukan lelehan primer, tingkat minimum yang diperlukan untuk menghasilkan sinter yang kuat. Senyawa tersebut adalah Fe2O3·CaO (1.205 derajat C) dan FeO·CaO (1.120 derajat C). Sifat lelehan yang terbentuk selama sintering menentukan struktur fase ikatan yang berasal dari sinter. Sifat leleh pada saat sebelum pemadatan sangat bergantung pada komposisi kimia lapisan halus yang menempel pada butiran dan asimilasi partikel inti.
MgO dalam sinter – MgO menyediakan kondisi terak BF yang optimal dalam hal kemampuan alir dan desulfurisasi yang baik. Itu dapat ditambahkan ke BF sebagai fluks mentah dalam bentuk dolomit atau dunit, atau sebagai sinter. Penambahan MgO ke dalam campuran mentah meningkatkan RDI, karena MgO menstabilkan magnetit dan dengan demikian menurunkan kandungan hematit, sehingga menimbulkan lebih sedikit tekanan di sinter selama reduksi hematit menjadi magnetit di tumpukan BF.
Telah ditentukan bahwa penggantian CaO dengan MgO dalam bentuk dolomit untuk tingkat kebasaan 1,6 hingga 1,9 menyebabkan sedikit penurunan kekuatan, reduksi, dan produktivitas sinter. Dalam sebuah penelitian yang dilakukan dalam pot sinter dengan 65 kg campuran mentah, kandungan MgO dari empat sinter yang dihasilkan meningkat dari 1,4% menjadi 2,6% dengan penambahan dolomit ke dalam campuran. Bijih besi yang digunakan memiliki kandungan MgO yang rendah (0,01%) dan kandungan Al2O3 yang tinggi (3%). Terlihat bahwa peningkatan kadar MgO dalam sinter, dari 1,4% menjadi 2,6%, meningkatkan kandungan FeO dan menurunkan produktivitas serta indeks RI, RDI dan TI (indeks tumbler).
Distribusi granulometrik – Distribusi ukuran yang memadai (dispersi rendah, ukuran partikel rata-rata tinggi) memungkinkan permeabilitas unggun sinter yang lebih tinggi dan karenanya produktivitas proses sintering yang lebih tinggi. Ukuran rata-rata umpan sinter yang lebih tinggi biasanya memungkinkan permeabilitas unggun sinter yang lebih tinggi.
Setelah dikeluarkan dari palet di mesin sintering, sinter disaring dengan panas. Distribusi granulometriknya merupakan parameter proses yang penting. Fraksi 10 mm hingga 30 mm dikirim langsung ke hopper BF, fraksi yang lebih besar dihancurkan untuk mendapatkan fraksi berukuran lebih kecil, dan fraksi kurang dari 5 mm (pengembalian halus) didaur ulang ke sinter plant hopper.
Untuk pengoperasian proses yang baik, penting untuk menjaga keseimbangan (B) antara pembangkitan dan daur ulang denda pengembalian (RF). Untuk pengoperasian yang baik, B =RF yang dihasilkan / RF yang dikembalikan dan B berada dalam kisaran 0,95 hingga 1,05.
Sinter disaring dan masing-masing fraksi yang dihasilkan ditimbang (lebih dari 40 mm, 20 mm hingga 40 mm, 10 mm hingga 20 mm, 5 mm hingga 10 mm, dan kurang dari 5 mm. Berat gabungan semua fraksi terdiri dari berat total kue. Sinter yang berguna adalah total kue dikurangi butiran halus yang dihasilkan (fraksi kurang dari 5 mm). Ukuran butir rata-rata dihitung sebagai fungsi dari kg sinter yang sesuai dengan setiap fraksi, dan dapat bervariasi dalam rentang yang luas. interval antara 25 mm dan 45 mm.
Porositas sinter – Porositas sinter merupakan parameter penting yang sangat mempengaruhi sifat sinter, khususnya perilaku reduksinya. Porositas (P) dihitung dengan menentukan densitas nyata (Dr) dan densitas semu (Da) sinter sebelum dan sesudah dilakukan uji reducibility. Diberikan oleh persamaan P =(Dr-Da) / Dr. Sinter mengalami peningkatan porositas yang kuat setelah menjalani uji reducibility.
Dalam studi yang dilakukan dengan bijih hematit dan goetit, perubahan yang terjadi pada struktur pori awal selama uji reduksi pada 550 derajat C dan 950 derajat C dianalisis. Terlihat bahwa diameter pori harus lebih besar dari 0,01 mikrometer agar gas pereduksi memiliki akses yang cukup ke pori-pori untuk mereduksi sinter secara memuaskan. Ketika pori-pori mikro menyatu menjadi pori-pori dengan ukuran lebih dari 1 mikrometer hingga 5 mikrometer, luas permukaan spesifik sinter menurun dan begitu pula pengurangannya.
Studi telah menunjukkan bahwa menghilangkan koalesensi pori-pori mikro dan meningkatkan jumlah pori-pori kecil memungkinkan untuk meningkatkan luas permukaan sinter dan mencapai peningkatan substansial dalam reducibility-nya. Ferit menstabilkan pori-pori mikro dan menyebabkan peningkatan porositas, sehingga mencapai reducibility yang lebih tinggi. Reaksi dekomposisi ferit untuk memproduksi magnetit dan silikat dapat dicapai pada suhu tinggi di atmosfer yang tereduksi, dan merupakan reaksi terpenting untuk mengurangi porositas sinter. Selain peningkatan porositas sinter setelah dilakukan uji reducibility, juga terjadi peningkatan volume yang berasal dari transformasi hematit heksagonal menjadi magnetit kubik. Peningkatan volume yang terjadi karena transformasi ini adalah 25%.
Struktur kristal magnetit (Fe3O4) bertipe spinel, dengan a =8,38 angstrom. Ia memiliki kisi kubik padat ion oksigen dengan ion Fe2+ dan Fe3+ yang lebih kecil didistribusikan di celah. Hematit (alpha Fe2O3) adalah jenis korundum rombohedral (a =5,42 angstrom dan x =55 derajat 14 menit). Ion oksigen tersusun dalam kisi heksagonal yang rapat dan dua pertiga celah oktahedral ditempati oleh ion Fe3+. Oksida memiliki defisit oksigen kecil, mungkin karena kekosongan oksigen, tetapi mungkin juga karena ion besi di posisi interstisial tambahan.
Indeks reduksibilitas – Reduksibilitas merupakan karakteristik penting dari sinter. Ini mengukur kemampuan untuk mentransfer oksigen selama pengurangan tumpukan BF, memberikan gambaran tentang kebutuhan konsumsi bahan bakar di tungku. Porositas dan struktur sinter dan fase mineral sangat erat hubungannya dengan reducibility sinter. Struktur heterogen lebih dapat direduksi daripada struktur homogen. Dimungkinkan juga untuk memprediksi perilaku reducibility dari konsentrasi setiap fase yang ada. Reduksibilitas fasa mineral dalam orde menurun adalah Fe2O3 lebih besar dari CaO·2Fe2O3, lebih besar dari CaO·Fe2O3, lebih besar dari 2 CaO·Fe2O3, dan lebih besar dari Fe3O4.
Hematit dan magnetit dengan cepat direduksi menjadi wustit (FeO), tetapi kecepatannya berbeda untuk reduksi selanjutnya menjadi besi metalik. Dari hematit, wustit direduksi dengan cepat dan homogen, meskipun beberapa wustit dikelilingi oleh logam. Dari magnetit, reduksi merupakan reaksi topokimia (reaksi kimia yang terjadi pada batas fase padat), mengikuti urutan Fe3O4 menjadi FeO hingga Fe, dan hampir semua butiran wustit dikelilingi oleh besi logam, yang menunda reaksi selanjutnya.
Reduksibilitas SFCA dapat dikaitkan dengan morfologi, porositas dan apakah dilapisi dengan kaca atau tidak. Ferit acicular (kurang dari 10 mikrometer) yang terbentuk pada suhu rendah (kurang dari 1.300 derajat C) lebih dapat direduksi, sedangkan ferit kolumnar (lebih besar dari 10 mikrometer) yang terbentuk pada suhu tinggi (lebih besar dari 1.300 derajat C, mungkin dilapisi dengan kaca) kurang direduksi. Hematit primer lebih dapat direduksi daripada hematit sekunder karena porositas intrinsiknya. Berbagai penelitian untuk menentukan hubungan antara porositas, reducibility dan TI telah menunjukkan bahwa porositas yang lebih tinggi mengarah pada reducibility yang lebih besar, dan sinter dengan luas permukaan terbesar (pori terbuka) menyajikan struktur yang lebih rapuh dan TI yang lebih rendah.
Studi yang dilakukan pada perilaku klorin dan alkali dalam BF dan pengaruhnya pada sifat sinter selama reduksi telah menunjukkan bahwa meskipun beberapa perbedaan efek klorin, yang bergabung untuk membentuk KCl dan NaCl, dan basa pada sinter, secara keseluruhan cukup serupa. Uji reduksi sinter pada suhu hingga 1.100 derajat C menunjukkan bahwa keberadaan alkali mendukung reduksi hematit menjadi magnetit, karena aksi katalitik alkali. Kehadiran senyawa klorin tidak menguntungkan, karena mereka disimpan pada permukaan sinter dan menghambat reduksi. Kehadiran alkali menyebabkan peningkatan tegangan sinter, karena peningkatan reduksi hematit menjadi magnetit, dan bentuk retakan yang meningkatkan abrasi. Dengan menghambat reaksi reduksi, senyawa klorin menjamin abrasi yang lebih sedikit hingga 700 derajat C. Pada suhu yang lebih tinggi, reaksi reduksi meningkat, dengan peningkatan abrasi yang sesuai.
Indeks penurunan degradasi – RDI adalah parameter yang sangat penting yang berfungsi untuk memprediksi perilaku degradasi sinter di bagian bawah tumpukan BF. Degradasi sinter selama reduksi pada suhu rendah biasanya ditentukan oleh uji statis RDI, yang dilakukan pada 550 derajat C. Nilai RDI yang rendah diinginkan.
Hematit sekunder, juga dikenal sebagai hematit rombohedral rangka, adalah penyebab utama nilai RDI sinter yang buruk. Hal ini didasarkan pada pengamatan yang sering dari retakan di sekitar daerah leher sempit dari hematit tersebut. Di sisi lain, telah disarankan bahwa retakan yang terbentuk karena perubahan volumetrik yang menyertai transformasi fase kristal dari hematit menjadi magnetit bertanggung jawab atas degradasi reduksi sinter.
Penelitian telah menunjukkan bahwa hematit sekunder adalah komponen sinter paling berbahaya untuk RDI. Hematit sekunder biasanya mengandung pengotor terlarut seperti Al2O3, TiO2 dan MnO yang meningkatkan tegangan magnetit dengan mendistorsi kisi. Magnetit ini terbentuk selama reduksi hematit pada 550 derajat C di BF. Telah ditemukan dalam studi bahwa struktur sinter tergantung pada suhu maksimum yang dicapai di tempat tidur, dan hematit sekunder hadir pada suhu yang lebih tinggi. Hematit sekunder terbentuk sebagai hasil rekristalisasi selama sintering hematit primer. Pada suhu yang lebih rendah, proporsi yang lebih besar dari hematit primer (hematit sisa) tetap dalam komposisi sinter. Telah diamati bahwa Al2O3 cenderung terkonsentrasi pada fase hematit sekunder ketika transformasi hematit primer menjadi hematit sekunder terjadi. Juga terlihat bahwa peningkatan konsentrasi Al2O3 dan TiO2 dalam sinter berbahaya bagi RDI.
Dalam studi lebih lanjut, ditentukan bahwa kehadiran pelarutan padat Al2O3 dan TiO2 dalam hematit berasal dari ekspansi volume 4% selama reduksi hematit menjadi magnetit pada 550 derajat C, dan menyebabkan distorsi kisi kristal fase ini dan peningkatan besarnya tegangan kisi pada magnetit yang terbentuk. Adanya retakan pada struktur sinter setelah reduksi pada 550 derajat C lebih sering terjadi di daerah dengan kandungan hematit sekunder yang lebih tinggi, dan berbahaya bagi RDI, seperti yang telah dicatat.
Laju produksi dan RDI telah dipelajari di pabrik sinter menggunakan jaringan saraf. Model tersebut mempertimbangkan 55 parameter dan menganalisis sekelompok 695 nilai RDI yang dicatat selama periode 3 tahun. Ditemukan bahwa tingkat produksi dan RDI bergantung pada variabel yang sama. Hubungan yang kuat terlihat antara RDI dan suhu lingkungan luar di pabrik. RDI juga sangat bergantung pada kandungan Ti di sinter, meskipun ini hanya sangat kecil. Tidak ada hubungan dengan alumina yang ditemukan karena kandungannya yang rendah (0,5%) dan variasi yang langka dalam periode pengujian. Model tersebut menemukan rasio kokas dalam campuran sinter menjadi variabel kontrol yang paling penting sehubungan dengan RDI.
Untuk meningkatkan pengoperasian BF, satu pabrik Jepang menurunkan kandungan SiO2 dalam sinter dari 4,8% menjadi 4,2%, dengan memperhitungkan laju injeksi batu bara bubuk sekitar 170 kg per ton HM. Hal ini menyebabkan peningkatan permeabilitas tungku dan reducibility, tetapi memperburuk RDI. Hubungan demikian ditemukan antara permeabilitas unggun dan RDI. Dengan tindakan gabungan untuk menurunkan kandungan silika dalam sinter dan meningkatkan kontrol suhu leleh, pabrik telah berhasil menurunkan kandungan silika dalam logam panas dari 0,3% menjadi 0,2%. Telah dilaporkan bahwa peningkatan 6% pada RDI sinter menurunkan tingkat kokas BF sebesar 14 kg per ton logam panas dan meningkatkan produktivitas BF sebesar 3%.
Indeks penurunan suhu rendah – Degradasi sinter ditentukan oleh RDI dan indeks 'degradasi suhu rendah' (LTD). Degradasi sinter selama reduksi pada suhu rendah ditentukan oleh uji LTD dinamis, yang dilakukan pada 600 derajat C. Degradasi berasal, sampai batas tertentu, dalam transformasi yang terjadi selama reduksi hematit menjadi magnetit, disertai dengan peningkatan volume, sehingga menimbulkan adanya tekanan struktural di sinter. The degradation of sinter in the BF occurs during reduction in the low temperature zone, and has a harmful effect on the burden strength in the furnace, with the resulting loss of permeability to reducing gases and an increase in coke consumption.
In the studies involving the addition of magnetite fines in a raw mix for sintering, a coke saving of 0.43 % was seen for each 1 % increase in magnetite in the raw mix, due to the fact that when hematite ore is replaced by magnetite fines, the bed temperature increases as a result of the exothermic oxidation reaction of magnetite to hematite. An increase of 5.1 % was also seen in the LTD index for each 1 % increase in hematite in the raw mix during the oxidation of magnetite, which is transformed into gamma Fe2O3 with the same cubic spinel lattice structure as magnetite. The TI and RI indices do not undergo any noticeable change when hematite is replaced by magnetite.
Tumbler index – The cold strength of sinter is determined by the tumbler test, and depends on the strength of each individual ore component, the strength of the bonding matrix components, and the ore composition. This test determines the size reduction due to impact and abrasion of the sinter during its handling, transportation, and in the BF process. Studies of the fracture strength of several mineral phases have allowed the following order to be established, primary (or residual) hematite is greater than secondary hematite, is greater than magnetite, and is greater than ferrites. Cold mechanical strength is directly related with the tendency for fines to form during transportation and handling between the sinter machine and the BF throat.
The sinter strength depends to a large extent on the properties of the matrix formed by vitreous glass, silicates, olivines and ferrites. Vitreous glass presents a high degree of stress. The allotropic transformation, which starts at 697 deg C, from beta-2CaO·SiO2 to gamma-2CaO·SiO2 is accompanied by a change in volume which causes the sinter strength to decrease. Ferrites have been identified as a strong bonding material which improves sinter strength.
The TI of sinter is dependent on critical faults in the sinter and their propagation through sinter particles. Faults are unavoidable since the different minerals and phases precipitate out of the melt at different times during the cooling cycle, and changes in volume almost always accompany the transformation of a liquid into a solid.
Studies have been carried out to improve the strength of the sinter with high iron (58.8 %) and low silica (4.38 %) content. By adding of serpentine and burnt lime into the ore mix to be sintered and with a deeper sinter bed, there is a significant increase in the amount of magnesium ferrite and SFCA, which is associated with improvement in the sinter strength.
Sinter plant productivity
In a sinter plant, the requirement is the achieving of high productivity. This is done by assuring good bed permeability, and for this it is essential to optimize the granulation process. Moreover, for high sinter productivity, it is necessary to maximize the sinter output. A variety of factors can influence output, such as (i) horizontal and vertical uniformity in the sinter bed,(ii) sinter bonding strength, (iii) crushing of product sinter, and (iv) selection of return fines screen opening.
Non-uniform sintering normally results in part of the bed being more friable and can lead to high fines production. Where there is a lack of vertical uniformity, it is frequently necessary to increase the coke content in the top part of the bed. This is possible by segregation of the feed using devices such as an intensified sifting feeder or a slit bar chute (Fig 4). Horizontal uniformity is improved by using multi-segment gates on the roll feeder outlet. The problem is mainly serious near the pallet walls where the air flow is highest. This can be reduced by compacting the top of the bed close to the side walls or installing a dead bar grate near the wall.
In some sinter plants, higher production has been achieved by increasing the bed depth, normally together with a reduction in the strand speed. For this type of operation, high permeability is necessary and some improvements to granulation can be essential, such as the addition of (more) lime.
In Japan, in one of the sinter plant, air is enriched with oxygen. Oxygen is injected below the hood which covers a large part of the strand, after the ignition hood. This improves coke consumption, with the result of operating with a narrower heating zone and a higher flame front speed. It is possible to improve production by 1 ton per hour with the use of a flow of 500 N cum of oxygen.
Several sinter plants produce sinter with a 1.5 % to 3 % MgO content by adding dolomite, serpentine or olivine in the feed. Higher productivity is achieved with olivine and serpentine than with dolomite, a fact which can be attributed to the harmful effect of dolomite on sinter strength, and thus on output.
In one of the study, it has been seen that the productivity is the main challenge being faced by the users of pisolitic ore. It has been widely observed that incorporating pisolitic ores in blends causes sinter plant productivity to drop. The reason for this is a reduction in bed permeability caused by excessive melt formation. To improve productivity, water addition during granulation can be increased in order to compensate the fact that porous pisolite ore particles absorb a significant part of the added granulation water and thus reduce the amount of free water available on their surfaces for inter-particle adhesion, leading to deterioration in granulation efficiency.
Study has been carried out in a laboratory pot grate, varying the MgO content in the raw material from 1.40 % to 2.60 %. Dolomite and dunite are used as fluxes to add magnesia. Increasing the MgO content in the sinter mix means a higher temperature is needed for melt formation, and the highly fluxed composition with MgO acts as a refractory phase, raising heat consumption and reducing productivity. On the other hand, it has been found that increasing the MgO content improves the RDI, due to the drop in hematite and ferrite phases and the increase in the magnetite phase, which presents lower degradation.
In a study, it has been see that increasing the MgO content (range 1.75 % to 3.25 %) caused the plant productivity to decrease. The TI increased, but it was considered that for MgO contents of more than 4 % the TI decreases due to the formation of a vitreous matrix which shows a high degree of stress and a low formation of bonding phases. In contrast with this study, it was seen that an increase in MgO also increases the RDI. This variation can be due to differences between experimental conditions and the actual plant data.