Penggunaan Besi Pereduksi Langsung di Tungku Busur Listrik
Penggunaan Besi Reduksi Langsung di Tungku Busur Listrik
Pembuatan baja oleh tungku busur listrik (EAF) memiliki fleksibilitas yang sangat baik sehubungan dengan pemilihan bahan muatan. Bahan pengisi tradisional untuk proses EAF adalah skrap dingin 100 persen, tetapi karena masalah terkait skrap seperti ketersediaan dan kualitasnya, fluktuasi harga pasar dan pembatasan yang diberlakukan oleh skrap dalam membuat beberapa nilai baja karena elemen residu dan tingkat nitrogen, dll. meningkat, operator EAF mengintensifkan pencarian alternatif bahan pengisi yang mengandung besi.
Besi pereduksi langsung (DRI) seperti pig iron dan hot metal merupakan salah satu bahan pengisi alternatif besi yang telah digunakan dalam berbagai persentase dalam proses pembuatan baja EAF. Penggunaan DRI dapat memiliki efek berbeda pada proses peleburan. Konsumsi energi, produktivitas dan hasil dipengaruhi oleh kimia DRI, persentase DRI yang digunakan dalam campuran sisa dan praktik operasi. DRI digunakan sebagai pengganti skrap dalam proses pembuatan baja EAF. Gambar 1 menunjukkan profil leleh yang khas dengan DRI dalam campuran muatan dalam EAF 150 ton.
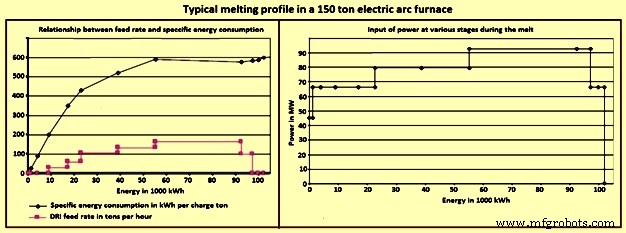
Gbr 1 Profil leleh khas dengan DRI dalam campuran muatan dalam EAF 150 ton
Keuntungan normal yang terkait dengan penggunaan DRI dalam proses pembuatan baja EAF adalah (i) ukuran dan dimensi yang konstan, (ii) komposisi yang diketahui, (iii) hampir tidak adanya elemen tramp, (iv) kemurnian, atau tidak adanya non-logam zat yang mengarah pada produktivitas dan konsumsi energi yang lebih baik, (v) penggunaan yang mudah di EAF, karena DRI dapat diisi ke dalam EAF bersama dengan sisa, menggunakan ember atau dengan pengumpanan terus menerus, (vi) ketersediaan yang lebih baik dibandingkan dengan residu rendah scrap, (vii) ketersediaan kandungan karbon terkait yang menghasilkan energi selama proses pembuatan baja, (vii) pembentukan terak berbusa yang mudah, (vii) pengisian langsung jika menggunakan DRI panas dengan DRI panas mengurangi konsumsi energi sebanyak sebagai 16 % hingga 20 % dengan memanfaatkan nilai energi DRI pada suhu lebih tinggi dari 600 derajat C, (viii) penanganan dan penyimpanan yang mudah dengan kemungkinan pengumpanan tanpa membuka atap tungku dengan sistem pengumpanan terus menerus yang menghasilkan bak baja yang stabil permukaan yang h mengurangi risiko kerusakan elektroda, (ix) kemungkinan bercampurnya DRI dengan scrap yang berarti dapat digunakan scrap grade yang lebih murah, dan (x) lebih ramah lingkungan karena menghindari masalah kontaminan berbahaya seperti timbal (Pb) atau kadmium (Cd) dalam debu EAF, dan mengurangi kemungkinan pembentukan dioksin dan furan.
Secara historis penggunaan DRI di EAF terbatas pada produksi baja residu rendah berkualitas tinggi dengan biaya yang diantisipasi lebih tinggi karena energi spesifik (kWh/ton), waktu tap to tap, konsumsi fluks, peningkatan FeO dalam terak, kehilangan hasil , dan keausan elektroda dan refraktori yang lebih tinggi. Ini telah terjadi sejak DRI telah digunakan tanpa mengidentifikasi dan memahami sifat yang melekat dan unik dan memodifikasi praktik yang sesuai.
Operasi EAF telah meningkat pesat sejak akhir 1970-an – awal 1080-an. Pembuatan baja di EAF telah diuntungkan secara signifikan dari praktik pengoptimalan, peningkatan penggunaan energi kimia lebih lanjut, dan penggunaan DRI dengan cara yang tepat. Praktik yang dikembangkan terkait penggunaan DRI telah menunjukkan bahwa penggunaan DRI dapat meningkatkan konsumsi energi, hasil, produktivitas, dan di atas semua biaya operasi. DRI lebih lanjut dengan kandungan karbon yang lebih tinggi memungkinkan pembuatan baja EAF memperoleh keuntungan finansial dan teknis yang substansial. Penggunaan karbon tinggi, DRI panas dapat menghasilkan peningkatan kemampuan pengoperasian, ditambah dengan produktivitas yang hemat biaya.
Parameter utama yang mempengaruhi operasi EAF adalah komposisi bahan baku (% gangue / kimia, metalisasi,% karbon,% fosfor, dan kandungan energi), praktik operasi (profil daya, terak berbusa, dan praktik peleburan), dan desain tungku ( tumit, penggunaan dan peralatan oksigen, AC/DC, dll.). Non-logam datang dengan DRI (biasanya dalam kasus DRI yang diproduksi oleh rotary kiln) juga memiliki efek buruk pada pembuatan baja EAF. Tanpa memperhatikan faktor-faktor ini, penggunaan DRI dalam pembuatan baja EAF dapat berdampak buruk pada parameter operasi EAF.
DRI adalah produk yang dihasilkan dari reduksi langsung bijih besi atau bahan bantalan besi lainnya dalam bentuk padat dengan menggunakan batu bara atau gas alam non-coking. Proses yang menghasilkan DRI dengan mereduksi bijih besi di bawah titik leleh besi biasanya dikenal sebagai proses reduksi langsung. Agen pereduksi adalah karbon monoksida (CO) dan hidrogen (H2), yang berasal dari gas alam, syngas, atau batubara yang direformasi. Bijih besi sebagian besar digunakan dalam bentuk pelet dan/atau kental. Oksigen (O2) dikeluarkan dari bijih besi melalui reaksi kimia berdasarkan H2 dan CO untuk produksi DRI yang sangat metalisasi.
Dalam proses reduksi langsung, besi logam padat (Fe) diperoleh langsung dari bijih besi padat tanpa menyebabkan bijih atau logam tersebut mengalami fusi. Reduksi langsung dapat didefinisikan sebagai reduksi dalam keadaan padat pada potensial O2 yang memungkinkan reduksi oksida besi, tetapi tidak untuk oksida lain (Al2O3, MnO, dan SiO2 dll.), ke elemen yang sesuai. Karena reduksi dalam keadaan padat, sangat kecil kemungkinan unsur-unsur ini larut (pada aktivitas termodinamika rendah) dalam besi tereduksi, sehingga oksida yang lebih stabil daripada besi pada dasarnya tetap tidak tereduksi. DRI memiliki struktur berpori.
DRI diproduksi dalam berbagai bentuk. Yaitu lump, pellet, hot briquetted iron (HBI), fines, dan cold briquetted iron (CBI). HBI dan CBI adalah bentuk DRI yang dipadatkan. Ketika DRI dikeluarkan dari tungku dalam kondisi dingin (suhu sekitar 50 derajat C) maka produk tersebut dikenal sebagai DRI dingin (CDRI) dan ketika DRI dikeluarkan dalam kondisi panas (suhu sekitar 650 derajat C) untuk digunakan dalam kondisi panas dalam pembuatan baja maka produk tersebut dikenal sebagai hot DRI (HDRI).
Kandungan zat besi dalam DRI ada dalam dua bentuk. Salah satunya dalam bentuk logam yang dikenal sebagai besi logam, Fe (M), dan bentuk kedua dari besi yang hadir dalam oksida besi sisa, Fe (O). Besi total, Fe (T), dalam DRI adalah jumlah dari kedua komponen besi ini. Besi metalik adalah jumlah agregat besi, baik bebas atau dikombinasikan dengan karbon (sebagai sementit) yang ada di DRI. Sifat kimia dan fisik DRI yang dihasilkan oleh proses yang berbeda biasanya bervariasi.
Kualitas DRI penting karena berdampak pada parameter pembuatan baja seperti hasil, konsumsi fluks, kuantitas terak, konsumsi energi, dan laju pengumpanan karbon, oksigen, dan bahan baku. Kualitas DRI tergantung pada (i) kualitas bahan masukan terutama bijih besi/pelet dan bahan bakar/reduktor yang menentukan bahan gangue/pengotor dalam DRI, (ii) proses produksi yang menentukan kandungan karbon dalam DRI, dan ( iii) parameter proses yang menentukan metalisasi DRI.
Derajat metalisasi yang rendah berarti lebih banyak FeO yang harus direduksi dalam EAF. Di sisi lain, tingkat metalisasi yang tinggi menghasilkan lebih sedikit CO dan agitasi mandi yang lebih rendah di EAF, yang pada gilirannya mengurangi efisiensi perpindahan panas dan karenanya meningkatkan kebutuhan energi tungku. Hasil terbaik diperoleh ketika metalisasi DRI terletak antara 94% dan 96%.
Ada dua alasan untuk menggunakan DRI sebagai bagian dari campuran muatan dalam pembuatan baja EAF. Ini adalah (i) kontrol residual, dan (ii) tidak tersedianya scrap premium. Tidak tersedianya skrap premium menciptakan tekanan pada operator EAF untuk beralih ke sumber skrap bermutu rendah, seperti skrap usang, sebagai sumber unit besi. Masalah dengan memo usang adalah kualitasnya. Selanjutnya, pertumbuhan pembuatan baja FAF telah menyebabkan perputaran skrap lebih cepat yang tidak dapat dihindari dan, sebagai akibatnya, meningkatkan kontaminasi skrap oleh elemen lain. Residu seperti krom (Cr), nikel (Ni), molibdenum (Mo), tembaga (Cu), dan timah (Sn), mulai dari 0,15% hingga 0,75% tergantung pada jenis skrap, memiliki efek buruk pada beberapa sifat mekanik. dari baja. Oleh karena itu, penggunaan pembuatan baja berbasis scrap-only di EAFs untuk produksi baja berkualitas, serta produk baja karbon rendah, umumnya dihindari.
Masalah lain yang terkait dengan pembuatan baja EAF berbasis scrap-only adalah nitrogen. Kandungan nitrogen baja EAF lebih tinggi daripada baja tungku oksigen dasar. Akibatnya, baja yang diproduksi dalam pembuatan baja EAF berbasis scrap-only biasanya memiliki karakteristik penuaan yang buruk sehingga praktis tidak cocok, misalnya, untuk aplikasi deep-drawing.
Untuk produksi grade baja khusus berkualitas tinggi dari skrap dengan kualitas dan komposisi kimia yang bervariasi, kepatuhan dengan tingkat kemurnian tinggi kadang-kadang hanya dicapai dengan pengenceran elemen gelandangan yang tidak diinginkan seperti Pb, Cu, Cr, Ni, Mo, dan Sn dengan bahan pengganti yang sangat murni seperti DRI. Level elemen tramp menurun secara linier ketika persen DRI dalam campuran muatan EAF meningkat. Persamaan aturan praktis untuk menghitung elemen tramp total dalam baja cair pada saat penyadapan adalah ‘persen (Cr + Ni + Cu +Sn) =0,3225 0,001174 x persen DRI.
Juga dengan peningkatan persen DRI dalam campuran muatan, kadar nitrogen menunjukkan pengurangan yang sama dengan pembusaan terak yang tepat. Pengurangan nitrogen memungkinkan EAF menghasilkan banyak baja khusus. Selanjutnya, DRI juga digunakan untuk produksi baja berkualitas tinggi yang ekonomis dengan kandungan fosfor dan hidrogen yang sangat rendah.
DRI memiliki densitas curah tinggi, yang lebih besar daripada sebagian besar jenis skrap baja. Kepadatannya lebih tinggi daripada terak di tungku, yang memfasilitasi peleburannya pada antarmuka terak / logam. FeO yang tersisa di DRI bereaksi dengan karbon dalam penangas logam cair untuk meningkatkan terak berbusa yang melindungi refraktori dari busur listrik. Namun, laju pemberian makan DRI merupakan parameter penting dari proses EAF yang harus dikontrol. Laju pengumpanan yang optimal tergantung pada komposisi kimia DRI, suhu rendaman, dan energi pengadukan yang disediakan oleh injektor oksigen-karbon dan sumbat pengaduk bawah. Laju pengumpanan DRI di sebagian besar tungku bermuatan DRI berada di kisaran 27 kg/mnt MW hingga 35 kg/mnt MW.
Kandungan karbon DRI penting sehubungan dengan penggunaannya dalam pembuatan baja EAF. Karbon dalam DRI dapat hadir dalam bentuk unsur atau dapat hadir sebagai kombinasi dari kedua unsur serta dalam bentuk terikat. Bentuk ikatan karbon dalam DRI adalah besi karbida (Fe3C) yang merupakan senyawa stabil dari besi dan karbon. Biasanya sekitar dua pertiga dari karbon yang terkandung dalam DRI hadir sebagai besi karbida, dan keseimbangannya dalam bentuk unsur karbon. Ketika karbon dalam bentuk terikat maka tidak ada kehilangan C yang tidak terikat karena pembakarannya di atmosfer EAF. Tab 1 memberikan spesifikasi khas DRI berbasis gas.
Tab 1 Spesifikasi umum DRI berbasis gas |
Dasar- Fe dalam bijih besi / pelet – 65,5% hingga 68 % |
No. Sl. | Parameter | Satuan | Rentang |
1 | Metalisasi | % | 92.0-96.0 |
2 | Fe (Total) | % | 86,1-93.5 |
3 | Fe (Logam) | % | 81,0-87,9 |
4 | Karbon | % | 1.0-4.0 |
5 | Belerang | % | 0,001-0,03 |
6 | Fosfor sebagai P2O5 | % | 0,005-0,09 |
7 | Gangue | % | 3.9-8.4 |
8 | Ukuran biasa | mm | 4-20 |
9 | Kepadatan yang terlihat | ton/cum | 3,4-3,6 |
10 | Kepadatan massal | ton/cum | 1,6-19 |
Catatan:Residu adalah oksida tak tereduksi seperti silika, mangan oksida, alumina, kapur, dan magnesium |
Biasanya terlihat bahwa dalam DRI berbasis gas, kandungan karbon DRI umumnya lebih dari persyaratan stoikiometrik yang diperlukan untuk mengurangi kandungan FeO yang tersisa dalam produk DRI. Kelebihan karbon berdampak signifikan pada kandungan FeO terak dan pada pembusaan terak yang diperlukan untuk proses pembuatan baja EAF yang efisien. Dalam kasus kelebihan karbon negatif, penambahan batubara antrasit yang diperlukan untuk reduksi FeO bermanfaat di akhir proses pembuatan baja EAF. Namun, tidak semua FeO direduksi menjadi Fe karena sebagian dari FeO selalu ada dalam terak tungku. Ini berarti bahwa jumlah praktis kelebihan karbon dari DRI yang tersedia untuk pembakaran di dalam bak baja EAF lebih banyak daripada kelebihan karbon yang dihitung untuk pengurangan DRI. Istilah ini disebut karbon yang mudah terbakar dan didefinisikan oleh persamaan ‘Karbon yang mudah terbakar =karbon dalam DRI – karbon stoikiometrik x (FeO dalam DRI – FeO dalam terak).
Karbon yang mudah terbakar bereaksi dengan oksigen yang disuntikkan ke penangas baja EAF untuk melepaskan panas di penangas baja dan juga menyumbangkan gas CO untuk pembusaan terak. Dengan meningkatnya karbon yang mudah terbakar di EAF, kandungan nitrogen dari baja yang disadap juga berkurang. Kelebihan karbon dari DRI menurunkan input batubara antrasit yang merupakan sumber utama nitrogen terlarut dalam bak EAF (0,1% N2) selain udara yang diinfiltrasi. Manfaat kedua yang diperoleh dari karbon dalam DRI adalah melalui manfaat energik dari besi karbida. Fe3C menghasilkan energi melalui reaksi eksotermik yang diperoleh selama disosiasi dalam penangas baja (- 0,4 kWh / kg C), berbeda dengan pelarutan endotermik partikel karbon dalam penangas baja (0,62 kWh / kg C).
Hasil logam dan jumlah terak
Hasil logam baja cair dipengaruhi selama pembuatan baja EAF dengan penambahan DRI dalam muatan EAF. Terlihat bahwa hasil logam menurun ketika persen DRI dalam campuran muatan EAF meningkat. Ini terutama karena peningkatan volume terak.
Volume terak meningkat saat persen DRI dalam campuran muatan EAF meningkat. Persamaan aturan praktis untuk kuantitas terak adalah 'Kuantitas terak (kg/ton baja cair) =127 + 2,43 x persen DRI'. Sesuai persamaan aturan praktis ini, peningkatan 10% DRI dalam campuran muatan EAF menyebabkan peningkatan berat terak sebesar 24,3 kg. Berat terak tergantung terutama pada konten dan komposisi gangue di DRI dan kebasaan terak.
Kimia dan volume terak mempengaruhi hasil di EAF. Dengan DRI dalam muatan EAF, operator harus berhati-hati dengan slag sehingga pembusaan yang baik terjadi dengan volume slag minimum pada kebasaan yang diperlukan. Karena reaksi reduksi endotermik FeO oleh karbon, (FeO + C =Fe + CO), dan volume terak yang lebih tinggi yang dihadapi karena penggunaan DRI, konsumsi daya listrik EAF biasanya meningkat dengan meningkatnya persentase DRI dalam logam. mengenakan biaya. Biasanya, konsumsi daya listrik meningkat kurang lebih secara linier dengan peningkatan persentase DRI di EAF.
Konsumsi daya listrik
Konsumsi daya listrik (kWh per ton baja cair) selama pembuatan baja EAF meningkat bila ada peningkatan persen DRI dalam campuran muatan EAF. Sesuai aturan praktis, dengan setiap kenaikan 10% dalam persen DRI menyebabkan peningkatan konsumsi daya listrik sebesar 14,5 kWh/ton baja cair dalam kondisi tertentu.
Banyak faktor yang cenderung meningkatkan konsumsi energi listrik saat menggunakan DRI dalam pembuatan baja EAF. Dengan pembusaan terak yang baik, EAF yang melelehkan 100% skrap dingin dan tanpa masukan energi lainnya biasanya mengkonsumsi energi dalam kisaran sekitar 400 kWh/ton hingga 435 kWh/ ton baja cair. Untuk tujuan perbandingan, EAF yang memiliki campuran muatan yang terdiri dari 98,2% DRI dengan pembusaan terak yang sangat baik telah mencapai tingkat konsumsi energi rata-rata 635 kWh/ton baja cair.
Metalisasi DRI mempengaruhi konsumsi energi. Semakin rendah tingkat metalisasi DRI berarti semakin tinggi kadar FeO. Reduksi kimia FeO adalah reaksi endotermik. Pengurangan satu ton FeO menjadi Fe membutuhkan sekitar 800 kWh pada suhu pembuatan baja. Peningkatan kadar SiO2 dalam DRI meningkatkan kebutuhan daya listrik. SiO2 membutuhkan penambahan kapur untuk menjaga rasio kebasaan. Mencairkan satu ton terak membutuhkan energi sekitar 530 kWh. Peningkatan jumlah SiO2 membutuhkan peningkatan jumlah CaO untuk mempertahankan rasio kebasaan. Baik SiO2 dalam DRI dan kapur yang dikalsinasi mengkonsumsi energi selama proses peleburan. Gambar 2 menunjukkan hubungan antara kandungan gangue DRI dan konsumsi energi per ton baja cair. Selain itu, ada sejumlah faktor tambahan yang mempengaruhi proses pembuatan baja. Ini termasuk hasil, kebutuhan kapur, dan kebutuhan oksigen dan injeksi karbon.
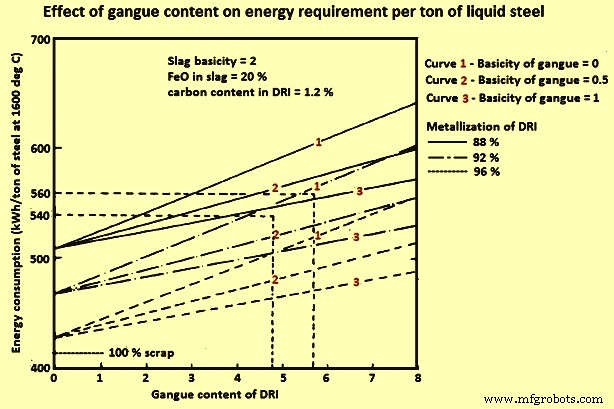
Gbr 2 Pengaruh kandungan gangue pada kebutuhan energi per ton baja cair
Kandungan fosfor dan belerang dapat memiliki efek negatif pada konsumsi energi karena kebutuhan kapur. CaO dalam kapur menyerap fosfor dari bak mandi. Jika EAF dioperasikan pada persentase FeO konstan maka satu-satunya cara untuk menghilangkan lebih banyak fosfor adalah dengan menambahkan lebih banyak kapur. Peningkatan jumlah kapur menyebabkan peningkatan konsumsi energi dan kehilangan hasil Fe. Penghilangan belerang yang efisien membutuhkan penggunaan terak pereduksi. EAF biasanya beroperasi dengan slag pengoksidasi dasar. Meskipun mungkin untuk menghilangkan beberapa belerang dari EAF dengan meningkatkan jumlah penambahan kapur, hal ini menghasilkan peningkatan konsumsi energi dan tidak terlalu efektif.
DRI karburasi memiliki efek positif pada konsumsi energi jika oksigen volume tinggi tersedia untuk disuntikkan ke dalam bak mandi. Konsumsi energi dapat dikurangi dengan 2 kWh/N cum menjadi 4 kWh/N cum oksigen, jika disuntikkan dengan jumlah karbon yang tepat dan dihasilkan foaming slag yang baik.
Pengisian DRI panas menghemat energi tetapi oksidasi adalah masalah. Pengangkutan DRI panas langsung dari modul DRI harus dilakukan di bawah nitrogen tertutup atau atmosfer gas proses sebelum mengisi daya ke EAF.
Pengaruh penambahan DRI dalam pengisian EAF pada waktu daya tepat waktu
Daya tepat waktu meningkat ketika persen DRI dalam campuran muatan EAF ditingkatkan. Persamaan aturan praktis untuk menghitung daya tepat waktu adalah 'EAF daya tepat waktu =46,36 +0,1320 x DRI persen. Substitusi scrap baja dengan DRI meningkatkan waktu yang dibutuhkan untuk mencairkan muatan EAF (power-on time). Hal ini disebabkan oleh rendahnya laju leleh DRI yang disebabkan oleh FeO yang perlu dikurangi. Apalagi memiliki terak asam yang disebabkan oleh SiO2 dan Al2O3 yang mengandung bahan gangue di DRI. Juga jelas bahwa konsumsi spesifik kapur dan dolomit meningkat untuk mengelola kebasaan terak yang sesuai di dekat (CaO / SiO2) sama dengan 2. Karena peningkatan kuantitas terak karena meningkatnya DRI dalam muatan logam, lagi-lagi waktu leleh yang lebih lama adalah diperlukan untuk membawa terak ke dalam larutan dan dengan demikian ada konsumsi daya listrik yang lebih tinggi, dan ini juga merupakan alasan untuk meningkatkan kapur, konsumsi fluks total dan kemudian kuantitas terak.
Pengaruh metalisasi pada hasil dan parameter lainnya
Hasil baja cair dari DRI adalah fungsi dari laju metalisasi, kandungan gangue total dan injeksi karbon dan praktik penambahan. Muatan khas DRI dapat mengandung 93% besi total dengan 86% besi metalik untuk metalisasi 92%. Jika pengurangan 100% FeO dimungkinkan maka muatan DRI memberikan hasil baja cair sebesar 93%. Dalam praktiknya, hasil ini tidak dapat dicapai di EAF. Jika hasil yang lebih tinggi diinginkan, maka DRI perlu memiliki metalisasi yang lebih tinggi. Selanjutnya, saat metalisasi turun, ia memiliki pengaruh negatif pada semua parameter. Gambar 3 menunjukkan hubungan khas metalisasi dengan hasil dan konsumsi daya yang dialami dalam EAF.
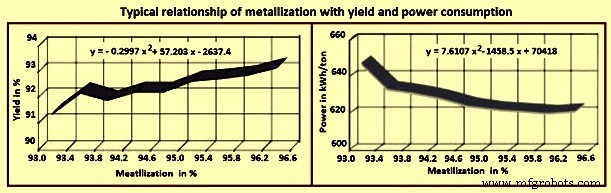
Gbr 3 Hubungan khas metalisasi dengan hasil dan konsumsi daya
Pengaruh persen DRI dalam campuran muatan pada kapur dan fluks total
DRI biasanya mengandung silika sebagai konstituen gangue utama bersama dengan tingkat pengotor lain yang rendah seperti belerang dan fosfor. Menurut konsentrasi komponen-komponen ini dalam DRI dan proporsi DRI dalam muatan logam, jumlah kapur yang bervariasi harus ditambahkan ke dalam EAF untuk menghilangkan silika dan menghilangkan belerang dan fosfor ke tingkat yang diizinkan dari elemen-elemen ini. untuk kelas baja yang akan diproduksi.
Total konsumsi kapur meningkat dengan meningkatnya persen DRI dalam campuran muatan EAF. Sesuai aturan praktis, ada peningkatan konsumsi kapur sebesar 2,6 kg/ton baja cair dengan setiap 10% peningkatan DRI dalam campuran muatan. Persamaan aturan praktis untuk menghitung konsumsi fluks total (dalam kg per ton baja cair) adalah ‘Konsumsi fluks (kg /t) =45,31 + 0,2416 x DRI persen.
Metodologi pengisian daya
Dengan meningkatnya penggunaan DRI dalam pembuatan baja EAF, metode pengisian telah berubah. Dengan tanaman DRI captive, persentase DRI dalam muatan EAF biasanya tinggi tanaman tersebut. Pada pembangkit seperti itu, suplai langsung ke EAF dilakukan melalui sistem pengisian terus menerus ke lubang kelima di atap EAF. Selalu ada tempat penyimpanan atau gudang besar untuk menerima pasokan DRI saat toko EAF sedang tidak beroperasi karena pemeliharaan atau penundaan atau saat penimbunan diperlukan untuk penutupan pabrik DRI. Gambar 4 menunjukkan praktik pengisian berbeda yang diikuti dengan penggunaan DRI dalam pembuatan baja EAF.
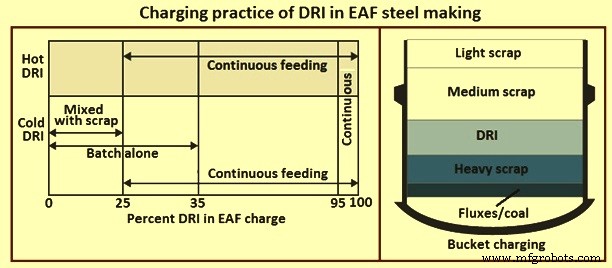
Gbr 4 Praktik pengisian yang berbeda diikuti dengan penggunaan DRI dalam pembuatan baja EAF
Pemberian makan terus menerus biasanya digunakan di atas 25% untuk memfasilitasi tingkat pemberian makan yang sesuai dengan input daya dan energi kimia dan untuk mencegah pembentukan 'gunung es' atau 'gunung ferro'. Pencegahan ferrobergs ditentukan sebagian oleh laju umpan dan input daya yang tersedia.
Pengisian ember digunakan dalam EAF yang biasanya menggunakan kurang dari 25% hingga 30% DRI dalam campuran muatan, meskipun lebih baik untuk terus mengisi DRI. DRI di dalam ember membantu densifikasi muatan serta menurunkan residu dalam baja cair. Pengisian bucket menghindari biaya sistem pengisian berkelanjutan. DRI biasanya diisi di atas skrap atau bundel berat (Gbr 4) untuk memaksimalkan kepadatan muatan, dan sisa ember dimuat sesuai dengan praktik spesifik lokasi. DRI biasanya dibagi antara ember dalam pengisian beberapa ember, dengan lebih banyak di ember terakhir untuk meningkatkan pemurnian lelehan di mana % C yang lebih rendah dan kandungan O2 yang meningkat dapat mengkompensasi kekurangan kapasitas input O2 dan meminimalkan blow down di akhir panas . Jika praktik pengisian satu ember digunakan, DRI dimasukkan dalam beberapa lapisan. DRI diisi lebih tinggi (lapisan ketiga dan kedua dari belakang) dalam ember untuk mencegah DRI jatuh melalui bagian bawah ember.
Atap melalui lubang kelima lebih disukai untuk DRI dan yang pasti lebih hemat bila menggunakan DRI lebih dari 30%. Pengisian terus menerus memfasilitasi koordinasi laju pengumpanan dengan input daya dan pengumpanan fluks untuk memastikan kontrol terak (tinggi buih, dan viskositas, dll.) dan mencegah ferroberg, yang terjadi saat DRI dingin diisi terlalu cepat.
Pengisian panas terus menerus (600 dg C) DRI dapat mengurangi energi yang dibutuhkan sebanyak 16% hingga 20%. Pengumpanan terus menerus sangat mengurangi kebutuhan energi EAF karena memungkinkan pengoperasian pintu tertutup. Ini meniadakan kehilangan panas dan waktu dari ayunan atap dan pengisian, juga potensi pengambilan nitrogen yang timbul dari masuknya udara yang terjadi saat atap terbuka. DRI pengisian panas mengurangi kebutuhan daya sebesar 20 kWh/100 derajat C menjadi 30 kWh/100 derajat C. Ada banyak metode pengisian daya panas yang berbeda. Salah satu metodenya adalah pengisian panas dengan mengangkut DRI dari pabrik DRI ke EAF dalam truk berinsulasi. Metode lain menggunakan konveyor sistem pneumatik dengan umpan gravitasi melalui lubang kelima. Beberapa pabrik menggunakan konveyor atau umpan gravitasi langsung. Studi pembandingan berdasarkan data yang dipublikasikan dari 150 EAF menunjukkan bahwa beberapa EAF yang mengisi HDRI cocok dengan konsumsi energi EAF berbasis scrap.