Ini adalah Bagian 2 dari seri perangkat lunak MES kami. Temukan artikel lainnya dalam seri ini:
- Panduan Pemula untuk Sistem Eksekusi Manufaktur Aditif (MES)
- Bagaimana Digitalisasi Dapat Membantu Mengubah Pasca-Pemrosesan AM dan Manajemen QA
- 3 Cara Konektivitas Akan Meningkatkan Operasi Manufaktur Aditif Anda
Saat produsen saat ini ingin meningkatkan operasi manufaktur aditif mereka, orang-orang yang berpikiran maju secara aktif mencari untuk mengoptimalkan satu bidang utama:perencanaan produksi.
Perencanaan produksi adalah inti dari setiap strategi manufaktur aditif yang hebat. Dengan manajemen produksi dan proses perencanaan yang tepat, produsen dapat berhasil mengintegrasikan AM ke dalam strategi manufaktur mereka yang lebih luas, mendapatkan visibilitas penuh ke dalam operasi mereka, dan secara signifikan meningkatkan efisiensi.
Artikel ini akan membahas pentingnya perencanaan produksi untuk aditif, tantangan umum yang dihadapi produsen saat mengelola operasi mereka, dan bagaimana Anda dapat menggunakan perangkat lunak MES untuk mengatasi tantangan ini — dan memaksimalkan peluang Anda untuk sukses dengan AM.
Mengapa saya perlu memikirkan perencanaan produksi untuk fasilitas AM saya?
“Jika Anda gagal merencanakan, Anda sedang merencanakan kegagalan.”― Benjamin Franklin
Keberhasilan pembuatan suku cadang AM bersertifikat memerlukan pertimbangan yang cermat dari seluruh proses produksi. Ini adalah hasil dari urutan langkah yang sangat terintegrasi yang harus diikuti untuk mencapai hasil akhir.
Kurangnya perencanaan produksi berarti kurangnya kontrol atas proses produksi. Hal ini meningkatkan kemungkinan inefisiensi di seluruh alur kerja dan menghilangkan hambatan utama dalam proses.
Perencanaan produksi untuk AM adalah strategi Anda untuk mengelola seluruh proses manufaktur aditif. Ini mencakup tahapan kunci dari proses produksi AM, seperti persiapan build, penjadwalan produksi, dan pemantauan status mesin.
Proses perencanaan produksi yang jelas membawa kontrol yang lebih besar atas proses produksi itu sendiri.
Kontrol produksi berarti Anda memiliki gambaran lengkap tentang operasi Anda dan dapat merespons peristiwa secara real time, di mana pun fasilitas Anda berada. Kemampuan ini pada akhirnya akan memungkinkan Anda untuk menskalakan operasi AM Anda dari waktu ke waktu.
Saat perusahaan ingin mengintegrasikan AM ke dalam operasi manufaktur mereka, sekaranglah saatnya untuk mempertimbangkan bagaimana Anda dapat mengoptimalkan proses manajemen produksi Anda untuk mencapai efisiensi dan produktivitas maksimum.
8 tantangan paling umum yang dihadapi produsen dengan perencanaan produksi untuk manufaktur aditif
40% produsen melaporkan telah mengadopsi manufaktur aditif di dalam perusahaan, menurut laporan EY. Dengan angka ini yang akan terus bertambah, OEM tidak pernah merasa lebih penting untuk mempertimbangkan perencanaan produksi sebagai bagian utama dari strategi AM internal mereka.
Namun, ada sejumlah potensi jebakan yang mungkin dihadapi perusahaan dalam hal menetapkan strategi perencanaan yang jelas. Berikut adalah delapan tantangan utama yang dihadapi dalam hal manajemen produksi untuk AM.
Tantangan #1:Tidak ada pemahaman yang jelas tentang kapasitas
Mendefinisikan kapasitas produksi yang ada adalah kunci untuk perencanaan produksi yang efisien.
Penilaian kapasitas produksi yang realistis mencakup faktor-faktor seperti ketersediaan waktu mesin, fleksibilitas berbagai jenis sistem AM untuk tugas yang berbeda, dan ketersediaan tenaga kerja terampil di dalam fasilitas.
Namun, banyak pabrikan AM menghadapi masalah perencanaan kapasitas, paling tidak karena mereka mengandalkan data tersembunyi.
Menggunakan sistem yang berbeda dan tidak terhubung berarti bahwa data sering kali perlu disinkronkan secara manual sebelum dapat ditindaklanjuti. Tidak hanya menambah waktu, tetapi juga membuat data menjadi usang bahkan sebelum dapat digunakan.
Tanpa visibilitas real-time ke dalam kapasitas, produsen AM akan berjuang untuk sepenuhnya memahami kapasitas mereka saat ini, yang mengarah pada perkiraan kebutuhan kapasitas masa depan yang tidak akurat.
Tantangan #2:Menggunakan teknologi yang tidak sesuai dan ketinggalan zaman untuk menjadwalkan produksi
Selain perencanaan kapasitas, terdapat juga tantangan dalam merencanakan kegiatan produksi pabrik AM. Produsen AM sering berjuang untuk meningkatkan throughput dan menjadwalkan aktivitas menit ke menit di lantai toko AM.
Banyak pabrikan AM mencoba melakukan perencanaan dan penjadwalan produksi dengan sistem lama atau alat manipulasi data yang tidak dilengkapi dengan baik untuk tugas tersebut.
Misalnya, sistem ERP Anda mungkin menyertakan modul perencanaan untuk penjadwalan produksi induk dan perencanaan kebutuhan material. Namun, tidak satu pun dari sistem perencanaan ini yang dirancang untuk menjadwalkan produksi AM.
Tanpa alat yang tepat untuk pekerjaan itu, akan sulit untuk membuat jadwal yang akurat, yang menjadi faktor dalam prioritas tak terduga dan perubahan yang mungkin muncul.
Tantangan #3:Proses pelacakan pekerjaan manual
Lembar kerja manual yang sudah usang sangat tidak efisien jika dibandingkan dengan lembar kerja otomatis dalam sistem perangkat lunak.
Lembar pekerjaan yang dicetak sering hilang saat teknisi menyerahkannya satu sama lain, yang menyebabkan penundaan. Selain itu, proses ini tidak memberikan visibilitas apa pun ke dalam pekerjaan yang sedang berlangsung tanpa secara fisik berada di lantai pabrik.
Tantangan #4:Mempersiapkan cetakan 3D untuk produksi
Berurusan dengan berbagai pesanan dari banyak pelanggan menambah lapisan kerumitan lain pada perencanaan produksi.
Pesanan biasanya harus diproduksi menggunakan bahan dan teknologi pencetakan 3D yang berbeda, yang berarti pesanan harus dikelompokkan terlebih dahulu.
Sistem berbasis kertas atau terputus membatasi kemampuan Anda untuk mengelompokkan pesanan dan menjadwalkannya secara efisien. Mereka juga tidak memberikan informasi waktu nyata dan, akibatnya, Anda tidak dapat memanfaatkan waktu atau kapasitas Anda secara maksimal.
Tantangan #5:Kurangnya visibilitas data
Data adalah inti dari semua produksi AM.
“Dengan semua pilihan bahan dan pasca-pemrosesan yang berbeda, manufaktur aditif dapat dengan mudah menjadi rumit ,” jelas Timm Kragl, Konsultan Senior di Phanos GmbH.
“Untuk perusahaan, pertanyaannya kemudian menjadi, bagaimana kami dapat melacak alur kerja yang kompleks dan data dalam jumlah besar ini? ”
Ini adalah pertanyaan kunci, karena dalam fasilitas AM mana pun, data dihasilkan di setiap tahap produksi — terus-menerus.
Ini termasuk:
- Data yang dihasilkan mesin (misalnya teknologi, status mesin, aktivitas, data sensor),
- Bagian data (misalnya orientasi bagian, posisi, parameter)
- Data bahan (misalnya jenis bahan, tingkat stok)
- Data pasca-pemrosesan dan pengelolaan kualitas (misalnya langkah pascapemrosesan, persyaratan kepatuhan)
- Data untuk pelaporan (mis. keberhasilan cetak vs. tingkat kegagalan, hasil)
Karena volume data yang dihasilkan selama proses produksi, melacak data ini dan menggunakannya untuk membuat keputusan penting merupakan tantangan utama.
Tantangan #6:Memastikan pengulangan
Kualitas adalah prioritas utama dalam hal AM.
Khusus untuk produksi serial, manufaktur aditif harus dapat mempertahankan standar yang sama dengan proses manufaktur tradisional.
Untuk mencapai hal ini, diperlukan langkah-langkah produksi yang berulang dan konsisten untuk memastikan bahwa setiap bagian memenuhi persyaratan yang sama.
Oleh karena itu, mendokumentasikan langkah-langkah proses yang tepat sangat penting untuk menghasilkan suku cadang berkualitas tinggi yang sama setiap saat.
Tanpa sistem untuk melacak ini, memastikan pengulangan produksi menjadi hampir mustahil untuk dicapai.
Tantangan #7:Ketertelusuran operasional
Siapa yang membuat perubahan itu ke file CAD? Apakah bagian ini sudah diperiksa? Batch material apa yang telah digunakan untuk memproduksi komponen ini?
Pertanyaan-pertanyaan ini (dan lainnya) hanya dapat dijawab jika ada ketertelusuran ujung ke ujung di seluruh operasi Anda.
Ketertelusuran berarti dapat melacak setiap langkah alur kerja AM Anda, bersama dengan langkah-langkah produksi yang perlu diambil pada setiap tahap.
Selain itu, ketertelusuran berarti mengetahui dengan tepat tindakan apa yang telah dilakukan pada jam berapa dan memberi Anda wawasan mendalam tentang potensi kemacetan dalam operasi Anda.
Pengetahuan ini adalah kunci untuk memahami dan mengoptimalkan kinerja operasi Anda.
Namun, ketertelusuran sangat menantang untuk dicapai, terutama jika Anda mengoperasikan banyak lokasi produksi.
“Perusahaan harus memiliki visibilitas informasi seperti apa yang telah dipesan, oleh siapa dan dalam jangka waktu berapa, serta berbagai langkah yang diperlukan untuk produksi, bagaimana menjadwalkan dan sebagainya,” jelas konsultan AM, Timm Kragl.
Dua hambatan terbesar untuk keterlacakan adalah sistem yang terputus dan proses manual, yang tidak memungkinkan akses data secara real-time.
Yang terpenting, kurangnya ketertelusuran akan membuat Anda hampir tidak mungkin menskalakan operasi Anda secara efektif.
Tantangan #8:Mengelola dan mengoordinasikan pemasok
26% OEM mengalihdayakan setidaknya sebagian dari produksi pencetakan 3D mereka ke pemasok mereka, menurut EY.
Outsourcing menyediakan cara bagi produsen untuk menyelesaikan pekerjaan AM yang tidak dapat dilakukan secara internal. Itu juga membuat manufaktur sesuai permintaan — konsep memproduksi produk sesuai permintaan, mendekati atau pada titik kebutuhan — menjadi kenyataan. Ini memiliki manfaat tambahan untuk mengurangi waktu henti pabrik dan meningkatkan efisiensi operasional.
Oleh karena itu, untuk sebagian besar produsen, perencanaan produksi AM perlu menyertakan pengelolaan outsourcing pekerjaan tertentu kepada pemasok pihak ketiga.
Ini berarti bahwa OEM harus mampu mengelola dan menjalankan operasi tidak hanya secara internal tetapi juga secara eksternal, di seluruh rantai pasokan mereka.
Outsourcing membutuhkan koordinasi dan integrasi tingkat tinggi untuk memastikan bahwa produk dikirimkan dengan spesifikasi yang tepat pada waktu yang tepat.
Untuk OEM dan pemasok, ini berarti mengetahui apa yang perlu dialihdayakan – dan kepada siapa – dan memastikan bahwa pemangku kepentingan utama selalu mendapatkan informasi terbaru setiap saat.
Tingkat koordinasi ini menantang jika, seperti halnya dengan sebagian besar produsen, tidak ada sistem terpusat untuk memfasilitasi komunikasi antara OEM dan pemasok mereka.
Bagaimana Anda dapat mengatasi tantangan manajemen produksi Anda dengan perangkat lunak Additive MES
Meskipun ada tantangan terkait perencanaan produksi untuk AM, kabar baiknya adalah perangkat lunak MES, yang dikembangkan secara khusus untuk manufaktur aditif, menawarkan alat yang diperlukan untuk mengatasi tantangan ini.
Perangkat lunak MES aditif adalah perangkat lunak alur kerja yang membantu produsen mengelola operasi AM mereka dengan memungkinkan keterlacakan yang lebih baik, wawasan data yang lebih baik, dan menetapkan proses praktik terbaik di seluruh alur kerja AM mereka.
Namun bagaimana Anda bisa menggunakan MES dan perangkat lunak alur kerja untuk meningkatkan proses manajemen produksi Anda?
1. Merampingkan penjadwalan produksi
Perangkat lunak MES aditif memberi produsen alat yang andal untuk menjadwalkan dan memprioritaskan pekerjaan produksi AM.
Saat pesanan masuk, manajer produksi tambahan dapat menggunakan perangkat lunak alur kerja untuk mengelompokkan pesanan dengan mudah menurut teknologi produksi, persyaratan material, dan tingkat prioritas mereka. Pesanan yang dikelompokkan membuat batch produksi, sering disebut build.
Dalam solusi manajemen alur kerja tingkat lanjut, ada juga fitur yang memungkinkan pesanan ditugaskan untuk membangun pekerjaan hanya jika memenuhi persyaratan pembangunan itu. Ini berarti bahwa penjadwal tidak akan dapat menambahkan, misalnya, suku cadang yang akan diproduksi di PA 12 ke build yang menggunakan PA 11. Fitur ini pada akhirnya membantu mencegah kesalahan dan pengerjaan ulang yang berpotensi mahal, sehingga merampingkan penjadwalan lebih jauh.
Bawa pulang: Gunakan MES dan perangkat lunak alur kerja untuk mengotomatiskan persiapan pembuatan dan memastikan penjadwalan yang akurat.
2. Tingkatkan visibilitas perencanaan produksi
Setelah bagian-bagian telah ditetapkan ke build, perangkat lunak MES memungkinkan untuk memvisualisasikan semua pekerjaan terjadwal pada bagan alur kerja bergaya kalender, yang dikenal sebagai bagan Gantt.
Bagan Gantt memberikan informasi yang relevan dengan penjadwalan produksi secara sekilas. Misalnya, di bagan Gantt AMFG Anda dapat melihat:
- Tanggal mulai dan berakhirnya pembangunan
- Buat waktu dan status
- Jumlah bagian dalam bangunan
- Informasi tentang mesin dan bahan yang digunakan
Tanggal dan tenggat waktu yang ditentukan dengan jelas memberdayakan staf Anda untuk memprioritaskan pekerjaan mereka dan memenuhi tenggat waktu. Selain itu, menampilkan jadwal pekerjaan AM terbaru membantu semua orang (tim dan pelanggan) mengetahui perkembangannya.
Selain itu, bagan Gantt memungkinkan Anda melihat garis waktu proyek di mana Anda dapat dengan mudah melihat bagaimana dan di mana sistem AM digunakan. Jika mesin dikelola dengan benar, pekerjaan AM kemungkinan besar akan diselesaikan sesuai anggaran dan tenggat waktu.
Bawa pulang: Gunakan MES dan perangkat lunak alur kerja untuk meningkatkan visibilitas produksi dan memahami kapasitas dengan lebih baik.
3. Gunakan perangkat lunak MES untuk membuat utas digital berbasis data
Seperti yang telah kita lihat, data sangat penting untuk operasi manufaktur aditif.
Pada dasarnya, MES dan perangkat lunak alur kerja memberikan landasan di mana OEM dapat melacak dan menganalisis data di seluruh proses produksi AM, termasuk pasca-pemrosesan dan manajemen kualitas.
Selain itu, data historis dapat diakses untuk memberikan pembelajaran utama dan mengoptimalkan proses.
Pelacakan, pelaporan, dan analitik KPI adalah cara lain di mana produsen dapat memanfaatkan perangkat lunak MES untuk mempelajari lebih dalam faktor-faktor utama yang mendorong produktivitas.
Memiliki proses ini yang dikelola oleh platform digital memberikan rangkaian digital yang mulus dan menciptakan efisiensi operasional dan ketertelusuran yang lebih besar.
Bawa pulang: Gunakan wawasan data yang disediakan oleh perangkat lunak MES untuk mempelajari, menskalakan, dan membangun proses produksi AM yang dapat diulang.
4. Pastikan pengulangan untuk produksi serial
Bagi produsen yang ingin memanfaatkan AM untuk memproduksi suku cadang akhir, pengulangan dan prediktabilitas adalah kuncinya.
Seperti yang telah kita lihat, memastikan bahwa bagian yang sama diproduksi setiap saat dan standar kualitas terpenuhi secara konsisten, sangat penting untuk produksi serial.
Untuk ini, proses manajemen alur kerja berulang yang memastikan prediktabilitas sangat penting. Kriteria utama untuk ini adalah:
- Orientasi bagian
- Posisi
- Materi
- Mesin
Perangkat lunak alur kerja dapat melacak parameter yang telah menghasilkan kesuksesan di masa lalu, memberi Anda detail tingkat tinggi ke dalam langkah-langkah proses yang optimal.
Misalnya, parameter yang diperlukan untuk bagian tertentu yang akan diproduksi dapat dilacak oleh sistem, dan diakses kembali jika bagian yang sama perlu diproduksi. Ini, pada gilirannya, dapat dikaitkan dengan langkah-langkah manajemen pasca-pemrosesan yang perlu diambil segera setelah produksi.
Bonus:Kelola produksi prototipe dengan lebih mudah
Dalam hal pembuatan prototipe, biasanya, Anda akan memproduksi suku cadang satu kali dalam jumlah besar.
Di sini, tantangannya bukanlah pengulangan, tetapi mengelola volume permintaan yang tinggi untuk pengembangan produk Anda dan tim lain.
Metode konvensional untuk mengelola ini, seperti email dan spreadsheet, biasanya mengganggu proses perencanaan produksi, karena tidak terintegrasi dengan alur kerja AM yang lebih luas. Perangkat lunak MES dapat mengatasi ini.
Bawa pulang: Gunakan MES dan perangkat lunak alur kerja untuk menetapkan langkah-langkah proses standar yang jelas yang memastikan pengulangan produksi dan prediktabilitas.
5. Dapatkan tampilan 360 derajat dari operasi Anda
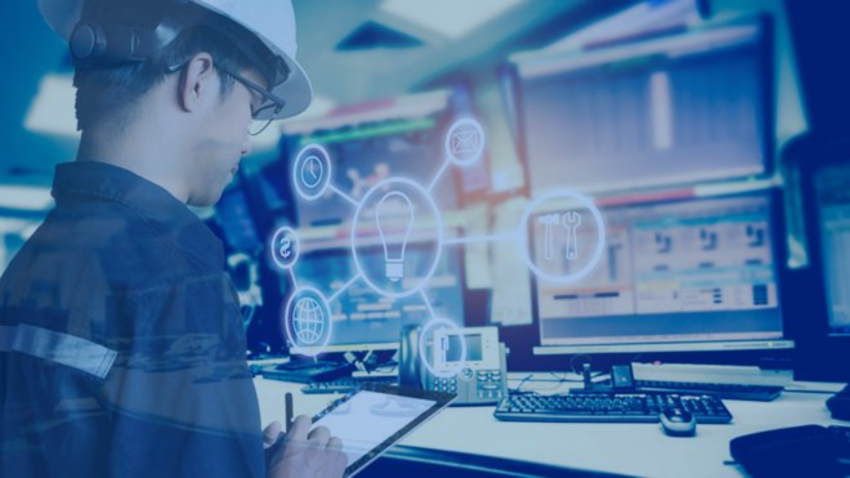
Perangkat lunak MES membantu menjaga ketertelusuran internal file, suku cadang, dan proses. Setiap produk atau batch dapat menerima nomor identifikasinya sendiri, yang juga dapat diberikan informasi tambahan selama proses manufaktur, seperti dimensi atau hasil QA.
Perangkat lunak alur kerja AM menawarkan 'satu versi kebenaran' yang membantu perusahaan memenuhi standar kualitas mereka dan menyelesaikan pemeriksaan audit.
Bawa pulang: Menggunakan perangkat lunak alur kerja memungkinkan Anda memperoleh keterlacakan lengkap di seluruh operasi AM Anda.
6. Mengkoordinasikan dan mengelola pemasok dengan lebih mudah
Sistem MES yang kuat adalah sistem yang memungkinkan Anda mengoordinasikan pemasok dan mengelola outsourcing pada satu platform standar.
Manfaatnya adalah ini membuat pemasok dan pemangku kepentingan internal Anda tetap selaras dan up-to-date dengan status real-time dari tugas dan tindakan tertentu.
Bawa pulang: Gunakan perangkat lunak MES untuk mengelola produksi internal dan eksternal Anda, dan merampingkan rantai pasokan Anda.
Memikirkan kembali perencanaan produksi dengan perangkat lunak MES tambahan
Manufaktur aditif menawarkan peluang strategis bagi produsen untuk mengembangkan keunggulan kompetitif.
Namun, sama seperti AM memerlukan pendekatan berbeda untuk memikirkan desain, mencapai tujuan di atas berarti memikirkan kembali pendekatan tradisional untuk mengelola produksi AM.
Pada kenyataannya, ini berarti mengadaptasi proses internal Anda agar sesuai dengan persyaratan produksi AM dan memastikan bahwa langkah-langkah alur kerja terintegrasi untuk mencapai efisiensi, visibilitas, dan produktivitas.
Menggunakan sistem yang tidak terhubung satu sama lain atau sangat manual adalah salah satu hambatan terbesar untuk efisiensi dan kontrol produksi.
Pada akhirnya, perangkat lunak MES yang dapat mengoordinasikan langkah-langkah proses, memberikan keterlacakan dan wawasan berbasis data adalah kunci untuk strategi manajemen produksi yang solid – dan memungkinkan Anda untuk menskalakan operasi AM Anda untuk masa depan.
Pelajari lebih lanjut tentang manajemen produksi untuk manufaktur aditif
Jika Anda ingin mempelajari lebih lanjut tentang cara menskalakan operasi AM Anda dengan perangkat lunak, kami sarankan untuk membaca buku putih baru kami, Additive Manufacturing MES Software:The Essential Guide.
Selain memberikan lebih banyak wawasan tentang perencanaan produksi untuk AM, Anda akan mempelajari lebih lanjut tentang cara mengembangkan strategi AM yang komprehensif dan bagaimana Anda dapat menggunakan software MES untuk membantu Anda menskalakan dan memperluas operasi AM Anda.
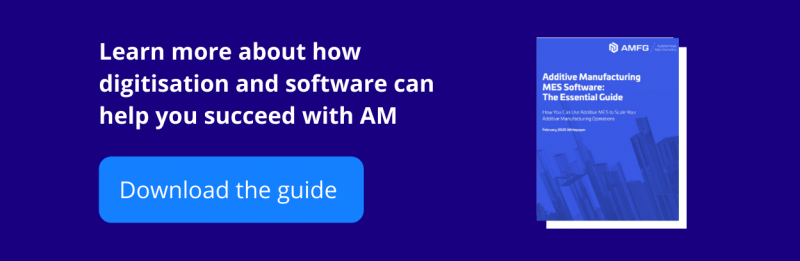