Pembentukan Awal Otomatis, Bagian 7:Isi Gesellschaft
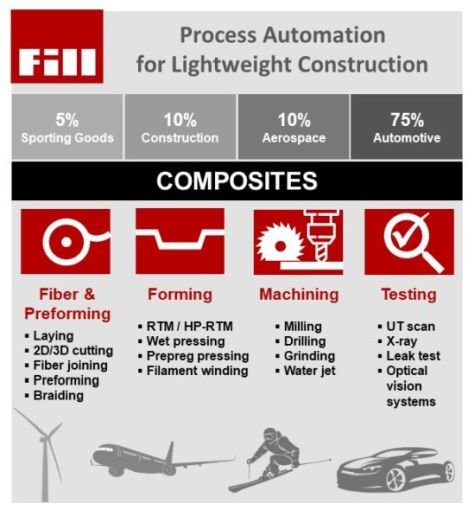
Ini adalah angsuran terakhir dari seri tujuh bagian tentang pembentukan awal. Untuk lebih lanjut tentang seri ini, klik tautan di bawah ini:
SUMBER:Isi Gesellschaft
Riwayat Kasus Otomatisasi
Mesin pertama Fill dikembangkan untuk mengotomatisasi produksi alat ski untuk Fischer. Saat ini dibutuhkan 25 persen pekerja untuk menghasilkan 80 persen dari volume produksi tahunan asli. Perhatikan juga bahwa ski adalah desain hibrida, yang terdiri dari lapisan kaca dan/atau komposit serat karbon, inti kayu, tepi baja, dan beberapa jenis plastik.
Isi telah disediakan beberapa generasi peralatan otomatis untuk memproduksi ski komposit.
SUMBER:Isi presentasi CAMX Gesellschaft 2017.
BMW
Saat BMW mengembangkan model i3, i8, dan Seri 7 baru—semuanya menggunakan komposit plastik yang diperkuat serat karbon (CFRP)—Fill menyediakan berbagai solusi otomatisasi.
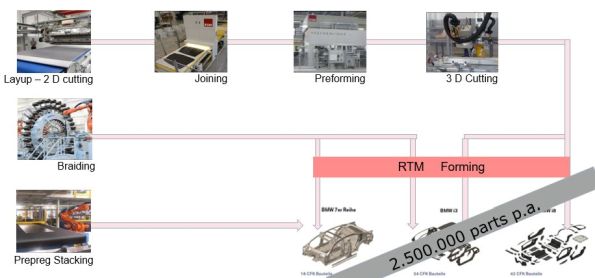
SUMBER:Isi Presentasi CAMX Gesellschaft 2017
Monocoque Komposit
Fill juga mengembangkan lini produksi unik untuk Mubea CarboTech yang mampu memproduksi monocoque CFRP untuk dua model mobil yang berbeda:Volkswagen VW XL1 dan Porsche 918 Spyder. Lini otomatis ini mencakup alat pencetakan multi-bagian yang digerakkan, mesin cetak transfer resin tekan tinggi (HP-RTM), kemampuan pasca perawatan dan pemesinan.
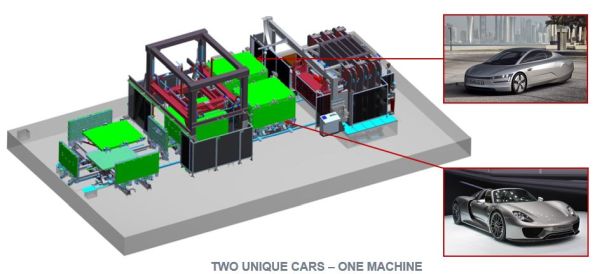
Isi yang disediakan lini produksi monocoque komposit untuk Mubea CarboTech.
SUMBER:Isi presentasi CAMX Gesellschaft 2017
Mengotomatiskan Tata Letak
Untuk layup otomatis, Fill telah mengembangkan sistem untuk berbagai bahan yang berbeda, termasuk kain kering dengan lebar hingga 3 m (untuk produksi volume lebih tinggi di BMW). Sistem peletakan tutup tiang otomatis SpeedLayer 800 untuk bilah turbin angin menerapkan prepreg serat karbon searah hingga lebar 800 mm pada kecepatan yang dilaporkan 1,5 m/s dan akurasi ±1,5 mm. Ini dapat menangani gulungan prepreg 600 kg dan mengintegrasikan validasi proses dan fungsi jaminan kualitas.
Isi telah dikembangkan berbagai sistem layup otomatis (kiri) termasuk SpeedLayer 800 untuk tutup tiang bilah angin menggunakan prepreg karbon UD dengan lebar hingga 800 mm (kanan).
SUMBER:Isi presentasi CAMX Gesellschaft 2017
Proyek Proses Komposit Terpadu Fleksibel Berbiaya Rendah (LOWFLIP) adalah inisiatif yang didanai Uni Eropa selama 3 tahun (Okt 2013-Okt 2016) yang mencakup Fill dan sembilan mitra lainnya, yang bertujuan untuk mengotomatiskan layup prepreg untuk transportasi yang disembuhkan di luar autoklaf (OOA). struktur. Ini terdiri dari tiga demonstran:
- Dinding depan 2,5 × 2,9 m untuk trailer truk
- Panjang balok silang otomotif 1,2 m
- Panel tailcone pesawat kulit yang kaku 1,0 × 1,2 m
Animasi
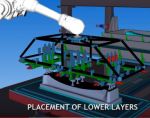
Pegangan multifungsi
Fill bekerja dengan sembilan mitra di LOWFLIP untuk mengembangkan sel layup otomatis untuk produksi struktur transportasi komposit besar tanpa autoklaf.
SUMBER:Isi presentasi CAMX Gesellschaft 2017
“Kami menggunakan pemanas hambatan listrik untuk memanaskan cetakan hingga 120°C,” kenang Wilhelm Rupertsberger, kepala Pusat Kompetensi untuk Komposit dan Plastik Fill. “Material selalu berada di bawah tekanan selama layup otomatis,” tambahnya, “dan kami mencapai draping tanpa kerutan langsung ke cetakan. Kami membangun proses manusia, tetapi yang menggunakan robot untuk meningkatkan pengulangan.”
Anda dapat melihat dinding trailer truk di sebelah kiri, serta demonstran panel balok silang mobil dan kerucut ekor pesawat pada foto tim LOWFLIP di atas .
SUMBER:Isi presentasi CAMX Gesellschaft 2017
Multi-Layup ke Sistem Multilayer
Sistem Multi-Layup Fill dikembangkan untuk produksi bagian body-in-white (BIW) otomotif seperti dinding belakang dan pengaku bumper bawah menggunakan pita termoplastik. Diperkirakan bahwa bagian-bagian ini akan mencakup tulang rusuk yang dicetak berlebih dan fitur lainnya, sehingga siklus layup untuk bentuk awal harus sesuai dengan siklus pencetakan injeksi berikutnya.
Posting blog pasca-pertunjukan JEC 2017 saya menyertakan video Sistem Multi-Layup, yang memasukkan kaset dari beberapa gulungan, menempatkan semua kaset yang dibutuhkan per lapisan secara bersamaan, bukan serial, satu per satu. Dengan cara ini, ia mencapai waktu siklus 10-15 detik per lapisan.
Fill sekarang telah memodifikasi sistem lebih lanjut dan menamainya Multilayer. Ini memberi makan, memotong, dan menempatkan hingga 16 pita dengan lebar hingga 50 mm (masing-masing setebal 0,01-0,04 mm) ke meja putar. Tempat tidur peletakan pita dapat menghasilkan bagian hingga 1,6 × 1,6 m. Kaset diterapkan pada kecepatan 500 m
2
/ jam—setiap 12-15 detik, lapisan bagian berukuran penuh diterapkan selama kira-kira 1 menit waktu siklus per bentuk awal yang telah selesai. Lapisan tidak sepenuhnya terkonsolidasi tetapi bergabung melalui ikatan termal. Saat setiap spool kehabisan pita, tape akan otomatis berubah tanpa menghentikan mesin.
Isi Multilayer otomatis sistem preforming memungkinkan pengurangan yang signifikan dalam limbah pemangkasan sementara menempatkan pita hanya jika diperlukan dan mengarahkannya seperlunya untuk mencapai laminasi yang disesuaikan.
SUMBER:Isi presentasi CAMX Gesellschaft 2017
Preforms yang sudah jadi kemudian dikonsolidasikan dalam pers. “Kami telah mengintegrasikan Multilayer dengan press konsolidasi otomatis dan sel cetakan injeksi Engel yang berfungsi bersama untuk menghasilkan waktu siklus 1 menit,” kata Rupertsberger. Fill menerima pesanan untuk sistem Multilayer pertama dari Swinburne University of Technology (Melbourne, Australia) awal tahun ini dan akan mendemonstrasikan peralatan tersebut secara langsung untuk pertama kalinya di JEC World 2019 (12-14 Maret, Paris, Prancis).
Tekan RTM dan Injeksi Adaptif
Fill telah memasok beberapa pengepres RTM, termasuk pengepres HP-RTM ke Komposit SGL.
Isi telah disediakan berbagai macam pengepres untuk produksi komposit, termasuk pengepres HP-RTM hingga Komposit SGL (kanan).
SUMBER:Isi Gesellschaft
Dengan Airbus Operations (Stade, Jerman) dan Institute of Plastics Processing (IKV) di RWTH Aachen University, Fill telah mengembangkan unit injeksi adaptif inovatif untuk RTM pada awalnya untuk struktur aerokomposit. Sebelum suku cadang yang dibuat dengan RTM dapat terbang di pesawat, suku cadang tersebut harus melewati proses jaminan kualitas (QA) yang memakan waktu dan mahal. Untuk mempersingkat proses ini, alat pembentuk RTM telah dilengkapi dengan sensor, yang memungkinkan QA diterapkan secara inline selama produksi. IKV, Airbus, dan Fill kini telah mengintegrasikan sensor ini ke dalam sistem injeksi, sehingga tidak perlu lagi melengkapi setiap alat pembentuk. Menggunakan kartrid sekali pakai dengan cara yang sama seperti sistem injeksi piston yang digunakan dalam sistem RTM biasa, unit injeksi adaptif dilengkapi dengan kotak sensor yang memungkinkan data berikut diukur dan direkam di lokasi:
- Suhu
- Tekanan
- Viskositas resin
- Kepadatan cross-link dari sistem resin
- Suhu transisi gelas (Tg).
Sambil memastikan kualitas bagian yang dicetak, data ini juga dapat digunakan untuk mengelola dan mengontrol proses injeksi. Sistem injeksi adaptif Industri 4.0 ini sedang dikembangkan untuk aerokomposit, dan juga diperluas ke industri lain seperti otomotif.
Pembentukan Tirai Panas
Dalam artikel tur baru-baru ini Sara Black dan saya menulis tentang komposit berkinerja tinggi di Israel, kami mencatat bahwa sebagian besar perusahaan menggunakan hot drape forming. Faktanya, di Elbit Cyclone, pemandu wisata kami Jonathan Hulaty menyatakan, "Saya tidak tahu bagaimana Anda melakukan jenis produksi suku cadang prepreg tingkat tinggi ini tanpa pembentukan tirai panas," mengacu pada balok dan tiang penyangga untuk rakitan Boeing 787. Pembentuk tirai panas (HDF) juga dipandang sangat diperlukan oleh FBM dan Israel Aerospace Industries. Fill telah memasok sistem HDF selama bertahun-tahun, termasuk beberapa unit yang diproduksi di FACC. Mereka pada dasarnya adalah sistem pembentuk vakum, dilengkapi dengan inframerah atau jenis elemen pemanas lainnya dan membran karet silikon yang dapat digunakan kembali untuk memanaskan dan mengompres—debulk—layup prepreg pada alat mereka sebelum proses curing. HDF menjadi bagian penting dalam lini produksi aerokomposit lengkap yang ditunjukkan di bawah ini.
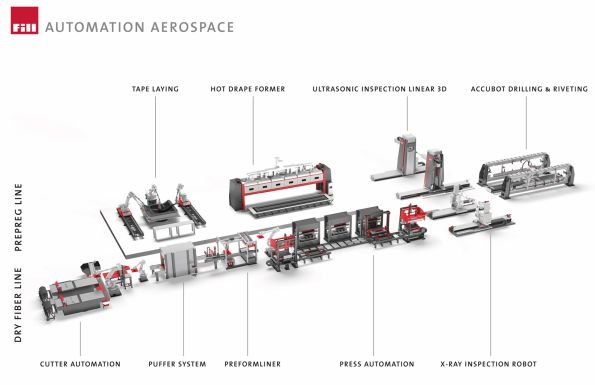
Pembentukan tirai panas telah menjadi enabler penting untuk produksi volume tinggi dari aerostruktur komposit prepreg dan diotomatisasi oleh Fill sebagai bagian dari solusi rantai proses lengkapnya. SUMBER: Isi Gesellschaft
Sel Produksi Industri 4.0 untuk CFRP
Pada akhir tahun 2013, Fill mulai mengembangkan sistem produksi untuk pembuatan stringer CFRP, yang digunakan untuk memperkuat cangkang penutup pendaratan Airbus A320, bekerja sama dengan pemasok Tier. Setelah instalasi, sistem ini berhasil mengurangi jumlah stasiun, meningkatkan aliran produksi, dan juga meningkatkan kemudahan penggunaan. Ini terdiri dari:
- Penyimpanan alat pembentuk otomatis
- Stasiun HDF
- Stasiun press-turn-lifting tempat laminasi diproses menjadi stringer.
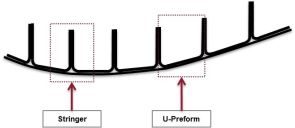
(klik gambar untuk memperbesar)
Isi telah dikembangkan tiga generasi sel produksi otomatis (kanan) untuk senar penutup roda pendarat yang terbuat dari prepreg (kiri).
SUMBER: Isi Gesellschaft
Sistem generasi kedua untuk memproduksi jenis suku cadang yang sama telah ditugaskan pada tahun 2017. Di mana sistem pertama berfokus pada pengoptimalan stasiun individu, sistem selanjutnya ini bertujuan untuk meminimalkan tugas manual dan mengintegrasikan semua logistik alat. Tiga bidang utama pengembangan memungkinkan sistem generasi kedua ini mencapai reproduktifitas tinggi dan produktivitas yang meningkat secara signifikan:
- Pengambilan manual dan penyimpanan alat pembentuk diganti dengan pengembalian alat sepenuhnya otomatis, mempersingkat waktu proses logistik. Ini juga mengurangi kebutuhan ruang lebih dari 50 persen.
- Otomasi subproses lebih lanjut telah mengurangi waktu yang tidak produktif.
- Digitalisasi Industri 4.0 dari semua perekaman dan pelaporan. Perangkat lunak yang dikembangkan oleh Fill memungkinkan visualisasi proses setiap saat dan perekaman riwayat setiap komponen di sepanjang rantai proses. Sensor mendeteksi ketersediaan alat dan bahan untuk menghindari kemacetan dan meningkatkan pemesanan ulang.
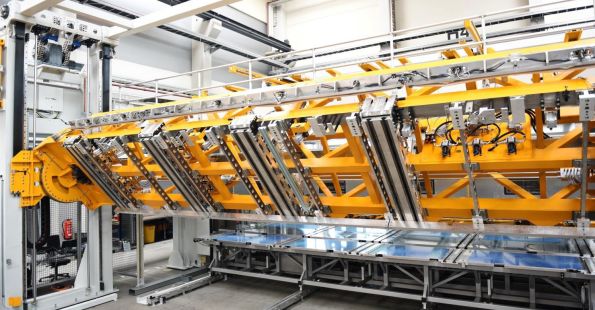
Tekan-putar -stasiun pengangkat yang digunakan dalam sel produksi otomatis untuk senar penutup roda pendarat A320 dan A350.
SUMBER: Isi Gesellschaft
Fill sekarang sedang mengerjakan sistem produksi generasi ketiga untuk cangkang penutup pendaratan yang ditujukan untuk Airbus A350-900. Ini juga terdiri dari penyimpanan alat, stasiun pembentuk membran (HDF), stasiun tekan-putar-angkat dan pengembalian alat otomatis tetapi telah ditingkatkan dengan sistem transportasi untuk alat autoklaf, menggantikan truk pengangkut manual sebelumnya dan traktor listrik dengan kendaraan berpemandu otomatis (AGVs). ). Fill sedang mengerjakan sistem masa depan, mencari cara untuk lebih meningkatkan kolaborasi manusia dan mesin.
Accubot
Bahkan sebelum industri komposit mulai mengungkapkan kebutuhan masa depan yang mereka bayangkan akan sel kerja multi-operasi, Fill sudah mengembangkan prototipe pertama, yang disebut Accubot. Idenya adalah untuk mengembangkan robot yang akurat menggunakan pelacak laser untuk kompensasi spasial serta sistem pengukuran eksternal langsung. Robot ini akan dapat beralih fungsi dengan efektor akhir, menjadi tidak hanya sel pengujian tak rusak (NDT) tetapi juga sel pemesinan. Aplikasi Accubot meliputi:
- Pengeboran
- Memukau
- NDT – Ultrasound dengan squirter
- NDT – Rontgen
- NDT – Computed tomography
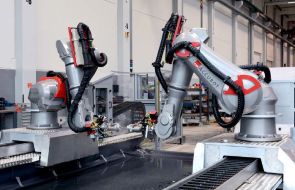
klik untuk memperbesar
Accubot untuk pengeboran (kiri) dan NDT menggunakan pemindaian ultrasonik berkecepatan tinggi (kanan).
SUMBER:Isi Gesellschaft.
FlexHyJoin
Fill adalah anggota dari proyek Flexible Production Cell for Hybrid Joining (FlexHyJoin) yang didanai oleh Uni Eropa. Program 3 tahun ini bertujuan untuk mengembangkan proses percontohan yang sepenuhnya otomatis untuk penyambungan braket/fitting logam dengan komposit termoplastik dalam aplikasi otomotif dengan menggabungkan teknologi penyambungan laser dan penyambungan induksi. Isi sel yang dirancang dan dibangun otomatis termasuk perangkat lunak dan integrasi berbagai teknologi.
Penelitian dan pengembangan Fill terus berlanjut. Ini memahami bahwa sistem produksi yang inovatif dan cerdas diperlukan untuk membuat pembuatan suku cadang komposit lebih ekonomis dan dapat menerima volume yang lebih tinggi. Dan berkomitmen untuk mengembangkan sistem ini sesuai dengan skala dan kebutuhan spesifik pelanggannya.
SUMBER:FlexHyJoin.
Hybrid otomatis bergabung dengan sel yang dikembangkan oleh Fill Gesellschaft sebagai bagian dari proyek FlexHyJoin. SUMBER:Isi Gesellschaft dan FlexHyJoin.