Memahami Operasi Pembuatan Baja Tungku Busur Listrik
Memahami Operasi Pembuatan Baja Tungku Busur Listrik
Teknologi pembuatan baja tanur busur listrik (EAF) berusia lebih dari seratus tahun. Meskipun De Laval telah mematenkan tungku listrik untuk peleburan dan pemurnian besi pada tahun 1892 dan Heroult telah mendemonstrasikan peleburan busur listrik dari paduan besi antara tahun 1888 dan 1892, EAF industri pertama untuk pembuatan baja baru beroperasi pada tahun 1900. Perkembangannya pesat dan ada peningkatan produksi sepuluh kali lipat dari tahun 1910 hingga 1920, dengan lebih dari 500.000 ton diproduksi pada tahun 1920, meskipun ini hanya mewakili persentase yang sangat kecil dari produksi baja global pada waktu itu. Awalnya, pembuatan baja EAF dikembangkan untuk memproduksi baja dengan grade khusus menggunakan bentuk umpan padat seperti scrap dan paduan besi. Bahan padat pertama-tama dilebur melalui peleburan busur langsung, disempurnakan melalui penambahan fluks yang sesuai dan disadap untuk diproses lebih lanjut. Gambar 1 menunjukkan rencana tipikal dan tampilan bagian dari EAF
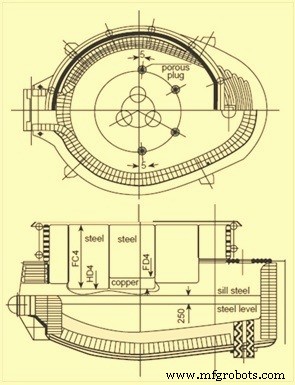
Gbr 1 Denah umum dan tampilan bagian EAF
Tungku busur listrik memiliki kapasitas mulai dari beberapa ton hingga 400 ton, dan toko peleburan baja dapat memiliki tungku tunggal atau hingga tiga atau empat. Singkatnya, tungku ini melelehkan baja dengan menerapkan arus AC ke muatan skrap baja melalui elektroda grafit. Itu membutuhkan listrik dalam jumlah yang sangat besar. Proses peleburan melibatkan penggunaan energi dalam jumlah besar dalam waktu singkat dan dalam beberapa kasus proses tersebut telah menyebabkan gangguan pada jaringan listrik. Gangguan ini biasanya dicirikan sebagai 'flicker' (ketidakteraturan singkat pada tegangan yang merupakan pecahan dari panjang siklus 50 -60 Hz), dan 'harmonik' (ketidakteraturan yang cenderung terjadi dalam pola yang berulang pada siklus 50-60 Hz) . Sampai hanya sekitar tiga puluh hingga tiga puluh lima tahun yang lalu, waktu ketuk untuk mengetuk lebih dari tiga jam cukup umum dan penggunaan daya spesifik seringkali lebih dari 700 kWh/ton, hampir dua kali lipat persyaratan termodinamika (350-370 kWh/ton).
EAF beroperasi sebagai proses peleburan batch yang menghasilkan batch baja cair. Siklus operasi EAF disebut tap to tap cycle atau panas dan terdiri dari komponen-komponen yaitu (i) pengisian tungku, (ii) fase peleburan, (iii) fase pemurnian, (iv) operasi deslagging, (v) penyadapan baja cair, dan perputaran tungku.
Waktu ketuk untuk mengetuk biasanya kurang dari 60 menit di EAF modern. Beberapa operasi tungku cangkang kembar mencapai waktu ketuk untuk mengetuk 35 hingga 40 menit.
Pengisian tungku
Langkah awal dalam produksi panas di EAF adalah memilih kelas baja yang akan dibuat. Bucket skrap di halaman skrap disiapkan untuk memenuhi persyaratan spesifikasi grade ini. Persiapan ember bekas untuk pengisian adalah operasi yang penting, tidak hanya untuk memastikan pelelehan yang tepat dalam kimia tetapi juga memastikan kondisi pelelehan yang baik. Potongan harus berlapis dalam ember sesuai dengan ukuran dan kepadatan untuk mempromosikan pembentukan cepat dari kolam cair baja di perapian sambil memberikan perlindungan untuk dinding samping dan atap dari radiasi busur listrik. Pertimbangan lain termasuk meminimalkan lubang masuk yang dapat merusak elektroda dan memastikan bahwa potongan besar yang berat tidak terletak langsung di depan port burner yang mengakibatkan tiupan api ke panel berpendingin air.
Muatan dapat mencakup kapur dan karbon atau ini dapat disuntikkan ke dalam tungku selama panas. Di banyak tempat, praktiknya adalah menambahkan kapur dan karbon ke dalam ember bekas dan melengkapinya dengan injeksi bahan-bahan ini.
Panas baru di EAF dimulai dengan pengisian memo. Atap dan elektroda dinaikkan dan diayunkan ke sisi tungku sehingga derek pengisi dapat bergerak dan menempatkan ember penuh skrap di atas tungku. Bagian bawah ember biasanya berdesain cangkang kerang. Ember terbuka dengan menarik dua segmen di bagian bawah ember dan skrap jatuh ke dalam tungku. Derek pengisi daya memindahkan ember bekas dan atap serta elektroda diayunkan kembali ke tempatnya di atas tungku.
Jumlah ember muatan skrap yang dibutuhkan untuk menghasilkan panas baja tergantung terutama pada kepadatan skrap dan volume tungku. Tungku modern dirancang untuk beroperasi dengan biaya balik minimum. Ini menguntungkan karena waktu pengisian adalah waktu mati (tungku tanpa power-on dan karenanya tidak meleleh). Meminimalkan waktu mati membantu memaksimalkan produktivitas EAF. Selain itu, sekitar 10 -20 kWh/ton energi hilang setiap kali atap tungku dibuka. Di banyak tungku, 2 hingga 3 ember skrap per panas ditujukan dengan pencampuran skrap untuk memenuhi persyaratan ini. Beberapa operasi mencapai satu biaya ember. Dalam kasus DRI (besi reduksi langsung) atau HBI (besi briket panas), pengisian terus menerus dengan bantuan hopper biasanya dilakukan. Operasi pengisian terus menerus dengan skrap juga dapat dicapai melalui 'Consteel' atau tungku poros.
Fase pencairan
Setelah pengisian EAF, atap dan kemudian elektroda diturunkan untuk membuat busur pada skrap. Ini memulai fase peleburan panas. Fase pencairan adalah inti dari operasi EAF.
EAF adalah peralatan peleburan yang sangat efisien dan desain modern didasarkan pada maksimalisasi kapasitas leburnya. Peleburan dilakukan dengan memasok energi ke interior tungku. Energi ini dapat berupa listrik atau kimia. Energi listrik disuplai melalui elektroda grafit dan biasanya memiliki kontribusi yang sangat besar dalam fase peleburan. Awalnya, tap tegangan menengah dipilih sampai elektroda masuk ke dalam memo. Biasanya, scrap ringan ditempatkan di atas muatan untuk mempercepat bore-in. Sekitar 15% dari scrap meleleh selama periode awal bore-in yang terdiri dari beberapa menit. Setelah ini, elektroda cukup menembus skrap dan kemudian keran busur panjang (tegangan tinggi) digunakan tanpa takut kerusakan radiasi pada atap. Busur panjang memaksimalkan transfer daya ke skrap dan kumpulan baja cair terbentuk di perapian tungku.
Pada awal fase ini, busur tidak menentu dan tidak stabil. Ayunan lebar dalam arus diamati yang disertai dengan gerakan cepat dari elektroda. Saat lingkungan tungku memanas, busur menjadi stabil. Setelah kolam cair terbentuk, busur menjadi cukup stabil dan input daya rata-rata meningkat.
Energi kimia disuplai melalui banyak sumber yang meliputi pembakar oxy-fuel dan tombak oksigen. Pembakar bahan bakar oxy membakar bahan bakar gas menggunakan oksigen (O2) atau udara yang diperkaya oksigen. Panas dipindahkan ke skrap oleh radiasi api dan konveksi oleh produk panas pembakaran. Panas ditransfer dalam memo dengan konduksi. Potongan yang lebih besar membutuhkan waktu lebih lama untuk meleleh ke dalam bak mandi daripada potongan yang lebih kecil. Dalam beberapa kasus, O2 disuntikkan melalui tombak pipa habis pakai untuk memotong potongan yang lebih besar.
Setelah kolam cair dihasilkan di tungku, O2 biasanya langsung dimasukkan ke dalam bak cair. O2 ini bereaksi dengan beberapa elemen dalam bak seperti aluminium (Al), silikon (Si), mangan (Mn), fosfor (P), karbon (C), dan besi (Fe) dll. Reaksi ini bersifat eksotermik dan memasok energi tambahan sehingga membantu dalam pencairan memo. Oksida logam yang terbentuk masuk ke terak. Reaksi O2 dengan C dalam penangas menghasilkan karbon monoksida (CO), yang terbakar di tungku jika ada cukup O2, dan/atau dibuang melalui sistem evakuasi langsung di mana ia dibakar dan dibawa ke sistem pengendalian polusi. O2 lancing juga dilakukan pada akhir meltdown untuk menurunkan level bath C ke level yang diinginkan pada saat penyadapan.
Setelah skrap yang cukup dicairkan untuk menampung muatan kedua, proses pengisian diulang. Setelah muatan sisa terakhir dicairkan, dinding samping tungku terkena radiasi intens dari busur listrik. Akibatnya, tegangan harus dikurangi. Atau, pembuatan terak berbusa memungkinkan busur dikubur dan ini melindungi cangkang tungku. Selain itu, sejumlah besar energi disimpan dalam terak dan dipindahkan ke bak mandi sehingga meningkatkan efisiensi energi EAF.
Setelah muatan sisa akhir meleleh sepenuhnya, kondisi rendaman datar tercapai. Pada titik ini, biasanya suhu mandi dan sampel mandi diambil. Analisis bath chemistry memungkinkan operator tungku untuk menentukan jumlah O2 yang dibutuhkan untuk dihembuskan selama pemurnian. Pada titik ini, operator juga mulai membuat pengaturan untuk penambahan paduan ferro pada penyadapan. Kuantitas diselesaikan setelah periode pemurnian.
Fase pemurnian
Pada tahap pemurnian dilakukan penghilangan Al, Si, Mn, C, P dan belerang (S) dari baja. Operasi pemurnian dilakukan setelah fase peleburan setelah kondisi rendaman datar tercapai.
Reaksi pemurnian tergantung pada ketersediaan O2. Unsur-unsur yang akan dihilangkan selama pemurnian, memiliki afinitas yang lebih tinggi untuk O2 daripada afinitas C untuk O2. Jadi O2 lebih disukai bereaksi dengan unsur-unsur ini untuk membentuk oksida yang mengapung keluar dan masuk ke terak. Dalam EAF modern, yang beroperasi dengan tumit panas dari baja cair dan terak yang tertahan dari panas sebelumnya, O2 ditiupkan ke dalam bak hampir sepanjang periode panas. Akibatnya, beberapa operasi peleburan dan pemurnian terjadi secara bersamaan.
Tingkat P dan S yang lebih tinggi dalam muatan tungku daripada yang dibutuhkan dalam baja dalam sesuai spesifikasi, harus dihilangkan. Biasanya kondisi yang menguntungkan untuk menghilangkan P adalah kebalikan dari yang diperlukan untuk menghilangkan S. Oleh karena itu, begitu elemen ini masuk ke fase terak, dapat kembali menjadi baja.
Retensi P dalam terak tergantung pada suhu rendaman, kebasaan terak, dan kadar FeO dalam terak. Pada suhu yang lebih tinggi atau kadar FeO rendah, P kembali dari terak ke dalam bak. Penghilangan P biasanya dilakukan dalam keadaan panas sedini mungkin. Latihan tumit panas sangat bermanfaat untuk menghilangkan P karena O2 dapat ditusukkan ke dalam bak mandi saat suhunya cukup rendah. Pada awal pemanasan, terak juga mengandung kadar FeO yang tinggi yang terbawa dari pemanasan sebelumnya sehingga membantu dalam penghilangan P. Kebasaan terak yang tinggi (rasio CaO/SiO2) juga bermanfaat untuk menghilangkan P tetapi diperlukan kehati-hatian tidak menjenuhkan terak dengan kapur. Hal ini dapat menyebabkan peningkatan viskositas terak, yang pada gilirannya membuat terak kurang efektif. Kadang-kadang fluorspar (CaF2) ditambahkan untuk membantu fluidisasi terak. Mengaduk rendaman dengan gas inert juga bermanfaat karena memperbaharui antarmuka terak/logam sehingga meningkatkan kinetika reaksi. Secara umum, jika tingkat P rendah merupakan persyaratan untuk mutu baja tertentu, skrap dipilih untuk memberikan tingkat lelehan yang rendah. Partisi P dalam slag ke P di bath biasanya berkisar antara 5 sampai 15. Umumnya P berkurang sebesar 20% sampai 50% di EAF.
Sulfur dihilangkan terutama sebagai sulfida yang dilarutkan dalam terak. Partisi S antara terak dan logam bergantung pada kimia terak dan disukai pada tingkat oksidasi baja yang rendah. Penghapusan S di EAF sulit terutama dalam praktek modern dimana tingkat oksidasi mandi cukup tinggi. Umumnya rasio partisi antara 3 sampai 5 dalam operasi EAF. Biasanya lebih efektif untuk melakukan desulfurisasi selama fase reduksi pembuatan baja. Ini berarti bahwa desulfurisasi dilakukan sesaat sebelum penyadapan (di mana terak kalsium aluminat dibuat) dan selama operasi tungku sendok. Untuk mengurangi kondisi di mana rendaman memiliki aktivitas O2 yang jauh lebih rendah, rasio distribusi untuk S antara 20 dan 100 dapat dicapai.
Kontrol konstituen logam dalam bak penting untuk memenuhi persyaratan spesifikasi baja. Biasanya, operator EAF mengarahkan konstituen ini pada tingkat yang lebih rendah di bak mandi daripada yang ditentukan untuk produk akhir. O2 bereaksi dengan Al, Si dan Mn membentuk oksida logam, yang merupakan konstituen terak. Logam-logam ini cenderung bereaksi dengan O2 sebelum C. Mereka juga bereaksi dengan FeO menghasilkan pemulihan unit Fe di bak. Contohnya ditunjukkan pada persamaan berikut.
Mn + FeO =MnO + Fe
Mn biasanya dikurangi menjadi sekitar 0,06 % di bak mandi.
Reaksi C dengan O2 dalam penangas untuk menghasilkan CO adalah penting karena memasok bentuk energi yang lebih murah ke penangas, dan melakukan beberapa reaksi pemurnian yang penting. Dalam EAF modern, kombinasi O2 dengan C dapat memasok sekitar 30% hingga 40% dari masukan panas bersih ke tungku. Evolusi CO sangat penting untuk pembusaan terak. Ditambah dengan terak dasar, gelembung CO terperangkap di terak menyebabkannya berbusa dan membantu mengubur busur listrik. Hal ini memberikan efisiensi termal yang jauh lebih baik dan memungkinkan tungku beroperasi pada tegangan busur tinggi bahkan setelah rendaman datar tercapai.
Gas terlarut, terutama hidrogen (H2) dan nitrogen (N2), menjadi perhatian para pembuat baja. Penguburan busur juga membantu mencegah N2 terkena busur di mana ia dapat terdisosiasi dan masuk ke dalam baja. Jika CO berevolusi di dalam bak baja, ini membantu untuk melepaskan N2 dan H2 dari baja. Kadar N2 dalam baja serendah 50 ppm dapat dicapai dalam tungku sebelum penyadapan. Penyadapan bawah bermanfaat untuk mempertahankan kadar N2 rendah karena penyadapan cepat dan aliran keran tetap terjaga. Potensi O2 yang tinggi dalam baja bermanfaat untuk kadar N2 yang rendah dan panasnya harus disadap secara terbuka daripada mematikan panasnya. Pada 1600 derajat C, kelarutan maksimum N2 dalam Fe murni adalah 450 ppm. Biasanya, kadar N2 dalam baja pada penyadapan berkisar antara 80 sampai 100 ppm. Dekarburisasi juga bermanfaat untuk menghilangkan H2. Telah terbukti bahwa dekarburasi dengan laju 1% per jam dapat menurunkan kadar H2 dalam baja dari 8 ppm menjadi 2 ppm dalam 10 menit.
Pada akhir pemurnian, pengukuran suhu mandi dan sampel mandi diambil. Jika suhu terlalu rendah, daya dapat diterapkan ke bak mandi. Temperatur rendah bukanlah masalah besar di toko peleburan baja modern di mana penyesuaian suhu dilakukan di tungku sendok.
Operasi deslagging
Operasi deslagging dilakukan untuk menghilangkan pengotor berupa terak dari tungku. Selama operasi peleburan dan pemurnian, beberapa elemen yang tidak diinginkan dalam bak teroksidasi dan masuk ke dalam terak. Adalah menguntungkan untuk menghilangkan P sebanyak mungkin ke dalam terak sedini mungkin. Tungku dimiringkan ke belakang dan terak dituangkan keluar dari tungku melalui pintu terak. Penghapusan terak menghilangkan kemungkinan pengembalian P.
Selama operasi pembusaan terak, C disuntikkan ke dalam terak di mana ia mereduksi FeO menjadi Fe logam dan dalam prosesnya menghasilkan CO yang membantu membuat busa terak. Jika terak P tinggi belum dihilangkan sebelum langkah operasi ini, pembalikan P umumnya terjadi. Selama pembusaan terak, terak dapat meluap ke tingkat ambang di EAF dan mengalir keluar dari pintu terak.
Komposisi khas dari terak EAF adalah CaO -45% sampai 58%, SiO2 – 5 % sampai 15 %, FeO- 10 % sampai 28%, MgO 5% sampai 8%, dan MnO – 2 % sampai 5 %.Selain itu juga mengandung CaF2, S, dan P.
Mengetuk baja cair
Setelah komposisi baja dan suhu yang diinginkan telah tercapai di tungku, lubang keran dibuka, tungku dimiringkan, dan baja dituangkan ke dalam sendok yang penuh untuk dipindahkan ke unit pembuatan baja sekunder. Selama proses penyadapan, penambahan paduan ferro dibuat berdasarkan analisis rendaman dan kadar baja yang diinginkan. Agen deoksidasi ditambahkan ke baja untuk menurunkan kandungan O2 sebelum diproses lebih lanjut. Deoxidizers umum adalah Al, ferrosilicon dan silika mangan. Saat membuat baja C memanas, minimal slag carry over ditujukan. Penutup terak baru dibuat selama penyadapan. Untuk operasi tungku sendok, terak kalsium aluminat adalah pilihan yang baik untuk mengontrol S. Senyawa pembentuk terak ditambahkan dalam sendok saat penyadapan sehingga penutup terak terbentuk sebelum dipindahkan ke tungku sendok.
Perputaran tungku
Perputaran tungku adalah periode antara selesainya penyadapan dan tungku siap untuk diisi untuk panas berikutnya. Selama periode ini, elektroda dan atap dinaikkan dan lapisan tungku diperiksa untuk kerusakan refraktori. Jika perlu, perbaikan dilakukan pada perapian, garis terak, lubang keran dan cerat. Dalam kasus tungku dengan sadapan bawah, lubang keran diisi dengan pasir. Perbaikan tungku dilakukan menggunakan refraktori monolitik dari campuran senjata. Peningkatan penggunaan panel berpendingin air di EAF telah mengurangi jumlah persyaratan penambalan atau pengotoran di antara pemanasan. Di banyak toko peleburan baja, bagian bawah tungku diganti dengan bagian bawah cadangan secara teratur (2 hingga 6 minggu). Pemeliharaan perapian dari bagian bawah yang diganti dilakukan secara off-line. Ini mengurangi waktu mati untuk EAF dan memaksimalkan produktivitas tungku. Waktu penyelesaian tungku biasanya merupakan periode waktu mati (mematikan) terbesar dalam siklus tap to tap. Dengan kemajuan dalam praktik tungku, ini telah berkurang dari 20 menit menjadi kurang dari 5 menit di beberapa tungku yang baru dipasang.
Keseimbangan panas EAF
Dibutuhkan minimum teoritis 300 kWh/ton untuk peleburan skrap baja. Untuk menyediakan panas berlebih di atas titik leleh 1520 derajat C memerlukan energi tambahan dan untuk persyaratan suhu keran yang umum, energi teoretis total yang dibutuhkan biasanya berkisar antara 350 hingga 370 kWh/ton. Namun, efisiensi pembuatan baja EAF berkisar antara 51% hingga 64% dan sebagai hasilnya, total masukan energi ekuivalen biasanya berkisar antara 550 hingga 700 kWh/ton di tungku modern. Energi ini dapat disuplai sebagai energi listrik, melalui pembakar oxy-fuel dari berbagai sumber bahan bakar, dan melalui reaksi kimia. Distribusi energi sangat tergantung pada bahan lokal dan biaya konsumsi dan unik untuk operasi toko peleburan tertentu. Diagram keseimbangan panas khas EAF ada di Gambar 2.
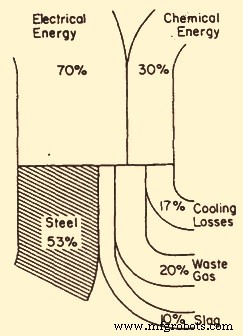
Gbr 2 Diagram keseimbangan panas tipikal untuk EAF
Konsumsi energi sangat tergantung pada operasi individu dan sangat bervariasi dari satu toko ke toko lainnya. Faktor-faktor seperti komposisi bahan mentah, tingkat input daya, dan praktik pengoperasian (misalnya pasca-pembakaran, pemanasan awal sisa) dapat sangat memengaruhi keseimbangan energi. Dalam operasi EAF yang menggunakan sejumlah besar karbon bermuatan atau bahan umpan karbon tinggi, hingga 60% energi yang terkandung dalam gas lepas dapat berupa kalori karena sejumlah besar karbon monoksida yang tidak terbakar. Pemulihan energi ini di EAF dapat meningkatkan input energi sebesar 8 hingga 10%. Oleh karena itu, penting untuk mempertimbangkan faktor-faktor tersebut saat mengevaluasi keseimbangan energi untuk operasi tungku tertentu.