Zona Terkena Panas dan Sifat Logam Las dalam Pengelasan Baja
Zona Pengaruh Panas dan Sifat Logam Las dalam Pengelasan Baja
Ada banyak faktor yang mengontrol sifat logam las dan zona terpengaruh panas (HAZ) saat pengelasan karbon (C) dan baja paduan rendah. Logam las dan HAZ sering disebut sebagai las baja. Proses pengelasan, bahan habis pakai pengelasan, dan parameter pengelasan juga mempengaruhi sifat-sifat ini. Sifat las baja juga dipengaruhi oleh atmosfer korosif dan pembebanan siklik yang sering dialami.
Zona terkena panas
Selama pemilihan baja, karakteristik HAZ lebih penting daripada logam las. Ini karena sifat metalurgi dan mekanik dari HAZ terkait langsung dengan baja yang dipilih. Namun, sifat ini dapat disesuaikan dengan parameter pengelasan dan perlakuan panas pasca las (PWHT). Juga masalah metalurgi dan/atau kemampuan las yang terkait dengan karakteristik HAZ lebih sulit untuk ditangani daripada yang berhubungan dengan logam las. Masalah pengelasan yang biasanya terjadi pada logam las seringkali dapat diatasi dengan mengganti elektroda las dan/atau bahan las lainnya. Sebagai perbandingan, kesulitan dengan HAZ seringkali dapat diselesaikan hanya dengan mengganti baja dasar, yang umumnya merupakan ukuran yang sangat mahal, atau dengan mengubah masukan panas. Setara C empiris yang berbeda (CE) telah dikembangkan dan digunakan untuk mengevaluasi kemampuan las dan kecenderungan retak terinduksi hidrogen (H2) pada baja dasar.
Persamaan yang paling sering digunakan untuk CE yang juga digunakan oleh International Institute of Welding (IIW) adalah CE =% C + % Mn/6 + (% Cu + % Ni)/15 + (% Cr + % Mo + % V)/5. Di Jepang, parameter karakterisasi komposisi Ito-Bessyo, Pcm, lebih banyak digunakan. Pcm dianggap memungkinkan penilaian yang lebih realistis dari kemampuan las baja C rendah, jika dibandingkan dengan persamaan IIW. Persamaan ini adalah Pcm =% C + % Si/30 + (% Mn + %Cu +% Cr)/20 + % Ni/60 + % Mo/15 + %V/10 + 5 B. Persamaan lain yang dikembangkan di Jepang adalah untuk bilangan ekuivalen C (CEN) yang menggabungkan persamaan IIW untuk CE dan Pcm. CEN serupa dengan Pcm untuk baja dengan level C yang kurang dari 0,17%, dan mengikuti persamaan IIW pada level C yang lebih tinggi. Persamaan untuk CEN adalah CEN =% C + A(C) [%Si/24 + % Mn/6 + % Cu/15 + % Ni/20 + (%Cr + % Mo + % Nb + % V)/ 5 + 5B]. Dalam persamaan ini A(C) sama dengan 0.75 + 0.25 tan h [20 (% C – 0,12)].
Meskipun persamaan CE ini awalnya dikembangkan untuk mengkarakterisasi kecenderungan retak H2 dalam baja, persamaan ini juga digunakan untuk menilai kemampuan mengeras baja berdasarkan kimia. Terdapat korelasi antara CE, Pcm dan volume martensit baik di daerah berbutir kasar maupun di daerah halus. Dengan meningkatnya nilai Pcm, volume dan kekerasan martensit di kedua wilayah meningkat.
Berbagai daerah di HAZ baja feritik telah ditentukan dan dikarakterisasi menggunakan suhu puncak spesifik dari siklus termal las HAZ bersama dengan diagram fase kesetimbangan Fe-C. Daerah ini adalah daerah berbutir kasar, halus, interkritis, subkritis, dan sebagian cair. Namun, perilaku metalurgi di HAZ yang mengalami pemanasan dan pendinginan cepat adalah proses non-ekuilibrium. Oleh karena itu, diagram continuous cooling transformation (CCT) lebih tepat digunakan untuk memprediksi struktur mikro di HAZ. Laju pendinginan terkait erat dengan ketebalan baja, geometri sambungan, dan masukan panas pengelasan. Laju pendinginan yang biasanya paling kritis dalam aplikasi pengelasan adalah yang turun antara 800 derajat C dan 500 derajat C. Saat masukan panas pengelasan meningkat atau ketebalan baja berkurang, laju pendinginan antara suhu ini berkurang.
Pengaruh elemen paduan utama pada baja C dan baja paduan rendah pada struktur mikro dan ketangguhan HAZ menunjukkan bahwa C memiliki peran yang sangat penting dalam kekerasan keseluruhan baja yang dilas. Hal ini dapat dilihat dengan jelas oleh perannya dalam persamaan CE dan Pcm. Peningkatan level C mendukung pembentukan produk transformasi suhu yang lebih rendah, seperti bainit dan martensit, dan mengarah pada penurunan yang signifikan dalam ketahanan pembelahan HAZ.
Mangan (Mn), selain pengerasan larutan padat, menurunkan suhu transformasi austenit menjadi ferit sambil memberikan efek penguatan dengan penyempurnaan butir. Namun, tingkat Mn harus dibatasi untuk meminimalkan segregasi solidifikasi dan ikatan mikrostruktur.
Kromium (Cr) adalah elemen penguat larutan padat dan pembentuk karbida. Ini meningkatkan hardenability baja dan meningkatkan ketahanan oksidasi dan korosi. Penambahan Cr menguntungkan dalam kasus di mana pengendapan Cr karbida menekan pembentukan pelat samping ferit melalui efek menjepit.
Nikel (Ni) dianggap memiliki efek menguntungkan pada transformasi baja, mirip dengan Mn, dengan menurunkan suhu transformasi austenit. Penambahan Ni juga meningkatkan ketangguhan, serta memberikan efek pengerasan larutan padat.
Vanadium (V) dan niobium (Nb) ditambahkan dalam jumlah kecil pada baja paduan rendah untuk mendapatkan sifat mekanik yang diinginkan. Dengan membentuk V(C,N) dan Nb(C,N), V dan Nb menghambat rekristalisasi dan pertumbuhan butir austenit selama pengerolan dan normalisasi. Selama pengelasan fusi, terutama dengan masukan panas tinggi, V(C,N) dan Nb(C,N) larut dalam HAZ dengan suhu puncak lebih dari 1100 derajat C dan mengendap kembali selama pendinginan yang lebih lambat. Pengendapan ulang V(C,N) dan Nb(C,N) melemahkan ketangguhan HAZ.
Titanium (Ti), dalam bentuk Ti nitrida yang stabil, mencegah pengkasaran butir austenit sebelumnya di daerah yang dekat dengan batas fusi las.
Melas logam
Penggunaan bahan pengisi sangat umum dalam banyak proses pengelasan fusi. Ketika memilih logam pengisi/elektroda yang tepat, pertimbangan utama adalah apakah logam las dapat diproduksi bebas cacat atau tidak dan apakah logam las kompatibel atau tidak dengan baja dasar dan dapat memberikan sifat yang memuaskan. Karakteristik ini ditentukan oleh (i) kimia elektroda, (ii) pengenceran baja dasar, (iii) bahan fluks atau gas pelindung, dan (iv) pemadatan kolam las serta pendinginan dan transformasi selanjutnya.
Pemilihan bahan pengisi yang tepat tidak didasarkan pada pencocokan kimia dengan baja dasar. Sebaliknya, ini didasarkan pada pencocokan logam las dan sifat baja dasar. Menggunakan bahan pengisi dengan bahan kimia yang identik dengan baja dasar mungkin tidak memberikan hasil yang diinginkan, karena struktur mikro logam las sama sekali berbeda dari baja dasar. Untuk banyak baja C dan baja paduan rendah, pemadatan dan laju pendinginan yang cepat yang terlibat dalam pengelasan fusi menghasilkan logam las yang memiliki kekuatan lebih tinggi dan sifat ketangguhan yang lebih rendah daripada baja dasar ketika memiliki kimia yang sama. Oleh karena itu, bahan pengisi seringkali mengandung kadar C yang lebih rendah daripada baja dasar. Kekuatan logam las tidak ditingkatkan dengan meningkatkan kandungan C, tetapi dengan menambahkan elemen paduan yang memberikan penguatan larutan padat atau pengendapan dan modifikasi struktur mikro.
Struktur mikro logam las dalam baja C dan baja paduan rendah mengandung berbagai konstituen, mulai dari ferit blok, ferit acicular, hingga bainit, hingga martensit. Efek elemen paduan dan pendinginan pada struktur mikro logam las dinyatakan dalam diagram skematik CCT (Gambar 1), sedangkan efek elemen paduan pada kekerasan dan ketangguhan takik logam las ditunjukkan pada Gambar 2.
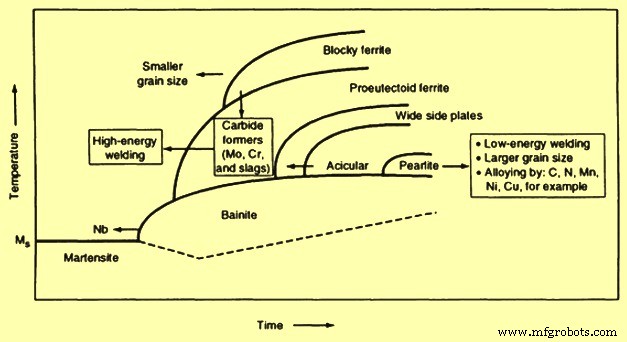
Gbr 1 Efek elemen paduan dan pendinginan pada struktur mikro logam las
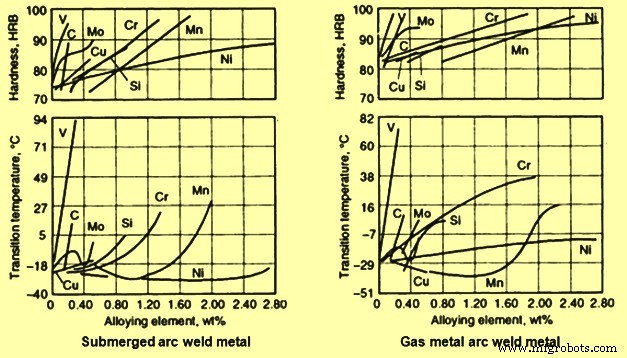
Gbr 2 Efek elemen paduan pada kekerasan dan ketangguhan takik logam las
Pelelehan baja dasar dan pencampuran selanjutnya dengan bahan pengisi menyebabkan kimia akhir dari deposit las berada antara baja dasar dan bahan pengisi. Ketika bahan pengisi memiliki kimia yang sama dengan baja dasar, kimia logam las akhir secara teoritis tetap sama. Tergantung pada jumlah baja dasar yang dicairkan dan jumlah bahan pengisi yang ditambahkan, kimia akhir dari deposit las dapat diperkirakan dengan menggunakan persamaan pengenceran yaitu % pengenceran =(berat baja induk yang dilebur/berat total baja bekas ) x 100. Faktor-faktor seperti konfigurasi sambungan dan preparasi tepi mempengaruhi pengenceran. Proses dan parameter pengelasan yang meningkatkan penetrasi juga dapat meningkatkan pengenceran.
Dalam sekali las lintasan, kandungan beberapa elemen dalam logam las dapat diperkirakan dengan menggunakan rumus 'Elemen spesifik dalam logam las =(elemen dalam logam dasar x pengenceran) + (elemen dalam bahan pengisi) x (1 – pengenceran)'. Dalam beberapa kasus, pengenceran yang lebih besar lebih disukai, mengingat ada perubahan drastis yang lebih kecil dalam sifat mekanik dan sifat lainnya melintasi batas fusi. Namun, dalam aplikasi yang melibatkan kelongsong las atau permukaan las, lebih diinginkan untuk meminimalkan pengenceran. Ini karena bahan pengisi mengandung elemen paduan yang lebih mahal yang disesuaikan untuk memberikan sifat logam las tertentu. Ketika ada kekhawatiran bahwa baja dasar dapat memasukkan kotoran dan/atau elemen paduan yang tidak diinginkan, maka disarankan teknologi pengelasan yang menurunkan pengenceran. Ini juga termasuk pertimbangan untuk fosfor (P) dan belerang (S) dan untuk kandungan C dan silikon (Si) yang lebih tinggi, yang berdampak buruk pada sifat logam las.
Perbandingan pengelasan single pass dan multi pass
Dalam hal sifat mekanik, khususnya ketangguhan, logam las multi-pass biasanya lebih baik daripada logam las single-pass karena alasan yaitu (i) siklus termal pemanasan ulang dari setiap pengelasan berikutnya menormalkan dan menghaluskan bagian-bagian dari struktur mikro pada logam las sebelumnya, (ii) lintasan las berikutnya meredam logam las sebelumnya dan mengurangi tegangan dari lintasan sebelumnya, (iii) masukan energi total per lintasan berkurang, yang membantu membatasi jumlah pertumbuhan butir, dan (iv) lintasan las sebelumnya memberikan pemanasan awal yang memperlambat laju pendinginan lintasan berikutnya.
Terlihat bahwa daktilitas logam las (luas penampang) meningkat seiring dengan bertambahnya luas butiran total. Selanjutnya, ketika fluks aktif digunakan dalam pengelasan busur terendam (SAW), jumlah lintasan las yang diterapkan pada sambungan terbatas. Hal ini karena ada kecenderungan elemen paduan (seperti Si dan Mn) terbentuk selama pengelasan multi-pass, yang menurunkan nilai ketangguhan fraktur pada pengelasan akhir.
Kemampuan las dan jenis baja
Baja paduan rendah kekuatan tinggi (HSLA) dirancang untuk memiliki sifat mekanik dan kemampuan las yang lebih baik, jika dibandingkan dengan baja C konvensional. Perbaikan ini diperoleh melalui penambahan sejumlah kecil elemen paduan, seperti Nb, V, Ti, N2 (nitrogen), dan C, yang memperkuat ferit, meningkatkan hardenability, dan mengontrol ukuran butir. Sebagian besar baja ini dipasok dalam kondisi as-rolled, normalisasi, dan beberapa dipasok dalam kondisi perlakuan pengendapan, juga. Ukuran butir yang lebih halus dan jumlah perlit yang lebih besar menghasilkan kekuatan dan ketangguhan yang lebih tinggi dari baja ini. Selain itu, kandungan C yang lebih rendah dari baja ini (maksimum 0,22%) menghasilkan kemampuan las yang baik.
Biasanya kemampuan las baja HSLA mirip dengan baja ringan. Meskipun baja HSLA memiliki kemampuan las yang baik, pertimbangan pemanasan awal dan pengendalian H2 dalam proses pengelasan tetap penting untuk memastikan pengelasan yang berhasil. Penggetasan di HAZ berbutir kasar adalah salah satu perhatian selama pengelasan baja HSLA. Penggetasan ini disebabkan oleh laju pendinginan yang lambat yang mengarah pada pembentukan struktur mikro yang tidak diinginkan, seperti pelat samping ferit kasar (ferit Widmanstätten dan bainit atas) dan ferit batas butir, terutama pada tingkat masukan energi yang tinggi.
Untuk baja HSLA yang mengandung Nb dan V, logam las dan HAZ menunjukkan ketangguhan takik rendah pada input panas tinggi, seperti yang digunakan dalam proses pengelasan terak elektro (ESW) dan SAW. Ini karena masukan panas yang tinggi meningkatkan tingkat HAZ berbutir kasar. Laju pendinginan rendah yang terkait di HAZ mengurangi kemungkinan penyempurnaan butir dan meningkatkan kemungkinan pengendapan karbida Nb dan V, yang menyebabkan penggetasan HAZ berbutir kasar. Masukan panas yang tinggi dan pengenceran yang lebih tinggi juga membawa masalah pengerasan presipitasi Nb dan V karbida ke logam las.
Penggunaan baja dengan sedikit penambahan Ti (maksimum 0,04%) dan N2 telah terbukti efektif meminimalkan pertumbuhan butir di HAZ berbutir kasar. Ini karena stabilitas Ti nitrida yang lebih besar pada suhu puncak yang dialami di daerah berbutir kasar (lebih dari 1100 derajat C), di mana Nb dan V karbida diubah kembali menjadi larutan.
Baja C rendah terdiri dari dua jenis baja, yaitu (i) baja C rendah dengan kandungan C kurang dari 0,15% dan (ii) baja ringan dengan kandungan C antara 0,15% dan 0,30%. Untuk baja C rendah dalam kondisi anil, struktur mikro utama adalah ferit yang relatif lunak dengan partikel karbida kecil yang tersebar, sedangkan baja C rendah dalam kondisi canai panas atau normal memiliki pulau perlit. Selama pengelasan fusi, HAZ mengalami transformasi dari ferit menjadi austenit pada saat pemanasan, dan dari austenit kembali menjadi ferit selama pendinginan. Pada level C ini, pengerasan yang terlibat dalam HAZ adalah sekitar 10 HRC atau kurang.
Namun, ketika pengelasan mengalami operasi pembentukan dingin, biasanya disarankan bahwa kandungan C dibatasi hingga 0,06%. HAZ baja dengan kandungan C yang lebih tinggi umumnya tidak memiliki keuletan yang baik untuk mengakomodasi regangan yang terlibat dalam pembentukan dingin.
Ketika baja C rendah disuplai sebagai baja berbingkai, wilayah inti pusatnya cenderung mengandung konsentrasi senyawa seperti karbon monoksida (CO) dan karbon dioksida (CO2), serta unsur-unsur seperti S dan P, sebagai akibat dari pemisahan selama tindakan rimming. Selain itu, gas-gas hasil reaksi antara oksigen terlarut (O2) dan C juga terperangkap di daerah inti pusat. Selama operasi pengelasan, sejumlah baja dasar meleleh dan bercampur dengan bahan pengisi karena pengenceran. Temperatur tinggi dari kolam las cair memberikan kondisi yang memungkinkan reaksi O2-C yang tidak lengkap berlanjut dan CO dan CO2 yang terperangkap berkembang. Ketika laju pemadatan kolam las sangat cepat untuk gas keluar maka jebakan mereka mengarah ke pori-pori di logam las. Oleh karena itu, deoksidasi kolam las yang cukup adalah cara praktis untuk menghindari masalah porositas saat mengelas baja berbingkai.
Ketika baja C rendah disuplai sebagai baja mati, porositas logam las tidak lagi menjadi masalah selama pengelasan fusi. Sebaliknya, terak tahan api kental kadang-kadang terbentuk pada permukaan kolam las dari baja yang terbunuh, yang membuat aliran logam cair lamban dan manipulasi kolam las menjadi sulit. Terak menjadi kental ketika deoksidasi, seperti Al (aluminium), Ti, dan Zr (zirkonium) digunakan dalam praktik pembunuhan baja, membentuk oksida dengan suhu leleh yang relatif tinggi. Masalah dengan terak ini lebih diperparah dengan pengelasan oxy-acetylene, karena suhu rendah yang terlibat dalam proses. Solusi yang biasa dilakukan adalah memilih bahan pengisi yang mengandung Mn dan Si dalam jumlah yang cukup untuk mengurangi titik leleh dan meningkatkan aliran terak.
Baja ringan juga dianggap dapat dilas, dan retak dingin biasanya tidak menjadi masalah jika kandungan C kurang dari 0,2% dan kandungan Mn kurang dari 1,0%. Pra-panas, kontrol suhu antar-lintas, PWHT, atau teknik pengelasan khusus biasanya tidak diperlukan saat mengelas baja dengan ketebalan 25 mm atau kurang. Kandungan C biasanya lebih tinggi pada baja yang lebih tebal untuk memberikan kekuatan yang dibutuhkan. Selain itu, tingkat pendinginan HAZ terkait selama pengelasan fusi baja lebih tebal lebih tinggi. Oleh karena itu, ketika mengelas baja yang lebih tebal dari 25 mm, atau ketika kandungan C dan Mn masing-masing lebih tinggi dari 0,3% dan 1,4%, maka tindakan pencegahan yang tepat dan penggunaan elektroda atau fluks H2 rendah diperlukan untuk mencegah retak H2.
Saran yang berguna dalam memilih baja C-Mn dan mikro-paduan C-Mn dengan kemampuan las dan ketangguhan yang optimal, seperti yang ditetapkan oleh Dolby diberikan di sini. Untuk baja ini dengan lebih dari 0,1% C, dasar baja dengan kandungan C rendah dan CE rendah, tetapi sifat ketangguhan tinggi harus digunakan. Baja yang diperlakukan Al untuk membatasi lebar daerah berbutir kasar di HAZ dan meminimalkan tingkat N2 bebas (endapan aluminium-nitrida relatif stabil) perlu dipilih. Baja yang dipilih harus bersih. Baja yang diberi perlakuan Al atau vakum degas memiliki tingkat S yang lebih rendah. Perlakuan kalsium (Ca) untuk kontrol bentuk sulfida meningkatkan sifat mekanik dalam arah ketebalan tembus dan mengurangi robekan pipih yang terkait dengan masalah retak likuidasi.
Saat menggunakan proses pengelasan dengan input energi tinggi untuk baja dasar dengan komposisi C-Mn yang sama, penambahan Nb dan V menurunkan ketangguhan HAZ, karena pengendapan Nb dan V karbida atau karbo-nitrida yang terjadi selama pendinginan dan pemanasan ulang. Baja paduan mikro dengan kurang dari 0,1% C biasanya memiliki ketangguhan yang lebih tinggi dan kecenderungan yang berkurang untuk retak H2 di HAZ. Baja dengan perlakuan Al yang bersih dengan nilai ketangguhan tinggi perlu dipilih karena alasan yang diberikan di atas untuk baja C-Mn. Tindakan pencegahan yang sama juga berlaku seperti yang disebutkan di atas mengenai proses pengelasan dengan input energi tinggi.
Baja paduan rendah yang memiliki kadar C rendah harus dipilih. Ketahanan pembelahan yang tinggi dapat diperoleh ketika kekerasan baja cukup untuk mengembangkan martensit C rendah untuk kondisi pengelasan yang digunakan. Perawatan diperlukan dalam PWHT baja yang memiliki kuantitas substansial pengendapan sekunder elemen paduan pengerasan, seperti Nb dan V. Perhatian juga harus diberikan pada PWHT baja yang mengandung sejumlah besar elemen sisa seperti P, Sb (antimon ), As (arsenik), dan Sn (timah).
Baja yang diolah dengan Al bersih dengan nilai ketangguhan tinggi harus dipilih untuk alasan seperti yang diberikan di atas untuk baja C-Mn. Selain itu, tindakan pencegahan yang sama terkait proses pengelasan dengan input energi tinggi juga berlaku di sini.
Baja proses yang dikontrol secara termo-mekanis (TMCP) menunjukkan sifat kekuatan dan ketangguhan yang jauh lebih baik serta kemampuan las. Teknologi ini menggunakan pendinginan yang dipercepat yang memungkinkan untuk mencapai tingkat kekuatan yang sama pada tingkat C yang lebih rendah seperti yang dicapai baja canai terkontrol konvensional pada tingkat C yang lebih rendah (kurang dari 0,06 %). Alih-alih memperkuat dengan meningkatkan kandungan C, baja TMCP mengembangkan kekuatan dan ketangguhannya dari ferit yang sangat halus dan struktur mikro fase kedua (perlit atau bainit yang tersebar halus) yang terjadi selama tahap pendinginan yang dipercepat dari proses tersebut. Sebagai hasil dari pengurangan kandungan C dan CE, baja ini secara signifikan meningkatkan ketahanan terhadap retak dingin yang diinduksi H2 (HICC). Oleh karena itu, kekhawatiran yang terkait dengan pemanasan awal, kontrol suhu inter-pass, dan PWHT selama proses pengelasan tidak kritis. Namun, pelunakan HAZ, terutama pada masukan panas tinggi, mengkhawatirkan, karena struktur mikro yang menguntungkan dari baja TMCP dikembalikan selama pendinginan lambat di HAZ pada tingkat masukan panas tinggi.
Baja Cr-Mo (molibdenum) adalah bahan yang relatif murah, jika dibandingkan dengan baja paduan tinggi dan digunakan dalam industri listrik dan petrokimia karena ketahanannya terhadap oksidasi, ketahanan mulur suhu tinggi, dan ketahanan korosi sulfida. Kandungan Cr memberikan baja ketahanan korosi oksidasi, sedangkan kandungan Mo meningkatkan kekuatan suhu tinggi. Kehadiran karbida stabil yang terdistribusi secara halus meningkatkan ketahanan mulur. Karena kandungan elemen paduan dan sekitar 0,15% tingkat C, baja ini dapat dikeraskan dengan udara. Baja ini biasanya dipasok dalam kondisi normalisasi dan temper atau padam dan temper (Q&T). Kemampuan las baja Cr-Mo sangat mirip dengan Q&T dan baja paduan rendah yang dapat dikeraskan. Masalah utama di HAZ adalah retak di daerah berbutir kasar yang diperkeras, serta pelunakan HAZ antara suhu Ac1 dan Ac3. Reheat cracking selama PWHT dan paparan jangka panjang pada suhu tinggi juga menyebabkan kesulitan yang parah. Untuk baja ini, pemanasan awal dan suhu inter-pass yang tepat perlu dipilih, dan teknik pengelasan H2 rendah harus digunakan.
Sementara PWHT tidak diperlukan untuk baja Cr-Mo dengan tingkat Cr yang lebih rendah dan pengukur yang lebih tipis, PWHT sering dilakukan segera setelah pengelasan sebagai bagian dari teknik pengelasan. PWHT dari lasan Cr-Mo kadang-kadang juga disebut sebagai perlakuan panas pelepas tegangan. Perlakuan panas tersebut ditujukan untuk menghilangkan tegangan sisa dengan proses relaksasi mulur dan untuk meredam struktur mikro yang dikeraskan seperti yang dilas untuk meningkatkan ketangguhan patah dari HAZ dan logam las. Efek menguntungkan tambahan dari PWHT adalah untuk memungkinkan disipasi H2 yang lebih tinggi di daerah las dan untuk lebih mengurangi kemungkinan HICC. Meskipun perlakuan pelepas tegangan atau PWHT sering digunakan dalam las baja Cr-Mo, jenis baja ini rentan terhadap retak pelepas tegangan di HAZ selama perlakuan tersebut atau retak reheat selama proses pemanasan ulang pasca las, termasuk jangka pendek. paparan atmosfer suhu tinggi. Kisaran suhu terjadinya stress relief/reheat cracking adalah antara 500 derajat C dan 700 derajat C. Meskipun tidak jelas, mekanisme retak diyakini terkait dengan penguatan bagian dalam butir sebagai akibat dari presipitasi.
Retak terjadi selama pemanasan ulang ketika batas butir yang relatif lunak yang bebas dari endapan tidak dapat mengakomodasi deformasi plastis selama relaksasi rangkak. Parameter yang dikenal sebagai 'Psr' telah dikembangkan untuk menghubungkan kerentanan baja Cr-Mo untuk memanaskan ulang retak ketika baja mengandung 1,5% max Cr, 1,0% max Cu, 2.0% max Mo, dan 0.15% max V, Nb, dan Ti. Hubungannya seperti yang diberikan oleh persamaan 'Psr =%Cr + %Cu + 2x %Mo + 10x %V + 7x %Nb + 5x %Ti – 2'.
Ketika Psr kurang dari nol, material dianggap sensitif terhadap retak panas ulang. Namun, bila ada lebih dari 2% Cr, kecenderungan retak dihilangkan. Parameter lain yang memperhitungkan elemen tramp dan yang mengarah pada penggetasan batas butir dan meningkatkan kecenderungan retak panas ulang, adalah 'faktor komposisi logam' (MCF) yang diberikan oleh persamaan 'MCF =%Si + 2x %Cu + 2x %P + 10x %As + 15x %Sn + 20x %Sb'. Nilai MCF yang lebih tinggi juga meningkatkan kerentanan baja Cr-Mo untuk memanaskan ulang retak.
Teknik pengelasan yang biasa digunakan untuk mengurangi kemungkinan retak panas ulang diringkas sebagai (i) mengurangi penambah tegangan dalam desain las, (ii) penggunaan praktik pengelasan yang meminimalkan tegangan sisa seperti meningkatkan suhu pemanasan awal dan mengurangi pengekangan. , (iii) pengurangan kekuatan logam las untuk akomodasi deformasi plastis pada logam las bila dapat diterapkan dan diperlukan, dan (iv) pengurangan konsentrasi tegangan di daerah berbutir kasar.
Baja Q&T biasanya disuplai dalam kondisi perlakuan panas yang melibatkan austenisasi dan/atau pendinginan dan temper untuk mendapatkan sifat kekuatan tinggi. Kemampuan mengeras baja Q&T sedemikian rupa sehingga HAZ terdiri dari struktur mikro martensit dan bainit C rendah. Jenis struktur mikro HAZ yang dilas ini memiliki sifat mekanik yang diinginkan yang dekat dengan baja dasar. Oleh karena itu, baja ini biasanya tidak memerlukan perawatan PWHT atau stress-relief, kecuali dalam situasi khusus tertentu.
Tidak seperti baja paduan rendah yang dapat dikeraskan lainnya di mana input energi tinggi digunakan untuk menghindari pembentukan martensit di HAZ, penggunaan baja Q&T membutuhkan kondisi pengelasan yang mencakup laju pendinginan di HAZ yang cukup cepat untuk memastikan reformasi struktur mikro martensit dan bainit. Hal ini diperlukan karena laju pendinginan HAZ terlalu lambat untuk menyebabkan HAZ austenitisasi berubah menjadi ferit dan campuran bainit dan martensit. Selama transformasi ferit pro-eutektoid dari austenit, austenit yang tidak tertransformasi menjadi kaya C yang kemudian berubah menjadi bainit dan martensit yang keras dan rapuh. Struktur mikro campuran ferit, bainit, dan martensit ini menyebabkan penggetasan HAZ berbutir kasar. Semakin lambat laju pendinginan, semakin besar tingkat embrittlement di HAZ. Laju pendinginan kritis yang lebih cepat (masukan panas yang lebih sedikit) diperlukan untuk menghindari transformasi struktur mikro campuran yang rapuh saat mengelas baja yang kurang dapat dikeraskan atau lebih tipis.
Kekhawatiran lain selama pengelasan baja Q&T adalah perawatan yang ketat dari teknik pengelasan H2 rendah untuk mencegah retak dingin di bawah manik. Pemanasan awal adalah salah satu cara paling efektif untuk mengurangi kecenderungan retak dingin. Namun, pemanasan awal juga secara signifikan mengurangi laju pendinginan di HAZ. Oleh karena itu, ini harus diterapkan sedemikian rupa sehingga laju pendinginan cepat yang memuaskan dapat dicapai di HAZ.
Ketika pengelasan baja Q&T memiliki tingkat kekuatan yang lebih tinggi, kecenderungan terjadinya retak H2 pada logam las meningkat. Oleh karena itu, kadar air yang diijinkan dalam pelapisan elektroda dan fluks, serta penanganan bahan-bahan ini, menjadi jauh lebih kritis. Untuk baja Q&T dengan tingkat kekuatan luluh (YS) di bawah 480 N/sq mm, kadar air 0,4% adalah batas yang diizinkan dalam elektroda tertutup, sedangkan untuk baja dengan tingkat kekuatan di atas 690 N/mm persegi, batasnya adalah 0,1%. Penggunaan teknik temper bead juga dapat membantu menghindari daerah yang tidak diinginkan dengan kekerasan tinggi dan ketangguhan rendah di HAZ.
Pengelasan multi pass adalah teknik yang baik dalam pengelasan baja Q&T. Selain efek pemurnian dan tempering pada logam las dari lintasan las sebelumnya, masukan panas yang lebih kecil dari pengelasan multi lintasan, dibandingkan dengan pengelasan lintasan tunggal membantu dalam mencapai laju pendinginan yang cepat. Jika retak H2 pada logam las mengkhawatirkan, maka pengelasan multi pass lapisan tipis akan digunakan, bersama dengan perendaman pada suhu inter pass untuk waktu yang telah ditentukan sebelum menyimpan pass berikutnya. Meskipun teknik ini membantu menghilangkan H2 dalam logam las di setiap lintasan las, teknik ini mengurangi produktivitas.
Pada baja Q&T, terdapat daerah pelunakan pada HAZ yang disebabkan oleh siklus termal HAZ dengan suhu puncak antara Ac1 dan Ac3 (inter critical region). Pada suhu di bawah Ac3 selama pemanasan, karbida tidak sepenuhnya larut dalam austenit. Oleh karena itu, tingkat C dalam austenit menjadi konsentrasi yang lebih rendah. Selama pendinginan, austenit tak jenuh berubah pada suhu tinggi dan menghasilkan struktur mikro dengan kekuatan lebih rendah.
Pertimbangan dalam pengelasan
Baja karbon dan baja paduan rendah yang digunakan untuk aplikasi struktural umumnya tidak digunakan dalam atmosfer korosif yang parah. Namun, mereka sering digunakan dalam kondisi korosif sedang, seperti di kilang minyak dan pipa gas/minyak asam. Kehadiran las biasanya menyebabkan penurunan ketahanan korosi karena alasan yaitu (i) variasi komposisi baja dasar, HAZ, dan logam las yang menghasilkan situasi yang mendukung korosi galvanik, (ii) adanya tegangan sisa dari pengelasan yang mengarah pada retak korosi tegangan (SCC), dan (iii) adanya diskontinuitas las seperti cacat permukaan, yang bertindak sebagai tempat yang menguntungkan untuk serangan korosi lokal.
Dalam suasana korosif, pencegahan retak korosi tegangan sulfida dan HIC (SSCC) adalah penting. HIC, yang telah diamati baik pada baja berkekuatan tinggi maupun baja berkekuatan rendah, bahkan dalam kondisi tidak tertekan, terjadi terutama pada baja berkekuatan rendah yang terpapar pada atmosfer yang mengandung H2. Karena pendinginan dan pemadatannya yang cepat, logam las membentuk struktur dendrit dan memiliki inklusi oksida yang tersebar dalam bentuk butiran halus. Telah terlihat bahwa logam las, bahkan ketika digunakan tanpa logam pengisi dari bahan kimia khusus, tidak mengembangkan HIC hingga kekerasan maksimum 280 HV. Sebagai perbandingan, HIC telah diamati terutama pada baja dasar dan HAZ.
SCC didefinisikan sebagai fenomena retak yang terjadi pada kondisi korosif sulfida ketika baja mengalami tegangan. Baja yang akan digunakan dalam atmosfer yang mengandung H2 sulfida (H2S) dapat dipilih dengan tepat. Umumnya nilai 22 HRC (248 HV) disarankan sebagai batas kekerasan untuk baja yang digunakan untuk pipa saluran yang digunakan dalam aplikasi gas asam.
Dalam kasus pengelasan, HAZ biasanya menjadi lebih keras daripada baja dasar, dan, akibatnya, lebih rentan terhadap SCC. Selain struktur mikro yang lebih rentan, faktor lain yang berkontribusi tidak baik terhadap SCC adalah tegangan sisa las dan adanya sudut masuk dari tutup las sebagai penambah tegangan di daerah yang dilas. Ketika sambungan las Q&T atau dinormalisasi, HAZ menghilang dan kecenderungan HAZ sebelumnya untuk mengembangkan SCC diubah. Kerentanan SCC lebih tinggi pada kondisi as-welded dibandingkan pada kondisi Q&T (PWHT).
Retak lelah pada struktur yang dilas di bawah pembebanan siklik sering terlihat berkembang di daerah ujung las. Hal ini disebabkan oleh fakta bahwa ujung las adalah daerah konsentrasi tegangan. Toe adalah titik pertemuan antara baja dasar dan logam las dan di mana perubahan tertinggi di kedua bagian. Juga, intrusi terak yang dihasilkan dari operasi pengelasan sering hadir di daerah kaki las. Teknik yang berbeda telah digunakan untuk meningkatkan kekuatan lelah struktur yang dilas dengan mengurangi konsentrasi tegangan di daerah ujung las dan tulangan las. Teknik-teknik ini adalah (i) menghilangkan tulangan las pada kedua sisi sambungan butt dengan pemesinan las ke tingkat baja dasar, (ii) meningkatkan radius dan sudut masuk dari ujung las dengan menggiling secara mekanis daerah berpotongan antara las dan the base steel, (iii) changing the state of surface weld residual stress by the mechanical cold working of the weld surface and the base steel at the weld toe region, (iv) coating and painting the welds and base steel to prevent corrosion in the region of stress concentration, (v) increasing the toe radius and weld entrant angle by adding a weld bead on both sides of the reinforcements using a filler material with high fluidity, (vi) using welding conditions which result in a greater weld toe radius and entrant angle, and (vii) re-melting the surface in the weld toe regions for flattening and smoothing weld profiles using the gas tungsten arc welding (GTAW) process.
Effect of welding technique on the properties of steel weldment
The American Welding Society (AWS) defines a welding technique as the detailed method and practice which includes all joint welding processes involved in the production of a weldment. In a detailed review of the relationship between techniques and weldment properties, the following are the conclusions.
- For any welding process/steel combination, welding techniques have a predominant role, along with the electrode (if a filler material is used), in determining the quality and mechanical properties of the weldment. However, these two variables (welding techniques and mechanical properties) do not have a direct cause-effect relationship.
- The mechanical properties of steel are attributable only to its soundness, microstructure, and chemical composition, and to whether or not it is base steel, weld metal, vapour-deposited metal, electrodeposited metal or any other type. The response of steel to mechanical forces depends on its present state and not on the manner in which this state has been created.
- Metallurgical research has established relationships between mechanical properties and microstructure, such as the inverse relationship between grain size and strength, the difference in strength between pearlite and martensite, the embrittling effect of grain boundary films, the harmful effect of inclusions, and others. On the other hand, there is no direct relationship between the current setting of a welding machine and the final properties of the weldment. Rather, the true cause and effect relationship is that (i) increased current introduces more heat into the steel, (ii) increased heat affects both the HAZ and the structure of the weld metal in a particular manner, depending on the steel chemistry, phases which are present, and other factors, and (iii) difference in structure results into different mechanical properties.
The factors connected with the specific welding technique, which affect weldment properties are given below.
Temperature of preheat
Preheating is the application of heat to the base steel immediately before welding, brazing, soldering, or cutting. The preheat temperature depends on many factors, such as the composition and mass of the base steel, the ambient temperature, and the welding technique.
Preheating is done for (i) reducing shrinkage stresses in the weld and adjacent base steel which is mainly important with highly restrained joints, (ii) making available a slower rate of cooling through the critical temperature range (around 880 deg C to 720 deg C), which prevents excessive hardening and lowers the ductility of both the weld and the HAZ of the base steel, and (iii) making available a slower rate of cooling down to 200 deg C, allowing more time for any H2 which is present to diffuse away from the weld and adjacent steel in order to avoid under bead cracking.
Gas torches, gas burners, heat treating furnaces, electric resistance heaters, low frequency induction heating, and temporary furnaces are some of the preheating methods which are used. The selection of the method depends on many factors, such as the preheat temperature, the length of preheating time, the size and shape of the parts, and whether it is a ‘one of a kind’ or a continuous production type of operation. For critical applications, the preheat temperature is to be precisely controlled. In these cases, controllable heating systems are used, and thermocouples are attached directly to the part being heated. The thermocouple measures the exact temperature of the part and provides a signal to a controller, which regulates the fuel or electrical power required for heating. By accurately regulating the fuel or power, the temperature of the part being heated can be held to close limits. Many standards need precise heat temperature control.
Temperature of inter pass
The inter pass temperature, which is involved in multi pass welds, is denoted by the minimum and maximum temperatures of the deposited weld metal and adjacent base steel before the next pass is started. Normally, steel which needs preheating to a specified temperature is also to be kept at this temperature between weld passes. With many weldments, the heat input during welding is adequate to maintain the inter pass temperature. On a massive weldment, it is not possible that the heat input of the welding process is enough to maintain the required inter pass temperature. If this is the case, then torch heating between passes is usually needed.
Once an assembly has been preheated and the welding has begun, it is required to finish welding as soon as possible in order to avoid the need for inter-pass heating. Because the purpose of preheating is to reduce the cooling rate, it logically follows that the same slow cooling is to be given for all passes. This can only be done by maintaining an inter pass temperature which is at least equal to the preheat temperature. If this is not done, then each individual bead is subjected to the same high quench rate as the first bead of a non-preheated assembly.
The required minimum temperatures which are needed are based on specific steel, welding process, and steel thickness. When heat buildup becomes excessive, the weldment is to be allowed to cool, but not below the minimum inter pass temperature. The temperature of the welding area need to be maintained within minimum and maximum inter pass temperatures.
Post weld heat treatment
A PWHT is normally considered necessary for welds in thicker section steel, in order to reduce the high as welded residual stress level and improve the toughness and defect tolerance of the joint. Many fabrication standards provide guidelines on the duration and temperature of the PWHT, although some differences between various standards exist. In assessing the time and temperature needed to provide a suitable PWHT, it is necessary to know how such parameters respond to different heat treatment schedules.
In all heat treatments, with the possible exception of fusion, the heating rate and time can be specified. The maximum temperature is related to the composition of the steel, the holding time (at the maximum temperature) is related to the steel thickness, and the cooling rate is related to the particular treatment and to the standard. The rate of heating generally ranges from 150 deg C to 180 deg C per hour. The holding time is typically 2.5 min/mm of maximum thickness in order to provide uniform heating throughout. The cooling rate also ranges from 150 deg C to 180 deg C per hour, down to a specific temperature. In some cases, the cooling rate can be increased when the part has cooled to a certain temperature. The rates of heating, holding, and cooling are usually part of the specification and need to be followed explicitly.
Effects of PWHT on the HAZ properties of welds in a C – Mn steel
A study was conducted to show the effects of PWHT on the variation in HAZ properties (strength, hardness, and toughness) with different PWHT parameters. The study was carried out on a 50 mm steel of C- Mn grade which had been killed with Si and treated with Al and Nb. This grade was chosen since it is increasingly being used in pressure vessel application and in many off-shore fabrication and other structures. The SAW process had been used with a heat input of around 3.4 kJ/mm of the fill pass. Also, the effects of multiple PWHT cycles, which are often encountered in pressure vessel fabrication or in cases where repairs have been made, have been studied in the same manner.
Longitudinal tensile tests of the HAZ were conducted. No noteworthy effect which was due to multiple stress-relief cycles was noted in the HAZ region. The values observed exceeded the steel plate minimum requirements. Adequate ductility and elongation values were observed at 600 deg C. No noteworthy effect of PWHT time on the HAZ yield stress (YS), tensile strength (TS) or ductility at this temperature was seen. The data indicated that only a minor reduction in YS and TS were noticed with increasing PWHT temperature. No significant effect on ductility was seen.
For Charpy impact tests, five testing temperatures were chosen and three samples were tested at each of the temperature. These temperatures were 0 deg C, -20 deg C, -40 deg C, -60 deg C, and -80 deg C. For the welds, one sample was taken from the first side of the HAZ, one from the second side of the HAZ, and one from the HAZ at the steel plate mid-thickness, which was associated with second side welds. The data had shown that multiple PWHT cycles had only a marginal effect, in that a slight increase in the number of low values at low temperatures was observed at two and three cycles, particularly from specimens machined from the steel plate mid thickness.
Although extended PWHT has not led to an appreciable variation in HAZ Charpy properties from the 1/4 t and 3/4t locations, a pronounced drop in absorbed energy levels was seen after 4 hours in samples machined from the steel plate mid-thickness. It was clearly seen that the toughness at the steel plate mid thickness appears to fall off with time, although this does not happen at the 1/4t locations.
The effects of increasing the PWHT temperature had shown that no pronounced effect of temperature on toughness exists, except at the steel plate mid thickness. Here, there seems to be a trend of increasing transition temperature with increasing PWHT temperature.
A survey on the hardness was also conducted. Hardness traverses were conducted in the macro section from two welds after PWHT, reaching from the parent steel plate which was unaffected by the welding processes into the weld metal. Similar traverses were made on welds 1 and 2 in the as welded condition. On each macro section, three traverses were made at the locations namely (i) 3 mm below the surface of the first side, (ii) at the steel plate mid thickness, and (iii) 3 mm below the surface of the second side. In all the cases, a 98 N load was used on a Vickers hardness machine. The as-welded hardness data from welds 1 and 2 had shown that the steel plate values were around 170 HV to 180 HV, weld-metal values were 200 HV to 220 HV, and the peak HAZ hardness was below 240 HV.
Multiple PWHTs had little influence on HAZ or steel plate hardness, where peak HAZ values of less than 240 HV were obtained and steel plate hardness values were around 140 HV to 160 HV. In all welds, the hardness at the steel plate mid thickness was slightly higher than it was at the surfaces, because of the presence of a segregated band, as is being frequently observed in continuously cast steels.
Weld-metal hardness had shown a more noticeable effect when exposed to multiple stress-relief cycles. Welds 1 and 2 had a fairly uniform hardness of around 200 HV, but after the third PWHT cycle, the weld metal hardness levels dropped to 160 HV to 220 HV, with the lowest values appearing at the weld mid thickness. The values had shown only a slight reduction in HAZ hardness as PWHT time increases. Steel plate hardness values were unaffected. The weld metal behaved in a nonsystematic manner. Hardness values between around 190 HV and 210 HV were observed after 1 hour, increasing to around 200 HV to 220 HV after 2 hours, and decreasing to around 160 HV to 195 HV after 4 hours.
It was seen that the steel plate and HAZ hardness levels appear to be fairly insensitive to PWHT temperature. No obvious trends in the variation of hardness with temperature were visible. However, a slight drop in steel plate hardness had been seen. Weld metal hardness appears to decline after a 650 deg C PWHT, where hardness values of around 180 HV to 190 HV had been recorded. This compared with hardness values of around 190 HV to 210 HV, which were recorded at 550 deg C and 600 deg C.
It was concluded that increasing the PWHT time at 600 deg C, whether by prolonging single treatment or by using multiple treatments, had little effect on the mechanical properties. In addition, increasing the PWHT temperature from 550 deg C to 650 deg C resulted in no significant drop in HAZ strength or hardness. However, evidence for a drop in the HAZ Charpy V notch toughness at the steel plate mid thickness with increasing temperature was found.
Heat Input
The welding process and welding technique both influence the energy input which is used to make a weld. The higher is the energy input, the slower us the cooling rate. Heat input is a function of welding current, arc voltage, and travel speed. To increase the heat input, either the welding current is required to be increased or the travel speed needs to be reduced. Welding current is related to the process and the electrode size. Heat input is calculated by using the equation H =EI (60/S) where H is the energy input in joules per linear measure of weld, E is the arc voltage in volts, I is the welding current in amperes, and S is the travel speed (linear measure) per minute. By increasing the amperage or voltage, heat input increases, but by increasing the travel speed, heat input decreases. The voltage has a minor effect, because it varies only slightly, when compared with the other factors.
In general higher input reduces the cooling rate. This is to be used with care, since with Q&T steels, very high heat input tends to soften the HAZ, and its strength level is reduced. In case of low hardenability steel, it is possible to produce an unhardened HAZ by increasing the heat input. In case of higher hardenability steel, the tendency toward cracking and the maximum hardness are reduced by a slower cooling rate. These factors limit the amount of heat input which can be applied. Normally preheating is used in order to reduce the cooling rates.
Welding process also influences the heat input. Each welding process has a different thermal cycle. For example, the rate of heat rise, the maximum temperature, the time at high temperature, and the rate at which the metal cools are quite different for the shielded metal arc welding (SMAW) and the ESW processes. Those processes with the highest concentration of heat generally cause the temperature to rise and to fall much more quickly. In case of SMAW, the rise is almost instantaneously, and the cooling rate of the base steel is very fast. In case of ESW the rise is slower and is held at a high temperature for a fairly long time, and then decreases slowly.
The temperature changes that occur during an arc welding operation are much quicker and more abrupt than for most metallurgical processes. The metallurgical reactions from the heat of welding do not follow the normal heat treatment relationships. The temperature changes with ESW are more similar to those encountered in foundry metallurgy.