Proses Pengecoran Logam
Proses Pengecoran Logam
Pengecoran logam adalah proses pembuatan bahan yang terbuat dari logam. Ini adalah proses pembentukan untuk pembentukan logam cair panas. Ini adalah rute paling sederhana dan paling langsung ke produk bentuk hampir bersih, dan seringkali yang paling murah. Ini adalah proses, di mana logam cair dituangkan ke dalam cetakan, yang berisi rongga berongga dari bentuk yang diinginkan, dan kemudian dibiarkan dingin dan mengeras. Bagian yang dipadatkan juga dikenal sebagai casting, yang dikeluarkan atau dikeluarkan dari cetakan untuk menyelesaikan proses. Pengecoran sangat sering digunakan untuk membuat bentuk kompleks yang sulit atau tidak ekonomis untuk dibuat dengan metode lain.
Proses pengecoran logam (Gambar 1) memiliki dua subdivisi yang berbeda yaitu (i) pengecoran cetakan yang tidak dapat dibuang, dan (ii) pengecoran cetakan yang dapat dibuang. Selanjutnya dipecah oleh bahan cetakan, seperti pasir atau logam, dan metode penuangan, seperti gravitasi, vakum, atau tekanan rendah.
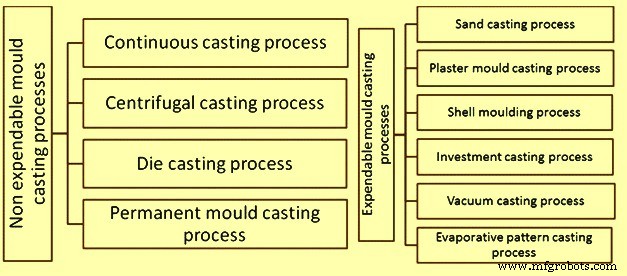
Gbr 1 Proses pengecoran logam
Proses pengecoran cetakan yang tidak dapat dibuang
Pengecoran cetakan yang tidak dapat dibuang adalah proses pengecoran di mana cetakan tidak perlu direformasi setelah setiap siklus produksi. Pengecoran cetakan yang tidak dapat dibuang adalah teknik pengecoran yang memiliki setidaknya 4 proses pengecoran yang berbeda. Ini adalah (i) pengecoran kontinyu, (ii) pengecoran sentrifugal, (iii) pengecoran mati, dan (iv) pengecoran cetakan permanen. Bentuk casting ini juga menghasilkan pengulangan yang lebih baik di bagian yang diproduksi dan menghasilkan casting yang mendekati bentuk bersih.
Proses casting berkelanjutan
Pengecoran logam secara terus menerus dapat didefinisikan sebagai proses pengecoran yang disempurnakan untuk produksi terus menerus dalam volume tinggi bentuk logam dengan penampang konstan. Selama proses tersebut, penuangan logam cair terjadi ke dalam cetakan tembaga ujung terbuka berpendingin air. Ini memungkinkan kulit logam padat terbentuk di atas pusat 'masih-cair'. Logam cair dalam pengecoran kontinyu secara bertahap mengeras dari luar menuju pusat. Setelah pemadatan awal, untaian, seperti yang sering disebut, terus menerus ditarik dari cetakan. Panjang untai yang telah ditentukan dipotong oleh gunting mekanis atau obor oxy-fuel dan dipindahkan ke proses pembentukan lebih lanjut, atau ke penyimpanan perantara. Ukuran cor dapat berkisar dari slab, slab tipis, strip, mekar atau billet. Pengecoran kontinu biasanya digunakan di mana persyaratannya adalah produksi berkelanjutan dari produk standar, dan juga peningkatan kualitas produk akhir. Ini banyak digunakan karena efektivitas biayanya. Logam yang terus menerus dicor adalah baja, aluminium, tembaga, dan timah.
Proses pengecoran sentrifugal
Pengecoran sentrifugal ditemukan oleh Alfred Krupp, yang menggunakannya untuk memproduksi ban baja tuang untuk roda kereta api pada tahun 1852. Dalam proses ini, logam cair dituangkan ke dalam cetakan dan dibiarkan mengeras saat cetakan berputar. Logam dituangkan ke tengah cetakan pada sumbu rotasinya. Karena gaya sentrifugal, logam cair terlempar keluar menuju pinggiran.
Pengecoran sentrifugal menggunakan cetakan permanen yang terus menerus diputar pada porosnya dengan kecepatan tinggi mulai dari 300 rpm (putaran per menit) hingga 3000 rpm saat logam cair dituangkan. Gaya sentrifugal menyebabkan logam terlempar keluar menuju bagian dalam dinding cetakan, di mana ia membeku setelah pendinginan. Bagian yang dicetak dengan metode ini memiliki struktur mikro butiran halus ke arah diameter luar karena efek pendinginan pada permukaan cetakan. Struktur mikro butiran yang lebih halus di permukaan luar membuat bagian cor tahan terhadap korosi atmosfer dan karenanya metode ini telah digunakan untuk pembuatan pipa. Karena logam lebih berat daripada pengotor, sebagian besar pengotor dan inklusi lebih dekat ke diameter dalam dan dapat dihilangkan dengan mesin. Permukaan akhir di sepanjang diameter dalam juga jauh lebih buruk daripada di sepanjang permukaan luar.
Mesin pengecoran sentrifugal dapat dengan sumbu horizontal atau vertikal. Mesin sumbu horizontal lebih disukai untuk silinder panjang dan tipis sedangkan mesin vertikal untuk cincin. Dalam pengecoran sentrifugal, coran dipadatkan dari luar terlebih dahulu. Aspek ini digunakan untuk mendorong pemadatan terarah dari pengecoran, dan dengan demikian memberikan sifat metalurgi yang berguna padanya. Terkadang lapisan dalam dan luar dibuang dan hanya bagian kolom perantara yang digunakan.
Proses pengecoran mati
Die casting adalah proses pengecoran logam yang ditandai dengan memaksa logam cair di bawah tekanan tinggi ke dalam rongga cetakan. Rongga cetakan dibuat menggunakan dua cetakan yang dikeraskan yang terbuat dari baja perkakas. Dies ini dikerjakan dengan mesin dan bekerja mirip dengan cetakan injeksi selama proses tersebut. Mayoritas die casting dibuat dari khusus seng, tembaga, aluminium, magnesium, timah, timah (paduan timah, tembaga dan antimon) dan paduan berbasis timah. Pengecoran logam besi juga dimungkinkan.
Tergantung pada jenis logam/paduan yang dicor, baik mesin ruang panas atau ruang dingin digunakan. Dalam proses ruang panas (digunakan untuk paduan Seng, dan magnesium) ruang tekanan yang terhubung ke rongga die diisi secara permanen dengan logam cair. Siklus dasar operasi meliputi (i) die ditutup dan silinder gooseneck diisi dengan logam cair, (ii) plunger mendorong logam cair melalui saluran gooseneck dan nozzle dan ke dalam rongga die di mana logam ditahan di bawah tekanan sampai mengeras, (iii ) die terbuka dan core, jika ada, ditarik, casting tetap di die ejector, plunger kembali, menarik logam cair kembali melalui nozzle dan gooseneck dan (iv) pin ejector mendorong casting keluar dari die ejector. Saat plunger membuka lubang masuk, logam cair mengisi ulang silinder leher angsa. Proses ruang panas digunakan untuk logam yang (i) memiliki titik leleh rendah dan (ii) tidak menyatu dengan bahan die, baja. Contohnya adalah timah, seng, dan timbal.
Dalam proses ruang dingin, logam cair dituangkan ke dalam ruang dingin di setiap siklus. Siklus operasi terdiri dari (i) die tertutup dan logam cair dimasukkan ke dalam silinder ruang dingin, (ii) plunger mendorong logam cair ke dalam rongga die di mana logam ditahan di bawah tekanan tinggi sampai mengeras, (iii) die terbuka dan plunger mengikuti untuk mendorong slug yang telah dipadatkan dari silinder, jika ada inti, mereka ditarik menjauh, dan (iv) pin ejector mendorong diejector die dan plunger kembali ke posisi semula. Proses ini sangat berguna untuk logam dengan titik leleh tinggi seperti aluminium, dan tembaga (dan paduannya).
Ada biaya modal besar yang terlibat karena peralatan pengecoran dan logam mati dan ini cenderung membatasi proses untuk produksi volume tinggi. Pembuatan suku cadang menggunakan die casting relatif sederhana, hanya melibatkan empat langkah utama, yang membuat biaya tambahan per item tetap rendah. Ini sangat cocok untuk coran berukuran kecil hingga sedang dalam jumlah besar. Karena itu, die casting menghasilkan lebih banyak casting daripada proses casting lainnya.
Die casting memiliki dua varian yaitu (i) die casting bebas pori yang digunakan untuk menghilangkan cacat porositas gas, dan (ii) die casting injeksi langsung yang digunakan dengan coran seng untuk mengurangi skrap dan meningkatkan hasil.
Metode die casting digunakan di mana bagian yang lebih halus diperlukan. Ini sangat cocok untuk aplikasi di mana banyak bagian berukuran kecil hingga menengah diperlukan dengan detail yang baik, kualitas permukaan yang halus, dan konsistensi dimensi.
Pengecoran logam semi padat (SSM) adalah proses die casting yang dimodifikasi yang mengurangi atau menghilangkan porositas sisa yang biasanya ada di banyak die casting. Daripada menggunakan logam cair sebagai bahan umpan, pengecoran SSM menggunakan bahan umpan dengan viskositas lebih tinggi yang sebagian padat dan sebagian cair. Mesin die casting yang dimodifikasi digunakan untuk menyuntikkan bubur semi-padat ke dalam cetakan baja keras yang dapat digunakan kembali. Viskositas tinggi dari logam semi-padat, bersama dengan penggunaan kondisi pengisian die yang terkontrol, memastikan bahwa logam semi-padat mengisi die dengan cara yang tidak bergolak sehingga porositas yang berbahaya pada dasarnya dapat dihilangkan. Coran SSM digunakan secara komersial terutama untuk paduan aluminium dan magnesium. Coran ini dapat diberi perlakuan panas pada temper T4, T5 atau T6. Kombinasi perlakuan panas, laju pendinginan yang cepat (dari penggunaan die baja yang tidak dilapisi) dan porositas minimal memberikan kombinasi kekuatan dan keuletan yang sangat baik. Keuntungan lain dari pengecoran SSM termasuk kemampuan untuk menghasilkan bagian berbentuk kompleks, bentuk jaring, kekencangan tekanan, toleransi dimensi yang ketat, dan kemampuan untuk mencetak dinding tipis.
[
Proses pengecoran cetakan permanen
Pengecoran cetakan permanen adalah proses pengecoran logam yang menggunakan cetakan yang dapat digunakan kembali (cetakan permanen), biasanya terbuat dari matal. Proses yang paling umum menggunakan gravitasi untuk mengisi cetakan. Namun, tekanan gas atau vakum juga digunakan. Sebuah variasi pada proses pengecoran gravitasi khas, yang disebut pengecoran lumpur, menghasilkan coran berongga. Logam tuang yang umum adalah aluminium, magnesium, dan paduan tembaga. Bahan lainnya termasuk timah, seng, dan paduan timah. Besi dan baja juga dicetak dalam cetakan grafit. Cetakan permanen, meskipun bertahan lebih dari satu kali pengecoran, masih memiliki masa pakai yang terbatas sebelum aus.
Di sini, dua bagian cetakan terbuat dari logam, biasanya besi tuang, baja, atau paduan tahan api. Rongga, termasuk runner dan sistem gating dikerjakan ke dalam bagian cetakan. Untuk bagian berongga, biasanya digunakan inti permanen (terbuat dari logam) atau terikat pasir, tergantung pada apakah inti dapat diekstraksi dari bagian tanpa kerusakan setelah pengecoran. Permukaan cetakan dilapisi dengan tanah liat atau bahan tahan api keras lainnya untuk meningkatkan umur cetakan. Sebelum dicetak, permukaannya ditutup dengan semprotan grafit atau silika, yang berfungsi sebagai pelumas. Ini memiliki dua tujuan yaitu (i) meningkatkan aliran logam cair, dan (ii) memungkinkan bagian cor ditarik dari cetakan dengan lebih mudah. Prosesnya dapat diotomatisasi, dan karenanya menghasilkan tingkat throughput yang tinggi. Selain itu, menghasilkan toleransi yang sangat baik dan permukaan akhir.
Cetakan untuk proses pengecoran terdiri dari dua bagian. Cetakan pengecoran umumnya dibentuk dari besi tuang abu-abu karena memiliki ketahanan lelah termal terbaik, tetapi bahan lainnya termasuk baja, perunggu, dan grafit. Logam ini dipilih karena ketahanannya terhadap erosi dan kelelahan termal. Mereka biasanya tidak terlalu rumit karena cetakan tidak menawarkan keruntuhan untuk mengkompensasi penyusutan. Sebaliknya cetakan dibuka segera setelah pengecoran dipadatkan, yang mencegah air mata panas. Inti dapat digunakan dan biasanya terbuat dari pasir atau logam. Cetakan dipanaskan sebelum siklus pengecoran pertama dan kemudian digunakan terus menerus untuk mempertahankan suhu yang seragam mungkin selama siklus. Ini mengurangi kelelahan termal, memfasilitasi aliran logam, dan membantu mengontrol laju pendinginan logam tuang. Ventilasi biasanya terjadi melalui celah kecil antara dua bagian cetakan, tetapi jika ini tidak cukup maka lubang ventilasi yang sangat kecil digunakan. Mereka cukup kecil untuk membiarkan udara keluar tetapi bukan logam cair. Riser juga digunakan untuk mengkompensasi penyusutan. Ini biasanya membatasi hasil hingga kurang dari 60%. Ejector mekanis dalam bentuk pin digunakan ketika pelapis tidak cukup untuk menghilangkan gips dari cetakan. Pin ini ditempatkan di seluruh cetakan dan biasanya meninggalkan bekas bulat kecil pada casting.
Empat jenis utama pengecoran cetakan permanen adalah (i) gravitasi, (i) lumpur, (iii) tekanan rendah, dan (iv) vakum.
Proses gravitasi dimulai dengan memanaskan cetakan hingga 150 derajat C hingga 200 derajat C untuk memudahkan aliran dan mengurangi kerusakan termal pada pengecoran. Rongga cetakan kemudian dilapisi dengan bahan tahan api atau pencuci cetakan, yang mencegah pengecoran menempel pada cetakan dan memperpanjang umur cetakan. Pasir atau inti logam apa pun kemudian dipasang dan cetakan ditutup rapat. Logam cair kemudian dituangkan ke dalam cetakan. Segera setelah pemadatan, cetakan dibuka dan coran dilepas untuk mengurangi kemungkinan robekan panas. Proses ini kemudian dimulai dari awal lagi, tetapi pemanasan awal tidak diperlukan karena panas dari pengecoran sebelumnya cukup dan lapisan tahan api biasanya berlangsung beberapa kali pengecoran. Logam dituangkan pada suhu praktis terendah untuk meminimalkan retakan dan porositas.
Proses pengecoran lumpur adalah varian dari pengecoran cetakan permanen untuk membuat pengecoran berongga. Dalam prosesnya logam cair dituangkan ke dalam cetakan dan dibiarkan dingin sampai cangkang material terbentuk di dalam cetakan. Logam cair yang tersisa kemudian dituangkan keluar untuk meninggalkan cangkang berongga. Pengecoran yang dihasilkan memiliki detail permukaan yang baik tetapi ketebalan dinding dapat bervariasi. Proses ini biasanya digunakan untuk logam dengan titik leleh rendah. Ini menggunakan bahan yang lebih sedikit daripada pengecoran padat, dan menghasilkan produk yang lebih ringan dan lebih murah. Angka cor berongga umumnya memiliki lubang kecil di mana kelebihan cairan dituangkan. Demikian pula, proses yang disebut 'slush moulding' digunakan dalam pembuatan dasbor termoplastik otomotif, di mana resin cair dituangkan ke dalam cetakan berongga yang panas dan membentuk kulit kental dan kemudian kelebihan lumpur dikeringkan, cetakan didinginkan, dan cetakan produk dilucuti.
Pengecoran cetakan permanen bertekanan rendah menggunakan gas pada tekanan rendah, biasanya antara 20 kPa hingga 100 kPa untuk mendorong logam cair ke dalam rongga cetakan. Tekanan diterapkan ke bagian atas kumpulan cairan, yang memaksa logam cair ke atas tabung penuang tahan api dan akhirnya ke bagian bawah cetakan. Tabung tuang memanjang ke dasar sendok sehingga logam cair yang didorong ke dalam cetakan sangat bersih. Tidak diperlukan riser karena tekanan yang diberikan memaksa logam cair masuk untuk mengkompensasi penyusutan. Hasil biasanya lebih dari 85 % karena tidak ada riser dan logam apa pun di tabung tuang hanya jatuh kembali ke sendok untuk digunakan kembali. Sebagian besar coran cetakan permanen bertekanan rendah berasal dari aluminium dan magnesium, tetapi beberapa adalah paduan tembaga. Keuntungannya termasuk sedikit turbulensi saat mengisi cetakan karena tekanan konstan, yang meminimalkan porositas gas dan pembentukan kotoran. Sifat mekanik sekitar 5% lebih baik daripada pengecoran cetakan permanen gravitasi. Kerugiannya adalah waktu siklus lebih lama daripada pengecoran cetakan permanen gravitasi.
Pengecoran cetakan permanen vakum mempertahankan semua keuntungan dari pengecoran cetakan permanen tekanan rendah, ditambah gas terlarut dalam logam cair diminimalkan dan kebersihan logam cair bahkan lebih baik. Proses ini dapat menangani profil berdinding tipis dan memberikan permukaan akhir yang sangat baik. Sifat mekanis biasanya 10% hingga 15% lebih baik daripada pengecoran cetakan permanen gravitasi.
Proses pengecoran cetakan yang dapat dibuang
Pengecoran cetakan yang dapat dibuang adalah klasifikasi umum yang mencakup pengecoran cetakan pasir, plastik, cangkang, plester, dan investasi (teknik lilin hilang). Metode pengecoran cetakan ini melibatkan penggunaan cetakan sementara yang tidak dapat digunakan kembali.
Proses pengecoran pasir
Proses pengecoran pasir juga dikenal sebagai proses pengecoran cetakan pasir, adalah salah satu jenis pengecoran yang paling populer dan sederhana. Prosesnya menggunakan pasir sebagai bahan cetakan. Ini telah digunakan selama berabad-abad. Pengecoran pasir memungkinkan batch yang lebih kecil daripada pengecoran cetakan permanen dan dengan biaya rendah. Pengecoran pasir memungkinkan sebagian besar logam dicor tergantung pada jenis pasir yang digunakan untuk cetakan. Pengecoran pasir diproduksi di bengkel khusus yang dikenal sebagai pengecoran. Lebih dari 70% dari semua pengecoran logam diproduksi melalui proses pengecoran pasir.
Pasir untuk pengecoran relatif murah dan cukup tahan api bahkan untuk produksi pengecoran baja. Selain pasir, bahan pengikat yang sesuai (biasanya tanah liat) dicampur atau dibuat dengan pasir. Campuran dibasahi, biasanya dengan air, tetapi kadang-kadang dengan zat lain, untuk mengembangkan kekuatan dan plastisitas tanah liat dan untuk membuat agregat cocok untuk dicetak. Pasir biasanya ditampung dalam sistem bingkai atau kotak cetakan. Rongga cetakan dan sistem gerbang dibuat dengan memadatkan pasir di sekitar pola yang diukir langsung ke pasir.
Pengecoran pasir memerlukan waktu tunggu berhari-hari, atau bahkan berminggu-minggu, untuk produksi pada tingkat output tinggi (1–20 lembar/jam-cetakan) dan tidak tertandingi untuk produksi sebagian besar. Pasir hijau (lembab) hampir tidak memiliki batas berat bagian, sedangkan pasir kering memiliki batas massa bagian praktis mulai dari 2.300 kg hingga 2.700 kg. Berat komponen minimum berkisar antara 0,075 kg hingga 0,1 kg. Pasir diikat bersama menggunakan tanah liat, pengikat kimia, atau oli terpolimerisasi (seperti oli motor). Pasir dapat didaur ulang berkali-kali di sebagian besar operasi dan hanya membutuhkan sedikit perawatan.
Pengecoran pasir menggunakan pasir alam atau pasir sintetis (pasir danau) yang sebagian besar merupakan bahan tahan api yang disebut silika (SiO2). Butiran pasir harus cukup kecil sehingga dapat dikemas padat dan cukup besar untuk memungkinkan gas yang terbentuk selama penuangan logam keluar melalui pori-pori. Cetakan berukuran lebih besar menggunakan pasir hijau (campuran pasir, tanah liat dan sedikit air). Pasir dapat digunakan kembali, dan kelebihan logam yang dituangkan dipotong dan digunakan kembali juga. Cetakan pasir khas terbuat dari dua bagian, bagian atas disebut cop, dan bagian bawah adalah drag. Cairan mengalir ke celah antara dua bagian, yang disebut rongga cetakan. Geometri rongga dibuat dengan menggunakan bentuk kayu, yang disebut pola. Bentuk pola (hampir) identik dengan bentuk bagian yang akan dicor. Ada rongga berbentuk corong. Bagian atas corong adalah tempat penuangan sedangkan leher corong yang berbentuk pipa adalah sariawan. Logam cair dituangkan ke dalam cangkir tuang, dan mengalir ke sariawan. Pelari adalah saluran berlubang horizontal yang menghubungkan bagian bawah sariawan ke rongga cetakan. Wilayah di mana setiap pelari bergabung dengan rongga disebut gerbang. Beberapa rongga tambahan dibuat menghubungkan ke permukaan atas cetakan. Kelebihan logam cair yang dituangkan ke dalam cetakan mengalir ke rongga-rongga ini, yang disebut riser. Mereka bertindak sebagai reservoir. Saat logam mengeras di dalam rongga, ia menyusut, dan logam tambahan dari riser mengalir kembali ke bawah untuk menghindari lubang di bagian cor. Ventilasi adalah lubang sempit yang menghubungkan rongga ke atmosfer untuk memungkinkan gas dan udara di rongga keluar. Inti dimasukkan untuk membuat permukaan interior bagian cor. Hal ini diperlukan karena banyak bagian cor memiliki lubang interior (bagian berongga), atau rongga lain dalam bentuknya yang tidak dapat diakses secara langsung dari salah satu bagian cetakan. Inti dibuat dengan memanggang pasir dengan beberapa pengikat sehingga dapat mempertahankan bentuknya saat ditangani. Cetakan dirakit dengan menempatkan inti ke dalam rongga drag, dan kemudian menempatkan mengatasi di atas. Cetakan setelah perakitan terkunci. Setelah pengecoran selesai, pasir dikocok, dan inti ditarik dan biasanya dipatahkan.
Proses pengecoran cetakan plesteran
Proses pengecoran cetakan gipsum mirip dengan pengecoran pasir kecuali bahwa plesteran paris (gipsum, CaSO4) menggantikan pasir sebagai bahan cetakan. Plester tersebut bukan merupakan plaster of paris murni, melainkan memiliki bahan tambahan untuk meningkatkan kekuatan hijau, kekuatan kering, permeabilitas, dan castability. Misalnya, talc atau magnesium oksida ditambahkan untuk mencegah keretakan dan mengurangi waktu pengerasan. Penambahan kapur dan semen membatasi ekspansi selama pemanggangan sementara penambahan serat kaca meningkatkan kekuatan. Pasir dapat digunakan sebagai bahan pengisi. Rasio bahan adalah 70% hingga 80% gipsum dan 20% hingga 30% zat tambahan.
Plester paris adalah bubuk putih halus, yang jika dicampur dengan air menjadi seperti tanah liat konsistensi dan dapat dibentuk di sekitar pola. Gips plester dapat diselesaikan untuk menghasilkan permukaan akhir yang sangat baik dan akurasi dimensi. Namun, relatif lunak dan tidak cukup kuat pada suhu di atas 1200 derajat C, sehingga metode ini terutama digunakan untuk membuat coran dari logam non-ferrous seperti seng, tembaga, aluminium, dan magnesium.
Selama pengecoran cetakan plester, pertama-tama, plester dicampur dan pola disemprot dengan lapisan tipis senyawa pemisah untuk mencegah plester menempel pada pola. Plester kemudian dituangkan di atas pola dan unit diguncang sehingga plester memenuhi semua fitur kecil. Plester biasanya mengeras dalam waktu sekitar 15 menit dan polanya kemudian dilepas. Cetakan kemudian dipanggang, antara 120 derajat C dan 260 derajat C, untuk menghilangkan kelebihan air. Cetakan kering kemudian dirakit, dipanaskan, dan logam dituangkan. Akhirnya, setelah logam mengeras, plester dipatahkan dari bagian cornya. Plester bekas tidak dapat digunakan kembali.
Karena plester memiliki konduktivitas termal yang lebih rendah, pengecoran mendingin secara perlahan, dan oleh karena itu memiliki struktur butir yang lebih seragam (yaitu lebih sedikit lengkungan, lebih sedikit tegangan sisa).
Umumnya, formulir membutuhkan waktu kurang dari seminggu untuk disiapkan, setelah itu tingkat produksi 1 unit hingga 10 unit /jam.cetakan dapat dicapai, dengan barang sebesar 45 kg dan sekecil 30 gram dengan penyelesaian permukaan yang sangat baik dan penutupan toleransi. Pengecoran cetakan gips adalah alternatif yang tidak mahal untuk proses pencetakan lainnya untuk bagian yang kompleks karena biaya plester yang rendah dan kemampuannya untuk menghasilkan cetakan yang mendekati bentuk bersih.
Proses pencetakan cangkang
Proses pencetakan cangkang, juga dikenal sebagai pengecoran cetakan cangkang, adalah proses pengecoran cetakan habis pakai yang menggunakan pasir berlapis resin untuk membentuk cetakan. Cetakan cangkang mirip dengan pengecoran pasir, tetapi rongga cetakan dibentuk oleh 'cangkang' pasir yang mengeras alih-alih labu yang diisi dengan pasir. Pasir yang digunakan lebih halus dari pasir pengecoran pasir dan dicampur dengan resin sehingga dapat dipanaskan oleh pola dan dikeraskan menjadi cangkang di sekitar pola. Karena resin dan pasir yang lebih halus, ini memberikan permukaan akhir yang jauh lebih halus. Prosesnya mudah otomatis dan lebih presisi daripada pengecoran pasir. Proses ini sangat ideal untuk item kompleks yang berukuran kecil hingga sedang dan yang membutuhkan presisi lebih tinggi. Dibandingkan dengan pengecoran pasir, proses ini memiliki akurasi dimensi yang lebih baik, tingkat produktivitas yang lebih tinggi, dan kebutuhan tenaga kerja yang lebih rendah.
Dalam proses pencetakan cangkang, seperti pengecoran pasir, logam cair dituangkan ke dalam cetakan yang dapat dibuang. Cetakan adalah cangkang berdinding tipis yang dibuat dari penerapan campuran pasir-resin di sekitar pola. Pola, potongan logam dalam bentuk bagian yang diinginkan, digunakan kembali untuk membentuk beberapa cetakan cangkang. Pola yang dapat digunakan kembali memungkinkan tingkat produksi yang lebih tinggi, sedangkan cetakan sekali pakai memungkinkan geometri yang kompleks untuk dicetak. Proses pencetakan cangkang memerlukan penggunaan pola logam, oven, campuran pasir-resin, kotak pembuangan, dan logam cair.
Proses pencetakan cangkang memungkinkan penggunaan logam besi dan non-besi, paling umum menggunakan besi tuang, baja karbon, baja paduan, baja tahan karat, paduan aluminium, dan paduan tembaga. Suku cadang tipikal berukuran kecil hingga sedang dan memerlukan akurasi tinggi, seperti rumah roda gigi, kepala silinder, batang penghubung, dan lengan tuas.
Proses pencetakan cangkang menghasilkan kualitas dan toleransi permukaan yang lebih baik. Prosesnya terdiri dari pembuatan pola 2 bagian dari logam (misalnya aluminium atau baja) yang kemudian dipanaskan antara 175 derajat C hingga 370 derajat C, dan kemudian dilapisi dengan pelumas (misalnya semprotan silikon). Masing-masing setengah pola yang dipanaskan ditutupi dengan campuran pasir dan pengikat resin/epoksi termoset. Pengikat merekatkan lapisan pasir ke pola, membentuk cangkang. Prosesnya bisa diulang untuk mendapatkan cangkang yang lebih tebal. Setelah ini, rakitan dipanggang untuk menyembuhkannya. Pola-pola tersebut kemudian dihilangkan, dan dua setengah cangkang bergabung bersama untuk membentuk cetakan. Logam tersebut kemudian dituangkan ke dalam cetakan. Saat logam mengeras, cangkangnya dipecah untuk mendapatkan bagiannya.
Proses casting investasi
Proses pengecoran investasi juga dikenal sebagai proses pengecoran lilin yang hilang. Ini adalah proses yang telah dipraktekkan selama ribuan tahun, dengan proses lilin yang hilang menjadi salah satu teknik pembentukan logam tertua yang diketahui. Dari 5000 tahun yang lalu, ketika lilin lebah membentuk polanya, hingga lilin berteknologi tinggi saat ini, bahan tahan api, dan paduan khusus, pengecoran memastikan komponen berkualitas tinggi diproduksi dengan manfaat utama akurasi, pengulangan, keserbagunaan, dan integritas.
Casting investasi mendapatkan namanya dari fakta bahwa polanya diinvestasikan, atau dikelilingi, dengan bahan tahan api. Pola lilin membutuhkan perawatan yang sangat hati-hati karena tidak cukup kuat untuk menahan gaya yang dihadapi selama pembuatan cetakan. Salah satu keuntungan casting investasi adalah lilin dapat digunakan kembali.
Langkah-langkah dalam proses pengecoran investasi adalah (i) pola lilin diproduksi dengan cetakan injeksi, (ii) beberapa pola dirakit ke sariawan lilin pusat, (iii) cangkang dibangun dengan merendam rakitan dalam bubur keramik cair dan kemudian ke dalam lapisan pasir yang sangat halus dan mungkin memerlukan beberapa lapisan, (iv) Keramik dikeringkan, lilin dilelehkan dan keramik dibakar untuk membakar semua lilin, (v) cangkang diisi dengan logam cair dengan penuangan gravitasi. Pada pemadatan, bagian, gerbang, sariawan dan cangkir tuang menjadi satu pengecoran padat. Pengecoran berongga dapat dilakukan dengan menuangkan kelebihan logam sebelum mengeras, (vi) setelah logam mengeras, cangkang keramik dipatahkan oleh getaran atau peledakan air, dan (vii) bagian-bagian dipotong dari sariawan menggunakan gesekan kecepatan tinggi gergaji dan finishing kecil diberikan pada bagian akhir.
Proses ini cocok untuk produksi berulang komponen bentuk bersih dari berbagai logam yang berbeda dan paduan kinerja tinggi. Meskipun umumnya digunakan untuk pengecoran kecil, proses ini telah digunakan untuk menghasilkan kusen pintu pesawat yang lengkap, dengan coran baja hingga 300 kg dan pengecoran aluminium hingga 30 kg. Dibandingkan dengan proses pengecoran lain seperti die casting atau pengecoran pasir, ini bisa menjadi proses yang mahal. Namun, komponen yang dapat diproduksi menggunakan pengecoran investasi dapat menggabungkan kontur yang rumit, dan dalam banyak kasus komponen dicetak mendekati bentuk jaring, sehingga memerlukan sedikit atau tanpa pengerjaan ulang setelah dicetak.
Proses pengecoran vakum
Proses ini juga disebut pengecoran counter-gravity. Proses ini digunakan ketika jebakan udara menjadi masalah, ada detail rumit atau undercut, atau jika bahannya diperkuat serat atau kawat. Pada dasarnya prosesnya sama dengan casting investasi, kecuali langkah pengisian cetakan yang merupakan langkah (v) di atas. Dalam hal ini, bahan tersedot ke atas ke dalam cetakan dengan pompa vakum. Cetakan muncul dalam posisi terbalik dari proses pengecoran biasa, dan diturunkan ke dalam labu dengan logam cair. Salah satu keuntungan dari pengecoran vakum adalah bahwa dengan melepaskan tekanan untuk waktu yang singkat setelah cetakan diisi, logam yang tidak padat dapat dilepaskan kembali ke dalam labu. Hal ini memungkinkan pembuatan pengecoran berongga. Karena sebagian besar panas dikonduksikan dari permukaan antara cetakan dan logam, maka bagian logam yang paling dekat dengan permukaan cetakan selalu membeku terlebih dahulu. Bagian depan yang solid bergerak ke dalam ke dalam rongga. Jadi, jika cairan dikeringkan dalam waktu yang sangat singkat setelah pengisian, maka dimungkinkan untuk mendapatkan benda berongga berdinding sangat tipis.
Proses pengecoran pola evaporatif
Proses pengecoran pola evaporasi adalah jenis proses pengecoran yang menggunakan pola yang terbuat dari bahan yang akan menguap ketika logam cair dituangkan ke dalam rongga cetakan. Artinya tidak perlu mengeluarkan bahan pola dari cetakan sebelum pengecoran. Bahan pola evaporasi yang paling umum digunakan adalah busa polistiren. Dua proses utama adalah pengecoran busa hilang dan pengecoran cetakan penuh.
Pengecoran busa hilang adalah jenis proses pengecoran pola penguapan yang mirip dengan pengecoran investasi kecuali busa digunakan untuk pola sebagai pengganti lilin. Proses ini memanfaatkan titik didih busa yang rendah untuk menyederhanakan proses pengecoran investasi dengan menghilangkan kebutuhan untuk melelehkan lilin dari cetakan.
Pengecoran cetakan penuh adalah proses pengecoran pola penguapan yang merupakan kombinasi dari pengecoran pasir dan pengecoran busa yang hilang. Ini menggunakan pola busa polistiren yang diperluas yang kemudian dikelilingi oleh pasir, seperti pengecoran pasir. Logam kemudian dituangkan langsung ke dalam cetakan, yang menguapkan busa saat bersentuhan.
Perbedaan utamanya adalah pengecoran dengan busa yang hilang menggunakan pasir yang tidak terikat dan pengecoran cetakan penuh menggunakan pasir yang terikat (atau pasir hijau). Karena perbedaan ini cukup kecil, ada banyak tumpang tindih dalam terminologi. Ada banyak istilah non-proprietary yang telah digunakan untuk menggambarkan proses ini. Ini termasuk pengecoran tanpa rongga, pengecoran busa evaporatif, pengecoran penguapan busa, pengecoran pola yang hilang, proses castral, dan pencetakan polistiren yang diperluas. Istilah kepemilikan yang digunakan meliputi Styro-cast, Foam cast, Replicast, dan Policast.